Introduction
In connection with the current decline in recent years consumption of coke and improve the mechanical and chemical loads of on coke, resulting from a significant increase in the effectiveness of other types of fuels ,there was a need to improve the strength properties of coke, which can be achieved by modern preparing of coke for smelting and optimization of its fractional composition.
The purpose and objectives of the study, the relevance of the topic.
Purpose - to examine the preparation of metallurgical coke for blast furnace and evaluate the change in flow of skip coke.
As fuel in modern blast furnace apply coke, fuel oil, natural and coke gases and a coal dust. Main type of fuel is coke. The porous caked substance remaining after removal from coal of flying substances at its heating to 950 - 1200 °C without access of air is called as coke. It is the only material which keeps a piece form in a blast furnace on all way of movement from a shaft top to a horn. Thanks to this circumstance passing of a gas stream through a layer of liquid, semi-fluid and firm materials in a blast furnace is provided. In the lower part of the furnace the heated coke forms a peculiar drainage lattice through which in a horn liquid products of melting flow down. Height of a column of furnace charge in a modern blast furnace reaches 30 m therefore coke, especially in the lower part of the furnace, perceives big loadings. From here the main demand made to coke follows: high mechanical durability both in cold, and in a heated condition. Coke which is loaded into a blast furnace shouldn't contain the small pieces which worsen gas permeability of furnace charge, excessively large pieces which are, as a rule, struck with cracks and easily collapse in the furnace with formation of small fractions.
Coke has to be porous for ensuring good combustibility in a horn of the furnace and to possess high warmth of combustion for receiving demanded quantity of heat and necessary temperature. Warmth of combustion of coke depends on the content in it of carbon which is defined by the content of the ashes, harmful impurity and flying substances in coke. The content of the ashes, harmful impurity and flying substances in coke is higher, the less warmth of its combustion is less in it than carbon. Besides, with increase in the content of ashes and sulfur the amount of slag, an expense of heat on its fusion increase in coke and the mechanical durability of coke decreases, and with increase in the content of sulfur and phosphorus in coke quality of cast iron worsens. The raised content of flying substances in coke testifies to incompleteness of process of coking that leads to decrease in mechanical durability of coke. Excessively low contents flying in the coke, turning out at пережоге coke, also negatively affects its quality. Therefore coke has to contain whenever possible less ashes, sulfurs, phosphorus and moderate quantity of flying substances. Coke always contains the moisture arriving from coke-chemical plant or from the atmosphere. As coke into a blast furnace load on weight, moisture content coke has to be maintained to constants for preservation of the set thermal mode of the furnace.
Researches and practice of work of blast furnaces show that only at the expense of change of the scheme of sorting of coke, without any other receptions, it is possible to reach significant improvement of technical and economic indicators of blast-furnace process.
Thus, coke sorting is the same full part of technological process of production of coke, as well as preparation of coal furnace charge and actually process of coking. In the conditions of deterioration of a source of raw materials of coking and increase of requirements to quality of coke along with improvement of all technological scheme of coking it is necessary to improve also mechanisms and schemes of sorting of coke for improvement of its quality. It is known that when passing coke from the bunker to распара a blast furnace the average diameter of pieces of coke decreases. In the furnace the fraction of coke of 40-60 mm is less destroyed. Depending on technological conditions coke use by fraction of 60-80 mm and to a lesser extent 25-40 mm is admissible. However fraction of coke 25-0 and 80 of mm already in modern and furthermore in perspective technological conditions, are undesirable.
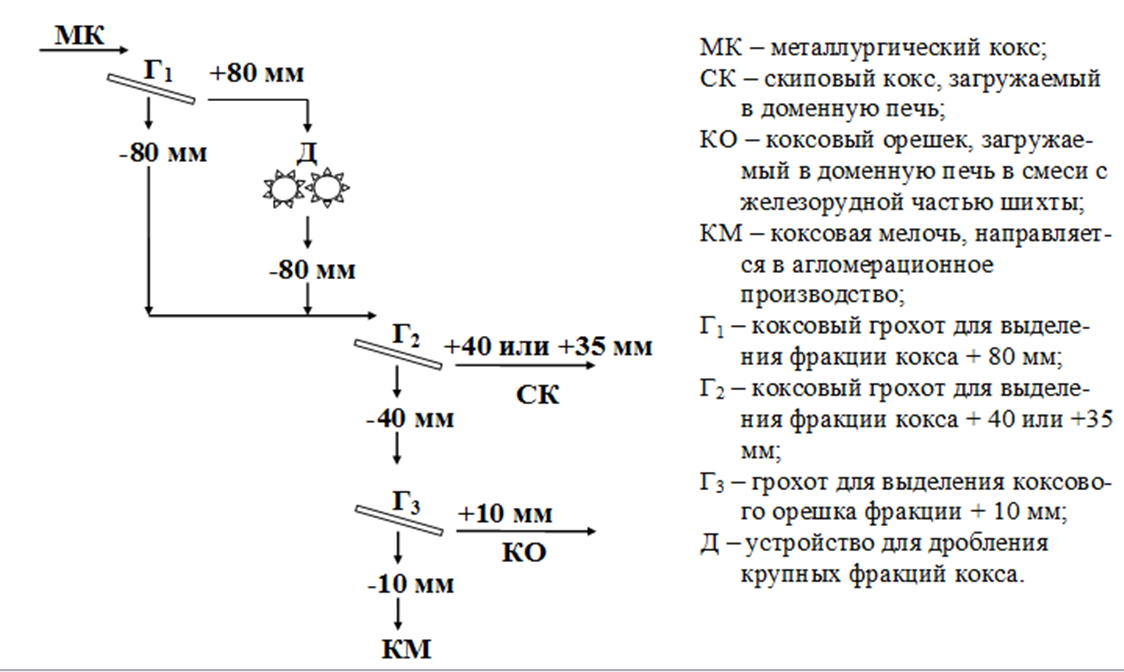
Image 1 - Contemporary tehnoldogiya preparation of coke for blast furnace
The increase in an expense of a coke nutlet fraction of 10-40 mm in quantity from 5 to 30% allows to improve gas permeability in "Sukhoi" zone of a blast furnace for 7-18%, and decrease in a consumption of metallurgical coke for 1,61-4,21%. At the metallurgical enterprises of Ukraine quality of coke on fractional structure can be improved significantly by its preliminary processing for the account:
• allocations from metallurgical coke of fraction more than 80 mm with the subsequent its crushing for the purpose of decrease in the maintenance of fraction more than 80 mm to 5%;
• elimination from metallurgical coke of fraction less than 40 mm;
• allocation on a separate vibroroar from elimination of coke of fraction more than 10 mm, and receiving a coke nutlet;
• transfers of a trifle of coke of fraction less than 10 mm on agglomerative factory;
This preparation allows to keep or increase of productivity of blast furnaces, especially during their work with application of a large number of PUT and a consumption of coke to 300 kg/t of cast iron and below.
Preparation of coke for domain melting will allow.существенно улучшить однородность скипового кокса;
• to improve strength characteristics of coke;
• to improve gas permeability of a column of furnace charge and work of a blast furnace as a whole;
• to reduce coke losses in the form of a class of 10-0 mm at a screen separation;
• to raise extent of use of metallurgical coke in domain melting.
Further decrease in a consumption of coke in domain melting is problematic without essential improvement of quality of coke on such indicators as hot durability.
Conclusion
The main indicators defining a complex of consumer properties of domain coke, its material structure, mechanical characteristics and reactionary ability are. Carrying out researches on development and realization in the industry of parameters of preparation and coking of coal furnace charges with various structure and the properties, providing receiving coke according to modern requirements of the main consumer – domain production is actual. Such approach will allow to increase technical and economic production efficiency both at production of coke, and at its use.
References
- Назюта Л.Ю. Структура энергопотребления доменного производства // Металл и литье Украины – 2009. –№3. – С. 33-39.
- Давидзон А.Р., Ильяшов М.А. Роль угля шахты «Красноармейская – Западная №1 » в производстве кокса для современной технологии выплавки чугуна // Теория и практика производства чугуна. Кривой Рог. 2004 г. - С.215-220
- Мищенко И.М. Черная металлургия и охрана окружающей среды: учебное пособие – Донецк.: ГВУЗ «ДонНТУ», 2012. – 448с.
- Улучшение качества доменного кокса с помощью спецреагентов / В.А. Тамко, И.В. Золотарев, Е.И. Збыковский и др.// Углехимический журнал. – 2009. - № 5-6. – С. 57- 64.
- К вопросу об оптимальном размере кусков скипового кокса / С.Л. Ярошевский, Н.С. Хлапонин, А.М. Кузнецов [и др.] // Металл и литье Украины. - 2009. - № 3. – С. 25-27.
- Ю. В. Филатов, А. Н. Рыженков, А. В. Емченко, к.т.н.; В. Е. Попов,А. И. Дрейко, С. Л. Ярошевский, д.т.н., проф.; И. В. Мишин. Показатели работы доменных печей на МЗ «ДОНЕЦКСТАЛЬ» с применением кокса «Премиум» // Черная металлургия. – 2011. –№1. – С. 30-40.
- Опытная доменная плавка на коксе улучшенного качества ОАО "Запорожкокс" / А.П. Фоменко, В.И. Набока, Н.В. Крутас и др. //Кокс и химия.-2009.-№4.-c.17-23.