Реферат за темою випускної роботи
Зміст
- Вступ
- 1. Актуальність теми
- 2. Мета і задачі дослідження та заплановані результати
- 3. Огляд існуючих поліолефінових композицій та методів їх аналізу.
- 3.1 Аналіз існуючої тришарової поліетиленової композиції
- 3.2 Поліетилен, його властивості
- 3.3 Методи оцінки трьохшарового покриття та їх доцільність
- 3.4 Катодний захист
- 3.5 Адгезія
- 4. Результати власних досліджень та подальший розвиток теми
- Висновки
- Перелік посилань
Вступ
Транспортування нафти, газу і нафтопродуктів по трубопроводах є найбільш ефективним і безпечним способом їх транспортування на значні відстані. Цим способом доставки нафти і газу від районів їх здобичі до споживачів користуються вже більше 100 років. Довговічність і безаварійність роботи трубопроводів безпосередньо залежить від ефективності їх протикорозійного захисту. Для зведення до мінімуму ризику корозійних ушкоджень трубопроводи захищають антикорозійними покриттями і додатково засобами електрохімзахисту. При цьому ізоляційні покриття забезпечують первинний (пасивну) захист трубопроводів від корозії, виконуючи функцію дифузійного бар'єру, через який утруднюється доступ до металу коррозійноактивних агентів (води, кисню, повітря). При появі в покритті дефектів передбачається система катодного захисту трубопроводів – активний захист від корозії.
Для того, щоб захисне покриття ефективно виконувало свої функції, воно повинне задовольняти цілому ряду вимог, основними з яких є: низька влагокислородопроницаємість, високі механічні характеристики, висока і стабільна в часі адгезія покриття до сталі, стійкість до катодного відшарування, хороші діелектричні характеристики, стійкість покриття до УФ і тепловому старінню. Ізоляційні покриття повинні виконувати свої функції в широкому інтервалі температур будівництва і експлуатації трубопроводів, забезпечуючи їх захист від корозії на максимально можливий термін їх експлуатації [1].
1. Актуальність теми
Актуальність цього питання постає в тому, що з одного боку, постійно підвищується якість захисних покриттів трубопроводів, практично кожні 10 років з'являються нові ізоляційні матеріали, нові технології і устаткування для нанесення покриттів на труби в заводських і трассових умовах. З іншого боку, стають усе більш жорсткими умови будівництва і експлуатації трубопроводів (будівництво трубопроводів в умовах Крайньої Півночі, в Західному Сибіру, освоєння морських родовищ нафти і газу, глибоководне прокладення, будівництво ділянок трубопроводів методами похило-спрямованного буріння, мікротоннелірувания, експлуатація трубопроводів при температурах до 100°С і вище, та ін.) [2].
Необхідно відмітити, що в останніх 7-8 років загальний рівень протикорозійного захисту трубопроводів значно підвищився за рахунок впровадженння нових технологій, якісних ізоляційних матеріалів, широкого використання при будівництві трубопроводів труб і фасонних деталей із заводськими покриттями. Можно також стверджувати, що сучасні захисні покриття за умови виконання вимог по будівництву і укладанню трубопроводів здатні забезпечити їх безаварійну (з причини корозії) роботу на увесь період експлуатації (40-50 років і більш).
У цій роботі будуть розглянуті:
- Тришарове поліетиленове покриття, його склад. Його відмінності, переваги використання на відміну від двошарового.
- Вимоги до поліетиленової композиції покриття, види поліетилену. Поліетилен високого та низького тиску, його властивості.
- Проведена оцінка фізико-механичних властивостей поліетиленового покриття ПВТ та ПНТ в центральній заводській лабораторії ПАО ХТЗ.
2. Мета і задачі дослідження та заплановані результати
Метою дослідження є розробка поліетиленової композиції для стальних труб, яке спроможне витиримати критичні температури експлутування.
Основні задачі дослідження:
- Аналіз тришарового поліетиленового покриття. Виявлення його недоліків та переваг.
- Дослідити поліетилен низького тиску та високого тиску, епоксидну композицію та обрати адгезив для створення нового якісного покриття.
- Провести оцінку існуючих методів аналізу та технологічного вдосконалення тришарового покриття для сталевих труб.
- Оцінити фізико-механічні властивості поліетиленового покриття високого та низького тиску.
- Дати аналіз тким характеристикам покриття, як стійкість до адгезії та катодного відшарування.
- Запропонувати методи вдосконалення поліетиленової композиції.
Об'єкт дослідження: трьохшарове поліетиленове покриття.
Предмет дослідження: технологічні методи та системи вдосконалення покриття для використання в умовах Крайної Півночі.
В рамках магістерської роботи планується отримання актуальних наукових результатів по наступним напрямкам:
- Підвищені вимоги до поліолефінових композицій.
- Визначення областей застосування різних варіантів поліетиленового покриття.
- Модифікація відомих сумішей поліетиленового покриття, та подальша експлуатація найефективнішого.
3. Огляд досліджень та розробок
Оскільки трьохшарове покриття стальних труб є актуальним питанням, то на даний момент цьому питанню присвячений ряд робіт університетів нафти та газу, як відчизняних, так і закордонних. Тому, в роботі будуть використані висновки вчених, зробелні в останні декілька років.
3.1 Аналіз існуючої тришарової поліетиленової композиції
В цьому розділі приводиться опис двошарового та трьохшарового поліетиленового покриття, проводиться аналіз. Уперше одношарові поліетиленові покриття труб на основі порошкового поліетилену стали застосовуватися у кінці 50-х років минулого століття. Технологія нанесення одношарового поліетиленового покриття аналогічна технології нанесення покриттів з порошкових епоксидних фарб. Із-за низької водостійкості адгезії і стійкості до катодного відшарування одношарові поліетиленові покриття не отримали досить широкого застосування. Їм на зміну прийшли двошарові покриття з м'яким адгезійним підшаром. У конструкції такого покриття як адгезійний шар застосовувалися ізоляційні бітумно-каучукові мастики (м'які адгезиви) завтовшки 150-300 мкм, що наносяться по шару праймера, а як зовнішній удароміцний шар використовувався екструдований поліетилен завтовшки не менше 2,0-3,0 мм.
Після того, як фірмою BASF (Німеччина) був розроблений сополімер етилену і ефіру акрилової кислоти (Lucalen), який уперше був випробуваний в конструкції заводського поліетиленового покриття труб як термоплавкого полімерний клейовий підшар, в практику будівництва трубопроводів було впроваджено двошарове поліетиленове покриття з жорстким адгезійним підшаром. Пізніше був розроблений ще цілий ряд термоплавких клейових композицій на основі сополімерів етилену і вінілацетата, етилену і акрилата. Двошарові поліетиленові покриття отримали дуже широке застосування і на довгі роки стали основними заводськими покриттями труб. Конструктивно двошарове поліетиленове покриття складається з адгезійного підшару на основі термоплавкої полімерної композиції завтовшки 250-400 мкм і зовнішнього поліетиленового шару завтовшки від 1,6 мм до 3,0 мм. Залежно від діаметрів труб загальна товщина покриття складає не менше 2,0 (для труб діаметром до 273 мм включно) і не менше 3,0 мм (для труб діаметром 1020 мм і вище). Для нанесення двошарових поліетиленових покриттів застосовуються як вітчизняні, так і імпортні ізоляційні матеріали (термоплавкі композиції на основі сополімерів – для нанесення адгезійного шару і композиції термосвітлостабілізованного поліетилену – для нанесення зовнішнього шару). З метою підвищення стійкості двошарових поліетиленових покриттів до дії води і стійкості до катодного відшарування при підвищених температурах проводиться обробка поверхні очищених труб (пасивація) розчином хромату. При правильному підборі ізоляційних матеріалів двошарове поліетиленове покриття має досить високі показники властивостей і відповідає технічним вимогам, що пред'являються до заводських покриттів труб. Воно здатне забезпечити захист трубопроводів від корозії на строк до 30 років і вище [3].
Уперше конструкція тришарового поліетиленового покриття була розроблена і запатентована фахівцями фірми BASF і Mannesmann, Німеччина 20 років тому. Тришарове покриття типу MAPEK складається з шару епоксидного праймера завтовшки від 60 до 200 мкм, адгезійного підклеюючого шару завтовшки від 200 до 500 мкм і зовнішнього поліетиленового шару завтовшки від 1,5 до 3,0 мм. Залежно від діаметрів труб і призначення трубопроводів загальна товщина тришарового покриття може змінюватися від 2,0 до 3,5 мм. На сьогодні тришарове поліетиленове покриття є найбільш ефективним зовнішнім антикорозійним покриттям труб заводського нанесення. Цей тип покриття широко застосовується у всьому світі для антикорозійного захисту трубопроводів різного призначення (магістральні газопроводи, нафтопроводи, продуктопроводи, трубопроводи комунального призначення та ін.). При правильному виборі системи ізоляційних матеріалів, при строгому дотриманні технологічних режимів очищення і зовнішньої ізоляції труб розрахунковий термін служби тришарового покриття при температурах експлуатації до плюс 60°С складає не менше 50 років [4]. У 1999 році з використанням устаткування фірми Bradero Price, США на заводі був освоєний процес заводської ізоляції труб діаметром 168-1420 мм тришаровим покриттям на основі ізоляційних матеріалів фірм DuPont і NOVA, Канада. У 2000 році на базі технологічного устаткування постачання фірми Selmers, Нідерланди була впроваджена технологія тришарової поліетиленової ізоляції труб діаметром до 1420 мм була освоєна на Харцизському трубному заводі, Україна. Харцизський трубний завод виробляє широкий спектр сталевих експандованних труб електрозварювань діаметром 508-1422 мм (20-56 дюймів) з товщиною стінки 6,0-40,0 мм, розрахованих на робочий тиск до 9,8 МПа для газонафтопроводів, теплових електростанцій і теплових мереж, загального призначення [5]. Зростання світового видобутку нафти і газу в 2012 році буде нерозривно пов'язано з ускладненням умов експлуатації родовищ: освоєнням шельфових ділянок здобичі вуглеводнів і підвищенням корозійної активності засобів, що транспортуються. Постійне вивчення кон'юнктури ринку вже зараз дає можливість Харцизському трубному заводу вести активну роботу по освоєнню нових перспективних видів продукції.
Після впровадження на вітчизняних підприємствах промислових виробництв по тришаровій ізоляції труб, ВНІІСТом за дорученням АК Транснафта і Держміськтехнагляду РФ були проведені комплексні випробування і сертифікація заводських тришарових поліетиленових покриттів труб на відповідність їх вимогам Технічних умов і ГОСТ Р 51164 Трубопроводи сталеві магістральні. Загальні вимоги до захисту від корозії [1]. На сьогодні Центром базової ізоляції ВНІІСТа випробувано вже більше 10 різних систем тришарових покриттів труб. Оцінка характеристик покриття проводилася по 15 показникам властивостей, включаючи: діелектричну сплошність, адгезію покриття до сталі, водостійкість адгезії, стійкість до катодного відшарування, ударну міцність в діапазоні температур, стійкість до розтріскування, до ультрафіолетового і термічного старіння та ін. Незважаючи на досить високі вимоги російського стандарту ГОСТ Р 51164, що значною мірою перевищують вимоги німецького стандарту ВГМ 30670 і французького стандарту МРА 49710, декілька систем тришарових покриттів витримали комплексні випробування і були рекомендовані до практичного застосування [6].
Найкращі результати були отримані при випробуванні заводських тришарових систем з використанням порошкових епоксидних фарб фірм BASF, 3 M, BS Coating, Akzo Nobel, композицій адгезиву і поліетилену виробництва Borealis, Basell, Atofina, UBE.
Необхідно відмітити, що до теперішнього часу не сертифікована жодна система тришарового покриття на базі вітчизняних ізоляційних матеріалів. Проблема в тому, що українські заводи-виготівники ізоляційних матеріалів працюють кожен сам по собі, а для розробки системи покриття потрібний комплексний підхід. Для певного епоксидного праймера вимагається саме той, що поєднується з праймером клейового підшарку і поліетилену. Це необхідно для того, щоб при пошаровому нанесенні покриття між епоксидним праймером і клейовим підшаром могли утворюватися хімічні зв'язки, стійкі до дії води, підвищених температур і до тривалої дії электро-химической захисту. Крім того, проведені ВНІІСТом випробування різних вітчизняних композицій поліетилену, які застосовуються на українських заводах для двошарової ізоляції труб, показали, що ці композиції не витримують вимог ГОСТ Р 51164 за показниками: стійкість до розтріскування під напругою, термостабільність, еластичність при мінусових температурах [7].
Має відбутися досить велика робота по вибору і доопрацюванню вітчизняних ізоляційних матеріалів, по розробці системи тришарового поліетиленового покриття труб, яка могла б конкурувати з імпортними системами покриттів. Тож, саме цьому останнім часом на конференціях, на засіданнях науково-технічних рад, у вітчизняних спеціалізованих журналах ведуться дискусії про переваги і недоліки різних систем двошарових і тришарових поліетиленових покриттів труб. За тих, що пройшли 5-6 років ВНІІСТом були проведені численні випробування двошарових поліетиленових покриттів труб різних українських заводів-виготівників.
Після 1000 ч випробувань у воді при температурах 20, 40 і 60°С адгезія тришарового покриття до сталі залишається на рівні початкових значень. У разі двошарового покриття спостерігається різке зниження адгезії покриття до сталі після випробувань у воді при температурі 60°С. Частенько при підвищених температурах випробувань відбувається повне відшарування двошарового покриття від сталі. При температурі плюс 60°С площа катодного відшарування тришарового покриття в 5-10 разів менше площі відшарування двошарового покриття. В деяких випадках, коли при нанесенні двошарового покриття не здійснюється обробка поверхні труб розчином хромату, внаслідок катодної поляризації відбувається повне відшарування покриття від сталі.
У зв'язку з тим, що в системах тришарових покриттів використовується, як правило, поліетилен високої щільності або бімодальний поліетилен, а для двошарових покриттів, застосовується поліетилен низької щільності ударна міцність тришарових покриттів в 2-3 рази перевищує ударну міцність двошарових покриттів. При товщині покриття близько 3 мм, ударна міцність тришарових покриттів складає 50-60 Дж, тоді як у разі двошарового покриття міцність при ударі не перевищує 20 Дж.
Тришарові покриття на основі бімодального поліетилену і поліетилену високої щільності характеризуються підвищеною механічною міцністю. Міцність при розтягуванні відшарованого покриття при 20°С при цьому складає від 22 до 28 МПа, в той час, як цей показник для двошарового покриття на основі поліетилену низької щільності кабельних марок змінюється в межах від 11 до 13,5 МПа. Відносне подовження при розриві при температурі мінус 40°С для вітчизняних марок поліетилену 102-10К, 153-10К не перевищує значень 40 до 60%, тоді як для імпортних марок поліетилену високої щільності цей показник складає 90-100%, а для бімодального поліетилену достигабельного поліетилену марок 102-10°К і 153-10°К стійкість до розтріскування складає 200-500 годин. У теж час стійкість до розтріскування сертифікованих ВНІІСТом імпортних поліетиленових композицій, вживаних в системах тришарових покриттів труб, перевищує 2000 г., а у разі бімодального поліетилену досягає значень 10 000 ч [8].
Таким чином, проведені ВНІІСТом комплексні випробування двошарових і тришарових поліетиленових покриттів труб, вироблюваних на українських підприємствах, свідчать про безумовні переваги тришарових систем покриттів на основі сучасних ізоляційних матеріалів. Використання таких покриттів дозволяє значною мірою підвищити надійність і ефективність протикорозійного захисту трубопроводів і збільшити тривалість терміну їх експлуатації.
3.2 Поліетилен, його властивості
Поліетилен – найдешевший полімер, що займає перше місце у світовому виробництві полеолефініов. Цей унікальний матеріал поєднує в собі цінні властивості і здатність перероблятися усіма високопродуктивними методами, існуючими для термопластів.
Поліетилен – це пластикат, що має хороші діелектричні властивості, підвищену ударостійкість, невелику поглинювальну здатність. Не ламається, володіє низькою газо- і паропроніцаємістю. Фізіологічно нейтральний, не має запаху. Поліетилен не сприйнятливий до лугів будь-якої концентрації, розчинів будь-яких солей, карбонових, плавиковою і концентрованою соляною кислотам. Стійкий до масла, овочевих соків, алкоголю, води, бензину. Руйнується азотною кислотою, газоподібними і рідким фтором і хлором. Не розчиняється, а тільки небагато набрякає в органічних розчинниках. Стійок до нагрівання у вакуумі, але руйнується на повітрі при нагріванні від вісімдесяти градусів.
Поліетилен морозостійкий (до сімдесяти градусів). Під дією ультрафіолетових променів – піддається фотодеструкції. Легко модифікується. Додаткове хлорування, сульфування, бромування або фторування надають поліетилену каучуко-подобні властивості, покращують хімічну і теплову стійкість. Сополімеризація з іншими полеолефінами або полярними мономерами підвищує його прозорість, еластичність, адгезійні характеристики, а також стійкість до розтріскування. Змішування поліетилену з іншими полімерними матеріалами покращує інші його фізичні властивості. Поліетилен нешкідливий для людини, з нього не виділяються небезпечні для його здоров'я речовини. Вид молекули поліетилену приведено на рисунку 1.
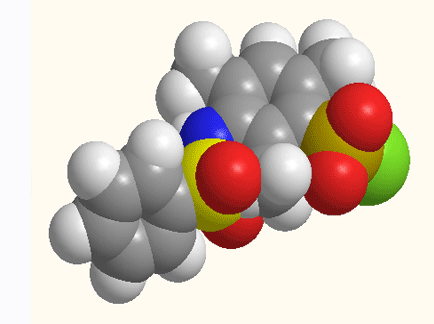
Рисунок 1 – Молекула поліетилену
(анимация: 6 кадров, 5 циклов повторения, 150 килобайт)
(xi – вхідні сигнали, yi – біти коду стану, zi – вихідні сигнали)
3.3 Методи оцінки трьохшарового покриття та їх доцільність
Показниками, за якими оцінюють якість трьохшарового поліетиленового покриття, є:
- висока корозійна стійкість;
- високий ступінь зціплення с матеріалом-основою;
- висока удароміцність та стійкість до дефомуючого впливу при транспортуванні та прокладанні труб;
- високий електричний опір, необхідний для антикорозійного захисту та запобігання витоків захисного струму труб;
- стійкість до катодного відшарування, викликаному дією катодного поляризації;
- стабільність у часі фізико-механічних і хімічних властивостей покриття;
- добрі діелектричні показники;
- стійкість до УФ-випромінювання;
- стійкість до теплового старіння;
- широкий діапазон експлуатаційних температур (навколишнього середовища та середовища, що перекачується);
- тривалий термін ефективної експлуатації.
Головне ж, від чого залежить надійність і безаварійність трубопроводів будь-якого призначення, є ряд чинників, до яких можна віднести, по-перше, кліматичні умови місцевості, в якій вони прокладаються, по-друге, умови експлуатації (хімічний склад рідини, що транспортується, її температуру, тиск, спосіб прокладки трубопроводу (прихований або відкритий), сумісність з іншими елементами трубопроводу) і, по-третє, ефективність антикорозійного захисту. Щоб звести до мінімуму ризики передчасного виходу трубопроводу з ладу, його необхідно захистити за допомогою антикорозійних покриттів (первинний або пасивний захист) та засобів електрохімічного захисту. Захисне антикорозійне покриття виконує бар'єрну функцію, ізолюючу метал труби від взаємодії з корозійним середовищем – вологою, киснем повітря та ін. Система катодного захисту трубопроводів (активний захист) призначена для запобігання корозійного руйнування металу труби при пошкодженнях покриття[9].
3.4 Катодний захист
Зрушення потенціалу металу може бути здійснений за допомогою зовнішнього джерела постійного струму (станції катодного захисту) або з'єднанням з іншим металом, більш електронегативний за своїм електродному потенціалу (так званий протекторний анод). При цьому поверхня захищається зразка (деталі конструкції) стає еквіпотенційної і на всіх її ділянках протікають тільки катодні процеси, а анодні, що обумовлюють корозію, перенесені на допоміжні електроди. Якщо, проте, зсув потенціалу в негативну сторону перевищить певне значення, можлива так звана перезащіта, пов'язана з виділенням водню, зміною складу приелектродних шару та іншими явищами, що може призвести до прискорення корозії. Катодний захист, як правило, поєднують із нанесенням захисних покриттів; необхідно враховувати можливість відшаровування покриття.
Особливо важливе використання катодного захисту для стаціонарних нафтогазопромислових споруд, трубопроводів і сховищ до них на континентальному шельфі. Подібні споруди не можуть бути введені в сухий док для відновлення захисного покриття, тому електрохімічний захист є основним методом запобігання корозії. Морських нафтопромислових вишка, як правило, забезпечена у своїй підводній частині протекторними анодами (на одну вишку доводиться до 10-ти і більше протекторних сплавів).
3.5 Адгезія
Поміряти рівноважну роботу адгезії між полімером і твердим тілом в переважній більшості випадків не представляється можливим через дуже високої в'язкості полімерів. Тому стосовно до полімерам визначають не адгезію, а адгезійну міцність. Вона вимірюється як питома робота або питома сила руйнування зв'язку між адгезивом і субстратом. З практичної точки зору при використанні полімерів в якості клеїв або матриці для ПКМ важлива не робота адгезії, а механічна міцність зв'язку полімеру з іншою поверхнею. Однак при механічному руйнуванні адгезійного з'єднання робота, витрачається на відшаровування двох тіл, йде не тільки на подолання адгезії, але і на інші побічні процеси (деформація тіла, подолання сил механічних зачеплень, тощо). Тому не тільки величини, але і поняття адгезії і адгезійної міцності не тотожні, і їх потрібно чітко розмежовувати [10].
Методів визначення адгезійної міцності дуже багато. Їх вибір залежить від того, який навантаженні буде піддаватися адгезионное з'єднання при експлуатації. Але з цих способів можна виділити три найбільш часто використовуваних – це адгезійна міцність при нормальному відриві (рис 3. а), при відшаруванні (рис 3. б) і при зсуві (рис 3.в).
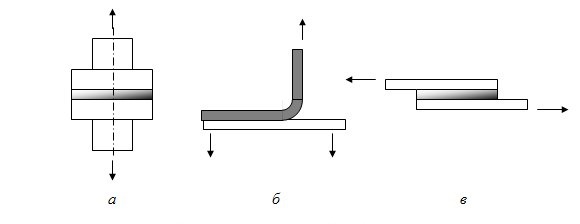
Рисунок 2 – Види адгезійної міцності
Отже, одними з головних показників якості трьохшарового покриття є: стійкість до катодного відшаровання, адгезія покриття та фізико-механічні характеристики. Міцність покриття повинна бути достатньою для того, щоб без наслідків перенести механічні удари і деформації, можливі при транспортуванні і підземному прокладанні труб. Система катодного захисту трубопроводів (активний захист) призначена для запобігання корозійного руйнування металу труби при пошкодженнях покриття. Знання величини адгезійної міцності між субстанціями виходячи з їх хімічної будови, структури і умов утворення контакту між ними дають можливість прогнозувати срок служби покриття та можливі умови експлуатаціі.
4. Результати досліджень та подальший розвиток теми
Експеримент №1 – Визначення відносного подовження і міцності при розриві.
Властивості вже готових виробів з поліетилену істотно залежать від режиму їх виготовлення (рівномірності і швидкості охолодження) і, звичайно, умов їх експлуатації (тиску, температури, тривалості дії навантаження і т.д.). Тому в лабораторії ЦЗЛ аналізу піддаватиметься поліетиленове покриття, перероблене в екструдері. Буде визначено: чи відповідають физико-механічні властивості поліетилену ГОСТу виробника після його переробки в екструдері і як він поводитиметься в експлуатації в якості покриття ( при температурі в 25 градусів і навантаженні в 700 Мпа). Також буде визначено, чи можно використовувати поліетилен для нанесення покриття спеціального призначення. Згідно ТУ У 27.2–00191135–009:2005 експеримент буде поширюватися на труби стальні електрозварювальні прямошовні експандовані звичайного і холодостійкого виконання діаметром від 530 до 120 мм із зовнішнім тришаровим поліетиленовим покриттям, призначені для будівництва магістральних нафтопроводів підземного і підводного прокладення [11].
В результаті експерименту видно, що міцність для матеріалу – полиетилен високої щільності низького тиску складає 26,727 мПА, а для полиетилена низької щільності високого тиску – 17,04 мПА. Тобто у поліетилена високої щільності міцність на 36,45 % вища, ніж у поліетилена низької щільності.
При виборі поліетиленової композиції для основного шару зовнішнього тришарового поліетиленового покриття газонафтопровідних труб виробництва ПАО Харцизький трубний завод, виходячи з цього експерименту поліетилен низької щільності не проходить по технічних вимогах. Його можна використовувати тільки для нанесення покриття нормального, теплостійкого і морозостійкого покриття. Поліетиленова композиція для нанесення покриття спеціального виконання з поліетилену високої щільності проходить за прочностними характеристиками. Згідно з нормою по ТУ У 27.2 – 001911135 – 009:2005 міцність при розтягуванні відшарованого покриття повинна складати для 18 мПА для спеціального виконання, і 12 мПА для звичайного [12].
Погані прочностні характеристики поліетилену високого тиску можна пояснити його молекулярною структурою і фізико-хімічними властивостями зокрема. Особливістю структури поліетилену ПВТ є велика кількість довгих і коротких відгалужень, що не дозволяють молекулам з високою молекулярною масою створювати кристалічну структуру. Зв'язки тому між ними не сильні, а це говорити про тих, що поліетилен має невисоку стійкість на розрив і підвищену пластичність, а також високу плинність в розплаві.
Враховуючи результати експерименту № 1, поліетилен для нанесення антикорозійного захисного покриття спеціального типу, вибриається високої щільності марки HE 3450. Наступною вимогою до виготовлення покриття спеціального призначення, тобто для використання в умовах критичних температур є високі показники корозійної стійкості, стійкість до катодного відшарування та високий ступінь зцепління з матеріалом основою.
Експеримент № 2 – Випробовування поліетиленового покриття на стійкість до катодного відшарування.
Переміщення підземного трубопроводу щодо навколишнього його грунту, а також вплив тиску з боку останнього є основними причинами виникнення відшарувань покриття. Тривалий вплив катодної поляризації може також призводити до відшарування покриття від трубопроводу – катодному відшаруванні. З відшаруванням покриття пов'язана найбільш масовий різновид корозії газопроводів – підплівкова корозія, а також корозійне розтріскування під напругою.
В даний час проблема підплівкової корозії залишається актуальною, досі не ясна роль катодного захисту в місці відшарування ізоляції. Одні фахівці вважають, що захист катодним струмом забезпечується за допомогою протікання через покриття (по-суті через перехідний опір ізоляції) або через середовище, яка проникає під покриття, що відшарувалося, інші автори стверджують, що катодний захист не робить ні якого впливу, треті – вважають, що катодний захист є джерелом утворення корозійних гальванічних пар, тобто її дію під покриттям виключно негативне [13].
Мета експерименту – дослідити ефективність дії катодного струму в відшаровування покриття та визначити доцільність використання його в умовах керитичних температур.
Матеріали для випробування:
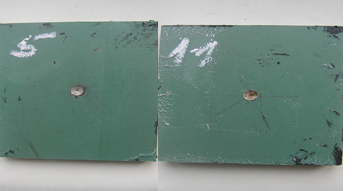
Рисунок 3 – Матеріали для випробування
З результатів експерименту було виявлено, що згідно вимогам ТУ У 27.2 – 00191135 – 009:2005 результати задовольняють вимоги до покриття номального типу виконання, тобто призначених для будування трубопроводів методом траншейної прокладки. Радіус відшарування повинген складати не більш 4 мм при 20°С та не більш 7 за температури в 60°С. Але, якщо використовувати труби з аналізуємим трьохшаровим покриттям в умовах 80°С, то стійкість до катодного відшарування дуже слабка. Вона превищує допустиму на 0,7. Тобто температура як транспортуємої рідини, так і оточуючого середовища не може дорівнювати 80°С.
Результати експериментів дозволяють сказати, що найоптимальнішим є дотримання умов при температурі в 60°С та витримці у воді 500 годин та за температури 80°С – 1000 годин. Ці значення входять в допустимі до використання трьохшарового покриття у нормальному виконанні, але для спеціальних умов необхідно покращувати показники якості адгезії та катодного відшарування. Це наглядно підтверджують залежності на рисунку 4.
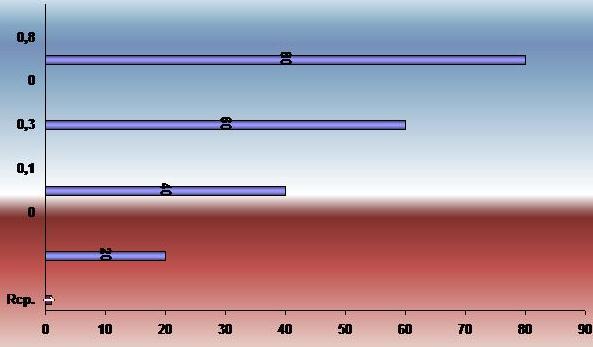
Рисунок 4 – Залежність для катодного відшарування
Експеримент № 3 – Визначення адгезії покриття до сталі при різних температурах випробувань в лабораторних умовах.
Адгезія між праймером та матеріалом основою трьохшарового покриття – сталлю згідно з нормою по ТУ У 27.2 – 00191135-014:2007 є задовільною. Згідно ескперименту вона складає при 20°С – 350°к(тобто когезійне відшарування); при 50°С – 235к; при 60°С – 200к. На графіку можно наглядно побачити, що зі збільшенням температури випробування зменшується адгезійна стійкість. При витримці у воді, починаючи від 500 до 1500 годин – показники адгезії зменшуються.
Найоптимальнішим є дотримання умов при температурі в 60°С та витримці у воді 500 годин та за температури 80°С – 1000 годин. Ці значення входять в допустимі до використання трьохшарового покриття у нормальному виконанні, але для спеціальних умов необхідно покращувати показники якості адгезії.
Результати експерименту можна побачити в таблиці 1.
Taблица 1 – Адгезійна міцність
Т, ºС | Адгезійна міцність після витримці у воді, г | |||
0 | 500 | 1000 | 1500 | |
60 | 25а | 25а | 30 | |
160а-к(70:30%) | 58а | 55 | ||
150а-к(65:35%) | 102а | 5 | ||
340 | 112а-к | 62а | 30а | |
80 | 200 а-к(15-85%) | 277 а-к(40:60%) | 230 | |
210а-к(15-85%) | 262а-к(30:70%) | 223 | ||
210а-к(15-85%) | 255а-к(50:50%) | 185 | ||
340к | 207а-к(15-85%) | 265а-к(40:60%) | 212а-к(10: |
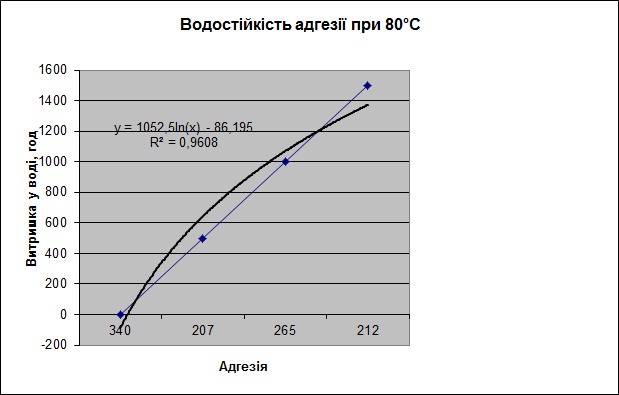
Рисунок 5 – Обробка результатів адгезійної міцності
Усі дослідження проводилися в умовах лабораторії Харцизького трубного заводу.
Висновки
В результаті проведеної роботи було вивчено тришарове поліетиленове покриття, його склад, його відмінності, переваги використання на відміну від двошарового. Також розглянуті вимоги до поліетиленової композиції покриття, види поліетилену, зокрема поліетилен високого та низького тиску, його властивості. На стадії експерименту проведена оцінка фізико-механічних властивостей поліетиленового покриття ПВТ та ПНТ, значення катодного выдшаровання та адгезії покриття.
Використовувані на заводі нині поліетиленові композиції низької щільності Luxene LDPE AM 97 виробництв компанії МРВ, Італія, і бімодальна поліетиленова композиція високої щільності Borcoat HE 3450 виробництв компанії Borealis, Фінляндія, були аттестовані центральною заводською лабораторією Харцизського трубного заводу в системі матеріалів тришарового покриття на відповідність вимогам ГОСТ Р 51164–98 і діючим ТУ.
Було визначено, що саме поліетилен високої щільності та низького тиску може бути використан для нанесення в якості полієтиленової композиції для основного шару трьохшарового поліетиленового покриття спеціального призначення газонафтопровідних труб. Отримані експериментальні дані експериментів катодного відшарування та адгезіі покриття свідчать про те, що покриття не достатньо якісне для використання при темперарурі плюс 80°С.
Проведен аналіз отриманих даних засобом Microsoft Exel, визначен показник достовірності співпадання розрахункових ліній на графіку з даними. Зроблено висновки по кожному експерименту. Визначена головна проблема( не задовільнітсть покриття щодо показників у використаані критичних температур) та в результаті подальших експериментів буде проводитися її усунення.
Магістерська робота присвячена актуальній науковій задачі – вдосконалити трьохшарове поліетиленове покриття за умови експлуатації в критичних температурах. В рамках проведених досліджень виконано:
- Розроблений склад поліолефінової композиції, який задоволняє вимогам німецького стандарту.
- На підставі аналізу літературних джерел відокремлені основні характеристики та недоліки існуючого покриття сталевих труб.
- Проведен ряд експериментів по модернізації трьохшарового покриття.
- Виявлено напрямки подальших дій по темі магістерської роботи.
Подальші дослідження направлені на наступні аспекти:
- Вдосконалення покриття сталевих труб для використання за умови критичних температур.
- Визначення подальших напрямків експериментів.
- Перевірка розробленого покриття в умовах реальної лабораторії.
- Розробка програми для автоматичної перевірки якості покриття.
При написанні даного реферату магістерська робота ще не завершена. Остаточне завершення: грудень 2013 року. Повний текст роботи та матеріали по темі можуть бути отримані у автора або його керівника після вказаної дати.
Перелік посилань
- ТУ У 27.2–00191135–0225:2011 Трубы стальные электросварные прямошовные экспандированные с трехслойным наружным антикоррозионным полиэтиленовым покрытием для магистральных нефтепроводов.
- ГОСТ 11262–80 Пластмассы. Метод испытания на растяжение.
- ГОСТ 24297–87 Входной контроль продукции. Основные положения
- ГОСТ Р 51164–98 Трубопроводы стальные магистральные. Общие требования к защите от коррозии.
- ГОСТ 16337–77 Полиэтилен высокого давления
- ГОСТ 16338–85 Полиэтилен низкого давления
- ТУ У 14–8–23–2000 Трубы стальные электросварные прямошовные диаметром 530-1420 мм с наружным полиэтиленовым антикокоррозионным покрытием для подземной прокладки в различных климатических условиях.
- Методические указания по разделу «Охрана труда» в дипломных проектах и работах. Под редакцией Макарова Г.В. М.: МХТИ им.Д.И. Менделеева, 1990-29 с.
- Н.А. Кочетков, А.Ф. Бочков, Б.А. Дмитриев и др. Химия углеводов // М.: Химия. - 1967. - с.672.
- Лебедев Л.М. Машины и приборы для испытания полимеров, М., 1967.253с.
- Красноярский В. В., Электрохимический метод защиты металлов от коррозии, М., 1961;
- Фрейман Л.И., Макаров В.А., Брыксин Е. И., Потенциостатические методы в коррозионных исследованиях и электрохимической защите, Л., 1972;
- Люблинский Е. Я., Протекторная зашита морских судов и сооружений от коррозии, Л., 1979;
- Кузуб B. C., Глазов Н.П., Шамшетдинов К.Л. и др. Об измерении поляризационного потенциала на подземных стальных трубопроводах/ Практика противокоррозионной защиты – 2000, №2 – с.24-29.
- Зиневич А.М., Храмихина В.Ф. и др. Воздействие катодной поляризации на стальную поверхность под пленочным покрытием / Строительство трубопроводов – 1979. №8 – С. 25-27.
- Ортон М.Д.
- Измерение защитного потенциала трубопровода в местах отслоения изоляционного покрытия. / Нефть, газ и нефтехимия, №3, 1986, С. 72-75.
- Закон Украины «Об охране труда» 2694-12 от 14.10.1992;
- «Правила охраны труда в трубном производстве», утвержденных приказом комитета Украины по промышленной безопасности, охране труда и горному надзору от 15.10.2009 №171, зарегистрированных в Министерстве юстиции Украины 05.11.2009 за № 1037/17053.
- «Правила охраны труда в металлургической промышленности», утвержденных приказом Государственного комитета Украины по промышленной безопасности, охране труда и горному надзору от 22.12.2008 №289 , зарегистрированных в Министерстве юстиции Украины 29.01.2009 за №87/16103
- «Положения о разработке инструкций по охране труда» НПАОП 0.00-4.15-98, утвержденного приказом Министерства труда и социальной политики Украины №9 от 29.01.1998, зарегистрированного в Министерстве юстиции Украины 07.04.1998 за №226/2666.
- Электронный журнал: физикохимия поверхности и защита материалов [электронный ресурс]. – Режим доступа: http://maik.rssi.ru...
- Электронный журнал: Территория нефти и газа, [электронный ресурс]. – Режим доступа: http://neftegas.info...