Abstract
content
- 1. Relevance of the theme of master's work
- 2. The goals and objectives of the study
- 3. justification of the control method
- 4. Functional development schemes
- 5. modeling the dynamics of self-propelled guns
- 6. findings
- References
1. Relevance of the theme of master's work
In recent years, Ukraine has seen the development of steel mini-mills, which are implemented energy-saving steel production technology and products. Energy saving in the steel industry is to combine the processes of continuous continuous casting and rolling from molten metal to the final rolled. The faster the metal comes from the liquid state to the final rolling, the better economic performance of energy-intensive metal production. In modern technologies of production of copper tubes used horizontal continuous casting units that meet the requirements of mini-mills, as it is convenient to place in existing shops, there is no need to increase the height of the building, or to form a deep well.
Analysis of the existing method of G. Bessemer [1-2-3] cast metal sheet rolls crystallizer has disadvantages. If the lower edge of the liquid metal bath of the metal reaches the minimum distance between the surfaces of the rolls, then the center of the band is formed due to segregation of impurities ousting two fronts crystallization going to meet each other. In this case, closed material flow can not display non-metallic inclusions to the top of the metal bath and due to its shrinkage occurs friability and porosity in the center of the sheet. Consequently, the casting process should be carried out so that the two crystallization front welded together in the field, located above the specified minimum distance between the rollers. However, the continuous casting of thin sheet metal due to its small thickness goes unstable, since the volume of the metal pool is not large, and the cooled water is required to dissipate heat temperature is unstable.
Thus, for stabilization of the casting process, solution to the problem of segregation zone to remove the middle portion of the sheet metal along its entire length, and to improve the structure of the metal and seals in the master's work will be developed ACS process of casting rolls-crystallizing on the Information parameter characterizing the position of the solidification front in the rolls, as well as stabilization of the heat flux on the mold.
2. The goals and objectives of the study
Purpose - to improve the quality of the metal seal its structure by stabilizing the position of the solidification front of the metal in rolls, molds, and heat flux on the mold. To achieve this goal it is necessary to solve the following problem.
1. To provide an overview of the technological scheme casting rolls, crystallizing in a twin roll caster production of rolled products.
2. Analyze the process of casting rolls-crystallizing as an object of management in terms of basic information variables.
3. Justify the selected control method and to develop a functional block diagram of ACS.
4. The synthesis of ACS. Check the operation of the system by means of mathematical modeling. To analyze the dynamics of self-propelled guns.
5. Estimate the expected cost-effectiveness of the introduction of self-propelled guns.
3. justification control method
The reaction force on the rolls of the ingot-molds Fnp is an information parameter corresponding to the position of the solidification front of the metal relative to the rolls - the molds((Fig1)).
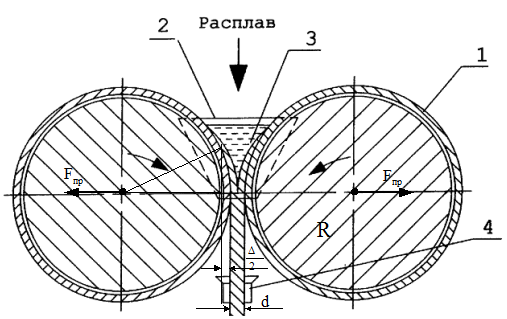
Figure1 - Mimic diagram of the casting process in windrows crystallizers
The purpose of the process control automation systems in the casting rolls crystallizers - maintaining a predetermined level, the reaction force applied to the rolls perpendicular to the plane formed by the ingot to be:
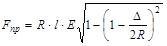
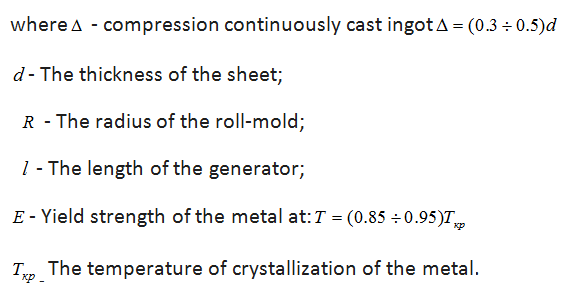
Consider for example the system specific implementation. Rolls-up molds = 800mm and the radius R = 400mm rotating at a
speed of 50 rev / min greater than the required casting technology [3]. At the ends of the rolls,
molds are electromagnetic devices forming the lateral edge of the metal and preventing its drain. In the roll area in which the seed is poured metal.
Strain gauges mounted on the axis of the roll-mold fix a reaction force applied perpendicular to the plane formed by the sheet metal thickness d=5mm
For a given metal swaging crystallized Δ = 2 ìì and its yield strength
at the process temperature
design force is:

The speed of rotation of the rolls, molds must be reduced as long as said force does not reach the calculated value. The process of casting - rolling proceeds at a rate corresponding to the target reaction force ingot (rolling force) to the rolls. Power for the process of casting - rolling reaction force during rolling forces crystallizers Fnp = 905 kH matches P = Fnp . Vë = 905 . 103 . 0,3 = 272 êÂê
4.Functional development schemes
Functional scheme of automation control system continuous casting process in a twin roll caster is shown in Fig.
The system works as follows. Please manually set the speed of rotation of the rolls, molds calculated technologist, and as the formation of solidified metal ingot fix results of measuring the strength of the reaction to the rolls of the ingot-molds. Until the current value is less than a predetermined reaction force calculation, the rotational speed of the rolls is reduced proportional to the difference between the current mismatch error reaction force on the rolls of the ingot and calculated rolling force. Upon reaching the rolling force to the calculated (equal to zero mismatch error) the magnitude of the speed of rotation of the rolls is regulated accordingly the current strength of rolling.
When the feedback signal increases in strength rolling speed of the rolls, molds is also increased proportional to the sum of the estimated rolling force and the current mismatch error by the reaction force of the rolls of the ingot. This variable speed roll-mold requires a control system with variable structure control, allowing inputs to agree on the circuits of the reference and feedback. This speed roll-molds corresponding to the current reaction force and the rolling ingot characterizing the performance of the casting process Vnp a master control system for control of electric pump, which provides for a given level of heat flow of chilled water to the mold:
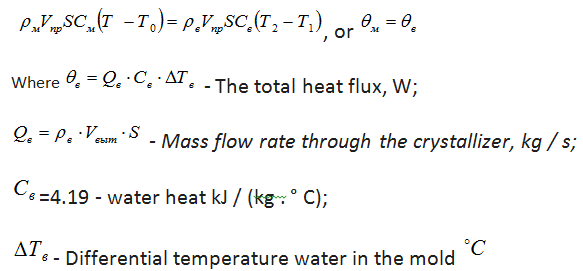
That is, heat flow, to give the metal is equal to the heat flow, pick up the water. Chilled water is not stable, so if the temperature at the inlet of the mold downstream water T1 increases, the heat flow of cooling water decreases, as evidenced by the feedback controller of the heat flow will be faster and the pump to pump water from the pool (Fig2).
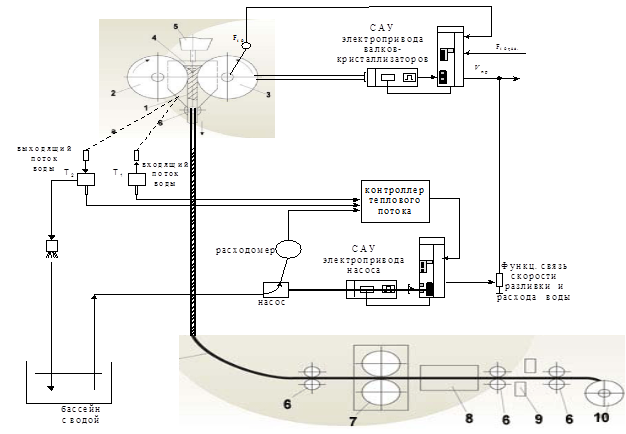
Figure2 - Functional diagram of CAY continuous casting process in the production of ALP crystallizing rolls rolled sheets
5. modeling the dynamics of self-propelled guns
Thus, a block diagram of a stabilization reaction force on the rolls, metal molds must have two control loops. Outer loop - Power Controller rolling. Internal - Speed Controller metal casting. CAY modeling scheme is shown in (Fig3).
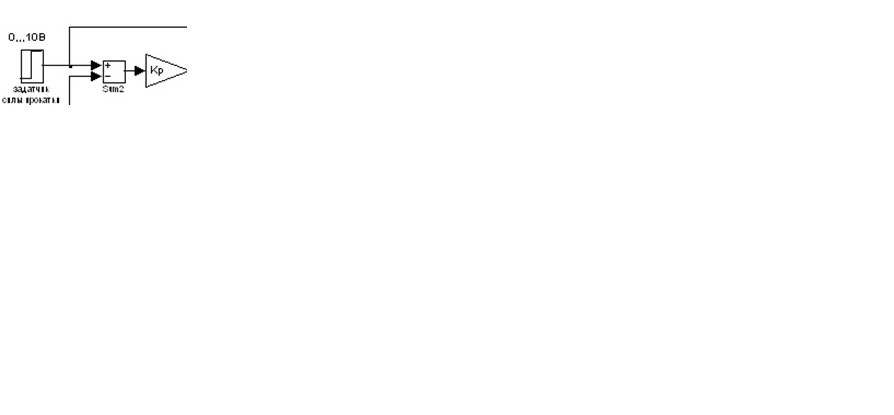
Figure 3- Schematic model of the stabilization force on the reaction of the metal rolls-molds
To ensure the stability of the casting process, the speed of casting billet rolling should be adjusted so as to reduce the reaction force when the rolls, metal molds, the setpoint speed is also decreased. To this end, adjustable mismatch error by rolling force is added to the minus sign to the set point signal strength rolling. Transient response of the system shown in (Fig4 and 5).
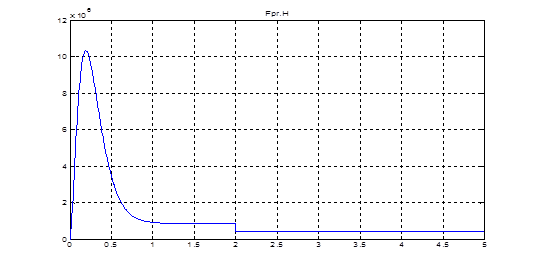
Figure4-step response of the reaction force on the metal rollers, molds
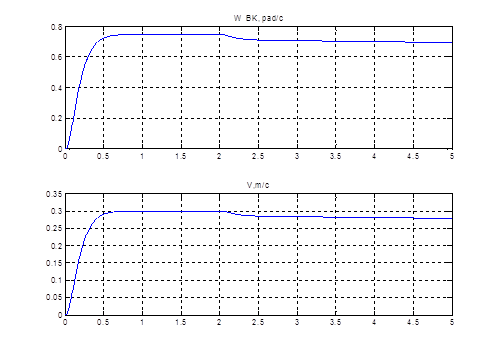
Figure5-step response of the speed of rotation of the rolls, molds and casting speed by reducing the rolling force
Analyzing the transient response (Fig.) it can be concluded efficiency stabilization system reaction force on the rolls, the metal molds. Speed-molding preform rolling varies according to the variation of the solidification front, depending on the heat transfer conditions in the mold.
The speed of rotation of the rolls, molds to meet the current strength of the reaction of the ingot to the rolls and characterizing the performance of the casting process Vë a master control system for control of electric pump, which provides for a given level of heat flow chilled water roller-crystallizers:
That is, heat flow, to give the metal is equal to the heat flow, pick up the water. Chilled water is not stable, however, if the temperature of the incoming water flow increases, the heat flow is reduced and the cooling water pump will be correspondingly faster pumping water from the pool. In view of the foregoing, in the thermal stabilization of the setpoint flow should be proportional to the casting speed VëAnd a feedback signal proportional to the water flow
The analysis of the dynamics of the stabilization system of the heat flow, as well as the entire SAU will be presented in a subsequent publication.
6. findings
- Analysis of the existing technological schemes of casting by H. Bessemer showed that in the center of the band at the minimum distance between the roll-casting molds segregation is formed, resulting in looseness and porosity of the metal in the center of the sheet. Therefore, the casting process should be carried out so that the two crystallization front welded in an area that is above the minimum distance between the rollers-casting molds. This maintenance process can be achieved by stabilizing the reaction force of the metal on the rolls, molds, corresponding to the above the solidification front, as well as stabilization of the heat flux on the rolls-mold.
- Synthesized and studied ACS stabilize the reaction force of the metal on the rolls, molds. The system is built on the principle of subordinate regulation. Outer loop - Power Controller rolling corrects the setpoint for the speed of rotation of the rolls, molds, and casting speed, respectively.
- The analysis of the simulation results confirmed the efficiency of the system. Speed-molding preform rolling varies according to the variation of the solidification front, depending on the heat transfer conditions in the mold.
- Study the dynamics of the entire casting process automation system - rolling rolls-crystallizing with the stabilization system of the heat flow will be given in subsequent developments.
This master's work is not completed yet. Final completion: December 2013. The full text of the work and materials on the topic can be obtained from the author or his head after this date.
References
- Brovman M., V. Poluhin, Nikolaev Opportunities roll casting and rolling units to create a mini-mills / "National Metallurgy», ¹ October 2010. - P.26 - 28.
- Casting and Rolling Complex: http://specural.com.
- Nikolaev, Victor A. Investigation of direct strand reduction rolling steel strip to identify effective technological and design data / Dissertation for the degree of Ph.D., WAC: 05.16.05 Occupation: Metal Forming.
- Denisenko VV Computer control of the process, experiment equipment. -M.: Hotline - Telecom 2009. - 608 p., Ill.
- Olsson, G., D. Piani Digital automation and control systems. - St. Petersburg.: Nevsky dialect, 2001. 557 p.: Ill.
- Information technology. A set of standards and guidelines for automated systems. - Moscow: Publishing Standards, 1991. - 36.
- GOST 19.005-85. Schemes of algorithms and programs. Terms of execution. - Moscow: Publishing Standards, 1985 - 18. - UDC 65.011.66:002:006.354. Group T58.
- Glinka GM Designing control systems and automatic control of metallurgical processes / ed. Glinkova GM -M.: 1986. - 452 p.