Abstract
Contents
- Introduction
- 1. Theme urgency
- 2. Goal and tasks of the research
- 3. Results of studies
- Conclusion
- References
Introduction
Process automation is one of the key elements in the overall system operation and development of any modern coal mine. Substitution in this area of human intellectual work machine, science-based distribution of functions between man and computer in the management of technology leads to improved efficiency and quality of decision-making process, reduce the time of implementation, cost reduction, fuller use of available reserves of industrial enterprise, providing the maximum level of efficiency and flexibility, substantially limit the number of engineering and technical personnel, etc.
Coal mining is one of the main economic activities in the Donetsk region, where most of the mining enterprises. At the same time the mining industry consumes vast quantities of energy for heating only the mine, which is done using coal-fired boilers, is the largest consumer of energy. Along with this, for mining companies the task of finding alternative sources of heat for boiler installations.
1. Theme urgency
Temperature of air entering the mine in winter, should be not less than +2 °C. To do this, use a variety of air heater installation. In this regard, saving fuel consumed by the needs of the mine, is an urgent task. In mining enterprises have the ability to operate furnaces designed to burn low-grade high-ash coal in a low-temperature fluidized bed. This setting allows the use of low-quality coal ash up to 75-80 %, and also eliminates the possibility of failure of the air heater installation by eliminating the intermediate heat – steam or water.
However, widespread adoption of this technology a mining constrained by shortcomings of automated control furnace, which is a series of separate control loops formed on the basis of outdated controls of the R-25. This is caused by the relevance of the automatic control system of the boiler plant with low-temperature fluidized bed. Development of the system will improve the efficiency of the boiler plant, resulting in decrease energy costs.
2. Goal and tasks of the research
Given the above, we can formulate the goal of work – an increase of boiler installation with low-temperature fluidized bed by synthesis of automatic control system of the boiler plant, which ensures the maintenance of the required technological parameters of the furnace at a predetermined level.
The overall objective of the work is specified the following tasks:
- Study the technological features of the boiler plant/
- Analysis of existing technical solutions in the field of automation of boiler plants with low-temperature fluidized bed
- Improvement of the management of the boiler plant.
3. Results of studies
As previously noted, in this regard, saving fuel consumed by the needs of the mine, in mining enterprises have the ability to operate furnaces designed to burn low-grade high-ash coal in a low-temperature fluidized bed. This setting allows the use of low-quality coal ash up to 75-80 %, and also eliminates the possibility of failure of the air heater installation by eliminating the intermediate heat – steam or water.
However, widespread adoption of
such technology constrained by shortcomings furnace control system.
Capacity control system of boiler plant with low-temperatured
fluidized bed
is only the contour Fuel
.
The transfer function of the contour Fuel
is a serial link connection
delay and vehicle delay element of the first order (box 1, figure 1)
and has the form [10]:
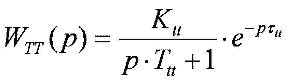
Conditions for modeling the
time constants in the expression are as
follows:Ttt=100 sec,
τtt=60 sec.
Unfortunately, this does not allow the circuit to
achieve the required quality management indicators (characteristic 1
fig. 2), so it is advisable to offer double-loop temperature
control
system with correction of the fluidized bed through the air. The
transfer function of the fluidized bed contour Air
has the form [10]:
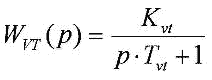
The transfer function of the fluidized bed:
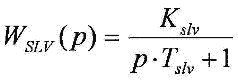
Structure of a two-management system is shown in figure 1, block 2.
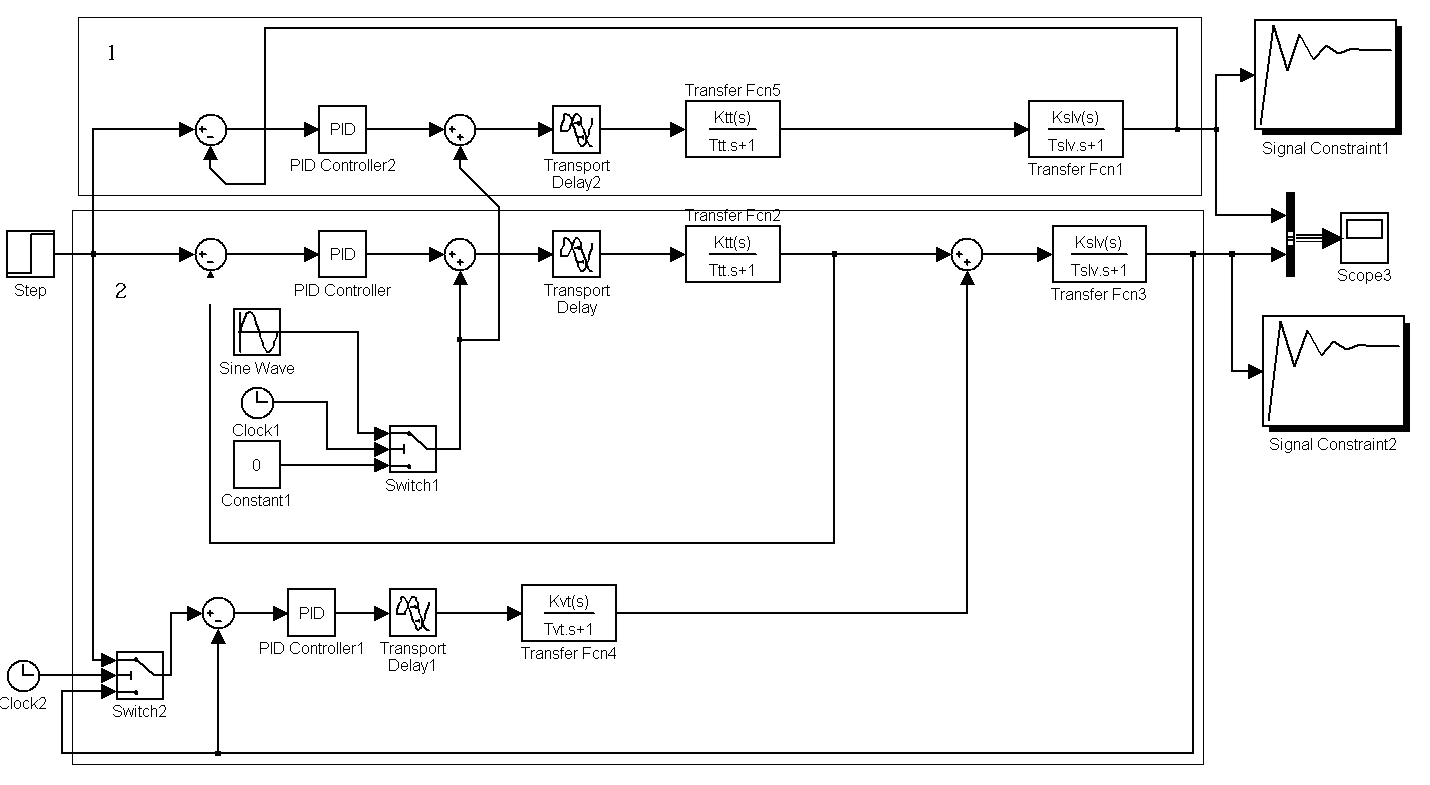
Figure 1 – Structure of a two-management control system of boiler plant with low-temperatured fluidized bed
A comparative modeling of traditional and proposed two-management system of boiler plant with low-temperatured fluidized bed is presented in figure 2.
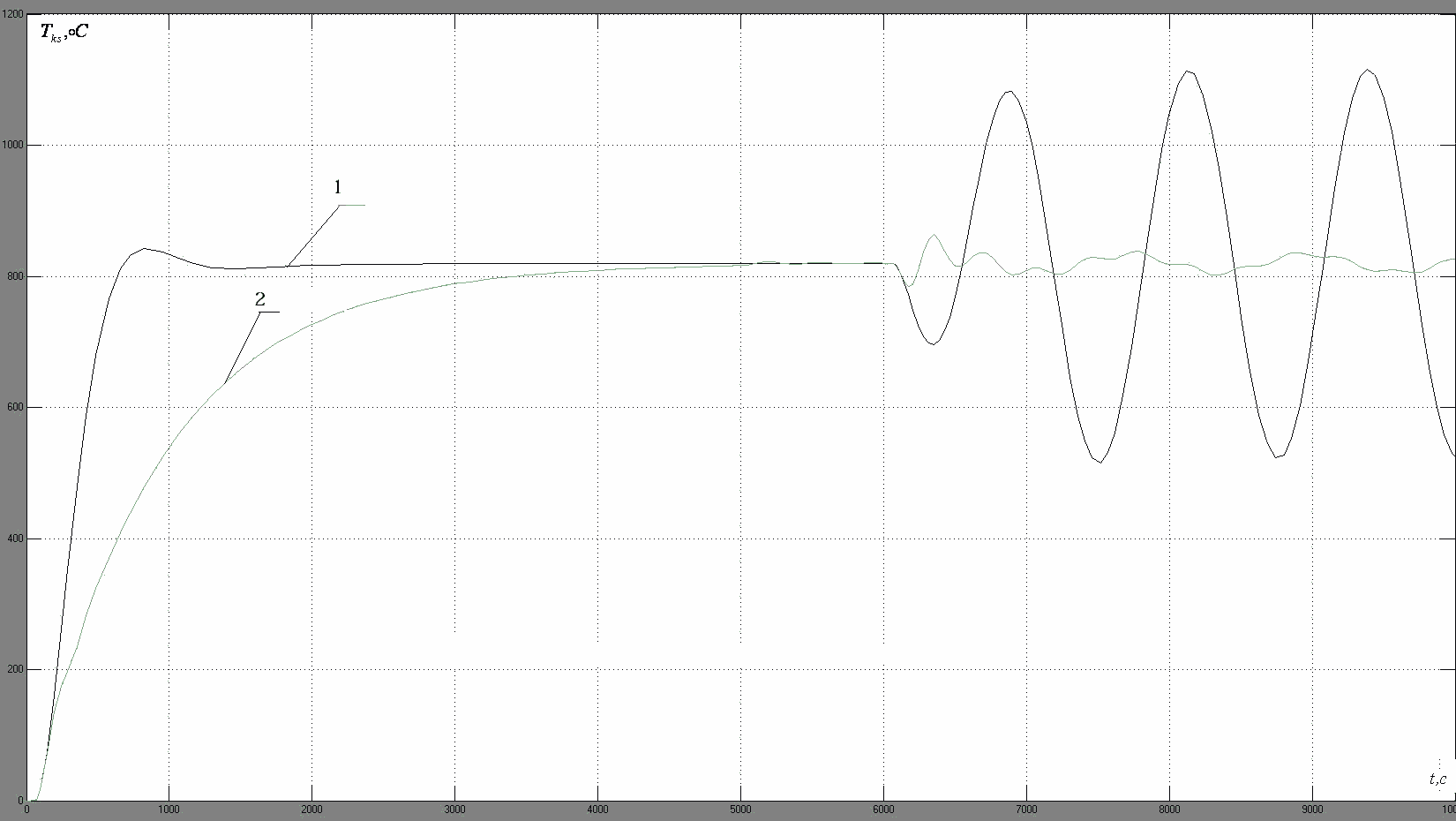
Figure
2 –Results of the comparative
modeling of traditional and proposed two-management system of
boiler
plant with low-temperatured fluidized bed
(1 – simulation system Fuel
;
2 – system modeling
with
correction of air)
From these graphs the transient can be concluded that the proposed control system of a two-management system of boiler plant with low-temperatured fluidized bed significantly higher resistance to disturbing influences than the traditional system.
Conclusion
Currently acquires relevance rational and efficient use of energy resources for heating, sanitary and household needs of mining companies. Thus, the process of fuel combustion in a fluidized bed has won recognition and gaining ground. Since its introduction solved equally important task for the use of low-grade and high-ash coals. In the following technical solutions for creating inserts will be widely used not only in the mines of the coal industry, but also in other branches of managing Ukraine.
However, despite the progress made, to ensure reliable operation of the boiler installations with a boiler plant with low‐temperatured fluidized bed, is required to solve a number of automation tasks: maintaining the desired temperature fluidized bed combustor to reduce the ignition time and reduce particulate emissions to the atmosphere.
When writing this abstract the master’s qualification work is not completed. Final date of completion is January 2015. Full text of the work and materials on the topic of work can be obtained from the author or his supervisor after the specified date.
References
- Вискин Ж. В. Сжигания угля в кипящем слое и утилизация его отходов, Донецк 1997, – 283 с.
- Кравцов В. В. Экономическое использование угля в теплоэнергетике / Кравцов В. В., Махмудов А. Г., Харченко А. В. – Донецк: ДонГТУ, 1999. – 320с.
- Сургай М. Пріоритети у вугіллі й ціна їхньої недооцінки / М. Сургай // Віче. Журнал Верховної Ради України. Київ, 2008. № 3. – С. 40-45.
- Забродский С. С. Высокотемпературные установки с псевдоожиженным слоем (общие вопросы разработки и исходные закономерности) / Забродский С. С. М.: «Энергия», 1971. 328 с.
- Кинетика и динамика выгорания высокозольного энергетического угля в кипящем пласте под давлением: Автореф. дисс… канд. техн. наук: 05.14.06 / О.И. Топал / НАН Украины. Ін-т газа. – К., 2000 – 19 с. – укр.
- Майстренко А. Ю. Горение и газификация высокозольных углей в кипящем слое. – Дисс. к-та техн. наук. – М./ЭНИН им. Г.М. Кржижановского, 1991, - 270 с.; ил.
- Наладка средств автоматизации и автоматических систем регулирования: Справочное пособие. А. С. Клюев, А. Т. Лебедев, С. А. Клюев, А. Г. Товарное; Под ред. А. С. Клюева. –2-е изд., перераб. и доп.- М.: Энергоатомиз дат, 1989.- 368 с.
- Шафрановский В. А. Справочник наладчика автоматики котельных установок. – Симферополь: Таврия, 1987. – 176 с.
- Роддатис К. Ф. Справочник по котельным установкам малой производительности / К. Ф. Роддатис, А. Н. Полтарецкий М.: Энергоатомиздат, 1989. 488 с.
- Неежмаков С. В. Исследование математической модели топки кипящего слоя шахтного автономного воздухоподогревателя / С. В. Неежмаков // Праці Таврійського державного агротехнологічного університету. - Вип. 8. Т. 10. - Мелітополь: ТДАТУ, 2008. С. 173 – 180.