Abstract
Contents
Introduction
The paper presents results of the studies steel 22K after electro-slag remelting (ESR) under different fluxes. Steel 22K (Table 1) is widely used in power engineering in particular as material for manufacturing elements of the boiler. On this basis, the metal have the following requirements: high mechanical properties - strength, ductility, toughness, hardness, the stability of the structure and mechanical properties under high loads and high temperatures for a long time, high resistance aggressive environments.
Chemical composition of steel, %mass. | |||||||
C | Si | Mn | Ni | S | P | Cr | Cu |
0,19 | 0,17-0,4 | 0,7-1,0 | äî 0,3 | äî 0,035 | äî 0,04 | äî 0,3 | äî 0,3 |
The initial steel grade 22K for consumable electrodes obtained in the conditions of electric steelmaking plant of JSC "Energomashspetsstal" (Kramatorsk, Ukraine) by melting the carbon semi-product in an electric arc furnace (EAF), followed by treatment of the metal in the ladle furnace (LF), and cell-type vacuum degasser. Melted steel poured into molds weighing 3.6 tons. The ingot was forged by the press 31.5 mn in the blank electrode ESR, the surface of which was further processed on machine tools (Figure 1). Of the metal bars are made of the same seed for the ESR and selected metal for comparative studies.
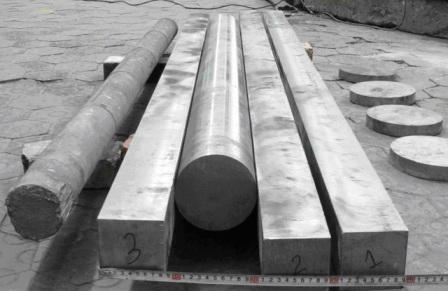
ESR obtained electrode was carried out in the research laboratory of special electrometallurgy department "Electrometallurgy", Donetsk National Technical University on industrial furnace ESR U-578 (Fig. 2). This single-position multi-purpose furnace designed for the smelting of solid and hollow ingots with diameter up to 700 mm and weight up to 700 kg. The furnace is working on a single-phase circuit and is powered by a low voltage transformer AC power frequency (50 Hz) brand ÒØÏ 10/1 (A 662M) output 724 kW.
A distinctive feature of furnace is that it's converted into a chamber furnace type. This makes it possible to create space in the melting furnace controlled atmosphere (Ar, N2, O2) and conduct electroslag remelting of various metals and alloys, including highly reactive under normal and excess (up to + 3·104 - 5·104 Ïà) pressures and in a vacuum under the industry standard and special fluxes, the so-called "active" calcium-containing (system ÑaF2-Ca).
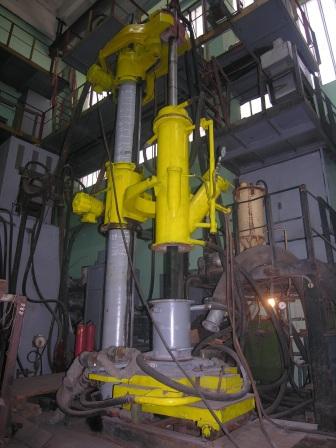
Consumable electrodes remelted in a stationary mold is 200 mm in diameter. Remelting was carried out at industrial fluxes AÍÔ-1Ï (melting ¹ 3), AÍÔ-6 (melting ¹ 1, 2) and under flux CaF2+Ca (melting ¹ 4). Flux is melted directly in the mold, using technology "solid" start. Data parameters of remelting are given in Table 3.
Flux | CaF2 | Al2O3 | CaO | SiO | Ca |
ÀÍÔ-1Ï | ~95 | -- | 5 | <1 | -- |
ÀÍÔ-6 | base | 23-31 | <8 | <2,5 | -- |
Experimental (calcium-containing) | 96,5 | -- | -- | -- | 3,5 |
Number of melting | Electrode: the side of the square (ø - diameter) / length in mm | Flux | Atmosphere | The height of the ingot, mm |
1 (À1Ø) |
ø90/1794 | ÀÍÔ-6 | Air | 373 |
2 (À2Ø) |
84,5/2108 | ÀÍÔ-6 | Air | 371 |
3 (À3Ø) |
84,5/2105 | ÀÍÔ-1Ï | Air | 370 |
4 (À4Ø) |
84,5/2104 | CaF2+Ca | Argon | 365 |
Electric melting regimes maintained at U = 40-45 V, I = 3,5-5,0 kA providing good quality surface formation of cast ingots (Fig. 3).
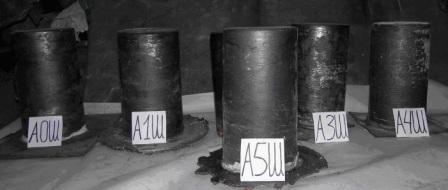
The resulting ingots were forge at press 31.5 mn to 100 mm diameter rods and together with the comparison rod of the 22K steel transferred to the heat treatment.The results of metallographic analysis showed that the ESR ingots metal, a decrease in defects liquation character and it has a more dense chemically homogeneous structure. Found that when remelting under "active" calcium-containing flux system CaF2 + Ca observed good refining of sulfur, phosphorus, oxygen, nitrogen and non-metallic inclusions (Table 4).
¹ melting - thin section | The number of inclusions in the square 100mm2 | The content of inclusions in volume percent |
1 - 1 | 674 | 0,01626 |
1 - 2 | 471 | 0,00729 |
2 - 1 | 623 | 0,02536 |
2 - 2 | 348 | 0,01164 |
3 - 1 | 775 | 0,02124 |
3 - 2 | 681 | 0,02496 |
4 - 1 | 312 | 0,01173 |
4 - 2 | 406 | 0,00625 |
22Ê ¹1 | 688 | 0,01531 |
22Ê ¹2 | 1022 | 0,03175 |
Mechanical properties were determined on samples of blanks that have passed the finish heat treatment hardening and tempering. Tests samples were cut longitudinally and transversely to the axis of the articles. Except room temperature mechanical tests were carried out at a temperature of +350 ° C. As compared with the starting material, ingots ChESR have highest isotropic of mechanical properties.
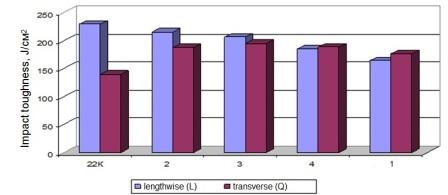
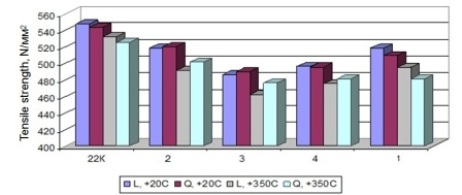
Conclusions.
1. It is shown that the ESR is an effective process for simultaneously refining of metal and production of structurally and chemically homogeneous ingots from steel 22K.
2. Comparative analysis showed that the most effective of the tested fluxes in ESR process of steel 22K (ÀÍÔ-1Ï, ÀÍÔ-6 è CaF2+Ca ) is the flux of the system CaF2+Ca, when remelting under which there is the best metal refining from sulfur-, phosphorus, oxygen, nitrogen and the smallest contents (index 2.5 times lower compared with the parent metal) and smallest sizes of nonmetallic inclusions.