Реферат по теме выпускной работы
Содержание
- Введение
- 1. Анализ технологии прокатки колесной заготовки на колесопроктных станах
- 2. Анализ силовых и скоростных режимов прокатки колес на ОАО «Выксунский Металлургический Завод» ВМЗ
- 3. Расчет условий контактного взаимодействия колеса с валками при прокатке его по существующей на ОАО ВМЗ технологии
- Выводы
- Список источников
Введение
Актуальной проблемой, стоящей сегодня перед ведущими заводами-производителями штамповано-катаных колес Украины (ОАО «Интерпайп НТЗ») и России (ОАО «Выксунский металлургический завод» (ВМЗ)), является снижение металлоемкости производства, в том числе за счет уменьшения процента брака на прессопрокатной линии. Решение данной проблемы связано с необходимостью выполнения исследований в двух направлениях. Первое направление – это анализ температурно-скоростных, силовых и деформационных режимов штамповки и прокатки колесных заготовок на основе экспериментальной информации, полученной в условиях промышленного производства колес. Второе направление – это теоре-тические исследования и разработки, направленные в конечном итоге на создание новых методов расчета и проектирования металло-сберегающих технологий штамповки и прокатки колес.
Ведутся работы в части совершенствования технологии прокатки колес и методов ее разработки. В то же время, в современной технической литературе недостаточно изучен вопрос изменения скоростных и силовых параметров при прокатке колес по калибровках, существующих в настоящее время, и режимах обжатий. В современных публикациях по прокатке колес авторы в своих разработках опираются на устаревшие данные экспериментальных исследований 70-х и ранних лет прошлого века. На сегодняшний день эти данные в целом позволяют получить общие представления о процессе деформации колесной заготовки в очаге деформации колесопрокатного стана (КПС), но только на качественном уровне, поскольку не имеют привязки к конкретным силовых и скоростных параметров прокатки и фактического калибровки инструмента деформации.
Поэтому необходим комплексный анализ современных технологических режимов прокатки колес, а именно, анализ силовых и скоростных параметров прокатки во взаимосвязис режимом обжатий колесной заготовки и приращение ее диаметра на разных стадиях процесса. Это позволит, во-первых, получить достоверную информацию озакономерности протекания современного процесса прокатки колес в количественном выражении, во-вторых, определить приоритетные направления развития существующейтехнологии с целью снижения процента брака колес имеет прокатное происхождения, а, в-третьих усовершенствовать режимы прокатки колесных заготовок и методаих расчета. Решению поставленных задач и посвящена магистерская работа.
Актуальной проблемой отечественного колесопрокатного производства является отсутствие методов расчета технологии прокатки заготовок колес,обеспечивающие высокую точность прогноза формоизменения металла и силовых параметров процесса. Решение данной проблемы связано с необходимостьюдальнейшего развития теории колесопрокатного производства и решения задач, которые не имели ранее актуальности.
Магистерская работа посвящена изучению и решению следующих задач: оценка современного состояния производства колесных заготовок на прессопрокатной линии, теоретические исследования процессов деформирования металла при производстве колес, совершенствование режимов прокатки колесных заготовок и метода их расчета.
1. Анализ технологии прокатки колесной заготовки на колесопроктных станах
Технология производства колес включает ряд основных операций. Непосредственное отношение к магистерской работе принадлежит процесс прокатки колес в колесопрокатном стане. Деформация колесных заготовок в современных колесопрокатных станах представляет собой непрерывную прокатку замкнутого круга - обода колесной заготовки - между рабочими валками различной конфигурации, расположенными в разных местах по окружности обода.
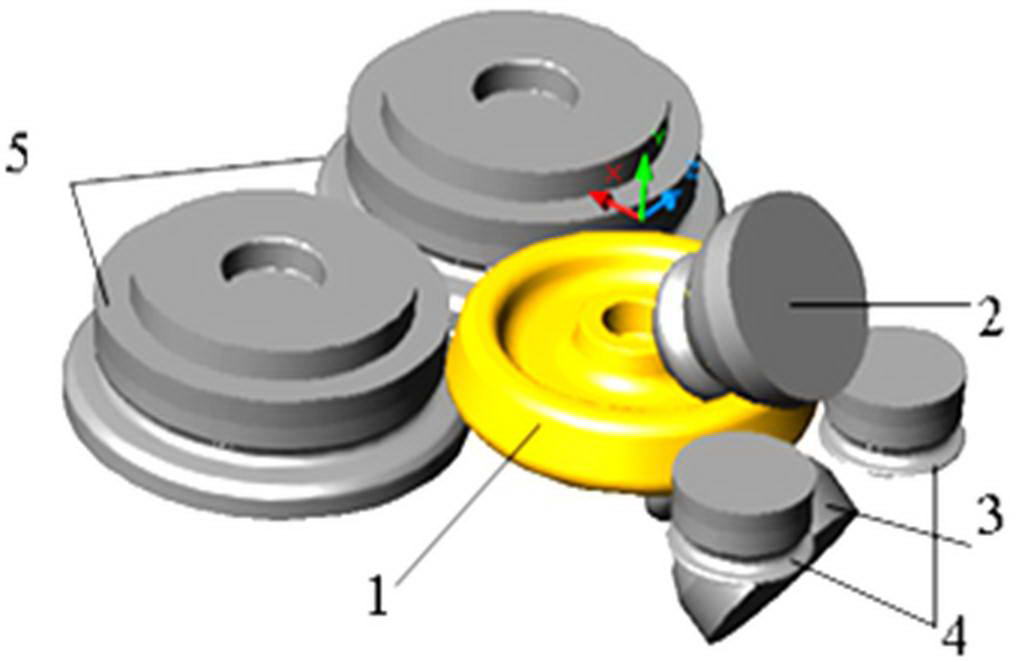
1 — колесная заготовка; 2 — верхний наклонный валок ; 3 — нижний наклонный валок; 4 нажимные валки; 5 — коренные валки.
Экспериментальная информация по силовым и скоростным параметрам процесса прокатки получена в условиях промышленного производства колес Ø957 мм с плоскоконическим диском на прессопрокатной линии ОАО «ВМЗ». По принятой схеме деформации, заготовки массой 485 кг после предварительной осадки гладкими плитами на прессе силой 20 МН транспортировали по рольгангу к прессу силой 50 МН. Поданные на стол пресса силой 50 МН заготовки, имеющие температуру 1190°С, подвергали осадке-разгонке конусной плитой в нижнем технологическом кольце. Подготовленные таким образом заготовки транспортировали по рольгангу к прессу силой 100 МН, где получали отформованные заготовки (рис. 2.1) с окончательными размерами ступицы с примыкающей к ней частью диска и предварительными для последующей прокатки размерами обода с примыкающей к нему частью диска. Поступившую с пресса силой 100 МН колесную заготовку, имеющую температуру 1150°С, с помощью загрузочного устройства задавали в стан. При выполнении исследований, в соответствии с технологической инструкцией, на КПС выполняли следующие операции:
- раскатка колеса по диаметру и выкатку диска;
- выкатка поверхности катания и внутренней поверхности обода;
- выкатку гребня;
- полировку элементов профиля обода.
Величина раскатки колес по внутреннему диаметру обода составляла 146–147 мм, а величина суммарного осевого обжатия обода равнялась 28 мм. После прокатки температура ободьев черновых колес повышалась в результате деформационного разогрева на ~ 50°С.
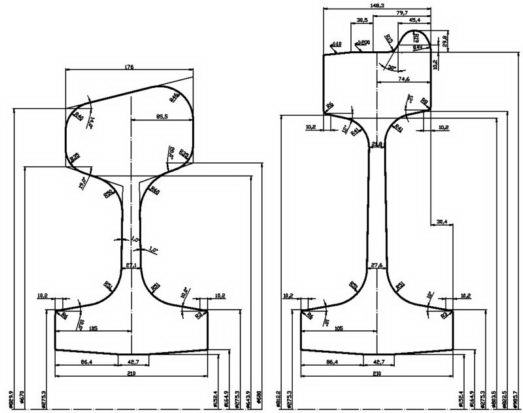
2. Анализ силовых и скоростных режимов прокатки колес на ОАО «Выксунский Металлургический Завод» ВМЗ
В процессе выполнения технологических операций, связанных с прокаткой колес, производили замеры давлений жидкости в гидросистеме КПС. Выполняли три параллельных замера давлений жидкости. В качестве измерительных приборов использовали: манометры избыточного давления МТП–160 – для замеров давлений в гидроцилиндре рабочего хода верхнего наклонного валка и гидроцилиндре прямого хода салазок нажимных валков; манометр избыточного давления МП 4–У – для замеров давления в гидроцилиндре прямого хода каретки коренных валков. Диапазон показаний манометров – (0–40) МПа, цена деления –5 МПа, класс точности – 1,5.
Фиксирование показаний манометров выполняли путем видеосъемки цифровой камерой Canon Power Shot A 570IS с последующей передачей информации в компьютер. Обработку результатов видеосъемок, включающую построение массивов данных по давлениям в зависимости от времени, осуществляли на компьютере с шагом по времени Δt=0,033 с.
Полученные значения сил (усредненные по 3-м параллельным замерам давлений) при прокатке черновых колес представлены в виде графических зависимостей от времени деформации и показаны на рис. 2.1
Расчет приращения внутреннего диаметра колеса при прокатке выполняли на основе данных о перемещении каретки коренных валков и перемещении салазок нажимных валков. Указанные данные при прокатке каждого колеса фиксируются с помощью специально предусмотренных датчиков и автоматически выводятся на дисплей в виде графических зависимостей в режиме реального времени. Кроме того, на данном дисплее также в автоматическом режиме строится график приращения внутреннего диаметра прокатываемого колеса. Настройка системы автоматики ведется по приращению внутреннего диаметра прокатываемого колеса. Система ведет отсчет от нуля и до требуемой величины раскатки колеса по внутреннему диаметру. Указанные графики, построенные с использованием усредненных по 3-м параллельным замерам значениям соответствующих параметров, пред-ставлены на рис. 2.2.
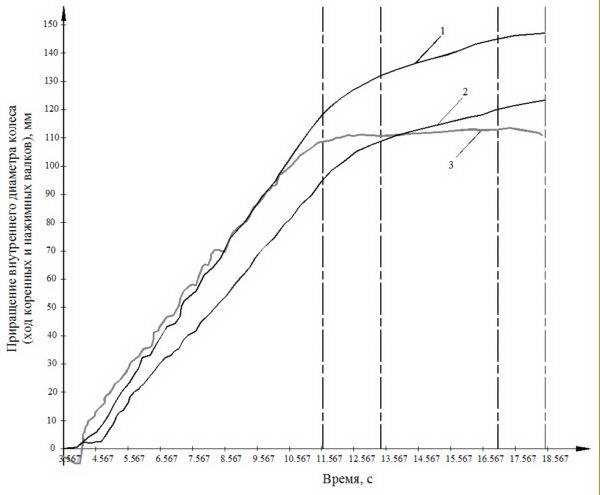
1 – приращение внутреннего диаметра колеса; 2 – ход каретки коренных валков; 3 – ход салазок нажимных валков.
3. Расчет условий контактного взаимодействия колеса с валками при прокатке его по существующей на ОАО ВМЗ технологии
В существующей методике расчета параметров прокатки заготовок колес условия контактного трения задают в виде условия Амантона и при этом используют ничем не обоснованные данные о величине коэффициента контактного трения равного 0,3 – 0,35. Однако, простое перенесение результатов экспериментальных исследований по определению величин коэффициента трения при горячей продольной прокатке стали на процесс прокатки колесных заготовок, является, по меньшей мере, необоснованным. Более того, задание условий трения в таком виде и использование таких значений коэффициента контактного трения применительно к прокатке колесных заготовок приводит к неверным значениям напряжения трения, превышающим напряжение текучести деформируемого металла на сдвиг.
В настоящее время при анализе процессов деформирования заготовок колёс широкое распространение получили методы математического моделирования, основанные на методе конечных элементов. Вместе с тем, в технической литературе отсутствует научно обоснованный метод расчёта условий контактного взаимодействия прокатных валков с колёсной заготовкой. На его создание и направлена часть магистерской работа.
В предложенном методе представлена схема нахождения толщины слоя металла с однородным напряженно-деформированным состоянием (НДС) рис. 3.1
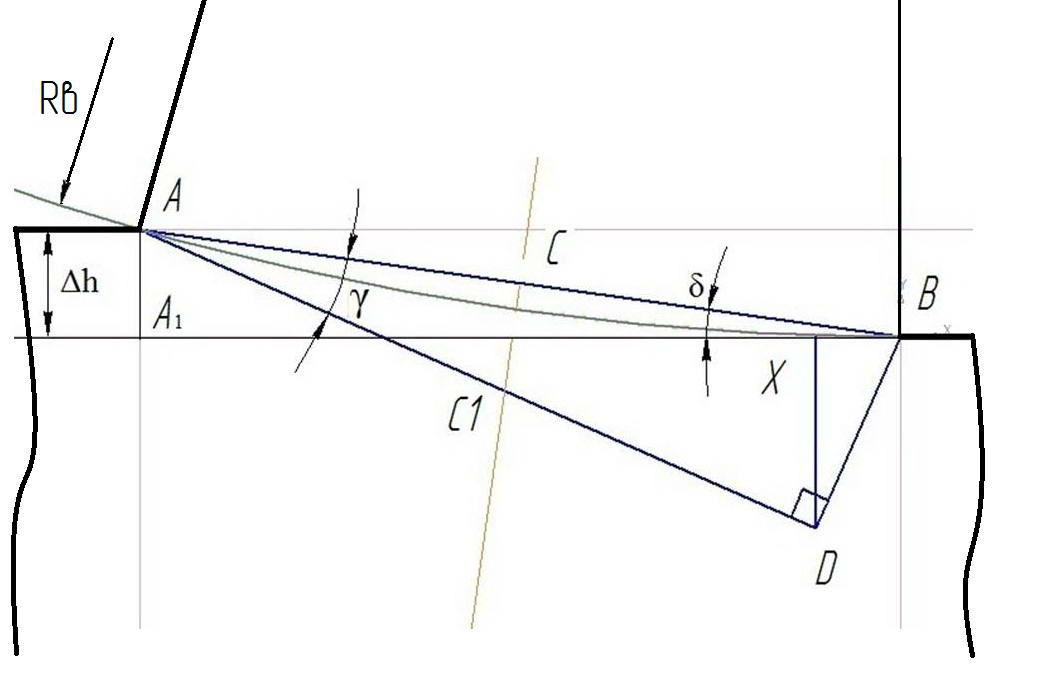
На основе этой схемы была получена экспериментально-теоретическая формула для расчета показателя сил контактного трения
Установлено, что в диапазоне изменения технологических факторов, существующих на практике, используемых при расчете в качестве исходных данных, показательсил трения на контакте с верхним наклонным валиком изменяется в пределах от 0,27 до 0,44, а на контакте с нижним наклонным валиком изменяется в пределах от 0,21 до 0,32.
Выводы
Изучение таких вопросов, как изменение скоростных и силовых параметров при прокатке колес по калибровках, существующих в настоящее время, и режимах обжатийи исследования условий контактного трения при прокатке колес дают возможность промоделировать данный процесс для дальнейшего его изучения и совершенствования,что обеспечит снижение металлоемкости производства.
Магистерская работа посвящена актуальной научной задачи совершенствования технологии производства железнодорожных колес. В рамках проведенных исследований выполнено:
- Анализ технологии деформирования при производстве железнодорожных колес.
- Анализ методов разработки технологии штамповки и прокатки колес.
- Математическое моделирование процессов деформирования на различных технологических переходах пресопрокатнои линии.
- Разработка метода расчета условий контактного взаимодействия колесной заготовки с прокатными валками.
Дальнейшие исследования направлены на следующие аспекты:
- Совершенствование режимов штамповки и прокатки колесных.
- Технологическая схема и калибровки для штамповки и прокатки колесных заготовок на пресопрокатний линии ОАО «ИНТЕРПАЙП-НТЗ.
При написании данного реферата магистерская работа еще не завершена. Окончательное завершение: декабрь 2013 года. Полный текст работыи материалы по теме могут быть получены у автора или его руководителя после указанной даты.
Список источников
- Шифрин М.Ю. Резервы производительности и выхода годного при прокатке колес / Михаил Юльевич Шифрин. – М.: Металлургия, 1989. – 144 с
- Производство железнодорожных колес / [Г.А. Бибик, А.М. Иоффе, А.В. Праздников и др.]. – М.: Металлургия, 1982. – 232 с.
- Яковченко А.В. Проектирование профилей и калибровок железнодорожных колес А.В. Яковченко, Н.И. Ивлева, Р.А. Голышков. - Донецк: Донецкий национальный технический университет, 2008. - 491с.
- Чекмарев А.П., Николаев В.А. Исследование коэффициента трения при горячей прокатке // Изв. вузов Черная металлургия. – 1958. – № 12. – С. 57–67.
- Трение и смазки при обработке металлов давлением: справочник / [А.П. Грудев, Ю.В. Зильберг, В.Т. Тилик]. – М.: Металлургия, 1982. – 312 с.
- Контактное трение в процессах обработки металлов давлением / [А.Н. Леванов, В.Л. Колмогоров, С.П. Буркин и др.]. – М.: Металлургия, 1976. –416 с.
- Хайкин Б.Е. Инженерные формулировки закона трения в условиях обработки металлов давлением / Б.Е. Хайкин // Изв. вузов Черная металлургия. – 1990. – № 1. – С. 38–41.
- Зильберг Ю.В. Закон и модели пластического трения / Ю.В. Зильберг // Изв. вузов Черная металлургия. – 2000. – № 11. – С. 22 – 24.
- Зильберг Ю.В. Некоторые физические особенности пластического трения / Ю.В. Зильберг // Кузнечно-штамповочное производство. – 2002. – № 6. – С. 22–26.
- Евстратов В.А. Теория обработки металлов давлением / Виталий Алексеевич Евстратов. – Харьков:Вища школа. Изд-во при Харьк. Ун-те, 1981. – 248 с.
- Снитко С.А. Анализ силовых и скоростных параметров прокатки колес / С.А. Снитко // Наукові праці ДонНТУ. Металургія: Зб. наук. пр. – Донецьк, 2008. – Вип. 10 (141). – С. 163–172.
- Целиков А.И. Теория продольной прокатки [учебник для студентов машиностроительных и металлургических вузов] / А.И. Целиков, Г.С. Никитин, С.Е. Рокотян – М.: Металлургия, 1980. – 320 с.
- Губкин С.И. Пластическая деформация металлов / Сергей Иванович Губкин. – М.: Металлургиздат, 1960. – Т.2. – 416 с.
- Томленов А.Д. Теория пластического деформирования металлов / Александр Дмитриевич Томленов. – М.: Металлургия, 1972. – 408 с.
- Солод В.С. Математическое моделирование сопротивления деформации при горячей прокатке углеродистых сталей / В.С. Солод Я.Е. Бейгельзимер, Р.Ю. Кулагин // Металл и литье Украины. 2006. – № 7–8. – С. 52 – 56.
- Целиков А.И. Теория прокатки. / А.И. Целиков, А.И. Гришков. – М.: Металлургия, 1970. – 358 с.