Реферат за темою випускної роботи
Реферат носить попередній характер, оскільки час його складання - березень-квітень 2014р., тоді як захист магістерської дисертації запланований на січень 2015р.
Зміст
- Актуальність заявленої теми
- 1. Мета і завдання дослідження
- 2. Аналіз сучасного стану питання дослідження
- 2.1 Класифікація процесів нанесення покриттів
- 2.2 Досвід підприємств у питанні нанесення зносостійких покриттів
- 2.3 Зносостійкість роликів прокатних станів
- 3. Методика і принципи нанесення функціонально-орієнтованих покриттів роликів прокатних станів
- Висновки
- Перелік посилань
Актуальність заявленої теми
В даний час в світі приділяється велика увага проблемам підвищення зносостійкості і корозійної захисту деталей машин і механізмів. Актуальність питання підвищення зносостійкості досить проілюструвати тим фактом, що в деяких галузях промисловості виробництво запасних деталей зрівнялося з виробництвом деталей, призначених для складання нових машин [1]. Знос деталей приносить втрати в промисловості всіх галузей і всіх країн світу. Сума збитків — мільярди доларів. Знос з'їдає не тільки ті гроші, які йдуть на закупівлю деталей, що замінюються. Оскільки під час зупинок обладнання, пов'язаних з його ремонтом, випуск продукції на підприємстві знижується, втрати істотно зростають. Час простою — також втрата прибутку. Крім всього цього знос стосується однієї глобальної проблеми — виснаження природних ресурсів планети.
У спряженні валки-смуга вивчають знос лише поверхні валків.
Під зносом в цьому випадку розуміють зміну форми і розмірів калібрів валків на сортових і трубних станах, і профілю бочки на листових станах. Знос прокатних валків в першу чергу пов'язаний з ковзанням металу смуги, що прокочується, щодо валків в зонах випередження і відстоювання. Ця дія призводить до того, що робоча поверхня валка піддається знакозмінному напруження, спрямованому по дотичній до поверхні бочки валка. Багаторазове повторення цих силових впливів і великий нормальний тиск викликають різке механічне стирання поверхні валків, відрив частинок металу, сколювання по їх поверхні [2].
Не дивлячись на успіхи в галузі теорії та практики прокатного виробництва багато завдань, щодо розрахунків оптимальних характеристик і підвищення експлуатаційної міцності і зносостійкості прокатних валків залишаються невирішеними.
Одним із способів підвищення функціональних характеристик роликів прокатних станів є метод нанесення покриттів. Нині є безліч технологій нанесення покриттів. Вибір того чи іншого способу залежить насамперед від вимог, що висуваються до виробів і виконання ними функцій.
Зазвичай застосовується однаковий технологічний вплив для всього виробу, що часто буває економічно невигідно, також це призводить до нерівномірної втрати властивостей різних зон поверхонь роликів. Такі умови стимулюють більш ретельну розробку спеціальних технологій. В даному випадку можливе застосування технологій на основі функціонально-орієнтованого підходу [3].
1. Мета і завдання дослідження
Метою даної роботи є підвищення зносостійкості роликів прокатних станів за рахунок застосування спеціальних покриттів на базі застосування функціонально-орієнтованих технологій.
Виходячи з цього, формуються такі завдання:
- Виконати аналіз особливостей нанесення функціонально-орієнтованих покриттів роликів прокатних станів.
- Розробити методику і принципи нанесення функціонально-орієнтованих покриттів роликів прокатних станів.
- Виконати структурний синтез функціональних досліджень та аналіз нанесення спеціальних покриттів роликів прокатних станів.
- Дослідити конструктивні особливості та синтез обладнання для нанесення функціонально-орієнтованих покриттів роликів прокатних станів.
- Провести експериментальні дослідження нанесення спеціальних покриттів роликів прокатних станів.
- Розробити рекомендації щодо технологічного забезпечення нанесення функціонально-орієнтованих покриттів роликів прокатних станів.
2. Аналіз сучасного стану питання дослідження
2.1 Класифікація процесів нанесення покриттів
Залежно від вимог, що пред'являються до експлуатаційних характеристик деталей, розрізняють три види покриттів [4]:
- захисні покриття, призначенням яких є захист від корозії деталей в різних агресивних середовищах, зокрема за високих температур;
- захисно-декоративні покриття, що служать для декоративного оздоблення деталей з одночасним захистом їх від корозії;
- спеціальні покриття, що застосовуються з метою надання поверхні спеціальних властивостей (зносостійкості, твердості, електроізоляційних, магнітних властивостей тощо), а також відновлення зношених деталей.
Класифікація процесів нанесення металевих покриттів наведена на рис. 1.
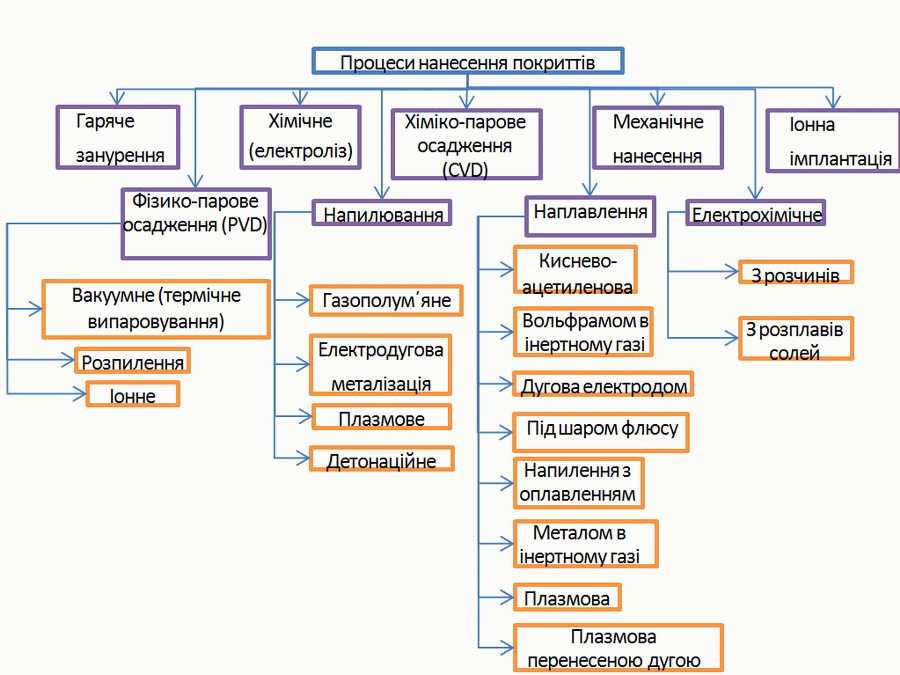
Рис. 1 Класифікація процесів нанесення металевих покриттів [4]
Серед усіх способів можна відзначити самі основні [4]:
- Гаряче занурення в розплав — один з найстаріших методів нанесення покриттів. Метали ванни мають низьку температуру плавлення — це цинк, олово, алюміній. Вони забезпечують захист основного металу від корозії.
- Напилювання здійснюється дрібними частинками матеріалу, що утворюються під час пропускання дроту або порошку через киснево-ацетиленове полум'я, з подальшим осадженням на холодну основу. Для нагрівання можна використовувати електродугову або плазмову металізацію. Це сприяє поліпшенню адгезії і зниження пористості покриття.
- Наплавлення здійснюється сплавленням матеріалу, що осідає з поверхневим шаром основи. Наплавлення широко застосовується для ремонту окремих деталей, Пошкодження або зношених в процесі експлуатації. Для нанесення покриттів методом наплавлення можуть використовуватися всі основні зварювальні процеси: газополум'яний, електродуговий, плазмовий, електроннопроменевий тощо.
- Електрохімічне осадження металів з розчинів солей зазвичай застосовується для отримання гальванічних покриттів з хрому і нікелю товщиною 0,12-0,60 мм.
- Електролітичне нанесення покриттів із сплавів Ni-P і Ni-B здійснюється внаслідок хімічної взаємодії. У цьому випадку покриття формуються по всій поверхні деталей з однаковою швидкістю товщиною до 0,12 мм, тоді як гальванічні покриття насамперед формуються на виступаючих місцях — крайках, ребрах, гранях.
- Хіміко-парове осадження, або процес CVD (chemical vapour deposition), є процес, під час якого стійкі продукти реакції зароджуються і ростуть на підкладці в середовищі, в якому протікають хімічні реакції(дисоціація, відновлення тощо) Завдяки високій температурі на поверхні утворюються дуже тонкі шари, наприклад, карбіду або нітриду титану. CVD-процес використовується для нанесення покриттів на інструмент і штампи.
- Фізичне осадження з парової фази (physical vapour deposition, PVD) протікає в декілька стадій:
- нагрівання матеріалу у вакуумі до випаровування;
- перенесення парів від джерела до підкладки;
- конденсація парів на основі — підкладці.
- Метод PVD володіє високою гнучкістю, і з його допомогою можна наносити будь-які метали, сплави, оксиди, карбіди і нітриди. Наприклад, його з успіхом застосовують для нанесення зносостійкої плівки TiN на сталевий інструмент. Перевагою методу PVD є висока чистота поверхні і чудова зв'язок з основою.
- Механічне нанесення покриттів використовують для отримання цинкових, кадмієвих та оловокадміевих покриттів. Деталі перемішують у посудинах з відповідними тонкими металевими порошками, активаторами і скляними кульками.
- Іонна імплантація передбачає іонізацію атомів з наступним прискоренням іонів в електричному полі у вакуумі. Іони гальмуються під час зіткнення з мішенню і розподіляються щодо глибини мішені. Хоча глибина проникнення іонів не більше 0,1-0,2 мкм, властивості металу можуть істотно змінюватися.
2.2 Досвід підприємств у питанні нанесення зносостійких покриттів
Досить багато підприємств працюють у даному напрямку. Зокрема, у ВАТ «ММК ім. Ілліча» використовують установки для механізованого дугового наплавлення.
У ВАТ «ММК ім. Ілліча » створені і освоєні дві установки для наплавлення сталевих валків прокатних станів. Річний економічний ефект від впровадження розробки склав більше 250 тис. грн. Витрати на відновлення зношеного прокатного валка становлять у середньому 15% від вартості нового. Зносостійкість ж наплавлених валків більш ніж в 2,5 рази перевищує показник нових валків (рис. 2) [5].
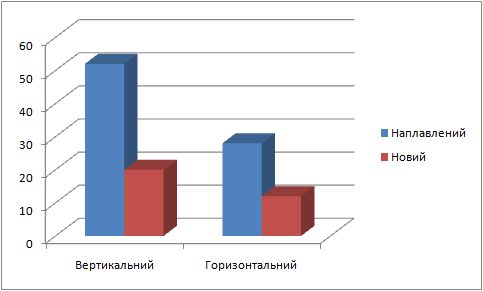
Рис. 2 Зносостійкість (тис. тонн / мм) наплавлених і нових валків прокатного стану слябінг-1150 ВАТ «ММК ім. Ілліча » [5]
Великий досвід з нанесення зносостійких покриттів має підприємство РУП «Технопарк БНТУ«Метоліт».
В «Технопарк БНТУ«Метоліт» виготовлені ролики з конструкційної сталі Сталь45 з газополум'яними покриттями робочих поверхонь сплавами на основі заліза системи Fe-Ni-Cr-B-Si з нерівноважної структурою товщиною до 3,5 мм.
Матеріали покриття за рахунок особливим чином організованої структури, що зберігається після напилювання і тривалий час в умовах експлуатації, мають більш високі механічні властивості, ніж традиційні на РУП БМЗ для виготовлення прокатних роликів термооброблені сталі 6ХВ2С, 5ХВ2С, 250Х24В3Т, 60С2, 60С2Г, 40Х. Це забезпечує збільшення стійкості деталей в порівнянні з базовим варіантом до 7,5 разів.
Зразки, що створюються, прокатних роликів можуть бути неодноразово реставровані без додаткового нанесення покриття тільки за рахунок переточки та відновлення робочого профілю. Це стало можливим завдяки нанесенню більш товстих шарів покриття, ніж традиційно. В РУП «Технопарк БНТУ «Метоліт» розроблена технологія нанесення покриттів зі сплавів системи Fe-Ni-Cr-B-Si на ролики товщиною не менше 3 мм, причому в цьому випадку міцність зчеплення з підкладкою не поступається міцності зчеплення покриття з товщиною 1 мм. Збільшення товщини покриттів призводить до зростання числа переточок ролика, істотно підвищуючи його довговічність.
Стійкість роликів з зносостійкими покриттями після кожної переточки перевищує більш ніж в 2 рази стійкість підшипників робочої кліті.
Подальше відновлення остаточно зношених роликів може бути здійснено шляхом нанесення покриття на основу без видалення залишків раніше нанесеного зносостійкого шару.
Вартість деталей, які створюються, в залежності від номенклатури нижча порівняно з базовим варіантом від 1,16 до 2,6 рази.
Для нанесення покриттів використовується обладнання [6]:
- установка струменево-абразивної обробки КАМЕТЕН 120Н (напірного типу з преціклоном);
- багатофункціональна установка газополум'яного напилення «ТЕХНИКОРД ТОП-ЖЕТ/2» (П) – для напилювання порошків;
- установка для газополум'яної наплавлення порошків підвищеної потужності ТЕНА-ГН-ПМ;
- обертач деталей ТЕХ-10;
- пальник для оплавлення ГЗУ-4.
2.3 Зносостійкість роликів прокатних станів
Робочі валки прокатних станів повинні забезпечувати надійне захоплення, бути досить міцними і зносостійкими, володіти високим опором ударних навантажень,які неминуче виникають у початковий момент захоплення.
Якість робочих валків і їх стійкість в значній мірі визначають техніко-економічні показники роботи станів.
Знос прокатних станів залежить від: хімічного складу, структури валка, температурного режиму прокатки і умов охолодження валків, прийнятої системи калібрування та режиму обтиснень, стану валкової арматури і налаштування стану.
Як показує досвід, температура поверхні валка поза зони деформації вище температури навколишнього середовища не більше ніж на 50 ° С. У епіцентрі деформації температура на поверхні валка близька до температури металу, що прокочується. У результаті коливань температури на поверхні валка з'являється сітка тріщин, де відбувається інтенсивне окислення металу, що сприяє подальшому розвитку утворених тріщин.
При охолодженні валків водою термін служби калібрів значно підвищується. Вода рясно подається з боку виходу смуги. Охолоджувальна вода не повинна потрапляти в калібр разом з смугою, що прокочується з боку входу, оскільки вода перетворюється на пару і сприяє руйнуванню поверхневого шару валка. На знос калібрів впливає також хімічний склад сталі, що прокочується. Під час прокатки сталей з високим вмістом вуглецю знос калібрів більше, ніж під час прокатки рядових сталей. Особливо швидко зношуються калібри під час прокатки багатьох легованих сталей.
Між величиною зносу валків і їх твердістю існує пряма залежність. Зменшення зносу і підвищення твердості чавуну, що спостерігається в повністю вибіленому шарі, автори пояснюють ослабленням анормальної структури під час віддалення від поверхні валка. З появою в структурі графіту знижується твердість і збільшується знос приблизно пропорційно зменшенню кількості карбідної складової. Максимальний знос спостерігається на межі між перехідною зоною і зоною сірого чавуну, де є дрібні пластинки графіту, а кристали карбіду відсутні.
Окремі частини калібру зношуються нерівномірно в результаті неоднакових умов тертя в різних місцях зони деформації. Це пов'язано з нерівномірним ковзанням металу по поверхні калібрів, що пояснюється змінною величиною радіусів, що катають, і умовами течії металу [7].
На рис. 3 представлені епюри зносу калібрів середньосортного стану 350 АО «Северсталь», побудовані за даними зносу через кожні 5 мм по периметру калібру з фіксацією кількості прокатаного металу в даному калібрі.
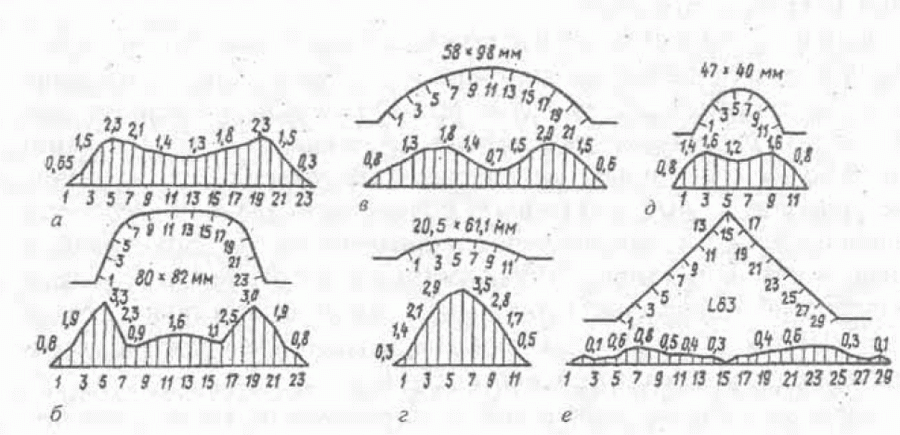
Рис. 3 Епюри зносу валків стану 350 [2]
На рисунку видно, що під час прокатки на гладкій бочці з'являються дві зони максимального зносу, розташування яких відповідає кутам смуги, що задається, мають знижену температуру і тому підвищений опір деформації (рис. 3, а).
Максимальний знос ящикових калібрів (рис. 3, б) спостерігається по їхніх стінках. По дну знос виявляється майже вдвічі меншим. Стан поверхні зношеного калібру свідчить про ковзанні металу по поверхні стінок калібру, зумовленого плином металу під дією сил, що обмежують уширение, і різницею окружних швидкостей по стінці калібру.
Овальні калібри (рис. 3, в), в які задається заготовка квадратного перетину, мають дві симетрично розташовані області максимального зносу, відповідні кутам квадрата, що задається.
Максимальний знос овального калібру, якому передує ребровой овал (рис. 3, г), відбувається на середній частині калібру, до країв калібру знос плавно зменшується.
Знос калібрів ребрового овалу (рис. 3, д) відбувається більш рівномірно, ніж знос овальних калібрів. Ділянки максимального зносу розташовані симетрично на деякій відстані один від одного.
Мінімальний знос кутових калібрів валків VI, VIII, LX і X клітей спостерігається в вершині їх кута. До країв полки знос поступово збільшується.
Оздоблювальні калібри валків XII і XIV клітей мають такий же характер зносу, що і кутові калібри (рис.3, е). Це пояснюється тим, що в реброва калібрі валків XI кліті спостерігається посилений знос стінки калібру [2].
3. Методика і принципи нанесення функціонально-орієнтованих покриттів роликів прокатних станів
Враховуючи особливості зношування різних роликів прокатних станів, можна встановити, що перспективним підходом до розробки технології нанесення покриттів є функціонально-орієнтовані технології.
Функціонально-орієнтована технологія виготовлення виробу машинобудування — це спеціальна технологія, яка заснована на точній топологічно орієнтованої реалізації необхідної кількості алгоритмів технологічного впливу знарядь і засобів обробки в необхідні мікро, макро зони і ділянки вироби, які функціонально відповідають умовам їх експлуатації в кожній окремій його зоні. Використання функціонально-орієнтованих технологій для виробів машинобудування дозволяє максимально підвищити їх загальні експлуатаційні параметри за рахунок місцевого збільшення технічних можливостей і властивостей окремих елементів, поверхонь і / або зон виробу залежно від функціональних місцевих особливостей їх експлуатації. При цьому вироби машинобудування, що виготовляються за пропонованими технологіями, максимально адаптуються за своїми властивостями до особливостей їх експлуатації і проявляють свій повний потенціал можливостей в машині. Слід зазначити, що пропонований новий клас технологій ускладнює процес виготовлення виробів, але в цілому забезпечує якісно нову сукупність властивостей і міру корисності виробів машинобудування під час експлуатації. Це дає можливість суттєво підвищити техніко-економічні показники експлуатації і використання машин і технічних систем. На рис. 4 показані основні етапи синтезу функціонально-орієнтованих технологічних процесів. Послідовність і методологія базуються на замкнутій рекурентній структурі [3]
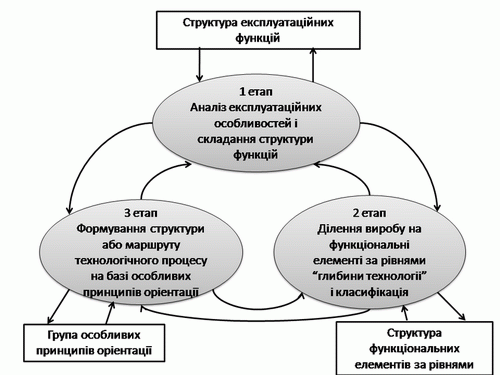
Рис. 4. Основні етапи синтезу функціонально-орієнтованих технологій [3]
Основними особливостями функціонально-орієнтованих технологій є те, що технологічні впливу знарядь обробки на вироби і процес забезпечення заданих і необхідних властивостей виробів виконується на наступних рівнях: на рівні всього виробу в цілому; на рівні дільниць; на рівні складових; на рівні зон; на рівні макрозон; на рівні мікрозон; на рівні нанозон.
При цьому задані, необхідні і граничні властивості виробів забезпечуються за рахунок орієнтації технологічних впливів потоків матерії, енергії та інформації на базі наступних восьми особливих принципів [3,8]:
- Функціональної відповідності особливостей дії елементарної функції в кожному функціональному елементі виробу, характеристик реалізації технологічних впливів і параметрів забезпечення необхідних властивостей цьому функціональному елементі виробу на кожному рівні глибини технології.
- Топологічного відповідності геометричних параметрів функціонального елемента виробу, в якому діє елементарна функція під час експлуатації, геометричним параметрам зонального елемента реалізації технологічних впливів потоків матерії, енергії та інформації на виріб і геометричних параметрів зонного елемента забезпечення необхідних властивостей на кожному рівні глибини технології.
- Кількісної відповідності множини функціональних елементів, в яких діє множина різних елементарних функцій під час експлуатації, множини реалізації технологічних впливів і множини елементів забезпечення необхідних властивостей у функціональних елементах виробу на кожному рівні глибини технології.
- Адекватною залежності просторових особливостей дії елементарної функції під час експлуатації, технологічних впливів та експлуатаційних властивостей у просторі кожного функціонального елемента виробу на кожному рівні глибини технології.
- Адекватної залежності тимчасових особливостей дії елементарної функції під час експлуатації, тимчасових або просторових особливостей реалізації технологічних впливів і тимчасових експлуатаційних властивостей в кожному функціональному елементі виробу на кожному рівні глибини технології.
- Структурної відповідності дії множини елементарних функцій, реалізації множини технологічних впливів і виконання множини властивостей у функціональних елементах вироби з умови забезпечення заданих, необхідних або граничних властивостей всього виробу на кожному рівні глибини технології.
- Адекватного структурно-функціонального відповідності властивостей у просторі і в часі кожного функціонального елемента заданому, необхідному чи граничного потенціалу загальних властивостей всього виробу в цілому на кожному рівні глибини технології.
- Адекватного структурно-функціонального відповідності властивостей навколо кожного функціонального елемента в просторі і в часі заданому, необхідному чи граничного потенціалу загальних властивостей всього виробу в цілому на кожному рівні глибини технології.
На основі розроблених принципів виконується синтез функціонально-орієнтованих технологій і виготовлення виробів, які забезпечують повну адаптацію виробу і його елементів за експлуатаційними властивостями до умов експлуатації. Виготовлення виробів на основі функціонально-орієнтованих технологій забезпечує можливість реалізації їх повного потенціалу функціональних можливостей під час експлуатації. Це істотно підвищує техніко-економічні показники виготовлення й експлуатації виробів.
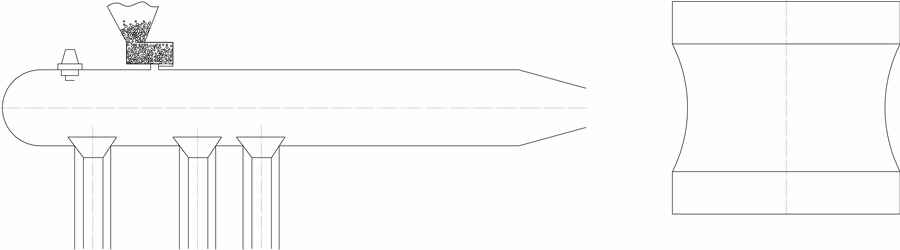
Рис. 5 Функціонально-орієнтоване детонаційне нанесення покриттів
Таким чином, досліджуючи ряд функцій, які виконує робоча поверхня ролика прокатного стану, можна розбити її на кілька зон. Розбиття відбувається залежно від нерівномірних впливів на довжині поверхні ролика. Тому потрібен індивідуальний підхід до кожного ролику, до якого застосовується функціонально-орієнтована технологія. У даному випадку вивчається нерівномірний знос і температурний вплив на поверхню ролика. До кожної обраної зоні необхідно підібрати оптимальні режими обробки, в тому числі і склад покриття, яке наноситься на виріб. Для підвищення продуктивності можливе використання принципу концентрації, а також інтенсифікації режимів обробки і скорочення допоміжного часу.
Висновки
Функціонально-орієнтовані технології є перспективними для багатьох областей застосування, в тому числі і для роликів прокатних станів. Головна особливість цього підходу — краща адаптація виробу до умов експлуатації. Це, в свою чергу, значно підвищує термін служби роликів, оскільки зменшується і стає рівномірним процес зносу по довжині бочки ролика, збільшується час між перевалками, і як наслідок, підвищується продуктивність прокатного стану.
Позитивну тенденцію у підвищенні зносостійкості можна відзначити, вивчаючи досвід підприємств, що розробляють технології нанесення зносостійких покриттів роликів прокатних станів. Так, спостерігається підвищення стійкості виробу у кілька разів, залежно від методу і режимів нанесення покриттів, від умов експлуатації і матеріалу підкладки.
З негативних явищ можна відзначити ускладнення процесу розробки технології для обробки виробу в цілому. Також ускладнюється сама технологія і устаткування, що веде до збільшення собівартості виробу, але економічний ефект досягається за рахунок збільшення терміну служби ролика прокатного стану і підвищення продуктивності прокатного обладнання.
Перелік посилань
- Бартенев С.С., Федько Ю.П., Григоров А.И. Детонационные покрытия в машиностроении.—Л.: Машиностроение, Ленингр. отд-ние, 1982.—215с.
- Яковлев Р.А. Расчет на износ узлов трения прокатных станов. Учебное пособие по курсу «Основы динамики и надежности прокатных станов». — Под ред. А.Г. Колесникова. — М.: Изд-во МГТУ им. Н.Э. Баумана, 2004. — 52с.
- Михайлов А.Н. Основы синтеза функционально-ориентированных технологий.—Донецк: ДонНТУ, 2009. — 346 с.
- Зборщик А.М. Конспект лекций по дисциплине «Новые материалы в металлургии». — Донецк: ГВУЗ «ДонНТУ», 2008.–253с.
- Портал Приазовского государственного технического университета [электронный ресурс]. — Режим доступа: http://www.pstu.edu...
- Сайт предприятия РУП «Технопарк БНТУ «Метолит» [электронный ресурс]. — Режим доступа: http://www.otnp.metolit.by...
- Чекмарев А.П., Гречко В.П., Гетманец В.В., Ховрин Б.В. Прокатка на мелкосортных станах. — М.: Изд-во «Металлургия», 1966. -363с.
- Михайлов А.Н. Общие особенности функционально-ориентированных технологий и принципы ориентации их технологических воздействий и свойств изделий. // Машиностроение и техносфера XXI века. Сборник трудов XIV международной научно-технической конференции в г. Севастополе 17-22 сентября 2007 г. В 5-ти томах.—Донецк: ДонНТУ, 2007. Т. 3. С. 38-52.