Abstract
Contents
- Introduction
- 1. Theme urgency
- 2. Goal and tasks of the research
- 3. Overview of Research and Development
- 4. The main material
- 4.1 The concept of economic efficiency of the company's quality
- 4.2 Models of research quality costs
- Conclusion
- References
Introduction
At present, today's enterprises have to work in a rapidly changing environment, because today is fast changing consumer preferences, develop new products and services, opening up new niches, upgraded equipment. Thus, not only to businesses that want to take a leading position in its industry, but businesses who simply want to work steadily on the market, must promptly respond to these changes, adapting to the prevailing conditions. One of the ways that greatly simplifies the process of adaptation, is the implementation of quality systems in the enterprise. However, to really integrate the principle of work, an evaluation of the effectiveness of the quality system that will determine how effective the strategy chosen and what improvements and enhancements need to be made in the future.
1. Theme urgency
Since the large–scale implementation of quality systems based on international standards ISO 9000, before every now the question is, how to evaluate the effectiveness of the quality system. This is the reason the relevance and practical significance of my thesis.
2. Goal and tasks of the research
Goal of the research: to study the peculiarities of the economic efficiency of the quality system implemented in the enterprise.
The object of the research: the economic efficiency of the quality system.
Subject of research: the identification of ways and methods to assess cost–effectiveness of the quality system.
Tasks of the research:
- to review the literature on the subject;
- to analyze the ways and methods to assess cost–effectiveness of the quality system;
- to formulate conclusions.
3. Overview of Research and Development
Studies of theoretical, methodological, and practical issues of economic analysis of quality management systems were many Russian and foreign scientists in various fields. In the development problems of quality management and quality management systems important role played by the works of W. Deming, J. Juran, K. Ishikawa, F. Crosby, G. Taguchi, A. Feigenbaum, J. Harrington, W. Shewhart.
Great contribution to the study of the economic aspects of the quality management system were works of scholars such as G. Azgaldov, R. Belobragin, A. Bogdanov, B. Gerasimov, A. Glitsch, D. Demidenko, N. Il'enkova, J. Campanella, Y. Kulikov, V. Lapidus, D. Lions, V. Okrepilov, S. Ponomarev, A. Hachaturov, V. Shvets, J.Ch. Shottmiller.
Scientific works of these authors are of great theoretical and practical significance. However considered in their approach to economic analysis can only partially assess the performance of quality management systems [14, с.5]
4. The main material
4.1 The concept of economic efficiency of the company's quality
Many experts believe that the effectiveness of quality systems should be defined primarily as a cost–effective way of communication (functional or correlation) between the implementation of quality management systems and the financial performance of companies. It is interesting to note that the different experts in a completely different understanding of the problem and therefore choose how to resolve it. Traditional economists are looking to determine the cost–effectiveness of the quality management system within the logic of traditional approaches. According to this logic, the cost effectiveness is determined in two ways:
- the economic effect = results - costs;
- economic efficiency = results / costs (or payback period) [4].
The economic impact is defined as the difference in costs before and after implementation of an intervention. As the economic performance includes the following cost parameters: the volume of production; gross income (or turnover), profits and the net. Because the costs and benefits are separated in time, then the determination of both groups are encouraged to consider their time difference with the discounting procedure [2, c.286].
In the Greater economic dictionary
Economic efficiency is defined as: the result of economic activity, economic development programs and activities, characterized by the ratio of the resulting economic impact to the cost of the factors of resources, contributing to obtaining this result, achieving greater output with the use of a particular resource value
[5, c.811]
In the electronic economic dictionary: Economic efficiency — the impact of the economic system, as expressed in respect of beneficial outcomes of its operation to wasted resources
[6]
In electronic sources, we find such a thing as Economic efficiency — rate determined by the relation of economic effect (outcome) and cost that generated this effect (result)
[7]
Thus we see that all these definitions are similar to each other and on semantic value is almost identical to the definition given in the standard ISO 9000:2008 [3, c.14], where efficiency is defined as the relationship between the result achieved and the resources used
.
In other words, economic efficiency is determined based on the ratio between benefits and their costs [2, c.288]
Based on the definitions of economic efficiency, to set the record performance without costing the quality is not possible.
A. Feygenbaum quality costs are divided into the following groups:
- prophylactic, including planning quality, i.e. costs associated with any activity that reduces or prevents the occurrence of defects or losses;
- the cost of testing, including the inspection, ie the costs of assessing and confirming the achieved level of quality;
- the internal losses, including the cost of a full marriage and alterations, ie costs incurred within the organization when the agreed level of quality is reached, ie before the product has been sold;
- external losses, including maintenance costs claims and guarantees, and so when a specified quality level is reached, i.e. after the product has been sold.
Thus, the sum of all of these costs will be equal to the total cost of the quality [1 c.166].
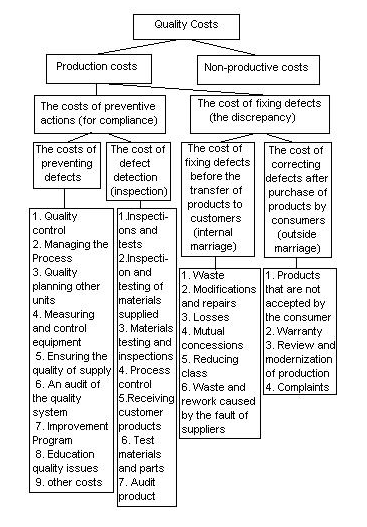
Figure 1 — Structure of Quality Costs
The structure formation of the cost of the quality of products and their types are shown in Figure 1. Note, however, that the distribution of the costs of these groups is very conditional. And in different organizations can use their methods of calculation. But this is not essential since the classification and analysis of quality costs — internal operations of each company. Enough that there was full coordination across the enterprise for selected types and categories of expenses. Cost categories must be permanent, not duplicate each other.
All initial cost data can be obtained by controlling the quality of the information, which includes maintaining appropriate records within the existing quality system. Analysis and evaluation of quality costs enables the company to control costs and to assess the impact of the system on the quality of performance.
Quality costs are inevitable in any business activity, since it is impossible to exclude useful quality costs
, associated with providing and maintaining the achieved level of quality. At the same time, there is a part of expenses on which the company can get rid of, if you reduce the number of inconsistencies in their work and products (services rendered). The logic of free quality
will become effective when the share of the costs of preventive measures (useful expenditure
) will grow. By increasing the preventive measures will decrease the number of inconsistencies that will provide the company with high quality products and services that will reduce the costs of monitoring and will enhance profits.
You can not manage what you can not change. Learning how to measure and evaluate the effectiveness of the implemented quality management system, the company's ability to control the efficiency of the system and improve its quality. Classification of quality costs — just the first step in the direction of quality cost management and evaluation of the effectiveness of the quality system. For a full evaluation of the effectiveness of the quality system must develop and implement a system for recording and analysis of the cost of quality. In this case, the company faces the following problems:
– сlassify the cost of quality;
– identify sources of data on the costs of quality;
– to choose a base for measurement;
– to determine the responsibility for the collection and analysis of information;
– the cost of quality control throughout the company, divisions, separate processes.
After the successful implementation of the tasks described above the company can build on the results and link quality objectives with the financial performance of the company. Embed the recording and analysis of the cost of quality in the daily work of staff will contribute to the closer integration of the quality system with a system of financial management of the company, thereby increase the usefulness, accessibility and visibility of operational economic indicators of the quality management system [8].
Thus, the performance management system is part of the quality control system of expenses of the company. Those enterprises that carry out an effective management strategy to optimize costs, understand that the management of quality cost — is a tool to reduce the total cost of the company, improve profitability and strengthen its competitive position in the market.
4.2 Models of research quality costs
To estimate the cost of quality is being formed by two basic pricing models: the cost model of the process described in the British Standard BS 6143:1992 Economics Manual of quality. Part 1. The cost model for the process
, and the model of prevention, assessment and failure (PAF), described in the British Standard BS 6143: 1990 Quality Management in economics. Part 2. Model of prevention and assessment and failure
[9].
The first part The cost model for the process
. According to this concept takes into account all the costs of executing a process that has its inputs and outputs, as desirable and undesirable.
The cost model of the process means that all the costs of production can be divided into two categories: the costs associated with achieving compliance in quality, and costs associated with the mismatch in quality. Both of these costs are considered as potential sources of savings. In this case, the costs of non–conformity in quality includes only those costs which are caused by a departure from the design, technological, regulatory, organizational documentation, and do not include the costs of prevention of deviations from the documentation (staff development, reliability testing, etc.). The focus of the cost model of the process is given to reduce the costs of the process [10, c.7].
First, consider the possible costs of quality in the production process or services. Next, you must determine the value of all the identified costs. It can be obtained from the financial reports, or by making a report on the cost of the process. The grouping of these indicators, the report does not solve problems, but allows them to detect. Even if a solution is found to be unfit because of cost or other reasons, the problem should not be neglected — the ability to apply the obtained solution may appear later.
The main object of this presentation, that after opening and determine the cost of the process it is possible to control and continuous improvement in all categories.
This system is applicable to all processes of different enterprises.
The second part is the Model PAF
(prevention, assessment, failure). In the model of PAF costs associated with quality assurance, are divided into two main categories: сosts associated with the mismatch in quality (non–repayable) and the costs associated with achieving compliance (preventive) in quality.
Costs associated with compliance, are divided into the cost of evaluation and prevention, and the costs associated with non–compliance — for internal failures and external failures. In accordance with the standard nomenclature consider all types of costs.
The costs of prevention:
– quality planning, development and design of measuring and test equipment;
– analysis of the quality of the design and testing;
– inspection and maintenance of equipment for measuring and testing;
– inspection and maintenance of manufacturing equipment used to measure the quality;
– guarantees suppliers;
– training in the field of quality;
– analysis of the quality of the program and to improve quality.
Evaluation costs:
– pre–production testing;
– selection of the control;
– laboratory acceptance testing;
– monitoring and testing;
– the control and test equipment;
– materials consumed during the inspection and testing;
– to analyze and report on the results of tests and controls;
– field test performance, approval or endorsement, the evaluation of stocks;
– inventory warehousing.
Evaluation costs are justified if the mismatch to detect the produce falls to the consumer. Such actions may include:
– product testing or checking the documentation before it will be given to the consumer;
– verification of documents and correct errors before they are shipped;
– restoration of damaged surfaces;
– checking accounts prepared before sending them to customers for payment.
Identify inconsistencies at this stage rule out serious failures costs and disruptions in the future, as well as helping to develop more effective methods of control [11,c.4].
The cost of compliance is often called prophylactic or preventative costs of quality improvement. These costs are profitable investments in quality improvement.
Costs associated with internal failures: marriage; replacement, modification and repair; troubleshooting and analysis of defects and failures; re-testing and control; permission to modify and concessions; downgrading of quality; downtime.
Costs associated with external failures: complaints; guarantee a refund; rejected and returned products; loss of sales; the cost of a product recall; product liability.
The costs associated with failures or irrecoverable costs of quality are on average 5.4% of sales.
In order to consider all the losses, in addition to the traditional costs, you need to take into account the hidden costs of non–conformity: the content of an additional service; delays in the implementation of plans; delays in the registration of documents; additional services; errors in the design of invoices for payment; partial fulfillment of orders; finalization of the construction of nonconforming product; loss of time for contact with dissatisfied customer; the unused production capacity, etc.
These are not recorded in the accounting documents of the costs are at least 15-20% of total sales.
Efforts to correct non-conformities identified outside the company, usually aimed at restoring the confidence of consumers, otherwise it threatens the loss of the market.
Consequently, not only costly organizational quality assurance, as inconsistencies that lead to alterations, repair and disposal of defective products [12].
The model considered PAF easily applied in the analysis of the cost of quality products in the industry, but to a lesser extent applicable in the analysis of the costs of processes and services. PAF model is based on a calculation of the specific costs associated with the amount
of a particular product [11,c.4].
Thus, at the present time to assess the cost of quality evaluation model, the following: the cost model and process model evaluation and prevention of failures (PAF). However, when assessing the cost-effectiveness of the quality system model on which will be assessed, should be selected based on the specifics of the enterprise.
Conclusion
Quality System — a set of organizational structure, procedures, processes and resources needed to implement quality management.
After the implementation of quality systems in the enterprise, in order to understand how effective this system is, how effective is the strategy chosen and what improvements and enhancements need to be made in the future – it is necessary to assess the effectiveness of the quality system.
In accordance with the terminology of the standard ISO 9000:2008, efficiency is defined as the relationship between the result achieved and the resources used
. Thus, to assess the cost–effectiveness is impossible without determining the cost of quality.
To estimate the cost of quality is being formed by two basic pricing models: the cost model of the process described in the British Standard BS 6143:1992 Economics Manual of quality. Part 1. The cost model for the process
, and the model of prevention, assessment and failure (PAF), described in the British Standard BS 6143: 1990 Quality Management in economics. Part 2. Model of prevention and assessment and failure
.
Quality costs are inevitable in any company, because we can not rule out useful quality costs
, associated with providing and maintaining the achieved level of quality. At the same time, there is a part of the costs from which the company can get rid of, if you reduce the number of inconsistencies in their work and products (services rendered). The logic of free quality
will become effective when the share of the costs of preventive measures (useful expenditure
) will grow. By increasing the preventive measures will decrease the number of inconsistencies that will provide the company with high quality products and services that will reduce the costs of monitoring and will enhance profits.
You can not manage what you can not change. Learning how to measure and evaluate the effectiveness of the implemented quality system, the company's ability to control the efficiency of the system and improve it. Classification of quality costs — just the first step in the direction of quality cost management and evaluation of the effectiveness of the quality system. For a full evaluation of the effectiveness of the quality system must develop and implement a system for recording and analysis of the cost of quality. In this case, the company faces the following problems:
- classify the cost of quality;
- identify sources of data on the costs of quality;
- to choose a basis for measurement;
- to determine the responsibility for the collection and analysis of information;
- the cost of quality control throughout the company, divisions, separate processes.
After the successful implementation of the tasks described above the company can build on the results and link quality objectives with the financial performance of the company. Embed the recording and analysis of the cost of quality in the daily work of staff will contribute to the closer integration of the quality system with a system of financial management of the company, thereby increase the usefulness, accessibility and visibility of operational economic indicators of the quality system for guidance.
Thus, the performance management system is part of the quality control system of expenses of the company. Those enterprises that carry out an effective management strategy to optimize costs, understand that the management of quality cost — is a tool to reduce the total cost of the company, improve profitability and strengthen its competitive position in the market.
No common methodology developed test the effectiveness of the quality system, so each company to decide for itself what methods to use the evaluation, based on the specific tasks and production. However, the undisputed fact remains that the effectiveness of quality management systems will grow naturally only in the case when management will conduct an ongoing analysis that will clearly display all the results achieved, financial performance, assess the quality of the products and the obtained data to evaluate the effectiveness of the entire system quality management. Thus, evaluation of the effectiveness of the quality management system should be carried out regularly, comprehensively and responsibly.
References
- Момот А.И. Менеджмент качества и элементы системы качества: Учебник. – 2-е изд., доп. и расш. – Донецк: Норд–Пресс, 2005. – 320с.
- Управление качеством: учебник для бакалавров / Е.А. Горбашко. – М.: Издательство Юрайт, 2012. – 463 с. – Серия: Бакалавр. Углубленный курс.
- Международный стандарт ISO 9000: 2008. Системы менеджмента качества. Основные положения и словарь.
- К вопросу определения результативности и эффективности СМК. [Электронный ресурс]. – Режим доступа: http://www.classs.ru
- Борисов А. Б. Большой экономический словарь. – М.: Книжный мир, 2003. – 895 с.
- Экономический словарь. [Электронный ресурс]. – Режим доступа: http://abc.informbureau.com
- Современная экономическая теория. [Электронный ресурс]. – Режим доступа: http://modern–econ.ru
- Повышение эффективности системы менеджмента качества компании. [Электронный ресурс]. – Режим доступа: http://www.psycho.ru
- Шулепова К.С., Морозова Е.В.
Модели управленческого учета затрат на качество
. [Электронный ресурс]. – Режим доступа: http://www.rae.ru - BS 6143. Руководство по экономике качества. Часть 1 : Модель затрат процесса (1992). – М. : НТК
Трек
, 2001. – 26 с. - BS 6143. Руководство по экономике качества. Часть 2 : Модель предупреждения, оценки и отказов (1990). – М. : НТК
Трек
, 2001. – 24 с. - Финансовый менеджмент и менеджмент качества. [Электронный ресурс]. – Режим доступа: http://www.logolex.com.ua
- Бондарец А.В., Чеснокова Ж.А., Чесноков А.Ю. МЕТОД ИССЛЕДОВАНИЯ ЗАТРАТ НА КАЧЕСТВО // Современные проблемы науки и образования. – 2011. – № 6. Электронный журнал. [Электронный ресурс]. – Режим доступа: http://www.science–education.ru
- Экономический анализ системы менеджмента качества промышленного предприятия / А.Н. Канивец, Б.И. Герасимов, Л.В. Пархоменко; под науч. ред. д-ра экон. наук, проф. Б.И. Герасимова. Тамбов: Изд-во Тамб. гос. техн. ун-та, 2005. 144 с.