Реферат по теме выпускной работы
Содержание
- Введение
- 1. Актуальность темы
- 2. Цель и задачи исследования, планируемые результаты
- 3. Технологический процесс очистки газов как объект автоматизации
- 4. Обзор исследований и разработок
- 5. Моделирование технологического процесса
- Выводы
- Список источников
Введение
На современном этапе развития экономики Украины обострились проблемы развития производственного сектора и, в частности, металлургического производства, которое в недавнее время составляло значительную долю ВВП. Причинами этого явились как и устаревшие технологические установки, оборудование и их низкий уровень автоматизации, так и внутренняя политическая обстановка в стране. Поэтому следует всячески стремиться к снижению себестоимости продукции путём внедрения новых технологий, увеличения объёмов выпускаемой продукции, повышения качества и увеличения уровня автоматизации производства, а не путём снижения оплаты труда и сокращений штата.
Так, в производстве стали с применением как устаревших, так и более новых технологий является перспективным применение установок внепечной обработки стали, которые позволяют ускорить технологический процесс путем снижения длительности плавки и повысить качество стали. Это неизменно приводит к снижению себестоимости продукции.
Для нормального функционирования таких установок необходимо наличие установок газоочистки. Основным рабочим элементом таких установок являются мешочные фильтры, срок службы которых напрямую зависит от температурного режима системы фильтрации. Повышенные температуры приводят к преждевременному износу фильтров, что приводит к увеличению издержек и накладывается на себестоимость продукции. Целью данной работы является создание системы автоматического контроля температуры отходящих газов с целью дальнейшего использования этих данных для создания эффективного режима работы системы газоочистки.
1. Актуальность темы
Ни для кого не секрет, что экологическая обстановка нашего региона оставляет желать лучшего, а объемы промышленного производства постепенно растут. Поэтому остро встает необходимость очистки промышленных отходов. Однако, строительство и эксплуатация таких установок – дорогое удовольствие, поэтому следует поддерживать в надлежащем состоянии существующие установки очистки и продлять срок их службы всеми возможными способами.
Данная магистерская работа посвящена исследованию процесса управления
охлаждением уходящих газов системы газоочистки установки Печь-Ковш
,
в которой возможно повышение температуры, что приводит к
преждевременному выходу из строя фильтрующих элементов. В связи с этим
возникает необходимость исследования процесса охлаждения отходящего
газа воздухом, определения его математической модели и получения
качественных характеристик, а также, на основе полученных данных,
автоматизации данного процесса.
2. Цель и задачи исследования, планируемые результаты
Целью данной работы является создание системы автоматического управления установкой очистки отходящих газов для обеспечения эффективного режима работы системы газоочистки.
Основными задачами при разработки данной системы являются:
- Разработка математической модели процесса разбавления уходящего газа воздухом.
- Поддержание температуры в фильтре на заданном уровне – 110 °С.
- Обеспечение эффективной загрузки установки путем своевременной очистки мешков фильтров.
- Передача на управляющую ЭВМ текущих значений технологических параметров.
- Выдача предупредительной сигнализации об отказе тех или иных устройств или возникновении аварийных ситуаций.
- Самодиагностика системы – автоматическое определение аварийного узла.
Объект исследования: система газоочистки.
Предмет исследования: Процесс охлаждения уходящего газа воздухом
По итогам выполнения данной работы планируется получение следующих практических результатов:
- Продление срока службы мешков фильтра. Это достигается путём быстрого установления требуемого значения температуры в фильтрах и недопущением длительного воздействия повышенных температур. Также износ уменьшается за счет уменьшения количества импульсов для очистки мешков. Это существенно снижает количество войлочного материала идущего на замену и уменьшает затраты на его приобретение.
- Устранение микропорывов мешка позволяет повысить качество очистки газов, что немаловажно, так как увеличение выбросов влечет за собой наложение штрафных санкций на предприятие государственными экологическими службами.
- Ограничение нижнего предела температуры позволяет добиться более эффективной загрузки установки и исключить перерасходы электроэнергии на излишние присосы воздуха в систему импульсной фильтрации.
- Применение современных средств диагностики исправности оборудования позволяет выявлять и оперативно устранять возникающие в ходе эксплуатации неисправности, сокращая тем самым простои установки.
3. Технологический процесс очистки газов как объект автоматизации
Система газоочистки установки внепечной обработки стали Печь-Ковш
предназначена для очистки уходящих газов с целью снижения количества
вредных выбросов в атмосферу, а также поддержания постоянства
внутренней инертной среды в установке Печь-Ковш
(УПК).
Отходящий газ удаляется из под свода установки Печь-Ковш
и по
трубопроводу диаметром 1250 мм поступает в систему газоочистки. Перед
поступлением сырого газа в фильтр происходит его смешивание со свежим
воздухом в сдвижном зазоре с целью его разбавления и охлаждения до
приемлемой температуры впуска в фильтр.
Для того, чтобы регулировать количество газа, имеется демпфер для регулирования потока Печи-Ковша. Зазор, предназначенный для разбавления отходящего газа воздухом, также имеет демпфер жалюзийного типа для регулирования притока свежего воздуха в систему фильтрации.
После прохождения отходящего газа через искроуловитель и охлаждения его до приемлемой температуры путем смешивания его со свежим воздухом происходит его очистка в фильтре импульсной очистки. Данный тип фильтров предназначен для очистки дымов из сталилитейных агрегатов с помощью мешочных фильтров, которые сами очищаются сжатым воздухом по определенному циклу. Конструкция фильтра импульсной очистки приведена на рисунке 1.
Сырой газ входит в фильтр через отверстия в бункерах пыли (5) и проходит в корпус фильтра с нижней стороны. Путем смены направление достигается предварительное осаждение более крупных частиц пыли. Эти более крупные частицы осаждаются непосредственно в бункере для пыли под корпусом пыли (1).

Рисунок 1 – Конструкция фильтра с импульсной очисткой
Отделение газа от частиц пыли осуществляется с внешней стороны мешков фильтра (2), которые установлены над корпусом фильтра. Газ проходит мешки фильтра снаружи внутрь, чистый газ затем проходит через трубку Вентури (9) в головку фильтра со стороны чистого газа (3). Во время фильтрации мешки прижимаются к корпусу фильтра.
Блок управления фильтром открывает мембранные клапаны (7) на короткое время (импульс примерно на 0,15 секунд), так что сжатый воздух пульсирует (впрыскивается) в мешки фильтра через сборочную трубку (4), сопло сборочной трубки (8) и трубки Вентури. Трубка Вентури сверху мешков фильтра, увеличивает эффект путем насасывания дополнительного окружающего воздуха со стороны чистого газа в мешок фильтра. Очищенный воздух, состоящий из сжатого воздуха и чистого газа, входит внутрь мешка фильтра с высокой скоростью. Мешок фильтра расширяется с высокой скоростью, и частицы пыли снаружи мешков выпадают на поверхности мешка. Импульс воздуха, который входит в мешок фильтра, также действует как воздух продувки, который продувается через мешок фильтра в противоположном направлении обычной фильтрации и усиливает очищающий эффект.
Пыль, которая счищается с мешков фильтра, падает в бункер для пыли. Устройство сбора пыли образовано одним цепным конвейером под фильтром и роторным клапаном, посредством которого она удаляется из системы газоочистки на дальнейшую утилизацию.
Главный вентилятор соединен с выходом фильтра трубопроводом диаметром 1250 мм. Главный вентилятор газоочистки – центробежный агрегат, который приводится в движение асинхронным трехфазным двигателем с короткозамкнутым ротором мощностью 315 кВт. Вентилятор работает на всасывание, создавая разрежение в подводящем трубопроводе и фильтрах, обеспечивает поступление сырого газа на очистку. После прохождения газом фильтрации, очищенный газ поступает через дымосос в дымовую трубу, посредством которой и сбрасывается в атмосферу [1].
Автоматизация данного объекта осуществляется при помощи комплекса
аппаратных и программных средств, которые объединены в общую систему
АСУ ТП Газоочистка
. Данная система является интегрированной в
систему управления установкой Печь-Ковш
, так как управление
газоочисткой находится в тесной взаимосвязи с управлением установкой
внепечной обработки стали. В свою очередь, система автоматизации УПК
интегрирована в общую систему АСУ ТП мартеновского цеха.
Управление осуществляется при помощи при помощи команд, вводимых оператором с управляющей ЭВМ РС Сталевара. От средств отбора информация поступает непосредственно на входы программируемого логического контроллера или к локальным устройствам управления. Информация о состоянии последних также передается на управляющую ЭВМ с целью мониторинга их состояния. В программируемом логическом контроллере происходит приём информации, её обработка и выработка управляющих воздействий согласно заложенному в нём алгоритму. Некоторые из полученных данных передаются на управляющую ЭВМ, где происходит их анализ, обработка и выработка управляющего воздействия согласно с алгоритмами и указаниями оператора.
Основными контролируемыми параметрами в этой системе являются:
- Данные, о положении демпферов и заслонок. Температуры их приводных двигателей и подшипниковых узлов, а также защита от заклинивания контролируются встроенными блоками управления. При этом на экране монитора РС Сталевара отображаются только данные о положении заслонок, а остальные выдаются только в случае превышения уставок в виде аварийного сообщения о неработоспособности того или иного механизма.
- Температура подшипниковых узлов и двигателя дымососа.
- Разрежение в фильтре, которое регулируется путем изменения положения заслонок газохода.
- Разность давлений в фильтрах со стороны загрязнённого и очищенного газов для определения степени засоренности фильтра.
- Температура газа на входе в трубопровод газоочистки и в фильтре.
Технология очистки уходящих газов непрерывно связана с технологией
обработки стали установки Печь-Ковш
. Регулирование некоторых
параметров системы газоочистки, таких как положение дымового демпфера
УПК, осуществляется по параметрам технологического процесса доводки
стали.
В связи с этим возникает необходимость интеграции системы автоматизации
газоочистки с системой управления установкой Печь-Ковш
.
Общий вид системы управления установкой Печь-Ковш
приведен на
рисунке 2.
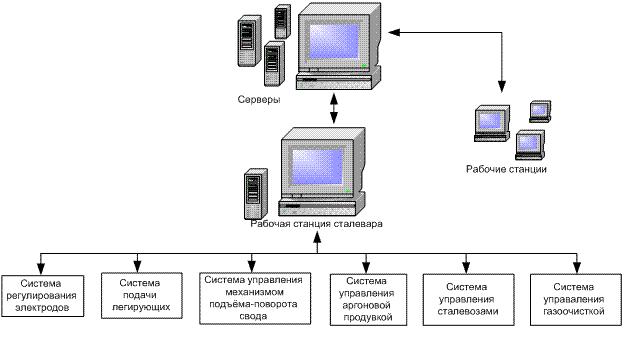
Рисунок 2 – Общий вид системы управления
установкой Печь-Ковш
.
(анимация: 6 кадров, 4 цикла повторения, 52 килобайта)
На данном рисунке показана взаимосвязь всех подсистем с управляющей ЭВМ – Рабочая станция сталевара (РС сталевара). С отдельных подсистем передаются данные о ходе технологического процесса на управляющую ЭВМ, где происходит их обработка и выдача соответствующих команд. Полученные данные передаются на общецеховой сервер, где происходи их архивация и хранение.
4. Обзор исследований и разработок
В данной главе рассмотрим теоретические и практические достижения отечественных и зарубежных исследователей в области газоочистки и автоматизации подобного рода систем.
Существует достаточное количество способов улавливания промышленной пыли. Основные конструктивные особенности и рекомендации по выбору способов для конкретных технологических условий содержатся в трудах Г.М. Алиева [2].
В учебнике Юдашкина М.Я. приведены основные положения по выбору материалов фильтрующих элементов рукавных фильтров. Выбор осуществляется на основе температуры газов, диаметрах микрочастиц пыли, требуемой степени очистки газов, срокам службы и др. параметрам [3].
Подход к автоматизации установок данного типа носит индивидуальный характер, поэтому серийная унифицированная аппаратура автоматизации для данного оборудования не выпускается. Общие положения по автоматизации металлургических объектов содержатся в книгах Глинкова Г.М [4].
В книге [5] рассмотрены технологические процессы как объекты автоматического управления. Кратко изложены основные принципы построения автоматизированных систем управления, вопросы организационного, информационного, математического, программного и технического обеспечения АСУ ТП. Рассмотрены особенности автоматизации металлургических установок.
В сборнике докладов международной конференции МЕТАЛЛУРГИЯ –
ИНТЕХЭКО
[6] приведены конструктивные
особенности, характеристики, а также сравнительный анализ рукавных
фильтров и электрофильтров.
В Украине разработкой и монтажом автоматизированных систем импульсной
фильтрации занимается Украинский государственный научно-технический
центр Энергосталь
.
УкрГНТЦ Энергосталь
разработаны и внедрены совмещенные системы
газоотвода, улавливания и сухой очистки печных газов и неорганизованных
выбросов крупно- и среднетоннажных электропечей, включающие:
водоохлаждаемый газоотвод горячих технологических газов от свода печи,
крышный зонт для улавливания потоков неорганизованных выбросов, сухие
пылеуловители (рукавные фильтры с импульсной регенерацией), дымососы,
систему газоходов, систему пылеуборки и окомкования пыли [7].
Существует множество зарубежных производителей автоматизированных систем импульсной фильтрации, которые предлагают автоматизированные системы рукавных фильтров с импульсной регенерацией: FLSmidth Airtech, VAI Fuchs и многие другие. Системы автоматизации этих производителей построены на программируемых контроллерах Simatic.
Информация о технологических датчиках и их основных параметрах, сфере их применения, а также поведении в составе систем автоматического управления изложена в учебнике, изданном на кафедре ГЭА [8]. Основные сведения по микросхемам, применяемым схемам гальванической развязки и их элементной базе, графическому представлению элементов электрических схем представлены в источниках [9 –11].
5. Моделирование технологического процесса
В связи с этим возникает необходимость исследования процесса охлаждения отходящего газа воздухом, определения его математической модели и получения качественных характеристик, а также, на основе полученных данных, автоматизации данного процесса.
При построении подсистемы управления температурой газа ан впуске фильтр учитываем, что зависимость между углом поворота заслонок приточного демпфера и температурой газа в фильтре можно выразить следующим аналитическим выражением [12]:
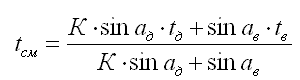
где К – усреднённый коэффициент, учитывающий отношение средних теплоёмкостей дымовых газов и воздуха;
sinaд – синус угла открытия (степень открытия) дымовой заслонки;
sinaв – синус угла открытия (степень открытия) воздушной заслонки;
tсм – температура дымовоздушной смеси;
tд – температура дыма;
tв – температура воздуха.
Трубопровод может характеризоваться диаметром, объёмом, излучающей способностью и т.д. В данном случае нас интересует его инерционность, т.е. за какое время отходящий газ пройдет от точки разбавления до точки входа в фильтр. Исходя из этого соображения, будем считать его апериодическим звеном первого порядка. Постоянные времени на различных участках трубопровода, определим зная среднюю скорость газового потока и длины данных участков.
Структурная схема моделированная с использованием среды Matlab [13] приведена на рисунке 3.
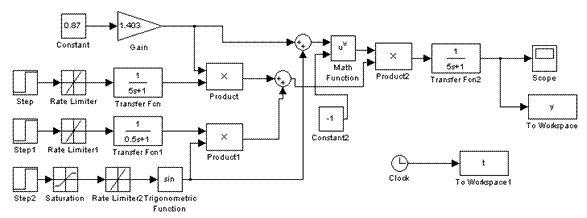
Рисунок 3 – Структура модели охлаждения дымовых газов
Заслонки, вместе со своими электроприводами ограничивают скорости нарастания дымового и воздушного потока. Для упрощения анализа в данной системе будем считать их линейными функциями. Блоки математических операций реализуют зависимость между углом поворота заслонок приточного демпфера и температурой газа в фильтре
При помощи модели, приведенной на рисунке 3, получаем переходный процесс охлаждения дымового газа воздухом, приведенный на рисунке 4.
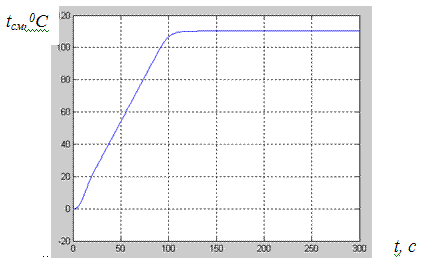
Рисунок 4 – График переходного процесса системы охлаждения
На рисунке 4 отображен процесс установления температурного режима при
запуске газа в систему фильтрации.
Как видно из графика, установившееся значение (110 °С) является
приемлемой рабочей температурой. Но так происходит далеко не всегда,
так как реально в данной системе могут происходить резкие изменения
температуры дымовых газов, что обусловлено работой системы поддержания
постоянного горения дуги – регулирования электродов установки Печь-Ковш
или изменения положения заслонки на газоходе УПК, управляемой системой
аргоновой продувки и перемешивания. Возможное влияние данных факторов
учтём при последующем моделировании. Переходный процесс установления
температуры в системе охлаждения, в данном случае, приведен на рисунке
5.
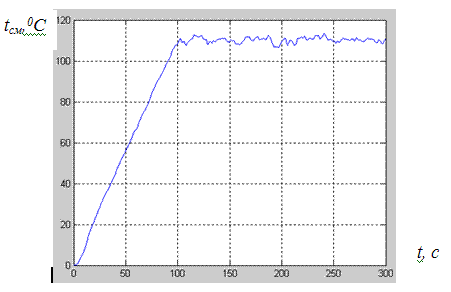
Рисунок 5 – График переходного процесса системы охлаждения с учетом внешних возмущений
Колебания температуры в зоне установившегося значения не являются значительными, т.е. не приводят к аварийному превышению температуры, но всё же являются нежелательными, так как могут вызывать постоянные включения приводов заслонок без весомой на то причины, что повлечет за собой преждевременный отказ последних. С этой целью следует ввести нечувствительность системы к малым отклонениям температуры от установившегося значения.
Ещё одной немаловажной проблемой является превышение допустимой рабочей температуры или излишнее её понижение. Первое влечет за собой повреждение мешков фильтра, а втрое – недогруз технологической установки и снижение её КПД. С учетом данных особенностей прейдем к моделированию процесса охлаждения с использованием системы автоматического управления.

Рисунок 6 – Модель процесса охлаждения с использованием системы автоматического управления
Для сравнения подадим на вход модели 6 воздействия, аналогичные тем, результаты которых приведены на рисунке 5. Результат моделирования приведен на рисунке 7.
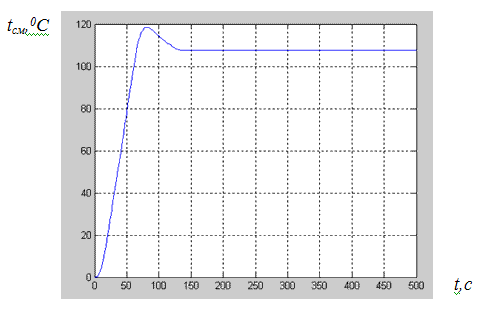
Рисунок 7 6 – Автоматический запуск и установление температуры
Несмотря на небольшое превышение температуры, полученный график в большей степени удовлетворяет технологическим параметрам установки, т.к. установившееся значение находится вблизи требуемого по технологическим параметрам установки, чем обеспечивается оптимальная нагрузка привода вентилятора и повышается КПД технологического процесса.
Выводы
В ходе проектирования была разработана система автоматизированного управления системой газоочистки установки внепечной обработки стали, соответствующая технологическим требованиям как по качественным характеристикам, так и по конструктивному исполнению.
Благодаря специальному способу установки измерительного преобразователя и соответствующей конструкции системы управления обеспечивается более оперативное регулирование температуры. Тем самым будет обеспечиваться максимально-эффективная загрузка технологической установки, что приведет к сокращению потребления электроэнергии, а также продление срока службы мешков фильтра импульсной фильтрации.
Важнейшим преимуществом данной системы являются использование более точной математической зависимости между изменением угла открытия заслонки демпфера и температурой газа.
Управление очисткой мешков на основании их засоренности позволяет снизить количество встряхивающих импульсов и тем самым уменьшить количество микроповреждений мешков, что не только продляет срок их службы, но и повышает качество самой очистки газов, выбрасываемых в атмосферу.
Разработанные схемы позволяют внедрить данную систему в общецеховую систему автоматизации на всех трех уровнях и обеспечить ее нормальное функционирование в условия интеграции с другими системами металлургического производства. Для более оперативного обнаружения и устранения неисправностей разработана система диагностики, снижающая простои установки на их устранение.
Эти мероприятия направлены на уменьшение издержек производства, понижение себестоимости продукции и, как следствие, повышение конкурентоспособности предприятия.
Список источников
- Руководтво по эксплуатации системы газоочистки УПК. – Д.: ЗАО «Донецксталь МЗ», 2003 г. – 465 с.
- Алиев Г.М. Техника пылеулавливания и очистки промышленных газов: Справ. изд. – М.: Металлургия, 1986 г. 544 с.
- Юдашкин М.Я. Пылеулавливание и очистка газов в черной металлургии. Изд. 2-е, перераб. и доп. – М.: Металлургия, 1984 г. – 320 с.
- Глинков Г.М., АСУ ТП в черной металлургии / Глинков Г.М., Маковский В.А. – М.: Металлургия, 1999 г. – 427 с.
- Бойко В.И. Автоматизированные системы управления технологическими процессами в черной металлургии / Бойко В.И. Смоляк В.А. – Днепродзержинск. 1997 г. – 574 с.
- Гольцев А.В. Системы снижения выбросов
пыли (FLSmidth Airtech, Дания). Сборник докладов международной
конференции
МЕТАЛЛУРГИЯ–ИНТЕХЭКО
г. Москва, 30–31 марта 2010 г. – 140 c. - "Сталь" №12. 2006г. с. 73–74 – 288 с.
- Груба В.И. Технические средства автоматизации в горной промышденности / Груба В.И., Никулин Э.К., Оголобченко А.С. – К.: ИСМО, 1998 г. – 373 с.
- Гутников В.С. Интегральная электроника в измерительных устройствах. – 2-е издание, перераб. и доп. – М.: Энергоатомиздат, 1989 г. – 431 с.
- С.Т. Усатенко. Графическое изображение электрорадиосхем: Справочник / С.Т. Усатенко, Т.К. Каганюк, Н.В. Терезова. – К.: Техника, 1986 г. – 210 с.
- В.И. Иванов. Полупроводниковые оптоэлектронные приборы: Справочник / В.И. Иванов, А.И. Аксенов, А.М. Юшин – 2-е издание, перераб. и доп. – М.: Энергоатомиздат, 1989 г. – 448 с.
- А.В. Павленко. Аналитическое определение температуры газов в фильтре системы газоочистки / Прикладные задачи математики в механике, экономике, экологии: Материалы IX международной студенческой научной конференции. А.В. Павленко, В.И. Ахонин, И.К. Юрченко – Севастополь, 18–22 апреля 2011 г. – 175с., с. 85–88.
- Дьяконов В.П. MATLAB. Анализ, идентификация и моделирование систем. Специальный справочник. / Дьяконов В.П., Круглов В.В. – Питер, 2001 г. – 448 c.