Реферат по темі випускної роботи
Зміст
- Актуальність переробки тонкодисперсних промислових відходів
- Цілі і
завдання роботи
- Основні
поняття
- Досліджуваний тонкодисперсний матеріал
- Закономірності компактування
- Методика
проведення дослідів
- Висновки
- Перелік посилань
Актуальність переробки тонкодисперсних промислових відходів
Промислове виробництво вогнетривких матеріалів є великим джерелом викидів тонкодисперсних відходів. Проблема ускладнюється ще й тим, що ці виробництва, як правило, зосереджені поруч з металургійними та гірничорудними, для яких екологічні проблеми є настільки ж актуальними. Більш того, за останнє сторіччя на території Україні навіть не ставилися питання про налагодженні небудь утилізації цих матеріалів і обмеження викидів на звалища.
Таким чином до теперішнього часу вже накопичено велику кількість тонкодисперсних
відходів, які є джерелом вторинного забруднення атмосфери,
поверхневих і підземних вод, грунтового шару.
У той же
час тонкодисперсний пил, який утворюється при виробництві вогнетривів,
володіє унікальними властивостями і є перспективною вторинною сировиною при
виробництві штучних виробів (цегли), а також неформованих вогнетривів
(вогнетривкі бетонів, торкрет-мас, набивних мас і сухих сумішей, вогнетривких
розчинів і т.д.). Тому його переробка та утилізація представляє особливий
інтерес. Використання тонкодисперсних відходів від вогнетривких виробів
ефективно, як з економічної, так і з екологічної точок зору, оскільки поряд з прямою вигодою застосування вторинної сировини, вирішується ряд
екологічно значущих проблем – раціонального використання природних ресурсів,
вторинного забруднення.
Цілі та завдання работы
Метою роботи
розробка безвідходної технології переробки тонкодисперсних відходів на діючих
підприємствах, що базується на дослідженні фізико- механічних властивостей та
процесів, які відбуваються під час компактування.
Для рішення цієї задачі необхідно знати комплекс фізико – механічних влативостей матеріалів. Основна особливість полягає у тому, що
матеріали, які використовують у виробництві мають різну структуру, частки у них
різної форми, розміру та по різному себе поводять у сумішах з іншими
матеріалами.
Властивості матеріалів необхідно знати для подальшого визначення можливості їх
застосування. Зокрема, для використання в якості добавок до основних виробів, а також як
самостійні вироби.Це особливо актуально в сучасних умовах при величезних масштабах забруднень.
У роботі проаналізовано процеси відбуваються під час компактування: пластична
деформація, пружна деформація, крихке руйнування. У роботі проаналізовано процеси відбуваються під час компактування: пластична
деформація, пружна деформація, крихке руйнування. Так само
врахована залежність реологічних особливостей. Розроблено математичну модель компактування тонкодисперсного матеріалу в
осесиметричній матриці. Предметом дослідження також є властивості матеріалу і отриманих формовок. Дані дослідження будуть застосовані для оптимізації технологічного процесу
компактірованія і зниження енергоємності.
Основні
поняття
Компактування – технологічний процес ущільнення шихти або порошку з метою
перетворення його на тверде виріб.
Основні параметри компактування – тиск ущільнення і спосіб його застосування,
середа і швидкість проведення процесу.
Основні труднощі, що виникають при використанні порошкових технологій для
отримання компактних виробів з тонкодисперсних часток, пов'язана із залишковою
пористістю, яка може бути зменшена додатком високого статичного чи динамічного
тиску.
Динамічні методи компактування тонкодисперсних матеріалів дозволяють подолати
сили адгезійного зчеплення, особливо значущі для часток з їх високорозвиненою
поверхнею, і при однаковому тиску досягти більшої щільності компактних зразків,
ніж в умовах стаціонарного компактування.
Основними
достоїнствами комактування:
1)
низьке споживання енергії;
2)
низький нагрів субстанцій;
3)
хороші властивості сипучості і, виходячи з цього, дозувальні властивості;
4)
підвищення насипної ваги;
5)
можливість вибору (відсіву) розміру гранул;
7)
відсутність пилу в разі опціональної замкнутої системи;
8)
відтворений масштабований процес.
Відзначаючи
всі особливості цього методу, можна також додати его досить просто
організувати практично на будь-якому вогнетривкому підприємстві без витрат
матеріальної бази.
Досліджуваний тонкодисперсный матеріал
Досліджуваний матеріал являє собою аеродісперсну систему (аерозоль),
в якій дисперсійним середовищем є повітря,а дисперсною фазою твердіпилові частинки.
Тонкодисперсні частинки утворюються при численних виробничихпроцесах:дробленні,змішуванні, пресуванні,випалюваннівиробів. Зокрема, це пил каоліну і глини різного ступеня випалення.Тонкодисперсні частинки були схоплені за допомогою циклонів, електрофільтрів,
гідравлічнихфільтрів і циклонів.
Пил є тонкодисперсною пудрою бежевого або сірого кольору
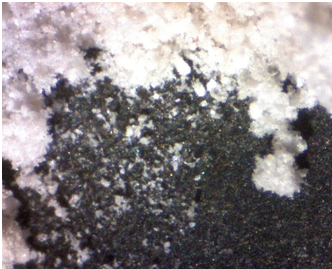
Рисунок 1 – Тонкодисперсний пыл електрофільтра
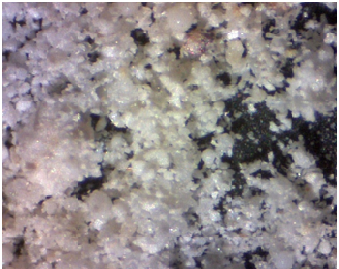
Рисунок 2 – Тонкодисперсний пыл циклона
Основные
закономерности компактирования
Тонкодисперсний матеріал є трифазною системою, що складається з
твердої мінеральної частини, рідкої фази води і повітря. Для отримання
високощільного формування необхідно вибрати кінцеве тиску, який забезпечить
повне усунення розташованих між частками вільних проміжків за рахунок
пластичної деформації частинок.
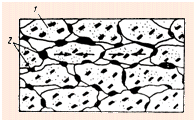
1 – рідка фаза, 2 – цементуючі глинисті агрегати
Рисунок 3 – Структура формовки
Початок компактування керамічного порошку супроводжується його ущільненням за
рахунок зміщення частинок щодо один одного і їх зближення. Це є першою
стадією ущільнення. При цьому відбувається часткове видалення повітря із системи.
Друга стадія ущільнення характеризується пластичної незворотною деформацією
частинок. При цьому збільшується контактна поверхня між частками.
Одночасно з цим ущільнення кожної елементарної частинки супроводжується
вижиманням вологи з її глибинних шарів на контактну поверхню частинки. обидва
ці чинники обумовлюють зростання зчеплення між частинками. Вода разом з
містяться в ній глинистими колоїдами цементує великі частки формування,
а зі збільшенням контактної поверхні зростає ефект такої цементації. В
цій стадії ущільнення може мати місце защемлення і пружне стиснення повітря,
який не встиг вийти з порошку.
На третій стадії ущільнення настає пружна деформація часток, яка переходить в крихке руйнування, при чому формовка отримує найбільшу
ущільнення і найбільшу зчеплення внаслідок сильного подальшого розвитку
контактної поверхні. Для здійснення крихких деформацій потрібний високий
тиск, який при компактування більшості виробів практично не
досягається.
Після припинення дії зусилля компактірованія та звільнення вироби з форми відбувається його пружне розширення. Пружне розширення не дає можливості
отримувати формовки з максимальною щільністю і є причиною утворення
інших вад виробів, спресованих з порошків.
Причинами пружного розширення можуть бути оборотні деформації твердих частинок,
розширення запресованого повітря, а також адсорбційна розклинення
контактів вологою, вичавленою при пресуванні з контактних поверхонь у більш
великі пори.
У міру зростання
тиску осаду спочатку
інтенсивно розвивається, потім починає затухати і при досягненні деякого
тиску, характерного для кожного порошку з даними властивостями, майже повністю
припиняється. Це вказує на те, що для кожного порошку з притаманними йому
властивостями існує певний тиск, перевищувати яку не має сенсу,
так як за його межами подальшого ущільнення пресування майже не відбувається.
Для виробів, спресованих з порошків, характерними є так звані
тріщини розшаровування. Вони виникають на бічних поверхнях пресування,
перпендикулярно напрямку пресуючого зусилля, і призводять до браку формовок.
Однак, насправді механізм їх виникнення набагато складніше.
Безпосередньої, найближчій причиною виникнення тріщин розшаровування є
пружне розширення формування. Розширення є деформацією, а всяка
деформація відбувається в результаті дії якихось сил. Природа цих сил,
виникають у скомпактірованноі виробі і викликають його пружне розширення,
пояснюється окремими авторами по-різному. Найчастіше їх виникнення
пояснюють пружним розширенням запресованого повітря (перший фактор) і пружним
стисненням самої форми (другий фактор), в якій ущільнюється виріб. Але, крім
того, в дійсності окремі ділянки ущільнюваного вироби при одному і тому
ж коефіцієнті стиснення і при одному і тому ж загальному тиску компактування отримують
неоднакове ущільнення і намагаються зміститися у відношенні один одного. В силу
цього у виробі виникає "баричний рельєф" (третій фактор), відповідний
різним тискам і зсувів, які випробовували окремі ділянки виробу під
час його пресування. Напруження цих зміщень і є зародками тріщин
розшаровування.
Вплив баричного рельєфу на утворення тріщин розшаровування не виключає
участі в їх освіту і запресованого повітря, що було підтверджено
спеціальними дослідженнями, якими було встановлено, що не все повітря,
міститься в порошку, витісняється з нього при пресуванні. Переважна
більшість воздухопроводящих каналів в периферійній частині формовок закривається
при порівняно низьких тисках 0,5 МПа при вологості порошку 10% і 5 МПа
при вологості 8 – 10%. Коефіцієнт запресовування повітря в порошку частка
запресованого повітря в загальному його обсязі в порошку при пресуванні
тонкозернистих глинистих порошків знаходиться в межах 0,37 – 0,715. зростання
швидкості пресування (перехід від гідравлічних пресів до важільним) збільшує
на 20 – 50%.
Збільшення вологості порошку підвищує внутрішній тиск запресованого в ньому
повітря. Тиск його всередині пресування (при W = 10 – 12%) досягає майже 10 МПа, в
той час як при вологості порошку 6 – 8% тиск запресованого повітря не
перевищує 2 МПа. Високий тиск повітря у вологих порошках призводить до
виникненню в пресування розтягуючих напруг і як наслідок до
утворення тріщин розшаровування.
При повільному пресуванні запресованих повітря більш рівномірно розподіляється
в пресованному порошку, в результаті чого запобігається утворення окремих,
більш небезпечних зон, в яких зусилля перевищують міцність пресування в момент кінця
її стиснення.
Четвертим фактором, що обумовлює пружне розширення пресування, є
пружні деформації плоских глинистих часток. Тому схильність до розшарування
прессовок зростає зі збільшенням вмісту глинистої частини в порошку.
Методика
проведення досліджень
Так як
процесом компактування необхідно керувати, то необхідно провести ряд
досліджень, які повною мірою допоможуть розкрити властивості тонкодисперсного
матеріалу.
Завданням
дослідження є визначення ряду фізико-механічних характеристик
тонкодисперсних матеріалів. Дослідження включали в себе: ситової аналіз,
визначення структурних характеристик, компресійні і міцнісні випробування.
Компресійні випробування дозволяють отримати залежність між тиском
ущільнення і щільністю матеріалу, а також енергоємність процесу, що в
комплексі з міцності випробуваннями дозволяє оцінити придатність матеріалу
для компактування.
У процесі дослідження використовують наступні величини:
Р – поточний
тмск випробування, МПа;
Рмах – максимальний тиск випробування, МПа;
ρ – щільність формовки, кг/м3;
ρ(р) – щільність формовки при відповідному тиску;
ρк – щільність формовки після компактування.
Кур – коефіцієнт пружного розширення;Кур = ρ(р)/
ρк.
а – питома енергоємність компактірованія до заданих параметрів.
Основний зміст компресійних випробування полягає у визначенні параметрів компресійної кривої зв'язує тиск компактірованія і
отримувану щільність у вигляді:

где ρ1 – щільність при одиничному ущільненні, кг/м3;
n – показник ступеня.
Компресійні випробування проводять на приладі, схема якого надана на рисунку 5. Конструктивні особливості приладу дозволили
підвищити точність вимірювання щільності зразка за рахунок використання індикатора
силовимірювача 7 в якості індикатора переміщення.
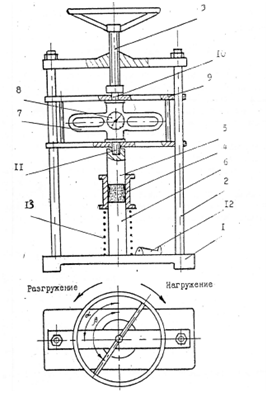
1 – підстава, 2 – стійка, 3 – гвинтове навантажує пристрій, 4 –
матрца, 5 – верхній поршень, 6 – нижній поршень, 7 – силовимірювача, 8
– індикатор, 9 – платформа, 10,
11 – штоки, 12
– фіксатор, 13 – пружина
Рисунок 4 – Прилад для компресійних випробувань
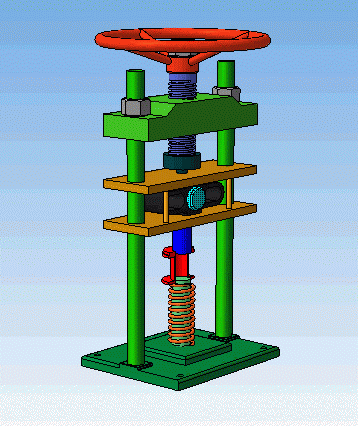
Рисунок 5 – Робота приладу для компресійних випробувань
(анімація: 8
кадрів, затримка 50 мс, 301 кілобайт)
Випробування здійснюють наступним чином. В підпружинену
матрицю 4 засипають досліджуваний матеріал і за допомогою гвинтового навантажуючого
пристрою незначно ущільнюють його, це положення приймається за початкове.
Потім послідовно повертаючи маховик навантажує пристрою 3 на 90
градусів і фіксуючи надання індикатора
8 створюють необхідний тиск ущільнення, після цього
розвантажують формування, фіксуючи пружне розширення, компактіруют продукт
вимірюють його розміри і масу [17].
Первинними даними є:
m –
маса формовки, г;
D –
діаметр формовки, мм;
H – висота формовки, мм;
N 1,2 – показники
індикатора силовимірювача.
Розрахунковими
величинами є:
– щільність формовки після компактірованія.
Ку.р. – коефіцієнт пружного розширення, визначається за показаннями індикатора 8.
Міцнісні випробування формовок є логічним завершенням компресійних і
здійснюються на тому ж приладі шляхом застосування відповідного навантаження.
Таким чином підвищується точність експерименту і його достовірність, оскільки
відомі умови навантаження. Залежно від завдання процесу руйнування може
передувати сушка та інші процеси.
Міцнісні
випробування відповідають рекомендаціям ГОСТу 24941-81 і виконані з урахуванням
масштабного фактора.
Первинними даними досвіду є:
D – діаметр формовки, мм;
H – діаметр формовки, мм;
N – величина руйнівного
навантаження, Н;
За цим величинам розраховують:
– міцність формовки на розколювання, МПа;
– міцність формовки на стиск, МПа.
Характеристики міцності матеріалів залежать від складу і змісту сполучного, тиску ущільнення і режиму сушки [17,19].
Висновки
На завершення даної роботи треба сказати, що компактування є перспективним та ефективним способом утилізації чи переробки тонкодисперсних промислових відходів. А дослідження процесів, що відбуваються всередині формовки при ущільненні матеріалу дозволить більшою мірою управляти процесом: підвищити продуктивність, знизити енергоємність і поліпшити екологічну ситуацію на підприємстві в цілому.
Важливо! При написанні даного реферату магістерська робота ще не завершена. Термін завершення: грудень 2012 необхідні матеріали по темі і повний текст роботи можуть бути отримані у автора або його керівника після зазначеної дати.
Перечень ссылок
1. Байсголов
В.Г., Галкин П.И.Оборудование предприятий силикатной промышленности, Москва,
Чёрная металургия, 1982.-752с.
2. Соколовский В.В. Статика сыпучей среды, – Москва, Физматгиз,
1960г., 243с.
3. Безухов Н.И., Основы теории упругости, пластичности и ползучести, Москва, Высшая
школа, 1968г., 434с.
4. Ред Ишлинский А.Ю. и др., Определяющие законы механики грунтов.– сб. статей «Новое в зарубежной технике», сер. Механика, вып 2, Москва,
1975г.,230с.
5. Клейн Г.К., Строительная механика сыпучих тел, – Москва, «Стройиздат», 1977г,
256 с.
6. Prager W., On ideal loking materials.- j.''Trans.Sok.Rheol,''1975, 5,6,p.169-175
7. Меерсон и др., Экспериментальное исследование процесса прессования порошковых материалов.–в ж.
«Порошковая металлургия», 1970 г., №1, с 21-29
8. Жданович Г.М. , Теория прессования металлических порошков.– Москва, «Металлургиздат», 1965г., 262с.
9. Генералов М.Б., Определение поля напряжений при одностороннем прессовании цилиндричеких брикетов из металлических порошков.–
в сб. трудов Московского института химического машиностроения , – Москва, 1975г., вып. 65, с 19-27
10. Сарматов М.И. , Элементы теории и расчёта прессов для брикетирования углей.,
Москва, «Углетехиздат», 1954г, 239с.
11. Файнбурд В.М. ,Контактная задача теории упругости., – Москва, «Наука», 1975г., 57с
12. СедовЛ.И. , О перспективных направлениях и задачах в механике сплошных сред.
– в.ж. «Прикладная математика и механика», 1976г.,т 40, вып 6, с. 963-980
13. Голушкевич С.С., Плоская задача теории предельного равновесия сыпучей среды.
– Москва, «Гостехиздат», 1948г., 148с.
14. Шашков И.П., Исследование движения грунта вверх по трубе. – в сб. «Труды Сибирского автомобильного института», вып. 55, 1976г, 121-124с
15. Крохин В.Н., Брикетирование углей, – Москва, «Недра», 1974г., 216с.
16. Карпов А.В. И др. Изучение сопротивления угольной засыпи при её продвижении в камере.– в сб.
«Теория и практика подготовки и коксования углей", вып. 5, Москва, «Металлугия», 1976г., с 15-21.
17.
Веpетельник С.П., Аннотированный отчет«Определение сдвиговых
и компрессионных характеристик шихт производства бытовых
брикетов», Донецк, Донецкий политехнический институт, 1993 г,
35с.
18.
Рассказов Н.И., исследование напряжений возникающих при прессовании
брикетов из порошковых материалов., – в сб. «Труды
XXIX научно технической конференции Московского института химического
машиностроения", Москва, 1968г., с. 77-79.
19.А.С.
№845059 СССР, МКИ G01N 3/24. Заявл. 03.08.79; Опубл. 07.07.81, Бул.№ 25
Парфенюк А.С., Веретельник С.П., Назаров В.Н. и др. Прибор для
компрессионных испытаний.