Реферат за темою випускної роботи
Змiст
- Вступ
- 1. Актуальність теми
- 2. Мета і задачі дослідження
- 3. Результати дослідження
- 3.1 Аналіз процесу транспортування гірської маси технологічного комплексу поверхні як об'єкта автоматизації
- 3.2 Критичний огляд існуючих технічних рішень
- 3.3 Розробка схемотехнічного рішення системи автоматичного управління бункерно-транспортним ланцюгом поверхні шахти
- Висновки
- Перелік посилань
Вступ
Гірнича маса з шахти скіпом видається на поверхню в приймальний бункер, який розташований в надшахтній будівлі скіпового ствола. Далі через розподільну воронку надходить у дробильно-сортувальний пристрій, де гірська маса розподіляється на вугілля і породу. Видана на поверхню порода поступає на породний відвал.
Породний комплекс відноситься до технологічних об'єктах шахти з низьким рівнем автоматизації. На даному об'єкті найчастіше застосовується малоефективне ручне управління, яке призводить до істотних матеріальних витрат, і не виключає наявність аварійних ситуацій. Таким чином, підвищення рівня автоматизації породного комплексу є актуальним завданням.
1. Актуальність теми
Проблема транспортування гірської маси на породний відвал є комплексною, ефективність якої здебільшого залежить від рівня застосовуваних технічних рішень.
Слід так само звернути увагу на вивчення вимірювання маси породи у вагонетці при розвантаженні бункера. Контроль цього параметра дозволить знизити динамічні навантаження на електродвигун лебідки; дозволить забезпечити рівномірний розподіл породних мас у виробленому просторі кар'єрів, зонах обвалення, ущелинах, ярах і т.п. з підвітряного боку населених пунктів і промислових майданчиків з метою зменшення шкоди для навколишнього середовища.
Вирішити дані проблеми можливо при розробці системи автоматичного управління бункерно-транспортним ланцюгом поверхні шахти.
2. Мета і задачі дослідження
Метою дослідження є підвищення ефективності роботи породного комплексу шахти за рахунок обгрунтування раціональних параметрів і структури системи автоматичного управління бункерно-транспортним ланцюгом поверхні шахти.
Для досягнення поставленої мети необхідно вирішити такі задачi:
- Аналіз процесу транспортування гірської маси технологічного комплексу поверхні як об'єкта автоматизації.
- Критичний огляд існуючих технічних рішень.
- Розробка схемотехнічного рішення системи автоматичного управління бункерно-транспортним ланцюгом поверхні шахти.
3. Результати дослідження
3.1 Аналіз процесу транспортування гірської маси технологічного комплексу поверхні як об'єкта автоматизації
Відвали служать для складування породи. Комплекс механізмів і споруд, призначених для цієї мети, називаються відвальним або хвостовим господарством. Відвали розрізняють:
1. За способом компонування – висотні, утворені на рівній місцевості, що захаращує поверхню, знищуючи придатний для сільського господарства грунт; глибинні, що використовують яри, балки, долини, занедбані кар'єри та інші поглиблення.
2. По виду обладнання – конвеєрні; рейкові; з підвісними канатними дорогами; з автомобільним транспортом; з гідротранспортом.
3. За формою штабеля – плоскі; хребтові; конічні; коноідальние.
Вугілля видається на поверхню вугільним скіпом в приймальний бункер, розташований в надшахтній будівлі скіпового ствола. З бункера вугілля подається через розподільну лійку в дробильно-сортувальне відділення, звідки через класифікаційний вузол йде розподіл на вугілля і породу. У всіх вугільних басейнах країни порода складується переважно у відвали конічної форми, обладнані рейкової канатної відкаткою. Схема транспортування породи на відвал наведена на рисунку 3.1
Для конічних рейкових відвалів (рис. 3.1) використовують саморозвантажувальні вагонетки або скіпи. Залежно від продуктивності влаштовують одно та двоколійні рейкові шляхи. Для переміщення судин застосовують одно та двохбарабанні лебідки. У міру заповнення відвалу кінцева ферма пересувається вперед за допомогою домкрата або лебідки [1].
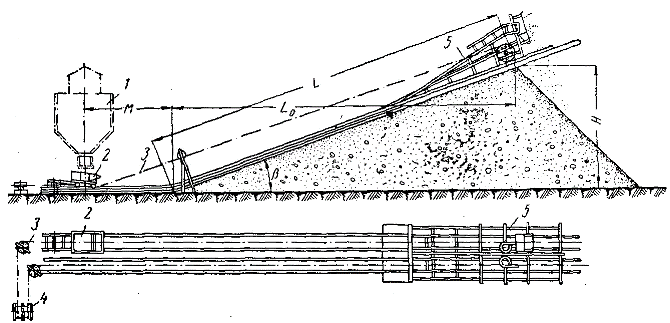
Рисунок 3.1 – Схема транспортування породи на відвал: 1 – бункер, 2 – скiп, 3 – канат, 4 – лебiдка, 5 – розвантажувальна ферма.
Технологічна схема доставки гірської маси на відвал наведена на рисунку 3.2.
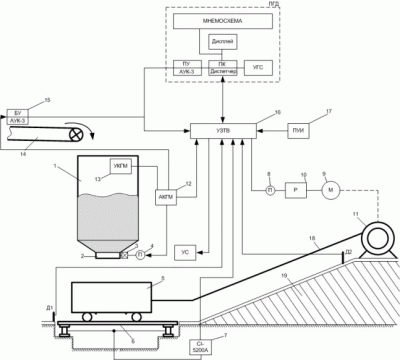
Рисунок 3.2 – Технологічна схема доставки гірської маси на відвал
(анімація: 8 кадрів, 7 циклів, 162 кілобайт)
Гірська маса в бункер 1 надходить з конвеєра 14, який обладнаний блоком управління 15 апаратури АУК-3. При досягненні верхнього рівня в бункері 1 порода надходить у вагонетку 5 через затвор 2, який обладнаний приводом 3 та пусковою апаратурою 4, і при досягненні встановленої максимальної маси, яка визначається ваговимірювальної платформою 6, вагонетка направляється на відвал 18 за рахунок лебідки 11, яка обладнана приводним електродвигуном 9, пусковою апаратурою 8 і регулятором швидкості 10. З тензодатчиків ваговимірювальної платформи [3] сигнали надходять на ваговий індикатор типу CI-5200A, де сигнали усереднюються, і далі надходять на пристрій автоматичного завантаження та транспортування вагонеток ПЗТВ 16. Контроль рівня гірської маси в бункері здійснюється апаратурою контролю гірської маси АКГМ з пристроєм контролю рівня гірської маси ПКГМ, яка встановлюється в спеціальний отвір на верхньому перекритті бункера. Також передбачені кінцеві датчики: датчик наявності вагонетки на завантажувальної майданчику Д1 і датчик положення вагонетки Д2, який призначений для уникнення перепідйому вагонетки. Інформація зі всіх датчиків поступає в пристрій ПЗТВ, який обробляє отриману інформація, виробляє керуючі сигнали, а також передає інформацію на ПГД.
Пульт гірничого диспетчера включає в себе мнемосхему, промисловий комп'ютер ПК, пульт управління апаратури АУК-3, пристрій оперативного зв'язку ПОЗ.
Процес транспортування породи може здійснюватися як автоматично з урахуванням всіх параметрів і формуванням команд автоматичного управління затвором бункера, роботи конвеєра і рухом вагонетки до місць завантаження і розвантаження, так і дистанційно оператором за допомогою пульта управління та індикації ПУИ 16, або з пульта гірничого диспетчера.
3.2 Критичний огляд існуючих технічних рішень
Проблема комплексної автоматизації робіт породного комплексу в цілому ще не вирішена, частково розроблені системи автоматизації та дистанційного керування окремими механізмами і вузлами породного комплексу.
Так, на деяких шахтах переведені на дистанційне автоматизоване управління лебідки породних відвалів.
На шахтних териконах зазвичай зайнято три і більше робітників у зміну.
Автоматизація управління лебідкою дозволяє скоротити обслуговуючий персонал до 1 людини в зміну. При цьому поліпшується робота установки і підвищується її продуктивність.
Тип лебідки БЛ-1200 з електродвигуном 75 кВт, 730 об / хв, 380 В. Електрична схема автоматизованого керування лебідкою показана на рисунку 3.3.
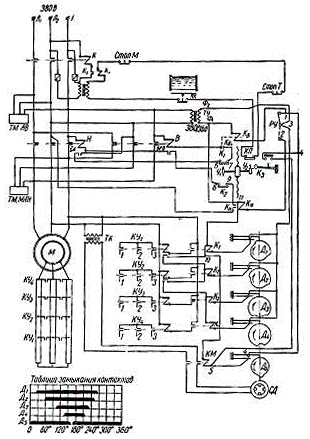
Рисунок 3.3 – Електрична схема автоматизованого управління одноконцевою лебідкою терикону
Пускач К встановлений на головному введенні і служить загальним пускачем установки. Пускач В служить для включення електродвигуна установки при підйомі вагонетки, а пускач Н – для включення електродвигуна установки при спуску вагонетки. Контакторна панель, що складається з чотирьох пускачів ПМВ-1365 (КУ1, КУ2, КУЗ, КУ4), застосовується для шунтування пускових опорів в ланцюзі ротора електродвигуна лебідки. Аварійний електромагніт ТМАВ утримує вантаж аварійного гальма, а електромагніт ТММАН – вантаж робочого гальма. Моторний комутатор виробляє послідовне включення і виключення пускачів контакторної панелі.
Кінцеві вимикачі К1, К2 і КЗ, встановлені на вказівнику глибини, мають свої контакти 6-7 в ланцюзі вмикання котушки пускача В; 8-9 – в ланцюзі вмикання котушки пускача Н; 4-5 – в ланцюзі пускача КМ і спрацьовують залежно від положення гайки вказівника глибини. Кнопка КП встановлена на індикаторі глибини і має свої контакти в ланцюзі загального пускача К. Триполюсний вимикач РУ служить для ручного пуску установки. Кнопки "Стоп", Т і М служать для аварійного гальмування установки при відмові засобів управління гальмівними пристроями. Контакторний пристрій предcтавляє собою металеву пластинку, розміщується під барабаном лебідки і зміцнюється на кронштейнах таким чином, що при сприйнятті навантаження від провисання каната пластинка опускається. При опусканні пластини розмикаються контакти ПК, які включені в ланцюг управління пускача К.
Пускач КМ, що служить для включення моторного комутатора, спрацьовує спочатку ходу вагонетки при замиканні рубильників РУ (положення I) і кінцевого вимикача К3 – наприкінці робочого ходу [2].
Вибухобезпечне реле з іскробезпечними ланцюгами керування типу ІКС-1 призначено для автоматичного контролю заповнення вугільних і породних бункерів. Це реле може застосовуватися також для автоматичного управління шахтними установками в якості колійного або кінцевого вимикача зі щітковими датчиками.
Реле типу ІКС-1 являє собою панель, на якій змонтовані наступні елементи
1. Поляризоване реле типу РП-5. Котушка реле має дві обмотки, з яких одна 4600 витків з омічним опором 700 Ом.
2. Виконавче реле типу РПТ-100М2 з котушкою на 36 В. Рухливі контакти виконавчого реле виконані у вигляді містків з сферичними контактами з срібла і мають миттєве перемикання. Нерухомі контакти являють собою латунні платівки з плоскими циліндричними контактами зі срібла.
3. Трансформатор живлення з первинною обмоткою на 127 В і двома вторинними обмотками.
4. Селеновий випрямляч зібраний з чотирьох стовпчиків типу АВС-7-4 з 18 шайбами діаметром 7 мм у кожному.
5. Селеновий шунтщо складається з двох плечей, з 4 шайбами діаметром 18 мм в кожному плечі.
6. Конденсатор металопаперові ємністю 2 мкФ 250 В.
7. Вимикач, що служить для перемикання котушок реле РП-7 при контролі великих чи малих опорів.
8. Перемикач напруги живлення іскробезпечного ланцюга.
9. Два запобіжника.
10. Пакетний вимикач.
Електрична схема реле ІКС-1 представлена на малюнку 3.4.
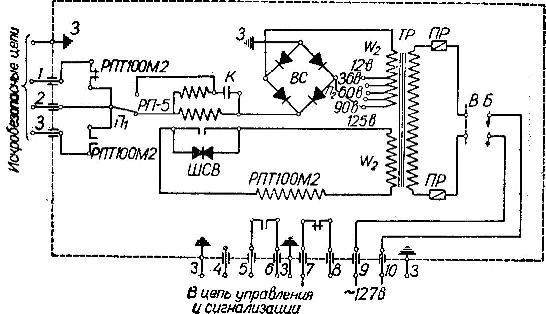
Рисунок 3.4 – Принципова схема реле типу ІКС-1
Через перемикач на високоомну обмотку трансформатора включені обмотки високочутливого поляризованого реле РП-5. Паралельно обмоткам реле РП-5 включений конденсатор К ємністю 2 мкФ, що виконує роль фільтра. За допомогою вимикача П1 можна включати в ланцюг управління одну обмотку реле РП-5 для контролю малих опорів або дві обмотки послідовно – для контролю великих опорів. Контакт реле РП-5 входить у ланцюг живлення виконавчого реле РПТ-100М2. Паралельно контактам реле РП-5 включений зустрічний селеновий шунт, що захищає контакти від надмірного електричного зносу.
Величина напруги, необхідна для контролю заданого опору, визначається з таблиці, укріпленої на верхній панелі апарату. Необхідну напругу встановлюється за допомогою перемикача П2.
До зажимів 1 і 2 іскробезпечної ланцюга контролю підводиться дріт від трубчастого датчика (рис. 3.5), встановленого безпосередньо в бункері. Електрод може бути розташований в 500-600 м від місця встановлення реле ІКС-1. До зажимів ланцюга управління і сигналізації реле можуть підключатися котушки пускових пристроїв конвеєрів або інших механізмів, що виробляють завантаження бункера, та сигнальні пристрої (сирени, лампи).
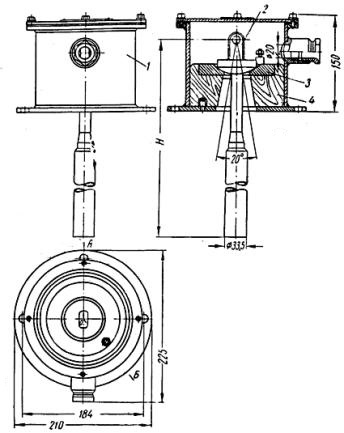
Рисунок 3.5 – Датчик трубчастий електродний: 1 – корпус; 2 – электрод; 3 – подпятник; 4 – ізолятор.
При використанні реле ІКС-1 для контролю рухомого складу застосовується щітковий датчик типу ДЩ-1, загальний вигляд якого показаний на рисунку 3.6 [3].
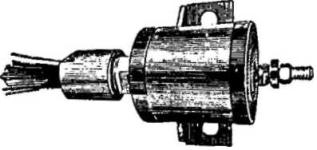
Рисунок 3.6 – Щітковий датчик типу ДЩ-1
До переваг можна віднести: дешевизну і простоту виконання.
До недоліків даного реле можна віднести: не високу надійність при контролі рухомого складу, тому що матеріал "щітки" має властивість стиратися і вигинатися, що може призвести до неточних показань; датчик трубчастий електродний під дією агресивного навколишнього середовища може деформуватися, виходячи з конструкції датчика при попаданні в корпус пилу або дрібних частинок породи може відбуватися залипання чутливого елемента, що може призвести до переповнення бункера і недостовірних показань датчика.
3.3 Розробка схемотехнічного рішення системи автоматичного управління бункерно-транспортним ланцюгом поверхні шахти
У відповідності з технологічною схемою транспортування гірської маси на відвал була складена структурна схема системи автоматичного управління бункерно-транспортним ланцюгом поверхні шахти, яка наведена на рисунку 3.7
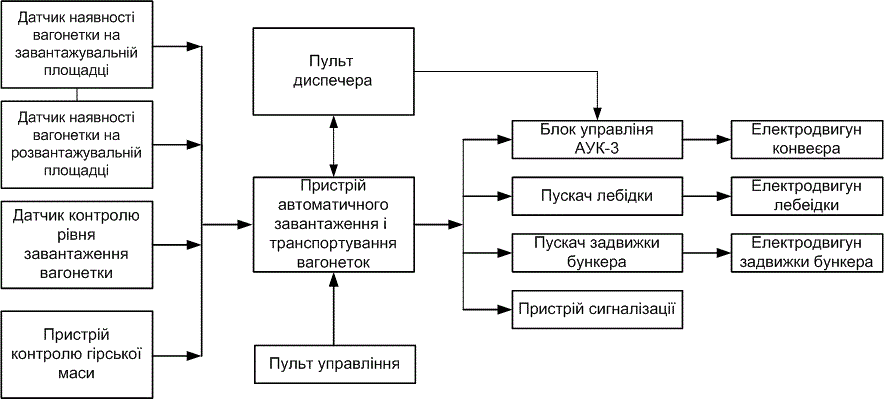
Рисунок 3.7 – Структурна схема системи автоматичного управління бункерно-транспортним ланцюгом поверхні шахти
Згідно структурній схемі системи автоматичного управління бункерно-транспортним ланцюгом поверхні шахти розроблено пристрій автоматичного завантаження та транспортування вагонеток, структурна схема якого наведена на рисунку 3.9
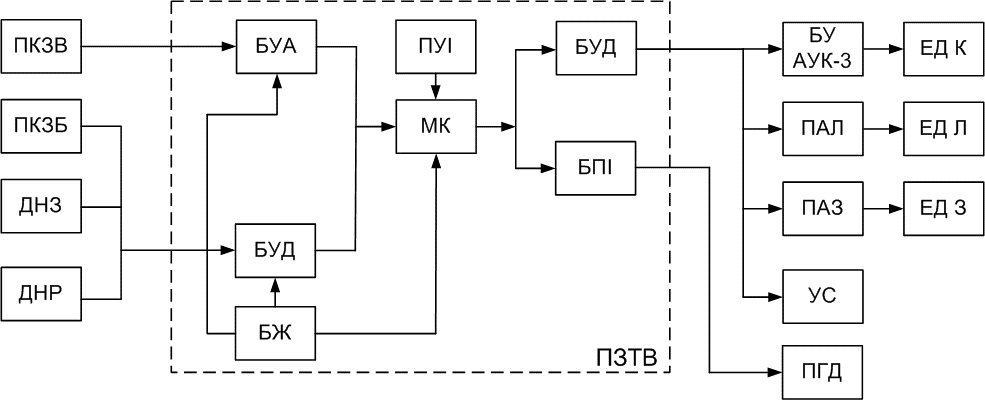
Рисунок 3.8 – Структурна схема пристрою автоматичного завантаження та транспортування вагонеток
Цей пристрій працює таким чином: інформація з апаратури контролю гірської маси (АКГМ), датчиків наявності вагонетки на завантажувальної (ДНЗ) і розвантажувальної (ДНР) площадках, через блок узгодження дискретних сигналів (БСД), а інформація з пристрою контролю завантаження вагонетки (УКЗВ) через блок узгодження аналогових сигналів (БСА) надходить на мікроконтролер (МК). У МК обробляється інформація, яка надійшла, і виробляється керуючий сигнал. Інформація про поточний стан процесів об'єкта передається через блок передачі інформації (БПІ) на пульт гірничого диспетчера (ПГД). У разі досягнення верхнього рівня в бункері відключається конвеєр, обладнаний блоком управління апаратури АУК-3 і опитується ДНЗ: якщо вагонетка відсутній на завантажувальної майданчику, тоді через пускову апаратуру приводу лебідки (ПАЛ) включається лебідка і доставляє вагонетку на завантажувальний майданчик, потім подається сигнал на пускову апаратуру приводу задвижки бункера (ПАЗ), задвижка відкривається і вагонетка наповнюється до тих пір, поки ПКЗВ не видасть сигнал про те, що досягнута уставка маси. Потім на ПАЗ подається сигнал на закриття бункеру. Включається лебідка і піднімає вагонетку на відвал. Для того, щоб вагонетка не проїхала місце розвантаження, в кінці підйому встановлюється ДНР, який при спрацьовуванні буде свідчити про прибуття вагонетки. Даним процесом можна керувати як безпосередньо з пульта управління (ПУІ), так і віддалено з пульта диспетчера (ПГД).
Висновки
Таким чином, запропонований пристрій дозволяє суттєво підвищити рівень автоматизації об'єктів, що беруть участь в процесі транспортування гірської маси на відвал, забезпечити контроль кількості гірської маси, що завантажується в вагонетку, що дозволяє стабілізувати зусилля на приводному двигуні і підйомному канаті. Це забезпечує зниження енерговитрат на транспортування, рівномірність розподілу гірничої маси на відвалі і зниження ймовірності аварійних ситуацій.
Новим у запропонованій системі є наявність автоматичного вимірювання маси породи у вагонетці при розвантаженні бункера. Вимірювання маси породи у вагонетках дозволить зменьшити динамічні навантаження на електродвигуни лебідки (так як при перевищенні норми завантаження вагонеток виникає підвищене навантаження на систему підйому, що призводить до перевитрати електроенергії, до зайвих економічних витрат у разі виходу з ладу елементів, що входять до складу лебідки).
Принцип роботи даної автоматизованої системи полягає в мінімізації людського фактору на вантажні і транспортні роботи, прискорити процес завантаження, збільшити точність показань ваги транспортованої гірської маси і здійснювати її підрахунок.
завершення: грудень 2013 року. Повний текст роботи та матеріали по темі можуть
бути отримані у автора або його керівника після вказаної дати.
Перелік посилань
- Кузнецов Б.А., Ренгевич А.А., Шорин В.Г. Транспорт на горных предприятиях. Изд. 2–е, перераб. и доп. М., «Недра», 1976. – 552 с.
- Авласенко Ю.Г., Ковалевский М.М. Автоматизация шахтных установок. Государственное издательство технической литературы УССР, Киев 1958. – 296 с.
- Вагонные весы [Электронный ресурс] – Режим доступа: http:www.etalon–ves.ru
- Евстифеев А.В. Микроконтроллеры AVR семейств Tiny и Mega фирмы ATMEL, 5–е изд., стер. – М.: Издательский дом «Додэка–XXI», 2008. – 560 с.
- Автоматизація технологічних об’єктів та процесів. Пошук молодих. Збірник наукових праць ХІІ науково–технічної конференції аспірантів та студентів в м. Донецьку 17–20 травня 2012 р. – Донецьк, ДонНТУ, 2012. – 300 с. Статья Ананичев В.В., студент; Жовтобрух С.А. Автоматизация процесса транспортирования породы на отвал.
- Горлова А.А. Исследование динамических процессов пуска электропривода одноконцевой откатки и разработка устройства автоматического управления его разгоном. Автореф. магистерской работы. [Электронный ресурс] – Режим доступа: Портал магистров ДонНТУ, Факультет КИТА, 2011 г.
- Коваленко Е.А. Разработка автоматизированной системы управления углепогрузочным комплексом поверхности шахты. Автореф. магистерской работы. [Электронный ресурс] – Режим доступа: Портал магистров ДонНТУ, Факультет ЭМА, 2004 г.
- Основные характеристики весового терминала с функцией дозирования CAS CI–5200A. [Электронный ресурс] – Режим доступа: СI–5200A
- Научно–технический центр проблем энергосбережения. [Электронный ресурс] – Режим доступа: АКГМ
- Техническая характеристика лебедки БЛ–1200. [Электронный ресурс] – Режим доступа: БЛ–1200