Abstract
Contents
- Introduction
- 1. Theme urgency
- 2. Mining methods of Ghana
- 3. Cargo transport units are also used in underground mines in Ghana
- Conclusion
- References
Introduction
Modern Ghana, a country whose territory was Ashanti, was lucky that a few centuries ago, gold mining was very primitive, much of the precious metal stocks remained unchanged. Now this state is one of the leading gold mining in Africa. Interestingly, the richest gold mine in Ghana is called Ashanti Gold Fields . And, as if to confirm that it is worthy to wear the legendary name, mine annually produces dozens of tons of yellow metal. Total each year is extracted from the bowels of Ghana for nearly 70 tons of gold - putting it among the countries of Africa in second place, just ahead of South Africa. The plight in which the largest portion of the population of Ghana, specifically affected the development of the country's gold mining industry. In Ghana there are many abandoned or smaller fields that are not profitable to develop industrially. These mines came prospectors. You can talk about that in Ghana, has formed a special social stratum, gold miners. After tightening the laws, virtually precluding prospecting activities, miners went underground, formed the so-called resistance of the miners, whose activities are not much different from the actions of the guerrillas. No actions taken by state and local police were not able to influence the decrease in activity of miners now gold is extracted mainly from the ore, not only gold, but also those in which the main mineral resources are the other non-ferrous metals, particularly copper, zinc silver and lead. In this case, are treated as companion. In all industrialized countries, for example, is widely practiced by gold mining of copper and lead - zinc ores.
The same pattern is observed in many countries, where non-ferrous metals are extracted, which fully complies with the international practice now in the direction of the comprehensive utilization of mineral resources. The gold content in the ore-ferrous metals, are generally much lower than directly to the gold ores, but the production costs of its production at the same time may be somewhat less. It should be noted that gold mining in this case will depend on the demand for other non-ferrous metals. Thus, in the 80s incidental gold production decreased markedly due to lower copper prices.
A significant amount of gold mined today by the development of silver deposits, as the demand for money is great and has a tendency to further growth, the source of this precious metal is more reliable. This type of field usually have an epithermal origin. When passing the extraction of gold mining is essentially remain the same, but the processes of enrichment and metallurgical processing of ores are much more complicated, since it is necessary to obtain not one but several metals.
1. Relevance of the topic
The total amount of gold extracted each year from the depths of Ghana is nearly 130 tons of gold - putting it among the countries of Africa in second place, just ahead of South Africa. Currently, gold is mined mainly from ores, not only gold, but also those in which the main mineral resources are the other non-ferrous metals, particularly copper, zinc, silver and lead. The performance is considerably inferior to gold mines, not only iron ore and coal mines, but many mines that develop deposits of nonferrous metals. To obtain 1 kg of gold in its ore content in a ton of 4.5 grams (the content is characterized at present for many fields developed in the Western countries), it is necessary to repel, to give to the surface and processed 200 - 250 tons of ore to produce 1 ton of gold needed to develop 200-250 thousand tons of ore.
Master's work is dedicated to the actual scientific task of development a unified approach to the synthesis of Moore FSM, which is directing on hardware amount reduction in resultant device and is including algorithmic, combinatory and circuitry optimizing techniques. FPGAs by Xilinx, which combine functionality, programmability and availability to consumers, are used as the target basis. CAD Xilinx ISE, Verilog HDL and Java SE are applied as tools of the research.
2. Mining methods of Ghana
Development of vein deposits - one of the most labor-intensive work in mining. The situation is further complicated by the fact that the seizure must be carried out without loss, it is possible to more fully, as the value of gold ore is very high. For these reasons, the development of an underground vein gold deposits are very labor intensive, and system design are less effective than, for example, the operation of coal or iron ore deposits. Open development in the mining industry is considered the most progressive, and its share has been steadily increasing in all countries, but in the practice of gold mining is widely used underground work, as the stripping ratio for the development of fine wire open fields would be too great.
In regard to the above there is a need to improve existing technologies of underground mining of gold and reduce the loss of ore in the pillars.
Main tasks of the research:
- Analysis methods of minimization amount of states in completely and incompletely specified Moore FSM.
- Estimation ways of hardware amount reduction with the help of encoding states of Moore FSM.
- Search and detection characteristics of existing construction methods of logic circuits of Moore FSM and estimation possibilities of their use on FPGA.
- Association of functionally different optimization directions of Moore FSM hardware amount into the unified approach to synthesis and formation recommendations for it's use.
- Design of alternative variants of basic stages of unified Moore FSM synthesis process and estimate of it's efficiency.
Research object: Moore FSM synthesis.
Research subject: association of hardware amount reduction methods at Moore FSM implementation on FPGA.
Room-and-pillar system - a system of development of solid minerals (ore, coal, etc.) chambers separated from each other as a whole, support the roof. It is used for excavation of shallow and inclined (up to 40-45 °) of mineral deposits with high stability and their host rocks.
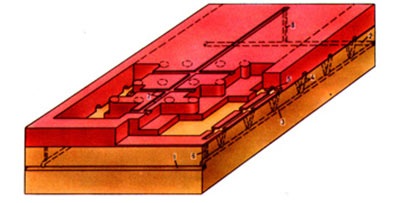
Fig. 1 - Chamber-and-pillar mining method
In ore mines are working deposit is divided into panels, or blocks, separated by tape or isolated entirely. Location of cameras (along strike, uprising) depends on the angle of incidence of the deposit and applicable to the treatment rabotahoborudovaniya. When excavation of shallow ore bodies with the delivery of ore to the scraper units (Fig. 1) set-threaded operation include conducting in the footwall of the main haulage, ventilation, and perpendicular to them, the panel drifts. Last connected with ore ore passes paneled drifts. There are also logistical and air-port output. Depending on the capacity of the ore body and used for drilling and blasting equipment are hollow or bezustupnym potolkoustupnym slaughter (height ledges 2.5-3.5 m). For drilling and ventilation system uses advanced rock faces (1.8-2.5 m) under the roof cameras. To reduce the repetitive operations of drilling holes and cleaning a broken ore in mnogoustupnoy recess (which greatly reduces the possibility of increasing the load on the camera) with the power of the ore deposits of more than 10 meters from the version used otboykoyrudy downstream wells drilled from the forward face. When using self-propelled equipment deposit is divided into panels, typically 150 m wide.
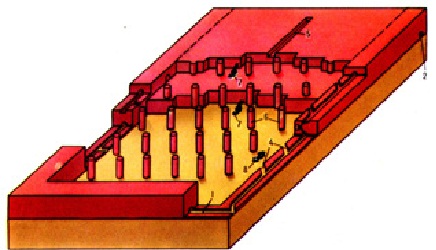
Fig. 2 - Chamber-and-pillar mining method with a breakdown of the panel
Following a major transport and ventilation are the panel drifts drifts, of which form a pillar races. On deposits capacity of more than 4-4.5 m from the panel airs traversed by its center under the roof of the ore body ventilatory output. When making a chamber between the pillars observed step configuration of the line production faces, promotes better aeration and maintenance of the roof. The self-propelled machinery primarily for heavy-duty diesel pneumatic course: drilling rigs with two or three punches, container loading and delivering cars, excavators, dump trucks, etc. for loading boreholes, inspection and ruffles on the roof of vehicles use auxiliary equipment works with an independent drive. Depending on the type of self-propelled equipment and power are the following deposits of technological options. Ore bodies of less than 2.5-3 m developing with overlapping or underlying podryvkoy species (determined by the stability of the roof and consistency of contact with the rocks of the ore body). Muck is moved with a bulldozer or Scooptrams and dispose of waste in the area of ??the same panel. Ore bodies of up to 7-8 m (when using the drill tower carriages - up to 12 m) in height and spend a continuous slaughter. The removal of the ore bodies with capacity of more than 8 meters is carried out in two layers in advance (30-40 m) of the upper layer 5-6 m tall This check on the soil overlying the bench can be inclined by Congress. For deposits of more than 16 power meters recess sometimes lead to the abandonment of the so-called ore bridge height 5-7 meters when it is appropriate anticipatory seizure of the overlying deposits. In room-and-pillar system design and use of sloping deposits of ore delivered to the scraper camera settings have to revolt. Capacity scrapers 0,25-0,45 m3 drilling with hand drills. When used at the treatment works of self-propelled equipment used or broken diagonal Transport Congress, have the camera along the strike. Depending on the angle and power of the ore body is cut layers of 2.5-4.5 m in height in the Making prosechek chamber between the pillars is retreating in order. When the power of the ore body 5-8 m (Fig. 3) training blocks (length 120-200 m) is to carry out haulage drift, ventilation (block) rebels and ore passes.
Following a major transport and ventilation are the panel drifts drifts, of which form a pillar races. On deposits capacity of more than 4-4.5 m from the panel airs traversed by its center under the roof of the ore body ventilatory output. When making a chamber between the pillars observed step configuration of the line production faces, promotes better aeration and maintenance of the roof. The self-propelled machinery primarily for heavy-duty diesel pneumatic course: drilling rigs with two or three punches, container loading and delivering cars, excavators, dump trucks, etc. for loading boreholes, inspection and ruffles on the roof of vehicles use auxiliary equipment works with an independent drive. Depending on the type of self-propelled equipment and power are the following deposits of technological options. Ore bodies of less than 2.5-3 m developing with overlapping or underlying podryvkoy species (determined by the stability of the roof and consistency of contact with the rocks of the ore body). Muck is moved with a bulldozer or Scooptrams and dispose of waste in the area of ??the same panel. Ore bodies of up to 7-8 m (when using the drill tower carriages - up to 12 m) in height and spend a continuous slaughter. The removal of the ore bodies with capacity of more than 8 meters is carried out in two layers in advance (30-40 m) of the upper layer 5-6 m tall This check on the soil overlying the bench can be inclined by Congress. For deposits of more than 16 power meters recess sometimes lead to the abandonment of the so-called ore bridge height 5-7 meters when it is appropriate anticipatory seizure of the overlying deposits. In room-and-pillar system design and use of sloping deposits of ore delivered to the scraper camera settings have to revolt. Capacity scrapers 0,25-0,45 m3 drilling with hand drills. When used at the treatment works of self-propelled equipment used or broken diagonal Transport Congress, have the camera along the strike. Depending on the angle and power of the ore body is cut layers of 2.5-4.5 m in height in the Making prosechek chamber between the pillars is retreating in order. When the power of the ore body 5-8 m (Fig. 3) training blocks (length 120-200 m) is to carry out haulage drift, ventilation (block) rebels and ore passes.
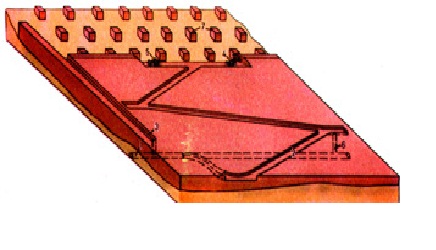
Fig. 3-Chamber-and-pillar mining method, broken down into blocks
Cut into blocks traffic diagonally arranged (or broken) inclined congresses. As the sewage extraction carried out with the use of autonomous self-propelled drilling rigs and Scooptrams, process chamber between the pillars. At a power reservoir for more than 8 meters of the development is option "twin chamber" (Fig. 4). At the same time take out parallel to the adjacent cell within the layer, which provides a more efficient use of self-propelled equipment. Preparation and cutting of the block is to conduct field and ore haulage drifts, field check haulage, storage and ventilation rebels, ore passes. Chamber between the pillars have to drop the deposit. Depending on the capacity of the reservoir, the angle of incidence, the equipment used daily productivity cutter unit varies from 200 to 1000 tons Removable downhole worker productivity 40-200 m, and the working of the system that is specific volume of 30-120 set-threaded work in the operation of inclined deposits is 4-6, shallow - 2-4 m by 1000 m stocks rudy.Razu bozhivanie with sewage seizure usually does not exceed 3-5%. The advantages of the technological schemes of chamber-pillar system design includes: high performance and the faces of the workers, a wide front of mining operations with many faces, the possibility of complete mechanization sewage extraction using a powerful self-propelled equipment, relatively low cost of mining. Disadvantages: high losses of ore (ore deposits of up to 40% in the salt - up to 60%), the complexity of a thorough inspection of the roof faces and proper ventilation in the broad development of sewage treatment works. The development of technological schemes follows the path of comprehensive mechanization using self-propelled diesel cars, hydraulic drills, reducing the loss of ore in pillars, finding cheaper methods of construction of artificial support with full mechanization of work.
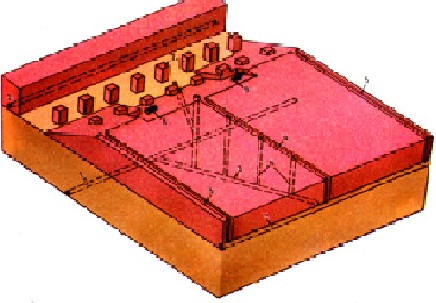
Fig. 4 - Development System "twin chamber"
In the gold mines of the chamber-pillar mining method is a two-stage process of extraction of mineral resources during mining of seam cells from the long narrow roadway to the vehicle ventilation and partial extraction chamber between the stope pillars with short (leaving between them narrow pillars) in the opposite direction (Figure . 5).
3. Cargo transport units are also used in underground mines in Ghana
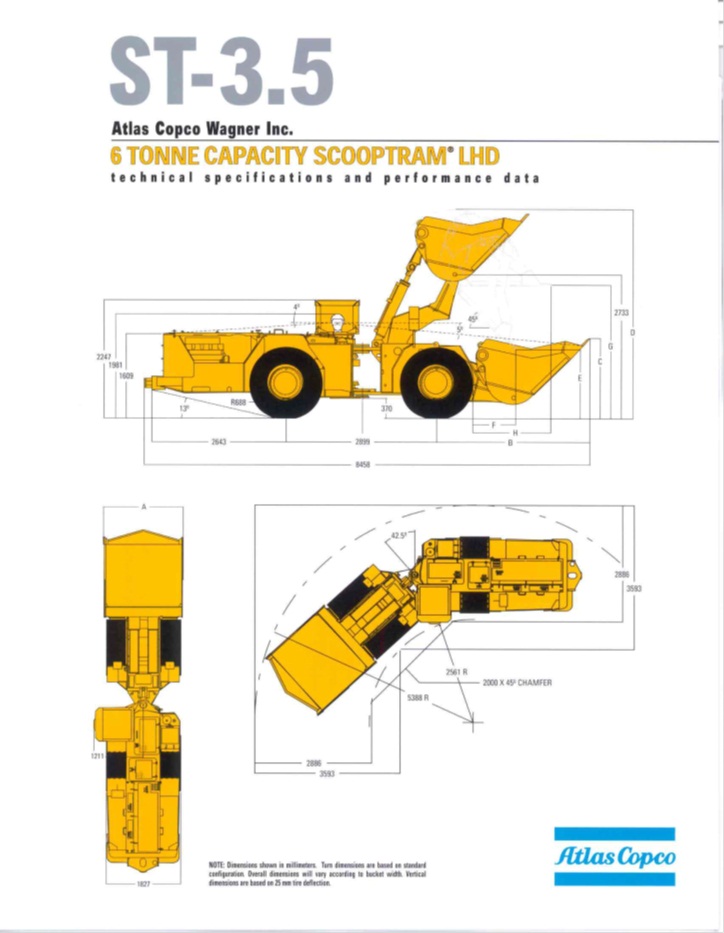
Fig. 5 - Cargo transport units are also used in underground mines in Ghana
In the clearing roadways pressure rocks is not seen bottom-hole bolting, and an array of bed and regularly left by the entire gold. As a result, eliminating the need to use a special lining to control the rock pressure. The roof is fixed in the cells, usually anchors in the extraction of stope pillars - not fastened. In Ghana, the room-and-pillar system design applied to a limited extent on the gentle power (up to 7-8 m) and medium-sized reservoirs during drilling and blasting breaking, manual or mechanical loading of gold, using a rack lining. Length of the chambers 30-50 m, width from 4 to 6 m, width of the partially recoverable pillars 5.4 m of coal losses of 30-45%. Labor productivity at the site did not exceed 10 tons / person per shift. Room-and-pillar mining method became widespread in the U.S. (up to 30% of underground mining of gold), Canada and Australia, mainly in shallow and medium-sized thin layers. The removal of gold complexes are self-propelled equipment. When drilling and blasting coal in breaking complex includes loading machine with manipulators for drilling and installation of roof bolting. Stope ventilated partial ventilation fans. In the recess at the seams with a high dust-raising capacity harvesters equipped Suction. With the comprehensive mechanization of mining the length of cells 100-150 m, width 5-6 m, width between the pillars of chamber to 15-18 m working areas shared by non-extractable barrier entirely. In favorable conditions, room-and-pillar mining method provides intensive extraction of stocks with high technical and economic performance: the load on the working face up to 1500-2000 tons per day, the productivity of workers on the site to 35-60 t / person per shift. The loss of coal in the bowels of 20-35% depending on the capacity of the reservoir roof rock of stability and depth of development. Significant losses of minerals and relatively complex mode of ventilation longwall faces make inappropriate use of room-and-pillar system design at the seams of gold spontaneously igniting in gassy mines at depths exceeding 500-600 m Collapse of the roof - displacement of rock covering a mineral seam or surrounding the ore body, accompanied by their dumped into an underground mine workings. Occurs spontaneously or artificially caused. Manifested in the separation from the array of blocks, slabs and pieces, and for any collapse of the roof earn a great pedigree depth (squeeze) - dynamic loads on the generation and air strikes in them. Adverse effects of the collapse of the roof prevents or reduces by installing roof supports in the mines, the state controls an array of minerals and rocks. The deliberate and systematic collapse of the roof is made periodic removal or shifting of bolting in the goaf. With solid rock roofs are prone to crash, to avoid severe manifestations of secondary sludge, reducing the stress concentration in prikraevoy of developed coal seam is also resorted to forced the collapse of the roof by blasting or other supplementary activities: advanced torpedo or hydrotreating main roof rocks, and other pre-underworking . purpose of the roof collapse - to weaken the action of rock pressure. In this case, the collapse of the roof is understood as the management of rock pressure (the roof). Parameters of intentional roof collapse (step landing close the roof, carried out by the removal or movement of roof supports, and the step of planting the main roof) determined by the properties of rocks, the depth of mining development and technological conditions. Depending on rock type, bed thickness, angle of bedding and other factors are accepted methods of rock pressure control by the collapse of the roof and the regulation of its set of events. The ability of the roof to collapse in the development of coal deposits is the basis for the different classifications of roofing obrushaemosti (for example, the classification for flat roofs woogie beds Donets Basin). In ore mines are sometimes used special development system, based on production technology based on the principle that the collapse of ores and host rocks. Patterns of roof collapse in underground are studying in order to support systems development, improvement of methods for calculating the lining, the rules of the workings and underground structures. Five. Cargo transport units used in underground mines in Hanna Cargo transport unit combines the operations of loading and transportation of minerals or rocks to the point of discharge. P.-t. a. used in underground mines during the mining and transportation of ore from the working faces in the construction of underground structures, as well as open cast mining and construction earthworks. By type accumulating capacity of distinguished P.-t. a. with a bucket or load-carrying body. P.-t. a. with the load-carrying body has a mechanism of scooping, chassis, storage vessel (body), drive motors, gears and controls. P.-t. a. with the load-carrying bucket of rock mass is transported in an elevated bucket to the destination, but they can unload it and dump trucks. Most P.-t. a. progress has pneumatic tires with high reliability for harsh conditions underground, equipped with pneumatic, electric and diesel drives with gas cleaning equipment. Developed many models of machines with load-carrying bucket (Fig. 1) carrying capacity of 2, 3, 5, 8 and 12 m (bucket capacity of 1 to 6 m 3) and 5 models of machines with a load-carrying body (Fig. 2) capacity of 2.5 4, 6, 10, 16 tons (capacity of the body from 2 to 6 m3). P.-t. a. with the load-carrying bucket produced overseas company "Wagner" (USA) - 10 models of the type «ST» with bucket capacity from 0.76 to 6.12 m3 firm "T x X Shterkrade" (Germany) - 14 models of the type «G-ST» with a bucket capacity from 0.76 to 8.5 m3 firm "Eymko" (USA) - 5 models of «LHD» and others P.-t. a. with the load-carrying body are made: the firm "Atlas Copco," (Sweden) - 6 models and the firm "Joey" (USA) - 3 models with bodies with a capacity of 0.75 to 5 m3i etc. The P.-t. a. implemented stand-alone drives, remote control, as unified units.
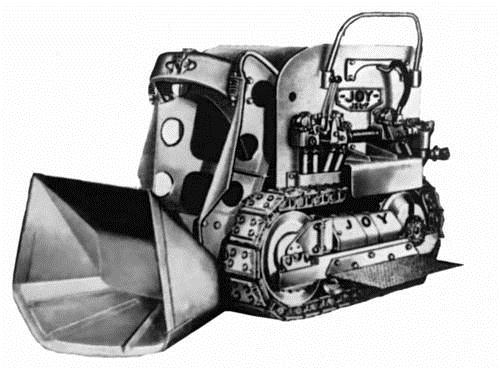
Fig.6-loading machines. Pelton direct loading
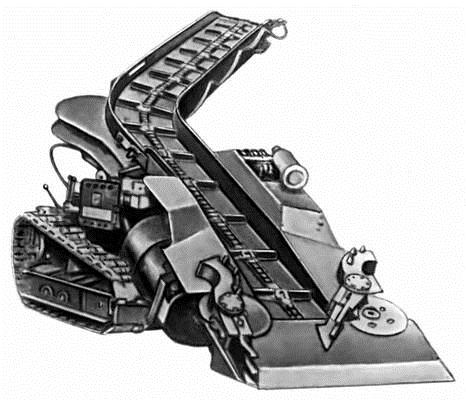
Fig. In Fig. 7-loading machines. The machine is paired with gathering arms.
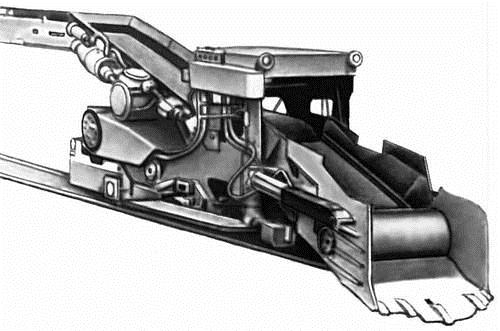
Fig. 8 - Loading the machine. Bucket with stepped loading.
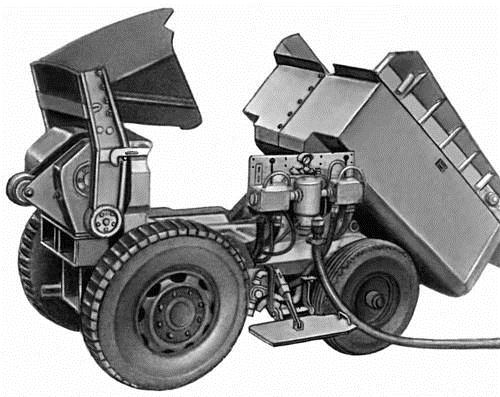
Fig.9-loading machines. Pelton dropside
Loading machines. Pelton dropside. At the bottom bucket scoops capture material (Fig. 1), which is a rollover discharged back to the vehicles (cars with direct loading), poured on the transmission pipeline (the machine with a loading speed), tilted forward or discharged to the side. Side grip is loading the body represents the slope of the receiving platform with double-shovel arms or legs with two bars and chains with a cantilevered scrapers, the upper grip - paddles mounted on the handle, which falls on the mountain mass, and shovel it into the transmission pipeline. L. m are wheel-rail, track progress, and pneumatic, pneumatic, electric and electro-or diesel drive self-contained, equipped with gas cleaning equipment. Some designs include the possibility of L. m to the installation of removable equipment (manipulators with rotary hammers to drill holes, small winches for lifting work, etc.). When mining the works of P. m are used in conjunction with self-propelled pneumatic downhole equipment on the go. In the bottom-hole complex, except for P. m, consists of drilling carriages, wagons and trucks, bulldozers, zaryadchiki holes and auxiliary machines (for installation of roof bolting, frills roofing, supply of equipment, materials and people). The characteristics of some models of P. m
manufactured in the USSR are given in Table. Foreign firms' Eymko "(USA)," Atlas Copco, "(Sweden)," Salzgitter "(Germany) and others are made with P. m bucket capacity from 0.1 to 1.15 m 3, a mass of 1.8 to 25 m with a total capacity of 10-120 kW engines, capacities from 0.3 to 6 m3/min. By "Joey" (USA) machines are available with double gathering arms on tracks, which are used in coal mines. Cargo transport unit with a load-carrying body. Ris1.Pogruzochno-transport unit with a load-carrying bucket. There are other technological solutions to extract gold from solution, however, they require special equipment, can be implemented only at the factory and therefore can not be used for Geotechnological gold. Cargo transport unit combines the operations of loading and transportation of minerals or rocks to the point of discharge. P.-t. a. used in underground mines during the mining and transportation of ore from the working faces in the construction of underground structures, as well as open cast mining and construction earthworks. By type accumulating capacity of distinguished P.-t. a. with a bucket or load-carrying body. P.-t. a. with the load-carrying body has a mechanism of scooping, chassis, storage vessel (body), drive motors, gears and controls. P.-t. a. with the load-carrying bucket of rock mass is transported in an elevated bucket to the destination, but they can unload it and dump trucks. Most P.-t. a. progress has pneumatic tires with high reliability for harsh conditions underground, equipped with pneumatic, electric and diesel drives with gas cleaning equipment. In the USSR, developed (1974) five models of load-carrying vehicles with a bucket (Fig. 1) carrying capacity of 2, 3, 5, 8 and 12 m (bucket capacity of 1 to 6 m 3) and 5 models of machines with a load-carrying body (Fig. 2 ) capacity of 2.5, 4, 6, 10, 16 tons (capacity of the body from 2 to 6 m3). P.-t. a. with the load-carrying bucket release (1974) overseas company "Wagner" (USA) - 10 models of the type «ST» with bucket capacity from 0.76 to 6.12 m3 firm "T x X Shterkrade" (Germany) - 14 models of the type «G -ST »with a bucket capacity from 0.76 to 8.5 m3 firm" Eymko "(USA) - 5 models of the type« LHD »and others P.-t. a. with the load-carrying body are made: the firm "Atlas Copco," (Sweden) - 6 models and the firm "Joey" (USA) - 3 models with bodies with a capacity of 0.75 to 5 m3i etc. The P.-t. a. implemented stand-alone drives, remote control, as unified units. Cargo transport unit with a load-carrying body. Cargo transport unit with a load-carrying bucket. Buropogruzochnye ispolzuyutsya machines for drilling under the tab of the explosive loading and further separated the rock mass at the sledueschee zvenl production chain. In Ghana ispolzuyutsya buropogruhzochnye car manufacturers in different countries, analogs of which can be called a Ukrainian-made car - BDP.
Conclusions and directions for further research
1) The development of gold deposits Hanna is mostly underground, which is very time consuming and complicated by the need for complete extraction of ore deposits.
2) The basic scheme used is the development of room-and-pillar. Depending on the applicable conditions are distinguished: chamber-and-pillar development system, broken down into blocks on the panel, system design, "paired cameras."
3) The main drawback of the existing technological schemes are large losses of ore is left in pillars.
4) A promising direction in the development of gold mining technology is the creation of alternatives in the form of wholly artificial supports and mechanization of the mining process.
5) The direction of future work is to develop a means of mechanization of mining and the improvement of technological schemes.
This master's work is not completed yet. Final completion: December 2011. The full text of the work and materials on the topic can be obtained from the author or his head after this date.
References
- Минеев Г.Г. Биометаллургия золота. – М.: Металлургия, 1989.
- Черняк А.С., Овчинникова О.В. Вторичные ионообменные явления в процессах выщелачивания золота и серебра // Гидрометаллургия золота. – М.: Наука, 1980.
- Байконуров О. А., Филимонов А. Т., Комплексная механизация очистных работ при подземной разработке рудных месторождений, А.—А., 1973;
- Barkalov Кальницкий Я. Б., Филимонов А. Т., Самоходное погрузочное и доставочное оборудование на подземных рудниках, М., 1974.
- www.mining-enc.ru