Анализ и разработка мероприятий по предупреждению стояночной коррозии котлов ТП-109 блока 200 МВт Кураховской ТЭС
Содержание
ВВЕДЕНИЕ
Как правило оборудование, находящееся в резерве или в стадии консервации, при плохом соблюдении технологии и не достаточной степени осушки, подвергается стояночной коррозии и выходит из строя.
Известно, что коррозия протекает на границе металл — рабочее тело (металл — теплоноситель). Она приводит к частичному или полному разрушению кристаллической решетки и соответствующему изменению свойств металла. Это разрушение может вызываться различными причинами: химическими, электрохимическими, механическими, влиянием нейтронного поля и других факторов.
Стояночная коррозия является самым распространенным видом разрушения котельного металла. Ей подвергаются все элементы котлов, изготовленные из углеродистых и низколегированных сталей, которые контактируют с водой практически с любым содержанием в ней кислорода. Однако, на практике коррозия приобретает опасный характер лишь при содержании кислорода в питательной воде, превышающем 10-20 мкг/кг. Коррозия, как правило, проявляется в виде язв с диаметром до 5 – 10 мм, зачастую покрытых рыхлым слоем ржавчины. При простаивании котлов коррозия практически захватывает все элементы паровых котлов, где имеется кислород и влага.
ОСНОВНЫЕ МЕТОДЫ БОРЬБЫ СО СТОЯНОЧНОЙ КОРРОЗИЕЙ
Методы борьбы со стояночной коррозией делятся на сухие и мокрые.
Простейшим методом борьбы со стояночной коррозией парогенераторов являются спуск из них еще горячей воды с температурой 80 °С и высушивание путем открывания всех лючков, лазов и воздушников для выхода образующегося пара. В отдельных случаях для улучшения и ускорения высушивания можно применять слабый обогрев опорожненного парогенератора газом или горячим (t = 200 - 250 °С) воздухом. Температура стенок должна превышать 100 °С.
При длительной стоянке парогенераторов в резерве в барабаны их после опорожнения и высушивания помещают противни с влагопоглотителем (хлористым кальцием CaCl2, негашеной известью CaO, силикагелем (высушенный золь кремниевой кислоты H2SiO3) и др.) и герметически закрывают все лазы, лючки, арматуру. На 1 м3 полного объема котла требуется не менее 2 кг прокаленного CaCl2, 3 кг свежеобожженной СаО или прокаленного силикагеля. Состояние влагопоглотителя проверяют каждые 3—6 мес и в случае расплывания CaCl2 или разрушения комков СаО в результате превращения их в Са(ОН)2 влагопоглотители заменяют свежими. Однако эти методы сопряжены с дополнительными затратами для нейтрализации этих растворов после их использования. В мировой практике, где учитывают не только первоначальные, довольно значительные затраты, но и стоимость утилизации отработанного раствора, экологически небезопасные соединения не нашели широкого применения.
Консервация нейтральным газом (как правило, азотом) с последующим поддержанием небольшого избыточного давления (5–10 кПа) предотвращает доступ наружного воздуха. Этот способ требует непрерывную подачу азота и качественную герметизацию системы. При этом большие трудности вызывает герметизация проточной части турбин. Практика показала, что утечки азота при консервации энергоблока 300 МВт составляют (в зависимости от качества запорной и предохранительной арматуры) от 2–3 до 40–50 м3/ч, т.е. фактически необходимо собственное азотное производство. Несмотря на высокую надежность этого метода консервации, он является довольно дорогостоящим из-за наличия большого числа мест возможных утечек азота и сложности их уплотнения.
Во многих случаях для того, чтобы предотвратить коррозию, достаточно понижения относительной влажности воздуха до 60 %. Снижение относительной влажности воздуха может быть достигнуто двумя путями: 1) нагреванием и 2) осушением. Если воздух с температурой 20 °C и относительной влажностью 70 % подогреть на 10 °С, то относительная влажность снизится ниже 40 % .
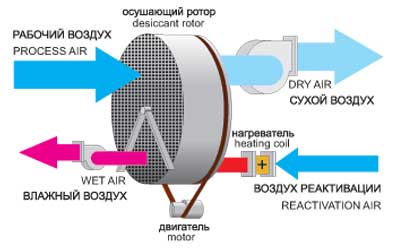
Рисунок 1 - Схема осушения воздуха
Затем подогретый воздух подается внутрь оборудования и, повышает температуру металла по сравнению с окружающей средой, что препятствует выпадению влаги, обеспечивает испарение влаги, оставшейся в оборудовании после дренирования, и предохраняет поверхности от коррозии. Поэтому применение такого метода предполагает высокие энергетические затраты. В реальных условиях после подачи подогретого атмосферного (а значит, влажного) воздуха в непрогретое оборудование он остывает, особенно в слабо продуваемых каналах, и его относительная влажность вновь оказывается в критической зоне активной коррозии. Также появляется опасность конденсации влаги, если имеются поверхности с пониженной температурой. Исходя из этих соображений, необходимо, чтобы все части оборудования были доведены до температуры выше точки росы подаваемого в целях консервации подогретого воздуха Кроме того, необходимо измерять характерные температуры разных участков консервируемой системы.
"Мокрые" методы консервации допустимы при плюсовых температурах и более удобны, чем "сухие", но они пригодны только при сохранении воды или консервирующего раствора в парогенераторе. К ним относятся также:
- пребывание парогенераторов в горячем резерве с поддержанием в них избыточного давления 0,3 - 0,5 МПа паром от других парогенераторов, от деаэраторов, от отборов турбин, от расширителей непрерывной продувки, от линии собственных нужд или растопочной;
- заполнение парогенератора деаэрированной водой и поддержание в нем давления выше атмосферного в самой верхней точке котла (воздушник). Давление в нем п оддерживается при помощи деаэрированной питательной или сетевой воды как после деаэраторов ДП (0,5 — 0,7 МПа), так и после питательных насосов.
ВЫВОДЫ
Анализ всех известных методов консервации позволяет выявить наиболее перспективные, одним из которых является применение метода заполнения котлов деаэрированной питательной водой в сочетании с поддержанием в них постоянного избыточного давления. Десорбционное обескислороживание воды весьма перспективно. Метод основан на десорбции растворенного в воде кислорода газообразным азотом, получаемым на месте. Он эффективен, дешев и экологически приемлем.
На основании этого метода, была предложена полезная модель установки для десорбционного обескислороживания воды.
При написании данного реферата магистерская работа еще не завершена. Окончательное завершение: декабрь 2012 года. Полный текст работы и материалы по теме могут быть получены у автора или его руководителя после указанной даты.
СПИСОК ИСТОЧНИКОВ
- Акользин П.А. Основы расчета установок для десорбционного обескислороживания воды. – «Теплоэнергетика», 1954, №2, с.31.
- Мейкляр М.В. Как работает металл парового котла – Госэнергоиздат, 1961, 95с.
- Роберт Д. Порт, Харви М. Херроу. Практическое руководство компании НАЛКО по анализу причин повреждения котлов – McGraw-Hill, Inc. 278с.
- Баранов П.А. Предупреждение аварий паровых котлов – М. Энергоатомиздат, 1991, 272с.
- Либерман Г.Р Предупреждение аварий и неполадок котельного оборудования – М., Энергия, 1972, 312с.
- Методические указания по консервации теплоэнергетического оборудования – ОРГРЭС, 1997,49с.