Реферат за темою випускної роботи
Зміст
- Вступ
- 1. Аналіз існуючих методів оптимізації режимів шліфування за пружною схемою
- 2. Аналіз існуючих конструкцій пристроїв для шліфування за пружною схемою
- 2.1 Пристрій для внутрішнього та зовнішнього круглого шліфування
- 2.2 Пристрій для круглого внутрішнього шліфування
- 3. Постановка завдань дослідження
- 4. Розрахунок динамічних характеристик шпиндельного вузла
- Висновки
- Перелік посилань
Вступ
У сучасній промисловості набули широкого поширення тверді сплави, які відносяться до важкооброблюваних матеріалів. Для їх ефективної обробки використовуються алмази, а також шліфувальні круги на металевій зв'язці, що заправлені електроерозійним способом.
Оптимізація режимів оброблення класичним способом потребує великих витрат часу, який може бути суттєво зменшений за рахунок використання нового способу визначення режимів, запропонованого на кафедрі металорізальних верстатів та інструментів ДонНТУ, з використанням миттєвої лімітованої різальної здатності круга, що визначається при шліфуванні за пружною схемою. Використання способу знаходження режимів з урахуванням поточної лімітованої різальної здатності круга сприяє зменшенню трудомісткості пошуку режимів і дозволяє повністю використати різальну спроможність робочої поверхні круга (РПК).
Актуальність теми: дослідження різальної спроможності РПК при внутрішньому шліфуванні твердих сплавів алмазними кругами у літературі відсутні, що свідчить про актуальність даної роботи.
Об'єкт дослідження: закономірність змінення різальної cпроможності поверхні круга при внутрішньому шліфуванні твердого сплаву кругами з надтвердих матеріалів, що заправлені електроерозійним способом.
Мета роботи: підвищення продуктивності внутрішнього шліфування твердих сплавів за рахунок повного використання різальної спроможності круга.
Наукова новизна роботи полягає в тому, що вперше будуть отримані рівняння, що описують змінення різальної спроможності круга при внутрішньому шліфуванні за пружною схемою.
Практична цінність результатів роботи: розробка нової конструкції шліфувальної бабки, в якій за рахунок нових конструктивних елементів забезпечується можливість внутрішнього шліфування отворів, радіус яких перевищує хід передній бабки, а також виконання шліфування зовнішньої циліндричної поверхні при збереженні якості обробки і матеріальних витрат, а також отримання рівнянь, що описують зміну різальної спроможності поверхні круга, які згодом можуть бути використані для оптимізації процесу шліфування.
1. Аналіз існуючих методів оптимізації режимів шліфування за пружною схемою
Забезпечення високопродуктивної механічної обробки різних груп матеріалів за умови отримання необхідних показників якості та мінімізації витрат на здійснення процесу обробки є перманентно актуальним завданням, яке постійно вирішується на етапі технологічної підготовки машинобудівного виробництва.
Обов'язковою процедурою при вирішенні зазначеної задачі є пошук оптимальних режимів обробки. Стосовно до процесів шліфування найпоширенішим й одним з найбільш точних методів до цього часу є класичний експериментально-теоретичний метод знаходження режимів, який включає наступні етапи [1]:
- складання системи рівнянь, що описують технічні обмеження, що накладаються на режими різання вимогами до деталі, верстатом, інструментом та умовами виробництва;
- математичний опис цільової функції, яка зазначає мету оптимізації;
- спільний розгляд технічних обмежень і цільової функції та визначення на цій основі оптимального режиму шліфування.
Головним недоліком цього методу, який істотно обмежує практичні можливості його використання в технологічній підготовці виробництва деталей з нових конструкційних матеріалів або в умовах шліфування кругами з новими характеристиками, є його висока трудомісткість, обумовлена великими витратами часу на експерименти, які необхідні для отримання всіх рівнянь і залежностей, що описують технічні обмеження. Крім того, він дає результати, які неможливо використовувати в випадку, коли режими або час оброблення виходить за межі, в яких були знайдені рівняння технічних обмежень, а також не враховує зміну різальної спроможності РПК під час роботи.
Протягом тривалого часу на кафедрі Металорізальні верстати та інструменти
ДонНТУ ведуться дослідження, які пов'язані з вивченням наступних питань:
- визначення параметрів процесу шліфування, що забезпечують задану шорсткість обробленої поверхні [2];
- знаходження допустимої сили взаємодії робочої поверхні круга (РПК) з поверхнею заготовки, при якій не відбудеться фазово-структурних змінень у поверхневому шарі оброблюваної заготовки [3];
- знаходження допустимої сили взаємодії РПК з поверхнею заготовки, при якій не відбудеться змін фізико-хімічних властивостей інструментального матеріалу [4,5];
- пошуком інтегрального технічного обмеження на режими шліфування, що забезпечують максимальну продуктивність при дотриманні заданих вимог за якістю обробки [4,5].
За результатами проведених досліджень розроблено ряд методик, які дозволяють визначати елементи режиму для обробки різних матеріалів і умов шліфування за умови дотримання всіх вимог до якості обробленої поверхні.
У роботі [6] проведене складання цілісного комплексу методик призначення режимів шліфування, що забезпечують стабільні показники якості обробки, і визначення узагальнених режимних параметрів процесу для пружною і жорсткої схем обробки.
Розглянемо комплекс методик, що застосовуються для визначення оптимальних режимів плоского врізного алмазного шліфування з електроерозійними впливами на РПК (за пружною схемою) згідно з запропонованою нами послідовністю оптимізації, яка включає наступні етапи [7]:
- Розрахунок швидкості деталі, при якій досягається необхідна шорсткість обробленої поверхні.
- Розрахунок максимально допустимого зусилля підтиску заготовки до круга в процесі шліфування за пружною схемою, при якому задовольняється лімітоване технічне обмеження.
- Експериментальне визначення закону зміни граничної ріжучої здібності круга у часі при шліфуванні за пружною схемою, яка кінематично є аналогічною жорсткій схемі.
- Визначення режимів електроерозійних впливів на РПК, що забезпечують мінімальну питому собівартість обробки, з урахуванням явищ, що викликали погіршення ріжучих властивостей круга.
- Опис закону зміни глибини шліфування за пружною схемою відповідно до закону зміни граничної ріжучої здібності круга без обліку процесу засолювання РПК.
- Визначення величини подачі на врізання з жорсткою схемою.
При алмазному шліфуванні продуктивність обробки залежить від різальної здатності круга, тому необхідно знайти параметр режиму різання, за допомогою якого можна буде в будь-який момент оброблення урівняти кількість матеріалу, який підводиться для видалення за рахунок робочих рухів, і кількість матеріалу, який може видалити робоча поверхня круга за рахунок її різальної здатності. Для цього користуються параметром – миттєвою поточною лімітованою різальною здатністю круга [8] – яка представляє собою об’єм матеріалу, який видаляється в одиницю часу, в будь-який час оброблення, при цьому виконуються технічні обмеження, що накладаються на режим обробки якістю обробленої поверхні або інструментом (наприклад, температурою порогу фазово-структурних перетворень у поверхневому шарі деталі, температурою графітизації алмаза, його міцністю і таке інше).
Визначення режимів максимальної продуктивності з використанням ріжучої здатності круга в якості обмежуючого параметра здійснюється у наступні етапи:
- знаходять граничні значення технічних обмежень, які накладаються на режим вимогами до якості обробленої поверхні, та шліфувальним кругом в межах технологічних можливостей верстата;
- з використанням технічного обмеження, яке задовольняє вимогам всіх розглянутих вище обмежень (лімітоване обмеження), розраховують силу підтискування зразка до робочої поверхні круга з використанням параметрів робочої поверхні, сформованої під час правки;
- з використанням пружної схеми шліфування, кінематика якої ідентична жорсткій, експериментально визначається регресійна залежність, що описує зміну ріжучої здатності РПК під час при шліфування.
Як показало порівняння класичного методу знаходження оптимальних режимів шліфування [1] та запропонованого методу [8], використання поточної лімітованої різальної здатності круга дозволяє значно зменшити витрати часу на пошук режимів внутрішнього шліфування, які забезпечують мінімальну собівартість оброблення при задоволенні вимог лімітованого технічного обмеження.
2. Аналіз існуючих конструкцій пристроїв для шліфування за пружною схемою
2.1 Пристрій для внутрішнього та зовнішнього круглого шліфування
Відомий пристрій (рис. 1) [10], який може використовуватись для внутрішнього та зовнішнього круглого шліфування. Він складається з нижньої плити 1, яка нерухомо з'єднана з передньою бабкою внутрішньошліфувального верстата, корпусу 2, розташованого в ластівкових напрямних плити 1 з можливістю переміщення відносно плити 1 в напрямку до робочої поверхні шліфувального круга.
![Розташування елементів пристрою для круглого шліфування перед обробленням [10]](images/prustriy dlya narugnogo shlifovaniya.png)
Рисунок 1 – Розташування елементів пристрою для круглого шліфування перед обробленням [10]
В циліндричній порожнині корпуса на підшипниках розмішена втулка 3 пристрою для закріплення заготовки (наприклад, трикулачковий патрон (на кресленні не показаний)). Поверхня 4 втулки 3 контактує з колесом 5, жорстко посадженим на вал 6, розташованим в отворі корпуса 2. На протилежному кінці валу 6 жорстко закріплене колесо 7, поверхня якого контактує з поверхнею паразитного колеса 8, розміщеного на одній із осей водила 9. Водило 9 має форму трикутника, на одній із вершин якого розташована ось паразитного колеса 8, а на інших вершинах – осі коліс 10 та 11. Планка 12 призначена для забезпечення постійної міжосьової відстані між колесами 8 і 7. Поверхні коліс 8, 10 та 11 знаходяться в контакті з поверхнею оболонки 13, закріпленої на шпинделі шліфувального верстата і забезпечують постійний збіг осей шпинделя і водила 9 незалежно від положення валу 6. Вантажі 14 через систему важелів шляхом переміщення корпусу 2 відносно нижньої плити 1 забезпечують притискання поверхні заготовки, закріпленої в трикулачковому патроні, до поверхні РПК.
Працює пристрій для круглого шліфування таким чином.
Перед шліфуванням елементи пристрою розташовані згідно рисунка 1. Після включення електричного двигуна приводу головного руху шпиндель починає обертатись, а разом з ним і оболонка 13. Рух від оболонки 13 через паразитне колесо 8 передається на колесо 7 і через вал 6 на колесо 5, далі на поверхню 4 втулки 3 з патроном в якому закріплено заготовку. Після включення приводу шліфувального круга корпус 2 під дією вантажу 14 починає переміщуватись в напрямку РПК, забезпечуючи шліфування з постійною силою притискання заготовки до робочої поверхні круга. Після видалення певної величини припуску відстань між осями шпинделя і оброблюваної заготовки характеризується величиною Н1 (рис. 2), яка менша від величини Н.
Враховуючи те, що міжосьова відстань між осями коліс 8 та 7 залишається за рахунок планки 12 постійною, при переміщенні верхньої плити в напрямку РПК колеса 8 та 7 знаходяться в постійному контакті, а водило 9 змінює своє положення в оболонці 13 відносно свого попереднього положення.
![Положення елементів пристрою для круглого шліфування після видалення певної величини припуску [10]](images/prustriy dlya narugnogo shlifovaniya_2.png)
Рисунок 2 – Положення елементів пристрою для круглого шліфування після видалення певної величини припуску [10]
При використанні пристрою при круглому зовнішньому шліфуванні плита 1 встановлюється на стіл круглошліфувального верстата, а в патрон закріплюють заготовку циліндричної форми, зовнішня поверхня якої підлягає обробленню.
Для забезпечення обертання заготовки у конструкції пристрою використовується безступінчастий привод головного руху, який є на верстаті. Це досягається завдяки виконанню верхньої плити в вигляді корпуса, встановленню на шпинделі верстата оболонки, з внутрішньою поверхнею якої контактують поверхні коліс, розташованих на водилі, причому одне із них є паразитним; колесо, яке встановлене на одному із кінців валу, розташованого в корпусі, має можливість контактування з поверхнею паразитного колеса, а колесо, яке розташоване на іншому кінці цього ж валу, встановлене з можливістю контактування з поверхнею втулки пристрою для закріплення заготовки; крім того, постійна відстань між віссю паразитного колеса та валом, розташованим в корпусі, забезпечується за допомогою планки, встановленої з можливістю повороту відносно осі паразитного колеса та корпуса.
Недоліком конструкції є її складність при виготовленні.
2.2 Пристрій для круглого внутрішнього шліфування
На рисунку 3 приведена модель внутрішнього шліфування.
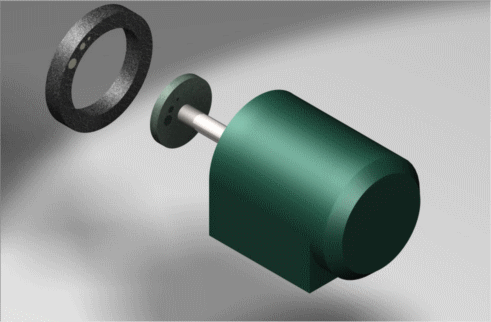
Рисунок 3 – Модель внутрішнього шліфування
В якості пристрою для внутрішнього шліфування є шліфувальна бабка (рис. 4) [11], яка складається з корпусу 1, що розташований на столі 2. Шліфувальна головка 3 з шліфувальним кругом 4 закріплена з двох сторін в обоймах 5, які мають зверху і знизу призматичні канавки з розташованими в них кульками 6. З шариками 6 знаходяться в контакті призматичні канавки планок 7, які закріплені на торці стаканів 8, закріплених в отворі корпуса 1. Канавки планок 7 утворюють кулькові напрямні, в яких в горизонтальному напрямку може переміщуватись відносно столу шліфувальна головка підтискаючи робочу поверхню шліфувального круга 4 до оброблюваної поверхні заготовки з постійною силою, яку задають за допомогою навантажувального пристрою.
Навантажувальний пристрій складається з вантажу 9, який пластинчатим ланцюгом 10 з'єднаний з шліфувальною головкою 3 через ролик 11. Електродвигун 12 закріплений на столі 2 за допомогою стійки 13 таким чином, що осі шківу 14 електродвигуна 12 та шківу 15 шліфувальної головки 3 знаходяться в одній вертикальній площині.
Таке розташування осей шківів 14 та 15 спрямовує силу натягування пасу 16 перпендикулярно напрямку переміщення шліфувальної головки і при величинах переміщень, характерних для виконання шліфування за пружною схемою, практично не впливає на величину сили притискання РПК до оброблюваної поверхні заготовки, яка задається вантажем 9.
![Шліфувальна бабка [11]](images/prustriy dlya vnutrennego shlifovaniya.png)
Рисунок 4 – Шліфувальна бабка [11]
Шліфування за пружною схемою виконується наступним чином.
Після установки заготовки в патроні бабки виробу, встановлюють величину переміщення столу вздовж осі заготовки, при якій шліфувальний круг повинен знаходитись по висоті в контакті з оброблюваною поверхнею, включають привід обертання заготовки, потім електродвигун, а шліфувальний круг вводять в оброблюваний отвір. Переміщуючи бабку виробу в напрямку, перпендикулярному осі шліфувальної головки, вводять РПК в контакт з оброблюваною поверхнею, забезпечивши при цьому зазор між зовнішньою циліндричною поверхнею шліфувальної головки з внутрішньою циліндричною поверхнею стаканів. В цьому випадку шліфування буде виконуватись з постійним підтисканням РПК до оброблюваної поверхні заготовки, величину якого задає вантаж. Під час видалення припуску при шліфуванні, зазор між зовнішньою поверхнею шліфувальної головки та внутрішньою поверхнею стаканів 8 буде зменшуватись, що потребує компенсації переміщенням бабки виробу, забезпечуючи постійну відсутність контакту між шліфувальною головкою та стаканами.
При закріпленні шліфувальної головки в корпусі нерухомо, наприклад, за допомогою гвинта встановленого в корпус (на графічних матеріалах гвинт не показаний), можливе виконання шліфування за жорсткою схемою.
Використання пружної схеми шліфування забезпечує зменшення трудомісткості пошуку оптимальних режимів та підвищення продуктивності оброблення до 30%.
Запропонована шліфувальна головка може застосовуватись на машинобудівних підприємствах та в лабораторних умовах при проведенні досліджень.
3. Постановка завдань дослідження
Як йдеться з приведеного аналізу, визначення оптимальних режимів шліфування із використанням узагальнюючих показників оброблення дозволяє зменшити трудомісткість пошуку оптимальних режимів.
Для визначення зміни поточної миттєвої різальної здатності круга використовується пружна схема шліфування з постійною силою притискання заготовки до РПК. Для виконання шліфування за пружною схемою розроблені пристрої, які з однієї сторони є складними або їх неможливо використати для шліфування за пружною схемою в широкому діапазоні зміни зміщення шліфувальної бабки відносно поверхні заготовки. У зв’язку з цим у магістерській роботі ставляться наступні основні завдання:
- Запропонувати конструкцію шліфувальної бабки, яка дозволяє виконувати на внутрішньо-шліфувальному верстаті не тільки внутрішнє шліфування за пружною схемою, але і шліфування зовнішніх поверхонь.
- Виконати розрахунок динамічних характеристик шпиндельного вузла.
- Проаналізувати напружено деформований стан шліфувальної бабки.
- Розробити робоче креслення шліфувальної бабки.
- Дослідити вплив виду надтвердих матеріалів (алмаз та ельбор) на зміну поточної різальної спроможності круга при внутрішньому шліфуванні швидкорізальної сталі Р6М5Ф3.
- Виконати статистичний аналіз досліджень.
- Підібрати рівняння регресії, які описують зміну різальної спроможності кругів з алмазу та ельбору при шліфуванні сталі Р6М5Ф3.
4. Розрахунок динамічних характеристик шпиндельного вузла
Серед чисельних методів розрахунку статичних і динамічних характеристик шпиндельні вузлів верстатів як лінійних пружних систем отримав поширення метод початкових параметрів у матричному формулюванні (метод перехідних матриць). Метод полягає в тому, що шпиндель (рис. 5) розглядають як балку на пружних опорах з в’язким демпфіруванням, яка складається з ділянок, розмежованих зміною моменту інерції перетину самого шпинделя, розташуванням опор, зосереджених мас деталей, змонтованих на шпинделі, зовнішніх зосереджених навантажень. Користуючись цим методом, за відомих значень параметрів на початку кожної ділянки шпинделя знаходять значення параметрів в кінці ділянки. Даний метод істотно спрощує і систематизує динамічний розрахунок, дозволяє застосовувати ЕОМ [14].
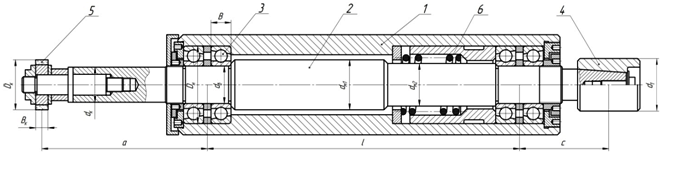
Рисунок 5 – Схема конструкції шпиндельного вузла шліфувальної бабки верстата моделі 3А227П: 1 – корпус шпиндельного вузла, 2 – вал шпинделя, 3 – підшипник ковзання, 4 – ведений шків, 5 – оправка з шліфувальним кругом, 6 – розпорна пружина
Розглянемо шпиндель приведений на рисунку 5, як балку на пружних опорах з в’язким демпфіруванням, та складемо розрахункову схему (рис. 6).
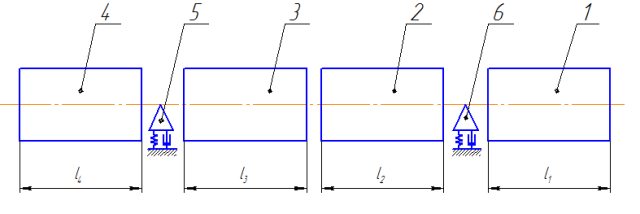
Рисунок 6 – Розрахункова схема шпиндельного вузла: 1 – ведений шків; 2, 3 – ділянки шпиндельного вузла; 4 – виліт шпинделю; 5,6 – опори підшипникові
Розрахунок динамічних характеристик шпиндельного вузла проводитися за допомогою програми на ПЕОМ в пакеті Mathcad. У якості вихідних даних для розрахунку є: погонні маси та моменти інерції ділянок шпиндельного вузла, жорсткість та величина демпферування у опорах.
Результатом розрахунку є графіки амплітудно-частотної характеристики (АЧХ) и амплітудно-фазово-частотної характеристики (АФЧХ), що показані на рисунку 7 та рисунку 8.
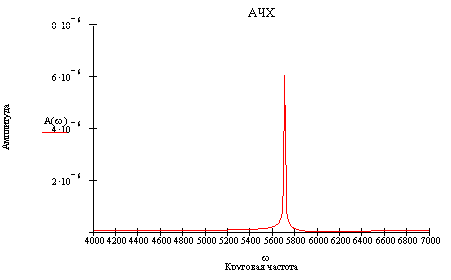
Рисунок 7 – Графік амплітудно-частотної характеристики шпиндельного вузла внутрішньошліфувального верстату мод. 3А227П
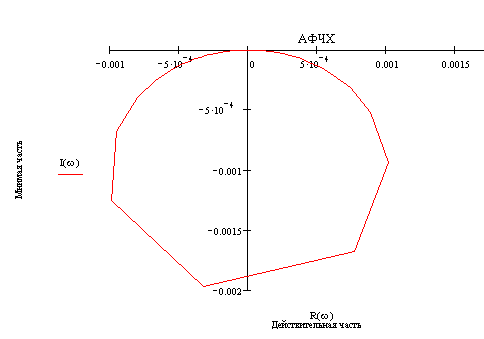
Рисунок 8 – Графік амплітудно фазово-частотної характеристики шпиндельного вузла внутрішньошліфувального верстату мод. 3А227П
За графіком АЧХ визначаємо, що зміна амплітуди відбувається, коли кругова частота ω = 5700 рад/с, що відповідає власній частоті коливань шпиндельного вузла f = 907 Гц. Проводити обробку у 30 % діапазоні від власної частоти коливань шпиндельного вузла, тобто 272 Гц, не рекомендується, так як можливе виникнення явища резонансу коливань – тобто система стає некерованою. Це явище є негативним, унаслідок чого неможливо провести механічну обробку із заданою точністю.
Розглянемо діапазон частот обертання, в якому виконується обробка на внутрішньошліфувальному верстаті 3А227П. Шліфування отвору D=45 мм виконується швидкості обертання шліфувального круга Vк = 20 м/хв.
Число обертів електродвигуна nд=2880 об/хв (ωд=302 рад/с), що відповідає частоті вимушених коливань fд=48 Гц; шпиндель шліфувального круга обертається з частотою nк = 9555 об/хв (ωк=1000 рад/с), що відповідає частоті вимушених коливань fк=160 Гц. Як видно, вимушені частоти коливань шпиндельного вузла не збігаються з частотою власних коливань, і не потрапляють в 30 % діапазон, і, отже, резонансні явища не виникнуть.
Висновки
У даній роботі проведений аналіз існуючих методів оптимізації режимів шліфування та встановлено, що використання узагальнюючих режимів процесу шліфування, які забезпечують стабільні показники якості, дозволяють зменшити трудомісткість пошуку оптимальних режимів.
На основі аналізу існуючої конструкції пристрою для шліфування за пружною схемою планується запропонувати конструкцію шліфувльної бабки, яка може бути застосована при при внутрішньому шліфуванні за пружною схемою з постійною величиною притискання РПК до поверхні зразка, забезпечуючи можливість внутрішнього шліфування отворів, радіус яких перевищує хід передньої бабки, виконання шліфування зовнішньої циліндричної поверхні при збереженні якості обробки та матеріальних витрат.
Також був проведений розрахунок динамічних характеристик шпиндельного вузла методом початкових параметрів у матричному формулюванні, який дозволяє визначити нижню власну частоту власних коливань шпиндельного вузла, при якій може виникати явище резонансу.
Важливе зауваження
При написанні даного реферату магістерська робота ще не завершена. Остаточне завершення: грудень 2012 року. Повний текст роботи та матеріали по темі можуть бути отримані у автора або його керівника після вказаної дати.
Перелік посилань
- Резников А.Н. Абразивная и алмазная обработка материалов. Справочник / Под ред. А.Н. Резникова. – М.: Машиностроение, 1977. – 391 с.
- Матюха П.Г. Научные основы стабилизации выходных показателей алмазного шлифования с помощью управляющих воздействий на рабочую поверхность круга: Автореф. дис.... докт. техн. наук: 05.03.01 / Матюха Пётр Григорьевич, Харьк. госуд. политехн. ун-т. – Харьков, 1996. – 48 с.
- Полтавец В.В. Обоснование режимов шлифования труднообрабатываемых материалов при электроэрозионном воздействии на рабочую поверхность круга: Автореф. дис…. канд. техн. наук: 05.03.01 / Полтавец Валерий Васильевич, Донецк. национальн. техн. ун-т. – Донецк, 2001. – 19 с.
- Матюха П.Г. Определение режимов плоского шлифования твердых сплавов с использованием нового критерия о текущей лимитированной режущей способности круга/ П.Г. Матюха, В.Б. Стрелков, В.В. Полтавец // Сверхтвердые материалы. Научно-теоретич. журнал. – Киев: 2004. – № 3. – С. 67-73.
- Матюха П.Г. Определение оптимальных режимов при алмазном шлифовании твердых сплавов по упругой схеме с периодическими электроэрозионными воздействиями на рабочую поверхность круга / П.Г. Матюха, В.Б. Стрелков // Сучасні технології в машинобудуванні. Зб. Наукових статей/ Уклад. А.І. Грабченко: За заг. ред. А.І. Грабченка. – Харків: НТУ „ХПІ”, 2007. – С. 330-332.
- Матюха П.Г. Узагальнені режими процесу шліфування, які забезпечують стабільні показники якості / П.Г. Матюха, В.В. Полтавець // Наукові праці Донецького національного технічного університету. Серія: «Машинобудування і машинознавство». Випуск 7 (166). – Донецьк: ДВНЗ «ДонНТУ», 2010. – С.35-49.
- Матюха П.Г. Определение оптимальных режимов шлифования с электроэрозионными управляющими воздействиями на рабочую поверхность круга/ Физические и компьютерные технологии в народном хозяйстве. / П.Г. Матюха, В.В. Полтавец // Труды 8-й международной научн.-техн. конф. 9-10 декабря 2003 г. – Харьков: ХНПК “ФЭД”, 2003. – С. 151-155.
- Матюха П. Режущая способность рабочей поверхности круга как ограничивающий параметр производительности шлифования / Петр Матюха, Валерий Полтавець // Надежность инструмента и оптимизация технологических систем. Сб. научных трудов. – 2003. – вып. 13, – с. 159-164.
- Корчак С.Н. Производительность процесса шлифования стальных деталей / Корчак С.Н. – М.: Машиностроение, 1974. – 280с.
- Патент України №91235 С2 МПК В24В47/00 Пристрій для круглого шліфування / Матюха П.Г., Полтавець В.В., Жулін І.С., Габітов В.В. Заявка а200803398 від 17.03.2008. Опубл. 12.07.2010 бюл. №13, 2010 р.
- Патент України №94813 С2 МПК В24В41/00 Шліфувальна бабка / Матюха П.Г., Габітов В.В., Войтов М.С., Благодарний А.О. Заявка а200911849 от 19.11.2009. Опубл. 10.06.2011 бюл. №11, 2011 р.
- Заявка а201012927 Україна, МПК В24В41/00. Навантажувальний пристрій для шліфування / Матюха П.Г., Габітов В.В., Благодарний А.О. заяв. 01.11.2010.
- Машиностроение. Энциклопедия в 40 томах. Том 4-7. Металлорежущие станки и деревообрабатывающее оборудование. М.: - Машиностроение. 2002. – 864 с.
- Орликов М.Л. Динамика станков / М.Л. Орликов – 2-е изд.,перераб. и доп.- К.: Выща шк.. Головное издательство,1989, - 272с.