Abstract
Содержание
- Introduction
- 1. Modern state of question and choice of directions of research
- 1.1 Threaded connections as element of metallurgical machines
- 1.2 Determinations of necessary effort of inhaling
- 1.3 Control of inhaling of the threaded connections
- 1.4 Raising of research tasks
- Conclusions
- References
Introduction
The threaded connections are the most responsible elements of metallurgical equipment [1]. In a number of cases the wrong inhaling of the threaded connections of metallurgical machines results in the considerable worsening of work of mechanisms, that accordingly influences on reliability and longevity of work of machines.
The threaded connections work mainly with the preliminary inhaling due to that the external variable loading is passed on the threaded detail only partly. In practice at the timely preliminary inhaling of tension diminish as a result of burries on joints, relaxation of tensions etc. Application of control methods becomes obligatory for prevention of breakages of mechanisms.
At the choice of the most effective method of control it is necessary to take into account the row of factors : type of construction, requirements to reliability, quality making, surrounding terms, qualification of personnel, – that does not allow to do an unambigiuous and simple choice. A substantial defect is a condition of application of certain method of control only for the corresponding group of the threaded connections. For example: method of control of corner of turn of nut &of ndash; simple in execution, however suitable for connections with short screw-bolts, because the calculation corner of turn of nut for such screw-bolts is small and the errors of method affect in a most degree; method of control of twisting moment of inhaling of nut – based on measuring of rotary-type moment by means of the keys, not effective for the threaded connections.
Possible decision of this problem – development of method of control that would be able to overcome all basic types of the threaded connections (long, short,) of metallurgical machines. For this purpose it is necessary to educe the lacks of existent methods of control, mathematically to ground the most perspective method and confirm his experimental way.
Efficiency is base on realization of timely repair works after inhaling or replacement of the threaded connections, decline of the dynamic loading and reduction of amount of the refuses related to the threaded connections.
1. Modern state of question and choice of directions of research
1.1 Threaded connections as element of metallurgical machines
Threaded connection – sectional connection of details of machines through a spiral or spiral surface (screw-thread). This connection is most widespread from his numerous dignities. In simplest case for connection it is necessary to twirl two details having screw-thread with going near each other parameters. For disconnection (slots) it is necessary to produce actions upside-down [2,3].
Screw-thread – equispaced ledges or cavities of permanent section, form on a cylindrical or conical surface on a spiral line with a permanent step. It is the basic element of the threaded connection.
Classification and basic signs of threads [4]:
- unit of diameter (metrical, one inch, module,);
- location on a surface (male and internal thread);
- direction of motion of helicoid (right, left);
- number of stopping (one and multiple-thread);
- profile (three-cornered, razor, rectangular, round to and other);
- formative surface on that a screw-thread (cylindrical screw-thread and conical screw-thread) is located;
- setting (timber, fastener-sealing, working to and other).
A metrical screw-thread (figure 1) is the basic type of timber screw-thread. The profile of screw-thread is set ГОСТ 9150-81 and is an equilateral triangle with the corner of profile α = 60°. The profile of screw-thread on a bar differs from the profile of screw-thread in opening in size dulling of his tops and cavities. The basic parameters of metrical screw-thread it is been: nominal diameter – d(D) and step of screw-thread – Р set ГОСТ 8724–81 [5].
For ГОСТ 8724–81 with a large step a few shallow steps correspond every nominal size of screw-thread. Screw-thread with a shallow step are used in the thin-walled connections for the increase of their impermeability, for realization of regulation in the devices of fine mechanics and optics, with the purpose of increase of resistibility of details to wrenching.
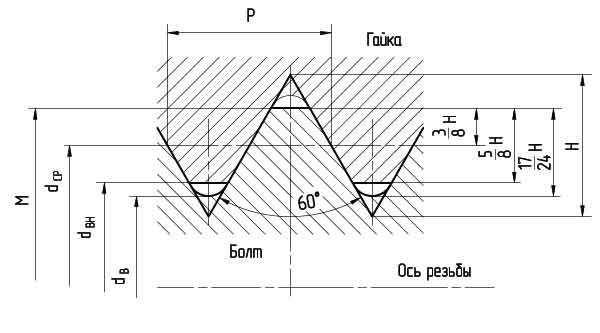
Figure 1 – Metrical screw-thread
Descriptions of the threaded connections
Dignities [6]:
- technologicalness;
- interchangeability;
- universality;
- reliability;
- mass character.
Defects:
- untwisting at the variable loading and without application of the special devices (facilities);
- opening under timber details cause the concentration of tensions;
- for the compression (pressurizing) of connection it is necessary to use additional technical decisions.
The standard timber threaded details are very various in due form, to exactness of making, material, coverage. They are divided into the detail of the general setting and special, intended for application in the certain types of wares or in the special terms [7].
Basic are screw-bolts, screws, hairpins and anchors.
A screw-bolt (figure 2) consists of two parts: head and bar screw-threaded. In most constructions of screw-bolts on his head there is conical chamfer smoothed the sharp edges of head and facilitating imposition of wrench at screwing together.
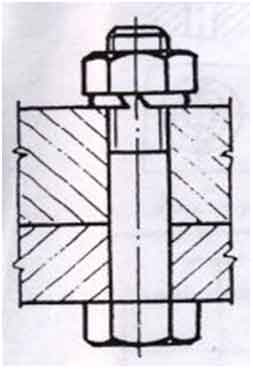
Figure 2 – Screw-bolt
The screw-bolts produced by industry distinguish [8]:
- in due form to the sizes of head;
- on a form a bar;
- on the step of screw-thread;
- by the nature executions;
- on exactness of making.
A form and sizes of head of screw-bolt depend on setting and terms of work.
Screw-bolts with hexagon-heads got a wideuse in industry.
Hairpin – timber detail, intended for connection of details inter se, having the smooth opening or threaded opening, executed as a cylindrical bar there is a screw-thread on the ends of that [9].
Hairpin the threaded is used for gathering and fixing on the set distance of elements of metallic constructions with a metrical screw-thread. Also hairpin the threaded can be used for fastening of the suspended constructions.
The threaded connections are one of the most responsible elements of metallurgical equipment. In a number of cases the wrong inhaling results in the considerable worsening of work of mechanisms, that accordingly influences on reliability and longevity of work of machine. It is therefore necessary to investigate the basic functions of the threaded connections that are the correct inhaling and control.
1.2 Determinations of necessary effort of inhaling
At maintenance of metallurgical equipment constantly there are the problems, related to the threaded connections that require an immediate removal. In order to avoid these problems it is necessary to know correct technology of inhaling. This question such specialists engaged in : Sedush S., Sedush V., Birger I., Iosilenich G., Tailor&bsp;L., Pesin L. et al. There is I. Birger,И.А., G. Iosilenich in a book Threaded and flange connections
general principles of planning of the threaded and flange connections are considered. Resulted taking about the calculation of the threaded connections on durability at quiescent and variable loads in the conditions of normal, lowered and enhanceable temperatures; influence of structural and technological factors is shown on durability of connections. Given to recommendation on the optimal constructions of the threaded and flange connections. In a book Sedush S. Calculation and constructing of hydraulic instruments
, Tailor L., Pesin L. Hand machines for assembling works
basic principles of calculation and choice of assembling equipment are considered for metallurgical machines. We will consider the theory of technology of inhaling expounded in a book Birger I. Calculation of the threaded connections
.
Technology of inhaling
Greater part of the threaded connections applied in modern machines, collect with the preliminary inhaling. Correct inhaling of connection – one of basic terms of reliable work of connection.
Tensions of the preliminary inhaling are set in accordance with the terms of impermeability and closeness (inflexibilities) of joint. The last is the necessary condition of providing of durability of the threaded connections at the variable loading [1]:
σ0 = σр(1-x),
where σ0 = F0/A1 – tension of the preliminary inhaling(F0 – force of inhaling);
σр = Fр/A1 – nominal tension from the most external (working) loading, arising up in the bar of screw-bolt (hairpins) during work;
х – coefficient of the basic loading (usually х = 0,2 ... 0,4).
At σ0 ≤ σр(1-x) a joint opens up and the external loading is fully passed on a screw-bolt, sharply reducing longevity of connection.
In practice, as a rule, tensions of the preliminary inhaling diminish as a result of crumpling of burries on joints, relaxation of tensions. Maybe also increase of workloads during work of machine on the off-design mode (for example, because of water-hammer, during work on the resonant mode of and other). Taking into account it calculation tension of inhaling is increased in ν one time:
σ0 = νσр(1-x).
According to the condition of closeness of joint ν = 1,25 ... 2,00 at a permanent ladening and ν – 2,5 ... 4,0 at a variable ladening.
In accordance with the condition of impermeability ν = 1,3 ... 2,5 at pads; ν = 2,5 ... 3,5 at the metallic shaped gaskets; ν = 3,0 ... 4,0 at flat metallic gaskets [1].
The increase of tension of the preliminary inhaling results in substantial reduction of stake of the workload perceived by the screw-bolts of connection, and assists her maintenance during exploitation.
Thus, large force of inhaling is the effective means of increase of reliability of work of the threaded connections (figure 3).
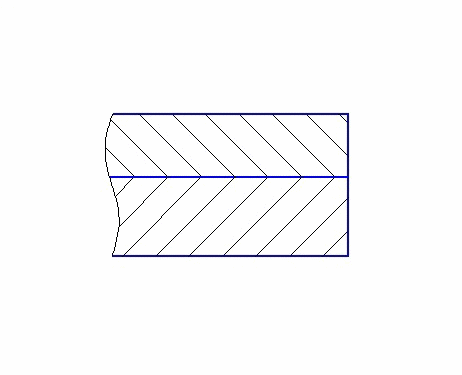
Figure 3 - Inhaling of the threaded connection
(animation: 6 shots, 6 cycles of reiteration, 45,8 kilobytes)
In order to avoid appearance of flowages (remaining lengthening and wring) the top limit of tensions of inhaling is limited to the minimum assumed value of coefficient of margin of safety on permanent tensions.
It should be noted that the increase of tension of inhaling reduces maximum amplitude of cycle (limit of endurance of connection) sometimes. However in this case the stake of the external loading perceived by a screw-bolt, as a rule, diminishes substantially [1].
Instrument
At tightening of the threaded connections control of effort of the preliminary inhaling is produced in parallel. Basic instruments for inhaling of the threaded connections it is been:
- Dynamometric key (figure 4) – it is a precision instrument for inhaling of the threaded connections with the exactly set moment. At planning of any building constructions, any industrial or building equipment, any technique, her assembling is assumed with the defined value of twisting moment for every concrete connection [1-4].
- Unlike traditional instruments hydraulic adaptations (figure 5) create axial pressure that provides more reliable inhaling and diminishes probability of cutting away and weakening of screw-bolt on-loading. In addition, their ability of the effective use of mechanical terms allows to decrease the tiredness of screw-bolt in the conditions of the dynamic loading. Hydraulic principle of inhaling of screw-bolts has next advantages [1]:
- the size of tension is exactly known from the primary loading;
- the size of tension from the primary loading can be maximally close to the limit of resiliency of screw-bolt;
- possibility of the simultaneous inhaling of a few screw-bolts;
- hydraulic adaptations are simpler and safer in exploitation, than dynamometric keys;
- ideally befits for the systems of the automatic inhaling of screw-bolts.
- Impact wrench – hand instrument intended for a rollup and unscrewing of the threaded connections on screw-bolts and nuts, and also for twisting in and unscrewing of wood grouses and bolt-screws, with the managed twisting moment [4].
- Key for measuring of corner of turn of nut (figure 6) – measuring of corner of turn of nut at editing with exactness 10... 15° does not cause difficulties, he is executed with the use of a measure lining.
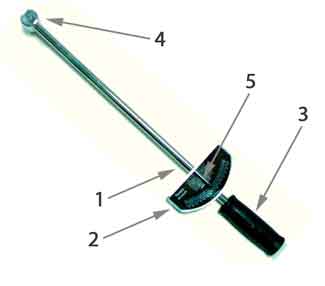
Figure 4 – Dynamometric key
1 – corps, 2 – scale, 3 – pen, 4 – square for a butt-end head, 5 – pointer
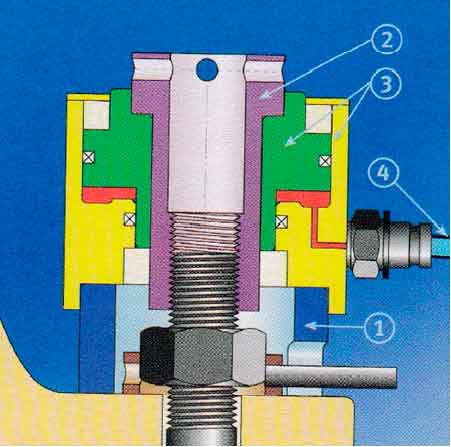
Figure 5 – Hydraulic key
1 – Twirling cartridge, 2 – Hydraulic adaptation, 3 – Working nut, 4 – Hydraulic pressure
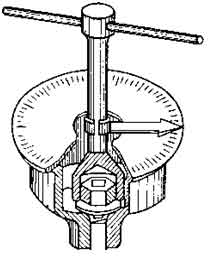
Figure 6 – Key for inhaling of connections, nut controlled on the corner of turn
The necessity of study of question of effort of the preliminary inhaling is brightly represented at the design of disrepairs of the threaded connections.
Design of disrepairs of the threaded connections
A construction of model is procedure of determination of principal reason of disrepair on the basis of existent list of types of refuses. Drafting of model flow-chart as a tree of cause-effect connections is usually used, to see the betweennesss of causes and effects by the refuses of different kinds. All data for procedure of diagnosticating already exist and does not require the repeated estimation. If a model is used for the construction of prognosis, then corresponding data must be predicted [Гост Р ИСО 13379-2009].
The tree of cause-effect connections puts in order present knowledge as follows:
- from past experience principal reason of refuse of one or a few kinds is known;
- betweennesss by the refuses of different kinds can be described through the factors of influence or criteria of initialising;
- the diagnostic signs of refuse of some kind can initiate other refuses, render or not have influence on them.
The tree of cause-effect connections of disrepairs of the threaded connections is shown on a figure 7.
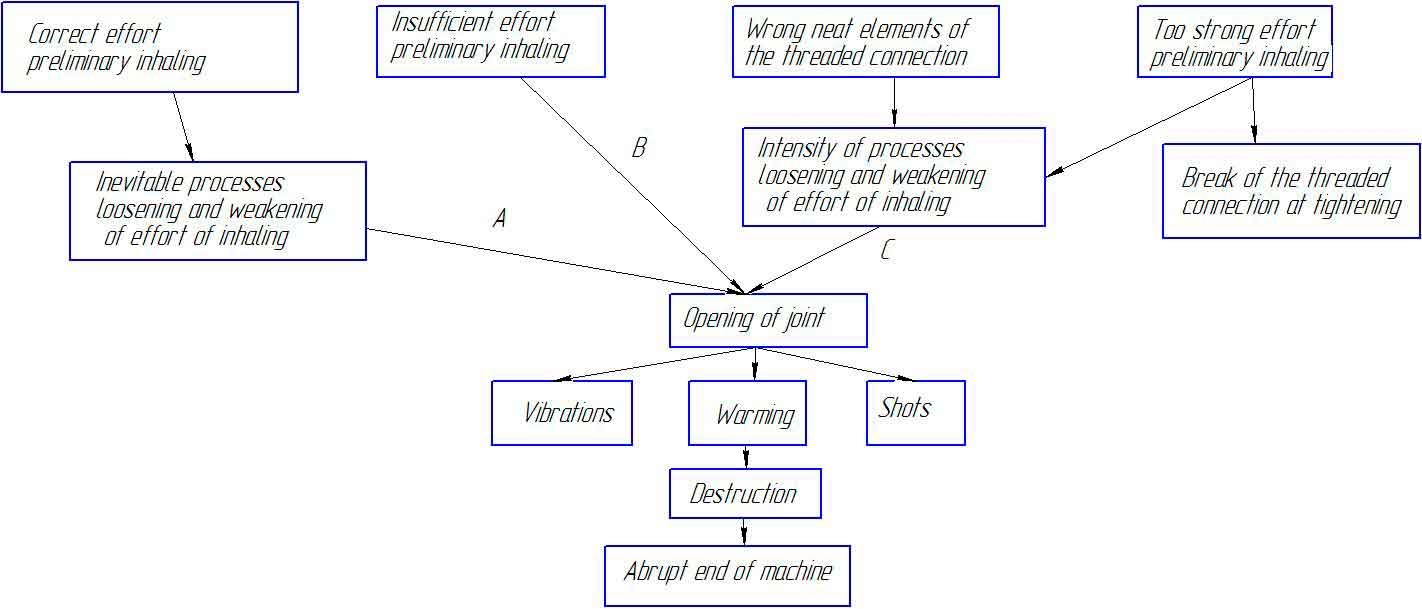
Figure 7 – The tree of cause-effect connections of disrepairs of the threaded connections is shown
А – minimum speed of processes, B – a joint is exposed initially, C – high-rate of processes
On a figure evidently, that the most dangerous state at insufficient effort of the preliminary inhaling (B). In this case a joint is exposed initially, therefore shots and vibrations result in wrong work of all mechanism, and also to destruction of the threaded connection. At the wrong selection of components and too strong effort (C) – middle speed of opening of joint
Normal work of machine depends (А) on the correct choice of components of the threaded connection and force of the preliminary tightening. Thus the inevitable processes of unscrewing and weakening of effort pass at minimum speeds.
From the tree of cause-effect connections evidently, that after opening of joint the threaded connection works wrong, by investigation what the abrupt ends of machine become. Therefore basic tasks hired is exposures of dependences of different descriptions before and after opening of joint, development of operating method of control that will allow timely to prevent the consequences of weakening of effort of the preliminary inhaling.
1.3 Control of inhaling of the threaded connections
Control of the threaded connections comes true with the purpose of maintenance of the set effort of inhaling. He is distinguished two kinds[10,11]:
- assembling;
- operating.
Assembling control is used directly at inhaling of the threaded connection. Distinguish such basic methods:
- Acoustic control of mechanical tensions is in the threaded connections – based on measuring of descriptions of resilient waves spreading in an environment, the calculation of operating size of mechanical tensions comes true on the basis of the precision measuring of time of distribution of BONDS of waves in material [12-15].
- Control on lengthening of screw-bolt (screw) – based on measuring of change of distance at inhaling between the end of screw-bolt and corps, applying indicators or templates for this purpose. For the responsible threaded connections apply wirestrain gauge (glued on smooth part of screw-bolt or inundated in the central opening) that after measuring can remain on a detail during further exploitation [1].
- Method of control on the corner of turn of nut – in this case in technical requirements on assembling of the threaded connection specify the corner of turn of nut (in degrees). Measuring of corner of turn of nut at editing with exactness 10 ... 15° does not cause difficulties; he is executed with the use of a measure lining, templates and othe.
- Control on the twisting moment of inhaling of nut – Based on measuring of rotary-type moment by means of the prograduirovannyh keys: dynamometric and maximum. Inhaling ceases at an achievement a moment on the key of the value set by technical requirements.
- Method of axial extraction of hairpin (screw-bolt) – consists in preliminary tension of screw-bolt (hairpins) with effort equal to the required effort of inhaling, by the subsequent rollup of nut from a hand to support in an underlayment and by the removal of loading from a screw-bolt throwing down of hydraulic pressure, whereupon connection gets the set effort of inhaling. Hairpin (screw-bolt) must come forward above a nut no less what on 0,8d, where d – diameter of hairpin [15-20].
Operating control presently is not used on metallurgical enterprises. Therefore this question is actual in our time. At a decision reduction of temporal resource is possible at technical service and repair, that will result in the increase of volume of the realized products.
1.4 Raising of research tasks
An aim hired is development of operating method of control of effort of inhaling.
Tasks:
- to define basic properties of the threaded connections as an element of metallurgical machines;
- to work out a mathematical model as dependences;
- to offer hypotheses on realization of experiment;
- to prepare a stand for realization of experiment;
- to conduct an experiment;
- to estimate the results of experiment;
- to check accordance of results of realization of experiment with adequacy of mathematical model;
- practical application;
- to check efficiency of the worked out method of control.
Conclusions
Operating control presently is not used on metallurgical enterprises. Therefore this question is actual in our time. At a decision reduction of temporal resource is possible at technical service and repair, that will result in the increase of volume of the realized products.
Within the framework of undertaken studies it is executed:
- The threaded connections, as elements of metallurgical machines, are investigational.
- On the basis of analysis of literary sources the basic types of the threaded connections are distinguished.
- Methodology of determination of effort of the preliminary inhaling is investigational.
- The basic methods of control of effort of inhaling of the threaded connections are educed.
- The tree of cause-effect disrepairs of the threaded connections is worked out.
At writing of this report master's degree work is not yet completed. Final completion: November, 2013. Complete text of work and materials on the topic can be got for an author or his leader after the named date.
References
- Седуш С.В. Расчет и конструирование гидравлических инструментов / С.В. Седуш – Донецк: 2004. – 152 с.
- Биргер И.А., Иоселенич Г.Б. Резьбовые и фланцевые соединения / И.А. Биргер, Г.Б. Иоселенич – М.: Машиностроение, 1990.– 368 с.
- Сидоров В.А., Седуш В.Я., Кравченко В.М. Техническое диагностирование механического оборудования / В.А. Сидоров, В.Я. Седуш, В.М. Кравченко. – Донецк: ООО «Юго Восток, Лтд», 2009. – 459 с.
- Портной Л.С., Песин Л.М. Ручные машины для монтажных работ / Л. С. Портной, Л.М. Песин. – К.: Будівельник, 1977. – 132 с.
- Рабинер Е.Г. Монтаж и эксплуатация подшипниковых узлов / Е.Г. Рабинер. – М.: Машгиз, 2–е издание, 1960. – 275 с.
- Бабат Г.И. Индукционный нагрев металла и его промышленное применение / Г.И. Бабат. – М., Л.: Энергия, 2–е изд., 1965. – 552 с.
- Бейзельман Р.Д., Цыпкин Б.В. Перель Л.Я. Подшипники качения / Р.Д. Бейзельман, Б.В. Цыпкин, Л.Я. Перель. – М.: Машиностроение, 1975.
- Федоров Б.Ф. Рациональный способ рачпрессовки и запрессовки деталей / Б.Ф. Федоров. – М., Свердловск: Машгиз, 1955. – 68 с.
- Александров М.П. Подъемно-транспортные машины / М.П. Александров. – М.: Высшая школа, 1972.
- Александров Б.И., Василец Ф.П. Влияние технологии изготовления и асимметрии цикла на циклическую прочность и долговечность соединений / Б.И. Александров, Ф.П. Василец. - Вестник машиностроения, 1964, № 4.
- Байков Б.А. Влияние пониженных температур на прочность крепежных винтов / Б.А. Байков. – Изв. вузов.: Машиностроение, 1968, № 6.
- Биргер И.А. Расчет резьбовых соединений / И.А. Биргер. – М.: Оборонгиз, 1959 – 252 с.
- Биргер И.А., Иосилевич Г.Б. Резьбовые соединения / И.А. Биргер, Г.Б. Иосилевич. – М.: Машиностроение, 1973 – 256 с.
- Биргер И.А., Шорр Б.Ф., Иосилевич Г.Б. Расчет на прочность дета¬лей машин / И.А. Биргер, Б.Ф. Шорр, Г.Б. Иосилевич. – М.: Машиностроение, 1979 – 702 с.
- Биргер И.А., Кутепова Т.В. Распределение нагрузки в резьбовых соединениях тонкостенных деталей / И.А. Биргер, Т.В. Кутепова – Вестник машиностроения, 1973, № 5.
- Вольфсон А.С., Либерман Л.Я. Испытание на длительную прочность резьбовых соединений / А.С. Вольфсон , Л.Я. Либерман. – Заводская лаборатория, 1968, № 11.
- Гоулд Д., Микич М. Площади контакта и распределение давлений в болтовых соединениях / Д. Гоулд, М. Микич. – Конструирование и технология машиностроения, 1972, № 3 – 99 с.
- Зенкевич О. Метод конечных элементов в технике / О. Зенкевич. – М.: Мир, 1975 – 539 с.
- Змиевский В.И., Замилацкий Е.П., Приведенцева В.С. Свинчиваемость резьбовых соединений из титановых сплавов / В.И. Змиевский, Е.П. Замилацкий, В.С. Приведенцева. – Вестник машиностроения, 1975, № 1 – 47 с.
- Иванов С.И., Шатунов М.П., Красота В.К. Меридиональные остаточные напряжения в резьбовой части болта / С.И. Иванов, М.П. Шатунов, В.К. Красота. – Вестник машиностроения, 1982, № 11 – 38 с..