Реферат по теме выпускной работы
Содержание
- Введение
- 1. Современное состояние вопроса и выбор направлений исследования
- 1.1 Резьбовые соединения как элемент металлургических машин
- 1.2 Определения необходимого усилия затяжки
- 1.3 Контроль затяжки резьбовых соединений
- 1.4 Постановка задач исследования
- Выводы
- Список источников
Введение
Резьбовые соединения являются наиболее ответственными элементами металлургического оборудования [1]. В ряде случаев неправильная затяжка резьбовых соединений металлургических машин приводит к значительному ухудшению работы механизмов, что соответственно влияет на надежность и долговечность работы машин.
Резьбовые соединения работают преимущественно с предварительной затяжкой, благодаря которой внешняя переменная нагрузка передается на резьбовую деталь лишь частично. На практике при своевременной предварительной затяжке напряжения уменьшаются в результате неровностей на стыках, релаксации напряжений и т.д. Применение методов контроля становится обязательным для предотвращения поломок механизмов.
При выборе наиболее эффективного метода контроля следует учесть ряд факторов: тип конструкции, требования к надежности, качество изготовления, окружающие условия, квалификация персонала, – которые не позволяют сделать однозначный и простой выбор. Существенным недостатком является условие применения определенного метода контроля лишь для соответствующей группы резьбовых соединений. Например: метод контроля угла поворота гайки – прост в исполнении, однако не пригоден для соединений с короткими болтами, так как расчетный угол поворота гайки для таких болтов невелик и погрешности метода сказываются в наибольшей степени; метод контроля крутящего момента затяжки гайки – основан на измерении вращающего момента с помощью проградуированных ключей, не эффективен для крупногабаритных резьбовых соединений.
Возможное решение этой проблемы – разработка метода контроля, который смог бы охватить все основные виды резьбовых соединений (длинные, короткие, крупногабаритные) металлургических машин. Для этого необходимо выявить недостатки существующих методов контроля, математически обосновать наиболее перспективный метод и подтвердить его экспериментальным путем.
Эффективность основывается на проведении своевременных ремонтных работ по затяжке или замене резьбовых соединений, снижении динамической нагрузки и уменьшении количества отказов, связанных с резьбовыми соединениями.
1. Современное состояние вопроса и выбор направлений исследования
1.1 Резьбовые соединения как элемент металлургических машин
Резьбовое соединение – разъёмное соединение деталей машин при помощи винтовой или спиральной поверхности (резьбы). Это соединение наиболее распространено из-за его многочисленных достоинств. В простейшем случае для соединения необходимо закрутить две детали, имеющие резьбы с подходящими друг к другу параметрами. Для рассоединения (разьёма) необходимо произвести действия в обратном порядке [2,3].
Резьба – равномерно расположенные выступы или впадины постоянного сечения, образованные на цилиндрической или конической поверхности по винтовой линии с постоянным шагом. Является основным элементом резьбового соединения.
Классификация и основные признаки резьб [4]:
- единица измерения диаметра (метрическая, дюймовая, модульная, питчевая резьба);
- расположение на поверхности (наружная и внутренняя резьба);
- направление движения винтовой поверхности (правая, левая);
- число заходов (одно- и многозаходная);
- профиль (треугольный, трапецеидальный, прямоугольный, круглый и др.);
- образующая поверхность, на которой расположена резьба (цилиндрическая резьба и коническая резьба);
- назначение (крепежная, крепежно-уплотнительная, ходовая и др.).
Метрическая резьба (рисунок 1) является основным типом крепежной резьбы. Профиль резьбы установлен ГОСТ 9150–81 и представляет собой равносторонний треугольник с углом профиля α = 60°. Профиль резьбы на стержне отличается от профиля резьбы в отверстии величиной притупления его вершин и впадин. Основными параметрами метрической резьбы являются: номинальный диаметр – d(D) и шаг резьбы – Р, устанавливаемые ГОСТ 8724–81 [5].
По ГОСТ 8724–81 каждому номинальному размеру резьбы с крупным шагом соответствует несколько мелких шагов. Резьбы с мелким шагом применяются в тонкостенных соединениях для увеличения их герметичности, для осуществления регулировки в приборах точной механики и оптики, с целью увеличения сопротивляемости деталей самоотвинчиванию.
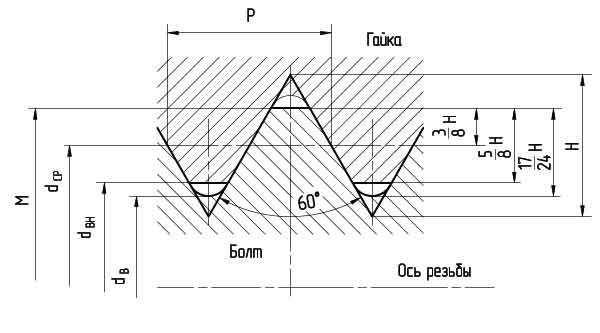
Рисунок 1 – Метрическая резьба
Характеристики резьбовых соединений
Достоинства [6]:
- технологичность;
- взаимозаменяемость;
- универсальность;
- надёжность;
- массовость.
Недостатки:
- раскручивание (самоотвинчивание) при переменных нагрузках и без применения специальных устройств (средств);
- отверстия под крепёжные детали вызывают концентрацию напряжений;
- для уплотнения (герметизации) соединения необходимо использовать дополнительные технические решения.
Стандартные крепежные резьбовые детали весьма разнообразны по форме, точности изготовления, материалу, покрытию. Их разделяют на детали общего назначения и специальные, предназначенные для применения в определенных видах изделий или в особых условиях [7].
Основными являются болты, винты, шпильки и анкеры.
Болт (рисунок 2) состоит из двух частей: головки и стержня с резьбой. В большинстве конструкций болтов на его головке имеется коническая фаска, сглаживающая острые края головки и облегчающая наложение гаечного ключа при свинчивании.
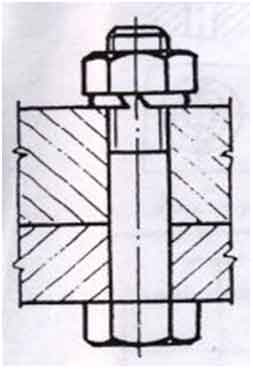
Рисунок 2 – Болт
Выпускаемые промышленностью болты различают [8]:
- по форме и размерам головки;
- по форме стержня;
- по шагу резьбы;
- по характеру исполнения;
- по точности изготовления.
Форма и размеры головки болта зависят от назначения и условий работы.
Болты с шестигранными головками получили широкое применение в промышленности.
Шпилька – крепёжная деталь, предназначена для соединения деталей между собой, имеющих гладкие отверстия или резьбовые отверстия, выполненная в виде цилиндрического стержня на концах которого имеется резьба [9].
Шпилька резьбовая используется для стягивания и фиксации на заданном расстоянии элементов металлических конструкций с метрической резьбой. Также шпилька резьбовая может использоваться для крепления подвесных конструкций.
Резьбовые соединения являются одними из наиболее ответственных элементов металлургического оборудования. В ряде случаев неправильная затяжка приводит к значительному ухудшению работы механизмов, что соответственно влияет на надежность и долговечность работы машины. Поэтому необходимо исследовать основные функции резьбовых соединений, которыми являются правильная затяжка и контроль.
1.2 Определения необходимого усилия затяжки
При обслуживании металлургического оборудования постоянно возникают проблемы, связанные с резьбовыми соединениями, которые требуют немедленного устранения. Во избежание данных проблем необходимо знать правильную технологию затяжки. Данным вопросом занимались такие специалисты: Седуш С.В., Седуш В.Я., Биргер И.А., Иоселенич Г.Б., Портной Л.С., Песин Л.М. и другие. В книге Биргер И.А., Иоселенич Г.Б. Резьбовые и фланцевые соединения
рассмотрены общие принципы проектирования резьбовых и фланцевых соединений. Приведены сведения о расчете резьбовых соединений на прочность при постоянных и переменных нагрузках в условиях нормальных, пониженных и повышенных температур; показано влияние конструктивных и технологических факторов на прочность соединений. Даны рекомендации по оптимальным конструкциям резьбовых и фланцевых соединений. В книге Седуш С.В. Расчет и конструирование гидравлических инструментов
, Портной Л.С., Песин Л.М. Ручные машины для монтажных работ
рассмотрены основные принципы расчета и выбора монтажного оборудования для металлургических машин. Рассмотрим теорию технологии затяжки изложенную в книге Биргер И.А. Расчет резьбовых соединений
.
Технология затяжки
Большую часть резьбовых соединений, применяемых в современных машинах, собирают с предварительной затяжкой. Правильная затяжка соединения – одно из основных условий надежной работы соединения.
Напряжения предварительной затяжки устанавливают в соответствии с условиями герметичности и плотности (жесткости) стыка. Последнее является необходимым условием обеспечения прочности резьбовых соединений при переменных нагрузках [1]:
σ0 = σр(1-x),
где σ0 = F0/A1 – напряжение предварительной затяжки (F0 – сила затяжки);
σр = Fр/A1 – номинальное напряжение от наибольшей внешней (рабочей) нагрузки, возникающее в стержне болта (шпильки) при работе;
х – коэффициент основной нагрузки (обычно х = 0,2 ... 0,4).
При σ0 ≤ σр(1-x) стык раскрывается и внешняя нагрузка полностью передается на болт, резко снижая долговечность соединения.
На практике, как правило, напряжения предварительной затяжки уменьшаются в результате смятия неровностей на стыках, релаксации напряжений и т. д. Возможно также повышение рабочих нагрузок при работе машины на нерасчетном режиме (например, вследствие гидравлического удара, при работе на резонансном режиме и др.). С учетом этого расчетное напряжение затяжки увеличивают в ν раз:
σ0 = νσр(1-x).
Согласно условию плотности стыка ν = 1,25 ... 2,00 при постоянном нагружении и ν – 2,5 ... 4,0 при переменном нагружении.
В соответствии с условием герметичности ν = 1,3 ... 2,5 при мягких прокладках; ν = 2,5 ... 3,5 при металлических фасонных прокладках; ν = 3,0 ... 4,0 при плоских металлических прокладках [1].
Повышение напряжения предварительной затяжки приводит к существенному уменьшению доли рабочей нагрузки, воспринимаемой болтами соединения, и способствует ее сохранению при эксплуатации.
Таким образом, большая сила затяжки является эффективным средством повышения надежности работы резьбовых соединений (рисунок 3).
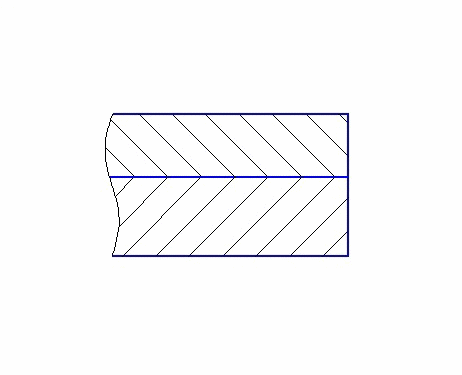
Рисунок 3 - Затяжка резьбового соединения
(анимация: 6 кадров, 6 циклов повторения, 45,8 килобайт)
Во избежание появления пластических деформаций (остаточного удлинения и скручивания) верхний предел напряжений затяжки ограничивают минимально допускаемым значением коэффициента запаса прочности по постоянным напряжениям.
Следует отметить, что увеличение напряжения затяжки иногда снижает предельную амплитуду цикла (предел выносливости соединения). Однако в этом случае доля внешней нагрузки, воспринимаемой болтом, как правило, существенно уменьшается [1].
Основные факторы, влияющие на правильную работу резьбовых соединений
Несмотря на то, что на первый взгляд резьбовое соединение является очень простым элементом оборудования, оно может стать источником проблем при монтажно-демонтажных и ремонтных работах. На практике выясняется, что для конструирования резьбовых соединений необходим методичный и точный подход, исключающий ошибки. Исследования показывают, что повреждения в резьбовых соединениях возникают, главным образом, из-за следующих факторов [10-15]:
- были неправильно подобраны компоненты соединения;
- недостаточное или превышенное усилие предварительного затягивания;
- неравномерное распределение усилия предварительного затягивания.
В связи с этим, наиболее важным становится вопрос правильного выбора компонентов применяемых резьбовых соединений и определение правильной величины усилия предварительного затягивания.
Для достижения надежного резьбового соединения решающее значение имеет правильное значение усилия затяжки. Она должна быть необходимой. Чем точнее выполнено предварительное затягивание, тем качественнее будет соединение, однако, с другой стороны, с увеличением точности увеличивается стоимость процедуры предварительного затягивания.
Недостаточное предварительное затягивание может привести к [10-20]:
- смещению поверхности соединения под действием осевой нагрузки;
- росту амплитуды напряжения болта;
- старению винта;
- отвинчиванию гайки от вибрации;
- скольжению соединения под действием сдвигающего момента.
Слишком сильное предварительное затягивание может привести к [10-20]:
- статической перегрузке болта;
- отвинчиванию болта под действием внешней растягивающей нагрузки в результате пластического удлинения;
- разрыванию болты еще при предварительном затягивании.
Имеется два наиболее существенных фактора снижающих прочность резьбового соединения [1]:
- самоотвинчивание;
- ослабление усилия затяжки.
О самоотвинчивании:
- по завершении процесса фиксации в болтовом соединении образуется нагрузка сжатия, поскольку болт затягивается, словно пружина и гайка, перемещаясь к головке болта, начинает создавать между фиксируемыми частями сжимающую силу. Как только напряжение сжатия исчезает, возникают условия, способствующие откручиванию гайки. Существующее в резьбе, а также между гайкой и головкой болта трение затрудняет затяжку болта [2];
- когда на резьбовое соединение воздействуют переменные нагрузки или вибрация, снижается вызванный трением эффект блокировки, что позволяет гайке скользить по резьбе свободно, уменьшая силу сцепления. Вибрационные воздействия могут быть в поперечном или продольном направлении, а также комбинированными, действующими в обоих направлениях. Наибольшую опасность представляют поперечные вибрации и знакопеременные горизонтальные нагрузки. Они довольно быстро приводят к ослаблению обычных незафиксированных резьбовых соединений. При чередовании продольных вибраций и осевых нагрузок ослабление резьбовых соединений менее значительно.
Об ослаблении усилия затяжки:
- в результате изменений осевых нагрузок на болт, а также температурного режима, происходит увеличение длины болта и, как результат, уменьшение усилия затяжки. Причиной подобного уменьшения может быть и деформация прокладочного материала. Изменение в длине может произойти при: проседании, когда шероховатые поверхности контактирующих деталей (например, шайбы, гайки) под воздействием давления болтового натяжения деформируются [5];
- проскальзывании, когда давление на опорную поверхность гаек или болтов выше сопротивления сжатия материалов соединяемых деталей.
Инструмент
При затягивании резьбовых соединений параллельно производится контроль усилия предварительной затяжки. Основными инструментами для затяжки резьбовых соединений являются:
- Динамометрических ключ (рисунок 4) – это прецизионный инструмент для затяжки резьбовых соединений с точно заданным моментом. При проектировании любых строительных конструкций, любого промышленного или строительного оборудования, любой техники, предполагается ее сборка с определенным значением крутящего момента для каждого конкретного соединения [1-4].
- В отличие от традиционных инструментов гидравлические приспособления (рисунок 5) создают осевое давление, которое обеспечивает более надежную затяжку и уменьшает вероятность срезания и ослабления болта под нагрузкой. Кроме того, их способность эффективного использования механических условий позволяет уменьшить усталость болта в условиях динамических нагрузок. Гидравлический принцип затяжки болтов имеет следующие преимущества [1]:
- точно известна величина растяжения от первоначальной нагрузки;
- величина растяжения от первоначальной нагрузки может быть максимально приближена к пределу упругости болта;
- возможность одновременной затяжки нескольких болтов;
- гидравлические приспособления проще и безопаснее в эксплуатации, чем динамометрические ключи;
- идеально подходит для систем автоматической затяжки болтов.
- Гайковерт – ручной инструмент, предназначенный для закручивания и откручивания резьбовых соединений на болтах и гайках, а также для вкручивания и выкручивания глухарей и анкер-шурупов, с регулируемым крутящим моментом [4].
- Ключ для измерения угла поворота гайки (рисунок 6) – измерение угла поворота гайки при монтаже с точностью 10... 15° не вызывает затруднений, его выполняют с применением мерных подкладок.
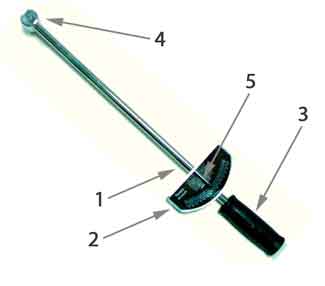
Рисунок 4 – Динамометрический ключ
1 – корпус, 2 – шкала, 3 – ручка, 4 – квадрат для торцевой головки, 5 – стрелка
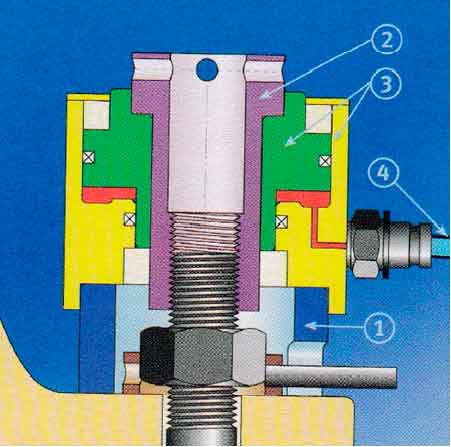
Рисунок 5 – Гидроключ
1 – Закручивающий патрон, 2 – Гидравлическое приспособление, 3 – Рабочая гайка, 4 – Гидравлическое давление
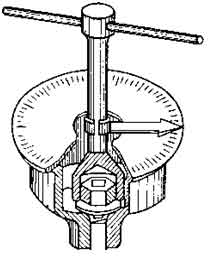
Рисунок 6 – Ключ для затяжки соединений, контролируемой по углу поворота гайки
Необходимость изучения вопроса усилия предварительной затяжки ярко отображается при моделировании неисправностей резьбовых соединений.
Моделирование неисправностей резьбовых соединений
Построение модели представляет собой процедуру определения основной причины неисправности на основе существующего перечня видов отказов. Составление блок-схемы модели в виде дерева причинно-следственных связей обычно используют, чтобы увидеть соотношения причин и следствий между отказами разных видов. Все данные для процедуры диагностирования уже существуют и не требуют повторной оценки. Если модель используют в целях построения прогноза, то соответствующие данные должны быть спрогнозированы [Гост Р ИСО 13379-2009].
Дерево причинно-следственных связей упорядочивает имеющиеся знания следующим образом:
- из прошлого опыта известна основная причина отказа одного или нескольких видов;
- соотношения между отказами разных видов могут быть описаны через факторы влияния или критерии инициализации;
- диагностические признаки отказа некоторого вида могут инициировать другие отказы, оказывать или не оказывать на них влияния.
Дерево причинно-следственных связей неисправностей резьбовых соединений показано на рисунке 7.
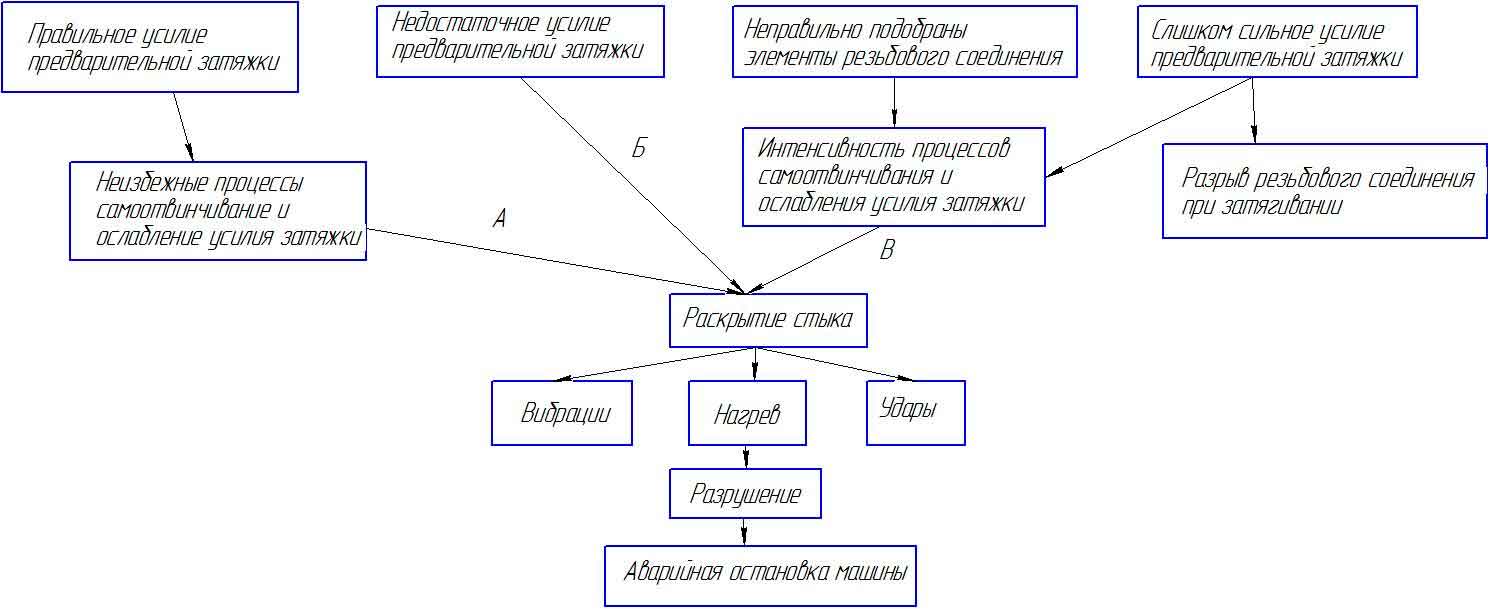
Рисунок 7 – Дерево причинно-следственных связей неисправностей резьбовых соединений
А – минимальная скорость процессов, Б – стык раскрыт изначально, В – высокая скорость процессов
На рисунке видно, что самое опасное состояние при недостаточном усилии предварительной затяжки (Б). В этом случае стык раскрыт изначально, поэтому удары и вибрации приводят к неправильной работе всего механизма, а также к разрушению резьбового соединения. При неправильном подборе компонентов и слишком сильном усилии (В) – средняя скорость раскрытия стыка
Нормальная работа машины зависит (А) от правильного выбора компонентов резьбового соединения и силы предварительного затягивания. При этом неизбежные процессы самоотвинчивания и ослабления усилия проходят при минимальных скоростях.
Из дерева причинно-следственных связей видно, что после раскрытия стыка резьбовое соединение работает неправильно, следствием чего становятся аварийные остановки машины. Поэтому основными задачами данной работы является выявления зависимостей различных характеристик до и после раскрытия стыка, разработка эксплуатационного метода контроля, который позволит своевременного предотвращать последствия ослабления усилия предварительной затяжки.
1.3 Контроль затяжки резьбовых соединений
Контроль резьбовых соединений осуществляется с целью поддержания заданного усилия затяжки. Его различают двух видов:
- монтажный;
- эксплуатационный.
Монтажный контроль применяется непосредственно при затяжке резьбового соединения. Выделяют такие основные методы:
- Акустический контроль механических напряжений в резьбовых соединениях – основан на измерении характеристик упругих волн, распространяющихся в среде, расчёт действующей величины механических напряжений осуществляется на основе прецизионных измерений времени распространения УЗ волн в материале [12-15].
- Контроль по удлинению болта (винта) – основан на измерении изменения расстояния при затяжке между концом болта и корпусом, применяя для этого индикаторы или шаблоны. Для ответственных резьбовых соединений применяют проволочные тензодатчики (наклеиваемые на гладкую часть болта или заливаемые в центральное отверстие), которые после измерения могут оставаться на детали при дальнейшей эксплуатации [1].
- Метод контроля по углу поворота гайки – в этом случае в технических условиях на сборку резьбового соединения указывают угол поворота гайки (в градусах). Измерение угла поворота гайки при монтаже с точностью 10 ... 15° не вызывает затруднений; его выполняют с применением мерных подкладок, шаблонов и др.
- Контроль по крутящему моменту затяжки гайки – Основан на измерении вращающего момента с помощью проградуированных ключей: динамометрических и предельных. Затяжка прекращается при достижении моментом на ключе значения, установленного техническими условиями.
- Метод осевой вытяжки шпильки (болта) – заключается в предварительном растяжении болта (шпильки) с усилием, равным требуемому усилию затяжки, последующим закручиванием гайки от руки до упора в опорную поверхность и снятием нагрузки с болта сбрасыванием гидравлического давления, после чего соединение получает заданное усилие затяжки. Шпилька (болт) должны выступать над гайкой не менее чем на 0,8d, где d – диаметр шпильки.
Эксплуатационный контроль в настоящее время не используется на металлургических предприятиях. Поэтому в наше время этот вопрос актуален. При решении возможно сокращение временного ресурса при техническом обслуживании и ремонте, что приведет к увеличению объема реализуемой продукции.
1.4 Постановка задач исследования
Целью данной работы является разработка эксплуатационного метода контроля усилия затяжки.
Задачи:
- определить основные свойства резьбовых соединений как элемента металлургических машин;
- разработать математическую модель в виде зависимостей;
- предложить гипотезы по проведению эксперимента;
- подготовить стенд для реализации эксперимента;
- провести эксперимент;
- оценить результаты эксперимента;
- проверить соответствие результатов проведения эксперимента с адекватностью математической модели;
- практическое применение;
- проверить эффективность разработанного метода контроля.
Выводы
Эксплуатационный контроль в настоящее время не используется на металлургических предприятиях. Поэтому в наше время этот вопрос актуален. При решении возможно сокращение временного ресурса при техническом обслуживании и ремонте, что приведет к увеличению объема реализуемой продукции.
В рамках проведенных исследований выполнено:
- Исследованы резьбовые соединения, как элементы металлургических машин.
- На основании анализа литературных источников выделены основные виды резьбовых соединений.
- Исследована методика определения усилия предварительной затяжки.
- Выявлены основные методы контроля усилия затяжки резьбовых соединений.
- Разработано дерево причинно-следственных неисправностей резьбовых соединений.
При написании данного реферата магистерская работа еще не завершена. Окончательное завершение: ноябрь 2013 года. Полный текст работы и материалы по теме могут быть получены у автора или его руководителя после указанной даты.
Список источников
- Седуш С.В. Расчет и конструирование гидравлических инструментов / С.В. Седуш – Донецк: 2004. – 152 с.
- Биргер И.А., Иоселенич Г.Б. Резьбовые и фланцевые соединения / И.А. Биргер, Г.Б. Иоселенич – М.: Машиностроение, 1990.– 368 с.
- Сидоров В.А., Седуш В.Я., Кравченко В.М. Техническое диагностирование механического оборудования / В.А. Сидоров, В.Я. Седуш, В.М. Кравченко. – Донецк: ООО «Юго Восток, Лтд», 2009. – 459 с.
- Портной Л.С., Песин Л.М. Ручные машины для монтажных работ / Л. С. Портной, Л.М. Песин. – К.: Будівельник, 1977. – 132 с.
- Рабинер Е.Г. Монтаж и эксплуатация подшипниковых узлов / Е.Г. Рабинер. – М.: Машгиз, 2–е издание, 1960. – 275 с.
- Бабат Г.И. Индукционный нагрев металла и его промышленное применение / Г.И. Бабат. – М., Л.: Энергия, 2–е изд., 1965. – 552 с.
- Бейзельман Р.Д., Цыпкин Б.В. Перель Л.Я. Подшипники качения / Р.Д. Бейзельман, Б.В. Цыпкин, Л.Я. Перель. – М.: Машиностроение, 1975.
- Федоров Б.Ф. Рациональный способ рачпрессовки и запрессовки деталей / Б.Ф. Федоров. – М., Свердловск: Машгиз, 1955. – 68 с.
- Александров М.П. Подъемно-транспортные машины / М.П. Александров. – М.: Высшая школа, 1972.
- Александров Б.И., Василец Ф.П. Влияние технологии изготовления и асимметрии цикла на циклическую прочность и долговечность соединений / Б.И. Александров, Ф.П. Василец. - Вестник машиностроения, 1964, № 4.
- Байков Б.А. Влияние пониженных температур на прочность крепежных винтов / Б.А. Байков. – Изв. вузов.: Машиностроение, 1968, № 6.
- Биргер И.А. Расчет резьбовых соединений / И.А. Биргер. – М.: Оборонгиз, 1959 – 252 с.
- Биргер И.А., Иосилевич Г.Б. Резьбовые соединения / И.А. Биргер, Г.Б. Иосилевич. – М.: Машиностроение, 1973 – 256 с.
- Биргер И.А., Шорр Б.Ф., Иосилевич Г.Б. Расчет на прочность дета¬лей машин / И.А. Биргер, Б.Ф. Шорр, Г.Б. Иосилевич. – М.: Машиностроение, 1979 – 702 с.
- Биргер И.А., Кутепова Т.В. Распределение нагрузки в резьбовых соединениях тонкостенных деталей / И.А. Биргер, Т.В. Кутепова – Вестник машиностроения, 1973, № 5.
- Вольфсон А.С., Либерман Л.Я. Испытание на длительную прочность резьбовых соединений / А.С. Вольфсон , Л.Я. Либерман. – Заводская лаборатория, 1968, № 11.
- Гоулд Д., Микич М. Площади контакта и распределение давлений в болтовых соединениях / Д. Гоулд, М. Микич. – Конструирование и технология машиностроения, 1972, № 3 – 99 с.
- Зенкевич О. Метод конечных элементов в технике / О. Зенкевич. – М.: Мир, 1975 – 539 с.
- Змиевский В.И., Замилацкий Е.П., Приведенцева В.С. Свинчиваемость резьбовых соединений из титановых сплавов / В.И. Змиевский, Е.П. Замилацкий, В.С. Приведенцева. – Вестник машиностроения, 1975, № 1 – 47 с.
- Иванов С.И., Шатунов М.П., Красота В.К. Меридиональные остаточные напряжения в резьбовой части болта / С.И. Иванов, М.П. Шатунов, В.К. Красота. – Вестник машиностроения, 1982, № 11 – 38 с..