Реферат по теме выпускной работы
Содержание
- Введение
- 1. Актуальность темы
- 2. Цель и задачи работы
- 3. Значение и применение продукции
- 4. Физико-химические основы производства
- 5. Описание технологической схемы и технологии производства
- Выводы
- Перечень ссылок
Введение
Принцип эмалирования известен с очень давних времен. Промышленное же эмалирование, как мы его понимаем теперь для технических целей, еще молодо по сравнению с металлургией, изготовлением стекла и керамики. Техническая суть эмалирования — связь эмали и металла — остается до настоящего времени в значительной степени неизменной, хотя количество металлов и эмалей с древних времен значительно увеличилось.
Эмалевые покрытия обладают рядом преимуществ перед другими антикоррозионными покрытиями: коррозионной стойкостью к растворам кислот, щелочей и солей при относительно высокой температуре (обычно до 300 °С, в специальных случаях до 600 °С), неизменностью эксплуатационных свойств в течение многих лет, зеркальной гладкостью поверхности, что обусловливает весьма низкий коэффициент трения, легкостью очистки, высокой гигиеничностью, стойкостью к коррозии, повышенной прочностью на истирание, стойкостью к воздействию атмосферы.
Одновременно эмалирование металлических изделий позволяет решать вопросы дизайна изделий бытового и промышленного назначения, в том числе с использованием их декоративно-художественной ручной и механизированной обработки.
1. Актуальность темы
В работе проведены исследования синтеза оптимального состава и технологии стеклоэмалевых покрытий для защиты от коррозии медных изделий различного назначения, работающих в условиях агрессивных сред и повышенных температур.
2. Цель и задачи работы
Главной целью является исследование состава и технологии стеклоэмалевых покрытий для защиты от коррозии изделий из меди.
Таким образом, сущность работы заключается в постановке и раскрытии следующих задач:
- Исследование оптимального состава и технологии стеклоэмалевых покрытий для защиты меди от высокотемпературной и газовой коррозии.
- Синтез бессвинцовых защитных стеклоэмалевых покрытий.
- Применение новых материалов в эмалировании.
3. Значение и применение продукции
Эмалирование меди и цветных металлов применяется в художественных и технических целях [1].
В художественных целях из меди и сплавов на ее основе изготавливают различные декоративные предметы быта: вазы, картины, портсигары, чаши, бижутерию, значки.
В связи с тенденциями внедрения индивидуального отопления возникает потребность в использовании водонагревателей, в которых широко применяются электронагреватели, сформированные на металлических эмалированных подложках. Так как медь имеет хорошую теплопроводность, то в качестве материала для изготовления теплообменников целесообразно ее использовать. Другим направлением в технических целях, благодаря высокой электро- и теплопроводности меди, является ее применение для проводов, индукторов, горелок, теплообменников. Эти изделия, в частности медные индукторы, должны обладать высокой прочностью, теплопроводностью, жаростойкостью, термостойкостью и коррозионной стойкостью при наличии пластичности [2]. Медные индукторы используют при закалке сложных изделий токами высокой частоты, что сопровождается их разогревом до 900 °С и значительными (≈7–10 %) потерями в виде окалины из-за окисления. Один из путей снижения этих негативных явлений — использование различных электроизолирующих покрытий: фторопластовых, кремнийорганических и других. Но фторопластовые покрытия при 200–250 °C, а кремнийорганические — при 500–600 °C частично или полностью сгорают, а слой, оставшийся на металле, становится хрупким и газопроницаемым, поэтому наиболее эффективным способом защиты меди и сплавов на ее основе является нанесение различных стеклокомпозиционных жаростойких покрытий. Такие покрытия могут быть как однослойными, так и двухслойными (с более тугоплавким подслоем) [3].
4. Физико-химические основы производства
Как известно [4], однослойные стеклоэмалевые покрытия для меди сравнительно легкоплавки и их состав обычно базируется на основе систем R2О — PbO — B2О3 — SiО2. В качестве легкоплавкого компонента в данной системе используется PbO. Однако с учетом жестких требований экологии наличие в составе разрабатываемого покрытия соединений, содержащих свинец крайне нежелательно. Поэтому не менее актуальная задача — синтез бессвинцовых защитных покрытий.
В основу разработки состава стекломатрицы для защитного термостойкого однослойного стеклоэмалевого покрытия положена бессвинцовая система R2О — CaO — BaO — B2О3 — Al2О3 — SiО2 (рис. 4.1) [4].
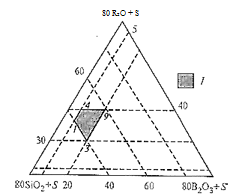
I — оптимальная область для получения эмалевого стекла, S = 7Al2О3 + 5CaO + BaO
Рисунок 4.1 — Область стеклообразования в системе R2О — CaO — BaO — B2О3 — Al2О3 — SiО2 (мас. %)
Для увеличения термостойкости и прочности сцепления использовали добавки Co2О3, Fe3О4 и MnО2, вводимые при помоле в процессе приготовления шликера. Выявлено, что оптимальными свойствами обладают эмали с добавками Co2О3, Fe3О4 и MnО2 в количествах 0,51–1,98; 0–4,5; 3,3–9,3 мас. % соответственно, составы которых лежат в области, указанной на рисунке 4.2 [4]. При введении вышеупомянутых добавок в эмалевый шликер максимальные значения прочности сцепления и термостойкости составляют 98 % и 72 цикла (20–400 °C) соответственно [4].
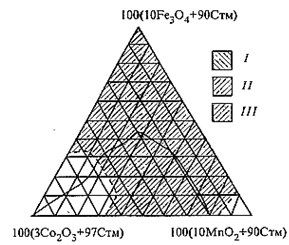
I — термостойкость, количество циклов (41–72);
II — прочность сцепления (96,5–98,0 %);
III — область оптимальных значений свойств;
Стм — стекломатрица
Рисунок 4.2 — Диаграмма оптимальных значений свойств
При разработке технологии защиты медных индукторов с применением стеклоэмалевых покрытий важно изучить сущность процесса формирования покрытия при обжиге.
При использовании эмали без добавок Co2О3, Fe3О4 и MnО2 (рис. 4.3) до момента оплавления частиц фритты при температуре 580 °С кислород воздуха, проникая сквозь пористый слой, окисляет медь в интервале температур 200–375 °C до СuО [5].
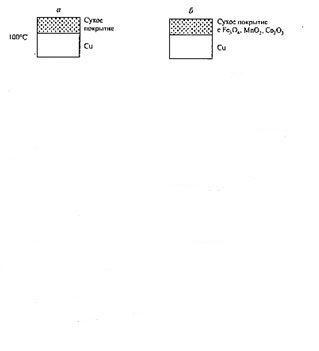
а — без добавок Co2О3, Fe3О4 и MnО2; б — с добавками
Рисунок 4.3 — Схема формирования бессвинцовой силикатной эмали на меди
(анимация: 6 кадров, 6 циклов повторения, 133 килобайтa)
При более высоких температурах в контактном слое между медью и стеклоэмалью образуется Cu2О за счет восстановления СuО до Cu2О при недостатке кислорода, а верхний слой представляет собой СuО [5]. При дальнейшем нагревании, в соответствии с изменением электропроводности покрытия, образуется расплав, который преграждает доступ кислорода к медной подложке. После появления расплава и до завершения обжига эмалевого покрытия в переходной зоне протекают процессы растворения СuО и Cu2О в близлежащем слое эмали. Кроме того, происходит дополнительные окисления меди за счет разрыва связей между ионами Сu2+ и О2− в расплаве и возникновение связи между ионами О2− и поверхностными атомами меди. Эта связь вносит свой вклад в сцепление покрытия с медью. Таким образом, в процессе обжига и после охлаждения покрытия между медью и эмалью формируется переходный слой, который в основном состоит из стеклофазы, насыщенной СuО и Cu2О, входящих в ее структурную формулу и обеспечивают прочность сцепления [5].
В результате обжига эмалевого покрытия установлено, что оно обогащается медью в окисленном, преимущественно в закисном (одновалентном) состоянии [6]. Эмалевые расплавы при обжиге — это своего рода защитные покрытия, хотя процессы взаимодействия здесь довольно интенсивные (рис. 4.4).
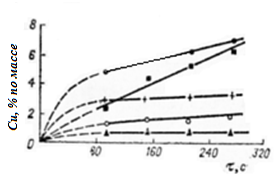
Рисунок 4.4 — Зависимость окисления меди под покрытием от времени обжига
Таким образом, можно считать, что при высоких температурах (для данной эмали) медь с подложки переходит в покрытие в окисленном состоянии или, вернее, оксиды меди, образующиеся при ее окислении на границе расплав-медь, растворяются в расплаве [6].
Исследование микроструктуры медных образцов с покрытиями после окисления при температурах ниже точки размягчения (рис. 4.5) показало, что между покрытием и медной полосой образуется слой оксидов меди, который в покрытии почти не растворяется и не нарушает его сплошности.
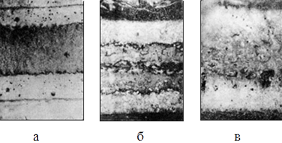
а — исходный образец; б, в — после выдержки в течение 116 и 150 ч при 700 °С
Рисунок 4.5 — Микроструктура медных образцов с покрытиями
При длительной выдержке можно полностью окислить медную полосу, после опыта слой оксидов меди остается заключенным в оболочку из неизменного покрытия (рис. 4.5, в). Целостность покрытия в данном случае не нарушается потому, что мольные объемы меди и ее оксидов достаточно близки. На рисунке 4.5 видно, что оксиды между полосой меди и покрытием образуют слой равномерной толщины [6].
В случае введения при помоле добавок Co2О3, Fe3О4 и MnО2 процесс формирования покрытия на меди носит иной характер. Присутствие активаторов сцепления в контактной зоне усиливает химическую активность взаимодействующих фаз и способствует протеканию следующих электрохимических реакций [5]:
Fe2О3 + 2Cu = 2FeO + Cu2О,
Fe2О3 + Cu = 2FeO + CuO,
Fe2О3 + Cu2О = 2FeO + 2CuO,
MnО2 + 2Cu = MnO + Cu2О,
MnО2 + Cu = MnO + CuO,
MnО2 + Cu2О = MnO + 2CuO,
Co2О3 + 2Cu = 2CoO + Cu2О,
Co2О3 + Cu = 2CoO + CuO,
Co2О3 + Cu2О = 2CoO + 2CuO.
Появляются CoO, FeO, и MnO, взаимодействующих с CuО с образованием твердых растворов (Cu, Fe)О2, (Cu, Mn)О2 и (Cu, Co)О2, которые взаимодействуют с силикатным расплавом, в частности с анионами [SiО4]4−, и образуют соответствующие силикаты
Это подтверждается электронно-микроскопическими исследованиями переходного слоя. Покрытие с добавками Co2О3, Fe3О4 и MnО2 в отличие от покрытия без добавок имеет ярко выраженный переходный слой между покрытием и медью. Кроме того, поверхность металла более распушена в результате прошлых электрохимических реакций. Поэтому при наличии добавок Co2О3, Fe3О4 и MnО2 прочность сцепления, обеспечиваемая промежуточным оксидным слоем Cu2О и СuО, связанным со стеклоэмалью, повышается вследствие образования силикатов и шпинелей, пронизывающих стеклофазу [5, 6].
5. Описание технологической схемы и технологии производства
В основу разработки состава стекломатрицы для защитного стеклоэмалевого покрытия для медных изделий нами была положена бессвинцовая система R2О — CaO — BaO — B2О3 — Al2О3 — SiО2.
Испытания проводили путем плавления шихт в огнеупорных тиглях для получения стеклоэмалевых фритт при температуре 1200–1250 °C с выдержкой в течение 0,5 ч.
Важнейшая предпосылка прочного сцепления эмали с медью — безукоризненное состояние металлической основы: гомогенная структура металла, отсутствие вредных примесей и внутренних напряжений, чистая обезжиренная поверхность металла. Подготовку поверхности медных образцов осуществляли обработкой в травильном растворе (метод блестящее травление
) [1, 7]. Нанесение эмалевого покрытия производили мокрым способом, первоначально наносился слой эмалевого шликера без тугоплавкого наполнителя. После закрепления этого слоя на поверхности медных образцов путем обжига при температуре 800 °С, наносили второй слой с огнеупорным наполнителем (Al2О3). Этот слой снова закреплялся обжигом при температуре 870 °С. Для повышения продолжительности службы заэмалированного изделия можно увеличивать количество наносимых слоев эмалевых покрытий с огнеупорным наполнителем (два и более). Обжиг эмалевого покрытия осуществлялся в лабораторной электрической муфельной печи. Схема производства стеклоэмалевого покрытия для защиты от коррозии медных изделий представлена на рисунке 5.1.
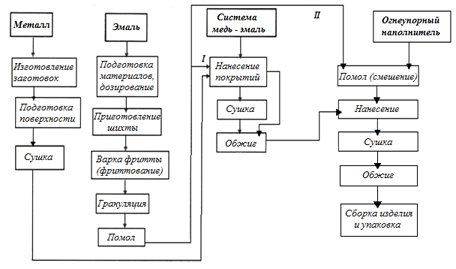
I — получение первого слоя эмалевого покрытия;
II — получение второго слоя эмалевого покрытия
Рисунок 5.1 — Схема производства стеклоэмалевого покрытия для защиты от коррозии медных изделий
При обжиге полученных эмалей на меди формировались стеклоэмалевые покрытия, в большинстве имеющие гладкую, ровную, без посторонних включений поверхность.
Выводы
Анализируя приведенный в работе материал, можно сделать следующие выводы:
- Установлено, что наиболее эффективным способом защиты от коррозии изделий из меди является применение стеклоэмалевых покрытий с повышенной термостойкостью.
- Медные изделия со стеклоэмалевыми покрытиями находят применение в качестве средств защиты металлов в течение длительного времени от окисления и разрушения в газовых средах при температурах до 600 °С и выше.
- В основу разработки состава стекломатрицы для защитного термостойкого стеклоэмалевого покрытия положены свинцовая R2О — PbO — B2О3 — SiО2 и бессвинцовая R2О — CaO — BaO — B2О3 — Al2О3 — SiО2 системы.
- Для лучшего закрепления стеклоэмалевого покрытия на медных изделиях рекомендуется использовать в качестве добавок при помоле эмалевой фритты незначительное количество оксидов Co2О3, Fe3О4 и MnО2 0,5–5 %.
- Наиболее важная предпосылка крепкого сцепления эмали с медью — безупречное состояние металлической основы. Основной этап — обработка поверхности меди методом
блестящего
травления. - Для повышения температуры использования медных изделий со стеклоэмалевыми покрытиями в состав смеси при помоле эмалевой фритты вводятся тугоплавкие материалы: кварцевый песок, глинозем, муллит и другие.
- Температура обжига стеклоэмалевых покрытий для медных изделий находится в интервале 720–800 °C для свинецсодержащих, и 800–880 °C для бессвинцовых эмалей.
Перечень ссылок
- Технология эмали и защитных покрытий / Л. Л. Брагина, А. П. Зубехин, И. Я. Белый и др. — Харьков: НТУ
ХПИ
, 2003. — 483 с. - Аппен, А. А. Температуроустойчивые неорганические покрытия / А. А. Аппен. — Л.: Химия. Ленингр. отд-ние, 1967. — 238 с.
- Эмалированние металлических изделий / Под ред. В. В. Варгина. — Л.: Машиностроение, 1972. — 494 с.
- Яценко, Е. А. Новое стеклоэмалевое бессвинцовое покрытие для меди, модифицированное добавками Fe3О4, MnО2 и Co2О3 / Е. А. Яценко, А. А. Непомящев, А. П. Зубехин // Журнал прикладной химии. — 2000. — Т. 73. Вып. 3. — С. 443–445.
- Яценко, Е. А. Защита меди от высокотемпературной коррозии / Е. А. Яценко, А. П. Зубехин, А. А. Непомящев // Стекло и керамика. — 1999. — № 9. — С. 28–30.
- Журавлев, Г. И. Химия и технология термостойких неорганических покрытий / Г. И. Журавлев. — Л.: Химия. Ленингр. отд-ние, 1975. — 199 с.
- Пат. 2149842 Рос. Федерация: МКИ C 03 C 8/02. Защитное покрытие для меди / А. П. Зубехин, Е. А. Яценко, А. А. Непомнящев; Заявл. 16.11.1998; Опубл. 27.05.2000. Бюл. № 15. — 5 с.