Abstract
Table of contens
- Introduction
- 1. Actuality
- 2. Purpose and research problems
- 3. The review of existing researches
- Analysis of the general principles of configuration of rotor systems, main properties, features and characteristics
- Conclusion
- References
Introduction
Now industrial automation is one of pacing factors of the modern scientific and technical revolution opening before mankind of possibility of conversion of the nature, creation of huge material riches, multiplication of creative abilities of the person. Development of automation is characterized by a row of large achievements. Implementation of assembly conveyors of Henry Ford in production process was one of the first. The considerable revolution in industrial automation was made by industrial robots and personal computers. All this pushed our society on a way of new automated management by production process.
Now for effective functioning of the enterprise automation is everywhere entered, it becomes an integral part of all production. And it is quite justified and favorable, after all expenses decrease and quality of production increases. Automated production – is system of machines, the equipment, the vehicles, providing execution of all stages of manufacture of products strictly coordinated in time, beginning from receiving the initial preparations and finishing monitoring (test) of a finished product and output at regular intervals [1].
At the first stage automatic transfer lines and rigid plants machine guns were created. The second period of development of automation is characterized by electronic program control appearance, creation of machines with numerical control (further ChPU), processing centers and automatic transfer lines. As premise of development of industrial automation at the third stage new possibilities of ChPU on the basis of the microprocessor technique, allowed to create new system of machines which combined high performance of automatic machines with requirements of flexibility of production served. At higher level of automation the self-starters of the future equipped with the equipment with machine intelligence are created [4].
Big share of expenses of time for productive works, in case of manufacture of machines and duration of the general cycle of production do to automation of production operations especially actual a problem. Value of the solution of this problem is defined not only tasks of improvement of quality of production, profitability of its production and productivity increase, Automation of productions by means of use of technological systems of the continuous action executed on the basis of rotor and rotor and pipeline machines, is especially effective in case of mass productions of products. That is Development of structural and technological support of rotor machines for manufacture of products of mass production is very actual scientific task having important economic value.
1. Actuality
Now fixing connective products such as bolts, screws, washers, selflocking nuts, screws are widely used. nails, etc. The separate technology equipment that is ineffective is applied to their manufacture as requires heavy expenses on the maintenance of floor spaces, transportation of details from the machine to the machine, etc., the solution of this problem is high-automated production. Simultaneous manufacture of these products on one process line will allow to raise technical and economic indexes of their manufacture, to reduce prime cost and to avoid transportation costs.
2. Purpose and research problems
The operation purpose – to increase productivity and quality of processing of details of machines at the expense of use of rotor machines for manufacture of products of mass production.
Main tasks of the research:
- ATo carry out the analysis of the general principles of configuration of rotor and rotor and pipeline systems, the main properties, features and characteristics.
- To execute structural synthesis of technological processes of the continuous action.
- To carry out the analysis of structure and algorithm of technological process.
- To make the analysis of feature and classification of technological processes of the continuous action.
- To develop options of constructions of a transport rotor for transmission of details like axially symmetrical bodies.
- To lower level of oscillations of mechanical system with the same perturbations.
Research object: rotor machines for manufacture of products of mass production.
3. The review of existing researches
Now a large number of researches on development of rotors and rotor lines is carried out. Efforts of many scientists made the significant contribution to development. Among which L.N.Koshkin, V.V.Preys, I.A.Klusov, etc.
Analysis of the general principles of configuration of rotor systems, main properties, features and characteristics
Variety of complex automatic transfer lines are the rotor automatic transfer lines developed by engineer L.N.Koshkin.
The automatic transfer rotor line – a complex of working machines, transport devices, the instruments integrated by a single system of automatic control in which at the same time with processing of preparation move on arcs of circles together with tools influencing them. Automatic transfer rotor lines for the operations executed by means of rectilinear labor movement (stamping, an extension, molding, assembly, monitoring) are most widespread [5].The automatic transfer rotor line consists of working rotors on which technological operations, and transport rotors which move processed subjects of operations (Fig. 1) are executed.
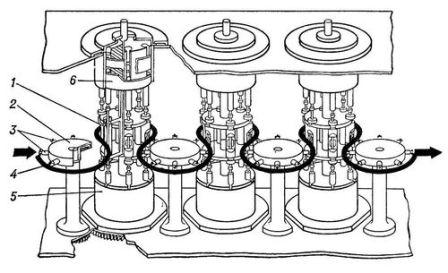
Figure 1 – Schematic diagram of the automatic transfer rotor line: 1 – the unit of the tool; 2 – a transport rotor; 3 – pincers; 4 – the line of relocation of a product when processing; 5 – a working rotor; 6 – the copier.
The working rotor represents rigid system on which the group of the tools uniformly located round the general gyrating system of a shaft is mounted. Necessary labor movements are reported to these tools by executive bodies, for small efforts mechanical executive bodies, are applied to the big — hydraulic (for example, rods of hydraulic force cylinders) [3]. Transport and working rotors are rigidly connected among themselves. On automatic transfer rotor lines it is possible to process at the same time subjects of several standard sizes of similar technology both in mass, and in a mass production. Rotor lines allow to automate processing of several same details, i.e. differ a certain level of flexibility (Fig.2)
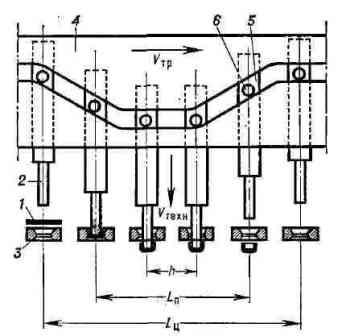
Figure 1 – Schematic scanning of press operation on the rotor line: 1 – a processing subject; 2, 3 – the tool; 4 – the grooving copier; 5 – a slider; 6 – rollers of slider
The tool is, as a rule, mounted completely in beforehand adjusted (out of working machines) the units interfaced to executive bodies of a rotor preferentially by only axial communication that provides possibility of fast changeover of units. Transport rotors accept, transport and transfer products. They represent drums or the disks equipped with bearing organs. Are more often applied the simple transport rotors having identical transport speed, the general plane of transportation and identical orientation of subjects of processing.
Transport rotors which can change angular speed and situation in space of transported subjects are intended for transmission of products between working rotors with different step distances or the different provision of subjects of processing. Working and transport rotors connect in the line the general synchronous drive moving each rotor on one step during the time, corresponding to rate of the line.
On automatic transfer rotor lines it is possible to execute the operations considerably differing on durations, for example press, control, thermal and chemical. The automatic transfer rotor line can process some different products at the same time.
Further distribution of automatic transfer rotor lines for release of mass products (radio components, stamped details, etc.) is especially perspective. Their application most rationally in production with short technological processes and in case of manufacture of rather simple subjects having the form of axially symmetrical bodies. Productivity of automatic transfer rotor lines is defined by the transport speed of a rotor and step distance between products in a rotor [10].
Application of automatic transfer rotor lines in comparison with separate machine guns not rotor type reduces a production cycle by 10 — 15 times, in-process inventories of preparations considerably decrease (by 20-25 times), are released floor spaces, labor input of manufacture and product cost several times decreases, capital expenditure pays off in 1-3 years [5].
One of the main directions of increase of production efficiency of fasteners – increase of productivity and reliability of the equipment. However increase of productivity of machines is connected to increase in speed of deformation that in case of certain high-speed factors leads to increase of resistance of deformation of stamped materials to growth of technological efforts, lowering of firmness of the tool, lowering of stability and reliability of operation of the equipment. Proceeding from results of the pilot studies which showed that the increase in speed of deformation in case of cold disembarkation of carbon steels leads to increase of resistance of deformation for 20-75% (depending on a deformation level). Therefore establishment of regularities of change of high-speed factors of disembarkation is an important element of increase of accuracy of calculations of high-performance technologies and the equipment. Generally plastic forming deforming speed:

where с – a level of deformation, t – time.
However in the course of disembarkation of fasteners when the speed of deformation changes from a maximum (at some stage of deforming) to zero (the end of deforming), and dependence to precisely speaker manages to be set not always, process it is possible to evaluate on average rate of deformation.
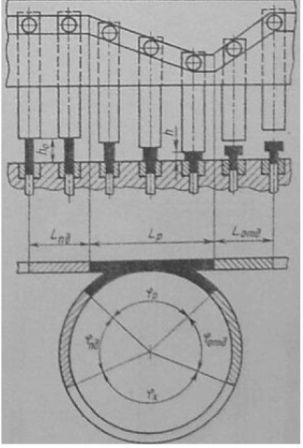
Figure 3 - The disembarkation Diagram by the rotor machine with the mechanical drive
Average rate of deformation in case of disembarkation by the rotor machine:
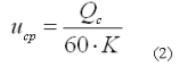
where K – number of the tool frames which are at the same time in a zone of processing.
It is necessary to mark that for rotor machines with the mechanical drive number K=3-5, and for machines with a hydraulic actuator of the working tool, as a rule, K=1 as in case of К>1; construction of system of hydrodistribution significantly becomes complicated [2].
The solution of the task of increase of production of manufacture of details like axially symmetrical bodies is connected to use of essentially new machines providing a high level of automatism and a continuity of production – socalled rotor machines in which transport movement of subjects of processing continuously and isn't restricted to technology factors. Such machines belong to the 3rd class.
Tool separation from executive bodies causes remarkable technical and economic capabilities: productivity increase, possibility of automation of functions of service of the tool, flux density increase, abbreviation of number and reduction of the sizes of executive bodies, the axial sizes and values of working courses of the tool that productivity izmerekniya leads to sharp abbreviation of cost of the machine on unit.
Proceeding from above-mentioned characteristics, it is expedient to apply rotor machines - machines 3 classes. Productivity of such machines is defined:
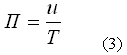
where P-productivity; T - a production cycle; u - quantity of line items.
To each class of technological processes there corresponds a certain method of execution. Therefore, application of the method providing full use of opportunities of processes of this class, is caused by nature of these processes. Processes of the III classes not only in itself contain the greatest potential opportunities for implementation of mechanization of production, but provide as well application of methods of their execution which allow to use these opportunities. Therefore existence of technological processes of the III classes, more precisely, accessory of all processes on manufacture of this product to processes of the III classes, providing possibility of application of the third and fourth methods, is not only necessary, but also a sufficient premise for broad application of automatic system of machines in a proizkvodstvo of this product. Technical capability of creation of each separate automatic system of machines and physical possibility of implementation of broad transition to automatic systems are connected, thus, to two last classes of technological processes, and implementation of these opportunities is connected to transition to classes of machines corresponding to them. Class machines III in the most full measure conform to requirements of the higher form of automatism and a continuity.
Class machines III as the class of processes corresponding to them solves problems of all purposes can be a real basis for broad implementation of complex automation now and envelops the whole branches of productions, and, at the same time, processes of all other classes also can be executed by means of class machines III. However class machines III still take a small place even in the productions which are based only on processes of the III class. Therefore the most important task of komkpleksny automation is the accelerated creation of broad gamma of the machine III of a class and their distribution first of all in the branches of production which are based on processes of the III class.
Machines III of a class can be executed according to two constructive diagrams — rotor: in case of the rotor diagram working tools are mounted on rigid transport systems — rotors together with the executive bodies telling to them necessary technological movements. In case of the rotor and pipeline diagram working tools are mounted on flexible closed transport systems — pipelines, and executive bodies — in servicing rotors bent by them. This distinction between two diagrams of machines III of a class has basic value and determines by itself fundamental differences of their major technical capabilities [9].
The rotor diagram corresponds to initial stage of development of machines III of a class and possesses limited opportunities both on technical and economic indexes, and on latitude of scope of application. The rotor and pipeline diagram corresponds to the developed form of machines III of a class. As class machines III appeared in the beginning in the form of rotor machines and lines, many technical solutions relating to them remain and in rotor and pipeline machines and lines. Therefore it is expedient to consider in the beginning diagrams and the constructive elements relating to rotor machines and lines.
The working rotors intended for execution of the main technological operations, are the most important and various elements on designs of rotor lines. Distinctions in constructions of working rotors are caused by the nature of technological operations defining the kinematic diagram of a rotor and type of executive bodies, and also scale of production for which they intend, defining one - or a multinomenclature of equipment of line items of a rotor and appropriate features of distributing devices [6,8].
Within the same class of processes working rotors differ depending on technological parameters (values of working courses and forces, the provision of preparation, methods of its installation, basing, etc.), character of the drive, layout of the working organs, applied kinematic elements and, at last, from constructive forms of mounting of tools in a rotor and the rotor on its axis. Reviewing of constructions of working rotors we will begin with the rotors intended for execution of operations, relating to technological processes of the III class as they contain a row of the basic elements inherent in working rotors, used for execution of operations of all other classes. These rotors it is constructive are developed better than others and are the most widespread.
Class operations III for bulk of almost meeting details are characterized by rectilinear labor movement of the tool and absence of fixing or preparation installation, or execution of this function by labor movement of the tool. Executive bodies of working rotors for processes of this class represent the mechanisms reporting to working tools rectilinear movement. Distinguish two main types of operations III of a class: the operations executed by means of one tool making labor movement (fig. 4, a) and the operations executed by means of two tools making labor movements (fig. 4, b). Operations belong to operations of the first type (stamping, a marking), preparations executed without input in a matrix, or the similar processes executed using matrixes or compression molds, not requiring pushing out of the processed detail as it is derived from a matrix by a punch or a stamp in case of its return motion.
The majority of the press, bending, chimney and other operations executed using stamps, the linear forms belong to operations of the second type, etc. from which the processed detail is derived by means of independent movement of the separate tool (a pusher, the second punch, etc.). The second type of operations most often meets in technological processes of the III class.
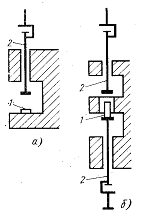
Figure 4 – Schematic diagrams one-sided (and) and double-sided technological processes for class operation III: 1 – preparation; 2 – the working tool
There are still the operations III of a class requiring application of a large number of tools, making independent labor movements both in the direction of one, and in the direction of different axes. Such operations meet much less often (in build processes, manufacture of the reinforced plastic details, etc.). The executive bodies reporting labor movement to tools, executing such operations, consist, however, of the elements, similar subjects which are necessary for execution of operations of the two first types. Therefore reviewing of working rotors for execution of operations III of a class can be carried out on the example of the two first types of operations [7]. Basic element of all rotors for execution of operations III of a class is the organ reporting to the tool rectilinear labor movement. In case of execution of operations of the first type each working organ of a rotor contains one tool making independent movement (fig. 5) and one executive body reporting to the tool movement. In case of execution of operations of the second type each working organ of a rotor consists of two tools making independent movements and two executive bodies telling to them these movements (fig. 6). The rotors executing operations of the first type, received the name one-sided, and the second — double-sided. Depending on type of executive bodies working rotors for operations III of a class can be mechanical, hydraulic, pneumatic and and combined [5].
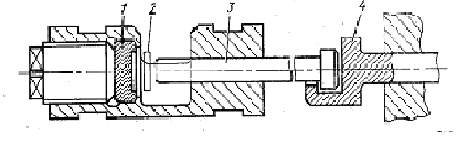
Figure 5 – The diagram of a working rotor for execution of one-sided operations of III classes: 1 and 3 – working tools; 2 – preparation; 4 – executive body
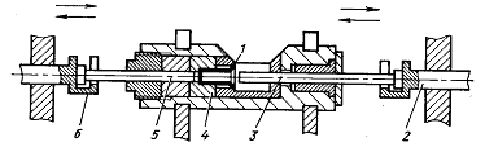
Figure 6 – The diagram of a working organ of a rotor for execution of double-sided operations III of a class: 1 – preparation; 2 and 6 – elements of the drive of executive bodies; 3, 4 and 5 – working tools
The first problem on importance to which all are connected others, is the problem of payback of the automatic devices replacing work of the person. The entity of a problem consists that such devices shall provide the economic effect, allowing to return their cost in a certain period. This requirement belongs to devices for loading of technological machines by subjects of processing or in-process transmission of subjects, automation of change of the tool, sampling inspection of subjects of processing etc. This requirement, as a rule, is mandatory.
Meanwhile this requirement can not be met actually of what it is possible to be convinced on the example of the task of automation of loading of the technological machine by processing subjects. Economic effect of use of such device in unit of time its uses makes R = Cp. nQ, where Sp, n – the cost of transmission of one subject manually; Q – productivity of connected machines. The condition of economic payback consists in, that effect for the given payback period Tok
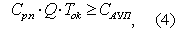
where Сауп – the cost of the automatic device, but this condition can not be met.
Really, in each case the cost of manual transmission of one subject and cost of the automatic device for transmission are the given values. The cost of manual transmission can't be randomly increased because it is defined depending on the sizes and the form of a subject of processing by necessary labor costs on subject transmission. The cost of the automatic device can't be randomly reduced because it also is defined by the sizes and the form of a subject of processing and real construction of the device. It can't be randomly increased and a payback period. Thus, the condition of payback can be met only in case of high performance. Productivity being necessary for support of payback of the automatic device, is defined from a payback condition:
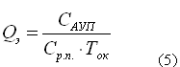
Support of this productivity during the whole kalendarkny time is the mandatory economic requirement. But for the majority of machines, now in use in production of the discrete subjects, the theoretical proizvodiktelnost is defined by duration of an operational cycle, t. е
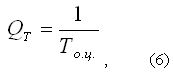
real productivity lasting an operational cycle
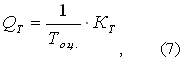
where Кт – utilization coefficient of calendar time.
Provided that and productivity is the given value which isn't allowing arbitrary choice. Transition to a new performance level is mandatory uslokviy cost-efficient increase of level of automatism and a continuity.
This transition is the general objective regularity of development of the machines, caused by that increase of level of automatism represents transmission to machines of more and more seldom realized production functions (tool change, sampling inspection, running repair, change of objects of prokizvodstvo), the sufficient which efficiency of automation necessary for its payback, comes only in case of higher performances. The understanding of this regularity has exceptional practical value as increase of level of automatism and a continuity out of absolutely certain communication with a performance level can lead to lowering важнейшею an economic index.
At present in mechanical engineering to manufacture of fasteners apply holodnovysadochny stamps (fig. 7). But they possess shortcomings:
- high speed of deformation (in the course of deformation there is a mechanical hardening (peening) of metal frictional forces and efforts of deforming increase;
- work in the conditions of high speeds and dynamic loads, it leads to big vibration amplitudes that in a consequence reduces productivity.
- Владзиевский, А. П. Автоматические линии в машиностроении/ А.П. Владзиевский , М., 1998
- Кошкин, Л. Н., Густов, А. А. Роторные машины для механической обработки/ Л. Н. Кошкин, А. А.Густов, К.,2002.
- Кошкин, Л. Н. Комплексная автоматизация на базе роторных линий/ Л. Н. Кошкин, М.,1999.
- Феденя, А.К. Организация производства и управление предприятием: Учеб. пособие/ А.К. Феденя. – Мн.: Тетра-Системс, 2004. – 192с.
- Соломатин, Н.А. Управление производством: Учебник/ под ред. Н.А. Соломатина. – М.: ИНФРА – М, 2001. – 219 с.
- Клусов И.А. и др. Автоматизация сборочных процессов на роторных линиях - Киев, 1967 - 48 с.
- Михайлов А. Н. Основы синтеза поточно-пространственных технологических систем. - Донецк: ДонНТУ, 2002. - 379 с.
- Прейс В.В. Технологические роторные машины вчера, сегодня, завтра - М.: Машиностроение, 1986 - 128 с.
- Автоматизация производственных процессов [Электронный ресурс]. – Режим доступа: http://www.elit-material.ru/promyshlennost_proizvodstvo/referat_avtomatizaciya_proizvodstvennyx.html.
- Роторные и роторно-кнвейерные линии [Электронный ресурс]. – Режим доступа: http://www.ekoslovar.ru/359.html.
Therefore to elimination of these shortcomings and increase of productivity it is more expedient to apply rotor lines.
Considering the above, from the point of view of productivity and automation of manufacture of details like axially symmetrical bodies by rotor machines it is possible to draw a natural output that this transition is expedient.
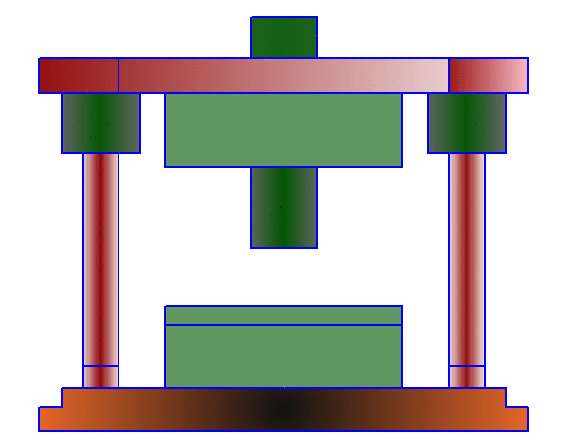
Figure 7 – The diagram of operation of a holodnovisadochny stamp in case of extrusion
(animation: 7 frames, 6 cycl of repeating, 165 kilobytes)
Conclusion
Now the problem of saving of resources is very actual, especially in power - and material-intensive branches. In this regard the intensive way of development of production which is offered to realize type of axially symmetrical bodies by production of details is perspective. Application for this purpose automatic transfer rotor lines will give essential increase in productivity and other technical and economic indexes, will allow to reduce time of equipment downtimes, to increase utilization coefficient of technological space, and implementation of such lines in practice will allow to resolve an issue of complex industrial automation.
During the process of writing, the master’s work hasn’t completed yet. Final completion: December, 2013. The full text of work and materials on the theme could be received from the author or him scientific adviser after the indicated date.