Реферат по теме выпускной работы
Реферат носит предварительный характер, поскольку время его составления — март-апрель 2014г., тогда как защита магистерской диссертации запланирована на январь 2015г.
Содержание
- Актуальность заявленной темы
- 1. Цель и задачи исследования
- 2. Анализ современного состояния вопроса исследования
- 2.1 Классификация процессов нанесения покрытий
- 2.2 Опыт предприятий в вопросе нанесения износостойких покрытий
- 2.3 Износостойкость роликов прокатных станов
- 3. Методика и принципы нанесения функционально-ориентированных покрытий роликов прокатных станов
- Выводы
- Список источников
Актуальность заявленной темы
В настоящее время в мире уделяется большое внимание проблемам повышения износостойкости и коррозионной защиты деталей машин и механизмов. Актуальность вопроса повышения износостойкости достаточно проиллюстрировать тем фактом, что в некоторых отраслях промышленности производство запасных деталей сравнялось с производством деталей, предназначенных для сборки новых машин [1]. Износ деталей приносит потери в промышленности всех отраслей и всех стран мира. Сумма убытков – миллиарды долларов. Износ съедает не только те деньги, которые идут на закупку заменяемых деталей. Поскольку при остановках оборудования, связанных с его ремонтом, выпуск продукции на предприятии снижается, потери существенно возрастают. Время простоя – также утрата прибыли. Кроме всего этого износ касается одной глобальной проблемы – истощение природных ресурсов планеты.
В сопряжении валки–прокатываемая полоса изучают износ лишь поверхности валков.
Под износом в этом случае понимают изменение формы и размеров калибров валков на сортовых и трубных станах и профиля бочки на листовых станах. Износ прокатных валков в первую очередь связан со скольжением металла прокатываемой полосы относительно валков в зонах опережения и отстаивания. Это воздействие приводит к тому, что рабочая поверхность валка подвергается знакопеременному напряжению, направленному по касательной к поверхности бочки валка. Многократное повторение этих силовых воздействий и большие нормальные давления вызывают резкое механическое истирание поверхности валков, отрыв частиц металла, скалывания по их поверхности [2].
Несмотря на успехи в области теории и практики прокатного производства многие задачи, связанные с расчетами оптимальных характеристик и повышением эксплуатационной прочности и износостойкости прокатных валков остаются нерешенными.
Одним из способов повышения функциональных характеристик роликов прокатных станов является метод нанесения покрытий. В настоящее время существует множество технологий нанесения покрытий. Выбор того или иного способа зависит прежде всего от требований, предъявляемых к изделиям и выполнение ими функций.
Обычно применяется одинаковое технологическое воздействие для всего изделия, что часто бывает экономически невыгодно, также это приводит к неравномерной потери свойств различных зон поверхностей роликов. Такие условия стимулируют более тщательной разработки специальных технологий. В данном случае возможно применение технологий на основе функционально-ориентированного подхода [3].
1. Цель и задачи исследования
Целью данной работы является повышение износостойкости роликов прокатных станов за счет применения специальных покрытий на базе применения функционально-ориентированных технологий.
Исходя из этого, формируются следующие задачи:
- Выполнить анализ особенностей нанесения функционально-ориентированных покрытий роликов прокатных станов.
- Разработать методику и принципы нанесения функционально-ориентированных покрытий роликов прокатных станов.
- Выполнить структурный синтез функциональных исследований и анализ нанесения специальных покрытий роликов прокатных станов.
- Исследовать конструктивные особенности и синтез оборудования для нанесения функционально-ориентированных покрытий роликов прокатных станов.
- Провести экспериментальные исследования нанесения специальных покрытий роликов прокатных станов.
- Разработать рекомендации по технологическому обеспечению нанесения функционально-ориентированных покрытий роликов прокатных станов.
2. Анализ современного состояния вопроса исследования
2.1 Классификация процессов нанесения покрытий
В зависимости от требований, предъявляемых к эксплуатационным характеристикам деталей, различают три вида покрытий [4]:
- защитные покрытия, назначением которых является защита от коррозии деталей в различных агрессивных средах, в том числе при высоких температурах;
- защитно-декоративные покрытия, служащие для декоративной отделки деталей с одновременной защитой их от коррозии;
- специальные покрытия, применяемые с целью придания поверхности специальных свойств (износостойкости, твердости, электроизоляционных, магнитных свойств и др.), а также восстановления изношенных деталей.
Классификация процессов нанесения металлических покрытий приведена на рис. 1.
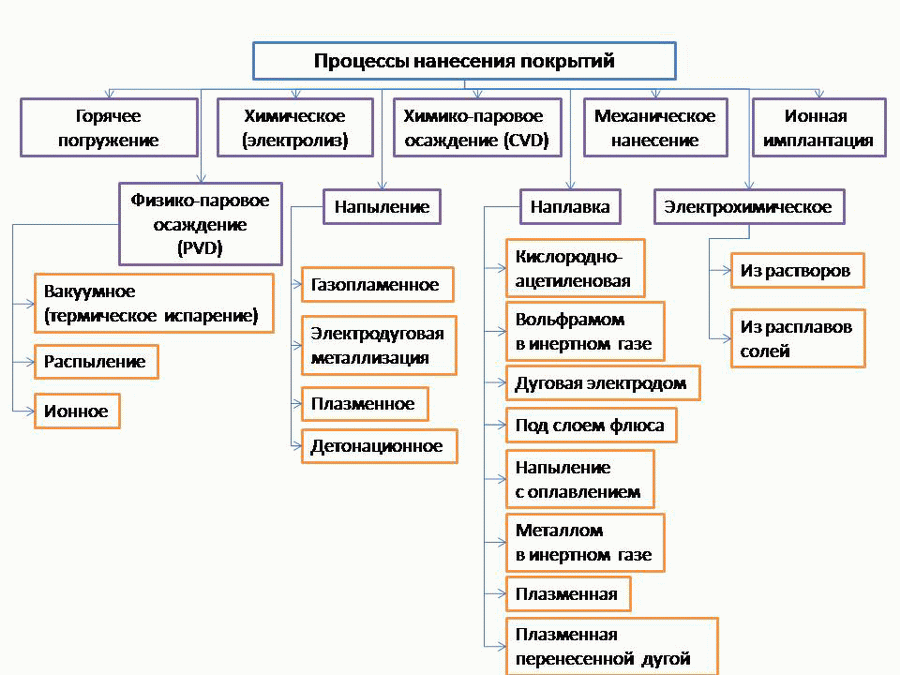
Рис. 1 Классификация способов нанесения покрытий [4]
Среди всех способов можно отметить самые основные [4]:
- Горячее погружение в расплав — один из самых старых методов нанесения покрытий. Металлы ванны имеют низкую температуру плавления – это цинк, олово, алюминий. Они обеспечивают защиту основного металла от коррозии.
- Напыление осуществляется мелкими частицами материала, образующимися при пропускании проволоки или порошка через кислородно-ацетиленовое пламя, с последующим осаждением на холодную основу. Для нагрева можно использовать электродуговую или плазменную металлизацию. Это способствует улучшению адгезии и снижению пористости покрытия.
- Наплавка осуществляется сплавлением осаждаемого материала с поверхностным слоем основы. Наплавка широко применяется для ремонта отдельных деталей, поврежденных или износившихся в процессе эксплуатации. Для нанесения покрытий методом наплавки могут использоваться все основные сварочные процессы: газопламенный, электродуговой, плазменный, электроннолучевой и др.
- Электрохимическое осаждение металлов из растворов солей обычно применяется для получения гальванических покрытий из хрома и никеля толщиной 0,12–0,60 мм.
- Электролитическое нанесение покрытий из сплавов Ni – P и Ni – B осуществляется вследствие химического взаимодействия. В этом случае покрытия формируются по всей поверхности деталей с одинаковой скоростью толщиной до 0,12 мм, тогда как гальванические покрытия прежде всего формируются на выступающих местах – кромках, ребрах, гранях.
- Химико-паровое осаждение, или процесс CVD (chemical vapour deposition), является процессом, при котором устойчивые продукты реакции зарождаются и растут на подложке в среде с протекающими в ней химическими реакциями (диссоциация, восстановление и др.). Благодаря высокой температуре на поверхности образуются очень тонкие слои, например, карбида или нитрида титана. CVD-процесс используется для нанесения покрытий на инструмент и штампы.
- Физическое осаждение из паровой фазы (physical vapour deposition, PVD) протекает в несколько стадий:
- нагрев материала в вакууме до испарения;
- перенос паров от источника к подложке;
- конденсация паров на основе – подложке.
- Метод PVD обладает высокой гибкостью, и с его помощью можно наносить любые металлы, сплавы, оксиды, карбиды и нитриды. Например, его с успехом применяют для нанесения износостойкой пленки TiN на стальной инструмент. Достоинством метода PVD является высокая чистота поверхности и превосходная связь с основой.
- Механическое нанесение покрытий используют для получения цинковых, кадмиевых и оловокадмиевых покрытий. Детали перемешивают в сосудах с соответствующими тонкими металлическими порошками, активаторами и стеклянными шариками.
- Ионная имплантация предусматривает ионизацию атомов с последующим ускорением ионов в электрическом поле в вакууме. Ионы тормозятся при соударении с мишенью и распределяются по глубине мишени. Хотя глубина проникновения ионов не более 0,1-0,2 мкм, свойства металла могут существенно меняться.
2.2 Опыт предприятий в вопросе нанесения износостойких покрытий
Довольно много предприятий работают в данном направлении. В частности, в ОАО «ММК им. Ильича» используют установки для механизированной дуговой наплавки.
В ОАО «ММК им. Ильича» созданы и освоены две установки для наплавки стальных валков прокатных станов. Годовой экономический эффект от внедрения разработки составил более 250 тыс. грн. Затраты на восстановление изношенного прокатного валка составляют в среднем 15 % от стоимости нового. Износостойкость же наплавленных валков более чем в 2,5 раза превышает показатель новых валков (рис. 2) [5].
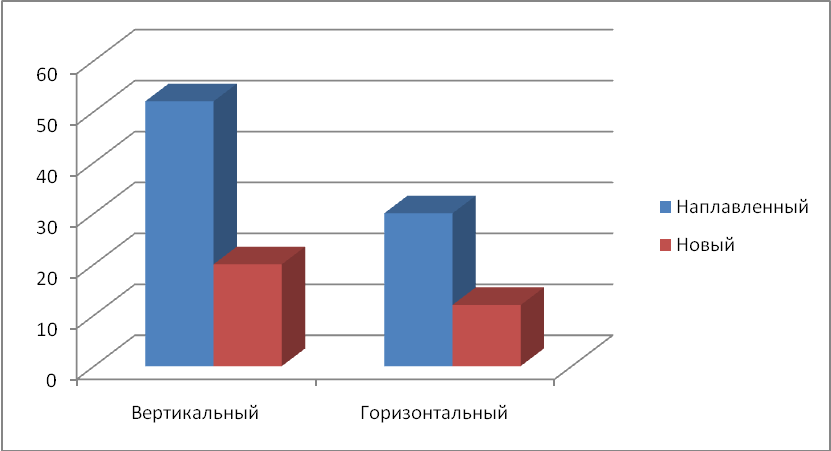
Рис. 2 Износостойкость (тыс. тонн/мм) наплавленных и новых валков прокатного стана слябинг-1150 ОАО «ММК им. Ильича» [5]
Большой опыт по нанесению износостойких покрытий имеет предприятие РУП «Технопарк БНТУ «Метолит».
В РУП «Технопарк БНТУ «Метолит» изготовлены ролики из конструкционной стали Сталь45 с газопламенными покрытиями рабочих поверхностей сплавами на основе железа системы Fe-Ni–Cr-B-Si с неравновесной структурой толщиной до 3,5 мм.
Материалы покрытий за счет специальным образом организованной структуры, сохраняющейся после напыления и длительное время в условиях эксплуатации, имеют более высокие механические свойства, чем традиционно применяемые на РУП БМЗ для изготовления прокатных роликов термообработанные стали 6ХВ2С, 5ХВ2С, 250Х24В3Т, 60С2, 60С2Г, 40Х. Это обеспечивает увеличение стойкости создаваемых деталей по сравнению с базовым вариантом до 7,5 раз.
Создаваемые образцы прокатных роликов могут быть неоднократно реставрированы без дополнительного нанесения покрытия только за счет переточки и восстановления рабочего профиля. Это стало возможным благодаря нанесению более толстых слоев покрытия, чем традиционно. В РУП «Технопарк БНТУ «Метолит» разработана технология нанесения покрытий из сплавов системы Fe-Ni–Cr-B-Si на ролики толщиной не менее 3 мм, причем в этом случае прочность сцепления с подложкой не уступает прочности сцепления покрытия с толщиной 1 мм. Увеличение толщины покрытий приводит к возрастанию числа переточек ролика, существенно повышая его долговечность.
Стойкость роликов с износостойкими покрытиями после каждой переточки превышает более чем в 2 раза стойкость подшипников рабочей клети.
Последующее восстановление окончательно изношенных роликов может быть осуществлено путем нанесения покрытия на основу без удаления остатков ранее нанесенного износостойкого слоя.
Стоимость создаваемых деталей в зависимости от номенклатуры ниже по сравнению с базовым вариантом от 1,16 до 2,6 раза.
Для нанесения покрытий используется оборудование [6]:
- установка струйно-абразивной обработки КАМЕТЭН 120Н (напорного типа с прециклоном);
- многофункциональная установка газопламенного напыления «ТЕХНИКОРД ТОП-ЖЕТ/2» (П) – для напыления порошков;
- установка для газопламенной наплавки порошков повышенной мощности ТЕНА-ГН-ПМ;
- вращатель деталей ТЕХ-10;
- горелка для оплавления ГЗУ-4.
2.3 Износостойкость роликов прокатных станов
Рабочие валки прокатных станов должны обеспечивать надежный захват, быть достаточно прочными и износостойкими, обладать высоким сопротивлением ударным нагрузкам, неизбежно возникающим в начальный момент захвата.
Качество рабочих валков и их стойкость в значительной степени определяют технико-экономические показатели работы станов.
Износ прокатных станов зависит от: химического состава, структуры валка, температурного режима прокатки и условий охлаждения валков, принятой системы калибровки и режима обжатий, состояния валковой арматуры и настройки стана.
Как показывает опыт, температура поверхности валка вне зоны деформации выше температуры окружающей среды не более чем на 50°С. В очаге деформации температура на поверхности валка близка к температуре прокатываемого металла. В результате колебаний температуры на поверхности валка появляется сетка трещин, где происходит интенсивное окисление металла, способствующее дальнейшему развитию образовавшихся трещин.
При охлаждении валков водой срок службы калибров значительно повышается. Вода обильно подается со стороны выхода полосы. Охлаждающая вода не должна попадать в калибр вместе с прокатываемой полосой со стороны входа, так как вода превращается в пар и способствует разрушению поверхностного слоя валка. На износ калибров оказывает влияние также химический состав прокатываемой стали. При прокатке сталей с высоким содержанием углерода износ калибров большие, чем при прокатке рядовых сталей. Особенно быстро изнашиваются калибры при прокатке многих легированных сталей.
Между величиной износа валков и их твердостью существует прямая зависимость. Уменьшение износа и повышение твердости чугуна, наблюдающееся в полностью отбеленном слое, авторы объясняют ослаблением анормальности структуры при удалении от поверхности валка. С появлением в структуре графита понижается твердость и увеличивается износ примерно пропорционально уменьшению количества карбидной составляющей. Максимальный износ наблюдается на границе между переходной зоной и зоной серого чугуна, где имеются мелкие пластинки графита, а кристаллы карбида отсутствуют.
Отдельные части калибра изнашиваются неравномерно в результате неодинаковых условий трения в разных местах очага деформации. Это связано с неравномерным скольжением металла по поверхности калибров, что объясняется переменной величиной катающих радиусов и условиями течения металла [7].
На рис. 3 представлены эпюры износа калибров среднесортного стана 350 АО «Северсталь», построенные по данным износа через каждые 5 мм по периметру калибра с фиксацией количества прокатанного металла в данном калибре.
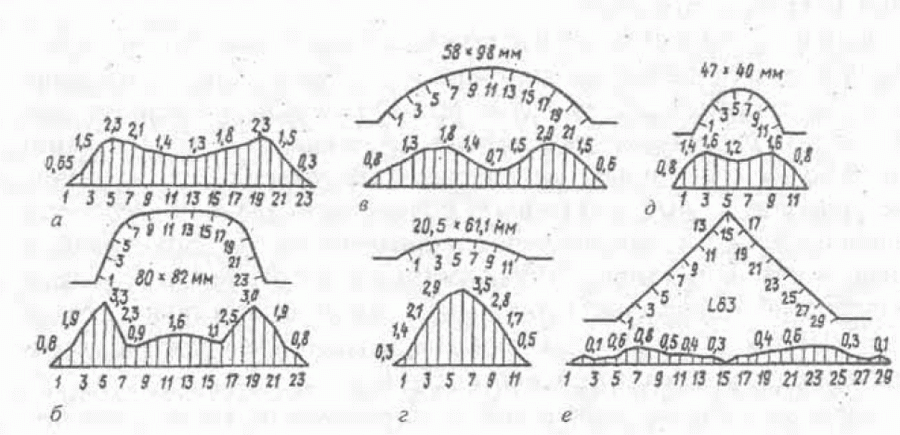
Рис. 3 Эпюры износа валков стана 350 [2]
На рисунке видно, что при прокатке на гладкой бочке появляются две зоны максимального износа, расположение которых ответствует углам задаваемой полосы, имеющим пониженную температуру и, следовательно, повышенное сопротивление деформации (рис. 3, а)
Максимальный износ ящичных калибров (рис. 3, б) наблюдается по их стенкам. По дну износ оказывается почти вдвое меньшим. Состояние поверхности изношенного калибра свидетельствует о скольжении металла по поверхности стенок калибра, обусловленного течением металла под действием сил, ограничивающих уширение, и разностью окружных скоростей по стенке калибра.
Овальные калибры (рис. 3, в), в которые задается заготовка квадратного сечения, имеют две симметрично расположенные области максимального износа, соответствующие углам задаваемого квадрата.
Максимальный износ овального калибра, которому предшествует ребровой овал (рис. 3, г), происходит по средней части калибра, к краям калибра износ плавно уменьшается.
Износ калибров ребрового овала (рис. 3, д) происходит более равномерно, чем износ овальных калибров. Участки максимального износа расположены симметрично на некотором расстоянии друг от друга.
Минимальный износ угловых калибров валков VI, VIII, LX и X клетей наблюдается в вершине их угла. К краям полки износ постепенно увеличивается.
Отделочные калибры валков XII и XIV клетей имеют такой же характер износа, что и угловые калибры (рис.3, е). Это объясняется тем, что в ребровом калибре валков XI клети наблюдается усиленный износ стенки калибра [2].
3. Методика и принципы нанесения функционально-ориентированных покрытий роликов прокатных станов
Учитывая особенности износа различных роликов прокатных станов, можно установить, что перспективным подходом к разработке технологии нанесения покрытий являются функционально-ориентированные технологии.
Функционально-ориентированная технология изготовления изделия машиностроения — это специальная технология, которая основана на точной топологически ориентированной реализации необходимого множества алгоритмов технологического воздействия орудий и средств обработки в необходимые микро, макро зоны и участки изделия, которые функционально соответствуют условиям их эксплуатации в каждой отдельной его зоне. Использование функционально-ориентированных технологий для изделий машиностроения позволяет максимально повысить их общие эксплуатационные параметры за счет местного увеличения технических возможностей и свойств отдельных элементов, поверхностей и/или зон изделия в зависимости от функциональных местных особенностей их эксплуатации. При этом изделия машиностроения, изготавливаемые по предлагаемым технологиям, максимально адаптируются по своим свойствам к особенностям их эксплуатации и проявляют свой полный потенциал возможностей в машине. Следует отметить, что предлагаемый новый класс технологий усложняет процесс изготовления изделий, но в целом обеспечивает качественно новую совокупность свойств и меру полезности изделий машиностроения при эксплуатации. Это дает возможность существенно повысить технико-экономические показатели эксплуатации и использования машин и технических систем. На рис. 4 показаны основные этапы синтеза функционально-ориентированных технологических процессов. Последовательность и методология базируются на замкнутой рекуррентной структуре [3]
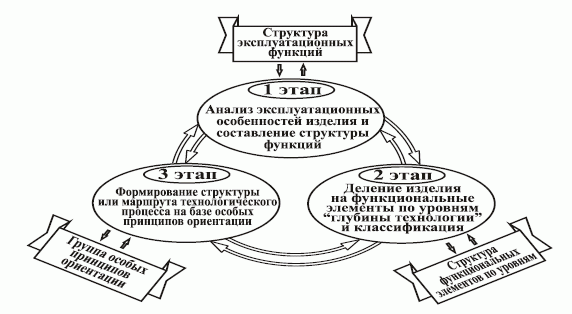
Рис. 4. Основные этапы синтеза функционально-ориентированных технологий [3]
Основными особенностями функционально-ориентированных технологий является то, что технологические воздействия орудий обработки на изделия и процесс обеспечения заданных и требуемых свойств изделий выполняется на следующих уровнях: на уровне всего изделия в целом; на уровне участков; на уровне составляющих; на уровне зон; на уровне макрозон; на уровне микрозон; на уровне нанозон.
При этом заданные, требуемые и предельные свойства изделий обеспечиваются за счет ориентации технологических воздействий потоков материи, энергии и информации на базе следующих восьми особых принципов [3,8]:
- Функционального соответствия особенностей действия элементарной функции в каждом функциональном элементе изделия, характеристик реализации технологических воздействий и параметров обеспечения необходимых свойств этом функциональном элементе изделия на каждом уровне глубины технологии.
- Топологического соответствия геометрических параметров функционального элемента изделия, в котором действует элементарная функция при эксплуатации, геометрическим параметрам зонального элемента реализации технологических воздействий потоков материи, энергии и информации на изделие и геометрических параметров зонного элемента обеспечения необходимых свойств на каждом уровне глубины технологии.
- Количественного соответствия множества функциональных элементов, в которых действует множество различных элементарных функций при эксплуатации, множеству реализации технологических воздействий и множеству элементов обеспечения необходимых свойств в функциональных элементах изделия на каждом уровне глубины технологии.
- Адекватной зависимости пространственных особенностей действия элементарной функции при эксплуатации, технологических воздействий и эксплуатационных свойств в пространстве каждого функционального элемента изделия на каждом уровне глубины технологии.
- Адекватной зависимости временных особенностей действия элементарной функции при эксплуатации, временных или пространственных особенностей реализации технологических воздействий и временных эксплуатационных свойств в каждом функциональном элементе изделия на каждом уровне глубины технологии.
- Структурного соответствия действия множества элементарных функций, реализации множества технологических воздействий и выполнения множества свойств в функциональных элементах изделия из условия обеспечения заданных, требуемых или предельных свойств всего изделия на каждом уровне глубины технологии.
- Адекватного структурно-функционального соответствия свойств в пространстве и во времени каждого функционального элемента заданному, требуемому или предельному потенциалу общих свойств всего изделия в целом на каждом уровне глубины технологии.
- Адекватного структурно-функционального соответствия свойств в окрестностях каждого функционального элемента в пространстве и во времени заданному, требуемому или предельному потенциалу общих свойств всего изделия в целом на каждом уровне глубины технологии.
На основе разработанных принципов выполняется синтез функционально-ориентированных технологий и изготовление изделий, которые обеспечивают полную адаптацию изделия и его элементов по эксплуатационным свойствам к условиям эксплуатации. Изготовление изделий на основе функционально-ориентированных технологий обеспечивает возможность реализации их полного потенциала функциональных возможностей при эксплуатации. Это существенно повышает технико-экономические показатели изготовления и эксплуатации изделий.
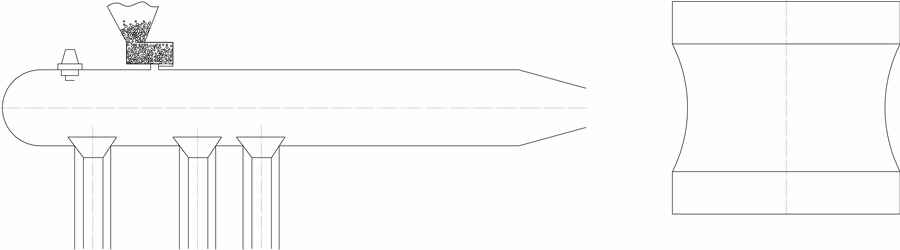
Рис. 5 Функционально-ориентированное детонационное нанесение покрытий
Таким образом, исследуя ряд функций, которые выполняет рабочая поверхность ролика прокатного стана, можно разбить ее на несколько зон. Разбитие происходит в зависимости от неравномерных влияний по длине поверхности ролика. Поэтому необходим индивидуальный подход к каждому ролику, к которому применяется функционально-ориентированная технология. В данном случае изучается неравномерный износ и температурное влияние на поверхность ролика. К каждой выбранной зоне необходимо подобрать оптимальные режимы обработки, в том числе и состав покрытия, которое наносится на изделие. Для повышения производительности возможно использование принципа концентрации, а также интенсификации режимов обработки и сокращение вспомогательного времени.
Выводы
Функционально-ориентированные технологии являются перспективными для многих областей применения, в том числе и для роликов прокатных станов. Главная особенность этого подхода – лучшая адаптация изделия к условиям эксплуатации. Это, в свою очередь, значительно повышает срок службы роликов, так как уменьшается и становится равномерным процесс износа по длине бочки ролика, увеличивается время между перевалками, и как следствие, повышается производительность прокатного стана.
Положительную тенденцию в повышении износостойкости можно отметить, изучая опыт предприятий, разрабатывающих технологии нанесения износостойких покрытий роликов прокатных станов. Так, наблюдается повышение стойкости изделия в несколько раз, в зависимости от метода и режимов нанесения покрытий, от условий эксплуатации и материала подложки.
Из отрицательных явлений можно отметить усложнение процесса разработки технологии для обработки изделия в целом. Также усложняется сама технология и оборудование, что ведет к увеличению себестоимости изделия, но экономический эффект достигается за счет увеличения срока службы ролика прокатного стана и повышения производительности прокатного оборудования.
Список источников
- Бартенев С.С., Федько Ю.П., Григоров А.И. Детонационные покрытия в машиностроении.—Л.: Машиностроение, Ленингр. отд-ние, 1982.—215с.
- Яковлев Р.А. Расчет на износ узлов трения прокатных станов. Учебное пособие по курсу «Основы динамики и надежности прокатных станов». — Под ред. А.Г. Колесникова. — М.: Изд-во МГТУ им. Н.Э. Баумана, 2004. — 52с.
- Михайлов А.Н. Основы синтеза функционально-ориентированных технологий.—Донецк: ДонНТУ, 2009. — 346 с.
- Зборщик А.М. Конспект лекций по дисциплине «Новые материалы в металлургии». — Донецк: ГВУЗ «ДонНТУ», 2008.–253с.
- Портал Приазовского государственного технического университета [электронный ресурс]. — Режим доступа: http://www.pstu.edu...
- Сайт предприятия РУП «Технопарк БНТУ «Метолит» [электронный ресурс]. — Режим доступа: http://www.otnp.metolit.by...
- Чекмарев А.П., Гречко В.П., Гетманец В.В., Ховрин Б.В. Прокатка на мелкосортных станах. — М.: Изд-во «Металлургия», 1966. -363с.
- Михайлов А.Н. Общие особенности функционально-ориентированных технологий и принципы ориентации их технологических воздействий и свойств изделий. // Машиностроение и техносфера XXI века. Сборник трудов XIV международной научно-технической конференции в г. Севастополе 17-22 сентября 2007 г. В 5-ти томах.–Донецк: ДонНТУ, 2007. Т. 3. С. 38-52.