Реферат по теме выпускной работы
Содержание
- Введение
- 1. Актуальность темы
- 2. Анализ технологических схем добычи золота в условиях Ганны
- 3.Погрузочно-транспортные агрегаты, используемые на подземных рудниках в условиях Ганны
- Выводы
- Список источников
Введение
Современной Гане, на чьей территории находилась страна Ашанти, повезло, что несколько веков назад добыча золота была весьма примитивной, большая часть запасов драгоценного металла осталась нетронутой. Теперь это государство является одним из лидеров по добыче золота в Африке. Интересно, что самое богатое золотое месторождение в Гане носит название Ашанти. И, как бы в подтверждение того, что оно достойно носить легендарное название, месторождение ежегодно выдает несколько десятков тонн желтого,металла. Всего каждый год из недр Ганы извлекается почти 70 тонн золота – по этому показателя она среди стран Африки занимает второе место, впереди лишь ЮАР. Бедственное положение, в котором находится наибольшая часть населения Ганы, специфично сказалось на развитии золотодобывающей отрасли страны. В Гане существует множество заброшенных или небольших месторождений, которые не выгодно разрабатывать промышленно. На эти рудники пришли старатели. Можно говорить о том, что в Гане сформировалась особая социальная прослойка,золотодобытчики. После ужесточения законов, практически пресекающих старательскую деятельность, золотодобытчики ушли в подполье, образовались так называемые группы шахтерского сопротивления, деятельность которых мало чем отличается от действий партизан. Никакие мероприятия, предпринимаемые государством и местной полицией, не смогли повлиять на снижение активности старателей В настоящее время золото добывают главным образом из руд , причем не только золотых , но и таких , в которых основными полезными ископаемыми являются другие цветные металлы , в частности медь, цинк, серебро, свинец. В этом случае рассматриваются как попутчик . Во всех промышленно развитых странах , например , широко практикуется добыча золота из медных и свинцов – цинковых руд.
Такая же картина наблюдается во многих странах , где производится добыча цветных металлов , что в полной мере соответствует принятому сейчас в мировой практике направлению на комплексное использование минерального сырья. Содержание золота в рудных цветных металлов , как правило , значительно ниже , чем непосредственно в золотых рудах , однако издержки производства на его добычу при этом могут быть несколько меньше. Необходимо отметить , что добыча золота в таком случае будет зависеть от спроса на другие цветные металлы. Так , в 80-е годы попутная добыча золота заметно сократилась в связи со снижением цен на медь.
Значительное количество золота добывается сейчас в результате разработки серебряных месторождений ; поскольку спрос на серебро велик и имеет тенденцию к дальнейшему росту , то этот источник получения драгоценного металла более надежен. Такого рода месторождения чаще всего имеют эпитермальное происхождение. При попутной добыче золота горные работы по существу остаются теми же , но процессы обогащения и металлургической переработки руд становятся значительно сложнее , так как необходимо получить уже не один , а несколько металлов.
1. Актуальность темы
Всего каждый год из недр Ганы извлекается почти 130 тонн золота – по этому показателю она среди стран Африки занимает второе место, впереди лишь ЮАР. В настоящее время золото добывают главным образом из руд, причем не только золотых, но и таких , в которых основными полезными ископаемыми являются другие цветные металлы , в частности медь, цинк, серебро, свинец.
Производительность золотодобывающих рудников значительно уступает не только железорудным и угольным шахтам, но и многим рудникам, разрабатывающим месторождения цветных металлов .Чтобы добыть 1 кг золота при его содержании в тонне руды 4-5 грамм (такое содержание характерно в настоящее время для многих месторождений, разрабатываемых в западных странах), нужно отбить, выдать на поверхность и переработать 200 – 250 тонн руды; для получения 1 тонн золота нужно разработать 200-250 тысяч тонн руды.
Разработка жильных месторождений – одна из самых трудоемких работ в горном деле. Положение осложняется еще и тем, что выемку надо производить без потерь, то есть по возможности более полно, так как ценность золотой руды очень высока. По этим причинам подземная разработка жильных месторождений золота очень трудоемка, а системы разработки менее эффективны, чем, например, при эксплуатации угольных или железорудных месторождений. Открытая разработка в горном деле считается наиболее прогрессивной, и ее удельный вес неуклонно возрастает во всех странах, однако в практике добычи золота широко применяют подземные работы, так как коэффициент вскрыши при открытой разработке тонкожильных месторождений был бы слишком велик.
В связи с вышеуказанным возникает необходимость усовершенствования существующих технологий подземной добычи золота и снижения потерь руды в целиках.
2. Анализ технологических схем добычи золота в условиях Ганны
КАМЕРНО-СТОЛБОВАЯ СИСТЕМА РАЗРАБОТКИ — система разработки твёрдых полезных ископаемых (руда, уголь и др.) камерами, отделёнными друг от друга целиками, поддерживающими кровлю. Применяется для выемки пологих и наклонных (до 40-45°) залежей полезных ископаемых при высокой устойчивости их и вмещающих пород.
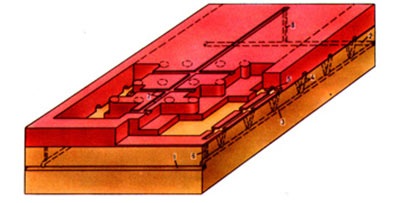
Рис. 1 - Камерно-столбовая система разработки
На рудных шахтах отрабатываемую залежь делят на панели или блоки, разделяемые между собой ленточными или изолированными целиками. Расположение камер (по простиранию, восстанию) зависит от угла падения залежи и применяемого на очистных работахоборудования. При выемке пологих рудных тел с использованием на доставке руды скреперных установок (рис. 1) подготовительно-нарезные работы включают проведение в лежачем боку основных откаточных, вентиляционных и, перпендикулярно им, панельных штреков. Последние соединяются рудоспусками с рудными панельными штреками. Проводятся также материально-ходовые и вентиляционные выработки. В зависимости от мощности рудного тела и применяемого на буровзрывных работах оборудования выемку ведут безуступным или потолкоуступным забоем (высота уступов 2,5-3,5 м). Для бурения и вентиляции используются передовые забои (1,8-2,5 м) под кровлей камер. Для сокращения многократного повторения операций бурения шпуров и уборки отбитой руды в условиях многоуступной выемки (что значительно сокращает возможности повышения нагрузки на камеру) при мощности рудной залежи свыше 10 м применяют вариант с отбойкойруды нисходящими скважинами, пробуренными из передового забоя. При использовании самоходного оборудования залежь разбивают на панели, обычно шириной 150 м.
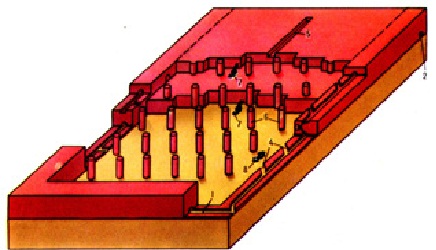
Рис. 2 - Камерно-столбовая система разработки с разбивкой на панели
После проведения основных транспортных и вентиляционных штреков проходят панельные штреки, из которых в целике образуют заезды. На залежах мощностью более 4-4,5 м панель проветривают за счёт пройденной по её центру под кровлей рудного тела вентиляционной выработки. При оформлении междукамерных целиков соблюдается ступенчатая конфигурация линии очистных забоев, способствующая лучшему проветриванию и поддержанию кровли. Самоходное оборудование главным образом мощное дизельное на пневмошинном ходу:буровые установки с двумя-тремя перфораторами, ковшовые погрузочно-доставочные машины,экскаваторы, автосамосвалы и др. Для заряжания шпуров, осмотра и оборки кровли на транспортных работах используют вспомогательное оборудование с автономным приводом. В зависимости от вида самоходного оборудования и мощности залежи выделяются следующие технологические варианты. Рудные тела мощностью менее 2,5-3 м разрабатывают с подрывкой подстилающих или налегающих пород (определяется устойчивостью кровли и выдержанностью контакта рудного тела с породами). Отбитую породу перемещают с помощью бульдозера или погрузочно-доставочных машин и располагают в отработанной зоне этой же панели. Рудные тела мощностью до 7-8 м (при использовании башенных буровых кареток — до 12 м) отрабатывают по высоте сплошным забоем. Выемку рудных тел мощностью свыше 8 м осуществляют в два слоя с опережением (на 30-40 м) верхнего слоя высотой 5-6 м. При этом заезд на почву вышележащего уступа может осуществляться по наклонному съезду. При мощности залежи свыше 16 м выемку иногда ведут с оставлением т.н. рудного моста высотой 5-7 м. При этом целесообразна опережающая выемка вышележащей части залежи. При камерно-столбовой системе разработки наклонных залежей и использовании на доставке руды скреперных установок камеры располагают по восстанию. Ёмкость скреперов 0,25-0,45 м3; бурение с помощью ручных перфораторов. При использовании на очистных работах самоходного оборудования применяют диагональный или ломаный транспортный съезд; камеры располагают по простиранию. В зависимости от угла падения и мощности рудного тела выемка производится слоями высотой 2,5-4,5 м. Оформление просечек в междукамерных целиках осуществляется в отступающем порядке. При мощности рудного тела 5-8 м (рис. 3) подготовка блоков (длина 120-200 м) заключается в проведении откаточного штрека, вентиляционного (блокового) восстающего и рудоспуска.
После проведения основных транспортных и вентиляционных штреков проходят панельные штреки, из которых в целике образуют заезды. На залежах мощностью более 4-4,5 м панель проветривают за счёт пройденной по её центру под кровлей рудного тела вентиляционной выработки. При оформлении междукамерных целиков соблюдается ступенчатая конфигурация линии очистных забоев, способствующая лучшему проветриванию и поддержанию кровли. Самоходное оборудование главным образом мощное дизельное на пневмошинном ходу:буровые установки с двумя-тремя перфораторами, ковшовые погрузочно-доставочные машины,экскаваторы, автосамосвалы и др. Для заряжания шпуров, осмотра и оборки кровли на транспортных работах используют вспомогательное оборудование с автономным приводом. В зависимости от вида самоходного оборудования и мощности залежи выделяются следующие технологические варианты. Рудные тела мощностью менее 2,5-3 м разрабатывают с подрывкой подстилающих или налегающих пород (определяется устойчивостью кровли и выдержанностью контакта рудного тела с породами). Отбитую породу перемещают с помощью бульдозера или погрузочно-доставочных машин и располагают в отработанной зоне этой же панели. Рудные тела мощностью до 7-8 м (при использовании башенных буровых кареток — до 12 м) отрабатывают по высоте сплошным забоем. Выемку рудных тел мощностью свыше 8 м осуществляют в два слоя с опережением (на 30-40 м) верхнего слоя высотой 5-6 м. При этом заезд на почву вышележащего уступа может осуществляться по наклонному съезду. При мощности залежи свыше 16 м выемку иногда ведут с оставлением т.н. рудного моста высотой 5-7 м. При этом целесообразна опережающая выемка вышележащей части залежи. При камерно-столбовой системе разработки наклонных залежей и использовании на доставке руды скреперных установок камеры располагают по восстанию. Ёмкость скреперов 0,25-0,45 м3; бурение с помощью ручных перфораторов. При использовании на очистных работах самоходного оборудования применяют диагональный или ломаный транспортный съезд; камеры располагают по простиранию. В зависимости от угла падения и мощности рудного тела выемка производится слоями высотой 2,5-4,5 м. Оформление просечек в междукамерных целиках осуществляется в отступающем порядке. При мощности рудного тела 5-8 м (рис. 3) подготовка блоков (длина 120-200 м) заключается в проведении откаточного штрека, вентиляционного (блокового) восстающего и рудоспуска.
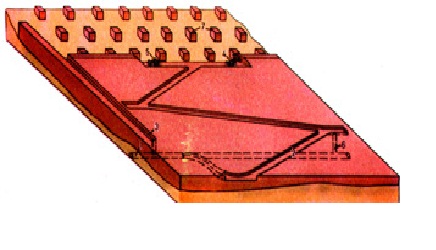
Рис. 3 -Камерно-столбовая система разработки с разбивкой на блоки
Нарезают блоки транспортными диагонально-расположенными (или ломаными) наклонными съездами. По мере очистной выемки, осуществляемой с применением самоходных автономных буровых установок и погрузочно-доставочных машин, оформляют междукамерные целики. При мощности залежи более 8 м её разработка ведётся вариантом "спаренные камеры" (рис. 4). При этом вынимают соседние камеры параллельно в пределах слоя, что обеспечивает более эффективное использование самоходного оборудования. Подготовка и нарезка блока заключается в проведении полевого и рудного откаточных штреков, полевого откаточного заезда, аккумулирующего и вентиляционного восстающего, рудоспуска. Междукамерные целики располагают по падению залежи.
В зависимости от мощности залежи, угла падения, применяемого оборудования суточная производительность выемочной единицы изменяется от 200 до 1000 т. Сменная производительность труда забойного рабочего 40-200 т, а рабочего по системе 30-120 т. Удельный объём подготовительно-нарезных работ при эксплуатации наклонных месторождений составляет 4-6, пологих — 2-4 м на 1000 т запасов руды.Разубоживание при очистной выемке обычно не превышает 3-5%. К достоинствам технологических схем камерно-столбовой системы разработки относятся: высокая производительность забоев и труда рабочих; широкий фронт горных работ с большим количеством забоев; возможность полной механизации очистной выемки с использованием мощного самоходного оборудования; относительно низкая себестоимость добычи руды. Недостатки: высокие потери руды (в рудных месторождениях до 40%, в соляных — до 60%); сложность тщательного осмотра кровли забоев и их надлежащего проветривания при широком развитии очистных работ. Развитие технологических схем идёт по пути комплексной механизации работ с помощью самоходных дизельных машин, гидравлических перфораторов, снижения потерь руды в целиках, изыскания дешёвых методов возведения искусственных опор с полной механизацией работ.
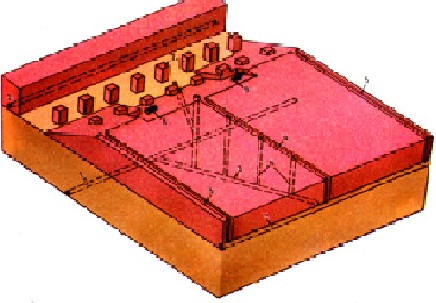
Рис. 4 – Система разработки "спаренными камерами"
На золотаных шахтах камерно-столбовая система разработки представляет собой двухстадийный процесс выемки полезных ископаемых при проведении по пласту полезных ископаемых узких протяжённых камер от транспортного штрека к вентиляционному и частичном извлечении междукамерных целиков короткими заходками (с оставлением между ними узких целиков) в обратном направлении
(рис. 5).3. Погрузочно-транспортные агрегаты, используемые на подземных рудниках в условиях Ганны
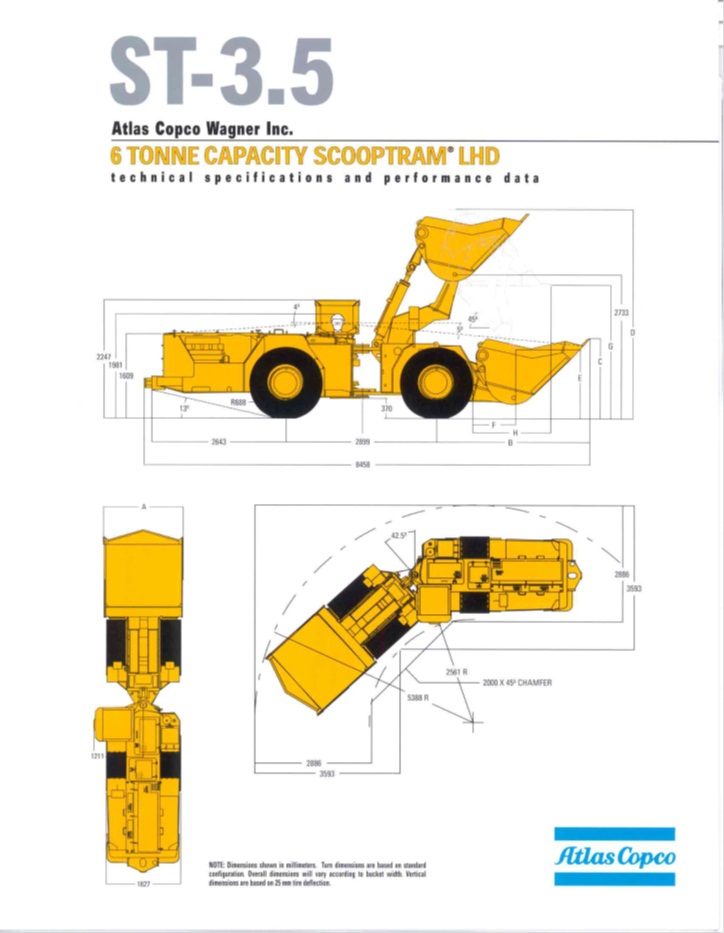
Рис. 5 - Погрузочно-транспортные агрегаты, используемые на подземных рудниках в условиях Ганны
В очистных выработках давление горных пород воспринимается не призабойной крепью, а массивом пласта и регулярно оставляемыми целиками золота. В результате этого исключается необходимость в применении специальной крепи для управления горным давлением. Кровлю в камерах закрепляют, как правило, анкерами, в заходках при извлечении целиков — не крепят. В Гане камерно-столбовые системы разработки применялась в ограниченном объёме на пологих мощных (до 7-8 м) и средней мощности пластах при буровзрывной отбойке, ручной или механизированной погрузке золота, с использованием стоечной крепи. Длина камер 30-50 м, ширина от 4 до 6 м, ширина частично извлекаемых целиков 4-5 м. Потери угля 30-45%. Производительность труда рабочих по участку не превышала 10 т/человек в смену.
Камерно-столбовая система разработки получила распространение в США (до 30% подземной добычи золота), Канаде и Австралии в основном на пологих тонких и средней мощности пластах. Выемку золота ведут комплексами самоходного оборудования. При буровзрывной отбойке угля в состав комплекса входит погрузочная машина с манипуляторами для бурения шпуров и установки анкерной крепи. Очистные забои проветриваются вентиляторами частичного проветривания. При выемке на пластах с высокой пылеобразующей способностью комбайны оборудуют пылеотсосами. При комплексной механизации горных работ длина камер 100-150 м, ширина до 5-6 м; ширина междукамерных целиков до 15-18 м. Выемочные участки разделяют неизвлекаемыми барьерными целиками. В благоприятных условиях камерно-столбовая система разработки обеспечивает интенсивное извлечение запасов при высоких технико-экономических показателях: нагрузка на очистной забой до 1500-2000 т в сутки, производительность труда рабочего по участку до 35-60 т/человек в смену. Потери угля в недрах 20-35% в зависимости от мощности пласта, устойчивости пород кровли и глубины разработки. Значительные потери полезных ископаемых и относительно сложный режим проветривания очистных забоев делают нецелесообразным применение камерно-столбовой системы разработки на пластах самовозгорающегося золота, в газообильных шахтах и на глубине свыше 500-600 м.
ОБРУШЕНИЕ КРОВЛИ – сдвижение горных пород, покрывающих пласт полезного ископаемого или вмещающих рудное тело, сопровождающееся их вывалом в подземную горную выработку. Происходит самопроизвольно или вызывается искусственно. Проявляется в отделении от массива блоков, глыб и кусков, а при произвольном обрушении кровли большой подработанной породной толщи (осадка кровли) — динамическими нагрузками на выработки и воздушными ударами в них. Вредные последствия обрушения кровли предотвращают или снижают путём установки крепи в выработках, управления состоянием массива полезных ископаемых и горных пород. Намеренное и планомерное обрушение кровли производится периодическим удалением или передвижкой крепи в выработанном пространстве. При прочных породах кровель, склонных к зависанию, во избежание проявления сильных вторичных осадок, снижения концентрации напряжений в прикраевой части разрабатываемого угольного пласта также прибегают к принудительному обрушению кровли взрывным способом или другим дополнительным мероприятиям: передовому торпедированию или гидрообработке пород основной кровли, предварительной подработке и др. Цель такого обрушения кровли — ослабить действие горного давления. В этом случае обрушение кровли понимается как управление горным давлением (кровлей). Параметры намеренного обрушения кровли (шаг посадки непосредственной кровли, осуществляемой путём удаления или передвижения крепи, и шаг посадки основной кровли) определяются свойствами пород, глубиной, горнотехническими и технологическими условиями разработки.
В зависимости от типа пород, мощности пласта, угла напластования и других факторов принимаются способы управления горным давлением посредством обрушения кровли и регулирования его совокупностью других мероприятий. Способность кровли к обрушению при разработке угольных месторождений служит основой различных классификаций кровель по обрушаемости (например, классификация кровель ВУГИ для пологих пластов Донецкого бассейна). В рудных шахтах иногда применяют специальные системы разработки, в основу технологии добычи которых положен принцип обрушения руд и вмещающих пород. Закономерности обрушения кровли при подземной разработке изучают с целью обоснования систем разработки, совершенствования методов расчёта крепи, правил охраны выработок и подземных сооружений.
5. Погрузочно-транспортные агрегаты, используемые на подземных рудниках в условиях Ганны Погрузочно-транспортный агрегат совмещает операции погрузки и транспортирования полезного ископаемого или породы к пункту разгрузки. П.-т. а. применяют на подземных рудниках при проведении горных выработок и транспортировании руд из очистных забоев, при строительстве подземных сооружений, а также на открытых горных и строительных земляных работах. По типу аккумулирующей ёмкости различают П.-т. а. с грузонесущими ковшом или кузовом. П.-т. а. с грузонесущим кузовом имеет механизм зачерпывания, ходовую часть, аккумулирующую ёмкость (кузов), приводные двигатели, передаточные механизмы и органы управления. П.-т. а. с грузонесущим ковшом транспортируют горную массу в приподнятом ковше до места назначения, но могут разгружать её и в самосвалы. Большинство П.-т. а. имеет пневмоколёсный ход с шинами повышенной надёжности для тяжёлых условий подземных работ; оборудуются пневматическими, электрическими и дизельными приводами с газоочистительной аппаратурой.
Разработано много моделей машин с грузонесущим ковшом (рис., 1) грузоподъёмностью 2, 3, 5, 8 и 12 т (ёмкость ковша от 1 до 6 м3) и 5 моделей машин с грузонесущим кузовом (рис., 2) грузоподъёмностью 2,5; 4; 6; 10; 16 т (ёмкость кузова от 2 до 6 м3). П.-т. а. с грузонесущим ковшом выпускают за рубежом фирма «Вагнер» (США) — 10 моделей типа «ST» с ковшами ёмкостью от 0,76 до 6,12 м3; фирма «ГХХ Штеркраде» (ФРГ) — 14 моделей типа «G-ST» с ёмкостью ковша от 0,76 до 8,5 м3; фирма «Эймко» (США) — 5 моделей типа «LHD» и др. П.-т. а. с грузонесущим кузовом изготовляют: фирма «Атлас-Копко» (Швеция) — 6 моделей и фирма «Джой» (США) — 3 модели с кузовами ёмкостью от 0,75 до 5 м3и др. На П.-т. а. внедряются автономные приводы, дистанционное управление, максимально унифицируются узлы.
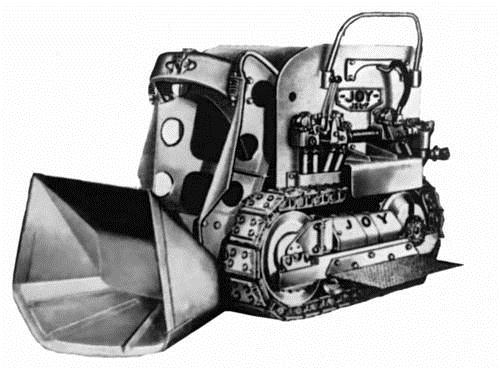
Рис.6 -Погрузочные машины. Ковшовая с прямой погрузкой
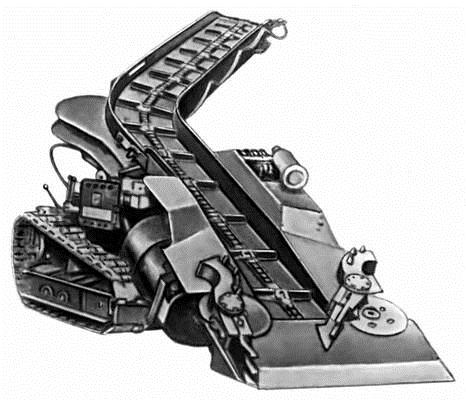
Рис. 7 -Погрузочные машины. Машина с парными нагребающими лапами.
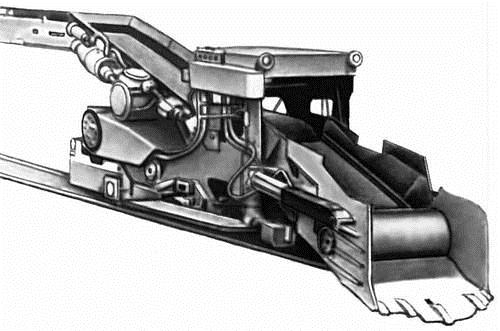
Рис. 8 - Погрузочные машины. Ковшовая со ступенчатой погрузкой.
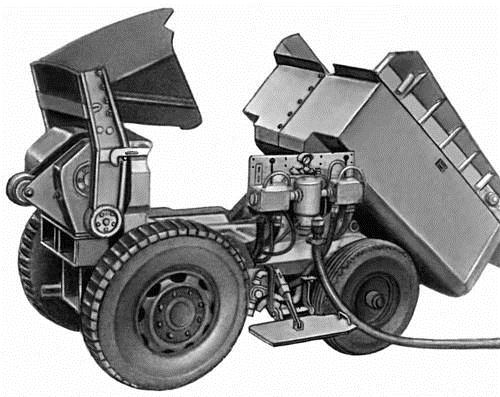
Рис.9-Погрузочные машины. Ковшовая с боковой разгрузкой
При нижнем захвате материал зачерпывается ковшом, который при опрокидывании назад разгружается в транспортные средства (машины с прямой погрузкой), высыпается на передаточный конвейер (машины со ступенчатой погрузкой), разгружается опрокидыванием вперёд или в сторону. Боковой захват осуществляется погрузочным органом, представляющим собой наклонную приёмную платформу с парными нагребающими рычагами-лапами или с двумя барами и цепями с консольными скребками; верхний захват — гребком, смонтированным на рукояти, который опускается на горную массу и нагребает её на передаточный конвейер.
П. м. имеют колёсно-рельсовый, гусеничный и пневмошинный ход; пневматический, электрический и электрогидравлический или автономный дизельный привод, снабженный газоочистительной аппаратурой. Конструкции некоторых П. м. предусматривают возможность установки на них съёмного оборудования (манипуляторов с перфораторами для бурения шпуров, малогабаритных лебёдок для такелажных работ и др.).
При добычных работах П. м. используются в комплексе с самоходным забойным оборудованием на пневмоколёсном ходу. В забойный комплекс, кроме П. м., входят буровые каретки, вагоны и самосвалы, бульдозеры, зарядчики шпуров и вспомогательные машины (для установки анкерной крепи, оборки кровли, подвоза оборудования, материалов и людей). Характеристики некоторых моделей П. м., изготавливаемых в СССР, приведены в табл.
Зарубежные фирмы «Эймко» (США), «Атлас-Копко» (Швеция), «Зальцгиттер» (ФРГ) и др. изготавливают П. м. с ковшами ёмкостью от 0,1 до 1,15 м3, массой от 1,8 до 25 т с суммарной мощностью двигателей 10—120 квт, производительностью от 0,3 до 6 м3/мин. Фирмой «Джой» (США) выпускаются машины с парными нагребающими лапами на гусеничном ходу, которые применяют в угольных шахтах и рудниках.
Существуют и другие технологические решения по извлечению золота из растворов, однако, они требуют специальной аппаратуры, могут быть осуществлены только в заводских условиях и поэтому не могут быть использованы при геотехнологической добыче золота.
Погрузочно-транспортный агрегат совмещает операции погрузки и транспортирования полезного ископаемого или породы к пункту разгрузки. П.-т. а. применяют на подземных рудниках при проведении горных выработок и транспортировании руд из очистных забоев, при строительстве подземных сооружений, а также на открытых горных и строительных земляных работах. По типу аккумулирующей ёмкости различают П.-т. а. с грузонесущими ковшом или кузовом. П.-т. а. с грузонесущим кузовом имеет механизм зачерпывания, ходовую часть, аккумулирующую ёмкость (кузов), приводные двигатели, передаточные механизмы и органы управления. П.-т. а. с грузонесущим ковшом транспортируют горную массу в приподнятом ковше до места назначения, но могут разгружать её и в самосвалы. Большинство П.-т. а. имеет пневмоколёсный ход с шинами повышенной надёжности для тяжёлых условий подземных работ; оборудуются пневматическими, электрическими и дизельными приводами с газоочистительной аппаратурой.
В СССР разработано (1974) 5 моделей машин с грузонесущим ковшом (рис., 1) грузоподъёмностью 2, 3, 5, 8 и 12 т (ёмкость ковша от 1 до 6 м3) и 5 моделей машин с грузонесущим кузовом (рис., 2) грузоподъёмностью 2,5; 4; 6; 10; 16 т (ёмкость кузова от 2 до 6 м3).
П.-т. а. с грузонесущим ковшом выпускают (1974) за рубежом фирма «Вагнер» (США) — 10 моделей типа «ST» с ковшами ёмкостью от 0,76 до 6,12 м3; фирма «ГХХ Штеркраде» (ФРГ) — 14 моделей типа «G-ST» с ёмкостью ковша от 0,76 до 8,5 м3; фирма «Эймко» (США) — 5 моделей типа «LHD» и др. П.-т. а. с грузонесущим кузовом изготовляют: фирма «Атлас-Копко» (Швеция) — 6 моделей и фирма «Джой» (США) — 3 модели с кузовами ёмкостью от 0,75 до 5 м3и др.
На П.-т. а. внедряются автономные приводы, дистанционное управление, максимально унифицируются узлы.
Буропогрузочные машины используються для бурения шпуров под закладку взрывчатого вещества и дальнейшей погрузки отделенной горной массы на следуещее звенл производственной цепи. В Гане исполььзуються буропогрухзочные машины производителей различных стран, аналогами которых можно назвать машину украинского производства – БПР.
4. Выводы и направление дальнейших исследований.
1) В Ганне разработка золотоносных месторождений ведется преимущественно подземным способом, который является весьма трудоемким и усложняется потребностью в полном извлечении рудных залежей.
2) Основной применяемой схемой разработки является камерно-столбовая. В зависимости от применяемых условий различают: камерно-столбовую систему разработки с разбивкой на блоки, на панели, систему разработки "спаренными камерами".
3) Основным недостатком существующих технологических схем являются большие потери руды, оставляемой в целиках.
4) Перспективным направлением развития технологии добычи золота является создание альтернатив целикам в виде искусственных опор и механизация процесса добычи.
5) Направлением дальнейшей работы является разработка средств механизации процесса добычи руды и совершенствование технологических схем.
Список источников
- Минеев Г.Г. Биометаллургия золота. – М.: Металлургия, 1989.
- Черняк А.С., Овчинникова О.В. Вторичные ионообменные явления в процессах выщелачивания золота и серебра // Гидрометаллургия золота. – М.: Наука, 1980.
- Байконуров О. А., Филимонов А. Т., Комплексная механизация очистных работ при подземной разработке рудных месторождений, А.—А., 1973;
- Кальницкий Я. Б., Филимонов А. Т., Самоходное погрузочное и доставочное оборудование на подземных рудниках, М., 1974.
- www.mining-enc.ru