Реферат по теме выпускной работы
Содержание
- Введение
- 1. Актуальность темы
- 2. Цель и задачи исследования
- 3. Классификация и предназначение штампов
- 4. Основные стратегии фрезерования при обработке пресс-форм
- 5. Перспективы и преимущества внедрения современного режущего инструмента и современных стратегий обработки
- Выводы
- Список источников
Введение
В настоящее время все большее внимание уделяется развитию и совершенствованию обработки полостей штампов со съемом относительно небольших слоев металла, использования высокопроизводительных методов обработки, современного режущего инструмента, и применению прогрессивных стратегий обработки, в рамках современного, безопасного и высокотехнологичного производства, при создании высококачественной продукции с применением новейших технологий.
Постоянное развитие техники на современном этапе требует использования деталей различных конфигураций, форм, размеров, которые имеют достаточно тонкие стенки (с целью экономии материала и облегчения конструкции в целом), при этом наиболее оптимальный способ получения данных изделий это штамповка. Сейчас их количество значительно увеличивается в общей массе деталей, подвергающихся механической обработке.
1. Актуальность темы
В настоящее время, производство штампов набирает обороты. Основную роль играют: скорость выполнения заказа, себестоимость изготовления штампа, высокое качество изделия, и конечно же применение новых веяний в обработке – что существенно повышает презентабельность и интерес к производителю данной продукции.
Одна из основных, развивающихся отраслей, где наиболее актуально применение штампов – автомобильная промышленность. Современный потребитель автомобилей не хочет видеть отсутствие дизайна и простоту линий в виде прямых углов.
На данном этапе развития автомобильной промышленности – важно воплотить в металле работу дизайнера. Особенно это касается кузовных панелей. Их производство невозможно без применения высокотехнологичных штампов. С каждым годом количество произведенных автомобилей увеличивается в среднем на 5-10%.
Страна | 1980 | 1990 | 2000 | 2010 | 2011 | Рост(раз) | |
1 | Китай | 222 | 509 | 2069 | 18264 | 184418 | 82,9 |
2 | США | 8009 | 9782 | 12800 | 7761 | 8653 | 1,1 |
3 | Япония | 11042 | 13487 | 10140 | 9625 | 8398 | 0,8 |
4 | Германия | 3978 | 4976 | 5526 | 5906 | 6311 | 11,6 |
5 | Южная Корея | 123 | 1322 | 3144 | 4272 | 4657 | 37,9 |
6 | Индия | 114 | 362 | 801 | 3536 | 3936 | 34,5 |
7 | Бразилия | 1165 | 914 | 1681 | 3382 | 3406 | 2,9 |
8 | Мексика | 490 | 820 | 1935 | 2345 | 2680 | 5,5 |
9 | Испания | 1181 | 2053 | 3032 | 2388 | 2354 | 2,0 |
10 | Франция | 3378 | 3769 | 3348 | 2228 | 2295 | 0,7 |
11 | Канада | 1369 | 1947 | 2962 | 2071 | 2134 | 1,6 |
12 | Россия | 1884 | 1074 | 1202 | 1403 | 1988 | 1,05 |
13 | Иран | 161 | 45 | 141 | 1599 | 1648 | 10,2 |
14 | Великобритания | 1312 | 1565 | 1813 | 1393 | 1464 | 1,1 |
15 | Таиланд | 73 | 305 | 325 | 1644 | 1458 | 20,0 |
Причем каждые 5-6 лет у каждой модели появляется новое поколение, каждые 2-3 года производится рестайлинг – все эти меры способствуют предзаказу новых штампов, с измененной конфигурацией полости штампа, что в свою очередь дает непрерывную загрузку производства штампов.
Поэтому высокопроизводительные методы производства штампов являются перспективными и актуальными[1, 2].
2. Цель и задачи исследования, планируемые результаты
Целью данной работы является: повышение производительности обработки полостей штампов в гибком автоматизированном производстве, за счет применения современного режущего инструмента и прогрессивных стратегий обработки. Для достижения указанной цели в магистерской работе были поставлены следующие задачи:
- Провести анализ литературных источников и каталогов на предмет выявления наиболее производительного и стойкого режущего инструмента.
- Разработать собственные стратегии обработки и оценить их производительность с учетом возможного снижения объема отхода металла.
- Разработать методику выбора стратегий обработки и режущего инструмента.
- Экономия средств при внедрении данных методик.
3. Классификация и предназначение штампов
Штамп – инструмент, предназначенный для придания детали заданной конфигурации посредством пластической деформации заготовки или разделением её на части. Для каждой детали требуется свой штамп[3].
Конструкция его зависит от типа заготовки (сортовой или листовой прокат), типа машин, используемых для штамповки (молот, пресс и т.п.), характера выполняемых операций, серийности производства и т.д.
Предназначен для придания детали заданной конфигурации посредством пластической деформации заготовки или разделением её на части. Для каждой детали требуется свой штамп.
Классифицируют штампы по технологическим и конструктивным признакам.
К технологическим относятся: выполняемая операция – вырубка, гибка, вытяжка д.; степень сложности операций (совмещение операций). К конструктивным признакам относятся: способы сопряжения рабочих частей, фиксации заготовок, способы съема и удаления изделий.
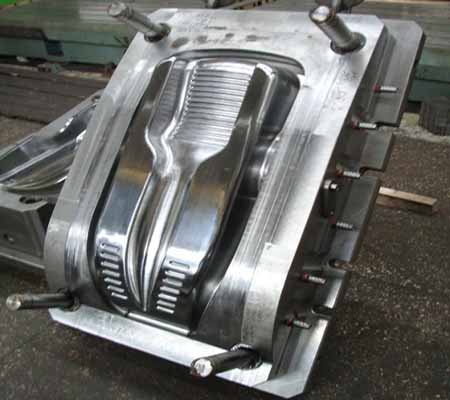
Рисунок 3.1 – Полость штампа
В зависимости от выполняемых функции в штампах различают детали технологического и конструктивного назначения. Детали технологического назначения – это детали, изменяющие форму заготовки, т.е. матрица, пуансон и детали, фиксирующие, прижимающие и удаляющие изделия. Детали конструктивного назначения – те, с помощью которых штамп связывается с прессом, детали, обеспечивающие сопряжение рабочих частей и их крепление, – плиты, хвостовики, колонки, втулки, болты и штифты.
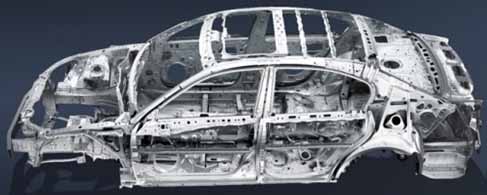
Рисунок 3.2 – Пример использования штампованных деталей в автомобилестроении
Ко всем штампам предъявляются требования, обеспечивающие качество деталей, высокую производительность, износостойкость, удобство и безопасность работы, простоту установки и снятия штампов. Штампы для холодной штамповки изготовляются из сталей марок: У8—У13, X, Х9, 9ХС, ХГ и др.
Наименование штампов определяют выполняемые ими операции: вырубку производят вырубными штампами, вытяжку – вытяжными, гибку – гибочными и т. д. Принципиальное различие этих штампов заключается в конструкции деталей технологического назначения – пуансона и матрицы[4, 5, 6].
Рабочая часть пуансона вырубного штампа соответствует форме контура вырубки, а матрица этого штампа имеет отверстие формы вырубки. Заготовкой для вырубки служит полосовой материал.
Гибка заготовки с помощью гибочных штампов широко применяется при изготовлении различных изделий. В зависимости от формы детали гибка заготовки может быть одно-, двух- и многоугловая, торцевая и т. п. Гибка металла осуществляется в результате упругопластической деформации, протекающей различно с каждой из сторон изгибаемой заготовки. Для гибки деталей швеллерного профиля, особенно с криволинейной осью или разной ширины, применяются гибочные штампы клинового типа. Гибка труб и тонкостенных профилей тоже производится на гибочных штампах.
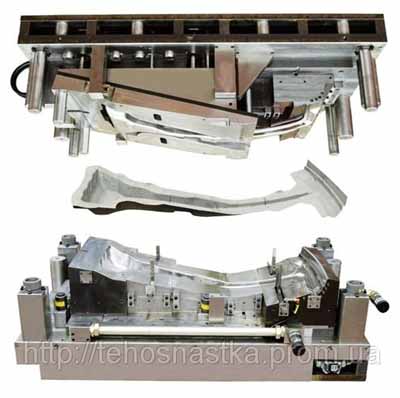
Рисунок 3.3 – Процесс штамповки
Гибочные штампы отличаются большим разнообразием конструкций в зависимости от формы штамповочной детали и наличия Прижимного устройства. Рабочая часть Пуансона имеет направленную выпуклость заданной кривизны, а матрицы – параллельную пуансону кривизну поверхности. Штамповка гибочными штампами происходит без изменения толщины штампуемых цеталей.
Вырубкой и пробивкой изготовливают из листового полуфабриката детали, используемые для формоизменяющих операций листовой штамповки. Путем вырубки образуется внешний контур детали, пробивкой – отверстие или паз. По качеству поверхности раздела различают обычную и чистовую вырубку-пробивку. В технологическом процессе используются, соответственно, вырубные штампы и пробивные штампы.
Пробивные штампы в принципе не отличаются от вырубных. Разница лишь в том, что заготовкой для них служит не полоса, а вырубленный полуфабрикат. Сложные пробивные штампы пробивают одновременно несколько отверстий, в результате получается ажурный рисунок. Штамповка деталей ювелирных изделий требует большой точности и минимума отходов драгоценного металла, Поэтому в качестве разделительных операций применяется листовая вырубка и пробивка. При чистом разделении металла вырубной и пробивной штампы дают возможность вырубать и пробивать детали с чистой поверхностью среза. Для листовой вырубки матрица изготовляется с закругленными и режущими кромками или пуансон с размерами, превышающими Отверстие матрицы. Чистовая пробивка возможна при пуансоне с закругленными режущими кромками.
Вытяжкой можно изготовить детали из металла и материалов толшиной от 0,2 до 30 мм. Вытяжка производится на эксцентриковых, кривошипных прессах, кри-вошипношарнирных прессах простого действия, кривошипных прессах двойного действия, гидравлических пресах и штампах различных типов и конструкций.
Трудоемкость процесса и способ вытяжки зависят от материала и конструктивного оформления изготовляемой детали 5 (соотношения размеров, характеризующих поперечное сечение и высоту детали, радиусов сопряжения дна, стенок и фланца, конфигурации фланца).
Вытяжные штампы насчитывают по сравнению с гибочными небольшое число типовых конструкций, хотя вытяжка – наиболее сложная операция листовой штамповки. Пуансон вытяжного штампа имеет поверхность рабочей части с контуром и выпуклостью заданной кривизны. На матрице штампа негативный пуансону рельеф. Не всегда вытяжка может производиться за один проход, поэтому и штампы могут быть: первой вытяжки, второй вытяжки, последующей и окончательной в зависимости от сложность вытяжки.
Для сокращения проходов с цель экономии времени в штампе совмещает две операции, чаще всего вытяжку с пробивкой. Такие штампы называют комбинированными.
Штампы для чеканки – самые простые и чаще всего представляют собой пуансон с плоской, гладкой рабочей поверхностью и матрицу, имеющую углубленный в пределах контура полуфабриката рисунок. Выполненные граверной техникой рисунки могут иметь сложный рельеф, но поверхность отштампованных деталей должна оставаться гладкой – раковин и неровностей. Как правил чеканные штампы не образовывают сложныхузлов (блоков), пуансон такого штамп крепится непосредственно к ползуну пресса, а матрица – к столу.
Координатные штампы – для более точной пробивки отверстий используется координатная пробивка на координатно-револьверных пресс-штампах. Открытые и закрытые штампы оснащены специальными направляющими устройствами (направляющие колонки и плиты), автоматически корректирующими и центрирующими движение пуансона. Современные технологии позволяют осуществлять одновременную позиционную пробивку группы отверстий на различных участках заготовки. Отверстия при этом могут иметь различную форму и диаметры.Координатная пробивка отверстий характеризуется высоким качеством деталей и производительностью.
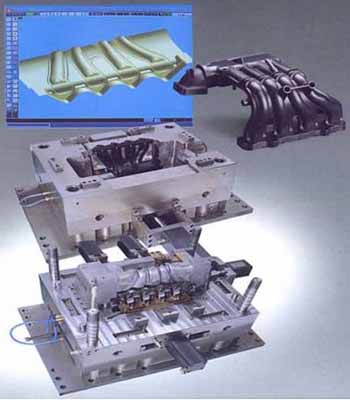
Рисунок 3.4 – Процесс штамповки с привязкой к 3D моделированию
Обрубные штампы – процесс обрубки является трудоемкой операцией и сопровождается значительным шумовым эффектом. В серийном производстве отливок из цветных сплавов получил широкое распространение процесс обрубки заливов и отливок на прессах в специальных обрубных штампах.
Формовочные штампы – штампы для рельефной формовки почти не отличаются от гибочных штампов с прижимом заготовки. Выполняются они, как правило, с направляющими колонками. Большое распространение имеют штампы для выполнения операций отбортовки наружных кромок деталей и разбортовки отверстий.
Комбинированные штампы – c целью снижения трудоемкости процессов штамповки, удешевления стоимости штампованных деталей и автоматизации работ применяется комбинированная штамповка, при которой ряд простых операций выполняется в одном штампе совмещенного или последовательного действия. Применяются также штампы комбинированные совмещенно-последовательного действия. Изготовление детали в штампах совмещенного действия происходит за один ход пресса, без перемещения заготовки. Переходы (операции) размещаются в направлении перемещения-ползуна пресса, и заготовка деформируется последовательно по мере перемещения ползуна (а следовательно, и верхней части штампа) вниз. Штамповка выполняется как из отдельной заготовки, так и из полосы (ленты). Обычно штампы совмещенного действия используются для изготовления деталей, требующих от 2 до 4 операций при толщине материала до 5 мм. Возможность совмещения зависит от толщины штампуемого материала и размеров детали, так как при определенных соотношениях наружного и внутреннего контуров детали толщина стенок у пуансонов и матриц может получиться слишком малой, что затруднит их изготовление и термообработку[7, 8, 9].
Штампы последовательного действия – cуществуют следующие виды штамповки: простого, последовательного и совмещённого действия. Штамп последовательного действия выполняет операции в различных позициях по направлению подачи, так что для очередной операции заготовка перемещается на шаг подачи.Штамп совмещённого действия все операции выполняет в одной позиции без перемещения заготовки в направлении подачи. Штамп простого действия – это штамповка, как правило, простых по форме деталей или отдельных элементов детали.
Последовательные штампы являются более производительными и менее сложными в изготовлении, чем штампы совмещенного действия. Это позволяет получать сложную конфигурацию деталей за счет разнесения операций пробивки внутренних отверстий и вырубки наружного контура на разные шаги или обрубки контура отдельными пуансонами.
Необходимые параметры, учитываемые при производстве полостей штампов:
- Четкий чертеж штампуемой детали, марка материала, допуски на размеры, ширина полосы (ленты).
- Модель пресса и его характеристика (для установки штампа на пресс).
- Тип подачи полосы (ленты).
- Конструкция штампа (штамп с жестким съемником, с верхним прижимом, совмещенного действия).
- Разрешается ли применение клея для крепления пуансонов и других деталей.
4. Основные стратегии фрезерования при обработке пресс-форм
Даже самые лучшие инструменты не смогут раскрыть свой потенциал, если они не используются в связке с определенными методиками. Ниже описано несколько ключевых стратегий фрезерования: толстая стружка, торцовое фрезерование с круговой подачей, радиальное перемещение фрезы под углом к обрабатываемой поверхности, винтовая интерполяция, позиционирование фрезы, встречное/попутное фрезерование и непрерывное врезание фрезы.
Правильный режущий эффект и стружкообразование позволяют сэкономить время, деньги и обеспечить стабильный процесс работы.
Ключевые стратегии фрезерования при обработке пресс-форм
Зачастую каждый из нас использует любой доступный инструмент для выполнения базовой операции фрезерования и при этом мы уверены, что сможем обойтись без оптимизации процесса. Также нам знакомы результаты подобного подхода: плохое качество и ужасный звук, возникающий при обработке углов. Кроме того, универсальная “панацея” в виде отключения подачи лишь только маскирует реальные проблемы и минимизирует производительность.
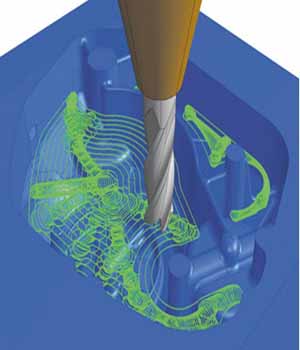
Рисунок 4.1 – Процесс обработки полости штампа
Прямое врезание фрезы
При врезании напрямую процесс обработки начинает сопровождаться вибрацией. Эта вибрация ведет к сокращению срока службы инструмента, плохому качеству поверхности и необходимости постоянно контролировать процесс, так как спрогнозировать длительность срока службы инструмента становится проблематично.
Рисунок 4.2 показывает наличие толстой стружки при отводе фрезы от обрабатываемой поверхности, когда та вращается, вследствие чего на инструмент оказывается максимальная нагрузка. Затем это усилие очень быстро исчезает, что вызывает небольшие колебания фрезы, когда очередная вставная режущая пластина в державке для режущего инструмента включается в процесс обработки, что вызывает увеличение усилия на инструмент вместе с нагрузкой на подшипники шпинделя машины.
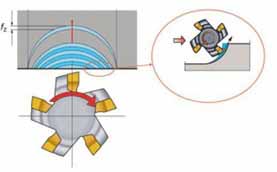
Рисунок 4.2 – Начало обработки детали при прямом врезании фрезы – толстая стружка на выходе
Начало обработки детали при прямом врезании фрезы – толстая стружка на выходе.
Еще до того, как фреза полностью войдет в заготовку, на выходе появляется толстая стружка, вызывающая вибрацию, повреждение режущих кромок и сокращение срока службы инструмента.
Все это происходит на очень высокой скорости, приводя к возникновению дребезжащего звука, который сохраняется, пока центральная осевая линия фрезы не пройдет край обрабатываемой формы. Когда фреза переместится в эту позицию, на выходе естественным образом появится тонкая стружка. Вы можете легко увидеть разницу в толщине линий в самой дальней точке на правой стороне.
Торцовое фрезерование с круговой подачей
Примечательно, что при использовании торцового фрезерования с круговой подачей (см. Рисунок 4.3) тонкая стружка будет покидать фрезу с самого начала процесса обработки, независимо от положения центральной осевой линии фрезы. В этом случае устраняются колебания инструмента из-за давления, а также возникновение/ослабление нагрузки на подшипники шпинделя машины[10, 11].
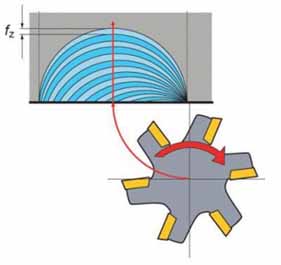
Рисунок 4.3 – Начало обработки детали при круговом врезании
Круговое врезание позволяет добиться минимальной толщины стружки на выходе, снижая вибрацию и продлевая срок службы инструмента.
Таким образом, техника торцового фрезерования с круговой подачей не только устраняет проблему вибрации, увеличивая срок службы инструмента и производительность процесса обработки, но и снижает износ подшипников шпинделя станка, а также делает процесс обработки более предсказуемым. Такая предсказуемость позволяет оператору машины покидать рабочее место с полной уверенностью в том, что по возвращении не возникнет сюрпризов. Получать тонкую стружку на выходе также позволяет и радиальное перемещение фрезы под углом к обрабатываемой поверхности. Если фреза начинает процесс обработки под углом в 20°-30° к обрабатываемой поверхности, возникает тот же самый эффект, как и при торцовом фрезеровании с круговой подачей. Этот вариант уместен при использовании упрощенного программирования машины.
Метод винтовой интерполяции
Метод винтовой интерполяции (см. Рисунок 4.4), в свою очередь, используется для обработки выемок или создания отверстий в форме с помощью фрезы.
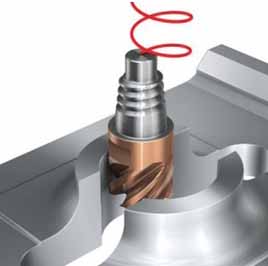
Рисунок 4.4 – Круговое врезание при круговом интерполировании
Круговое врезание – при осуществлении кругового интерполирования позволяет добиться минимальной толщины стружки на выходе и минимизировать углы врезания, снизив вибрацию и получив максимальную производительность.
Работа фрезы начинается с действий над формой, после чего она перемещается по круговой траектории и начинает углубляться в форму, инициируя процесс обработки. Получить тонкую стружку при выполнении этой операции немного легче, потому что необходимо лишь одно дополнительное круговое перемещение фрезы над формой – фреза просто начнет работу немного выше и будет перемещаться согласно круговому шаблону, углубляясь в поверхность самой формы. Многие не выполняют этот дополнительный шаг и становятся свидетелями все того же негативного эффекта вибрации, сокращенного срока службы инструмента и т. д.
Торцовое фрезерование с глубоким врезанием
Вам придется обзавестись приличным опытом в области позиционирования фрезы над формой, чтобы добиваться нужной точности. При торцовом фрезеровании с глубоким врезанием, 70-процентное врезание является оптимальным. Это дает твердосплавным пластинам время на сжатие соразмерно усилию на инструмент, и тонкая стружка на выходе позволяет постепенно уменьшать это сжатие. Опять же все это происходит очень быстро, но твердосплавные пластины не очень хорошо единовременно снимают давление толстой стружки – резкая смена нагрузки от сжатия к растяжению становится причиной откалывания карбида на выходе. Тогда как при неглубоком врезании, которое применяется главным образом при контурной обработке, врезание на 25 % от диаметра фрезы является оптимальным с точки зрения срока службы инструмента и производительности.
Важно иметь в виду возможные последствия появления толстой стружки на выходе из-за положения фрезы над формой. Большинство производителей центруют фрезу над центром обрабатываемой детали, и на выходе возникает толстая стружка. Вместо этого процесс должен быть оптимизирован для обеспечения наименьшей толщины стружки.
Попутное и встречное фрезерование
Также важно различать фрезерование по подаче (попутное фрезерование) и фрезерование против подачи (встречное фрезерование). Оба метода соотносятся с позиционированием фрезы над формой. При фрезеровании против подачи фреза смещена в правую сторону, что опять-таки приводит к появлению толстой стружки на выходе. При осуществлении прохода с фрезерованием по подаче фреза смещена в левую сторону, и стружка на выходе получается тонкой. Этот процесс называется фрезерованием по подаче, потому что режущий эффект достигается за счет вращения фрезы в одном направлении с подачей материала. При фрезеровании против подачи фреза ограничена сжимающими силами[12, 13].
Непрерывное врезание фрезы
Непрерывное врезание фрезы является еще одним методом выхода на оптимизированную производительность. Следует отметить, что ширина прохода (ширина обрабатываемого материала) остается неизменной на протяжении всего процесса обработки. Наиболее часто при изготовлении моделей, штампов и пресс форм фреза движется вокруг формы, придавая последней различные особенности. Подобный результат должен достигаться с помощью перемещения фрезы по запрограммированному радиусу, а не ряда прямолинейных проходов (см. Рисунок 4.5).
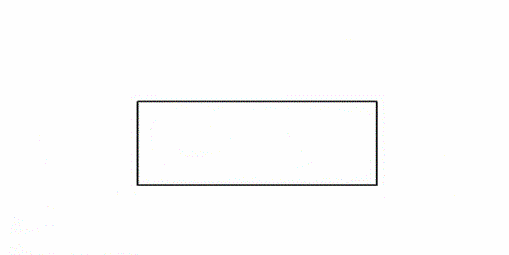
Рисунок 4.5 – Схема резания при торцовом фрезеровании. (Анимация: 16 кадров, 0.5 сек задержка, размер 80 Кб, неограниченное число повтров, программа – Easy GIF Animator)
Фреза должна непрерывно взаимодействовать с заготовкой. Многие производители используют прямолинейные проходы, но это не очень хорошая ситуация, потому что подобные действия нагружают и разгружают шпиндель, инициируют вибрацию, сокращают срок службы инструмента и значительно снижают общую производительность станка. Когда торцовое фрезерование с круговой подачей используется для начала обработки компонента, и фреза перемещается по определенному радиусу при достижении угловых частей заготовки, мы можем получить тонкую стружку на выходе, сохранить уровень врезания постоянным (даже по углам) и обеспечить устойчивость.
Стружкообразование и позиционирование фрезы
Обработка над пазами или отверстиями сделает процесс небезопасным, поэтому проведите повторное позиционирование фрезы и доработайте программу, чтобы на выходе постоянно была тонкая стружка. Опять же, многие производители вносят в программу работы фрезы прохождение непосредственно над полостями (см. Рисунок 4.6, верхняя часть). Подобный подход не только инициирует вибрации и неустойчивость, которые обсуждались ранее, но и осуществляет фрезерование против подачи и фрезерование по подаче на одном и том же пути перемещения фрезы, усиливая нежелательные эффекты. Вместо этого производители должны использовать пути справа. Необходимо провести круговое врезание, поддерживая непрерывность процесса – это позволит получить тонкую стружку на выходе (см. Рисунок 4.6, нижняя часть).
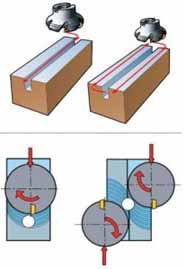
Рисунок 4.6 – Стружкообразование и позиционирование фрезы
Обработка над прорезями или отверстиями, присутствующими в компоненте, сделает процесс небезопасным. Повторное позиционирование фрезы и обработка с огибанием этих полостей приведет к увеличению безопасности и позволит выйти на максимальную производительность.
Обработка пресс-форм, моделей, штампов: профилирование
При изготовлении моделей, штампов и пресс форм проводится значительный объем работ по профилированию, что позволяет придать формируемому компоненту необходимые особенности. Все те же техники торцового фрезерования с круговой подачей и непрерывного врезания путем перемещения фрезы по запрограммированному радиусу позволяют получить тонкую стружку на выходе, что приводит к максимальной производительности (см. Рисунок 4.7).
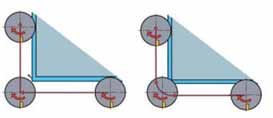
Рисунок 4.7 – Траектория резания при контурной обработке внешних углов
Изготовление моделей, штампов и пресс форм предполагает обработку множества внутренних углов, и никто вам не скажет, будет ли фреза вибрировать при достижении того или иного угла. Чтобы исключить проблемы, дуга врезания при приближении к внутреннему углу должна быть около 50 градусов. Однако когда фреза входит в угол, эта дуга врезания увеличивается до 140 градусов из-за материала, возникающего перед инструментом в тех областях, которые еще не были обработаны. Многие производители предусматривают 90-градусное изменение направления, чтобы начать обработку другой области формы. Это вызывает вибрацию, потому что дуга врезания превышает 90 градусов и нагрузка на фрезу снижается.
Это значит, что запрограммированное изменение направления фактически заставляет машину полностью остановить движение фрезы, в результате чего давление на инструмент теряется и начинается вибрация. Затем фреза начинает перемещаться в другом направлении, после чего давление и нагрузка на инструмент снова возрастают. Во время повышения усилия на инструмент и нагрузки на шпиндель, фреза будет продолжать вибрировать, пока уровень нагрузки не станет достаточно высоким, чтобы стабилизировать шпиндель. Наиболее корректным в данном случае будет использование запрограммированных радиусов, чтобы поддерживать непрерывное врезание, удерживать усилие на шпиндель и фрезу, а также избегать остановки машины (см.Рисунок 4.8).
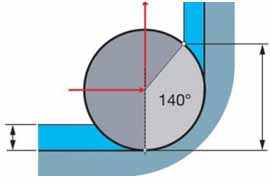
Рисунок 4.8 – Траектория резания внутренних углов – концевое измельчение
Обработка углов часто инициирует вибрацию; корректное программирование обхода углов позволит добиться увеличения срока службы инструмента и приведет к притоку данных для расчета режимов резания на станке с ЧПУ.
5. Перспективы и преимущества внедрения современного режущего инструмента и современных стратегий обработки
Правильный выбор режущего инструмента играет ключевую роль в повышении производительности при производстве штампов. Акцент делается на импортный режущий инструмент с наиболее оптимальной геометрией режущей части и разнообразием типов и конфигураций инструмента.
- Гарантированная стойкость импортного инструмента в 4 раза превышает режущий инструмент, выполненный по ГОСТам.
- Улучшение возможностей стружколомания, за счет сложных форм сменных твердосплавных пластин и широкие возможности их замены.
- Широта возможностей при подводе СОТС непосредственно в зону резания.
- Гарантия на инструмент от производителя, при выполнении норм использования, предписанных заводом-изготовителем.
- При выполнении всех пунктов, инструментальная база является гибкой, и легко подстраивается под обработку иных типоразмеров штампов, существенно сокращая время подготовки и обработки изделий.
- При этом, импортный инструмент дает лучшее качество обработанной поверхности, чем отечественный аналог, сокращая количество переходов при обработке в 1.5 раза.
- Применение инструмента со сменными неперетачиваемыми пластинами влечет за собой удешевление производства штампов, за счет низкого износа остова инструмента и возможностями утилизации вторсырья в виде твердосплавных пластин.
- Оптимизация стратегии обработки позволит существенно увеличить производительность и более чем в 1.5 раза сократить время получения единицы продукции.
- Осуществима выемка металла в виде объемных тел, взамен послойного съема в виде стружки.
Выводы
В данной работе проведен анализ используемого режущего инструмента, оптимизированных и передовых стратегий обработки и сделан вывод:
При выполнении пунктов работы будет достигнута главная цель – повышение производительности, сокращение времени обработки и существенное сокращение затрат на производство.
При успешном внедрении данного комплекса действий – на выходе получим высокотехнологичное и высокоорганизованное производство, экономически выгодную продукцию и для заказчика и для самого производства, с выполнением всех современных норм и требований к продукции, в том числе и экологических.
При написании данного реферата магистерская работа еще не завершена. Окончательное завершение: январь 2014 года. Полный текст работы и материалы по теме могут быть получены у автора или его руководителя после указанной даты.
Список источников
- Кожевников Д. В., Гречишников В. А., Кирсанов С. В., Кокарев В. И., Схиртладзе А. Г. Под редакцией С. В. Кирсанова. Режущий инструмент: Учебник для вузов- 2-е изд. доп. – М.: Машиностроение, 2005. – 528 с: ил.
- Терновой Ю.Ф., Канюк В.И., Терехов В.Н. Справочник по инструментальным сталям. 2-е издание – Х.: «Металлика», 2009. – 242 с.
- Соловцов, Л.Г. Степанский, В.Н. Субич, В.А. Ульянов, З.Г. Унанян, А.Е. Феофанова, А.П. Шляхин, С.С. Яковлев. Ковка и штамповка: справочник. В 4 т.
- Режущий инструмент в производстве штампов и пресс-форм. Краткое справочное руководство. ISCAR IMC Group.
- Автоматизация проектно-конструкторских работ и технологической подготовки производства в машиностроении / Под ред. О.И. Семепкова. В 2-х т. Том 2. Минск. Вышейшая школа. 1977. 334 с.
- Акастелова Н.А., Вдовий С.И., Щупляк Г.И. Расчёт на ЭВМ раскроя листового материала при вырубке деталей из полосы // Кузнечно-штамповочное производство. 1983. № 4. С. 18—19.
- Арефин Ю.И., Швайнштейн И.С. Прогрессивная штамповочная оснастка. Л., Лениздат, 1982. 111 с.
- Динер И.Г., Брун В.Я., Бирин Б.В. Конструкции твердосплавных разделительных штампов. Рига, ЛатНИИНТИ, 1982. 24 с.
- Динер И.Г., Брун В.Я., Стеблюк В.И. Проектирование и изготовление твердосплавных штампов // Кузнечно-штамповочное производство. М., Машиностроение, 1979. № 8. С. 28—30.
- Дурандин М.М., Рымзин А.П., Шихов Н.А. Штампы для холодной штамповки мелких деталей. Альбом конструкций и схем. М., Машиностроение. 1978. 108 с.
- Системы автоматизированного проектирования: Типовые элементы, методы и процессы / Д.А. Аветисян, И.Л. Башмаков, В.И. Геминтерн и др. М., Изд-во стандартов. 1985. 180 с.
- Справочник по заготовлению и ремонту штампов и пресс-форм / В.С. Мендельсон, Л.И. Рудман, М.Г. Аскинази и др. Киев, Техника. 1979. 176 с.
- Стеблюк В.И., Марченко В.Л., Белов В.В. Технология листовой штамповки. Курсовое проектирование. Киев, Вища школа, 1983. 280 с.