The analysis and development of the measures to prevent down time corrosion of Kurakhov power plant 200 MW boiler TP-109
Content
INTRODUCTION
Typically the equipment that is in the reserve or in the process of conservation, with poor compliance with technology and not enough drying, is subjected to down time corrosion.
It is known that corrosion occurs at the metal - working body ( metal - coolant). It leads to partial or complete destruction of the crystal lattice and a corresponding change in the properties of the metal. This destruction can be caused by various factors: chemical, electrochemical, mechanical, influence of the neutron field, etc.
Down time corrosion is the most common reason of boiler metal failure. It is exposed to all elements of the boiler, made of carbon and low alloy steels, which are in contact with the water that contents almost any oxygen in it. However, in practice, corrosion becomes dangerous only when the oxygen content in the feed water is more exess than 10-20 mg/kg. When idling boiler corrosion is almost captures all the elements of steam boilers, where there is oxygen and moisture.
BASIC METHODS TO DECREASE DOWN TIME CORROSION
Methods of dealing with down time corrosion can be divided into dry and wet.
The simplest method of decreasing steam generators down time corrosion is emptyfying when water has a temperature 80° C and drying by opening of the hatches, manholes and the air vent to release the steam. In some cases, to improve and accelerate the drying can be used slow heating with steam or hot air ( t = 200 - 250 ° C). Wall temperature has to exceed 100 ° C.
At long parking after emptying and drying of their drums, we can put the pan with a desiccant ( calcium chloride (CaCl2), lime (CaO), silica gel, etc.) and hermetically close all manholes, hatches, fittings. 1 m3 of the total volume of the boiler requires at least 2 kg of calcined CaCl2, 3 kg of CaO. State of desiccant has to be checked every 3-6 months in the case of spreading of CaCl2 or damage resulting from lumps of CaO conversion into Ca (OH) 2 is replaced with fresh dehumidifiers.
Conservation with the neutral gas (usually nitrogen) maintained at a small positive pressure ( 5-10 kPa) prevents access to the outside air. This method requires a continuous supply of nitrogen and high-quality sealing system. At the same time it cause great difficulties with pressurization of the flow path of turbines. Despite the high reliability of this method of preservation, it is quite expensive because of the large number of places for possible leaks of nitrogen and the complexity of their pressurisation.
Reducing of the relative humidity can be achieved in two ways: 1) heating and 2) draining. If the air at 20 ° C and a relative humidity of 70% is heated by 10 ° C, the relative humidity drops below 40%. Then the heated air is fed into the equipment and increases the temperature of the metal compared with the environment, which prevents loss of moisture, provides evaporation of moisture remaining in the equipment after the draining, and protects the surface from corrosion.
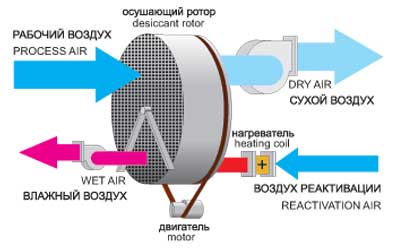
Figure 1 - The scheme of dehumidification
Therefore, the application of this method involves high energy costs. In the real condition after blowing of the heated (and therefore moist) air to the unheated equipment it cools, especially in poorly ventilated ducts, and the relative humidity is once again in the critical zone of active corrosion. Also, there is a risk of moisture condensation, if there is a surface with a low temperature. Based on these considerations, it is necessary that all the details of equipment were brought to a temperature above the dew point of the suppledwarmair for the conservation. It is also necessary to measure the characteristic temperatures of different parts of the system.
"Wet" conservation methods can be used under plus temperatures and are more convenient than the "dry", but they are only suitable for preservation of water or preservative solution into the steam generator. They also include:
- stay in the hot steam reserve under the steam pressure 0.3 - 0.5 MPa from other steam deaerator, from the turbines drafts, etc.;
- filling of the steam generator with deaerated water and maintaining it above the atmospheric pressure at the highest point of the boiler (air vent). Pressure is maintained with deaerated feed water or netpiping water after the deaerator (0.5 - 0.7 MPa), and after the feed pumps.
CONCLUSIONS
Analysis of all known methods of conservation allows to identify the most promising. One of which is filling of the boiler with deaerated feed water in conjunction with maintaining of the constant pressure. Desorption water oxygen content decrease by is very promising. The method is based on the desorption of dissolved oxygen with nitrogen, obtained on the site. It is effective, inexpensive and environmentally acceptable.
On the basis of this method useful model systemfor water oxygen content decrease by desorption of water has been proposed.
This master's work is not completed yet. Final completion: December 2012. The full text of the work and materials on the topic can be obtained from the author or his head after this date.REFERENCES
- Акользин П.А. Основы расчета установок для десорбционного обескислороживания воды. – «Теплоэнергетика», 1954, №2, с.31.
- Мейкляр М.В. Как работает металл парового котла – Госэнергоиздат, 1961, 95с.
- Роберт Д. Порт, Харви М. Херроу. Практическое руководство компании НАЛКО по анализу причин повреждения котлов – McGraw-Hill, Inc. 278с.
- Баранов П.А. Предупреждение аварий паровых котлов – М. Энергоатомиздат, 1991, 272с.
- Либерман Г.Р Предупреждение аварий и неполадок котельного оборудования – М., Энергия, 1972, 312с.
- Методические указания по консервации теплоэнергетического оборудования – ОРГРЭС, 1997,49с.