Реферат по теме выпускной работы
Содержание
- Введение
- 1. Актуальность темы
- 2. Цель и задачи исследований
- 3. Методика проведения исследований
- 4. Расчет схемы нагружения усилий
- 5. Конструкция стендовой установки
- Выводы
- Список источников
Введение
Создание средств комплексной механизации с повышенной, по сравнению с существующими, энерговооруженностью является общим научно-техническим направлением во всех отраслях промышленности.
Повышение максимальных моментов электродвигателей, обуславливающее соответствующий рост теоретической производительности комбайнов, при ограниченности габаритов машин по высоте, вызывает увеличение нагруженности редукторов исполнительных органов и затрудняет решение вопросов обеспечения требуемой надежности элементов зубчатых передач. Недостаточная, в ряде случаев, несущая способность зубчатых передач очистных комбайнов по изгибу сдерживает применение электропривода с повышенной энерговооруженностью. Повышение несущей способности передач является в связи с этим одним из резервов возможного увеличения производительности машины.
1. Актуальность темы
Несмотря на большой обьем исследований в области совершенствования зубчатых передач, вопрос повышения несущей способности и долговечности зубчатых колес очистных комбайнов является весьма актуальным.
Во всех угольных бассейнах страны набольшее распространение в высокопроизводительных лавах получили очистные комбайны со шнековыми исполнительными органами. Комбайны со шнековыми исполнительными органами составляют примерно 90% из всех машин, выпускаемых Горловским машиностроительным заводом им. С.М.Кирова для работы в лавах с полого-падающими пластами.
Применение рабочего органа шнекового типа обусловило ряд конструкторских особенностей многокорпусных редукторов очистных комбайнов и их зубчатых передач. Анализ конструкций зубчатых передач комбайнов со шнековыми исполнительными органами, а также рассмотрение научных работ по исследованиям, показывает, что отсутствие необходимого обьема экспериментальных данных о неравномерности распределения напряжений по ширине зубчатого венца и соответствующих теоретических обобщений не позволили, в ряде случаев, достаточно обоснований принимать параметры продольной модификации рабочих поверхностей зубьев передач. Излом зубьев зубчатых колес очистных комбайнов является самым опасным видом повреждений, так как приводит к аварии машины и длительной остановке технологического процесса выемки угля. Длительный же перерыв в работе высокопроизводительной лавы из-за аварии комбайна обуславливает снижение добычи угля на сотни тысяч тонн. Одной из главных причин большинства повреждений зубчатых колес очистных комбайнов включая излом является сосредоточение нагрузки на части зуба, вызванное неточностями изготовления зубчатых колес и корпусных деталей, деформация элементов передачи под нагрузкой, а также недостаточной жесткостью конструкции последних. Данная работа посвящена решению ряда вопросов, связанных с созданием высокопроизводительных и надежных в работе очистных комбайнов со шнековыми исполнительными органами[1].
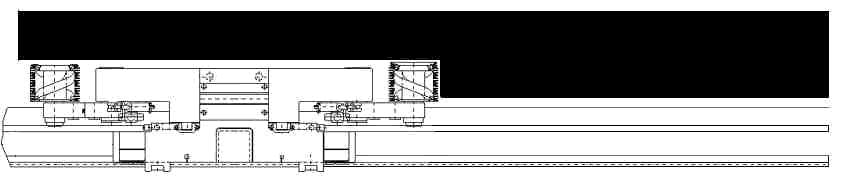
Рисунок 1 – Процесс добычи угля очистным комбайном (анимация: 9 кадров, 5 циклов повторения, 115 килобайт).
2. Цель и задачи исследований
Целью данной работы является разработка теоретических положений и методики выбора рациональных параметров продольной модификации зубьев колес цилиндрических прямозубых колес очистных комбайнов со шнековыми исполнительными органами, обеспечивающие снижение максимальных напряжений изгиба и обуславливающих возможность увеличения энерговооруженности и производительности машины.
Для обеспечения поставленной цели в работе требуется решить следующие основные задачи:
1. Исследование величин и распределения изгибных напряжений в зубьях колес передач серийно выпускаемых очистных комбайнов при нагруженности элементов привода исполнительных органов близкой к эксплуатационной и сравнение их с расчетными по существующим методикам.
2. Исследование характера изменения напряжений изгиба на переходных поверхностях зубьев в процессе зацепления пары зубьев при различных уровнях нагруженности передачи.
3. Разработка методики выбора рациональных параметров продольной модификации зубьев и ее экспериментальная проверка[2].
3. Методика проведений исследований
Методика определения максимальных напряжений на переходных поверхностях зубьев в процессе их зацепления и исследования распределения напряжений по ширине зубчатого венца заключалась в следующем:
1. Редукторы исполнительных органов комбайнов комплектовались «измерительными» зубчатыми колесами, на зубья которых в нескольких сечениях по ширине опасной по изгибу зоне на переходной поверхности на стороне сжатия были наклеены тензометрические элементы.
2. На специальных стендовых установках имитировалась нагруженность элементов привода комбайнов близкая по уровню нагруженности в условиях эксплуатации. Исследования проводились при нескольких схемах на работы машин, отличающихся между собой направлением перемещения машины и высотой пачки угля, разрушаемой отстающим шнеком.
3. Исследования проводились при нескольких уровнях нагруженности трансмиссий.
Максимальный уровень нагрузки соответствовал полному использованию потенциальных возможностей электродвигателя.
4. Максимальные напряжения на переходных поверхностях зубьев определялись путем тензометрии при повороте «измерительной» пары зубьев с постоянной скоростью в течение полного цикла зацепления.
5. Одновременно производилась регистрация величин моментов сил сопротивления в приводах исполнительных органов и осуществлялась запись углового перемещения одного из исследуемых элементов передачи[3].
Основной особенностью методики являлась имитация в лабораторных условиях эксплуатационной нагруженности приводов при различных схемах работы машин, что дало возможность при исследованиях напряженного состояния учета всех реальных деформаций узлов редукторов. Вследствие малой жесткости подвижных сопряжений, а также в результате деформаций опор, валов и других деталей имеет место в ряде случаев значительный перекос зубьев в плоскости зацепления, который определяется не только усилиями в зацеплении, но и нагрузками, обусловленными консольным расположением исполнительных органов, механизмом перемещения, опорами комбайна на конвейер и др[4].
4. Расчет схемы нагружения усилий
Внешние нагрузки имитировались с учетом усилий на резцах исполнительных органов со стороны разрушаемого забоя. При имитации нагруженности состояния редукторной группы комбайна шнекового типа пространственная система усилий на исполнительном органе заменялась одной силой, прилагаемой шнеку. При этом величина и расположение этой силы в пространстве создают моменты сил сопротивления относительно одного из торцов шнека равные соответствующим моментам, обусловленным пространственной системой сил. Условие соответствия нагружения органа машины на стенде его нагруженности при эксплуатации имеет вид:
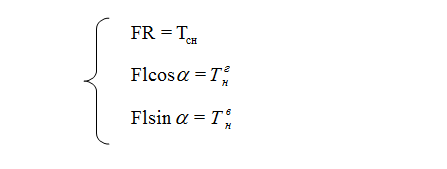
F – усилие, эквивалентное пространственной системе сил; R – расстояние линии действия усилия F от оси вращения шнека; l – расстояние линии действия эквивалентного усилия от плоскости «завального» торца шнека; α – угол наклона линии действия усилия F к горизонту; Tсн – среднее значение крутящего момента на шнеке за его оборот;Тнг Тнв – среднее значение моментов, изгибающих орган соответственно в горизонтальной и вертикальной плоскостях.
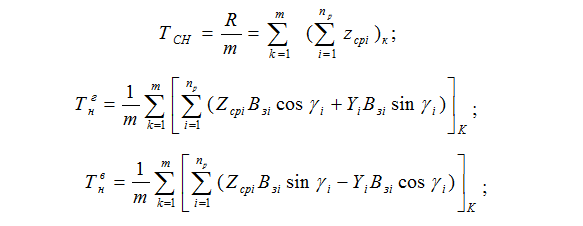
где m – количество рассматриваемых положений шнека за его оборот; np – количество резцов, одновременно находящихся в контакте с забоем в к-том положении шнека; Zсрі – усилие, резания і-того резца; Yі – усилие, отжимающее резец от забоя; Bзі – расстояние і-того резца от «завального» торца шнека;γі – угол, определяющий положение і-того резца на окружности шнека.
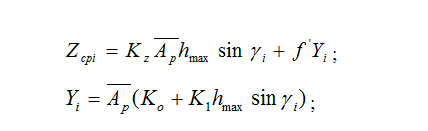
где Kz – интегральный коэффициент, учитывающий влияние хрупкопластичных свойств угля, его отжима, обнажения забоя, углов установки резцов, средней ширины среза на усилие резания при определенной схемы набора резцов и выбранном инструменте; Ар – сопротивляемость угля резанию в неотжатой зоне массива; hmax – максимальная толщина среза; f’– коэффициент сопротивления резанию; Ko,K1 коэффициенты, учитывающие соответственно влияние толщины среза и сопротивляемости угля резания на усилие, отжимающее резец от забоя. Расчет параметров нагруженности привода F, l и α для имитации эксплуатационной нагруженности комбайна производился из условия полного использования энергетических возможностей электропривода. Исходными данными являлись сопротивляемость угля резанию Ар и принятый из результатов эксперементальных исследований устойчивый момент электродвигателя[5].
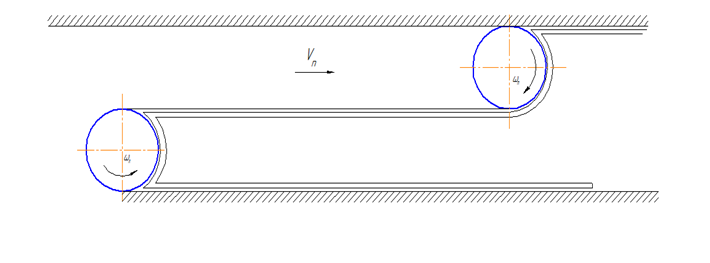
а).
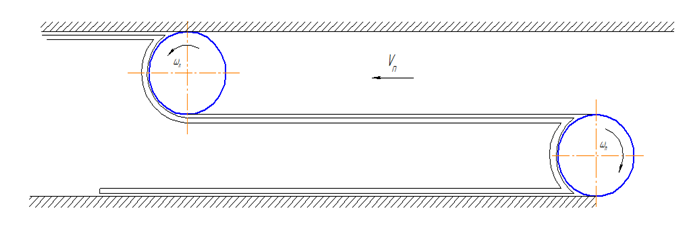
б).
Рисунок 2 – Схемы работы очистных комбайнов РКУ-13 при разном направлении Vп.
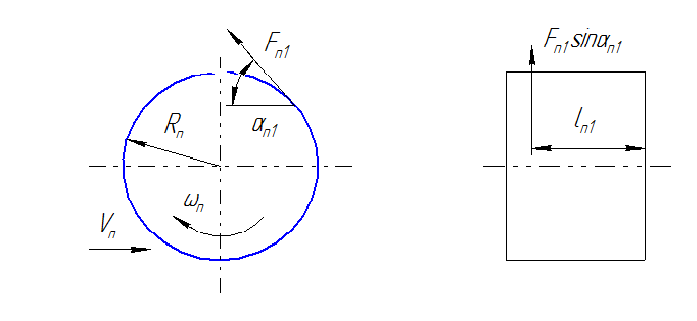
Рисунок 3 – Схема нагружения правого шнека комбайна РКУ 13 при его работе по схеме а).
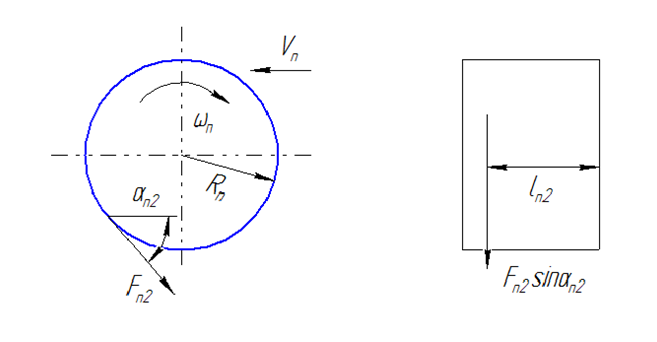
Рисунок 4 – Схема нагружения правого шнека комбайна РКУ 13 при его работе по схеме б).
5. Конструкция стендовой установки
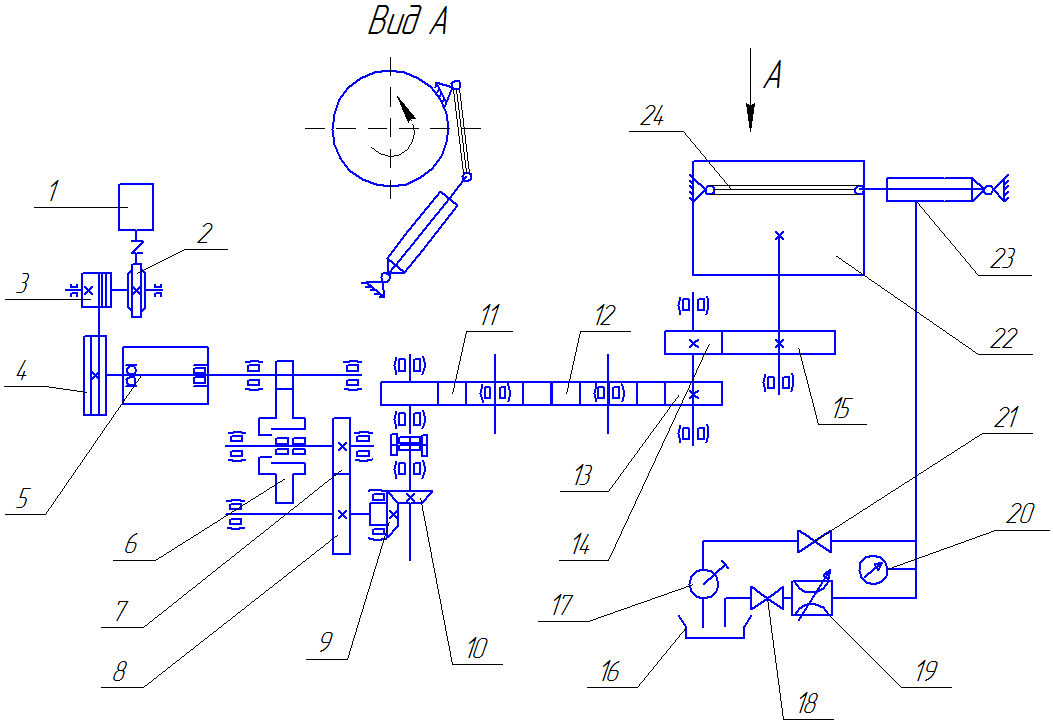
Рисунок 5 – Схема стендовой установки для исследований зубчатых колес комбайна РКУ 13.
Принципиальная схема стендовой установки для исследований зубчатых колес комбайна РКУ13 представлена на рисунке 4. Основным элементом установки является натурный образец привода исполнительного органа комбайна с присоединенным к нему электродвигателем. Способ крепления электродвигателей исключает искажение реальных деформаций при воздействии внешних нагрузок. Опорные лыжи комбайна опираются н6а секцию рештачного става, лежащего свободно на основании стенда, что соответствует реальной работе машины. Установка приводится в действие электродвигателем, который через червячный редуктор при помощи барабана сматывает трос со шкива, жестко расположенного на валу электродвигателя, и обеспечивает вращение первого вала редуктора. Нагрузка на исполнительном органе, имитирующая сопротивление со стороны разрушаемого угля, создается гидродомкратом, шток которого цепью соединяется со шнеком таким образом что обеспечивается постоянство угла наклона гидродомкрата по отношению к шнеку в процессе поворота. В зависимости от крепления к шнеку гиидродомкрат работает либо на растяжение, либо на сжатие, обеспечивая тем самым различные схемы работы шнека, имеющие место при эксплуатации.
При растяжении или сжатии штока гидродомкрата из его штоковой полости или поршневой выжимается масло, которое по шлангам сбрасывается в масляную ванну, Нагрузка на исполнительном органе обуславливается сопротивлением проходу жидкости через дроссель, который обеспечивает возможность регулирования усилия домкрата. Контроль осуществляется по показаниям манометра и по отклонению луча записи соответствующей величины на экране осциллографа.
Возврат домкрата системы нагружения и всей трансмиссии в исходное положение по окончании каждого цикла нагружения осуществляется насосом, который перекачивает масло из ванный в соответствующую полость гидродомкрата. Возврат системы проводится при отключенной муфте, соединяющей редуктор с валом электродвигателя. Краны предназначены для изменения направления потока жидкости. При включении двигателя лебедок и создания требуемого сопротивления на шнеке при помощи нагрузочного приспособления вся трансмиссия поворачивается под нагрузкой[6].
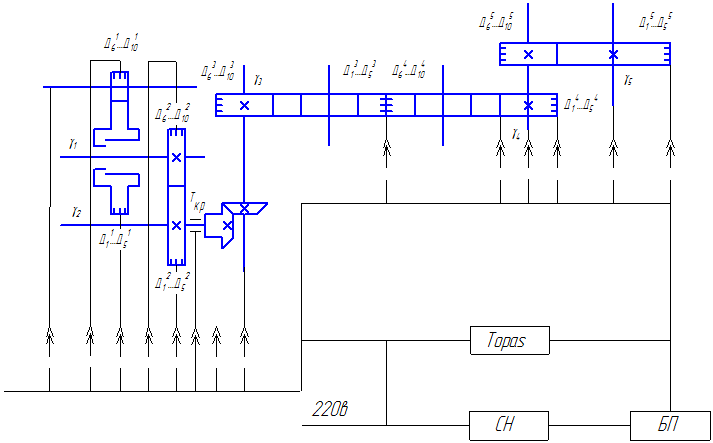
Рисунок 6 – Схема измерений при исследованиях зубчатых передач комбайна РКУ 13.
.Схема измерений при стендовых исследованиях прямозубых цилиндрических передач комбайна РКУ13 представлены соответственной на рисунке 6. В соответствии с методикой проведения исследований замеры напряжений на переходных поверхностях зубьев производятся последовательно для всех исследуемых пар. С целью определения распределения напряжений по ширине зубчатого венца «измерительные зубья» оборудуются пятью тензорезисторами наклеенными вдоль зуба. На рисунке 6 указаны места установки для тензорезисторов на «измерительных зубьях». Для измерения относительных угловых перемещений применяются датчики угла поворота. Стабилизация напряжений в блоках питания аппаратуры БП производится стабилизатором напряжений СН.Регистрация измеряемых величин производится двенадцатиканальным светолучевым регистратром Topas.
Выводы
Разработана методика опеределения максимальных напряжений на переходных поверхностях зубьев и их распределения по ширине зубчатого венца прямозубых цилиндрических колес очистных комбайнов в течении цикла зацепления пар зубьев.
Обоснованы схемы нагружения приводов исполнительных органов шнекового типа, позволяющие с достаточной степенью точности имитировать в лабораторных условиях нагруженность элементов приводов, имеющую место в условиях эксплуатации.
На базе натурных образцов приводов к исполнительным органам комбайна РКУ13 были создана стендовая установка, обеспечивающая возможность осуществления имитации нагруженности элементов трансмиссий машин при работе комбайнов в подобных условиях.
Конструкция стендовых установок и применяемая измерительная аппаратура обеспечивают возможность регистрации максимальных напряжений на переходных поверхностях в различных сечениях по ширен зубчатых колес всех прямозубых цилиндрических передач комбайнов в течении цикла зацепления пары зубьев при различной ее нагруженности.
Передачи зубчатые цилиндрические эвольвентные.Расчет на прочность ГОСТ 21534-75М.,1976, 61с
Список источников
- Повышение производительности и долговечности угледобывающих комбайнов. Донецк,1974, 212с
- Заблонский К.И. Жесткость зубчатых передач.Киев,"Техника",1967, 259с.
- Кудрявцев В.Н. Зубчатые передачи.М.-Л. Машгиз,1957, 263с.
- Устиненко В.Л. Напряженное состояние зубьев цилиндрических прямозубых колес.М.,"Машиностроение",1970, 89с.
- Комбайны очистные,выбор параметров и расчет сил резания и подачи на исполнительных органах.ОСТ 12.47.001.-73М,184с.
- Брюшин Н.В. Снижение максимальных напряжений изгиба в зубьях цилиндрических прямозубых колес очистных комбайнов со шнековыми исполнительными органами:диссертация,Донецк,1978, 198с.
- Передачи зубчатые цилиндрические эвольвентные.Расчет на прочность ГОСТ 21534-75М.,1976, 61с