Реферат за темою випускної роботи
Зміст
- Вступ
- 1. Актуальність теми
- 2. Мета і задачі дослідження
- 3. Опис області застосування
- 4. Огляд досліджень та розробок
- 4.1 Огляд міжнародних джерел
- 4.2 Огляд національних джерел
- 4.3 Огляд локальних джерел
- 5. Технологія безперервного розливання
- 5.1 Загальні відомості про процес безперервного розливання сталі
- 5.2 Класифікація МБЛЗ
- 5.3 Кристалізація безперервнолитої заготовки
- 5.4 Кристаллизатор
- 6. Математична модель процесу кристалізації безперервнолитих заготовок
- 6.1 Завдання Стефана
- 6.2 Модель температурного поля злитка
- 7. Розробка методу розв'язання задачі
- 7.1 Вибір засобів реалізації програмного забезпечення
- 7.2 Алгоритм побудови тривимірної моделі
- 8. Огляд існуючих програм моделювання процесу безперервного розливання
- 8.1 Програмне забезпечення
ПроНРС-1
- 8.2 Система
Термовізор
- 8.3 Програмний комплекс
Безперервне розливання сталі
- Висновки
- Перелік посилань
Вступ
Литтю піддаються всі метали. Але не всі метали володіють однаковими ливарними властивостями, зокрема жидкотекучестью – здатністю заповнювати ливарну форму будь-якої конфігурації. Ливарні властивості залежать головним чином від хімічного складу й структури металу. Важливе значення має температура плавлення. Метали з низькою температурою плавлення легко піддаються промисловому литтю. Із звичайних металів найвища температура плавлення у сталі. Метали діляться на чорні і кольорові. Чорні метали – це сталь, ковкий чавун і ливарний чавун. До кольоровим відносяться всі інші метали, що не містять в значних кількостях заліза. Для лиття застосовуються, зокрема, сплави на основі міді, нікелю, алюмінію, магнію, свинцю і цинку.
Теплові процеси в лиття сталі на кожному етапі досить складні і не піддаються аналітичному рішенням за великого числа змінних, що впливають на величину перепаду температури. Експериментальний метод у вирішенні таких завдань вимагає колосальних грошових витрат, найскладнішого обладнання, вирішення питань моделювання реальних умов. Сучасний розвиток чисельних методів і продуктивності комп'ютерів робить найбільш привабливим чисельний підхід у вирішенні теплових задач для безперервного розливання[1].
1. Актуальність теми
Сучасна МБЛЗ являє собою високотехнологічний агрегат, що дозволяє практично повністю захистити метал від вторинного окислення за допомогою застосування високоякісних ізостатично пресованих вогнетривів (захисна труба, погружной стакан і пр.), забезпечити оптимальні режими гойдання (за рахунок використання гідроприводу) і автоматична підтримка рівня металу в кристалізаторі, здійснювати автоматичне запобігання проривів металу, поліпшувати якість внутрішньої структури заготовки за допомогою накладання на рідку фазу електромагнітного поля і «м'якого» обтиску заготовки з рідкою серцевиною і пр.
У цілому ж до початку XXI століття в якісному і кількісному аспектах відбулося практично повне насичення металургійних підприємств світу різного роду МБЛЗ і відповідним технологічним забезпеченням. Одним з визначальних напрямків в частині розвитку концепції безперервного розливання сталі стало скорочення обсягів інвестицій і терміну їхньої окупності, як при будівництві нових цехів, так і при реконструкції вже існуючих[2]. При цьому особлива увага приділяється зменшенню питомих витрат на виробництво металопродукції. Провідні світові виробники устаткування для безперервного розливання досягли найвищих показників для класичних МБЛЗ (разливка сляба, блюма, кола, сортової заготовки) і сконцентрували основну свою увагу на альтернативних концепціях по створенню ливарно-прокатних агрегатів для одержання плоскої продукції. Розвиток технологій і конструкцій машин для безперервного розливання сталі відбуватиметься в частині створення високоефективних виробничих модулів, які придбають гнучку технологічну зв'язок при суміщенні процесів виплавки сталі, її розливання і подальшої прокатки заготовки[3].
2. Мета і завдання дослідження
Метою дослідження є вивчення теплових процесів затвердіння сталі в машинах безперервного лиття заготовок, а також розробка алгоритму програми, що дозволяє будувати тривимірні моделі процесів теплообміну і кристалізації в злитку при безперервному розливанні сталі.
Основні завдання дослідження:
- Огляд існуючих програмних рішень.
- Вибір відповідної математичної моделі.
- Дослідження процесу безперервного розливання в МБЛЗ.
- Огляд засобів реалізації програмного забезпечення.
- Розробка алгоритму побудови тривимірної моделі злитка.
Об'єкт дослідження : процеси теплообміну і кристалізації злитка в машині безперервного лиття заготовок.
Предмет дослідження : методи розрахунку і візуалізації теплового поля безперервнолитої заготовки.
3. Опис області застосування
Безперервне розливання сталі є найважливішим технологічним етапом у виробництві металопродукції, оскільки воно забезпечує переклад стали з рідкого стану в твердий з наданням їй певної геометричної форми. Крім цього умови охолодження і затвердіння стали під час безперервного розливання значною мірою визначають високу якість металопродукції в порівнянні з консервативною системою розливання в злитки.
Використання безперервного розливання у сталеплавильному виробництві сприяє економії капіталовкладень у зв'язку з виключенням витрат на парк виливниць, спорудження цеху підготовки складів, стріпперного відділення, обтискних станів, а також забезпечує значну економію металу внаслідок зменшення обрізів, економії енергії, яка витрачалася на підігрів злитків в нагрівальних колодязях, дозволяє знизити екологічне навантаження на атмосферу, підвищити якість металопродукції, автоматизувати процес лиття та поліпшити умови роботи обслуговуючого персоналу.
Конструктивні рішення, використовувані при створенні машин безперервного розливання, містять в собі знання з цілого ряду дисциплін в галузі металургії, матеріалознавства, теорії затвердіння, електротехніки, гідродинаміки, теплофізики, теорії вимірювань та автоматичних систем управління та інших. Такий комплексний підхід не має аналогів при створенні високоефективних агрегатів і машин для технологічних схем виробництва чавуну і сталі.
Технологічний процес і машини безперервного розливання сталі постійно розвиваються і удосконалюються, що розширює сферу їх застосування і створює передумови для трансформації сталеплавильного переділу в цілому. Рівень ефективності використання технологій безперервного розливання сталі враховується при створенні нових виробництв і модернізації діючих. У свою чергу це стимулює подальший розвиток конструкцій машин безперервного розливання сталі, забезпечуючи більшу привабливість їх дизайну та конкурентоспроможність[4].
Незважаючи на деякі незначні відмінності, основні технологічні і конструктивні особливості МБЛЗ досить добре вивчені і розроблені. Подальший їх розвиток і вдосконалення досягається за рахунок забезпечення високої гнучкості і функціональності машин безперервного лиття заготовок (МБЛЗ), включаючи поєднання процесів лиття і прокатки.
4. Огляд досліджень та розробок
Процес затвердіння стали є важливою частиною металургійної промисловості. Даний процес є широко дослідженим вченими з різних кінців світу. Дослідження процесу затвердіння сталі тривають і сьогодні.
4.1 Огляд міжнародних джерел
Сталь – не винахід Нового часу. Спосіб її отримання був відомий вже 1000 років тому. Однак до XIX ст. сталь практично не використовувалась. Оскільки її виробництво було занадто складним і дорогим. Швидким і доступним воно стало лише після того, як Генрі Бессемер винайшов в 1856 р. названий його ім'ям конвертер. Зазнавши ряд істотних змін, цей метод став сьогодні основним у чорній металургії.
Вміст вуглецю та інших небажаних домішок знижується так званим фрішеваннням. Для цього чавун необхідно знову нагріти до рідкого стану. З 1784 р. це робиться в пудлінговій печі, нагрівається кам'яним углем. Чавун плавлять на поду до тістоподібного стану, постійно помішуючи металевими штангами для збільшення доступу кісторода. Бессемер удосконалив цей процес, побудувавши доменну піч: крізь масу бідного фосфором чавуну продуваєтся стиснене повітря, сприяючи процесам окислення. Конвертор Бессемера видавав за 20 хвилин стільки ж сталі, скільки пудлінгова піч за цілий день. На подібному принципі заснований і винайдений в 1864 р. мартенівський процес. Пізніше з'явилися кисневі конвертери і електричні печі для виплавки сталі.
У 1742 р. Бенджамін Хантсман почав виплавляти сталь не у відкритій печі з деревним вугіллям, а в нагріваємому тиглі.
Завдяки французькому металургу П'єру Мартену, який в 1865 році запатентував піч для виплавки сталі нового зразка, у виробництві цього металу стало можливим використовувати лом, якого на планеті до того часу накопичилося величезна кількість.
Однак головна революція в сталеплавильному виробництві сталася в 1865 році, коли французи – батько і син П'єр і Еміль Мартены – використовували для одержання сталі газову піч, побудовану за кресленнями німецьких інженерів братів Вільгельма та Фрідріха Сіменс. У ній, завдяки підігріву газу та повітря, в особливих камерах з вогнетривкої насадкою досягалася така висока температура, що сталь у ванні печі переходила вже не в тістоподібної, як в пудлінговий печі, а в рідкий стан. Її можна було заливати в ковші і форми, виготовляти злитки і прокатувати їх в рейки, балки, будівельні профілі, листи[5]. Крім того, з'явилася можливість використовувати величезні кількості залізного брухту, що скупчився за довгі роки на металургійних і машинобудівних заводах.
У 1878 р. Сідні Гілкріст Томас винайшов «томасовський процес» для Вилучення фосфорних домішок з залізної руди в процесі плавки.
У 1952 р. в Австрії почав роботу перший в світі сталеливарний завод на основі ЛД–процесу. Наявні в чавуні домішки видаляються в такому конвертері продувкою технічним киснем.
Конкурент у конвертерних плавок сьогодні один – це електроплавка сталі, яка займає близько 30 відсотків світового виробництва головного металу важкої промисловості. Виплавка сталі в електропечах заснована на використанні електроенергії для нагріву металу.
4.2 Огляд національних джерел
Микола Тимофійович Гудцов, найбільший радянський вчений–металознавець, фахівець в області будови, властивостей, термічної обробки і легування стали, академік АН СРСР (1939), заслужений діяч науки і техніки РРФСР. Поряд з іншими видатними металургами і металознавцями старшого покоління – А.А. Байков, І.П. Бардін, С.С. Штейнберг, Н.А. Мінкевич, А.Л. Бабошин, А.М. Бочвар і інші. Гудцов був провідним вченим першої половини XX століття в розвитку науки про будову і властивості металів.
Коли в 1936 році радянський інженер Микола Іларіонович Мозговой вперше використовував для продувки чавуну в конвертері кисень, перспективи конвертерної виплавки сталі стали куди реалістичнішими. Метал, одержуваний киснево–конвертерним процесом, за якістю став рівноцінний мартенівської сталі, собівартість виплавки знизилася майже на чверть, серйозно зросла і продуктивність конвертерних виробництв[6].
Раузін Я.Р. працюючи з 1953 року завідувачем Лабораторією випробувань матеріалів і конструкцій Інституту Залізничного Транспорту СРСР займався дослідженнями в галузі підвищення якості, зокрема, підшипникової сталі, і поліпшення технології термічної обробки високохромистого і високовуглецевої сталі. Я.Р. Раузін займався розробкою нових методів випробувань металів на контактну витривалість, ударну в'язкість, натурних ударних випробувань при низьких температурах. Протягом багатьох років досліджував механізми початкових стадій пластичної деформації, відстоюючи гіпотезу про вирішальну роль ротаційних переміщень. Останні роботи Я.Р. Раузіна присвячені методам оцінки конструктивної міцності сталі і вибору способів підвищення міцності сталі.
Дослідження Раузіна з'явилися теоретичною основою для розвитку і широкого використання промисловістю СРСР прогресивних методів термічного зміцнення підшипникових, рейкових, інструментальних і конструкційних сталей, відіграли важливу роль в перекладі рухомого складу залізничного транспорту СРСР на роликові підшипники.
Левову частку у вивчення стали вніс Акімов Георгій Володимирович. Після виходу в світ в 1940 році монографії «Теорія і методи дослідження корозії металів» та підручника «Основи вчення про корозію і захист металів» почалася ціла серія робіт в області теоретичних і експериментальних досліджень корозії металів. З цими роботами пов'язане створення мережі корозійних станцій в представницьких кліматичних зонах країни – Дальні Зеленці, Звенигород, Владивосток, Батумі. Теорія структурної корозії і теорія багатоелектродних систем, створені Г.В. Акімовим, знайшли широке визнання в СРСР і за кордоном. Його роботи в області пасивності ознаменувалися відкриттям явища перепассіваціі. Акімов автор понад 250 наукових праць з проблем корозії металів.
4.3 Огляд локальних джерел
У Донецькому національному технічному університеті (ДонНТУ) спільно з НУО Донікс
С.П. Еронько, д.т.н, А.Ю. Цупрун, С.А. Бедарев, Д.А. Яковлєв, Є.П. Потапов, Г.С. Романова
та ін ведуть розробку шиберних пристроїв для технологічних переливів стали. Ними були розроблені і реалізовані нові шиберні системи, на котрорие вже отримані патенти.
Велику частку досліджень в області сталеплавленія зробив доктор технічних наук, доцент і завідувач кафедри Смирнов Євген Миколайович. Він є автором 140 наукових статей, 20 патентів і авторських свідоцтв на винаходи, а також співавтором 20 навчально–методичних посібників та методичних вказівок.
5. Технологія безперервного розливання
5.1 Загальні відомості про процес безперервного розливання сталі
Машини безперервного розливання сталі – системи, які забезпечують отримання готової заготовки з рідкої сталі. При використанні МБЛЗ сталь з сталерозливних ковша надходить у проміжний ківш, а з нього в кристалізатор. У кристалізаторі утворюється оболонка, заповнена рідкої сталлю по формі і перетину, відповідальному готової заготівлі. Частково затверділа заготівка за допомогою транспортуючої системи – тянущей кліті надходить в зону вторинного охолодження, де відбувається повне затвердіння заготовок[7]. Застиглий злиток розрізається на мірні довжини і готові заготовки за допомогою транспортних засобів направляються в прокатний цех або на склад.
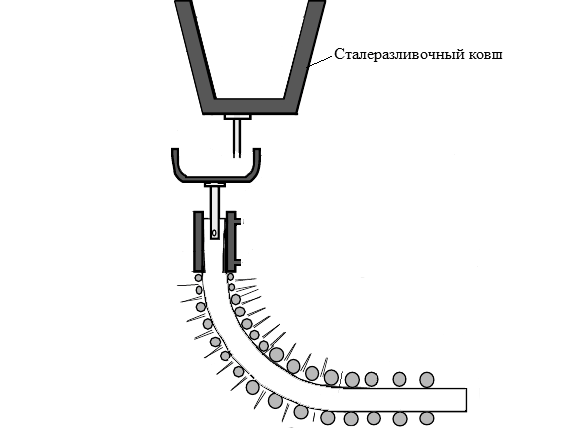
Малюнок 1 – Схема безперервного розливання в МБЛЗ
(Анімація: 6 кадрів, 7 циклів повторення, 48 кілобайт)
При підготовці МБЛЗ до розливання у кожному кристалізаторі за допомогою спеціального пристрою – затравки – влаштовується суцільне дно. Верхній кінець затравки, що має пази, вводиться в кристалізатор, її протилежний кінець знаходиться в зачепленні з тягнучим пристроєм. При наповненні внутрішньої порожнини кристалізатора металом починається процес руху затравки вниз. При цьому швидкість витяжки заготовки визначається товщиною і механічною міцністю твердої скоринки заготовки на виході з кристалізатора, яка необхідна для запобігання проривів рідкого металу по ходу розливання.
Для зменшення тертя між кіркою твердого металу і стінками кристалізатора, запобігання змочування стінка кристалізатора рідкої сталлю і створення нейтральної або відновної атмосфери, на поверхні металу в кристалізаторі вводять тверду або рідку змазку у вигляді різних масел, вуглеводнів або теплоізолюючих шлакових сумішей. У процесі розливання кристалізатор здійснює зворотно–поступальні рухи з певною частотою і амплітудою, що запобігає прилипання твердої скоринки заготовки до поверхні кристалізатора. Рівень металу в кристалізаторі підтримується постійним, що забезпечує підвищення якості поверхні заготовки і стабілізує процес лиття. Для утворення міцної оболонки – кірки металу стінки кристалізатора виготовляються з матеріалу, що володіє високою теплопровідністю, і інтенсивно охолоджуються водою[8].
З кристалізатора частково затверділий злиток потрапляє в зону вторинного охолодження (ЗВО), яка складається з опорних елементів і пристроїв, що забезпечують охолодження злитка. Опорні елементи повинні запобігати деформацію оболонки злитка і спотворення її форми. Охолодження здійснюється зазвичай зрошенням поверхні злитка водою або водоповітряної сумішшю, розпороли спеціальними форсунками, які встановлені по ходу руху заготовки. Витрата води залежить від разливаемой марки стали і швидкості витягування злитка.
Після того як повністю затверділий злиток в місці з'єднання з затравкою виходить з тягнучого пристрою, затравка від'єднується від злитка і забирається спеціальним механізмом, а злиток надходить у пристрій для різання. По закінченні розливання залишки злитка виводяться з машини, прибирається проміжний ківш, проводяться контроль і настройка дії механізмів і системи охолодження, потім знову вводиться затравка.
Таким чином, до основних функціональних елементів МБЛЗ можна віднести:
- Сталерозливних ківш – забезпечує транспортування сталі від сталеплавильного агрегату до МБЛЗ, доведення сталі по хімічному складу і температурі і перелив у проміжний ківш.
- Проміжний ківш (промковша) – забезпечує надходження металу в кристалізатор з певною витратою добре організованої струменем, дозволяє розливати сталь в кілька кристалізаторів одночасно і здійснювати серійну разливку при зміні сталерозливних ковшів без припинення і зниження швидкості розливання.
- Кристаллизатор – призначений для прийому рідкого металу, формування злитка заданого перерізу та первинного його охолодження (виконується з міді і охолоджується в процесі розливання водою).
- Зона вторинного охолодження – дозволяє створити оптимальні умови для повного затвердіння безперервно відливати злитка, що забезпечують рівномірне охолодження заготовки (розпилення води форсунками, підтримка її геометричної форми роликами) і необхідну якість металу.
- Тягнучеправильна машина (ТПМ) – призначена для витягування литої заготовки з кристалізатора, випрямлення її на радіальних і криволінійних пристроях і подачі до механізму для різання; ТПМ забезпечує подачу затравки в кристалізатор, утримання її в кристалізаторі на час ущільнення зазорів, витягування з безперервнолитої заготівлею з кристалізатора, відділення голівки затравки від заготівлі і т.п.
- Механізм для різання заготовок – забезпечує поділ безперервнолитого металу на мірні довжини.
- Запал – призначен для утворення тимчасового «дна» в кристалізаторі перед початком розливання і подальшого витягування зі зчепленої заготівлею ТПМ.
5.2 Класифікація МБЛЗ
В даний час в експлуатації знаходиться велика різноманітність установок безперервного розливання сталі. Це обумовлено вимогами до осортименту і якості заготовок і продуктивності МБЛЗ. Всі ці різновиди класифікуються за різними ознаками[9].
За типом заготовки:
- Cлябові – відливаємі заготовки мають форму поперечного перерізу у вигляді прямокутника з співвідношенням довгої сторони до короткої 3:1 і більше.
- Блюмові – відливають заготовки у формі круга, квадрата або прямокутника з малим співвідношенням сторін; розмір сторони – 200 мм і більше.
- Сортові – заготовки аналогічні блюмовим, але мають менші розміри сторін.
За принципом роботи:
- Установки безперервного розливання – злиток ріжеться на заготовки мірної довжини, що дозволяє розливати редагування серіями.
- Установки полунепреривного лиття – довжина заготовки обумовлена ходом механізму витягування, який вибирається з міркування спрощення і здешевлення машини в даних умовах виробництва; порізка злитка, якщо це необхідно, здійснюється поза машиною.
За складом:
- Однострумні.
- Багатострумні – дозволяють збільшити продуктивність установки.
За характером руху кристалізатора:
- З нерухомим кристалізатором (горизонтальна МБЛЗ).
- З зворотно–поступальним рухом – кристалізатор визначений період рухається одночасно зі злитком або випереджаючи його, а потім повертається в початкове положення; до цього типу відносяться основна кількість установок розливання сталі.
- З кристалізатором, двигающимся зі швидкістю злитка – забезпечує відсутність ковзання оболонки злитка щодо кристалізатора і тертя між ними, що знижує ймовірність розриву оболонки при високих швидкостях розливання; до цього типу відноситься так звана роторна МБЛЗ, де швидкість розливання в 2–3 рази перевищує швидкість звичайних установок.
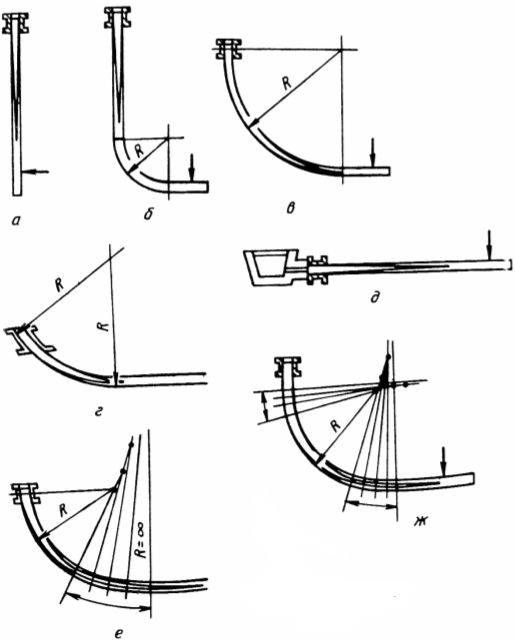
Малюнок 2 – Розташування технічних осей МБЛЗ
За розташуванням технологічній осі:
- Машини з постійною кривизною осі до закінчення затвердіння злитка.
- Машини зі змінною кривизною осі.
До машин з постійною кривизною технологічній осі ставляться:
- Вертикальні (див. малюнок 2а) та вертикальні з вигином (див. малюнок 2б), вигин злитка здійснюється після повного затвердіння для виведення технологічній осі в горизонтальне положення; мають малу швидкість розливання та низьку продуктивність установок.
- Радіальні з постійним радіусом кривизни (див. малюнок 2в) – мають більш високу швидкість розливання і продуктивність.
- Похило прямолінійні і похило–радіальні (див. малюнок 2г) – значне зниження висоти машини і ферростатіческого тиску дозволяє значно зменшити масу устаткування МБЛЗ.
- Горизонтальні (див. малюнок 2д) – технологічна вісь розташовується під кутом 7–12 градусів до горизонту.
До машин з технологічної віссю змінного радіуса відносяться:
- Криволінійні МБЛЗ з радіальним кристалізатором (див. малюнок 2е), що мають кристалізатор і частина ЗВО з постійною кривизною і ділянку змінної кривизни, де відбувається плавне випрямлення з рідкою серцевиною.
- Криволінійні МБЛЗ з вертикальним кристалізатором, в яких після невеликого вертикального ділянки ЗВО має ділянку вигину злитка, радіальний ділянку і ділянку випрямлення злитка (див. малюнок 2ж).
В даний час переважно експлуатуються радіальні і криволінійні МБЛЗ. Як правило, криволінійні МБЛЗ встановлюються в конвертерних цехах, а радіальні – в електросталеплавильних, виплавляли сталь більш складних марок. Горизонтальні МБЛЗ встановлюються в мартенівських цехах невеликої продуктивності.
Надалі в даній роботі буде розглядатися одноручьевая слябової МБЛЗ криволінійного типу з вертикальним кристалізатором.
5.3 Кристалізація безперервнолитої заготовки
У процесі затвердіння злитка при безперервному литті можна виділити два основних етапи: формування зовнішньої оболонки в кристалізаторі (зона первинного охолодження) і остаточне затвердіння в зоні вторинного охолодження[10].
5.4 Кристаллизатор
У машині безперервного лиття кристалізатор виконує функцію первинного холодильника, відвідного до 30% теплоти розплаву, і формообразователя, що забезпечує задану форму поперечного перерізу зливка.
Основним завданням кристалізатора є створення необхідних умов для інтенсивного відводу теплоти від рідкого металу. В результаті по його периметру відбувається безперервне формування весняній оболонки – скориночки майбутнього злитка. Обов'язковою умовою нормальної роботи кристалізатора є забезпечення на виході з нього оболонки з міцністю, що перевищує ферростатіческое тиск знаходиться в ній рідкого металу і зусиль витягування.
Роль кристалізатора як теплообмінника зводиться до того, що теплота від рідкої сталі через стінку кристалізатора передається охолоджуючої воді. Затвердевающий злиток являє собою посудину із змінною товщиною стінок, заповнений рідкою сталлю.
У процесі утворення оболонки і наростання її товщини відбуваються її усадка і освіта газового зазору між поверхнею оболонки злитка і стінками кристалізатора. При цьому термічний опір на шляху від рідкого металу до охолоджуючої води збільшується, а передане кількість теплоти за рахунок зменшення сумарного коефіцієнта теплопередачі знижується. Для усунення цього явища стінки кристалізатора виготовляються з урахуванням усадки металу, проте повністю позбавитися від газового зазору не вдається[11].
6. Математична модель процесу кристалізації безперервнолитих заготовок
6.1 Завдання Стефана
Загальноприйнятою моделлю, використовуваною при математичному описі різноманітних процесів кристалізації, є класична постановка задачі, запропонована Й. Стефаном у 1889 р [12 ].
Основні фізичні припущення, прийняті в класичній постановці задачі Стефана:
- Температурне поле в рідкій і твердій фазах описується рівнянням теплопровідності з відповідними теплофізичними характеристиками.
- Кристалізація відбувається на межі розділу фаз, обумовленої рівнянням
причому апріорі передбачається існування однозначної, достатньо гладкої поверхні розділу фаз. - Фазовий перехід відбувається в рівноважних умовах, тобто на межі розділу фаз задана рівноважна температура T k
- Швидкість просування кордону розділу фаз визначається умовою тепловідводу прихованої теплоти фазового переходу
де γ – питома прихована теплота фазового переходу; ρ – щільність матеріалу; νn – швидкість просування кордону розділу фаз у напрямку нормалі n; λT , λЖ – коефіцієнт теплопровідності в твердій і рідкій фазах відповідно.
Знаючи закони теплопереносу в рідкій і теплою фазах, крайові умови на границях розглянутої системи і початковий розподіл температури, необхідно визначити еволюцію температурних полів у твердій і рідкій фазах і закон переміщення в часі границі розділу фаз.
Математична модель процесу затвердіння, заснована на наближенні Стефана, може бути сформульована таким чином. Нехай система обмежена поверхнею P (x, y, z, t) .

де c – питома теплоємність; p – щільність; v – швидкість руху розплаву.
У момент часу t = 0 тверда фаза відсутня і є початковий розподіл температури в рідині T 2 (x, y, z, 0) . На поверхні P (x, y, z, t) задаються крайові умови, адекватно описують процес охолодження поверхні системи. У момент появи в процесі остигання твердої фази на межі розділу фаз ставиться умова рівності температур, що випливає з припущення ідеального теплового контакту між фазами і полягає в тому, що температури рідкої і твердої фаз однакові і рівні рівноважної температурі кристалізації

Далі передбачається, що прихована теплота кристалізації, що виділяється при русі міжфазної границі, відводиться через тверду фазу разом з рештою теплом перегріву. Тому для міжфазної границі R ставиться умова, що виражає баланс теплових потоків

де n – нормаль до поверхні розділу фаз; x – питома прихована теплота плавлення.
Необхідно знайти три невідомі функції: температурні поля T 1 (x, y, z, t) , T 2 (x, y, z, t) і положення міжфазної границі R (x, y, z, t) .
Вирішення цієї задачі дозволяє визначити еволюцію температурного поля в зливку та переміщення фронту кристалізації, якісно і кількісно вивчити закономірності формування безперервного злитка і вплив на цей процес початкових і крайових умов, що відображають технологічні особливості безперервного лиття, а також теплофізичних властивостей розливають металів і сплавів .
Припущення про виділення всій прихованої теплоти кристалізації на межі розділу фаз обмежує застосування наближення Стефана у разі сплавів з достатньо широким інтервалом кристалізації. При затвердінні таких сплавів теплота фазового переходу виділяється в області перехідної двофазної зони, яка в більшості випадків займає значну частину зливка в процесі його формування.
Таким чином, застосування наближення Стефана може дати досить добрі результати лише при аналізі процесу затвердіння чистих металів і сплавів з дуже вузьким температурним інтервалом кристалізації в припущенні, що умови охолодження забезпечують стійкість міжфазної кордону.
6.2 Модель температурного поля злитка
Поле температур може бути обчислене по математичної моделі процесу теплопереносу при відомих теплофізичних параметрах разливаемой марки металу, температурі надходить розплаву, конструктивних параметрах МБЛЗ, швидкості витягування злитка і коефіцієнтах тепловіддачі в ЗВО[13].
Розташуємо систему координат таким чином, щоб центр координат співпадав з центром верхньої грані зливка, при цьому вісь OX буде направлена перпендикулярно до широкої грані, а вісь OZ – в напрямі вектора швидкості витягування. Схематичне розташування осей координат для зони кристалізатора зображено на малюнку 3.
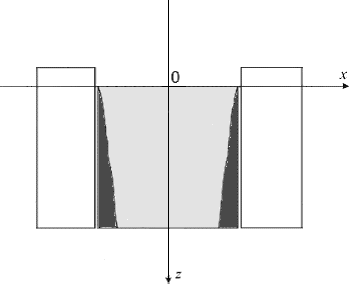
Малюнок 3 – Схема кристалізатора
У вертикальній зоні кристалізатора температура всередині злитка описується рівнянням

де ν – швидкість витягування злитка; T (x, y, z, t) – температура металу; c – питома теплоємність; p – щільність; λ – теплопровідність.
У зоні вторинного охолодження можна виділити криволінійний і прямолінійний ділянку (див. малюнок 3).
Для криволінійного ділянки зручно використовувати циліндричну систему координат[14]. Температура всередині злитка на криволінійному ділянці ЗВО описується рівнянням

де θ – кутова швидкість руху злитка; φ, r – полярні координати.
На прямолінійній ділянці ЗВО температура всередині злитка описується рівнянням

Положення границі розділу фаз описується рівнянням
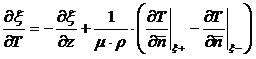
де ξ(z) – межа розділу фаз, μ – прихована теплота кристалізації, n – вектор нормалі до межі розділу фаз.
З метою спрощення розрахунку температурного поля приймається допущення, що в поперечному перерізі зливка розподіл температур і охолодження симетричні відносно початку координат, тому процес розглядається тільки в одній координатній чверті[15].
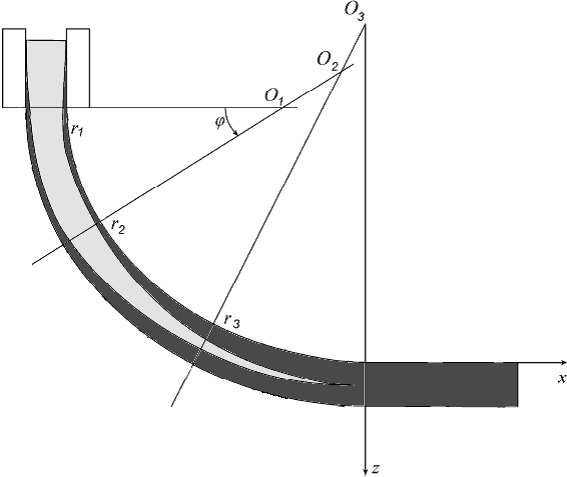
Малюнок 4 – Схема ЗВО
7. Розробка методу розв'язання задачі
7.1 Вибір засобів реалізації програмного забезпечення
Так як в проектованому програмному забезпеченні планується реалізація тривимірної моделі, виникає необхідність вибору графічної бібліотеки. При цьому вибір обмежений лише двома бібліотеками – OpenGL і Direct3D.
OpenGL (Open Graphics Library) – незалежний від мови програмування платформонезалежних програмний інтерфейс для написання додатків, що використовують двовимірну і тривимірну комп'ютерну графіку. Включає більше 250 функцій для малювання складних тривимірних сцен з простих примітивів. Використовується при створенні комп'ютерних ігор, систем автоматизованого проектування, віртуальної реальності, візуалізації в наукових дослідженнях. На платформі Windows конкурує з Direct3D.
Direct3D – інтерфейс виведення тривимірних примітивів, що є частиною пакету DirectX. Спочатку націлений на розробку відеоігор, проте популярний і в інших областях розробки програмного забезпечення. Приміром, Direct3D отримав дуже широке поширення в інженерному та математичному ПЗ. Головним недоліком Direct3D є орієнтованість на сімейство операційних систем Microsoft Windows.
Для реалізації даної системи був зроблений вибір на користь графічної бібліотеки OpenGL, тому її використання, на відміну від DirectX, дозволяє портувати програмне забезпечення на різні платформи.
7.2 Алгоритм побудови тривимірної моделі
Для побудови моделі затвердіння безперервного злитка в режимі реального часу необхідно виконати наступні кроки:
- Завдання початкових умов – параметрів охолодження, швидкості витягування злитка, теплофізичних параметрів стали.
- Розрахунок початкового теплового поля злитка і визначення вихідного положення кордону розділу фаз.
- Перерахунок температур злитка в точках, які не лежать поруч з кордонами.
- Перерахунок положення кордону розділу фаз.
- Перерахунок температур злитка в граничних та суміжних з ними точках.
- Формування візуальної тривимірної моделі злитка і виведення її на екран.
- Повторювати кроки 3–6 доти, поки температурне поле не стабілізується.
Блок–схема алгоритму представлена на малюнку 5.
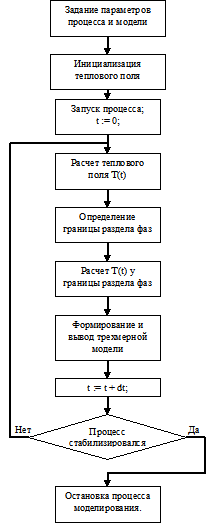
Малюнок 5 – Блок–схема алгоритму
При перерахуванні температур всередині злитка використовується метод кінцевих різниць. Звичайно–різницеве наближення для рівняння має вигляд

де Δx, Δy, Δz – задані розміри кроку вздовж відповідних осей координат; T n ijk – температура в (i, j, k) точці злитка в момент часу n.
Звичайно–різницеве наближення для рівняння має вигляд
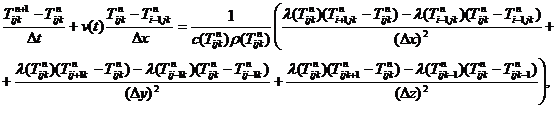
Таким чином, температура в точці (i, j, k) безперервного злитка в момент часу n +1 обчислюється за формулою
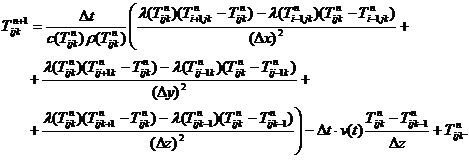
Після отримання температурного поля злитка в числовому вигляді виконується побудова тривимірної моделі. Вона повинна наочно відображати розподіл температур у зливку, кордон фазового переходу, а також надавати користувачеві можливість переглядати злиток в довільному поперечному перерізі.
Для цього було вирішено представити злиток безліччю полігонів, що покривають перетину злитка і його межі. Загальна кількість полігонів у моделі з дозволом k, l, m уздовж кожної з граней дорівнює 2 * (kl + km + lm ) З метою прискорення промальовування моделі її дозвіл може не відповідати розмірності масиву температур.
Колір кожного полігона визначається температурою відповідної ділянки злитка. З метою візуального розділення рідкої і твердої частини злитка різним діапазонам температур були поставлені у відповідність різні колірні градієнти. Наприклад, рідкій фазі (від температури кристалізації до температури плавлення) відповідає колірній перехід від червоного до жовтого. Твердій фазі – перехід від блакитного до темно-синього.
Крім температурного поля злитка модель повинна також відображати поверхню межфазовой кордону. Кількість полігонів у поверхні одно (k + l) * m .
8. Огляд існуючих програм моделювання процесу безперервного розливання
До теперішнього часу розроблено ряд програмних продуктів, що дозволяють моделювати теплові процеси в машинах безперервного розливання сталі. Незважаючи на це, часто виникає необхідність в розробці нового програмного забезпечення, яка може бути обумовлена неможливістю модернізації існуючих програм, непридатністю реалізованих алгоритмів, і т.д. Нижче розглянуті деякі існуючі програмні рішення.
8.1 Програмне забезпечення ПроНРС-1
Система ПроНРС-1
Призначена для моделювання процесів, що протікають в тривимірному зливку, що формується при безперервного розливання сталі з урахуванням вхідних теплофізичних властивостей стали, кристалізатора, зон охолодження і просторової конфігурації МБЛЗ. Вона дозволяє отримати тривимірні поля температур, напруг, концентрацій домішок і оптимізувати технологічний процес одержання литих заготовок.
За допомогою системи можна відстежувати:
- проблеми використовуваного технологічного процесу (візуалізація «больових» точок технологічного процесу і рекомендації щодо зниження браку);
- проблеми розроблюваного технологічного процесу на етапі проектування (це дозволить значно заощадити час і гроші на доведення технологічної оснастки і «побачити» дефекти на стадії проектування);
- проблеми та варіанти принципово нових технологічних рішень, які знаходяться на стадії обговорення.
У комп'ютерній системі ПроНРС-1
розвивається підхід, заснований на клітинно-автоматного моделювання процесу безперервного розливання сталі, що дозволяє розраховувати і візуалізувати на комп'ютері тривимірний процес одержання литих заготовок в реальних промислових умовах. В основі комп'ютерної системи лежить власне математичне ядро, яке може змінюватися, доповнюючись новими емпіричними залежностями і математичними рівняннями, які можна вводити, щоб змінювати модель і максимально враховувати природу процесів, що протікають при безперервного розливання сталі.
Вхідними характеристиками програми є розміри злитка, коефіцієнти тепловіддачі в зонах охолодження МБЛЗ, швидкість злитка, крок зміни по простору і часу, характеристики властивостей сталей, геометричні розміри різних зон МБЛЗ.
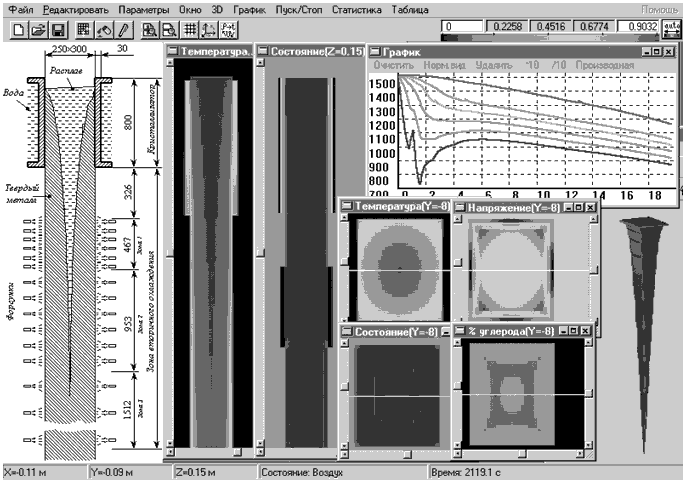
Малюнок 6 – Вікно програми ПроНРС-1
Вихідні характеристики – температурне поле промислової заготівлі для різних часових проміжків, довжина рідкої фази, що формується в процесі кристалізації, температура в області розкрою.
Недоліком даної системи є висока обчислювальна складність реалізованих алгоритмів і, як наслідок, велика тривалість розрахунку температурного поля.
8.2 Система Термовізор
Система Термовізор
призначена для автоматичного контролю процесу формування твердої скоринки злитка в кристалізаторі машини безперервного розливання сталі і виявлення порушень її однорідності.
Система забезпечує:
- автоматичну діагностику та контроль функціонування обладнання при включенні системи;
- автоматичне вимірювання розподілу температури по стінках кристалізатора МБЛЗ у всіх режимах роботи;
- відображення на моніторі оператора основних показників роботи системи;
- автоматичну генерацію попереджувальних звукових сигналів розливальник і оператору МБЛЗ при відхиленні умов розливання від норми;
- відображення на моніторах оператора і розливальник положення точки прилипання скоринки злитка до стінки кристалізатора;
- автоматичний облік напрацювання кристалізатора і мідних плит;
- відображення на екрані монітора параметрів, що настроюються кристалізатора і системи.
Система стежить за характером теплообміну між формується злитком і кристалізатором МБЛЗ. При відхиленні фактичних параметрів теплообміну від норми, система виробляє попереджувальні сигнали, що сповіщають оператора МБЛЗ про необхідність вживання заходів, що стабілізують процес розливання.
Принцип дії системи полягає в безперервному розрахунку розподілу температурних полів на стінках кристалізатора в процесі розливання та виявленні відхилень розподілу від характерного для вибраного температурно-швидкісного режиму розливки. Розподіл температури вимірюється за допомогою датчиків температури, рівномірно розподілених по поверхні мідних плит, що утворять робочу поверхню кристалізатора МБЛЗ. Збір вимірювальної інформації, отриманої від датчиків температури, проводить спеціалізований електронний процесорний блок. У цьому ж блоці проводиться обробка отриманої інформації, розрахунок температурного поля, визначається характер порушення, виявляється і аналізується тенденція його розвитку, виробляються сигнали попередження про розвиток аварійної ситуації. Результати вимірювань системи відображаються на моніторі, встановленому на посту керування МБЛЗ зображеному на малюнку 7.
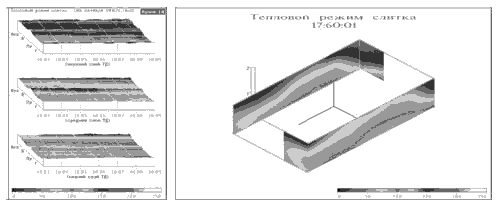
Малюнок 7 – Вікно програми термовізора
8.3 Програмний комплекс Безперервне розливання сталі
Основні особливості програми:
- дозволяє моделювати теплові процеси і розраховувати параметри кінетики затвердіння (ширина і глибина рідкої лунки, ширина двофазної області, товщина твердої скоринки);
- працює для різних типів сталі та режимів охолодження заготовки;
- пропонується для проведення багатоваріантних досліджень при проектуванні МБЛЗ і виробленню оптимальних технологічних режимів (схеми охолодження, параметрів заливки, конфігурації технологічної осі і т.п.).
Результат роботи програми представлений на малюнку 8.
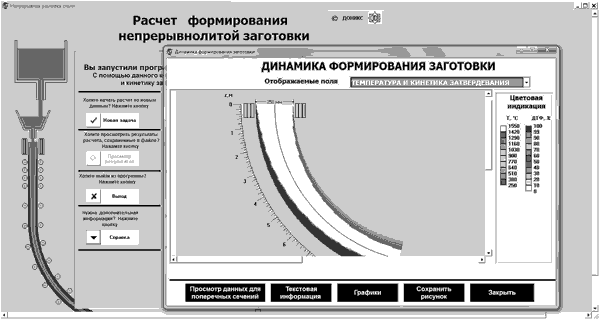
Малюнок 8 – Вікно програми Безперервне розливання сталі
Висновки
У процесі виконання дипломної работи магістра будуть вирішені наступні завдання:
- Розглянуто процес безперервного розливання сталі в МБЛЗ.
- Проаналізована математична модель процесу затвердіння злитка при безперервному розливанні.
- Розглянуто існуючі види програмного забезпечення, що реалізують моделювання температурних полів у МБЛЗ.
- Зроблено вибір засобів реалізації проектованого програмного забезпечення.
- Розроблено алгоритм програми побудови тривимірної моделі теплового поля безперервного злитка.
Надалі результати виконаної роботи будуть використані для розробки програмного продукту, в якому планується реалізувати розрахунок і побудова графічної моделі температурного поля злитка в машині безперервного розливання, спираючись на дані про теплофізичних параметрах разливаемой стали, технічних характеристиках МБЛЗ, режимі охолодження і т.д.
При написанні даного реферату магістерська робота ще не завершена. Остаточне завершення: грудень 2012 року. Повний текст роботи та матеріали по темі можуть бути отримані у автора або його керівника після зазначеної дати.
Перелік посилань
- Дюдкин Д.А. Виробництво сталі. Том 4. Безперервне розливання металу / Д.А. Дюдкин, В.В. Кисиленко, А.Н. Смирнов. – М.: Теплотехнік, 2009. – 528 с.
- Буланов Л.В. Машини безперервного лиття заготовок / Л.В. Буланов, Є.П. Парфьонов, Н.А. Юровський, В.Ю. Авдонін. – Єкатеринбург: Уральський центр ПР і реклами, 2003. – 320 с.
- Соболєв В.В. Теплофізика затвердіння металу при безперервному литті / В.В. Соболєв, П.М. Трефілов. – М.: Металургія, 1988. – 160 с.
- Андерсон Д. Обчислювальна гідромеханіка та теплообмін / Д. Андерсон, Дж. Танненхілл, Р. Плетчер. – М.: Мир, 1990. – 384 с.
- Скворцов А.А. Теплопередача і затвердіння стали в установках безперервного розливання / А.А. Скворцов, А.Д. Акименко. – М.: Металургія, 1966. – 191 с.
- Григор'єв В.П. Конструкції і проектування агрегатів сталеплавильного виробництва / В.П. Григор'єв, Ю.М. Нечкіна, А.В. Єгоров, Л.Є. Нікольський. – М.: МІСіС, 1995. – 512 с.
- Авдонін Н.А. Математичний опис процесів кристалізації / Авдонін Н.А. – Рига: Зінатне, 1980. – 180 с.
- Цаплін А.І. Теплофізика в металургії: навчальний посібник / Цаплін А.І. – Перм: ПДТУ, 2008. – 230 с.
- Іванова А.А. Дослідження температурних градієнтів безперервного злитка / Іванова А.А. / / Праці ІПММ НАН України. – Донецьк: ІПММ, 2008. – С. 93–102.
- Валуєв Д.В. Технологічний процес розливання сталі / Валуєв Д.В. – Томськ, ЮТІ ТПУ, 2011. – 256 с.
- Рутес В.С. Теорія безперервного розливання / В.С. Рутес, В.І. Аскольдів, В.П. Євтєєв, В.Я. Генкін, М.Г. Чигринов, А.І. Манохін. – М.: Металургія, 1971. – 296 с.
- Бровман М.Я. Безперервне розливання металів / Бровман М.Я. – М.: Екомет, 2007. – 484 с.
- Огурцов А.П. Безперервне лиття сталі / А.П. Огірків, А.В. Гресс. – Дніпропетровськ: Системні технології, 2002. – 675 с.
- Мастрюков Б.С. Теплофізика металургійних процесів / Мастрюков Б.С. – М.: МІСіС, 1996. – 268 с.
- Смирнов А.Н. Безперервне розливання сталі [Електронний ресурс]. – Режим доступу: http://uas.su/books/mnlz/mnlz.php