Реферат по теме выпускной работы
Содержание
- Введение
- 1. Актуальность темы
- 2. Цель и задачи исследования
- 3. Краткое изложение результатов магистерской работы
- Выводы
- Список источников
Введение
В настоящее время в Украине формирования рыночных отношений хозяйствования почти не сопровождается соответствующим реформированием сферы взаимодействия общества и природы, хотя накопленный международный опыт свидетельствует о невозможности достижения высокого уровня социально–экономического развития без экологизации хозяйственных отношений. Экологизация осуществляется через систему организационных мероприятий, инновационных процессов, реструктуризации сферы производства и потребительского спроса, технологическую конверсию, рационализацию природопользования, трансформацию природоохранной деятельности, осуществляемых как на макро, так и на микроэкономическом уровне. На макроуровне приоритетной является структурная перестройка природоохранных продуктовой вертикали экономики, а на микроуровне – это разработка малоотходных технологий и оборудования, ресурсосбережения, а также внедрение систем комплексного и рационального природопользования.
Особенно важное значение вышеприведенное имеет для природно–эксплуатирующих отраслей промышленности, одной из которых является угольная сфера. Ее хозяйственная деятельность непосредственно связана с разработкой природно ресурсного потенциала недр с целью получения конечного продукта – уголь. Одновременно образуется огромное количество попутно добываемых твердых, жидких и газообразных продуктов, которые до недавнего времени характеризовались как отходы. Значительное количество таких отходов позволяет рассматривать их как техногенные месторождения, которые негативно влияют на окружающую среду. В то же время в их содержании находится огромное количество полезных химических элементов и соединений.
В свете вышеперечисленных «атрибутов» и механизмов экологизации целесообразна оптимизация недропользования и охраны окружающей среды. Речь идет о рациональном использовании и охране недр в процессе эксплуатации природных ресурсов, заполнении их запасов, ресурсосбережении, комплексном использовании минеральных ресурсов недр и техногенных месторождений.
Таким образом, речь идет о преобразовании угольной отрасли с монопродуктового в полипродуктову. Физико–химической базой для осуществления такого перехода является как сам целевой продукт производства – уголь, так и попутные продукты добычи, а инструментом (механизмом) реализации – процесс диверсификации хозяйственной деятельности. Скорость преобразования угольной отрасли в полипродуктову не имеет технологических ограничений и определяется, прежде всего, финансированием этого процесса.
Развитие индустрии переработки и утилизации отходов на современной научно–технической и технологической основах в контексте инновационной модели устойчивого развития позволит комплексно решать экологические, экономические и социальные вопросы перестройки хозяйственного механизма горной отрасли. В частности, положительным следствием такого подхода является увеличения объема добычи угля и его качества, рост конкурентоспособности угледобывающих предприятий, снижение их убыточности, повышения рентабельности и инвестиционной привлекательности[8].
1. Актуальность темы
Проблема отходов является очень актуальной для донецкой области, принимая во внимание техногенную нагрузку на эту территорию и объемы промышленных отходов, образующихся. Целесообразность переработки отходов в нашем регионе обусловлена следующими факторами:
• природными, позволяющие благодаря мягкому климату разрабатывать отвалы практически весь год;
• социальными, связанными с закрытием шахт и высвобождается большого количества трудоспособного населения;
• экономическими, связанными с большой потребностью густонаселенного промышленно развитого региона в строительных материалах, а также наличием хорошо развитой инфраструктуры, что значительно облегчает внедрение предлагаемых технических решений.
2. Цель и задачи работы
Целью данной магистерской работы является проведение детального анализа и расчета эколого–экономической эффективности затрат на внедрение и эксплуатация технологии использования отходов шахты для производства строительной продукции, строительства дорожного полотна, использования породы для удобрения почвы.
Главной же задачей магистерской работы является определение целесообразности внедрения технологии использования шахтной породы для производства строительной продукции.
3. Краткое изложение результатов магистерской работы
Особенностью, характерна для Донецкой области, является накопление многочисленных отвалов, терриконов, золоотвалов, хвостохранилищ, в которых складируются огромные количества шахтных пород и золошлаковых отходов(рис. 1; рис. 2). Размещение техногенных массивов требует отторжения значительных территорий. Отходы являются источниками загрязнения окружающей среды, создают вокруг себя зоны поражения, в сотни раз превышающими площади, которые сами занимают. На строительство отвалов, складирование отходов и природоохранные мероприятия по снижению их негативного воздействия тратятся огромные средства. Поэтому, утилизация отходов добычи и сжигания угля является важной технико–эколого–экономической задачей.
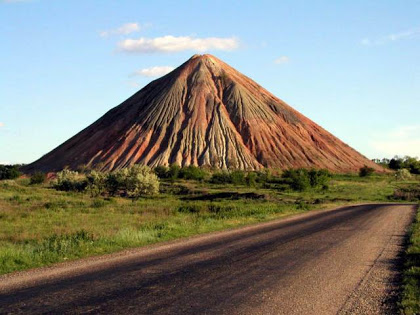
Рисунок 1 – Террикон образовавщийся в результате деятелности человека
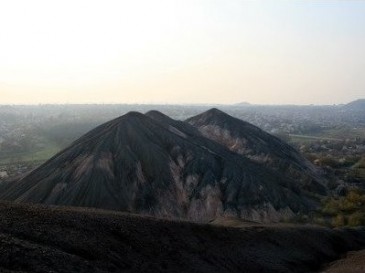
Рисунок 2 – Золоотвал
Остатки от процессов обогащения, газификация или сжигание в кипящем слое золошлаки наиболее целесообразно использовать по трем направлениям: для закладки выработанного пространства, как сырье в производстве строительных материалов и вяжущих веществ или минеральных удобрений.
Отходы угольного производства является потенциальным сырьем для изготовления аглопорита, кирпича, различных строительных материалов, золошлаки для производства цемента, заполнителей асфальтобетона, строительных растворов и т.д.
Продукция выпускаемая из отходов, по качеству не уступает изделиям из традиционной природной минеральной сырья. Предлагаемые на сегодняшний день технологии позволяют получать материалы с повышенной прочностью, морозостойкостью, износостойкостью, устойчивостью к атмосферным воздействиям и воздействию агрессивных сред. По физико–механическим свойствам и техническим характеристикам материалы соответствуют всем требованиям нормативных документов.
На основе горелых шахтных пород и золошлаковых отходов могут быть получены следующая продукция:
• инертные заполнители (щебень, песок из отсева дробления, щебеночно–песчаные смеси);
• тяжелые и легкие бетоны (изделия для промышленного, гражданского и социального строительства);
• ячеистые бетоны (блоки теплоизоляции, перегородки, панели, литой бетон для теплоизоляции полов, чердачных перекрытий, крыш);
• мелкозернистые бетоны (мелкоштучные стеновые изделия, тротуарные плиты, бортовое камни, элементы мощения);
• строительные и тампонажные растворы, обладающие коррозионной стойкостью и гидроизоляционной способностью;
• сыпучие материалы теплоизоляции (заменители керамзита);
• керамические материалы (изделия строительной, санитарно–технической и художественной керамики, огнеупоры);
• нерудные материалы для дорожного строительства (для создания оснований и покрытий, в том числе покрытий из мелко и крупнозернистого асфальтобетона с применением слоев износа);
• закладные материалы, сыпучие и такие, твердеющих (для выполнения закладочных работ в выработанном пространстве).
Утилизация отходов добычи и сжигания угля дает возможность решить ряд важных проблем:
• пополнить минерально–сырьевую базу строительной индустрии региона, снизить стоимость строительной продукции и расширить ее номенклатуру;
• трудоустроить население, освобождалось в связи с закрытием нерентабельных шахт;
• улучшить состояние окружающей среды.
Благодаря этому техногенная сырье завоевывает все больше позиций в индустрии строительных материалов. Для повышения эффективности деятельности шахты в сфере обращения с отходами предлагаем внедрить технологию по использованию отходов и производству из них строительных материалов.
По технологии производства стеновые блоки делятся на несколько видов: шлакоблоки; пенобетонные блоки; пескобетона или песчано–цементные блоки (пискоблокы) газосиликатные блоки или блоки зкомирчастого бетона; керамзитобетон блоки(рис. 3; рис. 4).
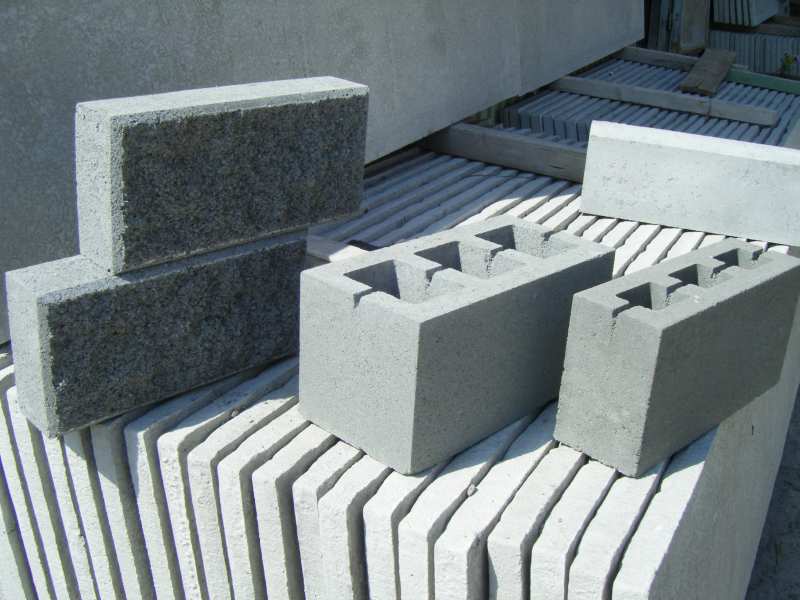
Рисунок 3 – Пеноблоки, керамзитобетон блоки и тротуарная плитка
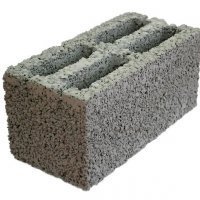
Рисунок 4 – Песчано–цементный блок
Их применение в строительстве имеет следующие преимущества: технологические преимущества, скорость монтажа в 4,5 раза выше; сооружения стен требует в 2,2 раза менее смеси; замечательная звукоизоляция; по объему блок заменяет 6 шт. Красной кирпича, а с учетом теплопроводности – 12 шт. Увеличения полезной площади помещения на 5 % за счет уменьшения толщины стенок, масса 1 кв. М кладки в 1,5 раза легче, в результате нагрузка на фундамент в 2 раза меньше, разнообразные цвета – серый, зеленый, желтый, красный и т.д.; экономия на издержках; себестоимость строительства на 30 – 40 % ниже; экологическая чистота составляющих наполнителей стеновых блоков [4].
Принимая во внимание преимущества стеновых блоков предлагаем внедрить их производство из шахтных отходов и на основе эколого–экономического обоснования выбрать лучший вид продукции.
Распространенная технология производства стеновых блоков состоит из следующих этапов:
1. Приготовление жесткой бетонной смеси.
Для приготовления раствора жесткой бетонной смеси используются: цемент, шлак (отсев) и вода. У нас в регионе (в зависимости от влажности наполнителей) жесткий раствор получается при смешивании от 0,4 до 1 части воды, равной части (по весу) цемента м 400 и от 4 до 9 (обычно 5–7) частей отсева (щебня, шлака, керамзита).
Раствор лучше готовить в бетономешалке, или вручную лопатами в любой емкости или на площадке (но для приготовления жесткой смеси потребуется значительные физические усилия). Температура в помещении или на площадке, где проводятся блоки, должна быть выше 1 °С.
2. Загрузка, уплотнение и удаление раствора из формы.
Загрузка раствора в формы, а затем происходит уплотнение в форме с помощью вибрации и прижима и удаление формы с оставлением блока на полу или поддоне. Жесткий раствор после виброуплотнения позволяет полученному блоку не рассыпаться и держать форму "самостоятельно" и не «поплыть» во время высыхания.
Конечно виброуплотнение длится 20–30 сек., На простых вибростанки без «усиленного» прижима это время больше – до 90 сек., На станках с прижимом и усилием в несколько тонн время виброуплотнение раствора можно значительно сократить. Затем, уплотненную и сжатую в форму блока, смесь удаляют из формы. Полученный таким образом блок оставляют на полу или поддоне.
3. Условия полного затвердевания и набора прочности.
Условия, при которых блок полностью затвердевает, очень просты и доступны. Они не требуют каких–либо специальных сооружений или приспособлений. Необходимый уровень прочности, требуется для складирования, хранения, использования и реализаций блоков, достигается при естественной температуре. Длится он от 36 до 96 часов (без применения специальных добавок). Если в бетонную смесь заранее были добавлены такие вещества, как релаксол, фулерон и другие, то время до полной готовности блока, сокращается. Полное затвердевание блоков происходит в течение месяца.
Температура должна быть от 20 градусов и выше и соблюдением условия высокой влажности. Влажность – максимально высокая. Это непременное условие, иначе процесс набора прочности может перейти в процесс «пересыхания» (так сказать «сгорания»). А это приведет к значительной потере прочности и ухудшения качества изделия. При температуре 20–25 °С изделие достигает необходимого набора прочности через 20–25 часов.
При использовании ускорителей схватывания бетона и более высокой окружающей температуре блоки набирают прочность, что требуется, быстрее. Положительно скажется на прочностных организация дополнительного пропаривания блоков. После этого они складируются, где происходит дальнейший набор прочности не менее 50 % от проектного согласно государственных стандартов для возможности отгрузки потребителю или применения на стройплощадке.
При этом необходимо использовать стеллажи для подблокових пластин. Применение этих стеллажей не только улучшит качество продукции, но и значительно сократит время полного «схватывания» изделий, а так же существенно уменьшит занимаемую производственную площадь (на 30–40 кв. М).
Для производства блоков и других строительных изделий используются следующие компоненты: вяжущее вещество, наполнитель, вода, химические добавки – пластификаторы и модификаторы бетона (по требованию заказчика). В качестве вяжущего вещества могут использоваться портландцемент как низких, так и высоких марок, а также гипс, который медленно твердеет.
В качестве заполнителя в любых сочетаниях используется песок, отсев щебня, керамзит, шлак, зола, опилки, торф, пенополистирол гранулированный, писчаногранитна смесь, мраморная крошка, бой кирпича и т.д. При температуре 20–25 °С твердения изделий происходит через 20–25 часов. Рекомендуется использовать портландцемент марки 400 (пц м 400). При использовании цемента марки 300 расход цемента следует увеличить на 10 %, использование цемента пятисотый марки позволяет снизить его расход на 10–20 %[3].
На производство смеси для блоков необходимы следующие материалы:
• цемент М–400,
• отходы угледобычи,
• вода,
• пластификатор.
Добавка способствует уменьшению соотношения «вода–цемент», быстрому набору прочности в начальный период, существенно повышает текучесть и возможности удобно заключаться бетонную смесь.
Для производства блоков нами было выбрано оборудование «Кондор–1» – малогабаритная вибропресующая механизированная установка для производства стенового, перегородочные бетонного камня, тротуарной плитки и других изделий (рис. 5)
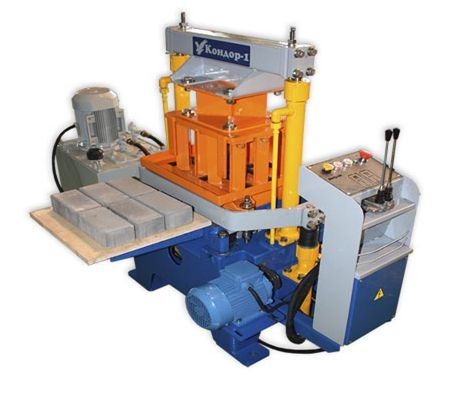
Рисунок 5 – Оборудование «Кондор–1» для изготовления стеновых блоков
Блок–схема технологического процесса производства стеновых блоков из отходов угольной промышленности (рис. 6)
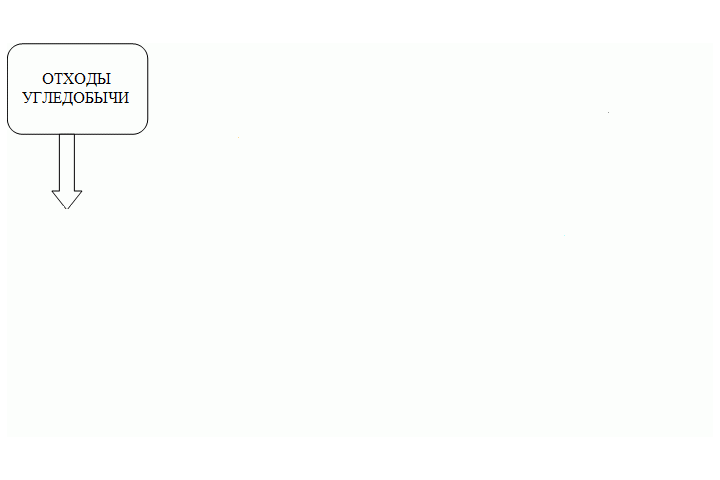
Рисунок 6 – Блок‐схема технологического процесс производства блоков
(анимация: 9 кадров; 6 циклов повторения; 89 килобайт)
В состав установки входит вибропресс, маслостанция, пульт управления, электрошкаф, 5 поддонов. Смеситель и матрицы в стоимость оборудования не входят. Таким образом, для производственного процесса кроме вибропресса потребуется следующее оборудование:
• дробилка;
• грохот;
• бетоносмеситель.
Производство расположим на основном промплощадке шахты. Действующий породный отвал находится близко от этой площадки. Также там находится электроподстанция для подачи электроэнергии. Из шахты по водоотливном трубопровода выдается вода, поступает в отстойник, расположенный также у промплощадке. То есть, есть все условия для организации производства шлакоблока.
Также для производства нужны следующая сырье и материалы:
• цемент – марка М–400;
• порода;
• добавка «С–3»;
• вода;
• электроэнергия.
Расходы материалов зависят от густоты полученной продукции
Выводы
В результате проведения анализов сделан вывод о целесообразности внедрения технологии использования шахтной породы для производства строительной продукции с целью повышения эффективности эколого–экономической деятельности предприятия и определены три вида эффекта: экологический, социальный и экономический.
Экологический эффект заключается в том что:
– уменьшаются выбросы вредных веществ в окружающую среду в результате использования породы вместо ее размещения на территории.
Экономический эффект заключается в:
– получении прибыли с продажи стеновых блоков, произведенных из горной породы;
– уменьшении экологического налога за загрязнение окружающей среды, который уплачивается государству в бюджет.
Социальный эффект:
– предоставляются новые рабочие места;
– уменьшение заболевание населения в близи санитарно–защитной зоны породного отвала;
–улучшение условий жизни населения прилегающей территории породного отвала;
– увеличение производительности труда.
Список источников
- Экология и закон: экологическое законодательство Украины. В 2–х кн. / Под ред. В.И. Андрейцева. – М.: Юринком Интер, 1997. – 704 с.
- Андрейцев В.И. Экологическое право: курс лекций. – М.: Вентури, 1996. – 208 с.
- Комплексное освоение угольных месторождений Донецкой области / А.И. Амоша, В.И. Логвиненко, В. Гринев. – Донецк: ИЭП НАН Украины, 2007. – 176 с.
- Гирусов Э.В. Экология и экономика природопользования: учебник для вузов, – М.: Закон и право, ЮНИТИ, 1998. – 455 с.
- Гребенкин С.С. Сохранение окружающей природной среды на горнодобывающих предприятиях / С.С. Гребенкин, В.К. Костенко, Е.С. Матлак, М.Н. Шафоростова. –Донецк: «ВИК», 2009. – 505 с.
- Колотило Д.М. Экология и экономика: учебное пособие для вузов / Д.М. Колотило. – М.: Финансы, 2005. – 576 с.
- Макарова Н.С. Экономика природопользования: учебное пособие для вузов / Н.С. Макарова, Л.Д. Гармидер, Л.В. Михальчук. – К.: ЦУЛ, 2007.– 451 с.
- Концепция программы «повышение эффективности использования энергоресурсов Украины» / А.В. Пешко, Н.Г. Белопольский, Д.К Турченко – М. – 2005. – 55 с.
- Организационно–экономические инструменты эффективного недропользования / М.Н. Шафоростова / / Проблемы экологии. – Донецк: ДонНТУ, 2007. – № 1,2. – С. 139–143.
- Шафоростова М.Н. Экономические инструменты комплексного использования недр / / Вестник Донецкого горного института. – Донецк: ДонНТУ, 2008. – № 1. – С. 83–86.
- Шевчук А.В.Экономика природопользования (теория и практика). – М.: Ниа–природа, 2000.– 311 с.