Реферат по теме выпускной работы
Содержание
- Введение
- 1. Актуальность темы
- 2. Цель и задачи исследования
- 3. Описание области применения
- 4. Обзор исследований и разработок
- 4.1 Обзор международных источников
- 4.2 Обзор национальных источников
- 4.3 Обзор локальных источников
- 5. Технология непрерывной разливки
- 5.1 Общие сведения о процессе непрерывной разливки стали
- 5.2 Классификация МНЛЗ
- 5.3 Кристаллизация непрерывнолитой заготовки
- 5.4 Кристаллизатор
- 6. Математическая модель процесса кристаллизации непрерывнолитых заготовок
- 6.1 Задача Стефана
- 6.2 Модель температурного поля слитка
- 7. Разработка метода решения задачи
- 7.1 Выбор средств реализации программного обеспечения
- 7.2 Алгоритм построения трехмерной модели
- 8. Обзор существующих программ моделирования процесса непрерывной разливки
- 8.1 Программное обеспечение
ПроНРС-1
- 8.2 Система
Термовизор
- 8.3 Программный комплекс
Непрерывная разливка стали
- Выводы
- Список источников
Введение
Литью поддаются все металлы. Но не все металлы обладают одинаковыми литейными свойствами, в частности жидкотекучестью – способностью заполнять литейную форму любой конфигурации. Литейные свойства зависят главным образом от химического состава и структуры металла. Важное значение имеет температура плавления. Металлы с низкой температурой плавления легко поддаются промышленному литью. Из обычных металлов наивысшая температура плавления у стали. Металлы делятся на черные и цветные. Черные металлы – это сталь, ковкий чугун и литейный чугун. К цветным относятся все другие металлы, не содержащие в значительных количествах железа. Для литья применяются, в частности, сплавы на основе меди, никеля, алюминия, магния, свинца и цинка.
Тепловые процессы в литье стали на каждом этапе весьма сложны и не поддаются аналитическому решению из-за большого числа переменных, влияющих на величину перепада температуры. Экспериментальный метод в решении таких задач требует колоссальных денежных затрат, сложнейшего оборудования, решения вопросов моделирования реальных условий. Современное развитие численных методов и производительности компьютеров делает наиболее привлекательным численный подход в решении тепловых задач для непрерывной разливки[1].
1. Актуальность темы
Современная МНЛЗ представляет собой высокотехнологичный агрегат, позволяющий практически полностью защитить металл от вторичного окисления посредством применения высококачественных изостатически прессуемых огнеупоров (защитная труба, погружной стакан и пр.), обеспечить оптимальные режимы качания (за счет использования гидропривода) и автоматическое поддержание уровня металла в кристаллизаторе, осуществлять автоматическое предотвращение прорывов металла, улучшать качество внутренней структуры заготовки посредством наложения на жидкую фазу электромагнитного поля и «мягкого» обжатия заготовки с жидкой сердцевиной и пр.
В целом же к началу XXI века в качественном и количественном аспектах произошло практически полное насыщение металлургических предприятий мира различного рода МНЛЗ и соответствующим технологическим обеспечением. Одним из определяющих направлений в части развития концепции непрерывной разливки стали стало сокращение объемов инвестиций и срока их окупаемости, как при строительстве новых цехов, так и при реконструкции уже существующих[2]. При этом особое внимание уделяется уменьшению удельных затрат на производство металлопродукции. Ведущие мировые производители оборудования для непрерывной разливки достигли высочайших показателей для классических МНЛЗ (разливка сляба, блюма, круга, сортовой заготовки) и сконцентрировали основное свое внимание на альтернативных концепциях по созданию литейно-прокатных агрегатов для получения плоской продукции. Развитие технологий и конструкций машин для непрерывной разливки стали будет происходить в части создания высокоэффективных производственных модулей, которые приобретут гибкую технологическую связь при совмещении процессов выплавки стали, ее разливки и последующей прокатки заготовки[3].
2. Цель и задачи исследования
Целью исследования является изучение тепловых процессов затвердевания стали в машинах непрерывного литья заготовок, а также разработка алгоритма программы, позволяющей строить трехмерные модели процессов теплообмена и кристаллизации в слитке при непрерывной разливке стали.
Основные задачи исследования:
- Обзор существующих программных решений.
- Выбор подходящей математической модели.
- Исследование процесса непрерывной разливки в МНЛЗ.
- Обзор средств реализации программного обеспечения.
- Разработка алгоритма построения трехмерной модели слитка.
Объект исследования: процессы теплообмена и кристаллизация слитка в машине непрерывного литья заготовок.
Предмет исследования: методы расчета и визуализации теплового поля непрерывнолитой заготовки.
3. Описание области применения
Непрерывная разливка стали является важнейшим технологическим этапом в производстве металлопродукции, поскольку она обеспечивает перевод стали из жидкого состояния в твердое с приданием ей определенной геометрической формы. Кроме этого условия охлаждения и затвердение стали во время непрерывной разливки в значительной мере предопределяют высокое качество металлопродукции в сравнении с консервативной системой разливки в слитки.
Использование непрерывной разливки в сталеплавильном производстве способствует экономии капиталовложений в связи с исключением затрат на парк изложниц, сооружение цеха подготовки составов, стрипперного отделения, обжимных станов, а также обеспечивает значительную экономию металла вследствие уменьшения обрези, экономию энергии, которая тратилась на подогрев слитков в нагревательных колодцах, позволяет снизить экологическую нагрузку на атмосферу, повысить качество металлопродукции, автоматизировать процесс литья и улучшить условия работы обслуживающего персонала.
Конструктивные решения, используемые при создании машин непрерывной разливки, содержат в себе знания из целого ряда дисциплин в области металлургии, материаловедения, теории затвердения, электротехники, гидродинамики, теплофизики, теории измерений и автоматических систем управления и др. Такой комплексный подход не имеет аналогов при создании высокоэффективных агрегатов и машин для технологических схем производства чугуна и стали.
Технологический процесс и машины непрерывной разливки стали постоянно развиваются и совершенствуются, что расширяет сферу их применения и создает предпосылки для трансформации сталеплавильного передела в целом. Уровень эффективности использования технологий непрерывной разливки стали учитывается при создании новых производств и модернизации действующих. В свою очередь это стимулирует дальнейшее развитие конструкций машин непрерывной разливки стали, обеспечивая большую привлекательность их дизайна и конкурентоспособность[4].
Несмотря на некоторые незначительные отличия, основные технологические и конструктивные особенности МНЛЗ довольно хорошо изучены и разработаны. Дальнейшее их развитие и совершенствование достигается за счет обеспечения высокой гибкости и функциональности машин непрерывного литья заготовок (МНЛЗ), включая совмещение процессов литья и прокатки.
4. Обзор исследований и разработок
Процесс закалки стали является важной частью металлургической промышленности. Этот процесс широко изучаются учеными всего мира. Исследование кристаллизации продолжаются и сегодня.
4.1 Обзор международных источников
Сталь – отнюдь не изобретение Нового времени. Способ ее получения был известен уже за 1000 лет назад. Однако до XIX в. сталь практически не использовалась. Поскольку ее производство было слишком сложным и дорогим. Быстрым и доступным оно стало лишь после того, как Генри Бессемер изобрел в 1856 г. названный его именем конвертер. Претерпев ряд существенных изменений, этот метод стал сегодня основным в черной металлургии.
Содержание углерода и других нежелательных примесей снижается так называемым фришеванием. Для этого чугун необходимо снова нагреть до жидкого состояния. С 1784 г. это делается в пудлинговой печи, нагреваемой каменным углем. Чугун плавят на поду до тестообразного состояния, постоянно помешивая металлическими штангами для увеличения доступа кисторода. Бессемер усовершенствовал этот процесс, построив доменную печь: сквозь массу бедного фосфором чугуна продувался сжатый воздух, способствуя процессам окисления. Конвертер Бессемера выдавал за 20 минут столько же стали, сколько пудлинговая печь за целый день. На сходном принципе основан и изобретенный в 1864 г. мартеновский процесс. Позже появились кислородные конвертеры и электрические печи для выплавки стали.
В 1742 г. Бенджамин Хантсман начал выплавлять сталь не в открытой печи с древесным углем, а в нагреваемом тигле.
Благодаря французскому металлургу Пьеру Мартену, который в 1865 году запатентовал печь для выплавки стали нового образца, в производстве этого металла стало возможным использовать лом, которого на планете к тому времени накопилось громадное количество.
Однако главная революция в сталеплавильном производстве произошла в 1865 году, когда французы – отец и сын Пьер и Эмиль Мартены – использовали для получения стали газовую печь, построенную по чертежам немецких инженеров братьев Вильгельма и Фридриха Сименс. В ней, благодаря подогреву газа и воздуха, в особых камерах с огнеупорной насадкой достигалась такая высокая температура, что сталь в ванне печи переходила уже не в тестообразное, как в пудлинговой печи, а в жидкое состояние. Ее можно было заливать в ковши и формы, изготавливать слитки и прокатывать их в рельсы, балки, строительные профили, листы[5]. Кроме того, появилась возможность использовать громадные количества железного лома, скопившегося за долгие годы на металлургических и машиностроительных заводах.
В 1878 г. Сидни Гилкрист Томас изобрел «томасовский процесс» для Удаления фосфорных примесей из железной руды в процессе плавки.
В 1952 г. в Австрии начал работу первый в мире сталелитейный завод на основе ЛД-процесса. Имеющиеся в чугуне примеси удаляются в таком конвертере продувкой техническим кислородом.
Конкурент у конвертерных плавок сегодня один – это электроплавка стали, занимающая около 30 процентов мирового производства главного металла тяжелой промышленности. Выплавка стали в электропечах основана на использовании электроэнергии для нагрева металла.
4.2 Обзор национальных источников
Николай Тимофеевич Гудцов, крупнейший советский учёный-металловед, специалист в области строения, свойств, термической обработки и легирования стали, академик АН СССР (1939), заслуженный деятель науки и техники РСФСР. Наряду с другими выдающимися металлургами и металловедами старшего поколения – А.А. Байковым, И.П. Бардиным, С.С. Штейнбергом, Н.А. Минкевичем, А.Л. Бабошиным, А.М. Бочваром и др. Гудцов являлся ведущим учёным первой половины XX столетия в развитии науки о строении и свойствах металлов.
Когда в 1936 году советский инженер Николай Илларионович Мозговой впервые использовал для продувки чугуна в конвертере кислород, перспективы конвертерной выплавки стали куда реалистичнее. Металл, получаемый кислородно-конвертерным процессом, по качеству стал равноценен мартеновской стали, себестоимость выплавки снизилась почти на четверть, серьезно возросла и производительность конвертерных производств[6].
Раузин Я.Р. работая с 1953 года заведующим Лабораторией испытаний материалов и конструкций Института Железнодорожного Транспорта СССР занимался исследованиями в области повышения качества, в частности, подшипниковой стали, и улучшения технологии термической обработки высокохромистой и высокоуглеродистой стали. Я.Р. Раузин занимался разработкой новых методов испытаний металлов на контактную выносливость, ударную вязкость, натурных ударных испытаний при низких температурах. В течение многих лет исследовал механизмы начальных стадий пластической деформации, отстаивая гипотезу о решающей роли ротационных перемещений. Последние работы Я.Р. Раузина посвящены методам оценки конструктивной прочности стали и выбору способов повышения прочности стали.
Исследования Раузина явились теоретической основой для развития и широкого использования промышленностью СССР прогрессивных методов термического упрочнения подшипниковых, рельсовых, инструментальных и конструкционных сталей, сыграли важную роль в переводе подвижного состава железнодорожного транспорта СССР на роликовые подшипники.
Львиную долю в изучение стали внес Акимов Георгий Владимирович. После выхода в свет в 1940 году монографии «Теория и методы исследования коррозии металлов» и учебника «Основы учения о коррозии и защите металлов» началась целая серия работ в области теоретических и экспериментальных исследований коррозии металлов. С этими работами связано создание сети коррозионных станций в представительных климатических зонах страны – Дальние Зеленцы, Звенигород, Владивосток, Батуми. Теория структурной коррозии и теория многоэлектродных систем, созданные Г.В. Акимовым, нашли широкое признание в СССР и за рубежом. Его работы в области пассивности ознаменовались открытием явления перепассивации. Акимов автор более 250 научных трудов по проблемам коррозии металлов.
4.3 Обзор локальных источников
В Донецком национальном техническом университете(ДонНТУ) совместно с НПО Доникс
С.П. Еронько, д.т.н, А.Ю. Цупрун, С.А. Бедарев, Д.А. Яковлев, Е.П. Потапов, Г.С. Романова
и др. ведут разработку шиберных устройств для технологических переливов стали. Ими были разработаны и реализованы новые шиберные системы, на котрорые уже получены патенты.
Большую долю исследований в области сталеплавления принес доктор технических наук, доцент и заведующий кафедрой Смирнов Евгений Николаевич. Он является автором 140 научных статей, 20 патентов и авторских свидетельств на изобретения, а также соавтором 20 учебно-методических пособий и методических указаний.
5. Технология непрерывной разливки
5.1 Общие сведения о процессе непрерывной разливки стали
Машины непрерывной разливки стали – системы, которые обеспечивают получение готовой заготовки из жидкой стали. При использовании МНЛЗ сталь из сталеразливочного ковша поступает в промежуточный ковш, а из него в кристаллизатор. В кристаллизаторе образуется оболочка, заполненная жидкой сталью по форме и сечению, отвечающему готовой заготовке. Частично затвердевшая заготовка с помощью транспортирующей системы – тянущей клети поступает в зону вторичного охлаждения, где происходит полное затвердевание заготовок[7]. Застывший слиток разрезается на мерные длины и готовые заготовки с помощью транспортных средств направляются в прокатный цех или на склад.
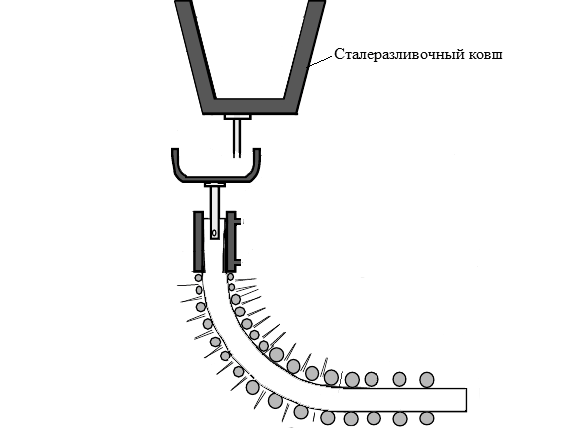
Рисунок 1 – Схема непрерывной разливки в МНЛЗ
(анимация: 6 кадров, 7 циклов повторения, 48 килобайт)
При подготовке МНЛЗ к разливке в каждом кристаллизаторе с помощью специального устройства – затравки – устраивается сплошное дно. Верхний конец затравки, имеющий пазы, вводится в кристаллизатор, ее противоположный конец находится в зацеплении с тянущим устройством. При наполнении внутренней полости кристаллизатора металлом начинается процесс движения затравки вниз. При этом скорость вытяжки заготовки определяется толщиной и механической прочностью твердой корочки заготовки на выходе из кристаллизатора, которая необходима для предотвращения прорывов жидкого металла по ходу разливки.
Для уменьшения трения между коркой твердого металла и стенками кристаллизатора, предотвращения смачивания стенок кристаллизатора жидкой сталью и создания нейтральной или восстановительной атмосферы, на поверхность металла в кристаллизаторе вводят твердую или жидкую смазку в виде различных масел, углеводородов или теплоизолирующих шлаковых смесей. В процессе разливки кристаллизатор совершает возвратно-поступательные движения с определенной частотой и амплитудой, что предотвращает прилипание твердой корочки заготовки к поверхности кристаллизатора. Уровень металла в кристаллизаторе поддерживается постоянным, что обеспечивает повышение качества поверхности заготовки и стабилизирует процесс литья. Для образования прочной оболочки – корки металла стенки кристаллизатора изготавливаются из материала, обладающего высокой теплопроводностью, и интенсивно охлаждаются водой[8].
Из кристаллизатора частично затвердевший слиток попадает в зону вторичного охлаждения (ЗВО), которая состоит из опорных элементов и устройств, обеспечивающих охлаждение слитка. Опорные элементы должны предотвращать деформацию оболочки слитка и искажение ее формы. Охлаждение осуществляется обычно орошением поверхности слитка водой или водовоздушной смесью, распыляемой специальными форсунками, которые установлены по ходу движения заготовки. Расход воды зависит от разливаемой марки стали и скорости вытягивания слитка.
После того как полностью затвердевший слиток в месте соединения с затравкой выходит из тянущего устройства, затравка отсоединяется от слитка и убирается специальным механизмом, а слиток поступает в устройство для резки. По окончании разливки остатки слитка выводятся из машины, убирается промежуточный ковш, проводятся контроль и настройка действия механизмов и системы охлаждения, затем вновь вводится затравка.
Таким образом, к основным функциональным элементам МНЛЗ можно отнести:
- Зона вторичного охлаждения – позволяет создать оптимальные условия для полного затвердевания непрерывно отливаемого слитка, обеспечивающие равномерное охлаждение заготовки (распыления воды форсунками, поддержание ее геометрической формы роликами) и требуемое качество металла.
- Механизм для резки заготовок – обеспечивает разделение непрерывнолитого металла на мерные длины.
- Сталеразливочный ковш – обеспечивает транспортировку стали от сталеплавильного агрегата к МНЛЗ, доводку стали по химическому составу и температуре и перелив в промежуточный ковш.
- Тянуще-правильная машина (ТПМ) – предназначена для вытягивания литой заготовки из кристаллизатора, выпрямления ее на радиальных и криволинейных устройствах и подачи к механизму для резки; ТПМ обеспечивает подачу затравки в кристаллизатор, удержание ее в кристаллизаторе на время уплотнения зазоров, вытягивание с непрерывнолитой заготовкой из кристаллизатора, отделение головки затравки от заготовки и т.п.
- Промежуточный ковш (промковш) – обеспечивает поступление металла в кристаллизатор с определенным расходом хорошо организованной струей, позволяет разливать сталь в несколько кристаллизаторов одновременно и осуществлять серийную разливку при смене сталеразливочных ковшей без прекращения и снижения скорости разливки.
- Кристаллизатор – предназначен для приема жидкого металла, формирования слитка заданного сечения и первичного его охлаждения (выполняется из меди и охлаждается в процессе разливки водой).
- Затравка – предназначена для образования временного «дна» в кристаллизаторе перед началом разливки и последующего вытягивания со сцепленной заготовкой ТПМ.
5.2 Классификация МНЛЗ
В настоящее время в эксплуатации находится большое разнообразие установок непрерывной разливки стали. Это обусловлено требованиями к сортаменту и качеству заготовок и производительности МНЛЗ. Все эти разновидности классифицируются по следующим признакам[9].
По типу заготовки:
- Cлябовые – отливаемые заготовки имеют форму поперечного сечения в виде прямоугольника с соотношением длинной стороны к короткой 3:1 и более.
- Блюмовые – отливают заготовки в форме круга, квадрата или прямоугольника с малым соотношением сторон; размер стороны – 200 мм и более.
- Сортовые – заготовки аналогичны блюмовым, но имеют меньшие размеры сторон.
По принципу работы:
- Установки непрерывной разливки – слиток режется на заготовки мерной длины, что позволяет разливать правки сериями.
- Установки полунепрерывного литья – длина заготовки обусловлена ходом механизма вытягивания, который выбирается из соображения упрощения и удешевления машины в данных условиях производства; порезка слитка, если это необходимо, осуществляется вне машины.
По составу:
- Одноручьевые.
- Многоручьевые – позволяют увеличить производительность установки.
По характеру движения кристаллизатора:
- С неподвижным кристаллизатором (горизонтальная МНЛЗ).
- С возвратно-поступательным движением – кристаллизатор определенный период движется одновременно со слитком или опережая его, а затем возвращается в начальное положение; к этому типу относятся основное количество установок разливки стали.
- С кристаллизатором, двигающимся со скоростью слитка – обеспечивает отсутствие скольжения оболочки слитка относительно кристаллизатора и трения между ними, что снижает вероятность разрыва оболочки при высоких скоростях разливки; к этому типу относится так называемая роторная МНЛЗ, где скорость разливки в 2-3 раза превышает скорость обычных установок.
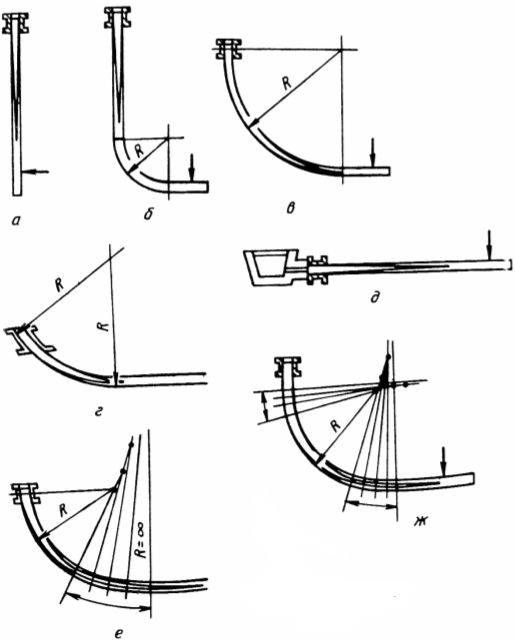
Рисунок 2 – Расположение технических осей МНЛЗ
По расположению технологической оси:
- Машины с постоянной кривизной оси до окончания затвердевания слитка.
- Машины с переменной кривизной оси.
К машинам с постоянной кривизной технологической оси относятся:
- Вертикальные (см. рис. 2а) и вертикальные с изгибом (см. рис. 2б), изгиб слитка осуществляется после полного затвердевания для вывода технологической оси в горизонтальное положение; имеют малую скорость разливки и низкую производительность установок.
- Радиальные с постоянным радиусом кривизны (см. рис. 2в) – имеют более высокую скорость разливки и производительность.
- Наклонно прямолинейные и наклонно-радиальные (см. рис. 2г) – значительное снижение высоты машины и ферростатического давления позволяет значительно уменьшить массу оборудования МНЛЗ.
- Горизонтальные (см. рис. 2д) – технологическая ось располагается под углом 7-12 градусов к горизонту.
К машинам с технологической осью переменного радиуса относятся:
- Криволинейные МНЛЗ с радиальным кристаллизатором (см. рис. 2е), имеющие кристаллизатор и часть ЗВО с постоянной кривизной и участок переменной кривизны, где происходит плавное выпрямление с жидкой сердцевиной.
- Криволинейные МНЛЗ с вертикальным кристаллизатором, в которых после небольшого вертикального участка ЗВО имеет участок изгиба слитка, радиальный участок и участок выпрямления слитка (см. рис. 2ж).
В настоящее время преимущественно эксплуатируются радиальные и криволинейные МНЛЗ. Как правило, криволинейные МНЛЗ устанавливаются в конвертерных цехах, а радиальные – в электросталеплавильных, выплавляющих стали более сложных марок. Горизонтальные МНЛЗ устанавливаются в мартеновских цехах небольшой производительности.
В дальнейшем в данной работе будет рассматриваться одноручьевая слябовая МНЛЗ криволинейного типа с вертикальным кристаллизатором.
5.3 Кристаллизация непрерывнолитой заготовки
В процессе затвердевания слитка при непрерывном литье можно выделить два основных этапа: формирование внешней оболочки в кристаллизаторе (зона первичного охлаждения) и окончательное затвердевание в зоне вторичного охлаждения[10].
5.4 Кристаллизатор
В машине непрерывного литья кристаллизатор выполняет функцию первичного холодильника, отводящего до 30% теплоты расплава, и формообразователя, обеспечивающего заданную форму поперечного сечения слитка.
Основной задачей кристаллизатора является создание необходимых условий для интенсивного отвода теплоты от жидкого металла. В результате по его периметру происходит непрерывное формирование вешней оболочки – корочки будущего слитка. Обязательным условием нормальной работы кристаллизатора является обеспечение на выходе из него оболочки с прочностью, превышающей ферростатическое давление находящегося в ней жидкого металла и усилий вытягивания.
Роль кристаллизатора как теплообменника сводится к тому, что теплота от жидкой стали через стенку кристаллизатора передается охлаждающей воде. Затвердевающий слиток представляет собой сосуд с переменной толщиной стенок, заполненный жидкой сталью.
В процессе образования оболочки и нарастания ее толщины происходят ее усадка и образование газового зазора между поверхностью оболочки слитка и стенками кристаллизатора. При этом термическое сопротивление на пути от жидкого металла к охлаждающей воде увеличивается, а передаваемое количество теплоты за счет уменьшения суммарного коэффициента теплопередачи понижается. Для устранения этого явления стенки кристаллизатора изготавливаются с учетом усадки металла, однако полностью избавиться от газового зазора не удается[11].
6. Математическая модель процесса кристаллизации непрерывнолитых заготовок
6.1 Задача Стефана
Общепринятой моделью, используемой при математическом описании многообразных процессов кристаллизации, является классическая постановка задачи, предложенная Й. Стефаном в 1889 г[12].
Основные физические предположения, принятые в классической постановке задачи Стефана:
- Температурное поле в жидкой и твердой фазах описывается уравнением теплопроводности с соответствующими теплофизическими характеристиками.
- Кристаллизация происходит на границе раздела фаз, определяемой уравнением
причем априори предполагается существование однозначной, достаточно гладкой поверхности раздела фаз. - Фазовый переход происходит в равновесных условиях, т.е. на границе раздела фаз задана равновесная температура Tk
- Cкорость продвижения границы раздела фаз определяется условием теплоотвода скрытой теплоты фазового перехода
где γ – удельная скрытая теплота фазового перехода; ρ – плотность материала; νn – скорость продвижения границы раздела фаз по направлению нормали n; λT, λЖ – коэффициент теплопроводности в твердой и жидкой фазах соответственно.
Зная законы теплопереноса в жидкой и теплой фазах, краевые условия на границах рассматриваемой системы и начальное распределение температуры, необходимо определить эволюцию температурных полей в твердой и жидкой фазах и закон перемещения во времени границы раздела фаз.
Математическая модель процесса затвердевания, основанная на приближении Стефана, может быть сформулирована следующим образом. Пусть система ограничена поверхностью P(x, y, z, t).

где c – удельная теплоемкость; p – плотность; v – скорость движения расплава.
В момент времени t = 0 твердая фаза отсутствует и имеется начальное распределение температуры в жидкости T2(x, y, z, 0) . На поверхности P(x, y, z, t) задаются краевые условия, адекватно описывающие процесс охлаждения поверхности системы. В момент появления в процессе остывания твердой фазы на границе раздела фаз ставится условие равенства температур , вытекающее из предположения идеального теплового контакта между фазами и заключающееся в том, что температуры жидкой и твердой фаз одинаковы и равны равновесной температуре кристаллизации

Далее предполагается, что скрытая теплота кристаллизации, выделяющаяся при движении межфазной границы, отводится через твердую фазу вместе с остальным теплом перегрева. Поэтому для межфазной границы R ставится условие, выражающее баланс тепловых потоков

где n – нормаль к поверхности раздела фаз; x – удельная скрытая теплота плавления.
Необходимо найти три неизвестные функции: температурные поля T1(x, y, z, t), T2(x, y, z, t) и положение межфазной границы R(x, y, z, t) .
Решение этой задачи позволяет определить эволюцию температурного поля в слитке и перемещение фронта кристаллизации, качественно и количественно изучить закономерности формирования непрерывного слитка и влияние на этот процесс начальных и краевых условий, отражающих технологические особенности непрерывного литья, а также теплофизических свойств разливаемых металлов и сплавов.
Предположение о выделении всей скрытой теплоты кристаллизации на границе раздела фаз ограничивает применение приближения Стефана в случае сплавов с достаточно широким интервалом кристаллизации. При затвердевании таких сплавов теплота фазового перехода выделяется в области переходной двухфазной зоны, которая в большинстве случаев занимает значительную часть слитка в процессе его формирования.
Таким образом, применение приближения Стефана может дать достаточно хорошие результаты лишь при анализе процесса затвердевания чистых металлов и сплавов с очень узким температурным интервалом кристаллизации в предположении, что условия охлаждения обеспечивают устойчивость межфазной границы.
6.2 Модель температурного поля слитка
Поле температур может быть вычислено по математической модели процесса теплопереноса при известных теплофизических параметрах разливаемой марки металла, температуре поступающего расплава, конструктивных параметрах МНЛЗ, скорости вытягивания слитка и коэффициентах теплоотдачи в ЗВО[13].
Расположим систему координат таким образом, чтобы центр координат совпадал с центром верхней грани слитка, при этом ось OX будет направлена перпендикулярно к широкой грани, а ось OZ – в направлении вектора скорости вытягивания. Схематичное расположение осей координат для зоны кристаллизатора изображено на рисунке 3.
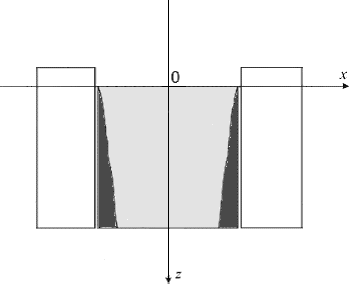
Рисунок 3 – Схема кристаллизатора
В вертикальной зоне кристаллизатора температура внутри слитка описывается уравнением

где ν – скорость вытягивания слитка; T(x, y, z, t) – температура металла; c – удельная теплоемкость; p – плотность; λ – теплопроводность.
В зоне вторичного охлаждения можно выделить криволинейный и прямолинейный участок (см. рис. 3).
Для криволинейного участка удобно использовать цилиндрическую систему координат[14]. Температура внутри слитка на криволинейном участке ЗВО описывается уравнением

где θ – угловая скорость движения слитка; φ, r – полярные координаты.
На прямолинейном участке ЗВО температура внутри слитка описывается уравнением

Положение границы раздела фаз описывается уравнением
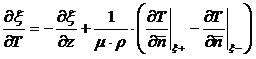
где ξ(z) – граница раздела фаз, μ – скрытая теплота кристаллизации, n – вектор нормали к границе раздела фаз.
С целью упрощения расчета температурного поля принимается допущение, что в поперечном сечении слитка распределение температур и охлаждение симметричны относительно начала координат, поэтому процесс рассматривается только в одной координатной четверти[15].
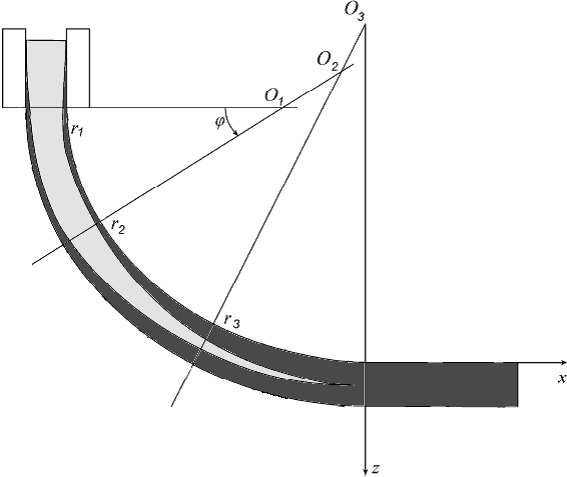
Рисунок 4 – Схема ЗВО
7. Разработка метода решения задачи
7.1 Выбор средств реализации программного обеспечения
Так как в проектируемом программном обеспечении планируется реализация трехмерной модели, возникает необходимость выбора графической библиотеки. При этом выбор ограничен лишь двумя библиотеками – OpenGL и Direct3D.
OpenGL (Open Graphics Library) – независимый от языка программирования платформонезависимый программный интерфейс для написания приложений, использующих двумерную и трёхмерную компьютерную графику. Включает более 250 функций для рисования сложных трёхмерных сцен из простых примитивов. Используется при создании компьютерных игр, систем автоматизированного проектирования, виртуальной реальности, визуализации в научных исследованиях. На платформе Windows конкурирует с Direct3D.
Direct3D – интерфейс вывода трёхмерных примитивов, являющийся частью пакета DirectX. Изначально нацелен на разработку видеоигр, однако популярен и в других областях разработки программного обеспечения. К примеру, Direct3D получил очень широкое распространение в инженерном и математическом ПО. Главным недостатком Direct3D является ориентированность на семейство операционных систем Microsoft Windows.
Для реализации данной системы был сделан выбор в пользу графической библиотеки OpenGL, т.к. ее использование, в отличие от DirectX, позволяет портировать программное обеспечение на различные платформы.
7.2 Алгоритм построения трехмерной модели
Для построения модели затвердевания непрерывного слитка в режиме реального времени необходимо выполнить следующие шаги:
- Задание начальных условий – параметров охлаждения, скорости вытягивания слитка, теплофизических параметров стали.
- Расчет начального теплового поля слитка и определение исходного положения границы раздела фаз.
- Пересчет температур слитка в точках, не лежащих рядом с границами.
- Пересчет положения границы раздела фаз.
- Пересчет температур слитка в граничных и смежных с ними точках.
- Формирование визуальной трехмерной модели слитка и вывод её на экран.
- Повторять шаги 3-6 до тех пор, пока температурное поле не стабилизируется.
Блок-схема алгоритма представлена на рисунке 5.
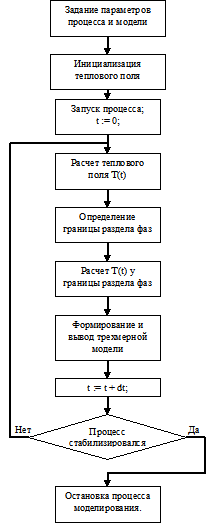
Рисунок 5 – Блок-схема алгоритма
При пересчете температур внутри слитка используется метод конечных разностей. Конечно-разностное приближение для уравнения имеет вид

где Δx, Δy, Δz – заданные размеры шага вдоль соответствующих осей координат; Tnijk – температура в (i, j, k) точке слитка в момент времени n.
Конечно-разностное приближение для уравнения имеет вид
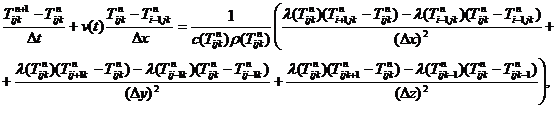
Таким образом, температура в точке (i, j, k) непрерывного слитка в момент времени n+1 вычисляется по формуле
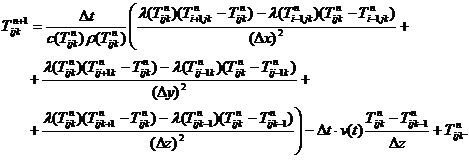
После получения температурного поля слитка в числовом виде выполняется построение трехмерной модели. Она должна наглядно отображать распределение температур в слитке, границу фазового перехода, а также предоставлять пользователю возможность просматривать слиток в произвольном поперечном сечении.
Для этого было решено представить слиток множеством полигонов, покрывающих сечения слитка и его границы. Общее количество полигонов в модели с разрешением k, l, m вдоль каждой из граней равно 2*(kl+km+lm) С целью ускорения прорисовки модели её разрешение может не соответствовать размерности массива температур.
Цвет каждого полигона определяется температурой соответствующего участка слитка. С целью визуального разделения жидкой и твердой части слитка различным диапазонам температур были поставлены в соответствие различные цветовые градиенты. Например, жидкой фазе (от температуры кристаллизации до температуры плавления) соответствует цветовой переход от красного к желтому. Твердой фазе – переход от голубого к темно-синему.
Кроме температурного поля слитка модель должна также отображать поверхность межфазовой границы. Количество полигонов в поверхности равно (k+l)*m.
8. Обзор существующих программ моделирования процесса непрерывной разливки
К настоящему времени разработан ряд программных продуктов, позволяющих моделировать тепловые процессы в машинах непрерывной разливки стали. Несмотря на это, часто возникает необходимость в разработке нового программного обеспечения, которая может быть обусловлена невозможностью модернизации существующих программ, непригодностью реализованных алгоритмов, и т.д. Ниже рассмотрены некоторые существующие программные решения.
8.1 Программное обеспечение ПроНРС-1
Система ПроНРС-1
Предназначена для моделирования процессов, протекающих в трехмерном слитке, формирующемся при непрерывной разливке стали с учетом входных теплофизических свойств стали, кристаллизатора, зон охлаждения и пространственной конфигурации МНЛЗ. Она позволяет получить трехмерные поля температур, напряжений, концентраций примесей и оптимизировать технологический процесс получения литых заготовок.
С помощью системы можно отслеживать:
- проблемы используемого технологического процесса (визуализация «болевых» точек технологического процесса и рекомендации по снижению брака);
- проблемы разрабатываемого технологического процесса на этапе проектирования (это позволит значительно сэкономить время и деньги на доводку технологической оснастки и «увидеть» дефекты на стадии проектирования);
- проблемы и варианты принципиально новых технологических решений, которые находятся на стадии обсуждения.
В компьютерной системе ПроНРС-1
развивается подход, основанный на клеточно-автоматном моделировании процесса непрерывной разливки стали, позволяющий рассчитывать и визуализировать на компьютере трехмерный процесс получения литых заготовок в реальных промышленных условиях. В основе компьютерной системы лежит собственное математическое ядро, которое может изменяться, дополняясь новыми эмпирическими зависимостями и математическими уравнениями, которые можно вводить, чтобы изменять модель и максимально учитывать природу протекающих процессов при непрерывной разливке стали.
Входными характеристиками программы являются размеры слитка, коэффициенты теплоотдачи в зонах охлаждения МНЛЗ, скорость слитка, шаг изменения по пространству и времени, характеристики свойств сталей, геометрические размеры различных зон МНЛЗ.
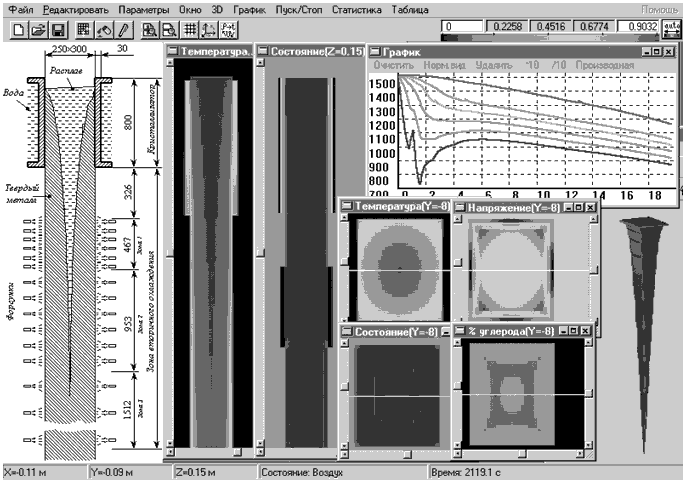
Рисунок 6 – Окно программы ПроНРС-1
Выходные характеристики – температурное поле промышленной заготовки для различных временных промежутков, длина жидкой фазы, формирующаяся в процессе кристаллизации, температура в области раскроя.
Недостатком данной системы является высокая вычислительная сложность реализованных алгоритмов и, как следствие, большая продолжительность расчета температурного поля.
8.2 Система Термовизор
Система Термовизор
предназначена для автоматического контроля процесса формирования твердой корочки слитка в кристаллизаторе машины непрерывной разливки стали и обнаружения нарушений ее однородности.
Система обеспечивает:
- автоматическую диагностику и контроль функционирования оборудования при включении системы;
- автоматическое измерение распределения температуры по стенкам кристаллизатора МНЛЗ во всех режимах работы;
- отображение на мониторе оператора основных показателей работы системы;
- автоматическую генерацию предупредительных звуковых сигналов разливщику и оператору МНЛЗ при отклонении условий разливки от нормы;
- отображение на мониторах оператора и разливщика положения точки прилипания корочки слитка к стенке кристаллизатора;
- автоматический учет наработки кристаллизатора и медных плит;
- отображение на экране монитора настраиваемых параметров кристаллизатора и системы.
Система следит за характером теплообмена между формирующимся слитком и кристаллизатором МНЛЗ. При отклонении фактических параметров теплообмена от нормы, система вырабатывает предупреждающие сигналы, извещающие оператора МНЛЗ о необходимости принятия мер, стабилизирующих процесс разливки.
Принцип действия системы состоит в непрерывном расчете распределения температурных полей на стенках кристаллизатора в процессе разливки и выявлении отклонений распределения от характерного для выбранного температурно-скоростного режима разливки. Распределение температуры измеряется с помощью датчиков температуры, равномерно распределенных по поверхности медных плит, образующих рабочую поверхность кристаллизатора МНЛЗ. Сбор измерительной информации, полученной от датчиков температуры, проводит специализированный электронный процессорный блок. В этом же блоке производится обработка полученной информации, расчет температурного поля, определяется характер нарушения, выявляется и анализируется тенденция его развития, вырабатываются сигналы предупреждения о развитии аварийной ситуации. Результаты измерений системы отображаются на мониторе, установленном на посту управления МНЛЗ изображенном на рисунке 7.
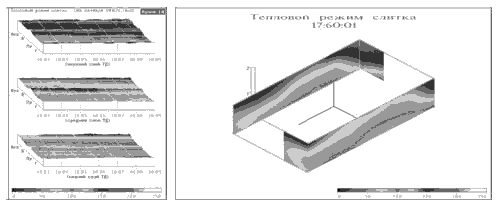
Рисунок 7 – Окно программы Термовизор
8.3 Программный комплекс Непрерывная разливка стали
Основные особенности программы:
- позволяет моделировать тепловые процессы и рассчитывать параметры кинетики затвердевания (ширина и глубина жидкой лунки, ширина двухфазной области, толщина твердой корочки);
- работает для различных типов стали и режимов охлаждения заготовки;
- предлагается для проведения многовариантных исследований при проектировании МНЛЗ и выработке оптимальных технологических режимов (схемы охлаждения, параметров заливки, конфигурации технологической оси и т.п.).
Результат работы программы представлен на рисунке 8.
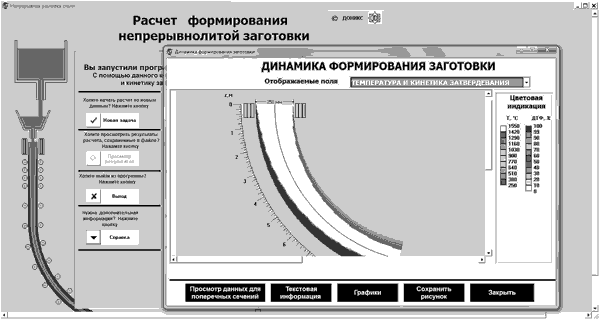
Рисунок 8 – Окно программы Непрерывная разливка стали
Выводы
В процессе выполнения дипломной работы магистра будут решены следующие задачи:
- Рассмотрен процесс непрерывной разливки стали в МНЛЗ.
- Проанализирована математическая модель процесса затвердевания слитка при непрерывной разливке.
- Рассмотрены существующие виды программного обеспечения, реализующие моделирование температурных полей в МНЛЗ.
- Сделан выбор средств реализации проектируемого программного обеспечения.
- Разработан алгоритм программы построения трехмерной модели теплового поля непрерывного слитка.
В дальнейшем результаты выполненной работы будут использованы для разработки программного продукта, в котором планируется реализовать расчет и построение графической модели температурного поля слитка в машине непрерывной разливки, опираясь на данные о теплофизических параметрах разливаемой стали, технических характеристиках МНЛЗ, режиме охлаждения и т.д.
При написании данного реферата магистерская работа еще не завершена. Окончательное завершение: декабрь 2012 года. Полный текст работы и материалы по теме могут быть получены у автора или его руководителя после указанной даты.
Список источников
- Дюдкин Д.А. Производство стали. Том 4. Непрерывная разливка металла / Д.А. Дюдкин, В.В. Кисиленко, А.Н. Смирнов. – М. : Теплотехник, 2009. – 528 с.
- Буланов Л.В. Машины непрерывного литья заготовок / Л.В. Буланов, Е.П. Парфенов, Н.А. Юровский, В.Ю. Авдонин. – Екатеринбург: Уральский центр ПР и рекламы, 2003. – 320 с.
- Соболев В.В. Теплофизика затвердевания металла при непрерывном литье / В.В. Соболев, П.М. Трефилов. – М. : Металлургия, 1988. – 160 с.
- Андерсон Д. Вычислительная гидромеханика и теплообмен / Д. Андерсон, Дж. Танненхилл, Р. Плетчер. – М. : Мир, 1990. – 384 с.
- Скворцов А.А. Теплопередача и затвердевание стали в установках непрерывной разливки / А.А. Скворцов, А.Д. Акименко. – М. : Металлургия, 1966. – 191 с.
- Григорьев В.П. Конструкции и проектирование агрегатов сталеплавильного производства / В.П. Григорьев, Ю.М. Нечкин, А.В. Егоров, Л.Е. Никольский. – М. : МИСИС, 1995. – 512 с.
- Авдонин Н.А. Математическое описание процессов кристаллизации / Авдонин Н.А. – Рига : Зинатне, 1980. – 180 с.
- Цаплин А.И. Теплофизика в металлургии: учебное пособие / Цаплин А.И. – Пермь : ПГТУ, 2008. – 230 с.
- Иванова А.А. Исследование температурных градиентов непрерывного слитка / Иванова А.А. // Труды ИПММ НАН Украины. – Донецк : ИПММ, 2008. – С. 93-102.
- Валуев Д.В. Технологический процесс разливки стали / Валуев Д.В. – Томск, ЮТИ ТПУ, 2011. – 256 с.
- Рутес В.С. Теория непрерывной разливки / В.С. Рутес, В.И. Аскольдов, В.П. Евтеев, В.Я. Генкин, М.Г. Чигринов, А.И. Манохин. – М. : Металлургия, 1971. – 296 с.
- Бровман М.Я. Непрерывная разливка металлов / Бровман М.Я. – М. : Экомет, 2007. – 484 с.
- Огурцов А.П. Непрерывное литье стали / А.П. Огурцов, А.В. Гресс. – Днепропетровск : Системные технологии, 2002. – 675 с.
- Мастрюков Б.С. Теплофизика металлургических процессов / Мастрюков Б.С. – М. : МИСИС, 1996. – 268 с.
- Смирнов А.Н. Непрерывная разливка стали [Электронный ресурс]. – Режим доступа : http://uas.su/books/mnlz/mnlz.php