Реферат за темою випускної роботи
Зміст
- Вступ
- 1. Актуальність теми
- 2. Мета і задачі дослідження та заплановані результати
- 3. Огляд досліджень та розробок
- 4. Комбіновані зенкери
- Висновки
- Перелік посилань
Введення
Після спаду виробництва, обумовленого світовою економічною кризою, машинобудування України набуває динаміки розвитку.
Одному з головних завдань у будь-якій галузі машинобудування є удосконалення і розробка нового устаткування і ріжучого інструменту для забезпечення високої якості виробів, а також збільшення продуктивності.
Обробка отворів займає не менш важливе місце в машинобудуванні і за об'ємом не поступається процесам обробки зовнішніх поверхонь. Отвори в деталях машин бувають циліндрові гладкі і ступінчасті. Під ступінчастими розуміють отвори різних діаметрів, розташовані на одній осі, послідовне одне за іншим. Отвори можуть бути відкриті з двох сторін або з одного боку (глухі). Отвори із співвідношенням довжини до діаметру більше п'яти вважаються глибокими.
Обробка отворів дещо складніше, ніж зовнішніх поверхонь тіл обертання. У зв'язку з цим точність (квалітет) на отвори призначають на один порядок грубіше і, як правило, не точніше 7-го квалітета.
Обробка отворів може вироблятися із зняттям і без зняття стружок. Обробка із зняттям стружки здійснюється лезвійним і абразивним інструментом. До обробки лезвійним інструментом відносяться свердління, зенкерування, розгортання, розточування і простягання. До абразивної обробки відноситься шліфування і хонінгування.
Обробка отворів без зняття стружки виробляється шляхом калібрування за допомогою вигладжуючих прошивок (дорнов) і кульок, а також розкочуванням [1].
Для підвищення точності отворів після свердління і зниження шорсткості їх поверхні застосовують зенкерування. Зенкеруванням можуть оброблятися також отвори у відливаннях і штампуваннях. Зенкерування може бути попередньою обробкою під подальше розгортання, розточування або простягання. Після чорнового зенкерування в заготівці забезпечується точність по 11.12 квалітету і шорсткість поверхні Rа=20.10 мкм. Чистове зенкерування залежно від матеріалу і конструкції зенкера дозволяє отримати точність по 9.10 квалітету і шорсткість Rа=6,3.3,2 мкм. Тому при обробці отворів по 11.13 квалітетам зенкерування може бути остаточною операцією.
Припуск під зенкерування заздалегідь просвердлених або розточених отворів складає приблизно 1/8.1/10 діаметру отвору. Швидкість різання для твердосплавного інструменту при обробці стали є 25.120 м/хв, подача 0,4.0,5 мм/об. Для чавунних заготовок відповідно швидкість різання складає 50.150 м/хв і подача – 0,3.0,6 мм/об. Отвори діаметром до 12 мм не зенкують, а відразу розгортають чорновою розгорткою.
Широке вживання знайшов комбінований інструмент. Поєднання чорнової і чистової обробки, обробка фасонних, ступінчастих або декілька співісний розташованих отворів, поєднання різних операцій, виконується таким інструментом за один прохід.
Конструкція комбінованого інструменту залежить також від конфігурації і розмірів оброблюваного отвору, форми, розмірів, розташування і кількості декількох співісних отворів, вимог точності, чистоти обробки, величини пріпуська, що знімається, а також від способу напряму інструменту [2].
1. 1. Актуальність теми
Зараз машинобудування зробило величезний скачок у сфері обробки важкооброблюваних матеріалів з використанням прогресивного ріжучого інструменту, з нових інструментальних матеріалів покращеної геометрії і підвищеної стійкості, вживанням різних способів комбінованої обробки з внесенням додаткових потоків енергії і нових кінематичних схем.
Дана магістерська робота присвячена актуального завдання – підвищення продуктивності за рахунок зміни геометричних параметрів інструменту.
2. Мета і завдання дослідження
Метою роботи є підвищення ефективності обробки отворів за рахунок оптимізації геометричних параметрів і конструкції збірного комбінованого зенкера.
Основні завдання:
- Провести аналіз існуючих конструкцій збірних зенкерів, виявити основні тенденції розвитку подібних інструментів.
- Провести аналіз впливу геометричних параметрів і режимів різання збірних зенкерів на продуктивність обробки і забезпечення необхідної точності
- Запропонувати раціональну конструкцію збірного зенкера, здатного забезпечити необхідну точність обробки при максимально-можливій продуктивності.
- Виробити оптимізацію режимів різання для пропонованої конструкції збірного зенкера.
- Розробити методику визначення оптимальних режимів різання при використанні збірного зенкера.
Об'єкт дослідження: обробка отворів збірним зенкером.
Предмет дослідження: Процеси, що роблять вплив на точність і продуктивність обробки збірними зенкерами.
Методи дослідження. Досягнення поставленої мети забезпечується раціональним поєднанням теоретичних і експериментальних методів досліджень.
3. Огляд досліджень і розробок
Проектуванням комбінованого осьового ріжучого інструменту, а зокрема, конструкцій збірного зенкера впродовж деякого часу займалися:
О.О. Черепанов в роботі "Вдосконалення конструкцій ріжучого інструменту за допомогою пошукового проектування" [3], розглянув особливості реалізації даної методології стосовно питань проектування збірних зенкерів.
О.Я. Шмельовим [4] частково систематизовані конструкції осьових комбінованих інструментів і дані аналітичні залежності для визначення деяких конструктивних параметрів ступінчастих свердел.
І.О. Малишко в роботі [5] привів рекомендації по проектуванню і експлуатації осьових комбінованих інструментів.
4. Комбіновані зенкери
Класифікація комбінованих осьових інструментів. Метою даної класифікації є аналіз і систематизація існуючих конструкцій комбінованих інструментів, з врахуванням робочих процесів, в яких вони функціонують.
Узагальнення конструктивних параметрів комбінованих інструментів з врахуванням їх взаємодії з робочими процесами створює теоретичні передумови для складання вербальних моделей, а, отже, дозволяє розробити математичні моделі адекватні фізичним.
Різнотипні інструменти в більшості випадків застосовуються для послідовної обробки отворів одного діаметру. Також вони застосовуються для обробки отворів різних діаметрів, але розташованих на одній осі.
По конструктивного виконання комбіновані інструменти розділяються на цілісні, складені і насадні. Цілісні комбіновані інструменти виготовляються з однорідних по найменуванню і марці матеріалів. До цілісних комбінованих інструментів також відносяться інструменти, в яких ріжуча частина виконана з інструментальної сталі, а хвостовик з конструкційної.
До складених комбінованих інструментів відносяться інструменти, які складаються з корпусу, до якого за допомогою паяння, зварки, гвинтів, рифлень і так далі кріпляться ріжучі елементи.
Ефективним є вживання комбінованих інструментів з непереточуваними пластинами, що дозволяють відносно швидко отримувати будь-яку комбінацію ріжучих кромок. Недоліком інструментів з непереточуваними пластинами є громіздкість елементів кріплення, що не дозволяє виготовляти інструменти для обробки отворів малих діаметрів.
Насадні комбіновані інструменти або набори, об'єднують однотипні або різнотипні інструменти загальним облямовуванням або одним з інструментів. Прикладом складених інструментів може служити декілька насадних зенкерів різних діаметрів, закріплених на одному облямовуванні.
Перевагою таких інструментів є можливість комбінацій на одному облямовуванні з різних діаметрів одновимірних інструментів, заміна зношеному або поламаному рівню, полегшення умов переточування.
За способом кріплення комбіновані інструменти діляться на: інструменти з жорстким кріпленням і однією направляючою втулкою; інструменти з плаваючим кріпленням без направляючих втулок; інструменти з плаваючим кріпленням і однією або декількома направляючими втулками.
Спосіб кріплення інструменту визначається його типом і розмірами, моделлю верстата, особливістю конструкції пристосування, в якому кріпиться деталь, силовими діями, точністю обробки.
Жорстко кріпляться, як правило, зенкери і свердла. Розгортки можуть кріпитися як жорстко, так і в плаваючому патроні. Спосіб кріплення розгортки визначається точністю устаткування: при високій його точності розгортка кріпиться жорстко, при низькій, в плаваючому патроні.
На агрегатних верстатах інструменти, як правило, прямують кондукторними втулками. При обробці деталей на верстатах з ЧПУ або багатоопераційних верстатах всі осьові інструменти працюють без кондукторних втулок, незалежно від способу кріплення.
Одним з основних елементів, складових робочий процес, є кінематика руху інструменту. Осьові інструменти, мають обертальний і поступальний рух, які задаються кінематикою верстата. Наявність зовнішніх дій у вигляді вимушених коливань викликає появу ограновування в поперечному перетині циліндрової поверхні, причому це явище спостерігається при роботі практично всіх осьових інструментів.
Особливістю процесу стружкоутворення для осьових інструментів є те, що передня поверхня ріжучого клину, що забезпечує формування стружки, одночасно є стружковою канавкою, що служить для транспортування стружки від попередніх рівнів. Тому величина переднього кута є функцією від кута нахилу стружкової канавки. Таким чином, процеси стружкоутворення і транспортування стружки взаємозв'язані.
Сили різання, що діє на інструмент, визначає положення його осі, а, отже, і точність обробки. Причому необхідно враховувати, що момент, що крутить, надає вплив на радіальні переміщення інструменту, тобто до кожного рівня прикладено три сили, що викликають викривлення осі. Взаємний вплив сил, що діють на кожен рівень, робить істотний вплив на загальне положення осі.
За способом утворення поверхневого шару комбіновані інструменти так само, як і одновимірні, можна розділити на інструменти, що працюють: із зняттям стружки; пластичною деформацією (випрасовуванням). Спосіб випрасовування в чистому вигляді для комбінованих інструментів зустрічається рідко. Прикладом може служити свердло з ущільнюючими стрічками. Дане свердло має дві ущільнюючі стрічки, діаметр яких більше діаметру допоміжних ріжучих кромок. В результаті в процесі обробки поряд зі свердлінням відбувається випрасовування обробленої поверхні. Найчастіше спосіб випрасовування застосовується у поєднанні з різанням, тобто застосовується комбіноване формування поверхневого шару.
Зенкери виготовляють хвостовими цілісними (рис.1), хвостовими збірними зі вставними ножами, насадними цілісними і насадними збірними (рис.2).
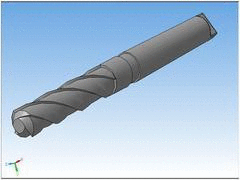
Рисунок 1 – Анімоване зображення цілісного зенкера (зроблено в mp_gif_animator 125 кБ, 5 кадр)
Зенкери роблять з швидкорізальної сталі або з пластинами твердого сплаву, що напаюваються на корпус зенкера або на корпус ножів в збірних конструкцій. Хвостові зенкери подібно до свердел кріплять за допомогою циліндричних або конічних хвостовиків, насадні зенкери мають конічний посадочний отвір (конусність 1:30) і торцеву шпонку для оберігання від провертування при роботі. По конструкції робочої частини хвостові зенкери аналогічні спіральним свердлам, але не мають поперечної ріжучої кромки і мають три зуби, завдяки чому забезпечується краще направлення при роботі і краща циліндричність і якість обробленої поверхні. Насадні зенкери мають чотири-шість зубів.
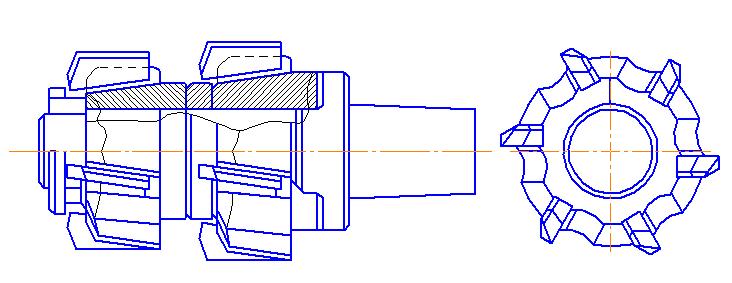
Рисунок 2 – Насадний збірний зенкер
Форма профілю поперечного перетину зенкера, що має три зуби, показана на рис. 3. Цей профіль аналогічний профілю канавки свердла і характеризується співвідношеннями: do = (0,35...0,5)d, В = (0,4...0,48)d, hл=(0,02...0,04)d.
Форма профілю зенкера, що має чотири зуби, показана на рис. 4. Висота зуба цих зенкерів h=(0,1...0,16) d. Спинка зуба криволінійна, що дозволяє обробляти зуб за один прохід, тоді як профіль, вказаний на мал. 3, вимагає роздільної обробки канавки і спинки зуба.
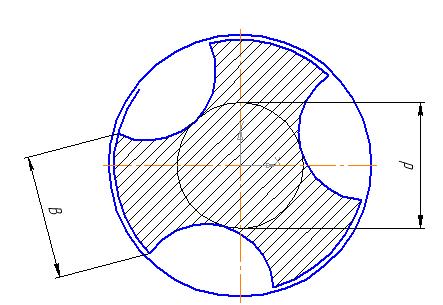
Рисунок 3 – Форма профілю поперечного перетину зенкера, що має три зуби
Зенкери з швидкорізальної сталі виготовляють хвостовими цілісними діаметрами від 10 до 40 мм, хвостовими збірними зі вставними ножами діаметром від 32 до 80 мм, насадними цілісними діаметром від 25 до 60 мм і насадними збірними діаметром від 40 до 120 мм. Хвостові зенкери роблять зварними – робоча частина з швидкорізальної сталі, хвостовик із сталей 45, 40Х, 45Х. Місце зварки зазвичай роблять на шийці. Задню поверхню в цілісних зенкерів оформляють по гвинтовій або конічній поверхні, в зенкерів збірної конструкції – по плоскості. Для кріплення ножів на корпусі роблять косі пази, нахилені до осі під кутом ω=10...20°. Передня поверхня корпуса плоска. Ножі мають клиновидну форму з кутом клину 5°, їх кріплять в корпусі за допомогою рифлень. Хвостові цілісні зенкери мають три зуби, насадні цілісні, – чотири.
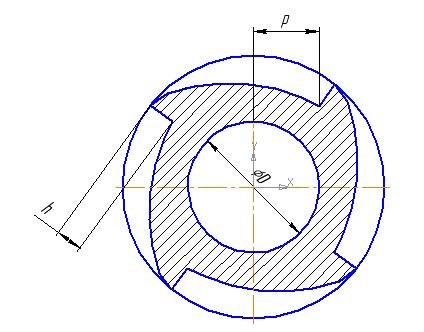
Рисунок 4 – Форма профиля поперечного сечения зенкера, имеющего четыре зуба
Висота зуба цих зенкерів h=(0,1...0,16) d. Спинка зуба криволінійна, що дозволяє обробляти зуб за один прохід, тоді як профіль, вказаний на мал. 2.67,, г вимагає роздільної обробки канавки і спинки зуба. Найчастіше зенкери виготовляють з розташуванням ріжучої кромки по радіусу (λ= 0°).
Зенкери, оснащені твердосплавними пластинами, можуть бути складеними і збірними. Складені хвостові зенкери виготовляють діаметром 14–50 мм, насадні 32–80 мм, насадні збірні зенкери діаметром 40–120 мм. Хвостові зенкери мають три зуби, насадні, – чотири, збірні зенкери – чотири-шість зубів. Корпуси зенкерів і ножів, що оснащуються пластинами з твердого сплаву, роблять із сталей 40Х або 45Х (36... 46hrcе), 9ХС (57...63HRCэ) або з швидкорізальної сталі (57...63HRCэ). Для їх оснащення застосовують пластини з твердих сплавів ВК6, ВК8, ВК6-М, ВК8-В, Т5К10, Т14К8, Т15К6. Кріплення пластин відбувається за допомогою напайки [6].
Висновок
Важливе значення, особливо для автоматизованого виробництва, має надійність інструменту, пристосованість до автоматизації, мала витрата інструментального матеріалу і низька собівартість. Цим вимогам відповідають збірні зенкери з механічним кріпленням ріжучих пластин. Заміна складених, зокрема напайних, зенкерів збірними є одній з найважливіших тенденцій розвитку технології обробки отворів в машинобудуванні.
При написанні даного реферату магістерська робота ще не завершена. Остаточне завершення: грудень 2013 року. Повний текст роботи і матеріали по темі можуть бути отримані у автора або його керівника після вказаної дати.
Список використаної літератури
- Костюкевич С. С. Точность обработки глубоких отверстий / Костюкевич C. C., Дечко Э. М., Долгов. В. И. – Минск: Вышейшая школа, 1978. – 144 с.
- Пазюк Е.И. Инструмент для обработки отверстий (сверла, зенкеры, развертки и расточной инструмент). - Л.: Ленинградское газетно-журнальное и книжное издательство, 1952. - 128 с.
- Совершенствование конструкций режущего инструмента посредством поискового проектирования // СТИН. – 2006 г. – №2.
- Максимов М.А. Комбинированные режущие инструменты./ Максимов М А., Киселева Л П., Шмелев А.Я. – Горький: Горьковский государственный университет, 1977, 86 с.
- Малишко І. О. Основи теорії проектування осьових комбiнованих інструментів: автореф. дис. на здобуття наук. ступеня доктора техн. наук : спец. 05.03.01 „Процессы механической обработки, станки и инструменты” / І. О. Малишко. – Київ, 1996. – 33 с.
- Сахаров Г.Н. Металлорежущие инструменты./ Сахаров Г.Н. Арбузов О.Б., Боровой Ю.Л., Гречишников В.А., Киселев А.С. – М.: Машиностроение, 1989. – 328 с.
- Технология обработки типовых отверстий деталей машин [электронный ресурс]. - Режим доступа:http://elite-instrument.ru/category/zenkery-/