Abstract
Content
- Introduction
- 1. Relevance of the theme
- 2. Object description
- 3. Goals and objectives of the master's work
- 4. Overview of methods and algorithms for modeling
- 5. Review of applications
- 6. The mathematical formulation of the problem
- Conclusion
- References
Introduction
Transmission companies is a company whose main activity is the main gas transportation and, sometimes, related petroleum products. Nowadays gas as an energy source is used almost universally in all plants and factories. Each of us used to seeing a beautiful blue light in his kitchen. Therefore, it is difficult to overestimate the importance of the transport enterprises. At first glance it may seem that there is nothing complicated about their activities are not self-gas flows through the pipes. However, this is not the case. Pipes with a diameter of 1.4 m to 75 atm. operating pressure in the pipe, complicated equipment for distribution and compression of gas. And all this complex can not just stop for a minute.
Many objects gas companies are the country's transportation system, a particular region of the city. And this whole system must somehow upravlyat.Dlya control transmission system are control towers and related automated systems with a hierarchical structure. The basis of such systems is the principle of unity and consistency of mathematical, information and logistics information system at all levels of management.
1.Relevance of the topic
Most pressing problems dispatching service gas transportation company objectives are to ensure the safe operation of process control and improvement of gas transmission. To address these challenges are developed and implemented supervisory control and automation systems, including remote control system. However, when using the "traditional" remote control system and supervisory control task situation analysis and decision-making person-to-controller solves. With the need to make responsible decisions within a limited period of time (especially in the localization of accidents) and on the basis of multi-criteria analysis of the data load on the controller increases significantly. The task of decision-making is complicated by the need to analyze the complex process of object structures, for example, loop piping system jumpers and a variety of gas streams.
Analysis of a number of accidents in the gas industry has shown that one of the causes of accidents are mistakes dispatching personnel, failure to control or making wrong decisions. Besides constantly increasing requirements for quality of performance of the operators and managers of their functions in a man-machine control system [3]
Based on the above, a special role automation of decision-making in the management of gas pipelines and other distributed objects. Necessary to provide assistance to the controller in the analysis of current operating mode of the object, to automate the identification of emergency situations and issue recommendations to the dispatcher of their localization and elimination while preserving performance transmission system or other processing facility as a whole, which can be done with the help of decision support systems (DSS). The problem is solved by the primary DSS automatic processing of data received from the remote control system and other systems of calculation and simulation modes of operation of the facility, and the use of expert system components in the form of rules describing the possible situations in the system with the relevant recommendations of the dispatcher.
2. Object Description
The object description, the process of transporting gas through hydraulic structures (technology). Most common method of delivery of gas to customers is to transport the pipes.
Gas transmission system (GTS) is a simplified representation of the linear part of the (pipeline) and gas compressor stations (pumps). By means of the linear part of the gas pipelines and gas pipelines outlets, as well as some other technological objects. Gas compressor station (GCS), called for simplicity pumps are extremely complex technological objects. The most common technological objects of the linear part of the gas transportation system include: Valve Platform (CP), the gas distribution stations (GDS), cathodic protection station (RMS) (Figure 1). KP serve to redistribute the gas flow between the gas pipelines, locating certain sections of gas pipelines in case of emergencies or repair work, etc. RMS installed to protect gas pipes from corrosion. At GDS produced gas preparation for the end user: reduction and adjustment of pressure odorization and others [7]
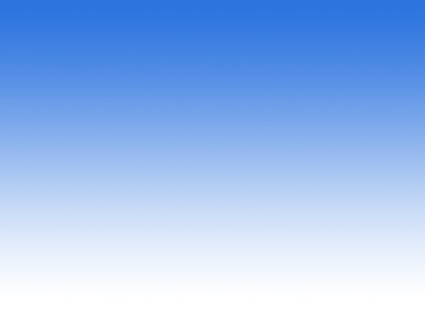
Figure 1 — Simplified representation of the transmission system
(Animation: 9 frames, 7 cycles of repetition, 41.5 kilobytes)
One of the main tasks of the development of management systems in the gas industry is the creation and development of an automated system of dispatching upravleniya.To have to control the gas transmission system are control towers and related automated systems with a hierarchical structure: the central control station gas transportation company (CDP GTP)—Dispatch center LPU—DP remote compressor station (if any) DP—compressor plant.
Below is an example snippet of TCU.
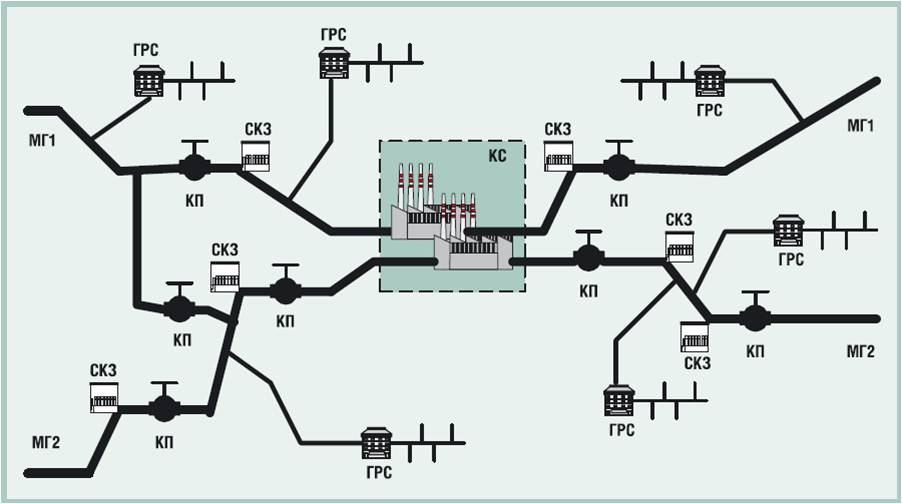
Figure 2 — Fragment transmission system
MG1, MG2-gas pipelines;
GDS-distribution stations;
KP-site crane;
RMS station cathodic protection;
COP-compressor station.
before putting gas pipes must be prepared. The fact that, together with natural gas from the well out the various impurities, which may damage equipment. Gas purified from them several times directly on exit from the hole in the separator surface, and then another for transportation and compression stations. The gas is dried, cooled by refrigeration, or by throttling (pressure decrease in conduit constriction).
Currently, in terms of the effectiveness of the maximum diameter of the pipeline is 1420 mm. The world's largest is the Russian gas transport system with a length of gas pipelines in its territory 161.7 kilometers. Length of Ukrainian gas pipelines with gas laterals, 5094, 408 km. [5]
3. Goals and objectives of the master's work
The aim is to increase the efficiency of process control gas trunkline through the development of methods and models to support decision-making dispatcher.
To address this goal the following objectives:
- analysis methods and models of gas transport management system with specific process
- research component models transmission system and parametric description of their relationship
- development process-oriented approach to the representation of the formalized process of gas transport
- development of discrete-continuous control models the gas transmission system in the form of hybrid automata
- check the adequacy of the model and the determination of its effective parameters
- Development of recommendations for gas transportation enterprises on the basis of experimental data
4. Overview of methods and algorithms for modeling
Process simulation allows you to: pinpoint elements of the process that need to be improved, to quantify the dependence of the accuracy of the processing technology factors, to predict the effect of the implementation of various measures to improve the technology, develop a mathematical framework for the development of automated control systems.
The process of building models can be represented as follows:
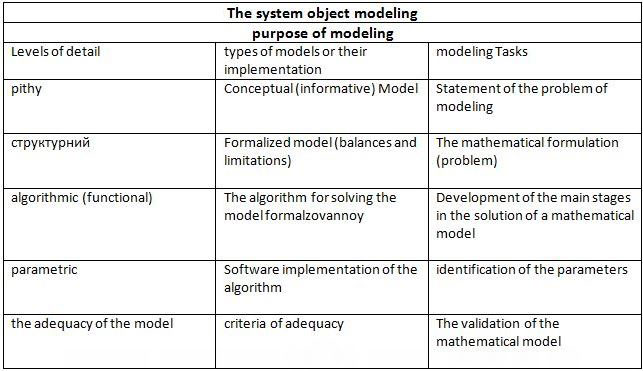
Figure 3 — The process of model building
At the first stage of the model stand out features that characterize the system and system-forming elements and the relations in which these features are implemented. This allows you to define the object of study as a system. On the second - defines the purpose of modeling the system. In the third stage, at every level of detail developed mathematical models and facilitators for communication between urovnyami.Na first level study the system of interest (object model) and describe its content. This description is called a conceptual (content) model, which is a verbal description of the mathematical formulation of the problem. Then formulate a conceptual model, which are developing the model structure. This structural or topological pattern forming layer, on which the model can be written as balance relations and constraints. Next on the algorithmic level are developing algorithms for solving mathematical model. Software implementation of which corresponds to the next level of detail - parametric, which defines the parameters of the model. And then on the final level of review the adequacy of the model object being modeled. [8]
For the simulation of manufacturing processes can be applied such methods [3,7]:
- analytical (mathematical) and numerical simulation
- Simulation Physical modeling
- natural modeling.
- analytical and numerical modeling techniques
These methods allow you to get some of the characteristics of the system as a function of the parameters of its operation. Thus, the model is a system of equations which is obtained in solving the parameters necessary for calculating the output of the system. But often, because of the complexity of most real systems, their complete mathematical description (model) either does not exist or has not yet developed analytical methods for solving a mathematical model. Second, the derivation of formulas, which are based on the analytical methods adopted certain assumptions that do not always correspond to the real system.
An example is a linear programming formulation of the problem for which a given system of equations: one target (minimum or maximum), and a number of limitations. A special case of linear programming - network problem. Another example of data modeling techniques - non-linear programming. It is used when the relationship between the variables can not be expressed lineyno.K this group of methods also include the finite difference method, finite element method, iterative methods, direct numerical simulation (one of the methods for the numerical simulation of liquid or gas).
Advantages of the method: does not cost much to carry, wide range of application, ease some of the methods and the availability of solutions without the use of computers [9].
The disadvantages of methods: It is often difficult to build a model adequately takes into account all the factors [9].
- Simulation modeling techniques (statistical)
The essence of the simulation (MI) is to simulate the functioning of the system in time, subject to the same proportions as the duration of the operations in the original. In this simulated elementary phenomena that make up the process, saved their logical structure, the sequence of the flow of time. As a result of them to get estimates of the output characteristics of the system that are necessary to solve the problems of the analysis, management and design.
There are various methods of MI, for example, based networks using graphs and finite automata.
Advantages of the method: a wide range of tasks, can solve the problems of any complexity, you can spend an unlimited amount of experimentation with different parameters [9].
Disadvantages of the method: the complexity of the description of all the conditions and requirements of computing power [9].
Physical modeling -
This experimental simulation based on the physical similarity in the size of the reduced model.
Advantages of the method: the area of application not found in other methods [9].
Disadvantages of the method: the method can give reliable results only if the physical similarity model [9].
- natural modeling
Assigns to the real object of his material or layout to experiment at the test object, which at specially selected experimental conditions provides a model of itself.
Advantages of the method: the ability to test the model in the real world [9].
Disadvantages of the method: the high cost of building models [9].
5.Review of applications
The following programs are used for modeling, analysis and management of CTA:
- SPS program to support decision-making dispatcher (includes different software products) The main functions: monitoring the composition and properties, the simulation of thermal conditions, the calculation of capacity pipeline system.
- PSIPrognosis-prograSynerGEE-calculations and optimize operation of pipeline simulation setey.Fizicheskoe
- SynerGEE-calculations and optimize operation of pipeline networks.
- Galiom-Integrity Management (RBI, RCM).
- Uptime-integrity management of pipelines.
- Scada-system (Supervisory Control And Data Acquisition-Supervisory Control And Data Acquisition). This industrial control systems, designed primarily to gather information about the object, its display and archiving.
- complex programs "ARM Manager." The automated workplace (AWP) Manager (operator) is used for operational monitoring of one or more parts of the process automation object, as well as to manage the limited part of the equipment.
- complex programs "Regime Manager magazine." The complex collection, displaying the data in a convenient form, and mezhduurovnevomu exchange of information.
The main disadvantages of the programs: the complexity of the implementation and operation are not always explained the results are not always taken into account specification of the Ukrainian GTS.
6.The mathematical formulation of the problem
During normal operation of the GTS problem of minimizing energy consumption for transportation in compliance with the plan of gas supply, and in emergency mode solves the problem of minimizing losses [2].
Power required to pump gas through a given pipe with a given mean pressure proportional to the flow of gas in a cube (L3).
Thus we can write that the energy consumption for pumping the gas is equal to:
proportionality factor characteristic for the given conditions (resistance line, the properties of gas pressure)
period T
L-gas flow
The amount of gas to be pumped in time T is:
For gas losses:
where ξ—coefficient of resistance tubes, u—average over the section of the gas velocity, ρ—gas constant.
Conclusion
Performing calculations and simulation modes of gas transportation networks is relevant and not completely solved problem, because on the one hand modeling is important for improving the efficiency of gas transmission networks, but on the other hand there are a large number of modeling techniques and they are not perfect and have flaws. During the work the basic methods of simulation of manufacturing processes and formulation of the problem is made, which will subsequently produce a working model of the transport of gas.
In writing this essay master's work is not yet complete. Final completion: winter in 2013-2014. Full text of the work and materials on the topic can be obtained from the author or his manager after that date.
Source List
- Abuzova FF, Aliev RA, Novoselov VF and other equipment and the technology of transport and storage of oil and gas. -M.: Nedra, 1992. - 320.
- Aliev RA, VD Belousov, Nemudrov AG and other pipeline transportation of oil and gas. - Moscow: Nedra, 1988
- Block modeling and prediction modes of operation of gas networks (http://www.atgs.ru)
- Novitsky KA The task flow management in the transport system: Mon. Scientific. tr. MADI. Rotaprint MADI - Moscow, 2009
- official website PJSC "Ukrtransgas» (Ukrtransgas)
- Sardanashvili SA Computational methods and algorithms (pipelines), M. 2005
- article "Decision on the organization and data on the linear part of the gas pipeline» (www.cta.ru/cms/f/342654.pdf)
- article "Types of mathematical models. The hierarchical structure of flexible models of chemical-technological system. »(article "Methods for modeling of industrial processes» (www.tehnomag.ru/doc/203858 . html)