Реферат за темою випускної роботи
Зміст
- Вступ
- Актуальність теми
- Мета і задачі
- 1. Основні напрямки розвитку технології брикетування
- 2. Стисла характеристика сировини для брикетування
- 3. Стисла характеристика в'яжучих для брикетування
- 4. Аналіз конструктивних особливостей пресів для отримання брикетів
- 5. Опис фізичної моделі штемпельного преса
- Перелік посилань
Вступ
В даний час при постійних темпах зростання промисловості значно збільшується рівень споживання природних ресурсів. Металургійна промисловість є одним з основних споживачів, зокрема залізовмісних руд. Однак разом із зростанням споживання ресурсів зростають і посилюються вимоги до якості продукції, що безпосередньо залежить від якості використовуваного сировини. У зв'язку з тим, що в природі значно зменшилися запаси багатих залізовмісних руд, тому з'явилася необхідність вдатися до переробки бідних залізовмісних руд з подальшим їх збагаченням.
Але процес збагачення руд передбачав собою мелкодисперсное подрібнення матеріалу, тому використання даного матеріалу без попереднього процесу окускования було неможливо.
З великим пониженням рівня вмісту в руді почали розвиватися технології рециклінгу металургійних відходів полягають у використанні вторинних матеріалів (залізовмісних відходів виробництва) таких як металургійний шлам, прокатна окалина і т.д. для отримання сталі. З розвитком цієї технології традиційні методи окускования такі як агломерація і обливання не могли забезпечити необхідну продуктивність і якість одержуваного матеріалу, оскільки металургійні відходи в основному находяться в пилоподібному стані. На цьому грунті в металургійній промисловості все частіше починають вдаватися до брикетування як методу окускования залізовмісних відходів виробництва.
Таким чином, в даний час брикетування отримало новий поштовх у розвитку при окускуванні залізовмісних відходів.
Актуальність теми
В останні роки в металургійній промисловості стала актуальною тема рециклінгу відходів виробництва. Одним з таких відходом є прокатна окалина. У прокатному виробництві утворюються велика кількість замасленої окалини, яка накопичується в шламозбірника. Прокатна окалина містить більше 60% заліза, тому економічно доцільно її використання в доменному та сталеплавильному процесах. Однак окалину в її початковому стані неможливо використовувати, оскільки при плавці дрібнодисперсні частинки окалини будуть вигоряти, на цьому грунті ставати питання про її окускуванні перед плавкою. Найбільш ефективним методом окускования прокатної окалини є брикетування.
Таким чином дослідження процесу й пристрої брикетування прокатної окалини в даний час є досить актуальним.
Мета і задачі
Об'єкт дослідження: процес і пристрій формування брикетів з прокатної окалини.
Мета: дослідження процесу брикетування прокатної окалини і розробка пристрою для отримання брикетів.
Для досягнення поставленої мети необхідно вирішити такі завдання:
- Проаналізувати можливий компонентний склад брикету і вибрати найбільш раціональні складові;
- Проаналізувати способи отримання металургійних брикетів і прийняти найбільш раціональний для брикетування прокатної окалини;
- Залежно від прийнятого способу брикетування спроектувати і побудувати фізичну модель брикетувального пресу;
- Провести лабораторні дослідження роботи преса в процесі виготовлення брикетів;
- Розробити методику розрахунку енергосилових параметрів спроектованого преса.
1. Основні напрямки розвитку технології брикетування
При сучасному рівні розвитку металургійного виробництва значно зростають масштаби матеріального споживання ресурсів і значення фактора повноти їх використання, тому залучення вторинних матеріальних ресурсів має першорядне значення. У зв'язку з цим вдосконалення традиційних і розробка нових технологій є необхідною умовою сталого розвитку металургії [1].
Відомі три способи окускования залізовмісних руд: агломерація, обливання і брикетування.
Агломерація – це процес окускування що полягає в спіканні тонкоподрібнених частинок руди на агломераційної машині і отриманні шматків матеріалу який підлягає подальшому дробленню на необхідні фракції.
Окативаніе – це процес огрудкування зволожених тонкоподрібнених частинок руди при якому утворюються кулясті гранули різних розмірів з наступним зміцненням – окатиші.
Брикетування – це процес окускования що полягає в пресуванні тонкоподрібнених частинок збагаченої руди із застосуванням і без застосування в'яжучих речовин у форми заданих розмірів.
Агломерація і огрудкування на відміну від брикетування набули більшого поширення так як ці технології мали досить високу продуктивність.
В даний час найчастіше застосовуються методи окускования сировини Окативаніе і агломерацією в чому вичерпали свої резерви і не можуть забезпечити необхідну продуктивність в існуючих умовах.
У зв'язку з тим, що в природі значно зменшилися запаси багатих залізовмісних руд, тому з'явилася необхідність вдатися до переробки бідних залізовмісних руд з подальшим їх збагаченням.
Процес глибокого збагачення железосодержащей руди можливий тільки при тонкому її подрібненні. Такі тонкоподрібнені концентрати для безпосередньої плавки не придатні, так як стовп дрібних шихтових матеріалів у доменній печі має низьку газопроникність, а сама плавка супроводжується інтенсивним виносом пилу. Спікання таких тонких матеріалів на агломераційних машинах протікає повільно, призводить до зниження продуктивності стрічок і погіршення якості агломерату. При роботі на одержуваному при цьому тендітному і різному за розмірами шматків агломерате не забезпечується хорошою газопроникності доменної шихти, і тим самим значно знижуються техніко-економічні показники доменних печей [2].
Так, при існуючому технічному рівні складно отримати металлізованних агломерат або міцні окатиші з високим вмістом вільного вуглецю. У той же час подібні матеріали виготовляють за допомогою брикетування. Однак брикетування в чорній металургії поки ще не отримало належного визнання. В основному це брикетовані металізованої матеріали, флюси і феросплави для виробництва сталі.
Брикетування має ряд істотних переваг, які в умовах, розвитку металургії дозволяють вважати його перспективним методом окускования. До їх числа відносяться наступні [1]:
- Брикетування пред'являє менш жорсткі вимоги до якості сировини, дозволяє окусковивать матеріали широких класів крупністю менше 10 мм, практично в будь-яких пропорціях і складах.
- Процес брикетування технологічно простий; деяку складність представляє лише дозування сполучних і їх змішування з брікетіруемим матеріалом.
- При брикетуванні зберігаються властивості компонентів, що входять у брикети.
- Брикетування є екологічно чистим способом окускования.
- Брикетування розширює сировинну і паливно-енергетичну базу металургії, дозволяє ширше впроваджувати позадоменні методи отримання заліза.
Ці переваги дозволяють ефективно вирішувати такі актуальні завдання, як отримання нових, комплексних видів сировини, що включають оксиди заліза, відновник і флюс, впровадження ефективних способів обробки сировини, наприклад, металізацією, зниження шкідливого впливу металургійних процесів на навколишнє середовище.
До основних недоліків брикетування зазвичай відносять наступні [1]:
- Недостатня міцність брикетів, особливо при високих температурах і в умовах відновної атмосфери.
- Використання в'яжучих, що містять шкідливі домішки і мають недостатні в'яжучі властивості.
- Висока вартість якісних зв'язуючих.
- Труднощі, пов'язані з рівномірним введенням сполучних у шихту.
- Недостатня продуктивність пресового устаткування.
До теперішнього часу більшість цих проблем частково вирішені. За кордоном сформовані декілька напрямків отримання міцних брикетів, до числа яких відносять «гаряче» брикетування, високотемпературну обробку брикетів, використання термостійких сполучних.
2. Стисла характеристика сировини для брикетування
У металургійному виробництві використовують велику кількість матеріальних ресурсів.
За призначенням і характером брікетіруемие металургійні матеріали діляться на основні і допоміжні.
Основні матеріали становлять головний зміст брикету, наприклад, руди, концентрати, відходи металургійного виробництва.
Допоміжні матеріали використовують у процесі виробництва брикетів як додаткові, поліпшують технологічний процес і якість отриманих брикетів. До допоміжних матеріалів відносяться флюси, легуючі добавки та ін
Паливне сировина може бути як основним, так і допоміжним матеріалом при брикетуванні. В якості паливної сировини може виступати вугільний пил, коксовий дріб'язок, бій електродів і т.д.
За джерелами утворення всі матеріали поділяють на первинні, свіжі матеріали та оборотні, вторинні матеріали або відходи. До оборотних матеріалів відносять використовувані відходи, просипу, повернення, побічні і попутні продукти.
Під відходами металургійного виробництва в широкому сенсі слова слід розуміти сировину, матеріали та енергоресурси, в силу тих чи інших причин не використані для отримання основної продукції. Відходи є неминучим елементом існуючої технології виробництва металів [1].
До рудному сировини відносяться руди такі як:
- Залізні руди;
- Марганцеві руди;
- Хромові руди;
- Никілеві;
- Мідні і т.д.
Зокрема для чорної металургії промислову цінність представляють залізні руди.
Залізні руди класифікують за типом рудного мінералу, найбільш поширені такі різновиди мінералів [2]:
- Водні оксиди заліза – оксиди заліза хімічно пов'язані з водою (лимоніт Fe2O3×3H2O, турьіт 2Fe2O3×H2O). У чистому вигляді вміст заліза в них становить від 52% до 66%.
- Безводні оксиди заліза Fe 2O3 – представлені гематитами і мартитом, в чистому вигляді містять 70,1% Fe.
- Магнетит Fe 3O4 – магнітна окис заліза. У чистому вигляді містить 72,4% Fe, утворюють магнітний залізняк і магнетит та ін
До брікетіруемим відходам металургійного виробництва відносять:
- Колошниковий пил.
- Дрібний металевий лом.
- Окалина.
- Металева стружка і т.д.
Окалина – це пластинчаті частинки різної товщини складаються з оксидів заліза, а також гематиту і магнетиту. За хімічним складом окалина близька до чистого магнетиту (65-72% Fe). У металургії окалина утворюється при сталеливарному виробництві і при холодної або гарячої прокатці сталі. Приміром, у прокатному виробництві вихід окалини становить в середньому 1,0-3,0% від маси готового прокату.
3. Стисла характеристика в'яжучих для брикетування
При брикетуванні багатьох видів подрібненого сировини, що володіє недостатніми аутогезіоннимі властивостями, навіть при високих тисках (180 МПа і більше) звичайним холодним пресуванням отримувати міцні брикети без їх спікання не представляється можливим. У таких випадках використовують сполучні – допоміжні матеріали, що покращують злипання частинок і підвищують міцність брикетів до заданого рівня [1].
Оскільки добавки таких матеріалів можуть становити від кількох до 10% і більше, вони повинні відповідати наступним вимогам [2, 3]:
- Володіти високими аутогезіоннимі властивостями, тобто забезпечувати високу холодну і гарячу міцність при мінімальній витраті сполучного.
- Забезпечувати швидку схвативаемость.
- Вносити мінімальна кількість шкідливих, баластних та інших домішок, небезпечних для обслуговуючого персоналу і знижують якість кінцевого продукту.
- Чи не погіршувати умов плавки брикетів.
- Бути поширеними і мати невисокою вартістю.
- Не вимагати складних прийомів і операцій з їх використання.
- Забезпечувати мінімальну вологостійкість.
Сполучні підрозділяють на три типи:
- Мінеральні (неорганічні);
- Органічні;
- Комбіновані.
До поширених неорганічним сполучною слід віднести гашене вапно, рідке скло, глиноземистий і портландский цементи. Однак багато з них володіють істотними недоліками. Так, гашене вапно і портландцемент при нагріванні віддають гідратну вологу і втрачають міцність, рідке скло містить значну кількість лугів і двоокис кремнію, а глиноземистий цемент до того ж надзвичайно доріг.
До поширених органічним зв'язуючим відносять кам'яновугільні і нафтові смоли, меляса, відходи гідролізної і целюлозної промисловості тощо Загальним недоліком органічних сполучних є їх піроліз чи вигоряння при високих температурах з втратою міцності, а також вносити до брикети значної кількості сірки.
До комбінованих сполучною відносять суміші різних зв'язуючих. Ці суміші дозволяють поліпшити позитивні і знизити негативні властивості. Наприклад, суміш, що містить рідке скло і лигносульфонат, вносить знижена кількість лугів, кремнезему або сірки, ніж кожне сполучна окремо, при одночасному забезпеченні високої механічної міцності брикетів.
В якості в'яжучих переважніше використовувати найбільш поширені і добре досліджені матеріали:
- Вапно гашене (портландіт);
- Рідке скло;
- Портландцемент;
- Глиноземистий цемент;
- Магнезійний цемент;
- Бішофіт;
- Бентоніт;
- Меляса;
- Кам'яновугільний пек.
Вапно, або оксид кальцію СаО в техніці називають негашеним або паленої вапном, яка при взаємодії з водою утворює гашене вапно, що володіє високими в'яжучими властивостями. Гашене вапно є порівняно дешевим, досить міцним і добре смешивающимся сполучною і одночасно флюсів матеріалом Основним недоліком гашеного вапна є те, що при нагріванні до 580 оС С починає віддалятися гідратна волога, через що міцність брикетів падає [1].
Рідке скло натрієве за ГОСТ 13078-81 містить в середньому 30% SiO2, 13% Na2O, 0,8% домішок Al2O3, SO3 і CaO, інше – вода. Добавки рідкого скла в кількості 5-7% (понад 100%) дають після сушіння досить міцний брикет, а що утворюється при нагріванні фаяліт сприяє утворенню рідких фаз. Істотним недоліком рідкого скла є значне підвищення в брикеті вмісту діоксиду кремнію і лугів.
Бішофіт MgCl2×6H2O, віддаючи при прожаренні вологу, перетворюється у виключно міцну кристалічну сіль MgCl2, яка може виступати не тільки в якості сполучного, але і речовини, що перекладає цинк у легколетучие з'єднання. Недоліком даного сполучного є те, що після прожарювання він поступово, приєднуючи вологу з повітря, розтікається, а брикет втрачає свою первісну міцність [4].
Бентоніт володіє хорошими в'яжучими властивостями. Його основою є монтморилоніт Al1,67Mg0,33×[(OH)2Si4O10]0,33×Na0,33(Н2О)4, який при розчиненні у воді утворює надзвичайно дисперсні колоїдні частинки, що володіють високими аутогезіоннимі властивостями, питома поверхня яких складає 600-900 м2/г. Його широко використовують при виробництві окатишів. Витрата бентоніту становить зазвичай 0,5-1,5% від використовуваного концентрату [4].
Меляса (патока кормова) є відходом цукробурякового виробництва, а тому відносно дешева і недефіцитних. Вміст сірки помірне [5]. Як сполучна, меляса володіє задовільними в'яжучими характеристиками. Добавки 7% меляси (понад 100%) дозволяють отримувати не тільки міцний брикет, але і знизити вміст відновника на 2%. Ізвлекаемость брикетів з прес-форми задовільна. Міцність на роздавлювання лабораторних брикетів з добавкою 7% меляси, сушених при 250 оС протягом 0,5 год, доходить до 40 МПа.
Незважаючи на те, що істотним недоліком даного сполучного є незадовільний змішування з основними компонентами брикетів, мелясу, поряд з рідким склом, слід віднести до найбільш ефективних видів зв'язуючих. Комбіноване сполучна, складене з суміші цих матеріалів може виявитися дуже перспективним [1].
Кам'яновугільний пек представляє собою тверде, крихке речовина чорного кольору, що є залишком перегонки кам'яновугільної смоли, здійснюваної на коксохімічних заводах. Щільність пеку 1100-1240 кг/м3, температура розм'якшення 50-140 оС (залежно від марки), температура займання 230-300 оС. Його зазвичай використовують при брикетуванні вугілля [2, 3].
4. Аналіз конструктивних особливостей пресів для отримання брикетів
Брикетні преси є основним обладнанням, які реалізують однойменний метод окускования сировини. У зв'язку з актуальністю окускования надзвичайно різноманітної сировини було розроблено значну кількість різних видів пресів, що відрізняються конструктивними особливостями.
У металургії найбільше поширення отримали наступні типи пресів:
- Вальцові;
- Штемпельні;
- Важільні;
- Кільцеві.
Вальцові преси є найбільш поширеними. Вони володіють високою продуктивністю до 100 т брикетів на годину і більше, розвивають великі тиску пресування (до 150 МПа), що дозволяють отримати досить міцні брикети, прості в управлінні і легко автоматизуються.
Принцип дії таких пресів представлений в [2, 7], див рис 1.
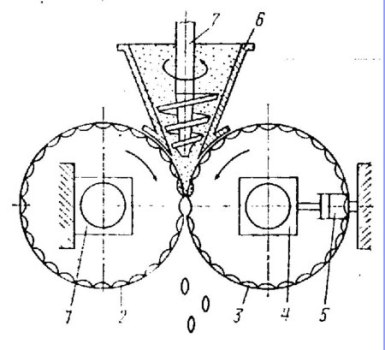
Рисунок 1 – Конструктивна схема вальцьових пресів.
1 – нерухома опора; 2, 3 – валки; 4 – плаваюча опора, 5 – гідроциліндр; 6 – завантажувальна воронка; 7 – конічний шнек подпрессовочного механізму.
Він полягає в тому, що шихта прямує в зазор між двома вулицями, обертовими назустріч один одному. При обертанні вальців відбувається зближення осередків, захоплення шихти та її ущільнення. При подальшому обертанні вальці розходяться, і брикети під власною вагою і невеликим розширенням після зняття тиску випадають з осередків. Поряд з простотою формоутворення вальцьові преси мають ряд недоліків. Зокрема, суттєвим недоліком вальцьових пресів є відсутність повного закриття формуючих елементів, а також невикористання фактора витримки матеріалу, що пресується під тиском, що призводить внаслідок цього до недобору брикетами міцності. При брикетуванні пухких сумішей, що володіють великою усадкою (40-50% і більше), необхідно використання двоступеневої схеми пресування з використанням подпрессовшіков-ущільнювачів різних систем.
Форма брикетів, одержуваних на вальцьових пресах, – переважно подушкообразной, проте може бути й інша форма. Наявність подушкообразной форми пояснюється максимальним використанням корисної поверхні вальців.
Штемпельні преси використовують для середніх обсягів виробництва продукції, невеликих і середніх розмірів брикетів, а також високих тисків пресування (120-150 МПа). Вони випускаються з 1-4 штемпелями.
Недоліком таких пресів є їх великі розміри, матеріаломісткість і відносно високий витрата електроенергії, а також швидке стирання матриць абразивними частинками. Тривалість циклу пресування завищена – 10-14 с [6]. В даний час, у зв'язку з розвитком техніки і виробництва зносостійких сталей, більшість з цих недоліків значною мірою усунути.
Процес пресування на штемпельних пресах відбувається в нерухомій матриці в наступному порядку [3], див рис 2.
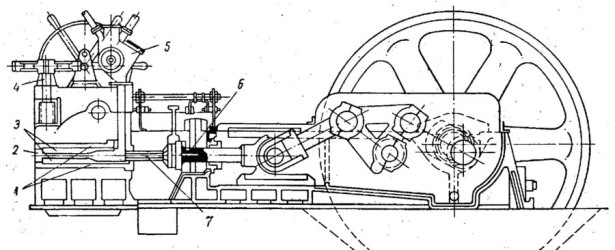
Рисунок 2 – Конструктивна схема штемпельного преса.
1 – рама матриці; 2 – вихід брикетів; 3 – матриця; 4 – натискний гвинт, 5 – дозатор; 6 – п'єзоелектричний датчик; 7 – штемпель.
Брікетіруемий матеріал подають у матричний канал, обжимают його в просторі між попереднім брикетом і штемпелем до утворення нового брикету і проштовхують брикети, що знаходяться в каналі, на товщину нового брикету. Потім цикл пресування повторюється.
Форма брикетів, одержуваних у штемпельному пресі, має вигляд циліндрів з плоскопараллельнимі підставами. Твірна брикетів визначається формою матричного каналу і може бути круглої, овальної або іншого виду.
Важільні преси використовують у разі, коли потрібні брикети великих розмірів, а обсяги їх виробництва не великі.
Пристрій важільного преса наведено в [3], див. рис. 3.
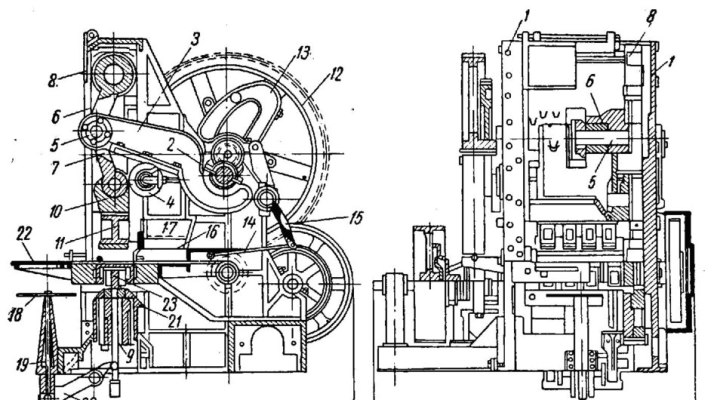
Рисунок 3 – Конструктивна схема важільного преса.
1 – рама преса; 2 – колінчастий вал, 3 – важіль; 4 – опорний ролик; 5 – вісь важеля; 6 – верхній шатун; 7 – нижній шатун; 8 – з'єднувальні штанги; 9 – нижній крейцкопф; 10 – верхній крейцкопф; 11 – верхній штамп; 12 – циліндрична шестерня; 13 – куліса; 14 – тяга живильника; 15 – важіль живильника; 16 – живильник; 17 – бункер для шихти; 18-21 – механізм регулювання глибини завантаження форм; 22 – стіл; 23 – нижній штамп.
Преси даного типу можуть виготовляти брикети у вигляді цегли висотою 65-88-138 мм і розмірами основи 120 ? 250 мм з шихти вологістю 8-12%, з коефіцієнтом стиснення, рівним 2, за ГОСТ 530-95 і ДСТУ Б В .2.7.61-97. При необхідності брикети можуть виконуватися різної пустотілості. Прес забезпечує двостороннє пресування за рахунок вертикального переміщення рами механізму пресування.
Кільцеві преси використовують для отримання міцних брикетів з деяких видів сировини, що вимагають високих і надвисоких тисків пресування. Звичайні типи пресів таких тисків або не розвивають, або різко втрачають при цьому свою продуктивність. Для отримання таких брикетів були розроблені кільцеві преси, розвиваючі питомий тиск пресування в 200-500 МПа.
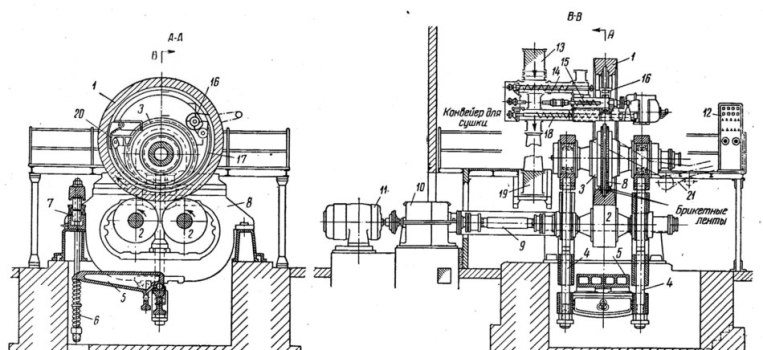
Рисунок 4 – Конструктивна схема двухленточние кільцевого преса [8].
Пресове кільце 1 приводиться в обертання двома приводними роликами 2, що виконують роль фрикційного приводу і опорою кільця, які розміщені в станині 8. Усередині кільця ексцентрично розміщений пресуючий диск 3, що обертається в ту ж сторону, що і кільце, під дією сил тертя, що виникають між стрічками брикетів. У результаті безперервного ущільнення шихти між циліндричною поверхнею каналів пресового кільця і ??циліндричної поверхнею диска шихта пресується.
На кінцях осі диск має тяги 4, з'єднані коромислом 5 і пружинами 6, які через тяги з'єднані з гідравлічним домкратом 7, що створює потрібний тиск пресування шихти. Приводні ролики обертаються від вала 9 через редуктор 10 і електропривод 11, для управління яким призначено щит 12. Завантаження шихти проводиться розподільним конвеєром 13, гвинтовими живильниками 14 і 15 і відцентровим живильником 16. Надлишки шихти надходять на конвеєри 18 і 19 і повертаються на конвеєр 13.
Спресовані брикети у вигляді двох стрічок піднімаються до розламують пристрої 20, де розпадаються на окремі брикети, які по похилому жолобу потрапляють на стрічковий конвеєр 21.
Брикети прямокутної форми з округленими ребрами мають розміри від 30×36×76 мм до 45×57×76 мм залежно від розміру паза пресового каналу. Щільність углебрікетов, одержуваних на це пресі, становить 1200 кг/м3.
5. Опис фізичної моделі штемпельного преса
Проаналізувавши існуючі конструкції пресів для брикетування, була обрана конструкція штемпельного преса для побудови її фізичної моделі, так як конструкція штемпельного преса є найбільш простою і надійною, що забезпечить високу інформативність експериментальних досліджень процесу брикетування.
Конструкція моделі штемпельного преса і процес формоутворення брикету представлені на рис. 5.
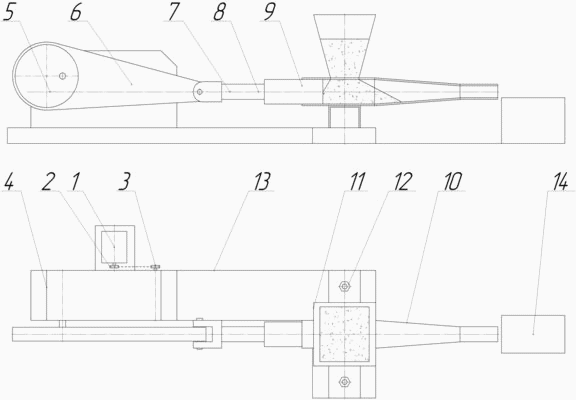
Рисунок 5 – Конструктивна схема штемпельного преса і процес формоутворення брикетів.(анімація: об'єм 83,8 кб, кадрів 8, кількість циклів повторень 7, затримка між кадрами 0,5 с).
1 – двигун; 2 – приводний шків клинопасової передачі; 3 – ведений шків клинопасової передачі; 4 – редуктор, 5 – ексцентрик; 6 – шатун; 7 – вилка; 8 – шток; 9 – пуансон; 10 – гільза; 11 – бункер; 12 – кріпильний болт; 13 – рама; 14 – приймач брикетів.
Брікетіруемий матеріал: прокатна окалина з напівобожженним доломітним пилом.
Зовнішній вигляд одержуваних брикетів являє собою циліндр діаметром 38 мм.
На даний момент магістерська робота знаходиться в стадії написання. Остаточне завершення: 31 cічня 2013 року. Повний текст роботи та матеріали по темі можуть бути отримані у автора або його керівника після зазначеної дати.
Список источников
- Ожогин В.В. Основы теории и технологии брикетирования измельчённого металлургического сырья: Монография. – Мариуполь, ПГТУ, 2010. – 442 с.
- Равич Б.М. Брикетирование в цветной и чёрной металлургии / Б.М. Равич. – М.: Металлургия, 1975. – 232 с.
- Лурье Л.А. Брикетирование в чёрной и цветной металлургии / Л.А. Лурье. – М.: Металлургиздат, 1963. – 324 с.
- Штрюбель Г. Минералогический словарь / Г. Штрюбель, З. Циммер. – М.: Недра, 1987. – 494 с.
- ГОСТ 30561-98. Меласса (патока кормовая). Технические условия. – М.: Изд-во стандартов, 1998.
- Ремесников И.Д. Анализ процесса обжатия угля в удлинённом криволинейном матричном канале / И.Д. Ремесников // Новое в брикетировании и коксовании углей. – Под ред. Е.М. Тайц. – М.: Наука, 1965. – С. 121-128.
- Целиков А.И. Машины и агрегаты металлургических заводов: учебник для вузов: В 3-х т. Т. 2. Машины и агрегаты доменных цехов / А.И. Целиков, П.И. Полухин, В.М. Гребенник и др. – 2-е изд., перераб. и доп. – М.: Металлургия, 1987. – 430 с.
- Пахалюк Н.Ф. Брикетирование угля / Н.Ф. Пахалюк, В.А. Болдырев. – М.: Углетехиздат, 1957. – 180 с.