Abstract
This abstract is used as an example, with the permission of Genadiy Kirpyakov.
Original: http://masters.donntu.ru/2012/fmf/Kirpyakov/diss/
Content
Introduction
The development of technological systems ladle refining of the melt makes it necessary to optimize the mixing conditions of the metal in the ladle. This mixing is usually carried out by injection into the melt a certain amount of inert gas - argon [1]. At the same time, the number of nodes and the intensity of blowing blowing in different plants is variable. In this respect, the study aimed at establishing the optimal number of blocks and scavenging nature of mixing of the metal in the ladle are relevant and are of great industrial importance.
1. Theme urgency
The main objective of this study is to establish the optimum conditions of mixing of the melt during processing, which would allow to solve the following problems: definition of rational purge assemblies and their position in the bottom of the bucket; prevention of stagnant zones in a bath of molten metal in the ladle; determine the conditions corresponding to the intensity of the sound mixing, in accordance with the technology of metal in the ladle. The location and amount of purge units subject to the following technological considerations. It is envisaged as a rule, one - two (rarely three) purge unit, the location of which is regulated by certain technological considerations. First, purge units must be placed in such a way that the argon injected into the metal did not get into the zone of the electrodes used to heat the metal and slag (PPC). Secondly, one of the blowdown sites must be located in the area of ??supply of ferroalloys, which will provide a high degree of assimilation. Third, the purge unit can not be located in the area falling metal stream during filling of the bucket. Fourth, the purge unit can not be located near the wall of bucket, as in this case will be increased wear of refractories in the upstream distribution. Fifth, depending on the technological sequence of operations performed on the aggregate bucket, the intensity of the argon purge of the metal may vary within wide limits [1,2].
2. Goal and tasks of the research
At the initial stage of the research was evaluation of the 160-ton steel ladles in converter shop of Mariupol. Lenin. Technical department concluded that failure to use a purge unit, which carried a number of problems. In the operation of the bucket were observed increased wear of refractories in the slag belt zone, as well as insufficient removal of nonmetallic inclusions. On this basis, the company decided to increase the number of nodes to purge the two (Figure 1). Due to the fact that the industrial experiment fraught with difficulties (the high cost of testing, the inability to visualize the characteristic stages of the process, the complexity of measuring the values ??of physical quantities), to study the processes occurring in the ladle with two stoppers purge, it was decided to use the methods of physical modeling [3 ].
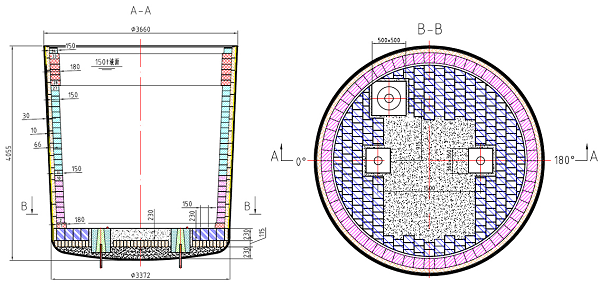
Figure 1 – Schematic design of a new ladle Mariupol metallurgical combine them. Illich
The physical model is a two-dimensional steel ladles, consisting of 3 plates of organic glass (center represents the inner contour of the industrial ladle Mariupol. Ilyich) and executed on a scale 1:6. As the working fluid simulation liquid steel, used water at a temperature of 18-25 ° C, since the viscosity of water and steel in the temperature furnace treatment and casting are close enough to each other (Table 1). For the mixing of the melt used compressed air. Flow was recorded with a digital camera. Given the fact that the injection of gas into the liquid is very important to the processes occurring under the action of gravity, which define the ascent of gas bubbles and the forces of inertia, as well as the development of flow patterns in a liquid bath bucket, in this paper as the basic criteria of similarity were Froude accepted criterion and the criterion homochronous.
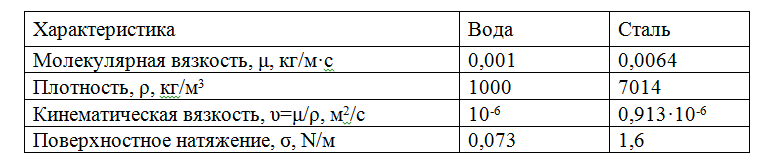
Table 1 – Physical properties of water at 20 ° C and steel at a temperature of 1600 ° C
The basis of pilot studies was based on four options for purging with compressed air rasskhodami equal to 150 liters / Minn. (soft shuffle), 250 l / min and 350 l / min (mean mixing), 800 l / min. The results of physical modeling are shown in Figure 2. Considering the variant a) must be noted that both threads do not interact with each other and their flow is independent. This character is most typical for purging the so-called "soft blow." The pattern of motion of gas bubbles at different intensity flushing: a) 150l/min b) 250 l / min, c) 350 l / min, d) 800 l / min
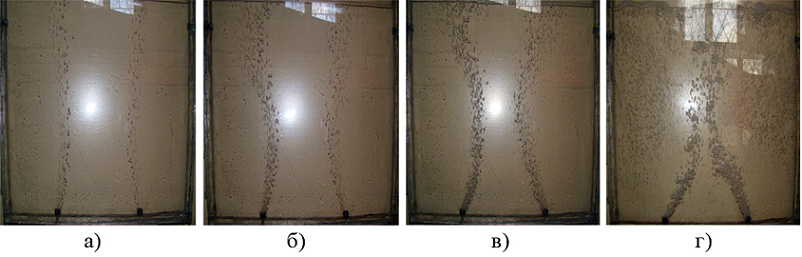
Figure 2 – The motion of gas bubbles with different intensity flushing: a) 150l/min b) 250 l / min, c) 350 l / min, d) 800 l / min
The nature of the end for the experiments with the higher costs of gas 250, 350 and 800 l / min (b, c, and d, respectively) is similar in nature. As the figure shows an increase in the intensity of flushing increases the mutual influence of one stream to another. Thus, in variant b) and c) a jet of air affect each other is not significant. At the bottom of the bucket, they are pressed against each other, but diverge slightly at the top. However, this is not the version of z), where the mid-level loading bucket is their mutual fusion, and surface waves arise as a consequence. Also, after passing under the mirror metal air jet continues its motion back deep into the bucket, creating, thus, the upper zone of circulation. Due to this non-metallic inclusions which should be deleted as a result of treatment with high probability will go into the metal. At the same time, will experience a significant reduction in the operational stability of the lining of casting ladles.
Conclusion
For this reason it must be concluded that the use of two plugs more efficiently both in terms of harmonizing traffic flows within the ladle and the removal of nonmetallic inclusions in the conditions of the bucket in the converter shop of Mariupol. Lenin. However, increasing the intensity of blowing up to 800 l / min leads to the opposite effect, as well as increased wear in the area of ??the slag belt.
References
- Smirnov, AN Safonov, VM After the converter and DSP (about the modern concept of technology in the steel processing plants, "ladle furnace") / / Metal. In 2005. Number 8. - P.34-43.
- AN Smirnov, EV Oshovskaya, IN Salmash, V. Safonov, KE Pismarev. Some questions assess the intensity of premeshivaniya by blowing the metal in the ladle with inert gas / / "Metal and Casting» - ¹ 3-4, - 2007. - P.44-49.
- D.Mazundar, H.B.Kim, R.I.L.Guthrie. Criteria for flow simulation in the processing of the metal in the ladle with gas purging: an experimental study / / - Ironmaking and steelmaking. 2000 - Vol.27.No4. - P.302-308