Реферат за темою випускної роботи
Зміст
- Введення
- 1. Актуальність роботи
- 2. Мета і завдання дослідження
- 3. Класифікація та призначення штампів
- 4. Основні стратегії фрезерування при обробці прес-форм
- 5. Перспективи та переваги впровадження сучасного ріжучого інструменту і сучасних стратегій обробки
- Висновки
- Список використаної літератури
Введення
В даний час все більша увага приділяється розвитку і вдосконалення обробки порожнин штампів зі зніманням відносно невеликих шарів металу, використання високопродуктивних методів обробки, сучасного ріжучого інструменту, і застосування прогресивних стратегій обробки, в рамках сучасного безпечного та високотехнологічного виробництва, при створенні високоякісної продукції із застосуванням новітніх технологій.
Постійний розвиток техніки на сучасному етапі вимагає використання деталей різних конфігурацій, форм, розмірів, які мають досить тонкі стінки (з метою економії матеріалу і полегшення конструкції в цілому), при цьому найбільш оптимальний спосіб отримання даних виробів це штампування. Зараз їх кількість значно збільшується в загальній масі деталей, що піддаються механічній обробці.
1. Актуальність роботи
В даний час, виробництво штампів набирає обертів. Основну роль відіграють: швидкість виконання замовлення, собівартість виготовлення штампу, висока якість виробу, і звичайно ж застосування нових віянь в обробці – що істотно підвищує презентабельність і інтерес до виробника даної продукції.
Одна з основних галузей, що розвиваються, де найбільш актуальне застосування штампів – автомобільна промисловість. Сучасний споживач автомобілів не хоче бачити відсутність дизайну і простоту ліній у вигляді прямих кутів.
На даному етапі розвитку автомобільної промисловості &ndash важливо втілити в металі роботу дизайнера. Особливо це стосується кузовних панелей. Їх виробництво неможливе без застосування високотехнологічних штампів. З кожним роком кількість вироблених автомобілів збільшується в середньому на 5-10%.
Країна | 1980 | 1990 | 2000 | 2010 | 2011 | Зростання(раз) | |
1 | Китай | 222 | 509 | 2069 | 18264 | 184418 | 82,9 |
2 | США | 8009 | 9782 | 12800 | 7761 | 8653 | 1,1 |
3 | Японія | 11042 | 13487 | 10140 | 9625 | 8398 | 0,8 |
4 | Німеччина | 3978 | 4976 | 5526 | 5906 | 6311 | 11,6 |
5 | Південна Корея | 123 | 1322 | 3144 | 4272 | 4657 | 37,9 |
6 | Індія | 114 | 362 | 801 | 3536 | 3936 | 34,5 |
7 | Бразилія | 1165 | 914 | 1681 | 3382 | 3406 | 2,9 |
8 | Мексика | 490 | 820 | 1935 | 2345 | 2680 | 5,5 |
9 | Іспанія | 1181 | 2053 | 3032 | 2388 | 2354 | 2,0 |
10 | Франція | 3378 | 3769 | 3348 | 2228 | 2295 | 0,7 |
11 | Канада | 1369 | 1947 | 2962 | 2071 | 2134 | 1,6 |
12 | Росія | 1884 | 1074 | 1202 | 1403 | 1988 | 1,05 |
13 | Іран | 161 | 45 | 141 | 1599 | 1648 | 10,2 |
14 | Великобританія | 1312 | 1565 | 1813 | 1393 | 1464 | 1,1 |
15 | Таїланд | 73 | 305 | 325 | 1644 | 1458 | 20,0 |
Причому кожні 5-6 років у кожної моделі з'являється нове покоління, кожні 2-3 роки проводиться рестайлінг – всі ці заходи сприяють передзамовленню нових штампів, із зміненою конфігурацією порожнини штампа, що в свою чергу дає безперервне завантаження виробництва штампів.
Тому високопродуктивні методи виробництва штампів є перспективними та актуальними[1, 2].
2. Мета і завдання дослідження
Метою даної роботи є: підвищення продуктивності обробки порожнин штампів у гнучкому автоматизованому виробництві, за рахунок застосування сучасного ріжучого інструменту і прогресивних стратегій обробки. Для досягнення зазначеної мети в магістерській роботі були поставлені наступні завдання:
- Провести аналіз літературних джерел і каталогів на предмет виявлення найбільш продуктивного і стійкого ріжучого інструменту.
- Розробити власні стратегії обробки і оцінити їх продуктивність з урахуванням можливого зниження обсягу відходу металу.
- Розробити методику вибору стратегій обробки і ріжучого інструменту.
- Економія коштів при впровадженні даних методик.
3. Класифікація штампів і виконувані ними функції
Штамп – інструмент, призначений для надання деталі заданої конфігурації за допомогою пластичної деформації заготовки або поділом її на частини. Для кожної деталі потрібно свій штамп[3].
Конструкція його залежить від типу заготовки (сортовий або листовий прокат), типу машин, використовуваних для штампування (молот, прес тощо), характеру виконуваних операцій, серійності виробництва і т.д.
Призначений для додання деталі заданої конфігурації за допомогою пластичної деформації заготовки або поділом її на частини. Для кожної деталі потрібно свій штамп.
Класифікують штампи за технологічними і конструктивними ознаками.
До технологічних належать: виконувана операція – вирубування, гнуття, витяжка д.; ступінь складності операцій (поєднання операцій). До конструктивних ознак належать: способи сполучення робочих частин, фіксації заготовок, способи знімання та видалення виробів.
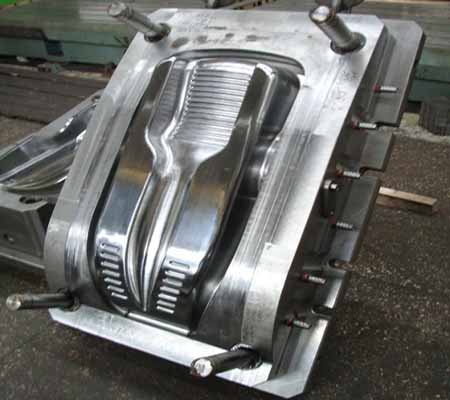
Рисунок 3.1 – Порожнина штампа
Залежно від виконуваних функцій в штампах розрізняють деталі технологічного та конструктивного призначення. Деталі технологічного призначення – це деталі, що змінюють форму заготовки, тобто матриця, пуансон і деталі, що фіксують, притискають і видаляють вироби. Деталі конструктивного призначення – ті, з допомогою яких штамп зв'язується з пресом, деталі, що забезпечують сполучення робочих частин та їх кріплення – плити, хвостовики, колонки, втулки, гвинти і штифти.
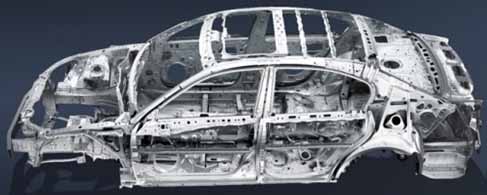
Рисунок 3.2 – Приклад використання штампованих деталей в автомобілебудуванні
До всіх штампів пред'являються вимоги, що забезпечують якість деталей, високу продуктивність, зносостійкість, зручність і безпеку роботи, простоту установки і зняття штампів. Штампи для холодного штампування виготовляються із сталей марок: У8-У13, X, Х9, 9ХС, ХГ та ін.
Найменування штампів визначають виконувані ними операції: вирубку виробляють вирубним штампами, витяжку – витяжними, згинання – згинальними і т. д. Принципова відмінність цих штампів полягає в конструкції деталей технологічного призначення – пуансона та матриці[4, 5, 6].
Робоча частина пуансона вирубного штампа відповідає формі контуру вирубки, а матриця цього штампу має отвір форми вирубки. Заготівлею для вирубки служить смуговий матеріал.
Гнуття заготовки за допомогою гибочних штампів широко застосовується при виготовленні різних виробів. Залежно від форми деталі гнуття заготовки може бути одне-, двох - і многоугловая, торцева і т. п. Гнуття металу здійснюється в результаті пружно-пластичній деформації, що протікає по-різному з кожної зі сторін згинальної заготовки. Для гнуття деталей швелерного профілю, особливо з криволінійною віссю або різної ширини, застосовуються гнучкі штампи клинового типу. Згинання труб і тонкостінних профілів теж проводиться на згинальних штампах.
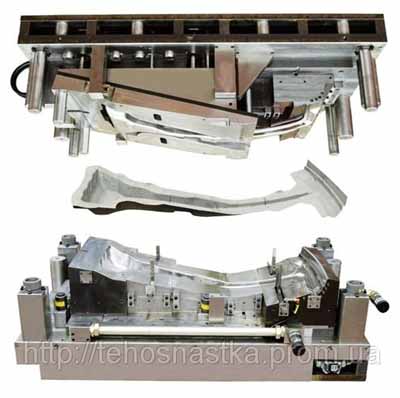
Рисунок 3.3 – Процес штампування
Згинальні штампи відрізняються великою різноманітністю конструкцій в залежності від форми штамповочной деталі і наявності Притискного пристрою. Робоча частина Пуансона має спрямовану опуклість заданої кривизни, а матриці – паралельну пуансону кривизну поверхні. Штампування згинальними штампами відбувається без зміни товщини штампованих цеталей.
Вирубкою і пробиванням изготовливают з листкового напівфабрикату деталі, використовувані для формоизменяющих операцій листового штампування. Шляхом вирубки утворюється зовнішній контур деталі, пробиванням – отвір чи паз. За якістю поверхні розділу розрізняють звичайну і чистову вирубку-пробивання. В технологічному процесі використовуються, відповідно, вирубні штампи і пробивні штампи.
Пробивні штампи в принципі не відрізняються від вирубних. Різниця лише в тому, що заготівлею для них служить не смуга, а вирубаний напівфабрикат. Складні пробивні штампи пробивають одночасно кілька отворів, в результаті виходить ажурний малюнок. Штампування деталей ювелірних виробів вимагає великої точності і мінімуму відходів дорогоцінного металу, Тому в якості розділових операцій застосовується листова вирубка і пробивання. При чистому поділі металу вирубний і пробивний штампи дають можливість вирубувати і пробивати деталі з чистою поверхнею зрізу. Для листової вирубки матриця виготовляється з закругленими і ріжучими крайками або пуансон з розмірами, що перевищують Отвір матриці. Чистова пробивання можлива при пуансоні з закругленими ріжучими крайками.
Витяжкою можна виготовити деталі з металу і матеріалів толшиной від 0,2 до 30 мм. Витяжка здійснюється на ексцентрикових, кривошипних пресах, кри-вошипношарнирных пресах простої дії, кривошипних пресах подвійної дії, гідравлічних пресах і штампах різних типів і конструкцій.
Трудомісткість процесу і спосіб витяжки залежать від матеріалу і конструктивного оформлення виготовленої деталі 5 (співвідношення розмірів, що характеризують поперечний переріз і висоту деталі, радіусів сполучення дна, стінок і фланця, конфігурації фланця).
Витяжні штампи налічують порівняно з згинальними невелике число типових конструкцій, хоча витяжка – найбільш складна операція листового штампування. Пуансон витяжного штампа має поверхня робочої частини з контуром і опуклістю заданої кривизни. На матриці штампа негативний пуансону рельєф. Не завжди витяжка може проводитися за один прохід, тому і штампи можуть бути: першої витяжки, другий витяжки, подальшою та остаточної залежно від складність витяжки.
Для скорочення проходів з метою економії часу в штампі поєднує дві операції, найчастіше витяжку з пробиванням. Такі штампи називають комбінованими.
Штампи для карбування – найпростіші та найчастіше являють собою пуансон з плоскою, гладкою робочою поверхнею і матрицю, що має поглиблений в межах контуру напівфабрикату малюнок. Виконані граверної технікою малюнки можуть мати складний рельєф, але поверхня отштампованных деталей повинна залишатися гладкою – раковин і нерівностей. Як правил карбовані штампи не утворюють сложныхузлов (блоків), пуансон такого штамп кріпиться безпосередньо до повзуна преса, а матриця – до столу.
Координатні штампи – для більш точної пробивання отворів використовується координатна пробивання на координатно-револьверних прес-штампах. Відкриті та закриті штампи оснащені спеціальними напрямними пристроями (направляючі колонки та плити), автоматично коригуючими і центруючими рух пуансона. Сучасні технології дозволяють здійснювати одночасну позиційну пробивання групи отворів на різних ділянках заготівлі. Отвори при цьому можуть мати різну форму і диаметры.Координатная пробивання отворів характеризується високою якістю деталей і продуктивністю.
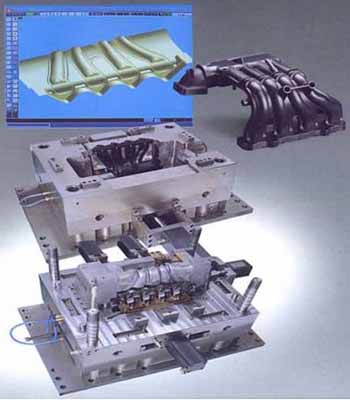
Рисунок 3.4 – Процес штампування з прив'язкою до 3D моделювання
Обрубні штампи – Процес обрубки є трудомісткою операцією і супроводжується значним шумовим ефектом. У серійному виробництві виливків з кольорових сплавів отримав широке поширення процес обрубки заток і виливків на пресах у спеціальних обрубных штампах.
Формувальні штампи – штампи для рельєфного формування майже не відрізняються від згинальних штампів з притиском заготовки. Виконуються вони, як правило, з направляючими колонками. Велике поширення мають штампи для виконання операцій відбортовки зовнішніх кромок деталей і разбортовки отворів.
Комбіновані штампи – c метою зниження трудомісткості процесів штампування, здешевлення вартості штампованих деталей і автоматизації робіт застосовується комбінована штампування , при якій ряд простих операцій виконується в одному штампі суміщеного або послідовної дії. Застосовуються також штампи комбіновані сумісно – послідовної дії. Виготовлення деталі в штампах поєднаної дії відбувається за один хід преса, без переміщення заготовки. Переходи (операції) розміщуються в напрямку переміщення – повзуна преса, і заготівля деформується послідовно принаймні переміщення повзуна (а отже , і верхньої частини штампу) вниз. Штампування виконується як з окремої заготівлі, так і зі смуги (стрічки). Зазвичай штампи поєднаної дії використовуються для виготовлення деталей, що вимагають від 2 до 4 операцій при товщині матеріалу до 5 мм. Можливість суміщення залежить від товщини штампувало матеріалу і розмірів деталі, так як при певних співвідношеннях зовнішнього та внутрішнього контурів деталі товщина стінок у пуансонів і матриць може вийти занадто малою, що ускладнить їх виготовлення і термообробку[7, 8, 9].
Штампи послідовної дії – існують наступні види штампування: простого, послідовного і поєднаної дії. Штамп послідовної дії виконує операції в різних позиціях по напрямку подачі, так що для чергової операції заготівля переміщається на крок подачі. Штамп поєднаної дії всі операції виконує в одній позиції без переміщення заготовки в напрямку подачі. Штамп простої дії – це штамповка, як правило, простих за формою деталей або окремих елементів деталі.
Послідовні штампи є більш продуктивними і менш складними у виготовленні, ніж штампи поєднаної дії. Це дозволяє отримувати складну конфігурацію деталей за рахунок рознесення операцій пробивки внутрішніх отворів і вирубки зовнішнього контуру на різні кроки чи обрубки контуру окремими пуансонами.
Необхідні параметри, що враховуються при виробництві порожнин штампів:
- Чіткий креслення штампуемой деталі, марка матеріалу, допуски на розміри, ширина смуги (стрічки).
- Модель преса і його характеристика (для встановлення штампа на прес).
- Тип подачі смуги (стрічки).
- Конструкція штампа (штамп з жорстким знімачем, з верхнім притиском, поєднаної дії).
- Чи дозволяється застосування клею для кріплення пуансонів та інших деталей.
4. Основні стратегії фрезерування при обробці прес-форм
Навіть найкращі інструменти не зможуть розкрити свій потенціал, якщо вони не використовуються в зв'язці з певними методиками. Нижче описано кілька ключових стратегій фрезерування: товста стружка, торцеве фрезерування з круговою подачею, радіальне переміщення фрези під кутом до оброблюваної поверхні, гвинтова інтерполяція, позиціонування фрези, зустрічне / попутне фрезерування і безперервне врізання фрези.
Правильний ріжучий ефект і стружкообразования дозволяють заощадити час, гроші і забезпечити стабільний процес роботи.
Ключові стратегії фрезерування при обробці прес-форм
Часто кожен з нас використовує будь-який доступний інструмент для виконання базової операції фрезерування і при цьому ми впевнені, що зможемо обійтися без оптимізації процесу. Також нам знайомі результати такого підходу: погана якість і жахливий звук, який виникає при обробці кутів. Крім того, універсальна "панацея" у вигляді відключення подачі лише маскує реальні проблеми і мінімізує продуктивність.
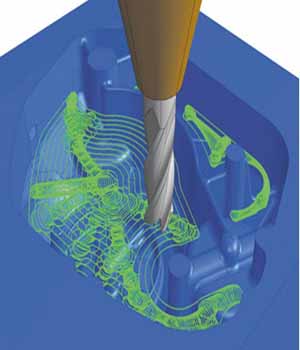
Рисунок 4.1 – Процес обробки порожнини штампа
Пряме врізання фрези
При врізання безпосередньо процес обробки починає супроводжуватися вібрацією. Ця вібрація веде до скорочення терміну служби інструменту, поганої якості поверхні і необхідності постійно контролювати процес, так як спрогнозувати тривалість терміну служби інструменту стає проблематично.
Рисунок 4.2 показує наявність товстої стружки при відведенні фрези від оброблюваної поверхні, коли та обертається, внаслідок чого на інструмент виявляється максимальна навантаження. Потім це зусилля дуже швидко зникає, що викликає невеликі коливання фрези, коли чергова вставна ріжуча пластина в державка для ріжучого інструменту включається в процес обробки, що викликає збільшення зусилля на інструмент разом з навантаженням на підшипники шпинделя машини.
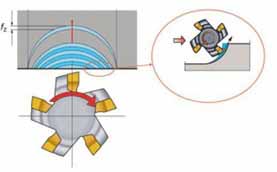
Рисунок 4.2 – Початок обробки деталі при прямому врізанні фрези – товста стружка на виході
Початок обробки деталі при прямому врізання фрези – товста стружка на виході.
Ще до того, як фреза повністю увійде в заготовку, на виході з'являється товста стружка, викликає вібрацію, пошкодження ріжучих кромок і скорочення терміну служби інструменту.
Все це відбувається на дуже високій швидкості, приводячи до виникнення деренчливий звук, який зберігається, поки центральна осьова лінія фрези не пройде край оброблюваної форми. Коли фреза переміститься в цю позицію, на виході природним чином з'явиться тонка стружка. Ви можете легко побачити різницю в товщині ліній в найдальшій точці на правій стороні.
Торцеве фрезерування з круговою подачею
Примітно, що при використанні торцевого фрезерування з круговою подачею (див. Рисунок 4.3) тонка стружка буде залишати фрезу з самого початку процесу обробки, незалежно від стану центральної осьової лінії фрези. У цьому випадку усуваються коливання інструменту з-за тиску, а також виникнення/ослаблення навантаження на підшипники шпинделя машини[10, 11].
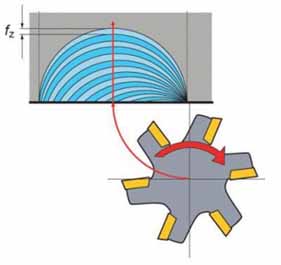
Рисунок 4.3 – Початок обробки деталі при круговому врізанні
Кругове врізання – позволяет добиться минимальной толщины стружки на выходе, снижая вибрацию и продлевая срок службы инструмента.
Таким чином, техніка торцевого фрезерування з круговою подачею не тільки усуває проблему вібрації, збільшуючи термін служби інструменту і продуктивність процесу обробки, але і знижує знос підшипників шпинделя верстата, а також робить процес обробки більш передбачуваним. Така передбачуваність дозволяє оператору машини залишати робоче місце з повною впевненістю в тому, що після повернення не виникне сюрпризів. Отримувати тонку стружку на виході також дозволяє і радіальне переміщення фрези під кутом до оброблюваної поверхні. Якщо фреза починає процес обробки під кутом 20°-30° до оброблюваної поверхні, виникає той же самий ефект, як і при торцевому фрезеруванні з круговою подачею. Цей варіант можливий при використанні спрощеного програмування машини.
Метод гвинтовий інтерполяції
Метод гвинтовий інтерполяції (дв. Рисунок 4.4), в свою чергу, використовується для обробки виїмок або створення отворів у формі за допомогою фрези.
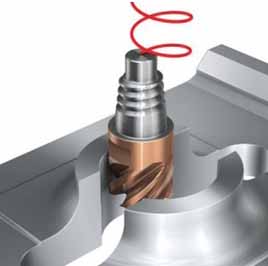
Рисунок 4.4 – Кругове врізання при круговому інтерполяцію.
Кругове врізання при здійсненні колового інтерполювання дозволяє добитися мінімальної товщини стружки на виході і мінімізувати кути врізання, знизивши вібрацію і отримавши максимальну продуктивність.
Робота фрези починається з дій над формою, після чого вона переміщується по круговій траєкторії і починає заглиблюватися у форму, ініціюючи процес обробки. Отримати тонку стружку при виконанні цієї операції трохи легше, тому що необхідно лише одне додаткове кругове переміщення фрези над формою – фреза просто почне роботу трохи вище і буде переміщатися згідно круговому шаблоном, заглиблюючись у поверхня самої форми. Багато хто не виконують цей додатковий крок і стають свідками того ж негативного ефекту вібрації, скороченого терміну служби інструменту і т. д.
Торцеве фрезерування з глибоким врізанням
Вам доведеться обзавестися пристойним досвідом в області позиціонування фрези над формою, щоб досягти потрібної точності. При торцевому фрезеруванні з глибоким врізанням, 70-відсоткове врізання є оптимальним. Це дає твердосплавним пластин час на стиск пропорційно зусиллю на інструмент, і тонка стружка на виході дозволяє поступово зменшувати це стиснення. Знову ж все це відбувається дуже швидко, але твердосплавні пластини не дуже добре одноразово знімають тиск товстої стружки – різка зміна навантаження від стиснення до розтягування стає причиною відколювання карбіду на виході. Тоді як при неглибокому врізання, яке застосовується головним чином при контурної обробки, врізання на 25 % від діаметру фрези є оптимальним з точки зору терміну служби інструменту і продуктивності.
Важливо мати на увазі можливі наслідки появи товстої стружки на вихід з положення фрези над формою. Більшість виробників центруют фрезу над центром оброблюваної деталі, і на виході виникає товста стружка. Замість цього процес повинен бути оптимізований для забезпечення найменшої товщини стружки.
Попутне і зустрічне фрезерування
Також важливо розрізняти фрезерування по подачі (попутне фрезерування) і фрезерування проти подачі (зустрічне фрезерування). Обидва методу співвідносяться з позиціонуванням фрези над формою. При фрезеруванні проти подачі фреза зміщена праворуч, що знову-таки призводить до появи товстої стружки на виході. При здійсненні проходу з фрезеруванням з подачі фреза зміщена ліворуч, і стружка на виході виходить тонкою. Цей процес називається фрезеруванням по подачі, тому що ріжучий ефект досягається за рахунок обертання фрези в одному напрямку з подачею матеріалу. При фрезеруванні проти подачі фреза обмежена стискають силами[12, 13].
Безперервне врізання фрези
Безперервне врізання фрези є ще одним методом виходу на оптимізовану продуктивність. Слід зазначити, що ширина проходу (ширина оброблюваного матеріалу) залишається незмінною протягом усього процесу обробки. Найбільш часто при виготовленні моделей, штампів і пресз форм фреза рухається навколо форми, надаючи останній різні особливості. Подібний результат повинен досягатися з допомогою переміщення фрези по запрограмованому радіусу, а не низки прямолінійних проходів (див. Рисунок 4.5).
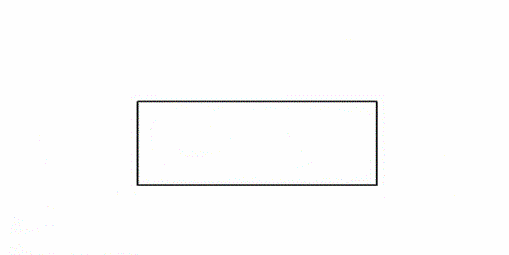
Рисунок 4.5 – Схема різання при торцевому фрезеруванні. (Анімація: 16 кадрів, 0.5 сек затримка, розмір 80 Кб, необмежене число повтров, програма - Easy GIF Animator)
Фреза повинна безперервно взаємодіяти з заготівлею. Багато виробників використовують прямолінійні проходи, але це не дуже хороша ситуація, тому що подібні дії навантажують і розвантажують шпиндель, ініціюють вібрацію, скорочують термін служби інструменту і значно знижують загальну продуктивність верстата. Коли торцеве фрезерування з круговою подачею використовується для початку обробки компонента, і фреза переміщається по певному радіусу при досягненні кутових частин заготовки, ми можемо отримати тонку стружку на виході, зберегти рівень врізання постійним (навіть по кутах) і забезпечити стійкість.
Стружкотворення і позиціонування фрези
Обробка над пазами або отворами зробить процес небезпечним, тому проведіть повторне позиціонування фрези і доробіть програму, щоб на виході постійно була тонка стружка. Знову ж таки, багато виробники вносять у програму роботи фрези проходження безпосередньо над порожнинами (див. Рисунок 4.6, верхня частина). Подібний підхід не тільки ініціює вібрації і нестійкість, які обговорювалися раніше, але і здійснює фрезерування проти подачі і фрезерування по подачі на одному і тому ж шляху переміщення фрези, посилюючи небажані ефекти. Замість цього виробники повинні використовувати шляху праворуч. Необхідно провести круговий врізання, підтримуючи неперервність процесу – це дозволить отримати тонку стружку на виході (див. Рисунок 4.6, нижня частина).
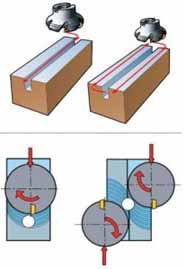
Рисунок 4.6 – Стружкообразование і позиціонування фрези
Обробка над прорізами або отворами, присутніми в компоненті, зробить процес небезпечним. Повторне позиціонування фрези і обробка з огинанням цих порожнин призведе до збільшення безпеки і дозволить вийти на максимальну продуктивність.
Обробка прес-форм, моделей, штампів: профілювання
При виготовленні моделей, штампів і прес-форм проводиться значний обсяг робіт по профілюванню, що дозволяє надати формованому компоненту необхідні особливості. Все ті ж техніки торцевого фрезерування з круговою подачею і безперервного врізання шляхом переміщення фрези по запрограмованому радіусу дозволяють отримати тонку стружку на виході, що призводить до максимальної продуктивності (див. Рисунок 4.7).
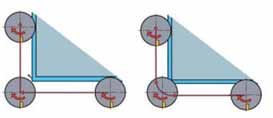
Рисунок 4.7 – Траєкторія різання при контурної обробки зовнішніх кутів
Виготовлення моделей, штампів і прес-форм передбачає обробку безлічі внутрішніх кутів, і ніхто вам не скаже, чи буде фреза вібрувати при досягненні того чи іншого кута. Щоб виключити проблеми, дуга врізання при наближенні до внутрішнього кута повинна бути близько 50 градусів. Однак коли фреза входить в кут, ця дуга врізання збільшується до 140 градусів з матеріалу, що виникає перед інструментом в тих областях, які ще не були оброблені. Багато виробники передбачають 90-градусне зміна напрямку, щоб почати обробку іншої області форми. Це викликає вібрацію, тому що дуга врізання перевищує 90 градусів і навантаження на фрезу знижується.
Це означає, що запрограмоване зміна напрямку фактично змушує машину повністю зупинити рух фрези, в результаті чого тиск на інструмент втрачається і починається вібрація. Потім фреза починає переміщатися в іншому напрямку, після чого тиск і навантаження на інструмент знову зростають. Під час підвищення зусилля на інструмент і навантаження на шпиндель, фреза буде продовжувати вібрувати, поки рівень навантаження не стане достатньо високим, щоб стабілізувати шпиндель. Найбільш коректним в даному випадку буде використання запрограмованих радіусів, щоб підтримувати безперервне врізання, утримувати зусилля на шпиндель і фрезу, а також уникати зупинки машини (див. Рисунок 4.8).
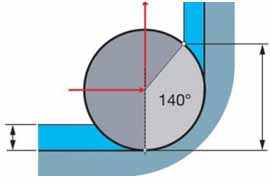
Рисунок 4.8 – Траєкторія різання внутрішніх кутів – кінцеве подрібнення
Обробка кутів часто ініціює вібрацію; коректне програмування обходу кутів дозволить домогтися збільшення терміну служби інструменту і призведе до припливу даних для розрахунку режимів різання на верстаті з ЧПУ.
5. Перспективи та переваги впровадження сучасного ріжучого інструменту і сучасних стратегій обробки
Правильний вибір ріжучого інструменту відіграє ключову роль у підвищенні продуктивності при виробництві штампів. Акцент робиться на імпортний ріжучий інструмент з оптимальною геометрією різальної частини та різноманітністю типів і конфігурацій інструменту.
- Гарантована стійкість імпортного інструменту в 4 рази перевищує ріжучий інструмент, виконаний по ГОСТам.
- Поліпшення можливостей стружколомания, за рахунок складних форм змінних твердосплавних пластин і широкі можливості їх заміни.
- Широта можливостей при підводі СОТС безпосередньо в зону різання.
- Гарантія на інструмент від виробника, при виконанні норм використання, запропоновані заводом-виготовлювачем.
- При виконанні всіх пунктів, інструментальна база є гнучкою і легко підлаштовується під обробку інших типорозмірів штампів, істотно скорочуючи час підготовки і обробки виробів.
- При цьому, імпортний інструмент дає кращу якість обробленої поверхні, ніж вітчизняний аналог, скорочуючи кількість переходів при обробці в 1.5 рази.
- Застосування інструменту зі змінними неперетачиваемыми пластинами тягне за собою здешевлення виробництва штампів, за рахунок низького зносу остова інструменту і можливостями утилізації вторсировини у вигляді твердосплавних пластин.
- Оптимізація стратегії обробки дозволить істотно збільшити продуктивність і більш ніж в 1.5 рази скоротити час отримання одиниці продукції.
- Здійсненна вилучення металу у вигляді об'ємних тіл, натомість пошарового знімання у вигляді стружки.
Висновки
В даній роботі проведено аналіз використовуваного ріжучого інструменту, оптимізованих і передових стратегій обробки і зроблено висновок:
При виконанні роботи пунктів буде досягнута головна мета – підвищення продуктивності, скорочення часу обробки і суттєве скорочення витрат на виробництво.
При успішному впровадженні даного комплексу дій – на виході отримаємо високотехнологічне і високоорганізоване виробництво, економічно вигідну продукцію і для замовника, і для самого виробництва, з дотриманням усіх сучасних норм і вимог до продукції, в тому числі і екологічних.
При написанні даного реферату магістерська робота ще не завершена. Остаточне завершення: січень 2014 року. Повний текст роботи і матеріали по темі можуть бути отримані у автора або його керівника після зазначеної дати.
Список використаної літератури
- Кожевников Д. В., Гречишников В. А., Кирсанов С. В., Кокарев В. И., Схиртладзе А. Г. Под редакцией С. В. Кирсанова. Режущий инструмент: Учебник для вузов- 2-е изд. доп. – М.: Машиностроение, 2005. – 528 с: ил.
- Терновой Ю.Ф., Канюк В.И., Терехов В.Н. Справочник по инструментальным сталям. 2-е издание – Х.: «Металлика», 2009. – 242 с.
- Соловцов, Л.Г. Степанский, В.Н. Субич, В.А. Ульянов, З.Г. Унанян, А.Е. Феофанова, А.П. Шляхин, С.С. Яковлев. Ковка и штамповка: справочник. В 4 т.
- Режущий инструмент в производстве штампов и пресс-форм. Краткое справочное руководство. ISCAR IMC Group.
- Автоматизация проектно-конструкторских работ и технологической подготовки производства в машиностроении / Под ред. О.И. Семепкова. В 2-х т. Том 2. Минск. Вышейшая школа. 1977. 334 с.
- Акастелова Н.А., Вдовий С.И., Щупляк Г.И. Расчёт на ЭВМ раскроя листового материала при вырубке деталей из полосы // Кузнечно-штамповочное производство. 1983. № 4. С. 18—19.
- Арефин Ю.И., Швайнштейн И.С. Прогрессивная штамповочная оснастка. Л., Лениздат, 1982. 111 с.
- Динер И.Г., Брун В.Я., Бирин Б.В. Конструкции твердосплавных разделительных штампов. Рига, ЛатНИИНТИ, 1982. 24 с.
- Динер И.Г., Брун В.Я., Стеблюк В.И. Проектирование и изготовление твердосплавных штампов // Кузнечно-штамповочное производство. М., Машиностроение, 1979. № 8. С. 28—30.
- Дурандин М.М., Рымзин А.П., Шихов Н.А. Штампы для холодной штамповки мелких деталей. Альбом конструкций и схем. М., Машиностроение. 1978. 108 с.
- Системы автоматизированного проектирования: Типовые элементы, методы и процессы / Д.А. Аветисян, И.Л. Башмаков, В.И. Геминтерн и др. М., Изд-во стандартов. 1985. 180 с.
- Справочник по заготовлению и ремонту штампов и пресс-форм / В.С. Мендельсон, Л.И. Рудман, М.Г. Аскинази и др. Киев, Техника. 1979. 176 с.
- Стеблюк В.И., Марченко В.Л., Белов В.В. Технология листовой штамповки. Курсовое проектирование. Киев, Вища школа, 1983. 280 с.