Реферат по теме выпускной работы
Содержание
- Введение
- 1. Актуальность темы
- 2. Цель и задачи исследования
- 3. Характеристика котельной установки НТКС как объекта автоматизации
- 4. Обзор существующих технический решений в области автоматизации котельных установок НТКС
- 5. Усовершенствование структуры системы управления котельной установки НТКС
- Выводы
- Список источников
Введение
Автоматизация технологических процессов является одним из ключевых звеньев в общей системе функционирования и развития любого современного угольного предприятия. Замена в этой сфере интеллектуального труда человека машинным, научно‐обоснованное распределение функций между человеком и компьютером в процессе управления технологией приводит к повышению эффективности и качества принимаемых технологических решений, сокращению сроков их реализации, снижению затрат, более полному использованию имеющихся резервов производственной системы предприятия, обеспечению максимального уровня оперативности и гибкости, существенному ограничению численности инженерно‐технического персонала и т.д.
Угольная промышленность является одним из основных видов хозяйственной деятельности в Донецком регионе, где сосредоточено большинство горных предприятий. В то же время горная промышленность потребляет огромное количество энергетических ресурсов только лишь на теплоснабжение шахты, которое осуществляется с помощью угольных котельных, являющихся крупными потребителем энергии. Наряду с этим для горных предприятий стоит задача поиска альтернативных источников тепла для котельных установок.
1. Актуальность темы
Температура воздуха, поступающего в шахту в зимний период, должна составлять не менее +2 °С. Для этого используют различные калориферные установки. В связи с этим экономия топлива, расходуемого на нужды шахты, является актуальной задачей. На горных предприятиях есть возможность эксплуатировать топочные устройства, предназначенные для сжигания низкосортных высокозольных углей в низкотемпературном кипящем слое (НТКС). Данная установка позволяет использовать низкокачественный уголь зольностью до 75‐80 %, а также исключает возможность выхода из строя калориферной установки, благодаря отсутствию промежуточного теплоносителя – пара или воды.
Однако широкое внедрение такой технологии на горном предприятии сдерживается несовершенством системы автоматизированного управления топкой, которая представляет собой ряд обособленных контуров управления, выполненных на основе устаревших регуляторов типа Р‐25. Этим обуславливается актуальность создания системы автоматического управления котельной установки НТКС. Разработка данной системы позволит повысить эффективность функционирования котельной установки, в результате чего снизятся энергетические затраты.
2. Цель и задачи исследования
Учитывая выше сказанное, можно сформулировать цель работы – повышение работы котельной установки НТКС путем синтеза системы автоматического управления котельной установки, которая обеспечивает поддержания требуемых технологических параметров топки на заданном уровне.
Общая цель работы конкретизируется следующими задачами:
- Исследование технологических особенностей котельной установки;
- Анализ существующих технических решений в области автоматизации котельных установок НТКС;
- Усовершенствование системы управления котельной установки топки НТКС.
- возможно использование низкореакционных и высокозольных углей с зольностью до 75‐80 %, что недостижимо при других способах сжигания. Это обусловлено стабилизацией процесса горения топлива из‐за наличия в слое большого количества нагретых твёрдых частиц с высокой удельной теплоёмкостью;
- повышается тепловая мощность котлоагрегатов, находящихся в эксплуатации, и снижается металлоемкость вновь создаваемых благодаря интенсификации процессов тепломассообмена в кипящем слое;
- обеспечивается сжигание топлива с широким диапазоном зольности в одном топочном устройстве;
- увеличивается надежность работы топочных устройств котлоагрегатов ввиду отсутствия движущихся колосниковых решеток, а также упрощается конструкция;
- повышается КПД котлов при сжигании низкосортных и высокозольных углей;
- улучшаются условия труда обслуживающего персонала за счет возможности автоматизации процесса сжигания и поддержания температуры горения топлива ниже начала размягчения золы, обеспечивающей бесконгломентарное его сжигание;
- достигается высвобождение обслуживающего персонала на жаротрубных котлах устаревшей конструкции;
- за счет пониженной температуры слоя (до 1000 °С) обеспечивается уменьшение выбросов оксидов серы (на 70‐80 %) и оксидов азота (на 30‐40 %).
- неравномерность времени пребывания в псевдоожиженом слое частиц твердой фазы и порции ожижающего агента. Одинаково возможны как быстрый проскок частиц, так и их нахождение в слое дольше среднего статистического времени пребывания;
- повышенный унос твердых веществ с уходящими газами и, следовательно необходимость установки более мощных пылеулавливающих устройств (двухступенчатой очистки) дымовых газов, особенно при большом содержании мелких фракций в составе горной массы, подаваемой в топку;
- ограниченность рабочих скоростей дутьевого воздуха пределами, соответствующими началу псевдоожижения твердой фазы и ее уносу из слоя;
- значительная эрозия оборудования в зоне псевдоожиженого слоя, особенно в случае использования частиц с высокими абразивными свойствами;
- достаточно жесткие требования к фракционному составу топлива, нарушение которых ведет к возможности зашлаковки топки;
- возможность истирания, растрескивания и других нежелательных изменений свойств материалов инертной засыпки и составляющих пород горной массы, ведущих к невосполнимому уносу золы из слоя. Вследствие этого накладываются ограничения по нижнему пределу зольности сжигаемой горной массы без принятия дополнительных мер для поддержания постоянного уровня кипящего слоя;
- ограничение по нижнему пределу регулирования минимальной тепловой мощности;
- увеличение удельного расхода электрической энергии на единицу получаемого тепла;
- повышение требований к техническому уровню обслуживающего персонала.
- влажность углей оказывает незначительное влияние на процесс сжигания их в кипящем слое. Однако из условий обеспечения работоспособности забрасывателя допустимая влажность не должна превышать 10‐12 %. Кроме того, при повышенной влажности усложняется подача топлива из‐за залипания его в бункере;
- зольность сжигаемых углей может находится в пределах от 15 до 80 %. Значение зольности ниже 15 % может привести к уменьшению количества инертного наполнителя и, следовательно, к нарушению процесса сжигания в кипящем слое;
- плавкость золы оказывает значительное влияние на устойчивость работы топки с низкотемпературным кипящим слоем, т. к. от температуры начала размягчения золы зависит допустимая температура в слое по её верхнему пределу регулирования. Для донецких углей температура начала размягчения золы составляет около 1000 °С;
- фракционный состав топлива из условий обеспечения псевдоожижения слоя не должен превышать 13 мм. Однако, при большом количестве мелких фракций (0‐1 мм) увеличиваются потери тепла с механическим недожогом в уносе. Поэтому оптимальным является размер топливных частиц 5‐6 мм;
- выход летучих оказывает влияние на температуру воспламенения топлива. Высокий выход летучих обеспечивает более низкую температуру воспламенения угля, снижая расход жидкого топлива во время розжига.
- невысокая надежность;
- необходимость применения дополнительных звеньев (дифференциаторов) для образования взаимосвязанных контуров регулирования;
- необходимость иметь отдельный регулятор на каждый контур регулирования;
- сложность ремонта и обслуживания аппаратуры, невозможность ремонта приборов Р‐25 в условиях предприятия;
- малофункциональность приборов Р‐25;
- использование морально устаревшей элементной базы.
- Вискин Ж. В. Сжигания угля в кипящем слое и утилизация его отходов, Донецк 1997, – 283 с.
- Кравцов В. В. Экономическое использование угля в теплоэнергетике / Кравцов В. В., Махмудов А. Г., Харченко А. В. – Донецк: ДонГТУ, 1999. – 320с.
- Сургай М. Пріоритети у вугіллі й ціна їхньої недооцінки / М. Сургай // Віче. Журнал Верховної Ради України. Київ, 2008. № 3. – С. 40-45.
- Забродский С. С. Высокотемпературные установки с псевдоожиженным слоем (общие вопросы разработки и исходные закономерности) / Забродский С. С. М.: «Энергия», 1971. 328 с.
- Кинетика и динамика выгорания высокозольного энергетического угля в кипящем пласте под давлением: Автореф. дисс… канд. техн. наук: 05.14.06 / О.И. Топал / НАН Украины. Ін-т газа. – К., 2000 – 19 с. – укр.
- Майстренко А. Ю. Горение и газификация высокозольных углей в кипящем слое. – Дисс. к-та техн. наук. – М./ЭНИН им. Г.М. Кржижановского, 1991, - 270 с.; ил.
- Наладка средств автоматизации и автоматических систем регулирования: Справочное пособие. А. С. Клюев, А. Т. Лебедев, С. А. Клюев, А. Г. Товарное; Под ред. А. С. Клюева. –2-е изд., перераб. и доп.- М.: Энергоатомиз дат, 1989.- 368 с.
- Шафрановский В. А. Справочник наладчика автоматики котельных установок. – Симферополь: Таврия, 1987. – 176 с.
- Роддатис К. Ф. Справочник по котельным установкам малой производительности / К. Ф. Роддатис, А. Н. Полтарецкий М.: Энергоатомиздат, 1989. 488 с.
- Неежмаков С. В. Исследование математической модели топки кипящего слоя шахтного автономного воздухоподогревателя / С. В. Неежмаков // Праці Таврійського державного агротехнологічного університету. - Вип. 8. Т. 10. - Мелітополь: ТДАТУ, 2008. С. 173 – 180.
3. Характеристика котельной установки НТКС как объекта автоматизации
Кипящий слой – совокупность полидисперсных твердых частиц, через которые продувается ожижающий воздух со скоростью выше первой критической скорости (скорости ожижения) и ниже второй критической скорости(скорости уноса или пневмотранспорта). На равномерность ожижения слоя влияет прежде всего разница удельных плотностей твердой фазы и ожижающего воздуха. при ожижении воздуха, даже при скоростях больших первой критической скорости ожижения кипящий слой может быть неравномерным для всех составляющих слоя [1].
По сравнению с традиционным слоевым сжиганием твердого топлива, технология НТКС обладает рядом преимуществ [2]:
В тоже время рассматриваемый способ сжигания угля имеет следующие недостатки [1]:
Недостатки использования рассмотренной технологии носят, прежде всего, технологический характер, достоинства же обуславливают актуальность использования сжигания низкосортных и высокозольных углей в топках НТКС [2].
Технологическая схема котельной установки НТКС представлена на рисунке 1 .
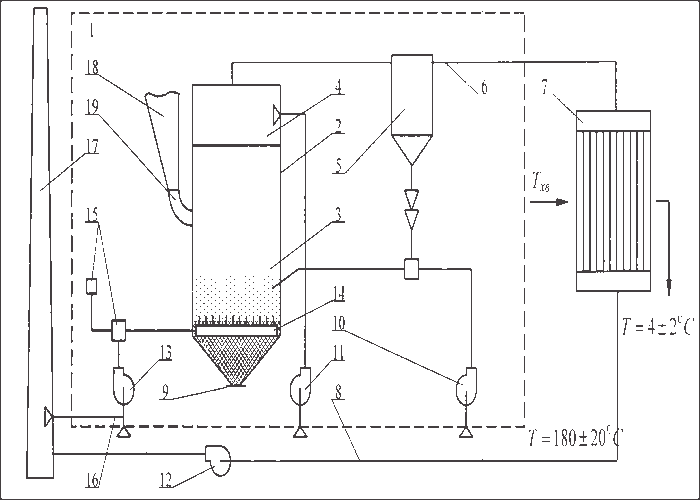
Рисунок
1 – Технологическая схема котельной установки НТКС
(анимация: 5 кадров, интервал 1000 мс, 133 килобайт)
На рисунке 1 обозначено:
1 – здание котельной;
2 – теплогенератор низкотемпературного кипящего слоя на
твердом топливе;
3 – топочная камера;
4 – камера смешения;
5 – двухступенчатая система газоочистки;
6 – газопровод горячих газов;
7 – воздухоподогреватели;
8 – газопровод холодных газов;
9 – система золоудаления;
10 и 11 – вентиляторы, соответственно, возврата уноса и
разбавочного воздуха;
12 – дымосос;
13 – вентилятор дутьевого воздуха;
14 – провальная трубная колпачковая воздухораспределительная
решетка;
15 – растопочное устройство;
16 – газопровод рециркуляции дымовых газов;
17 – дымовая труба;
18 – угольный бункер;
19 – забрасыватель;
Тхв – температура холодного воздуха.
Для нагрева подаваемого в шахту воздуха предусматривается использование тепла, получаемого от сжигания низкосортного высокозольного угля в топке 3.
Дымовые газы, являющиеся теплоносителем с температурой кипящего слоя, из топочной камеры направляются в камеру смешения 4, в которую центробежным вентилятором 11 подается также и холодный воздух. Забор этого воздуха осуществляется вне топочного здания. В результате смешения температура газовоздушной смеси снижается до 500 °С.
После камеры смешения за счет разрежения, создаваемого дымососом 12 газовоздушная смесь проходит двухступенчатую систему очистки от твердых частиц 5. Далее газовоздушная смесь по газоходам 6 направляется в трубчатые воздухонагреватели 7. Пройдя по трубам воздухоподогревателя, газовоздушная смесь передает тепло наружному воздуху, поступающему через жалюзийные решетки в межтрубное пространство и воздухоподогреватели за счет общешахтной депрессии.
Воздух после воздухоподогревателей может быть нагрет до температуры 2…50 °С. Непосредственно нагретый воздух или воздушная смесь, образующаяся после его разбавления засасываемым холодным наружным воздухом, с температурой не ниже 2…6 °С поступает в ствол шахты.
Отработанная газовоздушная смесь с температурой 100…250 °С транспортируется по газоходу 8 и выбрасывается в атмосферу через дымовую трубу 17.
Регулирование и стабилизация температуры в слое в интервале 850…950 °С для топок НТКС является основным условием технологического процесса сжигания угля. При повышении температуры слоя выше 950 °С возникает возможность размягчения золы, что приводит к зашлоковке топки, т.е. к аварийной ситуации. при понижении температуры до 700 °С возможно прекращение горения топлива в виду того, что данный диапозон температур поддерживать в ручном режиме не предоставляется возможными, температура слоя регулируется автоматически, путем изменения количества подаваемого топлива и воздуха. Регулирование осуществляется изменением скорости движения ленты забрасывателя в зависимости от температуры слоя, измеряемой термоэлектрическим термометром, от которого подается сигнал на регулятор, управляющий электрическим исполнительным механизмом, воздействующим на вариатор забрасывателя [1].
Характеристики твердого топлива влияют на процесс горения следующим образом [4- 6]:
4. Обзор существующих технический решений в области автоматизации котельных установок НТКС
В настоящие время для автоматического регулирования применяется базовая аппаратура автоматизации системы «Контур», выполненная на базе регулирующего прибора P‐25. Технологическая схема включает в себя четыре контура регулирования:
1. Регулятор топлива управляет подачей угля в топку в зависимости от температуры слоя. Контур «Температура» содержит датчик (термопару), регулятор и пусковую аппаратуру для управления однооборотным электродвигателем механизма регулирования топливоподачи. Автоматическое регулирование подачи топлива в топку производится по сигналам от термопары, установленной в кипящем слое.
2. Регулятор воздуха стабилизирует подачу дутьевого воздуха путем поворота лопаток направляющего аппарата. Контур «Воздух» состоит из датчика, пусковой аппаратуры для управления однооборотным электродвигателем механизма поворота направляющего аппарата в подводящей трубе дутьевого вентилятора.
3. Регулирование высоты слоя по расходу воздуха осуществляется выгрузкой золы из топки (контур «Высота слоя»). Измерение высоты кипящего слоя для поддержания ее на заданном уровне осуществляется косвенно и основано на повышении давления воздуха перед топкой в зависимости от аэродинамического сопротивления слоя при этом своевременное удаление золы золоудалителем обеспечивает необходимую высоту слоя.
4. Регулятор разряжение тяги регулирует разряжение в топке путем поворота лопаток направляющего аппарата дымососа (контур «Тяга»). Для выброса газообразных продуктов горения в атмосферу дымосос создает постоянное разряжение, обеспечиваемое регулятором «Разряжение» с высокой точность. Разряжение измеряется в верхней части топки датчиком, вырабатывающим электрический сигнал, который поступает на регулятор. С регулятора сигнал поступает на пусковую аппаратуру управления. При измерении разряжения в топке на величину, превышающую зону нечувствительности усилителя регулятора, электродвигатель исполнительного механизма перемещает направляющий аппарат дымососа до тех пор, пока не восстановит заданное разряжение.
Прибор типа Р‐25
предназначен для применения в схемах автоматического регулирования
различных теплотехнических процессов. Прибор выполняет следующие
функции [8]:
а) суммирование сигнала от источника информации (датчиков первичных
приборов);
б) введение сигнала задания и усиление сигнала отклонения;
в) формирование ПИ‐закона регулирования совместно с ИМ
постоянной скорости;
г) формирование сигналов постоянного и переменного тока для управления
ИМ постоянной скорости;
д) формирование сигналов постоянного и переменного тока для управления
ИМ постоянной скорости;
е) преобразование сигналов от
дифференциально‐трансформаторного датчика положения ИМ в
сигнал постоянного тока.
Регулирующий прибор Р‐25 реализует в комплекте с ИМ постоянной скорости закон ПИ‐регулирования с демпфированием входною сигнала. Приборы Р‐25 работают в комплекте с дифференциально‐трансформаторными датчиками, термосопротивлениями, термоэлектрическими термометрами и унифицированными токовыми преобразователями на 0‐5, 0‐20 мА, а также 0‐10 В (последний подается на специальный вход). При включении по специальной схеме приборы могут работать с реостатными и ферродинамическими датчиками.
Функциональная схема прибора Р‐25 приведена на рисунке 2 [7].
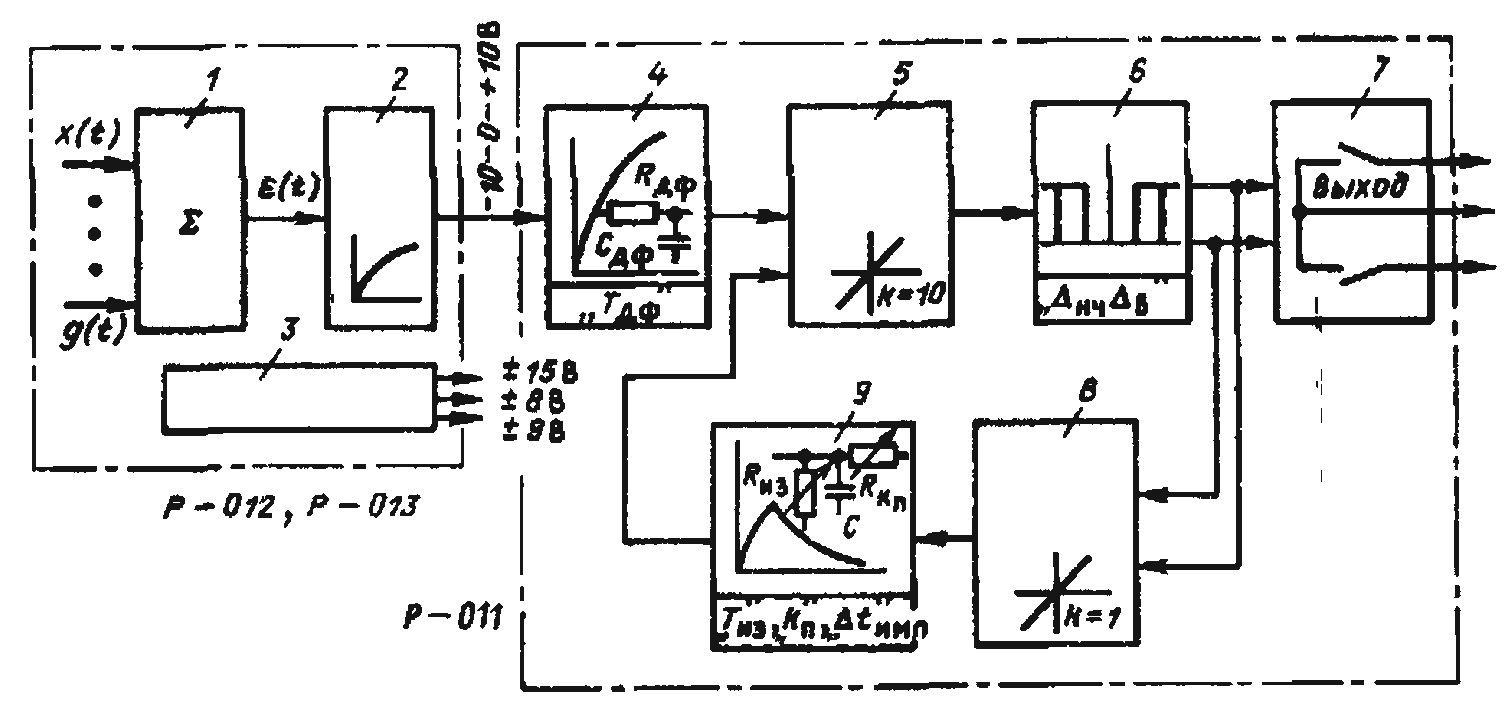
Рисунок 2 – Функциональная схема прибора Р‐25
Она содержит измерительный блок Р‐012 или Р‐013 и peгулирующий блок Р‐011, одинаковый для всех модификаций приборов. Измерительный блок Р‐012 включает в себя сумматор 1, нормирующий операционный усилитель 2, построенный на интегральной микросхеме (ИМС) и стабилизированный источник напряжения постоянного тока 3. В сумматоре измерительного блока Р‐012 суммируются сигналы от датчиков и сигнал от моста «задатчик – корректор». Суммарный сигнал выпрямляется, фильтруется и поступает на вход нормирующего операционного усилителя.
Электронный блок Р‐011 предназначен для формирования закона регулирования и коммутации выходных цепей. Он включает в себя демпфер 4, суммирующий усилитель 5, схему сравнения 6, выходные ключи 7, операционный усилитель обратной связи 8, инерционное звено блока отрицательной обратной связи 9.
Сигнал рассогласования с измерительного блока поступает на демпфер 4, представляющий собой RC‐звено с регулируемой постоянной времени демпфирования.
С выхода демпфера сигнал поступает на вход суммирующего усилителя 5, выполненного на ИМС, где суммируется с сигналом обратной связи, поступающим с выхода звена 9. Усилитель 5 имеет передаточную функцию апериодического звена первого порядка с коэффициентом усиления . Далее сигнал поступает на один из двух триггеров схемы сравнения 6 в зависимости от полярности сигнала на выходе усилителя 5. Схема сравнения имеет регулируемые зону нечувствительности и зону возврата (неоднозначности). При сигнале рассогласования, превышающем порог срабатывания, на выходе схемы сравнения скачком появляется сигнал, который подается на выходные ключи 7 и в цепь отрицательной обратной связи. В зависимости от полярности сигнала на входе электронного блока открывается один из выходных ключей и коммутируется внешняя цепь
Однополярные сигналы схемы сравне¬ния преобразуются в операционном усилителе 8, построенном на интегральной микросхеме и имеющем коэффициент усиления К=1, в двухполярные и подаются на вход инерционного звена 9. Инерционное звено 9, построенное на высокоомном усилителе, сдвоенном полевом транзисторе и интегральной микросхеме, выполняет функции звена отрицательной обратной связи.
Сигнал отрицательной обратной связи с выхода эвена 9 поступает на вход суммирующего усилителя 5 для компенсации сигнала рассогласования. При этом сигнал на входе схемы сравнения уменьшается до значения порога срабатывания. Выходные ключи закрываются, и сигнал обратной связи становится равным нулю. Наступает пауза.
Длительность первого импульса зависит от значения сит нала рассогласования и скорости компенсации его сигналом отрицательной обратной связи. Время паузы определяется значением постоянной времени изодрома.
После отключения сигнала обратной связи сигнал с выхода звена 9 начинает плавно уменьшаться, а сигнал на входе схемы сравнения возрастать до порога срабатывания, в результате чего открывается выходной ключ и подается сигнал обратной связи в звено 9. Цикл повторяется.
Чередование импульсов и пауз будет продолжаться до тех нор, пока сигнал рассогласования не окажется в пределах зоны нечувствительности. Таким образом, блок формирует на своем выходе последовательность импульсов и пауз. Интегрирование импульсов при помощи ИМ постоянной скорости позволяет получить пропорционально‐интегральный закон регулирования.
Длительность импульсов на выходе звена 9 регулируется при помощи сигнала дополнительной положительной обратной связи, поступающего на вход усилителя 5 и расширяющего зону возврата схемы сравнения при срабатывании блока. Во время паузы этот сигнал отсутствует. При выключении звена обратной связи Р‐011 выполняет функции трехпозиционного релейного элемента.
Опыт эксплуатации аппаратуры системы «Контур» и регуляторов Р‐25 в частности позволил выявить ее основные недостатки [9]:
Таким образом, можно сделать вывод о несовершенстве существующей аппаратуры и необходимости внедрения нового средства управления, которое позволит не только регулировать процесс горения, но и управлять розжигом твердого топлива, процессом подготовки его перед заполнением бункера, а также выполнять функции контроля, сигнализации, защиты и блокировок.
5. Усовершенствование структуры системы управления котельной установки НТКС
Как отмечалось ранее, в связи с экономией топлива, расходуемого на нужды шахты, на горных предприятиях есть возможность эксплуатировать топочные устройства, предназначенные для сжигания низкосортных высокозольных углей в низкотемпературном кипящем слое. Данная установка позволяет использовать низкокачественный уголь зольностью до 75‐80 %, а также исключает возможность выхода из строя калориферной установки, благодаря отсутствию промежуточного теплоносителя – пара или воды.
Однако широкое внедрение такой технологии сдерживается несовершенством системы управления топкой. Регулирование производительности топки НТКС осуществляется только по контуру «Топливо». Передаточная функция по контуру «Топливо» представляет собой последовательное соединение звена транспортного запаздывания и апериодического звена первого порядка (блок 1 рис.3) и имеет вид [10]:
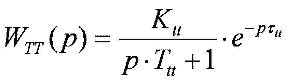
где Ktt
– передаточный коэффициент, ккал/м³;
Ttt, τtt
– постоянные времени, с.
Для условий моделирования постоянные времени в данном выражении составили:Ttt=100 с, τtt=60 с. К сожалению, данный контур не позволяет добиться требуемых качественных показателей управления (характеристика 1 рис. 4), поэтому целесообразно предложить двухконтурную систему управления температурой кипящего слоя с коррекцией по воздуху. Передаточная функция кипящего слоя по контуру «Воздух» имеет вид [10]:
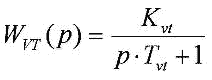
где Kvt
– передаточный коэффициент, ккал/м³;
Tvt
– постоянная времени,Tvt=200 c
Передаточная функция кипящего слоя:
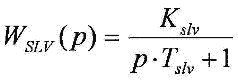
Структура двухконтурной системы управления приведена на рисунке 3 блок 2.
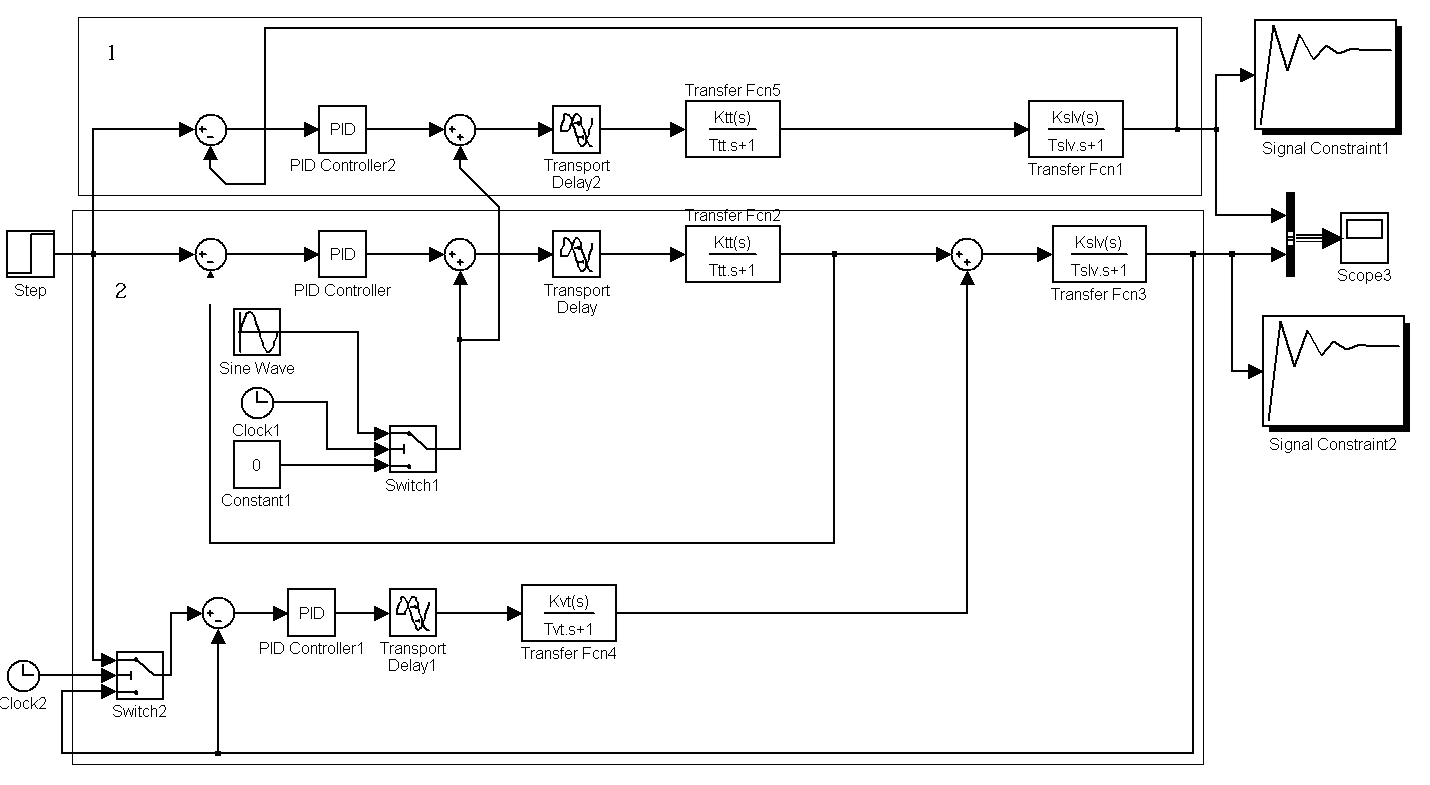
Рисунок 3 – Структура двухконтурной системы управления топки НТКС
Результаты сравнительного моделирования традиционной и предложенной двухконтурной системы управления топки НТКС представлены на рисунке 4.
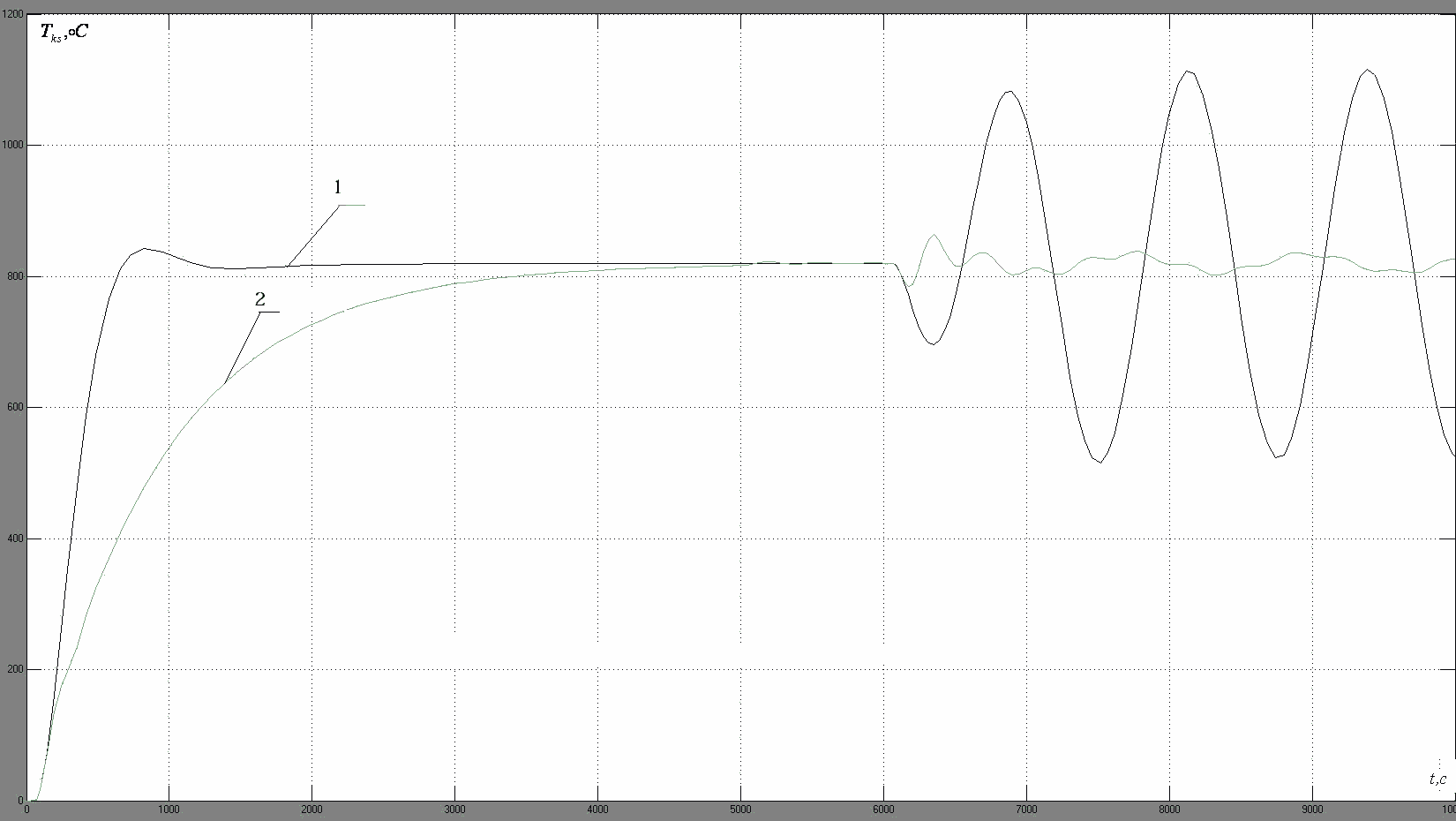
Рисунок
4 – Результаты сравнительного моделирования традиционной и
предложенной двухконтурной системы управления топки НТКС
(1 –моделирование системы по контуру
«Топливо»; 2 - моделирование системы с коррекцией
по воздуху)
Из представленных графиков переходного процесса можно сделать вывод, что у предложенной двухконтурной системы управления топкой НТКС значительно выше устойчивость к возмущающим воздействиям, чем у традиционной системы.
Из представленных графиков переходного процесса можно сделать вывод, что у предложенной двухконтурной системы управления топкой НТКС значительно выше устойчивость к возмущающим воздействиям, чем у традиционной системы.Выводы
В настоящее время приобретает актуальность рациональное и эффективное использование энергетических ресурсов на отопление, санитарно‐бытовые нужды горных предприятий. Таким образом, способ сжигания топлива в кипящем слое завоевал признание и получает все большее распространение. С его внедрением решается не менее важная задача по использованию низкосортных и высокозольных углей. В последующем технические решения по созданию топок найдут широкое применение не только на шахтах угольной промышленности, но и в других отраслях хозяйствования Украины.
Однако, несмотря на достигнутые успехи, для обеспечения надежной эксплуатация котельных установок с топкой НТКС, требуется решить ряд задач по автоматизации: поддержание требуемой температуры кипящего слоя, сократить время розжига топки, а также сократить выброс твердых частиц в атмосферу.
При написании данного реферата квалификационная работа магистра не завершена. Дата окончательного завершения работы – январь 2015 г. Полный текст работы и материалы по теме работы могут быть получены у автора или его научного руководителя после указанной даты.