Реферат за темою випускної роботи
Зміст
- Вступ
- 1. Актуальність теми і постановка завдань
- 2. Огляд досліджень і розробок по темі
- 3. Моделювання інструменту
- 4. Визначення елементарних складових сили різання
- 5. Аналіз напружено-деформованого стану конструкції збірного свердла
- Висновки
- Перелік посилань
Вступ
З кожним роком стають все більш жорсткими вимоги до конструкційних матеріалів, з яких виготовляються відповідальні деталі й вузли, важко навантажені елементи. Одним із шляхів поліпшення властивостей металів є їх легування і відповідна термічна обробка. В результаті отримують задані експлуатаційні характеристики деталей, але це призводить до ускладнення їх обробки. Наприклад, залізничні рейки піддають об'ємної гарту, внаслідок чого обробка отворів у поруччі під кріпильні елементи можлива лише твердосплавним інструментом.
1. Актуальність теми і постановка завдань
На сьогоднішній день для лезвійной обробки отворів у поруччі застосовують збірні свердла з механічним кріпленням змінних непереточуюмих пластин (СНП). На практиці встановлена відносно невисока стійкість даного інструменту. Основною причиною втрати працездатності є вищерблення ріжучих крайок і відколи вершин. Характерні види зносу змінних непереточуюмих пластин наведені на рисунку 1.
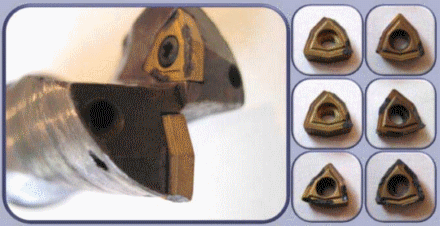
Рисунок 1. Характерний вигляд зносу змінних непереточуюмих пластин
Периферійна і центральна пластини працюють в різних умовах, тому характер зносу в них відрізняється. Для периферійної пластини характерною рисою є знос по задній поверхні і сколювання вершини пластини, яка знаходиться на максимальному діаметрі (мал. 1). Для центральної пластини, розташованої поблизу осі свердла, характерним є вищерблення ділянки ріжучої кромки, яка розташована ближче до осі свердла (мал. 1).
Причинами низької працездатності збірних твердосплавних свердел вважаються важкі умови різання, викликані особливостями процесу свердління - швидкістю різання біля осі інструменту рівною нулю, і змінною геометрією і як наслідок - змінними складовими сили різання уздовж ріжучих крайок центральної і периферійної пластин. Одним із шляхів підвищення працездатності збірних свердел є створення інструменту з раціональними конструктивними і геометричними параметрами, які забезпечують більш рівномірне завантаження ріжучих крайок і мінімізацію неврівноваженою радіальної складової сили різання, яка виникає під час свердління.
2. Огляд досліджень і розробок по темі
У [2] описана методика визначення амплітуди коливання при обробці металів різанням. Процес різання часто супроводжується коливаннями з порівняно невеликою амплітудою, відомими під назвою вібрації. Коливання, з одного боку, негативно позначаються на роботі верстата, точності і якості оброблюваної вироби, з іншого боку, можуть впливати, наприклад при вібраційної обробки.
У зв'язку з цим основними завданнями динаміки процесу різання є:
- Вивчення причин виникнення і розвитку коливань;
- Вивчення стійкості системи СПІД та дослідження ефективних методів усунення коливань;
- Визначення раціональних режимів вібраційної обробки.
На металорізальних верстатах зустрічаються різні види коливальних рухів. Разом з власними коливаннями, в процесі різання можливі вимушені коливання, що виникають при роботі многолезвийного інструменту, обробці виробів з нерівномірним припуском та інші, а також автоколивання в саме збуджуються системах. Власні коливання відбуваються в системі при зміні її стану, що визначає необхідну енергію для порушення цих коливань. Вимушені коливання виникають під дією періодичної сили, джерело якої дає енергію коливань. Автоколивання порушуються у відсутність зовнішнього періодичної дії і визначаються пристроєм самої системи, при цьому джерело енергії є невіддільною частиною системи.
Труднощі вивчення коливального руху полягає не тільки в його різноманітті і складності, але і в тому, що процесу різання властивий цілий ряд нелінійних залежностей, наприклад, нелінійна залежність сили різання від товщини шару, що зрізується, нелінійна залежність сили різання від швидкості. Для аналізу коливального руху при різанні металів необхідно скласти математичну модель системи. Вибір схеми цієї моделі, насамперед, пов'язане з визначенням числа ступенів свободи, тобто числа незалежних змінних, необхідних для повного опису процесів в системі СПІД. Реальна система металорізального верстата зазвичай має велике число ступенів свободи, кожній з яких відповідає своя власна парціальна частота. При складанні математичної моделі можна знехтувати деякими ступенями свободи, якщо ці мірою пов'язані з частотами, значно відрізняються за розміром від основних (що лімітують) частот системи. Тому кожному дослідження коливальних рухів повинно передувати визначення власних парціальних частот. Якщо немає можливості аналітичного рішення цієї задачі, проводиться експериментальне визначення парціальних частот осциллограммам затухаючих коливань.
Після вимірювання частот і визначення числа ступенів свободи встановлюються інші параметри коливальних контурів математичної моделі:
- За осциллограммам затухаючих коливань обчислюється логарифмічний декримент;
- На підставі діаграми навантаження-переміщення визначається жорсткість системи;
- З урахуванням жорсткості і власної частоти обчислюється величина наведеної маси;
- Встановлюється характеристика сили різання і при необхідності характеристика сили тертя;
- При наявності зовнішньої збуджуючлї сили визначається її амплітуда і частота.
Остаточне рішення про правильність прийнятої моделі і значень її параметрів дає порівняння результатів математичного аналізу з експериментальними даними.
Для опису вимушених коливань системи верстата складаються диференціальні рівняння. Методика написання диференціальних рівнянь вимушених коливань систем верстатів розглянута в [2]:
В процесі різання поява зовнішньої періодичної сили може бути обумовлений наступними причинами:
- Роботою многолезвийного інструменту;
- Наявністю нерівномірного припуску;
- Можливістю освіти елементної стружки.
Останнє більш значуще в області малих значень швидкості різання, коли частота освіти елементів порівнянна з власної частотою системи. Крім того, змушені коливання можуть виникнути в системі СНІД від приводу верстата, незбалансованих обертових мас і т. д. Вплив умов обробки на статичне і динамічне компоненти сили різання розглянуті в [3, стор.314-332]: Процес фрезерування характеризується приривчатістю різання і миттєво змінюється товщиною зрізу, що призводить до виникнення коливань сили різання, які у свою чергу викликають небажані вібрації в технологічній системі, високу шорсткість обробленої поверхні і поломку інструменту.
Разом з тим, неоднозначні літературні дані про склад спектру сили різання при фрезеруванні кінцевими фрезами, а саме: в одних джерелах стверджується, що динамічна складова сили різання змінюється на частоті fz проходження зубів через зону різання, а в інших, що коливання сили різання відбуваються на частоті обертання фрези f0 і частоті fz.
У зв'язку з цим виникає необхідність дослідження характеру зміни сили різання при фрезеруванні площині кінцевими фрезою і встановлення домінуючою частоти її зміни. Крім цього відома математична модель головною складовою сили різання при фрезеруванні кінцевими фрезами, однак емпірична модель динамічної складової сили різання відсутній. Проведені дослідження показали, що з-за впливу радіального биття фрези спектр сили різання зрушується від частоти fz проходження зубів через зону різання до частоти обертання шпинделя. Це може мати шкідливий вплив на процес різання, оскільки домінуючими в спектрі сили різання стають більш низькочастотні гармоніки.
Крім того, встановлено, що при наявності биття фрези різниця у потужності гармонік на оборотній і зубцовой частотах знаходиться у назад пропорційній залежності від величини хвилинної подачі. З зменшенням подачі вплив биття кінцевими фрези на зсув частот проявляється помітніше. Отже, за наявності ексцентриситету низькочастотні складові сили різання будуть надавати ще більший вплив на якість остаточної обробки.
Знаючи частотний складу спектру сили різання і характер її зміни при фрезеруванні площин кінцевими фрезою, можна перейти до встановлення закону зміни динамічної складової сили різання. В [3] наведена методика розробки емпірична модель динамічної складової сили різання.
3. Моделювання інструменту
На етапі проектування різального інструменту можливо спрогнозувати яким чином будуть впливати конструктивні та геометричні параметри на напружено-деформований стан робочої частини збірного свердла з допомогою чисельного моделювання і прикладних програм на їх основі. З метою аналізу впливу конструктивних і геометричних параметрів робочої частини збірного свердла на її напружено-деформований стан, нами була створена тривимірна геометрична модель (рис. 2) і проведена її дискретизація (рис. 3).
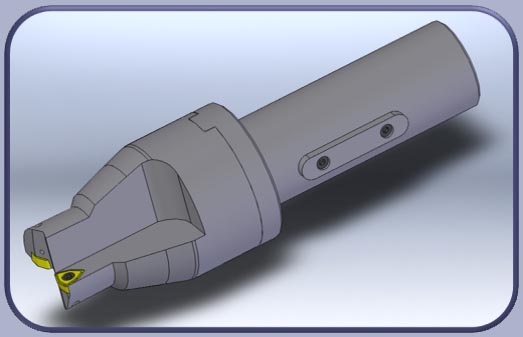
Рисунок 2. Модель збірного свердла
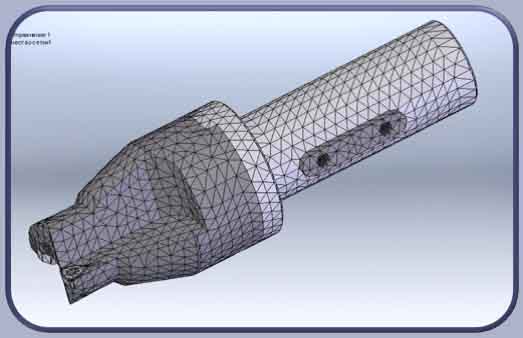
Рисунок 3. Дискретизація моделі
Моделювання проводилося умов для обробки свердлом зі стандартними конструктивними і геометричними параметрами на центральної і периферійної пластинах. Початкові умови розрахунку відповідали статичного аналізу збірної конструкції з урахуванням коефіцієнта тертя між елементами свердла і їх відносної кінематики.
Кінематичні граничні умови імітували закріплення хвостовика свердла оправці (рис. 4), а навантаження відповідала силам закріплення елементів свердла і розподілу складових сили різання уздовж ріжучих крайок пластин у відповідності з геометрією (рис. 5).
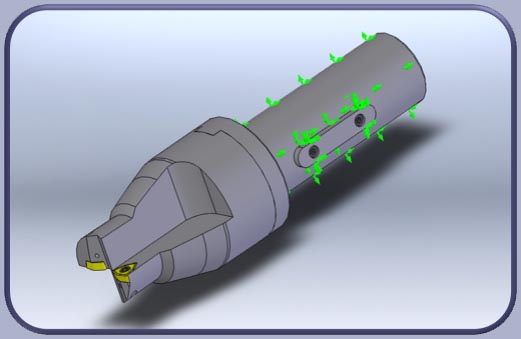
Рисунок 4. Кінематичні граничні умови моделі
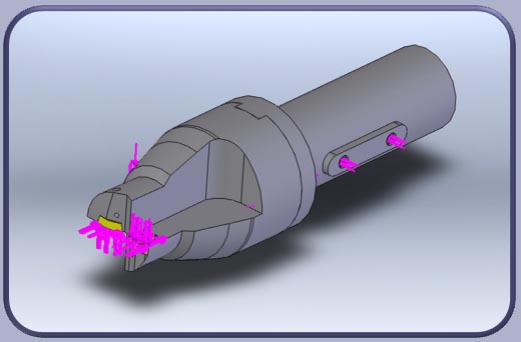
Рисунок 5. Навантаження моделі
Для цього були проаналізовані геометричні параметри свердла по ріжучих крайок і навантаження, що виникають на ріжучих крайках кожної змінної неперетачиваемой пластини в процесі різання.
4. Визначення елементарних складових сили різання
На основі наявної розрахункової схеми (рис. 6) і аналітичних досліджень [1] овизначені елементарні складові сили різання, діючі в окремих точках ріжучих крайок кінцевих інструментів, які мають такий вигляд:
- елементарна тангенціальна складова:

- елементарна осьова складова:

- елементарна радіальна складова:

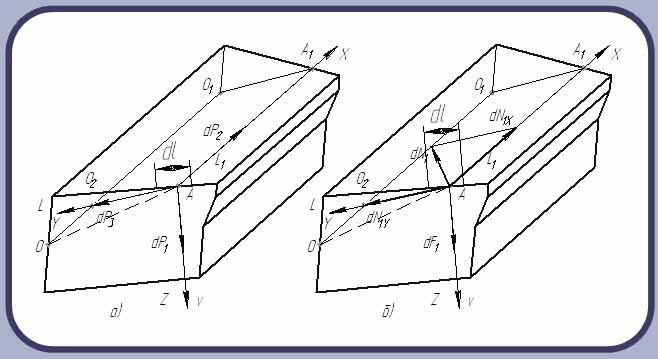
Рисунок 6. Схема сил, що діють на передній і задній (б) поверхнях зуба свердла
В результаті були отримані епюри розподілу складових сили різання, діючих уздовж головної ріжучої кромки периферійної (рис. 7) і центральної (рис. 8) пластин.
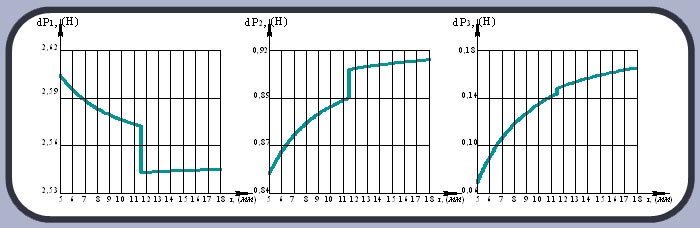
Рисунок 7. Епюри розподілу складових сили різання, діючих уздовж головної ріжучої кромки периферійної пластини
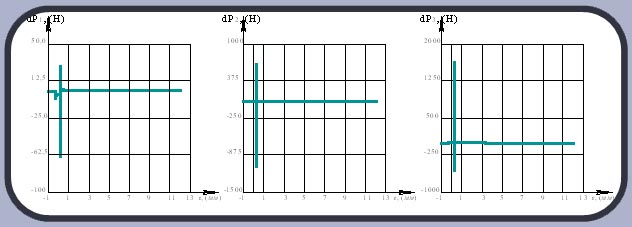
Рисунок 8. Епюри розподілу складових сили різання, діючих уздовж головної ріжучої кромки центральної пластини
5. Аналіз напружено-деформованого стану конструкції збірного свердла
В результаті розрахунку була отримана інформація про напружено-деформованому стан конструкції збірного свердла. На рисунку 9 наведено деформації конструкції та її елементів. Для більшої наочності наведена деформована форма інструменту з збільшенням деформацій в 100 разів.
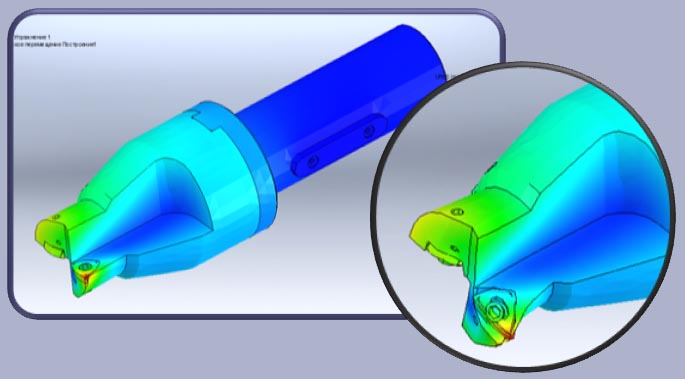
Рисунок 9. Напружено-деформований стан конструкції збірного свердла
На рисунку 10 наведені еквівалентні напруги, розраховані за критерієм Мізеса.
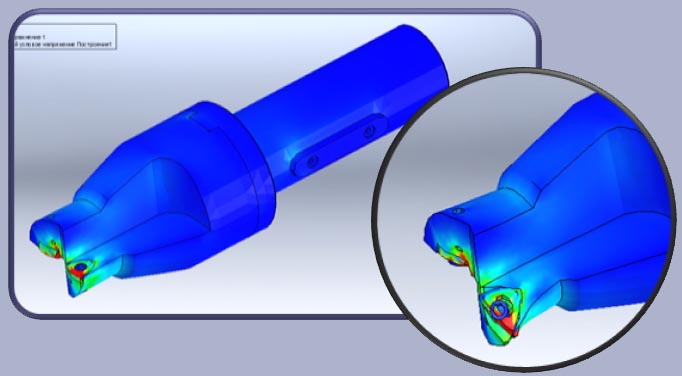
Рисунок 10. Еквівалентні напруги, розраховані за критерієм Мізеса
Висновки
Проведене моделювання показало, що розрахункове розподіл переміщень і напруг в конструкції збірного свердла відповідає дійсному розподілу навантаження. Це підтверджується тим, що місця з максимальними значеннями переміщень і напруг на моделі (рис. 9) відповідають місцям руйнування ріжучих пластин на реальній конструкції свердла (рис. 1). Таким чином, робимо висновок про можливість застосування чисельного моделювання при пошуку раціональної конструкції збірного свердла, яка забезпечить щодо рівномірне завантаження ріжучих крайок інструменту і підвищення його працездатності.
Надалі планується провести експериментальне дослідження з метою підтвердження висунутих гіпотез, з урахуванням зміни геометричних параметрів робочої частини свердла, силових і динамічних параметрів процесу.
Примітка:
При написанні даного реферату магістерська робота ще не завершена. Остаточне завершення: грудень 2012 року. Повний текст роботи та матеріали по темі можуть бути отримані у автора або його керівника після вказаної дати.
Перелік посилань
- Холмогорцев Ю. П. Оптимизация процессов обработки отверстий / Холмогорцев Ю. П. – М.: Машиностроение, 1984. – 184 с.
- Мурашкин Л. С., Мурашкин С. Л. Прикладная нелинейная механика станков /«Машиностроение», 1977. – 192с.
- Васин С. А., Маслов А. Р. Прогнозирование виброустойчивости инструмента при точении и фрезеровании / М.: Машиностроение, 2006. – 384с.
- Денисенко В. И. Управление стружкоотводом при сверлении / В. И. Денисенко// Известия высших учебных заведений. Машиностроение. – 1988. – Вып. 7. – С. 141 – 145.
- Виноградов А. А. Расчёт усадки стружки и длины контакта её с резцом / А. А. Виноградов // Сверхтвёрдые материалы. – 1990. – №2. – С.58–63.
- ГОСТ 51685-2000 Рельсы железнодорожные. Общие технические условия. – М.: Издательство стандартов, 2001. – 27 с.
- Баканов А.А., Петрушин С.И. Работоспособность сверл с СМП при сверлении железнодорожных рельсов // Современные проблемы машиностроения: Труды III Междунар. научнотехн. конф. – Томск: Изд_во ТПУ, 2006. – С. 186–189.
- Петpушин С.И., Баканов А.А., Махов А.В., Геометрический и силовой анализ сбоpных свеpл со сменными многогpанными пластинами/Технология машиностроения, Вып. 10(64), 2007. – С. 27 – 30.
- Справочник технолога машиностроителя: в 2 т. /[ред.: Косилова А. Г., Мещеряков Р.К.]. - 4-е изд., перераб. и доп. - М.:Машиностроение, 1986. Т.2 - 1985. – 496 с.
- Гринёв Ю.А. Определение статических геометрических параметров сборных сверл / Ю.А. Гринёв, Т.А. Воеводина, Е.Н. Царенко // Наукові праці Донецького національного технічного університету. Серія: Машинобудування і машинознавство. Донецьк: ДонНТУ, 2011. – Випуск 8 (190). – С. 200 – 209