Реферат по теме выпускной работы
Содержание
- Введение
- 1. Актуальность темы
- 2. Цель и задачи исследования, планируемые результаты
- 3. Обзор исследований и разработок
- 4. Комбинированные зенкеры
- Выводы
- Список источников
Введение
После спада производства, обусловленного мировым экономическим кризисом, машиностроение Украины приобретает динамику развития.
Одной из главных задач в любой отрасли машиностроения является усовершенствование и разработка нового оборудования и режущего инструмента для обеспечения высокого качества изделий, а также увеличение производительности.
Обработка отверстий занимает не менее важное место в машиностроении и по объему не уступает процессам обработки наружных поверхностей. Отверстия в деталях машин бывают цилиндрические гладкие и ступенчатые. Под ступенчатыми понимают отверстия разных диаметров, расположенные на одной оси, последовательно одно за другим. Отверстия могут быть открытые с двух сторон или с одной стороны (глухие). Отверстия с соотношением длины к диаметру больше пяти считаются глубокими.
Обработка отверстий несколько сложнее, чем наружных поверхностей тел вращения. В связи с этим точность (квалитет) на отверстия назначают на один порядок грубее и, как правило, не точнее 7-го квалитета.
Обработка отверстий может производиться со снятием и без снятия стружек. Обработка со снятием стружки осуществляется лезвийным и абразивным инструментом. К обработке лезвийным инструментом относятся сверление, зенкерование, развертывание, растачивание и протягивание. К абразивной обработке относится шлифование и хонингование.
Обработка отверстий без снятия стружки производится путем калибровки с помощью выглаживающих прошивок (дорнов) и шариков, а также раскаткой [1].
Для повышения точности отверстий после сверления и снижения шероховатости их поверхности применяют зенкерование. Зенкерованием могут обрабатываться также отверстия в отливках и штамповках. Зенкерование может быть предварительной обработкой под последующее развертывание, растачивание или протягивание. После чернового зенкерования в заготовке обеспечивается точность по 11…12 квалитету и шероховатость поверхности Rа=20…10 мкм. Чистовое зенкерование в зависимости от материала и конструкции зенкера позволяет получить точность по 9…10 квалитету и шероховатость Rа=6,3…3,2 мкм. Поэтому при обработке отверстий по 11…13 квалитетам зенкерование может быть окончательной операцией.
Припуск под зенкерование предварительно просверленных или расточенных отверстий составляет примерно 1/8…1/10 диаметра отверстия. Скорость резания для твердосплавного инструмента при обработке стали состовляет 25…120 м/мин, подача 0,4…0,5 мм/об. Для чугунных заготовок соответственно скорость резания составляет 50…150 м/мин и подача – 0,3…0,6 мм/об. Отверстия диаметром до 12 мм не зенкеруют, а сразу развертывают черновой разверткой.
Широкое применение нашел комбинированный инструмент. Совмещение черновой и чистовой обработки, обработка фасонных, ступенчатых или нескольких соосно расположенных отверстий, совмещение различных операций, выполняется таким инструментом за один проход.
Конструкция комбинированного инструмента зависит также от конфигурации и размеров обрабатываемого отверстия, формы, размеров, расположения и количества нескольких соосных отверстий, требований точности, чистоты обработки, величины снимаемого припуска, а также от способа направления инструмента [2].
1. Актуальность темы
В настоящий момент машиностроение сделало огромный скачек в сфере обработки труднообрабатываемых материалов с использованием прогрессивного режущего инструмента, из новых инструментальных материалов улучшенной геометрии и повышенной стойкости, применением различных способов комбинированной обработки с внесением дополнительных потоков энергии и новых кинематических схем.
Данная магистерская работа посвящена актуальной задачи – повышения производительности за счет изменения геометрических параметров инструмента.
2. Цель и задачи исследования
Целью работы является повышение эффективности обработки отверстий за счет оптимизации геометрических параметров и конструкции сборного комбинированного зенкера.
Основные задачи исследования:
- Провести анализ существующих конструкций сборных зенкеров, выявить основные тенденции развития подобных инструментов.
- Провести анализ влияния геометрических параметров и режимов резания сборных зенкеров на производительность обработки и обеспечение требуемой точности.
- Предложить рациональную конструкцию сборного зенкера, способного обеспечить требуемую точность обработки при максимально-возможной производительности.
- Произвести оптимизацию режимов резания для предлагаемой конструкции сборного зенкера.
- Разработать методику определения оптимальных режимов резания при использовании сборного зенкера.
Объект исследования: обработка отверстий сборным зенкером.
Предмет исследования: Процессы, оказывающие влияние на точность и производительность обработки сборными зенкерами.
Методы исследования. Достижение поставленной цели обеспечивается рациональным сочетанием теоретических и экспериментальных методов исследований.
3. Обзор исследований и разработок
Проектированием комбинированного осевого режущего инструмента, а в частности, конструкций сборного зенкера на протяжении некоторого времени занимались:
А.А. Черепанов в работе «Совершенствование конструкций режущего инструмента посредством поискового проектирования» [3], рассмотрел особенности реализации данной методологии применительно к вопросам проектирования сборных зенкеров.
А.Я. Шмелевым [4] частично систематизированы конструкции осевых комбинированных инструментов и даны аналитические зависимости для определения некоторых конструктивных параметров ступенчатых сверл.
И.А. Малышко в работе [5] привел рекомендации по проектированию и эксплуатации осевых комбинированных инструментов.
4. Комбинированные зенкеры
Классификация комбинированных осевых инструментов. Целью данной классификации является анализ и систематизация существующих конструкций комбинированных инструментов, с учетом рабочих процессов, в которых они функционируют.
Обобщение конструктивных параметров комбинированных инструментов с учетом их взаимодействия с рабочими процессами создает теоретические предпосылки для составления вербальных моделей, а, следовательно, позволяет разработать математические модели адекватные физическим.
Разнотипные инструменты в большинстве случаев применяются для последовательной обработки отверстий одного диаметра. Также они применяются для обработки отверстий разных диаметров, но расположенных на одной оси.
По конструктивному исполнению комбинированные инструменты разделяются на цельные, составные и насадные. Цельные комбинированные инструменты изготавливаются из однородных по наименованию и марке материалов. К цельным комбинированным инструментам также относятся инструменты, у которых режущая часть выполнена из инструментальной стали, а хвостовик из конструкционной.
К составным комбинированным инструментам относятся инструменты, которые состоят из корпуса, к которому при помощи пайки, сварки, клея, винтов, рифлений и т.д. крепятся режущие элементы.
Эффективным является применение комбинированных инструментов с неперетачиваемыми пластинами, позволяющими относительно быстро получать любую комбинацию режущих кромок. Недостатком инструментов с неперетачиваемыми пластинами является громоздкость элементов крепления, что не позволяет изготавливать инструменты для обработки отверстий малых диаметров.
Насадные комбинированные инструменты или наборы, объединяют однотипные или разнотипные инструменты общей оправкой или одним из инструментов. Примером составных инструментов может служить несколько насадных зенкеров различных диаметров, закрепленных на одной оправке.
Преимуществом таких инструментов является возможность комбинаций на одной оправке из различных диаметров одномерных инструментов, замена изношенной или поломанной ступени, облегчение условий переточки.
По способу крепления комбинированные инструменты делятся на: инструменты с жестким креплением и одной направляющей втулкой; инструменты с плавающим креплением без направляющих втулок; инструменты с плавающим креплением и одной или несколькими направляющими втулками.
Способ крепления инструмента определяется его типом и размерами, моделью станка, особенностью конструкции приспособления, в котором крепится деталь, силовыми воздействиями, точностью обработки.
Жестко крепятся, как правило, зенкеры и свёрла. Развертки могут крепиться как жестко, так и в плавающем патроне. Способ крепления развертки определяется точностью оборудования: при высокой его точности развертка крепится жестко, при низкой, в плавающем патроне.
На агрегатных станках инструменты, как правило, направляются кондукторными втулками. При обработке деталей на станках с ЧПУ или многооперационных станках все осевые инструменты работают без кондукторных втулок, независимо от способа крепления.
Одним из основных элементов, составляющих рабочий процесс, является кинематика движения инструмента. Осевые инструменты, имеют вращательное и поступательное движение, которые задаются кинематикой станка. Наличие внешних воздействий в виде вынужденных колебаний вызывает появление огранки в поперечном сечении цилиндрической поверхности, причем это явление наблюдается при работе практически всех осевых инструментов.
Особенностью процесса стружкообразования для осевых инструментов является то, что передняя поверхность режущего клина, обеспечивающая формирование стружки, одновременно является стружечной канавкой, служащей для транспортировки стружки от предыдущих ступеней. Поэтому величина переднего угла является функцией от угла наклона стружечной канавки. Таким образом, процессы стружкообразования и транспортировки стружки взаимосвязаны.
Силы резания, действующие на инструмент, определяют положение его оси, а, следовательно, и точность обработки. Причем необходимо учитывать, что крутящий момент оказывает влияние на радиальные перемещения инструмента, т.е. к каждой ступени приложено три силы, вызывающие искривление оси. Взаимное влияние сил, действующих на каждую ступень, оказывает существенное влияние на общее положение оси.
По способу образования поверхностного слоя комбинированные инструменты так же, как и одномерные, можно разделить на инструменты, работающие: со снятием стружки; пластическим деформированием (выглаживанием). Способ выглаживания в чистом виде для комбинированных инструментов встречается редко. Примером может служить сверло с уплотняющими ленточками. Данное сверло имеет две уплотняющие ленточки, диаметр которых больше диаметра вспомогательных режущих кромок. В результате в процессе обработки наряду со сверлением происходит выглаживание обработанной поверхности. Наиболее часто способ выглаживания применяется в сочетании с резанием, т.е. применяется комбинированное формирование поверхностного слоя.
Зенкеры изготавливают хвостовыми цельными (рис.1), хвостовыми сборными со вставными ножами, насадными цельными и насадными сборными (рис.2).
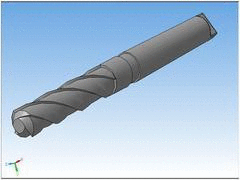
Рисунок 1 – Анимированное изображение цельного зенкера (зделано в mp_gif_animator 125 кБ, 5 кадр)
Зенкеры делают из быстрорежущей стали или с пластинами твердого сплава, напаиваемыми на корпус зенкера или на корпус ножей у сборных конструкций.
Хвостовые зенкеры подобно сверлам крепят с помощью цилиндрических или конических хвостовиков, насадные зенкеры имеют коническое посадочное отверстие (конусность 1:30) и торцовую шпонку для предохранения от провертывания при работе. По конструкции рабочей части хвостовые зенкеры аналогичны спиральным сверлам, но не имеют поперечной режущей кромки и имеют три зуба, благодаря чему обеспечивается лучшее направление при работе, и лучшая цилиндричность и качество обработанной поверхности. Насадные зенкеры имеют четыре-шесть зубьев.
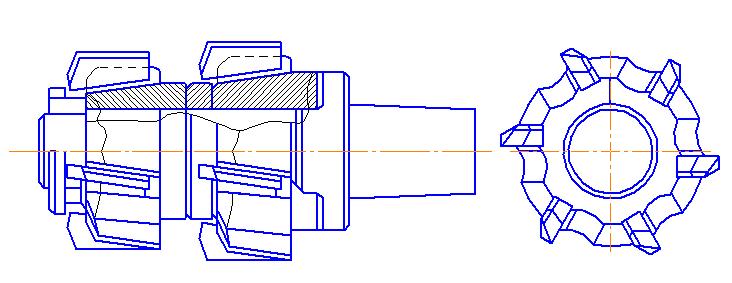
Рисунок 2 – Насадной сборный зенкер
Форма профиля поперечного сечения зенкера, имеющего три зуба, показана на рис. 3. Этот профиль аналогичен профилю канавки сверла и характеризуется соотношениями: do = (0,35...0,5)d, В = (0,4...0,48)d, hл=(0,02...0,04)d.
Форма профиля зенкера, имеющего четыре зуба, показана на рис. 4. Высота зуба этих зенкеров h=(0,1...0,16)d. Спинка зуба криволинейная, что позволяет обрабатывать зуб за один проход, тогда как профиль, указанный на рис. 3, требует раздельной обработки канавки и спинки зуба.
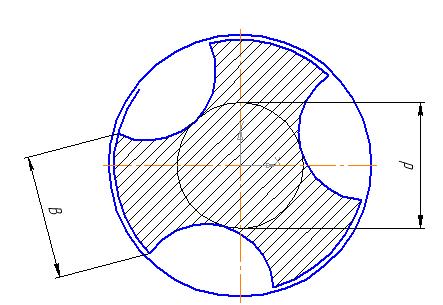
Рисунок 3 – Форма профиля поперечного сечения зенкера, имеющего три зуба
Зенкеры из быстрорежущей стали изготавливают хвостовыми цельными диаметрами от 10 до 40 мм, хвостовыми сборными со вставными ножами диаметром от 32 до 80 мм, насадными цельными диаметром от 25 до 60 мм и насадными сборными диаметром от 40 до 120 мм. Хвостовые зенкеры делают сварными — рабо¬чая часть из быстрорежущей стали, хвостовик из сталей 45, 40Х, 45Х. Место сварки обычно делают на шейке. Заднюю поверхность у цельных зенкеров оформляют по винтовой или конической поверхности, у зенкеров сборной конструкции — по плоскости. Для крепления ножей на корпусе делают косые пазы, наклоненные к оси под углом ω=10...20°. Передняя поверхность корпуса плоская. Ножи имеют клиновидную форму с углом клина 5°, их крепят в корпусе с помощью рифлений. Хвостовые цельные зенкеры имеют три зуба, насадные цельные — четыре.
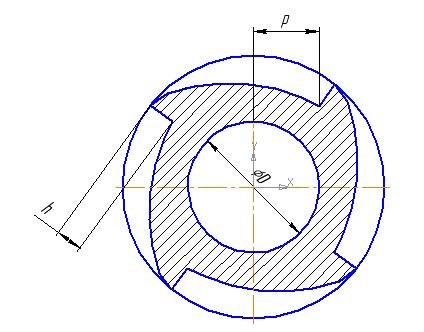
Рисунок 4 – Форма профиля поперечного сечения зенкера, имеющего четыре зуба
Высота зуба этих зенкеров h=(0,1...0,16)d. Спинка зуба криволинейная, что позволяет обрабатывать зуб за один проход. Наиболее часто зенкеры изготовляют с расположением режущей кромки по радиусу (λ= 0°).
Зенкеры, оснащенные твердосплавными пластинами, могут быть составными и сборными. Составные хвостовые зенкеры изготавливают диаметром 14–50 мм, насадные 32–80 мм, насадные сборные зенкеры диаметром 40–120 мм. Хвостовые зенкеры имеют три зуба, насадные – четыре, сборные зенкеры – четыре-шесть зубьев. Корпуса зенкеров и ножей, оснащаемые пластинами из твердого сплава, делают из сталей 40Х или 45Х (36... 46HRCэ), 9ХС (57...63HRCэ) или из быстрорежущей стали (57...63HRCэ). Для их оснащения применяют пластины из твердых сплавов ВК6, ВК8, ВК6–М, ВК8-В, Т5К10, Т14К8, Т15К6. Крепление пластин производится напайкой [6].
Выводы
Важное значение, особенно для автоматизированного производства, имеет надежность инструмента, приспособленность к автоматизации, малый расход инструментального материала и низкая себестоимость. Этим требованиям отвечают сборные зенкеры с механическим креплением режущих пластин. Замена составных, в частности напайных, зенкеров сборными является одной из важнейших тенденций развития технологии обработки отверстий в машиностроении.
При написании данного реферата магистерская работа еще не завершена. Окончательное завершение: декабрь 2013 года. Полный текст работы и материалы по теме могут быть получены у автора или его руководителя после указанной даты.
Список источников
- Костюкевич С. С. Точность обработки глубоких отверстий / Костюкевич C. C., Дечко Э. М., Долгов. В. И. – Минск: Вышейшая школа, 1978. – 144 с.
- Пазюк Е.И. Инструмент для обработки отверстий (сверла, зенкеры, развертки и расточной инструмент). - Л.: Ленинградское газетно-журнальное и книжное издательство, 1952. - 128 с.
- Совершенствование конструкций режущего инструмента посредством поискового проектирования // СТИН. – 2006 г. – №2.
- Максимов М.А. Комбинированные режущие инструменты./ Максимов М А., Киселева Л П., Шмелев А.Я. – Горький: Горьковский государственный университет, 1977, 86 с.
- Малишко І. О. Основи теорії проектування осьових комбiнованих інструментів: автореф. дис. на здобуття наук. ступеня доктора техн. наук : спец. 05.03.01 „Процессы механической обработки, станки и инструменты” / І. О. Малишко. – Київ, 1996. – 33 с.
- Сахаров Г.Н. Металлорежущие инструменты./ Сахаров Г.Н. Арбузов О.Б., Боровой Ю.Л., Гречишников В.А., Киселев А.С. – М.: Машиностроение, 1989. – 328 с.
- Технология обработки типовых отверстий деталей машин [электронный ресурс]. - Режим доступа:http://elite-instrument.ru/category/zenkery-/