Реферат за темою випускної роботи
Зміст
- Вступ
- 1. Актуальність теми
- 2. Мета і задачі дослідження
- 3. Стан коксохімічної промисловості України
- 4. Стан зарубіжного коксохімічного виробництва
- 5. Екологізація коксохімічного виробництва
- 5.1. Різновиди і джерела утворення шкідливих викидів коксохімії
- 5.2. Підвищення ефективності існуючої технології підготовки та коксування вугілля
- 5.3. Зниження шкідливих викидів шляхом вдосконалення технології охолодження коксу
- Висновки
- Перелік посилань
Вступ
Підвищення якості основної продукції коксохімії - металургійного коксу є одним з основних напрямів скорочення шкідливих викидів в доменному і коксохімічному виробництвах. Це пов'язано, зокрема, з можливим скороченням споживання, а, отже, і виробництва коксу кращої якості. P>
Різке посилення екологічних вимог до коксохімічних підприємств, основним агрегатам та устаткування, які виробили свої нормативні терміни експлуатації, морально і фізично застаріли, стало вимагати від коксохіміків концентрації зусиль для реконструкції та технічного переоснащення підприємств з вирішення питань охорони повітряного і водного середовища. Тому вдосконалення технологічних процесів коксохімічного виробництва має здійснюватися на основі комплексних еколого-економічних оцінок. P>
1. Актуальність теми
Актуальність даної теми зумовлена тим, що в даний час в Україні функціонує 13 великих коксохімічних підприємства, 7 з яких зосереджені в Донецькій області. Екологічні проблеми посилюються ще і тим, що ці підприємства розташовані в регіонах зі значною концентрацією промислового виробництва і високою щільністю населення. Вкрай несприятлива екологічна обстановка, що склалася в останні роки у великих металургійних центрах, в певній мірі обумовлена ??низькими темпами технічного переозброєння коксохімічної підгалузі, повільним впровадженням у практику нових технологічних процесів, сучасних агрегатів і устаткування [ 1 ].
Коксохімічне виробництво займає «провідне» місце за різноманітністю, високої токсичності і специфічного задушливого запаху багатьох газоподібних викидів, скидів і твердих відходів. До них відносять пил, оксиди азоту, діоксид сірки, оксид вуглецю, аміак, фенол, бензол, нафталін, сірководень, ціаністий водень і графіт. Тому найважливішим соціальним завданням, що стоїть перед коксохімічними підприємствами, є підвищення екологічної безпеки виробництва, технічне переоснащення коксохімічних підприємств, здійснення великомасштабної програми будівництва природоохоронних об'єктів, впровадження сучасних екологічно безпечних технологічних процесів.
На сучасних заводах впроваджують передові технології, що дозволяють знизити викиди забруднюючих речовин в атмосферу. До основних з них відносять установки бездимної завантаження вугільної шихти в камери коксування, установки безпилової видачі та сухого гасіння коксу. Однак, останнім часом все більшої актуальності набуває вдосконалення технологічних процесів на всіх стадіях виробництва коксу (підготовка, завантаження, коксування вугілля, видача, охолодження і сортування коксу). Цим стадіям виробництва коксу належить зараз більше 70% залпових викидів. При розробці та впровадженні природоохоронних заходів особливу увагу також звертають на оновлення коксових батарей.
Підвищення якості основної продукції - металургійного коксу є одним з найбільш перспективних напрямків екологізації коксохімічного і доменного виробництв. При використанні в доменній плавці більш якісного коксу значно зменшується потреба в ньому, а отже з'являється можливість виведення з експлуатації зношених коксових батарей з природним зниженням виробництва коксу та спадом сполучених з ним викидів, скидів і твердих відходів.
Найкращі світові технології припускають вдосконалення процесів підготовки шихти: трамбування вугільної шихти перед завантаженням у коксові печі і регулювання її вологості.
Виходячи зі сказаного, зниження шкідливих викидів на всіх стадіях виробництва коксу є актуальним завданням.
2. Мета і задачі дослідження
Метою є дослідження технологічних процесів та визначення раціональних технологій виробництва коксу, що дозволяють підвищити якість коксу й одночасно скоротити шкідливі викиди.
Для досягнення поставленої мети необхідно вирішити такі завдання:
- Вивчити сучасні вітчизняні та зарубіжні технології виробництва коксу;
- Розглянути можливі способи екологізації традиційної технології коксування;
- Проаналізувати різні методи підготовки вугільної шихти до коксування і визначити оптимальний склад сировини потрібної якості;
- Дати характеристику факторам, що впливають на основні характеристики металургійного коксу, та розробити пропозиції щодо поліпшення якості коксу;
- Пошук оптимальних шляхів вдосконалення технологічних процесів виробництва коксу;
- Розрахувати економічний і екологічний ефект від впровадження технології виробництва високоякісного коксу.
Об'єкт дослідження : існуючі технології виробництва коксу в коксових батареях
Предметом дослідження є технологічні процеси виробництва коксу та методи покращення якості вихідної сировини.
3. Стан коксохімічної промисловості України
Коксохімічна промисловість є однією з основних підгалузей гірничо-металургійного комплексу (ГМК) України і призначена забезпечувати доменне виробництво необхідною кількістю коксу, а також широким спектром продукції для хімічної галузі, кольорової металургії та ін З 81 млн. т рядового вугілля, видобутого в Україні, 37,5% припадає на частку коксівного.
У країні працюють 14 коксохімічних підприємств (КХП), на яких в експлуатації перебувають 57 коксових батарей. Їх середній вік становить 24 роки. 63% від загальної кількості печей мають термін експлуатації більше 20 років (нормативно-амортизаційний термін батарей), а 20% - понад 35 років.
Основні фонди коксохіміческогo виробництва в більшості своїй виробили експлуатаційний потенціал, фізично і морально застаріле основне і допоміжне обладнання не відповідає сучасним вимогам і здобутків світової науки і практики в галузі охорони навколишнього середовища, праці та техніки безпеки.
Основним напрямком у вирішенні проблеми захисту навколишнього середовища є вдосконалення технологічних процесів з доведенням їх до безвідходного або маловідходного виробництва. Однак, враховуючи, що існуюча технологія коксування збережеться в найближчі роки, основним завданням щодо захисту навколишнього середовища в коксохімічному виробництві є виведення з експлуатації застарілих агрегатів і устаткування та заміні їх сучасними, оснащеними ефективними природоохоронними установками.
Найбільш гостро стоїть проблема якості коксу. Низька якість вітчизняного коксу є основною причиною його перевитрати в доменному виробництві. Згідно з рейтингом якості коксу різних країн і фірм, виконаному українською асоціацією виробників чавуну і думку основних споживачів, коксохімічні підприємства України виробляють найгірший у світі кокс, як за характеристиками міцності, так і за хімічним складом.
Український кокс не відповідає світовим стандартам за хімічним складом (він має більш високий вміст сірки - 1,3-1,5%), технічними характеристиками (зольність - 10-12%), а також міцності властивостями, які оцінюються показниками холодної міцності М 40 , М 25 та стиранням М 10 . У світовій практиці в якості основних показників якості все частіше використовують визначаються за методом фірми «Ніппон Стіл» реакційну здатність (CRI) і термомеханічну міцність (CSR) - міцність нагрітого до 1100 °С коксу після його взаємодії з діоксидом вуглецю.
За європейськими стандартами високоякісний доменний кокс повинен мати наступні показники:
— високу міцність у холодному стані М 40 > 80% при М 10 < 7,0%;
— низьку реакційну здатність CRI < 25-30%;
— високу міцність в гарячому стані CSR > 60-70%.
Згідно з дослідженнями УХІНу, якість українського коксу, одержуваного з звичайної сировини, при оцінці за методом «Ніппон Стіл», майже в два рази нижче якості коксу зарубіжних фірм Німеччини, Австрії, а також Росії [ 2 ].
Український державний науково-дослідний вуглехімічний інститут виконує великий комплекс робіт з природоохоронної тематики для коксохімічних підприємств України. Так, розроблені галузеві питомі викиди (показники емісії) для основного виробництва КХП, а також безпосередньо для конкретних підприємств; технологічні нормативи викидів з коксових печей, устаткування для помолу вугілля та виробництва вуглехімічний продуктів коксування. На підставі комплексних досліджень по викидах забруднюючих речовин з димових труб коксових та пекококсових батарей, котельних установок, що працюють на коксовому газі, а також з інших джерел нами запропоновані технологічні нормативи для діючого обладнання з урахуванням його віку і технічного стану. Розроблено перспективні технологічні нормативи з урахуванням будівництва нових коксових батарей і нормативів, встановлених для аналогічних виробництв у європейських країнах.
Великий обсяг робіт виконується по інвентаризації викидів забруднюючих речовин з рекомендаціями щодо їх зниження, з розробки обгрунтовуючих документів для отримання дозволу на викиди забруднюючих речовин.
У найближчій перспективі планується впровадження технології з вдування не менше 5 млн. т на рік пиловугільного палива в доменну піч, що призведе до зменшення споживання коксу на 4 млн. т. Бажане скорочення виробництва коксу має забезпечити зменшення валових викидів до 15 тис. т на рік. Очищення коксового газу від сірководню до 0,5 г/м3 на більшості коксохімічних заводів знизить викиди сірчистого ангідриду більш ніж на 5 тис. т. Оптимізація виробництва коксу дозволить повністю виключити некваліфіковане використання надлишків коксового газу, так як весь він буде витрачатися на обігрів коксових батарей та іншого паливовикористовуючого обладнання, виробництво пари та електроенергії.
Технічна політика коксохімічної підгалузі грунтується на постійному впровадженні останніх досягнень в області технології коксування і переробки вуглехімічний продуктів з обов'язковою розробкою природоохоронних заходів, що дозволяє істотно знизити екологічне навантаження на населення та навколишнє середовища в містах, де розташовані коксохімічні підприємства [3].
4. Стан зарубіжного коксохімічного виробництва
Традиційна технологія виробництва коксу в печах камерного типу з непрямим обігрівом в результаті постійних удосконалень протягом всегo періоду свого розвитку досягла до теперішнього часу практично граничного рівня технічного прогpесса. Основними досягненнями сучасного коксохімічного виробництва є:
— висока одинична потужність коксових батарей (l, 0 - 1,2 млн т/рік) в результаті збільшення габаритів коксових печей (корисний обсяг пічної камери досягає 70-80 м 3 , висота збільшена до 7,85 м, довжина - до 18 м, ширина - до 620 мм);
— освоєння ефективних процесів підготовки вугільної шихти до коксування (часткового брикетування, підсушування і термічної підготовки, вимоги, контрольованого виборчого подрібнення та ін), що забезпечило поліпшення якості одержуваного коксу і дало можливість знизити витрату дорогих добре спекаються вугілля і витрати на шихту в результаті збільшення частки слабоспекающихся і неспекающегося вугілля в шихті для коксування; p>
— підвищення рівня автоматизації виробництва коксу, що дозволяє вирішувати проблему забезпечення коксохімічного виробництва обслуговуючим персоналом;
— скорочення приблизно на 40% енерговитрат на виробництво коксу в результаті застосування технології сухого гасіння коксу та освоєння інших енергозберігаючих технологій (у тому числі впровадження автоматизованих систем керування тепловим режимом коксування);
— розробка і впровадження нових технологій, що запобігають або скорочують освіта пилогазових викидів на коксових батареях, а також оснащення коксових батарей ефективним пиловловлювальним і газоочисним обладнанням з метою максимально можливого ступеня захисту навколишнього середовища (на сучасних батареях практично на 100% усунені викиди при завантаженні коксових печей; з 0,5-1,0 кг / т до менше 5 г / т знижені викиди пилу при вьдаче коксу з печей; скорочено обсяги неорганізованих пилогазових викидів) [4].
В області науки, техніки і технології коксохімічного виробництва безперечним лідером науково-технічного прогресу є Німеччина. В інших країнах Західної Європи коксохімічне виробництво також переживає стадію серйозної реорганізації, хоча стратегічна концепція тут відмінна від німецької. Якщо процес структурної перебудови в Німеччині йшов по шляху будівництва нових коксових батарей високої продуктивності і технічного рівня, то інші країни Євросоюзу (Бельгія, Нідерланди, Іспанія, Франція, Італія, Швеція, Великобританія) провели (або проводять) перебудову коксової галузі, головним чином, шляхом ремонту та реконструкції діючого печногo фонду.
В останнє десятиріччя розвиток коксохімічного виробництва Японії xapaктерізуется прогpесуючим зниженням виробничих потужностей в умовах їх надлишку і Eстественно старіння пічного фонду (після 1982 нові батареї в країні не вводили). Значний прогрес в коксохімічному виробництві Японії досягнутий в тexнологіях, що забезпечили розширення сировинної бази коксування і продовження ефективного терміну служби коксових печей. Серед технологій, що забезпечили збільшення використання слабспекающіхся і полуспекающіхся вугілля в шихті для виробництва коксу, в Японії, крім впроваджених у 70-80-e роки технологій підготовки шихти до коксування шляхом її часткового брикетування (на 16 коксових батареях), виборчого дроблення (на чотирьох батареях ), термоподоготовкі (на одній батареї), в 90-e роки отримала подальше поширення ефективна технологія СМС peгyлірованія вологості вугільної шихти шляхом її часткової підсушування (застосовується на 22 коксових батареях) [5 ].
5. Екологізація коксохімічного виробництва
5.1. Різновиди та джерела утворення шкідливих викидів коксохімії
Технологічна схема виробництва коксу полягає в наступному: вибрані вугілля просівають, розмелюють до розміру < 3 мм і змішують в залежності від їх петрографії для виробництва високоякісного коксу з найбільш ефективних за вартістю вугілля. Суміш завантажують в пічні камери, де кокс формується завдяки руйнуючої дистиляції вугілля при температурах 1100 °C і вище. По закінченні циклу коксування гарячий кокс виштовхується з печі в вагон для гасіння, який транспортує його до башти гасіння для охолодження та стабілізації. Гасіння проводиться за допомогою води (мокре гасіння) або азоту (сухе гасіння). Потім кокс транспортується до доменної печі або укладається в штабелі [ 6 ]. Спрощена схема процесу виробництва коксу наведена на мал. 1.
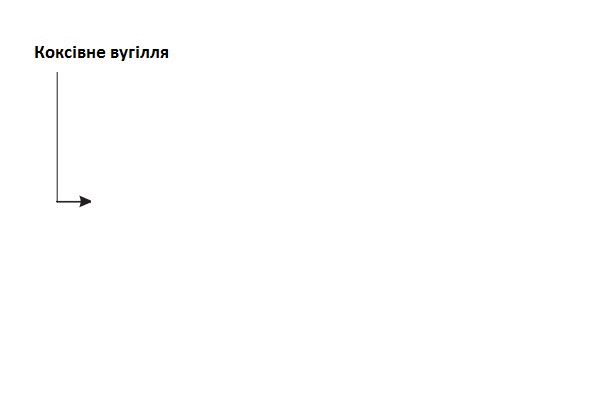
Рисунок 1 - Технологічна схема виробництва коксу
Основний комплекс технологічних процесів коксової батареї (підготовка, завантаження, коксування шихти, вивантаження, гасіння і обробка коксу) є джерелом 75-80% і більше викидів коксохімічного виробництва, 30% утворюється у відділеннях обробки коксового газу.
Коксохімічне виробництво займає провідне місце за різноманітністю і токсичності газоподібних викидів, скидів і твердих відходів. Якщо при виробництві окускованного рудної сировини (агломерату та обкотишів), чавуну, сталі, прокату контролюють в основному викиди пилу, оксидів вуглецю, сірки та азоту, то в коксохімічному виробництві додатково визначають концентрації в технологічних, аспіраційних газах і атмосферному повітрі ще мінімум 7-10 шкідливих речовин: аміак, сірководень, фенол, бензол, ціаністий водень, нафталін, сажистий вуглець.
Відділення підготовки та коксування вугілля є основними джерелами газопилових викидів. Забруднені стічні води формуються в основному у відділеннях обробки «брудного» коксового газу і, у значно меншою мірою, в цехах переробки хімічних продуктів коксування.
Відділення спеціальної підготовки вугілля, що включає процеси складування, усереднення, дроблення, дозування, збагачення, змішування і транспортування вугілля, характеризується, головним чином, великим пиловиділенням, що досягає 480-500 г/т коксу. При збагаченні вугілля утворюється до 35-40% від їх маси твердих відходів, з яких 30-50% складає відходи флотації - вугільні шлами з вологістю до 50-60%.
Завантаження вугільної шихти з вологістю 7-9% і більше в розпечені коксові печі з температурою гріючих стін 1100-1200 °С супроводжується утворенням залпових викидів парогазової суміші у кількості 3-5м3/т шихти, яка забирає в атмосферу шкідливі речовини, в кількості, г/т коксу: 400 пил; 46 СО; 22 Н 2 S; 17NH 3 ; 0,6 HCN; 1,1 C 6 H 5 OH; 190 C n H m ; 32 SO 2 і 55 NO x .
Дуже важлива правильна експлуатація коксових печей. Порушення режимів нагріву, несолюденіе пропорцій, правильної шихтовки, тобто планування вугільної шихти і недоведення до кінця процесу коксування, все це може призвести до ЗНОС печі, утворення тріщин і прогарів в кладці стін. У цьому випадку значну кількість газу з камер коксування потрапляє в опалювальну систему. Вуглеводні прямого коксового газу в опалювальній системі розкладаються з утворенням Н 2 і сажистого вуглецю. У результаті з димових труб коксових батарей видаляються гази, пофарбовані густим чорним кольором сажі, яка є дуже концерогенність.
Видача коксу з камер коксування в гасильний вагон призводить до залповим, протягом 30-40с газопиловим викидам, г / т коксу: 750 пил; 7,6 H 2 S; 51 NH 3 ; 0,5 C 6 H 5 OH; 22 SO 2 ; 3,6 NO x ; 36 C n H m , 0,1 HCN. При русі гасильного вагона з вивантаженим з печі палаючим коксівним спеком до установки мокрого або сухого гасіння в атмосферу виділяються шкідливі запилені гази в кількості приблизно 100 м 3 / т коксу. Концентрація окремих забруднювачів в цих газах становить, г / м 3 : 110 пил; 31 CO; 16 SO 2 ; 0,2 Н 2 S ; 2,9 NO x ; 70 C n H m . Багато інших інгредієнти викидів не досліджені [ 7 ].
5.2. Підвищення ефективності існуючої технології підготовки та коксування вугілля
Головним напрямком подальшого зростання ефективності коксового виробництва стає eгo інтенсифікація. Відповідно до теорії шарового процесу, в основу технологічних рішень для цієї мети повинні бути покладені розробки, що сприяють підвищенню спікливості вугілля, зниження загальної напруженості в коксованої масі, отриманню коксу однорідної структури. Найбільшою мірою цим умовам відповідає виборче подрібнення з пневмосепарації і термічна підготовка шихт.
Роздільне, послідовне здійснення при підготовці вугільної шихти до коксування, спочатку, шляхом її виборчого подрібнення з пневматичною сепарацією, а потім - термічним нагріванням нераціонально, так як: при нагріванні подрібненої шихти газовим теплоносієм з неминучим залишковим киснем, у присутності парів води, відбувається окислення новоствореної поверхні зерен вугілля, що знижує їх спікливість: нерівномірно нагріваються різні класи крупності [ 8 ].
Одним з напрямків інтенсифікації коксохімічного виробництва на основі науково-технічного прогресу є глибока сушка і термічна підготовка вугілля. Глибока сушка пов'язана з видаленням практично всієї вільної вологи, а термічна підготовка - це нагрів шихти до 150-250 ° С. У результаті глибокої сушки та термічної підготовки шихти для коксування відбуваються суттєві зміни її властивостей, що безпосередньо впливає на хід коксування, механізм термохімічних перетворень вугільного завантаження і якість коксу.
Основною метою термічної підготовки вугілля і шихт є підвищення продуктивності коксових печей і залучення в сировинну базу коксування слабоспекающихся вугілля. Незмінний склад шихти сприяє поліпшенню якості коксу і підвищенню газопроникності його насипної маси. При цьому ефект впливу термічної підготовки тим значніше, чим гірше спікливість вугілля. Наприклад, при термічній підготовці вугілля марок Г і ОС газопроникність насипної маси коксу збільшується відповідно на 23 і 13,6%, в той час як термічна підготовка вугілля марки Ж сприяє збільшенню газопроникності коксу всього лише на 4%. Аналогічна картина спостерігається і для шихти. Якщо при термічній обробці шихти за участю вугіль Г 6 + ОС 70% газопроникність коксу збільшується на 23%, то для коксу з шихти за участю вугілля марки г 6 26% цей показник збільшується тільки на 1 3%. [ 9 ].
Увага, яка приділяється цьому методу, пояснюється тим, що при його реалізації створюється можливість: значно інтенсифікувати процес шарового коксування - підвищити продуктивність коксових печей; використовувати в шихті для коксування значно більше слабоспекающихся вугілля; поліпшити техніко-економічні показники виробництва коксу при деякому підвищенні його якості.
Крім зазначених основних переваг цього методу можна ще назвати зниження витрат теплоти на коксування, зменшення термічних ударів на вогнетривку кладку камер коксування, зниження навантажень на конденсаційну апаратуру хімічних цехів у зв'язку із зменшенням кількості водяної пари в коксовому газі, а також значне скорочення кількості стічних вод.
Метод термічної підготовки вугілля перед коксуванням є одним з найбільш ефективних серед інших нових методів інтенсифікації виробництва коксу. Нагріта до 200-250 °С шихта втрачає більше 90% вологи, і насипна щільність її збільшується на 15-20%.
Найбільш різко підвищується насипна маса трамбуванням шихти. У трамбовочную машину шарами завантажується подрібнена шихта, а отримуваний вугільний блок вдвигается в камеру коксової печі. Якщо при звичайному завантаженню насипом можна досягти насипної маси до 0,85 т / м 3 , то щільність трамбувати вугільного блоку складає 1,0-1,1 т / м 3 . Трамбування шихти істотно впливає на коксованість: зменшується крупність шматків, збільшується міцність тіла коксу, змінюється тріщинуватість.
5.3. Зниження шкідливих викидів шляхом вдосконалення технології охолодження коксу
Першим процесом підготовки коксу для доменних печей є охолодження (гасіння) до температур, при яких можливі його транспортування та сортування. При гасінні властивості коксу змінюються. Отже, гасіння являє собою перший посткоксовальний процес формування властивостей доменного коксу.
Відомі два способи гасіння: сухе і мокре. Установки сухого гасіння і мокрого гасіння коксу представлені на рис. 1, 2. Мокре (охолодження коксу водою) стали застосовувати з появою процесу виробництва коксу. Цей спосіб поки що застосовується на підприємствах України, хоча в багатьох відношеннях є відсталим. Більш прогресивним є сухе гасіння коксу - поступово впроваджується в практику на зарубіжних і вітчизняних підприємствах [ 10 ].
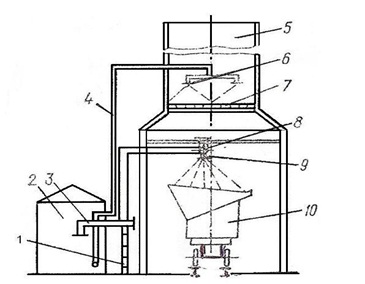
1 - колона з опорою під трубопровід; 2 - насосна гасильним вежі, 3 - трубопровід для подачі води на гасіння, 4 - трубопровід для подачі води на промивку насадки Каплевідбійники від коксового пилу; 5 - гасильним залізобетонна вежа; 6 - форсунки для промивання насадки Каплевідбійники; 7 - дерев'яна насадка Каплевідбійники; 8 - колектор зрошувального пристрою; 9 - форсунка зрошувального пристрою; 10 - гасильний вагон.
Рисунок 2 - Схема установки мокрого гасіння коксу
Мокре гасіння коксу має ряд великих недоліків, серед яких: величезні шкідливі викиди, знижена, через різке охолодження, міцність, підвищена і непостійна вологість товарного коксу, повна втрата теплоти розпеченого коксу. Вихід запилених парогазових викидів від установок мокрого гасіння коксу досягає 600 - 650 м3 /т коксу, питомі викиди в середньому становлять, г/т коксу: 20 H2S; 42 NH3; 89 C6H5OH; 9 HCN.
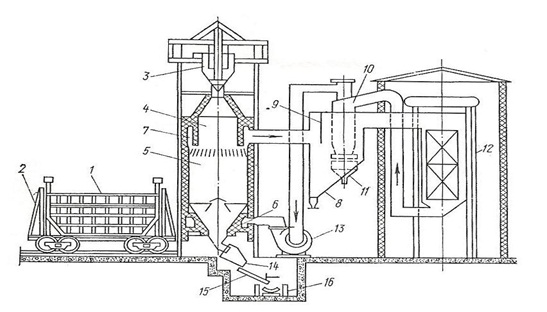
1 - гасильний вагон; 2 - напрямні стійки, 3 - завантажувальний пристрій, 4 - форкамера; 5 - камера гасіння; 6 - газокамера; 7 - кільцевий відвід газів; 8 - пилеосадітельних камера; 9 - перегородка; 10 - циклон; 11 - бункер циклону; 12 - котел-утилізатор, 13 - димосос; 14 - розвантажувальний пристрій; 15 - коксова рампа; 16 - транспортер
Рисунок 3 - Схема установки сухого гасіння коксу
Циркулюючий газ являє собою суміш горючих і негорючих складових. Поява горючих компонентів у газі обумовлено реакціями первинно утворилися продуктів горіння з розпеченим коксом, а також виділенням етучіх речовин коксу в камері УСТК. Кількість СО в газі може збільшуватися до 23-24%. Горючі компоненти в значній мірі ускладнюють експлуатацію УСТК, роблять установку вибухонебезпечною, а газ високотоксичним.
Утилізація тепла важливе, але не єдине достоїнство способу сухого гасіння. Сухе гасіння коксу має такі еколого-економічні переваги: ??
1) відсутність викидів отруйної паро-газопилової суміші в атмосферне повітря;
2) відсутність стоків забруднених токсичних вод в систему оборотного водопостачання;
3) значне поліпшення якості коксу: зниження від 3-5 до 0,3-0,4% вологості, стабілізація її рівня, підвищення міцності, поліпшення гранулометричного складу коксу.
Незважаючи на переваги УСТК, в багатьох випадках вітчизняної практики мокре гасіння продовжують використовувати як основний або резервний варіант охолодження коксу. В останні роки установки мокрого гасіння істотно модернізували, застосувавши імпульсна зрошення коксу тонкорозпиленою водою, охолодження кузова гасильного вагона знизу, відвід паро-газопилової суміші в атмосферу через діффузорного-конфузорно витяжну трубу, виготовлену, як і вся установка, із залізобетону. Однак, основна мета перетворення коксохімічного виробництва - повне виведення з експлуатації установок мокрого гасіння коксу [ 11 ].
Висновки
У зв'язку з дефіцитом енергетичних ресурсів в Україні розвиток та освоєння техніки сухого гасіння коксу набуває особливого значення і актуальність. Широке впровадження цього процесу в коксохімічному виробництві дозволить істотно поліпшити екологічну обстановку в промислових центрах і умови праці на коксохімічних підприємствах, зменшити втрати від корозії устаткування, значно підвищити якість коксу.
З'являються в найближчі 8-10 років можливості щодо істотного скорочення споживання виробництва коксу і заміною його пиловугільним паливом (частково антрацитом, коксівним, природним газом), доцільно використовувати для зносу старих, будівництва нових коксових батарей, модернізації технології виробництва коксу з метою поліпшення його якості та практично повної ліквідації газопилових викидів на всіх стадіях коксохімічного виробництва
Перелік посилань
- В. И. Рудыка, Трембач Т. Ф., Каменюка В. Б. Защита окружающей среды: основне мероприятия и их эффективность // Кокс и химия. – 2003 – №12 – С. 34-35.
- Анализ сырьевой базы металлургического производства. Стратегический аспект. Кокс доменный / Л. Ю. Назюта, Н. В. Косолап, А. В. Губанова // Металл и литье Украины . - 2005. - № 11-12. - С. 3-9.
- Ковалев Е.А. Коксохимические предприятия Украины и проблемы экологии // Деловой вестник. - 2008. - № 3 [Электронный ресурс] – Режим доступа: http://www.ucci.oгg.ua/synopsis/dv/2008/dv0803161.гu.html.
- Ухмылова Г. С. Современное состояние коксохимического производства // Приложение №3 к журналу «Новости черной металлургии за рубежом». – 2000 – с. 10 – 18.
- Антонов А. В. Технический прогресс в технологии производства кокса в Китае // ОАО «Черметинформация». Новости черной металлургии за рубежом – 2010 г., – № 4 — c. 10 – 12.
- Товсей П., Камерон Я., Гордон Я., Красавцев А. Сравнение технологий производства кокса рекуперативного типа и с улавливанием побочных продуктов коксования // Кокс и химия. – 2013 – №1 – С. 9.
- Черная металлургия и охрана окружающей среды: учебное пособие / И.М. Мищенко. – Донецк.: ГВУЗ «ДонНТУ», 2012. – c. 97-103.
- Научные основы совершенствования техники и технологии производства кокса. Сухоруков В. И. Екатеринбург. 1999 г. – с. 273-280.
- Перспективные нaпpaвлeния развития коксохимического производсва. Браун Н. В.,Глущенко И. М. – М.: Металлургия, 1989. С. 59-70.
- Мучник Д. А. Перспективы совершенствования внекамерных процессов производства кокса // Кокс и химия. – 2011 – №3 – С. 45-49.
- Мучник Д. А. Анализ состояния вопроса сухого тушения кокса // Кокс и химия. – 2011 – №2 – С. 23-31.
Важливе зауваження
При написанні даного автореферату магістерська робота ще не завершена. Остаточне завершення: грудень 2013. Повний текст роботи та матеріали та матеріали по темі можуть бути отримані у автора або його керівника після зазначеної дати.