Реферат по теме выпускной работы
Содержание
- Введение
- 1. Актуальность темы
- 2. Цель и задачи исследования, планируемые результаты
- 3. Обзор существующих полиолефиновых композиций и методов их анализа
- 3.1 Анализ существующей на данный момент трехслойной полиолефиновой композиции
- 3.2 Полиэтилен, его свойства
- 3.3 Методы оценки трехслойного покрытия и их целесообразность
- 3.4 Катодная защита
- 3.5 Адгезия
- 4. Результаты собственных исследований и дальнейшее развитие темы
- Выводы
- Список источников
Ввведение
Транспортировка нефти, газа и нефтепродуктов по трубопроводам является наиболее эффективным и безопасным способом их транспортировки на значительные расстояния. Этим способом доставки нефти и газа от районов их добычи до потребителей пользуются уже более 100 лет. Долговечность и безаварийность работы трубопроводов напрямую зависит от эффективности их противокоррозионной защиты. Для сведения к минимуму риска коррозионных повреждений трубопроводы защищают антикоррозионными покрытиями и дополнительно средствами электрохимзащиты. При этом изоляционные покрытия обеспечивают первичный (пассивную) защиту трубопроводов от коррозии, выполняя функцию «диффузионного барьера», через который затрудняется доступ к металлу коррозийноактивних агентов (воды, кислорода, воздуха). При появлении в покрытии дефектов предусматривается система катодной защиты трубопроводов – «активный» защита от коррозии.
Для того, чтобы защитное покрытие эффективно выполняло свои функции, оно должно удовлетворять целому ряду требований, основными из которых являются: низкая влагокислородопроницаемость, высокие механические характеристики, высокая и стабильная во времени адгезия покрытия к стали, стойкость к катодному отслаиванию, хорошие диэлектрические свойства, стойкость покрытия к УФ и тепловому старению. Изоляционные покрытия должны выполнять свои функции в широком интервале температур строительства и эксплуатации трубопроводов, обеспечивая их защиту от коррозии на максимально возможный срок их эксплуатации [1].
1. Актуальность темы
Актуальность этого вопроса возникает в том, что с одной стороны, постоянно повышается качество защитных покрытий трубопроводов, практически каждые 10 лет появляются новые изоляционные материалы, новые технологии и оборудование для нанесения покрытий на трубы в заводских и трассовых условиях. С другой стороны, становятся все более жесткими условия строительства и эксплуатации трубопроводов (строительство трубопроводов в условиях Крайнего Севера, в Западной Сибири, освоение морских месторождений нефти и газа, глубоководное прокладки, строительство участков трубопроводов методами «наклонно-направленного бурения», «микротоннелирувания» эксплуатация трубопроводов при температурах до 100°С и выше, и др.) [2].
Необходимо отметить, что в последних 7-8 лет общий уровень противокоррозионной защиты трубопроводов значительно повысился за счет внедрения новых технологий, качественных изоляционных материалов, широкого использования при строительстве трубопроводов труб и фасонных деталей с заводскими покрытиями. Можно также утверждать, что современные покрытия при условии выполнения требований по строительству и укладке трубопроводов способны обеспечить их безаварийную (по причине коррозии) работу на весь период эксплуатации (40-50 лет и более).
В этой работе будут рассмотрены:
- Трехслойное полиэтиленовое покрытие, его состав. Его отличия, преимущества использования в отличие от двухслойного.
- Требования к полиэтиленовой композиции покрытия, виды полиэтилена. Полиэтилен высокого и низкого давления, его свойства.
- Проведена оценка физико-механических свойств полиэтиленового покрытия ПВТ и ПНД в центральной заводской лаборатории ПАО «ХТЗ».
2. Цель и задачи исследования, планируемые результаты.
Целью исследования является разработка полиэтиленовой композиции для стальных труб, которое способно выдержать критические температуры експлуатации.
Основные задачи исследования:
- Анализ трехслойного полиэтиленового покрытия. Выявление его недостатков и преимуществ.
- Исследовать полиэтилен низкого давления и высокого давления, эпоксидную композицию и выбрать адгезив для нового качественного покрытия.
- Провести оценку существующих методов анализа и технологического совершенствования трехслойного покрытия для стальных труб.
- Оценить физико-механические свойства полиэтиленового покрытия высокого и низкого давления.
- Дать анализ таким характеристикам покрытия, как устойчивость к адгезии и катодное отслаивание.
- Предложить методы совершенствования полиэтиленовой композиции.
Объект исследования: трехслойное полиэтиленовое покрытие.
Предмет исследования: технологические методы и системы совершенствования покрытия для использования в условиях Крайнего Севера.
В рамках магистерской работы планируется получение актуальных научных результатов по следующим направлениям:
- Повышенные требования к полиолефиновых композиций.
- Определение областей применения различных вариантов полиэтиленового покрытия.
- Модификация известных смесей полиэтиленового покрытия, и дальнейшая эксплуатация наиболее эффективного.
3. Осмотр достижений и результатов
Поскольку трехслойное покрытие стальных труб является актуальным вопросом, то сейчас этому вопросу посвящен ряд работ университетов нефти и газа, как отечественных, так и зарубежных. Поэтому, в работе будут использованы выводы ученых, сделанные в последние несколько лет.
3.1 Анализ существующей полиэтиленовой композиции
В этом разделе приводится описание двухслойного и трехслойного полиэтиленового покрытия, проводится анализ. Впервые однослойные полиэтиленовые покрытия труб на основе порошкового полиэтилена стали применяться в конце 50-х годов прошлого века. Технология нанесения однослойного полиэтиленового покрытия аналогична технологии нанесения покрытий из порошковых эпоксидных красок. Из-за низкой водостойкости адгезии и стойкости к катодной отслойка однослойные полиэтиленовые покрытия не получили достаточно широкого применения. Им на смену пришли двухслойные покрытия с «мягким» адгезионным подслоем. В конструкции такого покрытия как адгезионный слой применялись изоляционные битумно-каучуковые мастики («мягкие» адгезивы) толщиной 150-300 мкм, наносимых по слою праймера, а как внешний ударопрочный слой использовался экструдированный полиэтилен толщиной не менее 2,0-3, 0 мм.
После того, как фирмой BASF (Германия) был разработан сополимер этилена и эфира акриловой кислоты (Lucalen), впервые был опробован в конструкции заводского полиэтиленового покрытия труб как термоплавкого полимерный клеевой подслой, в практику строительства трубопроводов было введено двухслойное полиэтиленовое покрытие с «жестким» адгезионным подслоем. Позже был разработан еще целый ряд термоплавких клеевых композиций на основе сополимеров этилена и винилацетата, этилена и акрилата. Двухслойные полиэтиленовые покрытия получили очень широкое применение и на долгие годы стали основными заводскими покрытиями труб. Конструктивно двухслойное полиэтиленовое покрытие состоит из адгезионного подслоя на основе термоплавкой полимерной композиции толщиной 250-400 мкм и наружного полиэтиленового слоя толщиной от 1,6 мм до 3,0 мм. В зависимости от диаметров труб, общая толщина покрытия составляет не менее 2,0 (для труб диаметром до 273 мм включительно) и не менее 3,0 мм (для труб диаметром 1020 мм и выше). Для нанесения двухслойных полиэтиленовых покрытий применяются как отечественные, так и импортные изоляционные материалы (термоплавкие композиции на основе сополимеров – для нанесения адгезионного слоя и композиции термосветостабилизированного полиэтилена – для нанесения наружного слоя). С целью повышения устойчивости двухслойных полиэтиленовых покрытий к воздействию воды и устойчивости к катодному отслаиванию при повышенных температурах производится обработка поверхности очищенных труб (пассивация) раствором хромата. При правильном подборе изоляционных материалов двухслойное полиэтиленовое покрытие имеет достаточно высокие показатели свойств и соответствует техническим требованиям, предъявляемым к заводским покрытиям труб. Оно способно обеспечить защиту трубопроводов от коррозии на срок до 30 лет и выше [3].
Впервые конструкция трехслойного полиэтиленового покрытия была разработана и запатентована специалистами фирмы BASF и Mannesmann, Германия 20 лет назад. Трехслойное покрытие типа MAPEK состоит из слоя эпоксидного праймера толщиной от 60 до 200 мкм, адгезионного слоя толщиной от 200 до 500 мкм и наружного полиэтиленового слоя толщиной от 1,5 до 3,0 мм. В зависимости от диаметров труб и назначения трубопроводов общая толщина трехслойного покрытия может изменяться от 2,0 до 3,5 мм. Сегодня трехслойное полиэтиленовое покрытие является наиболее эффективным наружным антикоррозионным покрытием труб заводского нанесения. Этот тип покрытия широко применяется во всем мире для антикоррозионной защиты трубопроводов различного назначения (магистральные газопроводы, нефтепроводы, продуктопроводы, трубопроводы коммунального назначения и др.). При правильном выборе системы изоляционных материалов, при строгом соблюдении технологических режимов очистки и наружной изоляции труб расчетный срок службы трехслойного покрытия при температурах эксплуатации до плюс 60°С составляет не менее 50 лет [4]. В 1999 году с использованием оборудования фирмы Bradero Price, США на заводе был освоен процесс заводской изоляции труб диаметром 168-1420 мм трехслойным покрытием на основе изоляционных материалов фирм DuPont и NOVA, Канада. В 2000 году на базе технологического оборудования поставки фирмы Selmers, Нидерланды была внедрена технология трехслойной полиэтиленовой изоляции труб диаметром до 1420 мм была освоена на Харцызском трубном заводе, Украина. Харцызский трубный завод производит широкий спектр стальных экспандированных электросварных труб диаметром 508-1422 мм (20-56 дюймов) с толщиной стенки 6,0-40,0 мм, на рабочее давление до 9,8 МПа для газонефтепроводов, тепловых электростанций и тепловых сетей, общего назначения [5]. Рост мировой добычи нефти и газа в 2012 году будет неразрывно связан с усложнением условий эксплуатации месторождений: освоением шельфовых участков добычи углеводородов и повышением коррозионной активности средств, транспортируемых. Постоянное изучение рынка уже сейчас дает возможность Харцызскому трубному заводу (на базе которого выполняется магистерская работа) вести активную работу по освоению новых перспективных видов продукции.
После внедрения на отечественных предприятиях промышленных производств по трехслойной изоляции труб, ВНИИСТ по поручению АК Транснефть и Госгортехнадзора РФ были проведены комплексные испытания и сертификация заводских трехслойных полиэтиленовых покрытий труб на соответствие их требованиям Технических условий и ГОСТ–Р–51164 «Трубопроводы стальные магистральные. Общие требования к защите от коррозии». В настоящее время Центром базовой изоляции ВНИИСТ испытано уже более 10 различных систем трехслойных покрытий труб. Оценка характеристик покрытия проводилась по 15 показателям свойств, включая: диэлектрическую сплошнисть, адгезию покрытия к стали, водостойкость адгезии, устойчивость к катодной отслойка, ударную прочность в диапазоне температур, стойкость к растрескиванию, к ультрафиолетовому и термическому старению и др. Несмотря на достаточно высокие требования российского стандарта ГОСТ–Р–51164, в значительной мере превышают требования немецкого стандарта ОГМ 30670 и французского стандарта МРА 49710, несколько систем трехслойных покрытий выдержали комплексные испытания и были рекомендованы к практическому применению [6].
Наилучшие результаты были получены при испытании заводских трехслойных систем с использованием порошковых эпоксидных красок фирм BASF, 3 M, BS Coating, Akzo Nobel, композиций адгезива и полиэтилена производства Borealis, Basell, Atofina , UBE.
Необходимо отметить, что до настоящего времени не сертифицирована ни одна система трехслойного покрытия на базе отечественных изоляционных материалов. Проблема в том, что украинские заводы-изготовители изоляционных материалов работают каждый сам по себе, а для разработки системы покрытия требуется комплексный подход. Для определенного эпоксидного праймера требуется именно то, что сочетается с праймером клеевого подслоя и полиэтилена. Это необходимо для того, чтобы при послойном нанесении покрытия между эпоксидным праймером и клеевым подслоем могли образовываться химические связи, стойкие к воздействию воды, повышенных температур и к длительному воздействию электро-химической защиты. Кроме того, проведены ВНИИСТ испытания различных отечественных композиций полиэтилена, применяемые на украинских заводах для двухслойной изоляции труб, показали, что эти композиции не выдерживают требований ГОСТ–Р–51164 по показателям: стойкость к растрескиванию под напряжением, термостабильность, эластичность при минусовых температурах [7].
Предстоит достаточно большая работа по выбору и доработке отечественных изоляционных материалов, по разработке системы трехслойного полиэтиленового покрытия труб, которая могла бы конкурировать с импортными системами покрытий. Поэтому, именно этому в последнее время на конференциях, на заседаниях научно-технических советов, в отечественных специализированных журналах ведутся дискуссии о преимуществах и недостатках различных систем двухслойных и трехслойных полиэтиленовых покрытий труб. По прошедших 5-6 лет ВНИИСТ были проведены многочисленные испытания двухслойных полиэтиленовых покрытий труб различных украинских заводов-изготовителей.
После 1000 ч испытаний в воде при температурах 20, 40 и 60°С адгезия трехслойного покрытия к стали остается на уровне начальных значений. В случае двухслойного покрытия наблюдается резкое снижение адгезии покрытия к стали после испытаний в воде при температуре 60°С. Зачастую при повышенных температурах испытаний происходит полное отслоение двухслойного покрытия от стали. При температуре плюс 60°С площадь катодной отслойка трехслойного покрытия в 5-10 раз меньше площади отслойки двухслойного покрытия. В некоторых случаях, когда при нанесении двухслойного покрытия не производится обработка поверхности труб раствором хромата, вследствие катодной поляризации происходит полное отслоение покрытия от стали.
В связи с тем, что в системах трехслойных покрытий используется, как правило, полиэтилен высокой плотности или бимодальное полиэтилен, а для двухслойных покрытий применяется полиэтилен низкой плотности ударная прочность трехслойных покрытий в 2-3 раза превышает ударную прочность двухслойных покрытий. При толщине покрытия около 3 мм, ударная прочность трехслойных покрытий составляет 50-60 Дж, тогда как в случае двухслойного покрытия прочность при ударе не превышает 20 Дж.
Трехслойные покрытия на основе бимодального полиэтилена и полиэтилена высокой плотности характеризуются повышенной механической прочностью. Прочность при растяжении отслоенного покрытия при 20°С при этом составляет от 22 до 28 МПа, в то время как этот показатель для двухслойного покрытия на основе полиэтилена низкой плотности кабельных марок изменяется в пределах от 11 до 13,5 МПа. Относительное удлинение при разрыве при температуре минус 40°С для отечественных марок полиэтилена 102-10°К, 153-10°К не превышает значений 40 до 60%, тогда как для импортных марок полиэтилена высокой плотности этот показатель составляет 90-100%, а для бимодального полиэтилена достигабельного полиэтилена марок 102-10°К и 153-10°К устойчивость к растрескиванию составляет 200-500 часов. В тоже время устойчивость к растрескиванию сертифицированных ВНИИСТ импортных полиэтиленовых композиций, применяемых в системах трехслойных покрытий труб, превышает 2000 ч, а в случае бимодального полиэтилена достигает значений 10 000 ч [8].
Таким образом, проведенные ВНИИСТ комплексные испытания двухслойных и трехслойных полиэтиленовых покрытий труб, производимых на украинских предприятиях, свидетельствуют о безусловных преимущества трехслойных систем покрытий на основе современных изоляционных материалов. Использование таких покрытий позволяет в значительной степени повысить надежность и эффективность противокоррозионной защиты трубопроводов и увеличить продолжительность срока их эксплуатации.
3.2 Полиетилен, его свойства
Полиэтилен – самый дешевый полимер, занимает первое место в мировом производстве полеолефиниов. Этот уникальный материал сочетает в себе ценные свойства и способность перерабатываться всеми высокопроизводительными методами, существующими для термопластов.
Полиэтилен – это пластикат, что имеет хорошие диэлектрические свойства, повышенную ударопрочность, небольшой поглотительной способности. Не ломается, обладает низкой газо-и паропроницаемость. Физиологически нейтральный, не имеет запаха. Полиэтилен не восприимчив к щелочам любой концентрации, растворов любых солей, карбоновых, плавиковой и концентрированной соляной кислотам. Устойчив к маслу, овощных соков, алкоголя, воды, бензина. Разрушается азотной кислотой, газообразными и жидким фтором и хлором. Не растворяется, а только немного отекает в органических растворителях. Стоек к нагреванию в вакууме, но разрушается на воздухе при нагревании от восьмидесяти градусов.
Полиэтилен морозоустойчив (до семидесяти градусов). Под действием ультрафиолетовых лучей подвергается фотодеструкцией. Легко модифицируется. Дополнительное хлорирование, сульфирование, бромирования или фторирование предоставляют полиэтилена каучуко-подобные свойства, улучшают химическую и тепловую устойчивость. Сополимеризации с другими полеолефина или полярными мономерами повышает его прозрачность, эластичность, адгезионные характеристики, а также устойчивость к растрескиванию. Смешивание полиэтилена с другими полимерными материалами улучшает другие его физические свойства. Полиэтилен безвреден для человека, из него не выделяются опасные для его здоровья вещества. Вид молекулы полиэтилена приведена на рисунке 1.
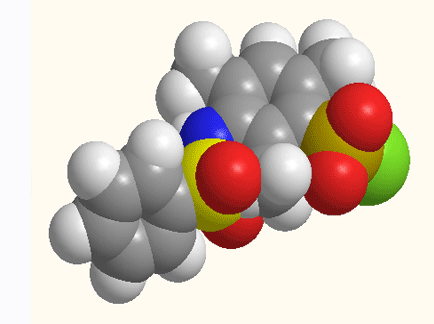
Рисунок 1 – Молекула полиэтилена
(анимация: 6 кадров, 5 циклов повторения, 140 килобайт)
(xi – входные сигналы, yi – биты кода состояния, zi – выходные сигналы)
3.3 Методы оценки трехслойного полиэтиленового покрытия и их целесообразность
Показателями, по которым дают оценку полиэтиленовому покрытию, являются:
- высокая коррозионная стойкость;
- высокую степень сцепления с материалом-основой;
- высокая ударопрочность и устойчивость к деформирующему воздействию при транспортировке и прокладке труб;
- высокое электрическое сопротивление, необходимое для антикоррозионной защиты и предотвращения утечек защитного тока труб;
- устойчивость к катодному отслаиванию, вызванное действием катодной поляризации;
- стабильность во времени физико-механических и химических свойств покрытия;
- хорошие диэлектрические показатели;
- устойчивость к УФ-излучению;
- устойчивость к тепловому старению;
- широкий диапазон эксплуатационных температур (окружающей среды и перекачиваемой);
- длительный срок эффективной эксплуатации.
Главное же, от чего зависит надежность и безаварийность трубопроводов любого назначения, есть ряд факторов, к которым можно отнести, во-первых, климатические условия местности, в которой они прокладываются, во-вторых, условия эксплуатации (химический состав транспортируемой жидкости, ее температуру, давление, способ прокладки трубопровода (скрытый или открытый), совместимость с другими элементами трубопровода) и, в-третьих, эффективность антикоррозионной защиты. Чтобы свести к минимуму риски преждевременного выхода трубопровода из строя, его необходимо защитить с помощью антикоррозионных покрытий (первичный или пассивная защита) и средств электрохимической защиты. Защитное антикоррозионное покрытие выполняет барьерную функцию, изолирующую металл трубы от взаимодействия с коррозионной средой – влажной, кислородом воздуха и др. Система катодной защиты трубопроводов (активная защита) предназначена для предотвращения коррозионного разрушения металла трубы при повреждениях покрытия [9].
3.4 Катодная защита
Сдвиг потенциала металла может быть осуществлен с помощью внешнего источника постоянного тока (станции катодной защиты) или соединением с другим металлом, более электроотрицательным по своему электродном потенциала (так называемый протекторным анод). При этом поверхность защищается образца (детали конструкции) становится эквипотенциальной и на всех ее участках протекают только катодные процессы, а анодные, обусловливающие коррозию, перенесены на вспомогательные электроды. Если, однако, сдвиг потенциала в отрицательную сторону превысит определенное значение, возможна так называемая перезащита, связанная с выделением водорода, изменением состава приэлектродных слоя и другими явлениями, что может привести к ускорению коррозии. Катодная защита, как правило, совмещают с нанесением защитных покрытий; необходимо учитывать возможность отслаивания покрытия.
Особенно важно использование катодной защиты для стационарных нефтегазопромысловых сооружений, трубопроводов и хранилищ к ним на континентальном шельфе. Подобные сооружения не могут быть введены в сухой док для восстановления защитного покрытия, поэтому электрохимическая защита является основным методом предотвращения коррозии. Морских нефтепромысловых вышка, как правило, обеспечена в своей подводной части протекторными анодами (на одну вышку приходится до 10-ти и более протекторных сплавов).
3.5 Адгезия
Померить равновесную работу адгезии между полимером и твердым телом в подавляющем большинстве случаев не представляется возможным из-за очень высокой вязкости полимеров. Поэтому применительно к полимерам определяют не адгезию, а адгезионную прочность. Она измеряется как удельная работа или удельная сила разрушения связи между адгезивом и субстратом. С практической точки зрения при использовании полимеров в качестве клеев или матрицы для ПКМ важна не работа адгезии, а механическая прочность связи полимера с другой поверхностью. Однако при механическом разрушении адгезионного соединения работа, затрачиваемая на отслаивание двух тел, идет не только на преодоление адгезии, но и на другие побочные процессы (деформация тела, преодоление сил механических зацеплений и т.д.). Поэтому не только величины, но и понятие адгезии и адгезионной прочности не тождественны, и их нужно четко разграничивать [10].
Методов определения адгезионной прочности очень много. Их выбор зависит от того, какой нагрузке будет подвергаться адгезионное соединение при эксплуатации. Но из этих способов можно выделить три наиболее часто используемых – это адгезионная прочность при нормальном отрыве (рис 3. А), при отслойке (рис 3. Б) и при сдвиге (рис. 3.В).
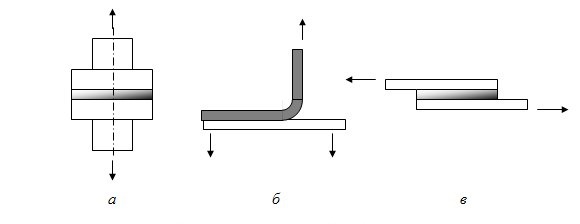
Рисунок 2 – Види адгезионной прочности
Итак, одним из главных показателей качества трехслойного покрытия являются: устойчивость к катодной видшаровання, адгезия покрытия и физико-механические характеристики. Прочность покрытия должна быть достаточной для того, чтобы без последствий перенести механические удары и деформации, возможные при транспортировке и подземной прокладке труб. Система катодной защиты трубопроводов (активная защита) предназначена для предотвращения коррозионного разрушения металла трубы при повреждениях покрытия. Знание величины адгезионной прочности между субстанциями исходя из их химического строения, структуры и условий образования контакта между ними дают возможность прогнозировать срок службы покрытия и возможные условия эксплуатации.
4. Результаты исследований и дальнейшее развитие темы
Эксперимент № 1 – Определение относительного удлинения и прочности при разрыве.
Свойства уже готовых изделий из полиэтилена существенно зависят от режима их изготовления (равномерности и скорости охлаждения) и, конечно, условий их эксплуатации (давления, температуры, продолжительности действия нагрузки и т. д.). Поэтому в лаборатории ЦЗЛ анализа подвергаться полиэтиленовое покрытие, переработанное в экструдере. Будет определено: соответствуют физико-механические свойства полиэтилена ГОСТ производителя после его переработки в экструдере и как он будет вести себя в эксплуатации в качестве покрытия (при температуре в 25 градусов и нагрузке в 700 МПа). Также будет определено, можно использовать полиэтилен для нанесения покрытия специального назначения.Согласно ТУ У 27.2 – 00191135–009:2005 эксперимент будет распространяться на трубы стальные электросварные прямошовные экспандированных обычного и холодостойкие выполнения диаметром от 530 до 120 мм с наружным трехслойным полиэтиленовым покрытием, предназначены для строительства магистральных нефтепроводов подземного и подводного прокладки [11].
В результате эксперимента видно, что прочность для материала – полиэтилен высокой плотности низкого давления составляет 26,727 МПа, а для полиэтилена низкой плотности высокого давления – 17,04 МПа. Есть в полиэтилена высокой плотности прочность на 36,45% выше, чем в полиэтилена низкой плотности.
При выборе полиэтиленовой композиции для основного слоя внешнего трехслойного полиэтиленового покрытия газонефтепроводных труб производства ПАО «Харцызский трубный завод», исходя из этого эксперимента полиэтилен низкой плотности не проходит по техническим требованиям. Его можно использовать только для нанесения покрытия нормального, термостойкого и морозостойкого покрытия. Полиэтиленовая композиция для нанесения покрытия специального исполнения из полиэтилена высокой плотности проходит по прочностными характеристиками. Согласно норме по ТУ У 27.2 – 001911135 – 009:2005 прочность при растяжении отслоенного покрытия должна составлять для 18 МПа для специального исполнения, и 12 МПа для обычного [12].
Плохие прочностные характеристики полиэтилена высокого давления можно объяснить его молекулярной структурой и физико-химическими свойствами в частности. Особенностью структуры полиэтилена ПВД является большое количество длинных и коротких ответвлений, которые не позволяют молекулам с высокой молекулярной массой создавать кристаллическую структуру. Связи поэтому между ними не сильны, а это говорить о тех, что полиэтилен имеет невысокую устойчивость на разрыв и повышенную пластичность, а также высокую текучесть в расплаве.
Учитывая результаты эксперимента № 1, полиэтилен для нанесения антикоррозионного защитного покрытия специального типа, вибриаеться высокой плотности марки HE 3450. Следующим требованием к изготовлению покрытия специального назначения, т.е. для использования в условиях критических температур являются высокие показатели коррозионной стойкости, устойчивость к катодной отслойка и высокую степень сцепления с материалом основой.
Эксперимент № 2 – Испытание полиэтиленового покрытия на стойкость к катодному отслаиванию.
Перемещение подземного трубопровода в окружающей его почвы, а также влияние давления со стороны последнего являются основными причинами возникновения отслоений покрытия. Длительное воздействие катодной поляризации может также приводить к отслоению покрытия от трубопровода – «катодном отслаивании». С отслоением покрытия связана наиболее массовый вид коррозии газопроводов – «подпленочная коррозия», а также коррозионное растрескивание под напряжением.
В настоящее время проблема «подпленочной коррозии» остается актуальной до сих пор не ясна роль катодной защиты в месте отслойки изоляции. Одни специалисты считают, что защита катодным током обеспечивается посредством протекания через покрытие (по сути через переходное сопротивление изоляции) или через среду, которая проникает под покрытие, отслоившееся другие авторы утверждают, что катодная защита не оказывает ни какого влияния, третьи – считают, что катодная защита является источником образования коррозионных гальванических пар, т.е. ее действие под покрытием исключительно отрицательное [13].
Цель эксперимента – исследовать эффективность действия катодного тока в отслаивания покрытия и определить целесообразность использования его в условиях керитичних температур.
Материалы для испытания:
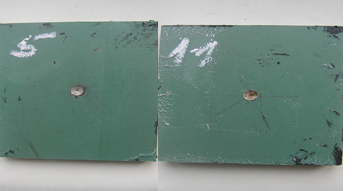
Рисунок 3 – Материалы для испытания
Из эксперимента было выявлено, что согласно требованиям ТУ У 27.2 – 00191135-009:2005 результаты удовлетворяют требования к покрытию Номально типа исполнения, т.е. предназначенных для строительства трубопроводов методом траншейной прокладки. Радиус отслаивания должен составлять не более 4 мм при 20°С и не больше 7 при температуре в 60°С. Но если использовать трубы из анализируемых трехслойной покрытием в условиях 80°С, то устойчивость к катодному отслаиванию очень слабое. Она превышающую допустимую на 0,7. Есть температура как транспортируемого жидкости, так и окружающей среды не может равняться 80°С [13].
Результаты экспериментов позволяют сказать, что оптимальным является соблюдение условий при температуре в 60°С и выдержке в воде 500 часов и при температуре 80°С – 1000 часов. Эти значения входят в допустимые к использованию трехслойного покрытия в нормальном исполнении, но для специальных условий необходимо улучшать показатели качества адгезии и катодной видшарування. Это наглядно подтверждают зависимости на рисунке 4.
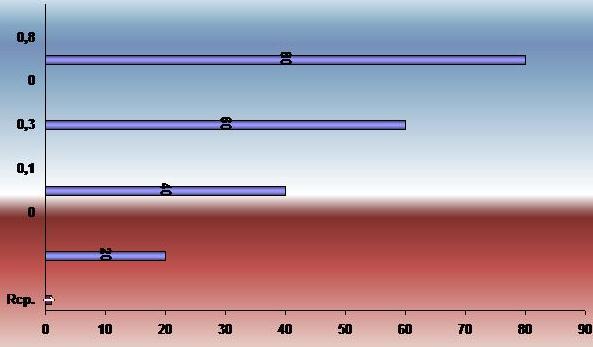
Рисунок 4 – Зависимость для катодного отслаивания
Эксперимент № 3 – Определение адгезии покрытия к стали при различных температурах испытаний в лабораторных условиях.
Адгезия между праймером и материалом основой трехслойного покрытия – сталью согласно норме по ТУ У 27.2 – 00191135 – 014:2007 является удовлетворительной. Согласно опытам она составляет при 20°С – 350л.с. (т.е. когезионное отслойка) при 50°С – 235°К, при 60°С – 200°к. На графике можно наглядно увидеть, что с увеличением температуры испытания уменьшается адгезионная стойкость. При выдержке в воде, начиная от 500 до 1500 часов – показатели адгезии уменьшаются.
Оптимальным является соблюдение условий при температуре в 60°С и выдержке в воде 500 часов и при температуре 80°С – 1000 часов. Эти значения входят в допустимые к использованию трехслойного покрытия в нормальном исполнении, но для специальных условий необходимо улучшать показатели качества адгезии.
Результаты эксперимента можно увидеть в таблице 1.
Taблица 1 – Адгезионная прочность
Т, ºС | Adhesion strength after aging in water, h | |||
0 | 500 | 1000 | 1500 | |
60 | 25а | 25а | 30 | |
160а-к(70:30%) | 58а | 55 | ||
150а-к(65:35%) | 102а | 5 | ||
340 | 112а-к | 62а | 30а | |
80 | 200 а-к(15-85%) | 277 а-к(40:60%) | 230 | |
210а-к(15-85%) | 262а-к(30:70%) | 223 | ||
210а-к(15-85%) | 255а-к(50:50%) | 185 | ||
340к | 207а-к(15-85%) | 265а-к(40:60%) | 212а-к(10: |
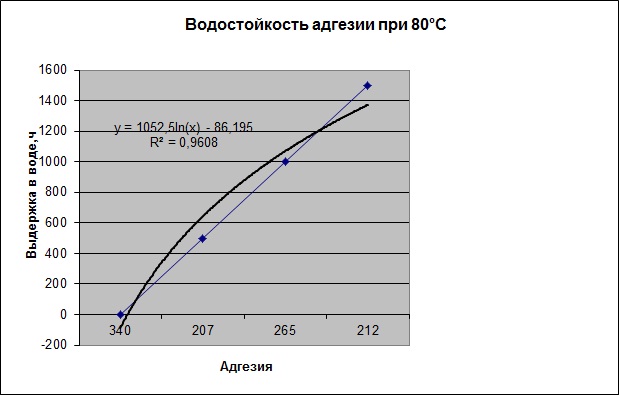
Рисунок 5 – Обработка результатов адгезионной прочности
Все исследования проводились в условиях лаборатории Харцызского трубного завода.
Выводы
В результате проведенной работы было изучено трехслойное полиэтиленовое покрытие, его состав, его отличия, преимущества использования в отличие от двухслойного. Также рассмотрены требования к полиэтиленовой композиции покрытия, виды полиэтилена, в частности полиэтилен высокого и низкого давления, его свойства. На стадии эксперимента проведена оценка физико-механических свойств полиэтиленового покрытия ПВТ и ПНД, значение катодного отслаивания и адгезии покрытия.
Было определено, что именно полиэтилен высокой плотности и низкого давления может быть использована для нанесения в качестве полиэтиленовых композиции для основного слоя трехслойного полиэтиленового покрытия специального назначения газонефтепроводных труб. Полученные экспериментальные данные экспериментов катодного отслаивания и адгезии покрытия свидетельствуют о том, что покрытие не достаточно качественное для использования при темперарури плюс 80°С.
Проведен анализ полученных данных средством Microsoft Exel, определен показатель достоверности совпадение расчетных линий на графике с данными. Сделаны выводы по каждому эксперимента. Определена главная проблема – несоответствие покрытия по показателям в условиях критических температур; и в результате дальнейших экспериментов будет проводиться ее устранения.
Магистерская работа посвящена актуальной научной задачи – усовершенствовать трехслойное полиэтиленовое покрытие при эксплуатации в критических температурах. В рамках проведенных исследований выполнено:
- Разработан состав полиолефиновой композиции, который удовлетворяет требованиям немецкого стандарта.
- На основании анализа литературных источников выделены основные характеристики и недостатки существующего покрытия стальных труб.
- Проведен ряд экспериментов по модернизации трехслойного покрытия.
- Выявлены направления дальнейших действий по теме магистерской работы.
Дальнейшие исследования направлены на следующие аспекты:
- Совершенствование покрытия стальных труб для использования при критических температур.
- Определение дальнейших направлений экспериментов.
- Проверка разработанного покрытия в условиях реальной лаборатории.
- Разработка программы для автоматической проверки качества покрытия.
При написании данного реферата магистерская работа еще не завершена. Окончательное завершение: декабрь 2013 года. Полный текст работы и материалы по теме могут быть получены у автора или его руководителя после указанной даты.
Перечень ссылок
- ТУ У 27.2 – 00191135 – 0225:2011 Трубы стальные электросварные прямошовные экспандированные с трехслойным наружным антикоррозионным полиэтиленовым покрытием для магистральных нефтепроводов.
- ГОСТ 11262 – 80 Пластмассы. Метод испытания на растяжение.
- ГОСТ 24297 – 87 Входной контроль продукции. Основные положения
- ГОСТ Р 51164 – 98 Трубопроводы стальные магистральные. Общие требования к защите от коррозии.
- ГОСТ 16337 – 77 Полиэтилен высокого давления
- ГОСТ 16338 – 85 Полиэтилен низкого давления
- ТУ У 14–8–23–2000 Трубы стальные электросварные прямошовные диаметром 530-1420 мм с наружным полиэтиленовым антикокоррозионным покрытием для подземной прокладки в различных климатических условиях.
- Методические указания по разделу «Охрана труда» в дипломных проектах и работах. Под редакцией Макарова Г.В. М.: МХТИ им.Д.И. Менделеева, 1990 – 29 с.
- Н.А. Кочетков, А.Ф. Бочков, Б.А. Дмитриев и др. Химия углеводов // М.: Химия. - 1967. - с.672.
- Лебедев Л.М. Машины и приборы для испытания полимеров, М., 1967.253с.
- Красноярский В. В., Электрохимический метод защиты металлов от коррозии, М., 1961;
- Фрейман Л.И., Макаров В.А., Брыксин Е. И., Потенциостатические методы в коррозионных исследованиях и электрохимической защите, Л., 1972;
- Люблинский Е. Я., Протекторная зашита морских судов и сооружений от коррозии, Л., 1979;
- Кузуб B. C., Глазов Н.П., Шамшетдинов К.Л. и др. Об измерении поляризационного потенциала на подземных стальных трубопроводах/ Практика противокоррозионной защиты – 2000, №2 – с.24-29.
- Зиневич А.М., Храмихина В.Ф. и др. Воздействие катодной поляризации на стальную поверхность под пленочным покрытием / Строительство трубопроводов – 1979. №8 – С. 25-27.
- Ортон М.Д. Измерение защитного потенциала трубопровода в местах отслоения изоляционного покрытия. / Нефть, газ и нефтехимия, №3, 1986, С. 72-75.
- Закон Украины «Об охране труда» 2694 – 12 от 14.10.1992;
- «Правила охраны труда в трубном производстве», утвержденных приказом комитета Украины по промышленной безопасности, охране труда и горному надзору от 15.10.2009 №171, зарегистрированных в Министерстве юстиции Украины 05.11.2009 за № 1037/17053.
- «Правила охраны труда в металлургической промышленности», утвержденных приказом Государственного комитета Украины по промышленной безопасности, охране труда и горному надзору от 22.12.2008 №289 , зарегистрированных в Министерстве юстиции Украины 29.01.2009 за №87/16103
- «Положения о разработке инструкций по охране труда» НПАОП 0.00–4.15–98, утвержденного приказом Министерства труда и социальной политики Украины №9 от 29.01.1998, зарегистрированного в Министерстве юстиции Украины 07.04.1998 за №226/2666.
- Электронный журнал: физикохимия поверхности и защита материалов [электронный ресурс]. – Режим доступа: http://maik.rssi.ru...
- Электронный журнал: Территория нефти и газа, [электронный ресурс]. – Режим доступа: http://neftegas.info...