Abstract
Contents
- Introduction
- 1. Relevance of the topic
- 2. The purpose and objectives of the study
- 3. The practical part
- Conclusion
- Source List
Introduction
Iron and its alloys are the basis of modern technology and equipment. Back in the mid 70s of last century, Academician Boris Patoncalled the twentieth century "iron" does not agree with him is impossible. In a series of structural metals iron is in the first place and do not give upit for a long time, despite the fact that the non-ferrous metals, polymers and ceramic materials are being increasingly used. Iron andalloys comprise more than 90% of the metals used in modern industry.
A number of new and effective ways to improve the quality of steel directly from metallurgical processes. In Paton. Patondeveloped and passed a long period of testing technology melting of various wastes related to specific types of electric metallurgy, in particular to the electroslagremelting. Its distinguishing oslbennostyu is used as the feed material waste in a non-compact form. Waste can be used withoutpreparatory operations ochistki.Elektroshlakovy remelting chip allows return of its own production for the manufacture of ingots, which significantlyincreases the utilization of metal without reducing the quality, reliability and performance of hardware.Electroslag remelting (ESR) is a secondary process of refining metals. It is used for further purification afterprimary impurities removal operations and refining. The starting material is usually applied a continuous consumable electrodePrimary metal which may be cast, or produced by pressure treatment consisting of scrap.In 1971-72. at the same institute batch process was developed electroslag casting, wherein a water-cooled mold with no consumableselectrodes melted slag mixture components. In the mold slag is poured through a portion of the steel melting unit. When pouring the electrodes pick up.After pouring the lead electroslag heating, ensuring the maintenance of a liquid metal mirror, while the bottom-drenched metal solidifies. The next portionpoured become mixed with the remainder of the first batch of molten steel. These cycles are repeated to fill the entire mold.
Electroslag permanent mold casting is a form ESHL. Technology electro chill casting produces castings for mechanical properties are not inferior to hire and himichemkogo without changing the composition.This two-step process: first, in electroslag crucible furnace receive electroslag liquid metal, and then pour it into a mold together with the slag used in smelting.
1. Relevance of the topic
The most important area of improvement and development of the domestic foundry in market conditions is the maximum reductioncosts of producing castings in providing the specified quality. Long-term forecasts of the cost of metal is continuously growing.In this regard, there is a problem facing enterprises make full use of any waste. Most of this waste is shaving.Transition metal shavings from 25-50% in the manufacture of parts of the workpiece. Remelting chips in a market economy and competition allowswith efficient technology to save a considerable amount of expensive primary charge materials. Metallurgists developed the processes Redsmelt,Hismelt, Primus, etc. Most of these processes involve a long series of practical preparation of the waste for processing: drying of raw materials, briquetting,heating and removing impurities prior to recovery of the solid phase, the melting and refining, which greatly increases the price of the metal.Electro-technology, is characterized by high efficiency and a wide range of technical capabilities. It provides high qualitymetal produced in processing of metal (mostly metal shavings), as well as electro-technology allows to achievereduce costs at all stages of processing metals and the exclusion of certain stages.
2. The purpose and objectives of the study
The aim of research is to investigate the structure of the ingot produced by ESHKP, the study of the mechanical properties of the steel after different types of heat treatment and working conditions of heat treatment for the product key made from the resultant metal.
3. The practical part
To conduct the study was melted ingot using 40Cr steel shavings and steel 45, which is not subjected to washing and drying (i.e., possible incorporating coolant oil, oxides, etc.) by electroslag remelting nonconsumable (graphite) electrode. We used the flux core brands of AN-295, dioxidizers FS-75 + Al (999) was additionally added flux AN-348A. Steel casting held submerged in a metal mold. Then he was made a joke of the ingot and cutting it on the samples.
Chemical analysis was performed ingot, which is listed in the table.
Table - Chemical compound the ingot%, wt.
Zone ingot | С | Mn | Si | S | P | Cr | Ni | Cu | Al |
Upper part | 0,57 | 0,63 | 0,11 | 0,024 | 0,021 | 0,32 | 0,229 | 0,18 | 0,052 |
The central part | 0,49 | 0,62 | 0,12 | 0,024 | 0,023 | 0,34 | 0,229 | 0,18 | 0,047 |
To investigate samples were taken from three different regions of the ingot: the top, middle and bottom of the ingot. The study was conducted on the macrostructure Nu-2 microscope with increasing x100. The microstructure was studied by Nu-2 microscope at magnifications x100 and x200. Quantitation of porosity were performed using Image Tool.
The microstructure of samples is shown in Figure 1.
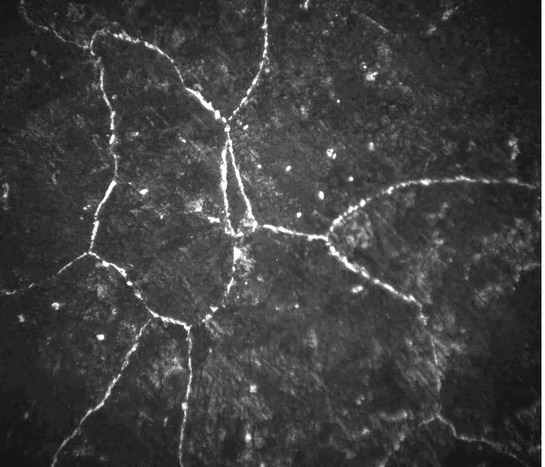
а) the upper part of the ingot-cast"
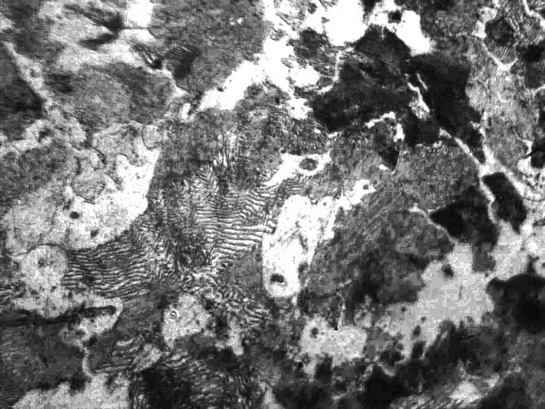
б) the middle part of the ingot after annealing
Figure 1 - The microstructure of the samples
The processing of images macrostructure by a computer program Image Tool was obtained frequency distribution curves of pore size adjustment of the ingot are shown in Figure 2.
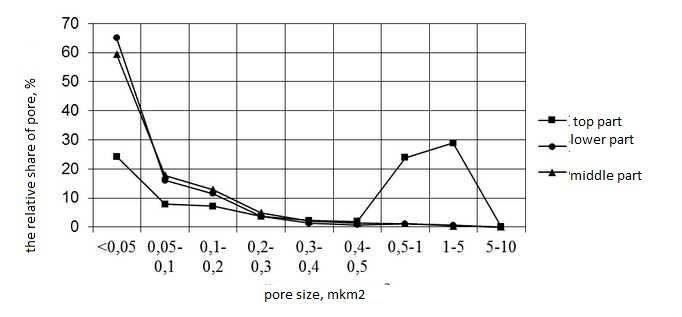
Figure 2 – Frequency curves ratio of pore sizes and the number of
As can be seen from the figure, at the top of the ingot appears a large proportion of pores with an average area of 5 mkm2. In the lower and central part of these has not been detected.Mounted effect can be explained by the fact that, together with the gas bubbles to the top of the ingot present rise in the burden of pollution.
Conclusions
This master thesis was devoted to the urgent problem to date on recycling scrap metal machine shops or offices.Various methods of waste machining steel products, of which as the most economical was selected and tested method of recycling scrap metal by electro chill casting. In this paper the distribution of the chemical compositionthe height of the ingot investigated its macrostructure and microstructure, studied the distribution of pores and their height dimensions of the ingot.
In the future we plan to conduct mechanical tests of strength and toughness, for which the samples were manufactured according to GOST 1497-84 and GOST 9454-78.It is also planned to manufacture the control key from the resulting ingot and develop the optimal heat treatment regime for manufactured products.
In writing this essay master's work is not yet complete. Final completion: December 2013. Full text of theand materials on the topic can be obtained from the author or his manager after that date.
Source List
- Патон Б.Е., Медовар Б.И. Электрошлаковый металл / Патон Б.Е., Медовар Б. Н. - Киев: Наукова Думка, 1981. - 680 с.
- Кнорозов Б.В. Технология металлов и материаловедение / Кнорозов Б.В., Усова Л.Ф., Третьяков А.В. и др. – М. : Металлургия, 1987. – 800 с.
- Глебов А.Г., Мошкевич Е.И. Электрошлаковый переплав / Глебов А.Г., Мошкевич Е.И. - М.: Металлургия, 1985. - 343 с.
- Хольцгрубер В. Металлургические основы электрошлакового переплава сталей / Хольцгрубер В., Плекингер Э. // Черные металлы. - 1968. - № 12. - С. 30 - 41.
- Поволоцкий Д.Я. Электрометаллургия стали и ферросплавов / Поволоцкий Д.Я., Рощин В.Е., Мальков Н.В. - М.: Металлургия, 1995. - 592 с.
- Клюев М.М., Каблуковский А.Ф. Металлургия электрошлакового переплава / Клюев М.М., Каблуковский А.Ф. - М.: Металлургия, 1969. - 256 с.
- Медовар Б.И. Электрошлаковая технология за рубежом / Медовар Б.И., Цикуленко A.K., Богаченко А.Г. и др. - Киев: Наукова думка, 1982. - 319 с.
- Пат. 2263560 Российская Федерация, МПК B22D23/10, C22B9/18. Способ электрошлакового кокильного литья. Шульгин А.Ю., Карицын О.Н., Ранич С.Д., Авдюхин С.С.; заявитель и патентообладатель ООО "НОРМА-ИМПОРТ ИНСО". – № 2003110866/02; заявл. 16.04.03; опубл. 20.10.04.
- Гаревских И.А. Преимущества и вопросы совершенствования электрошлакового переплава стали / И.А. Гаревских, Ю.А. Шульте, В.Д. Максименко и др. // Сталь. - 1962. -№ 1.- С. 39-41.
- Лахтин Ю. М. Металловедение и термическая обработка металлов / Лахтин Ю. М. – [3-е изд.]. – М. : Металлургия, 1983. – 365 с.
- Бернштейн М. Л. Металловедение и термическая обработка стали // Т. 1 Методы испытаний и исследования / Бернштейн М. Л., Рахштадт А. Г. - М.: Металлургия, 1983. - 352 с.
- ГОСТ 1497-84. Металлы. Методы испытаний на растяжение. – М. : Издательство стандартов, 1985.
- ГОСТ 9454-78. Металлы. Метод испытания на ударный изгиб при пониженной, комнатной и повышенных температурах. – М. : Издательство стандартов, 1979.