Реферат по теме выпускной работы
Содержание
- Введение
- 1. Актуальность темы
- 2. Цель и задачи исследования
- 3. Обзор исследований и разработок
- 3.1 Снижение выбросов в углеподготовительном цехе
- 3.2 Снижение выбросов при загрузке коксових печей
- 3.3 Снижение выбросов при выдаче кокса
- 3.4 Пылеподавление при тушении кокса
- 4. Исследование экологических проблем и разработка мероприятий по повышению экологической безопасности при производстве кокса в условиях Макеевского коксохимического завода ЧАО «Макеевкокс»
- Выводы
- Список источников
Введение
В настояшее время на современных коксохимических заводах внедряются новые передовые малоотходные ресурсосберегающие технологии, позволяющие не только повысить качество производимого кокса, но и снизить потребление невозобновляемых природных ресурсов (уголь, природный газ), снизить образование выбросов, сбросов и отходов на выходе. Однако в Украине почти все оборудование предприятий коксохимической промышленности марально и физически устарело, это связано в первую очередь с тем, что в Украину не идет больших финансовых инвестиций на реконструкцию заводов. И как следствие предприятия не могут позволить себе устанавливать более современное оборудования для подготовки угольной шихты, производства кокса более высокого качества, его охлаждения, а также высокоэффективных очистных сооружений для очистки загрязненных отходящих газов, и обезвреживания отходов.
Ужесточение экологических требований к коксохимическим предприятиям, основным агрегатам и оборудованию, стало требовать от коксохимиков усилий для реконструкции и технического переоснащения предприятий по решению вопросов охраны воздушной и водной среды.
1. Актуальность темы
Предприятия коксохимической промышленности являются одними из основных источников поступления загрязняющих веществ в окружающую среду (ОС). В настоящее время в Украине функционирует 13 крупных коксохимических предприятия, 7 из которых сосредоточены в Донецкой области. Экологические проблемы усугубляются еще и тем, что эти предприятия расположены в регионах со значительной концентрацией промышленного производства и высокой плотностью населения. Крайне неблагоприятная экологическая обстановка, сложившаяся в последние годы в крупных металлургических центрах, в определенной степени обусловлена низкими темпами технического перевооружения коксохимической подотрасли, медленным внедрением в практику новых технологических процессов, современных агрегатов и оборудования.
Коксохимические заводы занимают ведущее место по выбросам вредных веществ среди предприятий черной металлургии. К ним относят пыль, оксиды азота, диоксид серы, оксид углерода, аммиак, фенол, бензол, нафталин, сероводород, цианистый водород и графит. Поэтому важнейшей социальной задачей, стоящей перед коксохимическими предприятиями, является повышение экологической безопасности производства, техническое переоснащение коксохимических предприятий, осуществление крупномасштабной программы строительства природоохранных объектов, внедрение современных экологически безопасных технологических процессов.
На современных заводах внедряют передовые технологии, позволяющие снизить выбросы загрязняющих веществ в атмосферу. К основным из них относят установки бездымной загрузки угольной шихты в камеры коксования, установки беспылевой выдачи кокса из камері коксования и сухого тушения кокса. Однако, в последнее время все большую актуальность приобретает совершенствование технологических процессов на всех стадиях производства кокса (подготовка, загрузка, коксование углей, выдача, охлаждение и сортировка кокса). Этим стадиям производства кокса принадлежит сейчас более 70 % залповых выбросов.
2. Цель и задачи исследования
Целью является разработка и внедрение рациональных технологий производства кокса, позволяющих повысить качество кокса и одновременно сократить вредные выбросы.
Основные задачи исследования:
- Изучить основные источники загрязнения окружающей среды на всех этапах производства кокса.
- Изучить современные отечественные и зарубежные технологии производства кокса: подготовки угольной шихты, загрузки ее в коксовую печь, процес коксования, выгрузка кокса из коксовой печи и его охлаждение.
- Рассмотреть возможные способы снижения выбросов загрязняющих веществ на всех этапах производства кокса.
- Дать характеристику факторам, влияющих на основные характеристики металлургического кокса, и разработать предложения по улучшению качества кокса.
- Поиск оптимальных путей совершенствования технологических процессов производства кокса.
- Рассчитать экономический и экологический эффект от внедрения технологии снижающих вредные выбросы и повышающих качество кокса
Объект исследования: Макеевский коксохимический завод ЧАО «Макеевкокс».
Предмет исследования: Технологические процессы подготовки угольной шихты, загрузки ее в коксовую печь, процес коксования, выгрузка кокса из коксовой печи и его охлаждение.
3. Обзор исследований и разработок
В настоящее время на коксохимических заводах применяется следующая классификация коксовых цехов в экологическом отношении:
- цехи, где нет никаких мероприятий по защите атмосферного воздуxa.
- цехи, где имеется бездымная загрузка угольной шихты, очистка отопительного газа от сероводорода до остаточного содержания 3,0 г/м3 и биохимическая очистка сточных вод перед их использованием на тушение кокса;
- цехи, где помимо указанных в п. 2 мероприятий имеется установка для беспылевой выдачи кокса.
3.1 Снижение выбросов в углеподготовительном цехе
В углеподготовительных цехах из углей, предназначенных для коксования, приготовляется угольная шихта заданного качества. При этом в соответствии с технологической схемой выполняются следующие операции: прием, разгрузка и складирование углей, дозирование, дробление, сепарация и смешение компонентой шихты. Все эти операции, а также транспортирование углей и шихты сопровождаются выделением в окружающий воздух угольной пыли, количество которой зависит от влажности угля. При колебаниях влажности угля в пределах 7,0-8,5% количество уносимой пыли практически постоянно и составляет при открытом складе угля без обработки штабелей связывающими веществами 350 г/т, при обработке штабелей раствором винилацетата или стиролбутадиеновой смолы 140 г/т, при наличии закрытого склада угля 60 г/т кокса.
Радикальным мероприятием по снижению выбросов при складировании углей является сооружение закрытого склада с эффективными системами аспирации и пылеулавливания: Запыленность воздуха рабочей зоны может быть уменьшена путем следующих мероприятий: герметизации пылящего оборудования; сооружения аспирационных систем, предназначенных для удаления запыленного воздуха; систем с эффективным пылеулавливающим оборудованием; устройством приточной вентиляции; блокировкой технологического оборудования с аспирационными системами; регулярной уборкой помещений и оборудования от осевшей пыли; систематическим контролем за состоянием воздуха производственных помещений. Одним из факторов, влияющих на запыленность воздуха производственных помещений, является уборка осевшей пыли с поверхностей полов, стен и оборудования. На коксохимических предприятиях наибольшее распространение получила мокрая уборка, что обусловлено взрывоопасными свойствами угольной пыли. Однако опыт сухого пылеулавливания на ряде предприятий показывает, что в принципе можно производить и сухую уборку. В этом случае целесообразно использовать централизованные пылесосные установки с водокольцевыми вакуум-насосами. Это позволит избавиться от водно- шламового хозяйства, упростить эксплуатацию системы, но потребует устройства разветвленной сети коммуникаций, очистки воздуха перед выбросом в атмосферу и решения вопросов утилизации уловленной сухой пыли.
До настоящего времени основным способом улавливания угольной пыли остается мокрый. В связи с этим на предприятиях наиболее распространены центробежные скрубберы, скоростные промыватели, циклоны с водяной пленкой; в ряде случаев применяются оригинальные конструкции, разработанные предприятиями. В последнее время появились ротоклоны. Сухие коллекторы, используемые в качестве первой ступени очистки, в большинстве случаев оборудуют устройствами для подачи и распыления воды. Эффективность улавливания угольной пыли в мокрых аппаратах весьма различна, что связано, по-видимому, как с плотностью орошения и качеством распыления жидкости, так и с дисперсностью улавливаемых частиц. Необходимость комплексного решения природоохранных проблем обусловливает перспективность сухих методов при обеспыливании газов и воздуха. Это подтверждает многолетний опыт эксплуатации сухих пылеуловителей на ряде предприятий (ОАО «Северсталь», АО «Испат-Кармет», ОАО «Магнитогорский металлургический комбинат»). В частности, циклоны СИОТ успешно эксплуатируются на Губахинском заводе более 25 лет для обеспыливания аспирационного воздуха при подготовке и обогащении угля. Степень очистки составляет 70-84%, что при фактической начальной запыленности < 200 мг/м3 вполне достаточно для достижения санитарных норм на выбросе в атмосферу. В циклонах диаметром 4000 мм после сушилок флотоконцентрата в АО «Западно-Сибирский металлургический комбинат» степень очистки достигает в среднем 88,5% при колебаниях начальной запыленности от 10 до 130 г/м3 и расходе очищаемых газов от 43,2 до 61,3 тыс. м3/ч.
К перспективным методам следует отнести применение электрофильтров. Как известно, в угольной промышленности и на тепловых электростанциях широко применяются электрофильтры УВП (угольный, вертикальный, пластинчатый). В последнее время вместо этих электрофильтров выпускаются аппараты УВВ (унифицированный, вертикальный, взрывобезопасный). Электрофильтры УВВ предназначены для улавливания угольной пыли с концентрацией до 60 г/м3 при температуре газа до 130 °С.
Применение таких сравнительно дорогих аппаратов, как электрофильтры, экономически оправдано при больших масштабах очистки. Общая производительность достаточно громоздкой установки ~ 1500 тыс. м3/ч. При начальной концентрации коксовой и агломерационной пыли порядка 1,42 г/м3 остаточная запыленность составляет 40-60 мг/м3 (т.е. средняя степень очистки ~ 96,5%).
Приемлемые результаты получены ВУХИНом при испытаниях конических циклонов. Избыточный газ-теплоноситель разбавляли воздухом до содержания кислорода 3-7% (объемы.), подогревали до 450-550 °С, подвергали каталитической очистке от органических соединений в реакторе кипящего слоя, а затем направляли в циклон на очистку от пыли. Степень улавливания тонкодисперсной пыли с концентрацией 4,8-6,9 г/м3составила около 90%.
В АО «НЛМК» также имеется опыт применения циклонов для обеспыливания аспирационного воздуха на закрытом складе угля. Степень улавливания угольной пыли в группах из трех циклонов диаметром 1,2 м составляет 96,8-97,0%.
Таким образом, наиболее эффективные технические решения проблемы улавливания угольной пыли - применение высокоэффективных сухих циклонов, а при проектировании новых предприятий децентрализованных систем с использованием электрофильтров
3.2 Снижение выбросов при загрузке коксових печей
При загрузке влажной угольной шихты в раскаленную печную камеру образуется ~5 м3 газов на каждую тонну загруженной шихты. Эти газы содержат 10-60 г/м3 взвешенных частиц угольной и полукоксовой пыли. В пересчете на 1 т производимого кокса выделение пыли при загрузке печей достигает 150-400 г/т, при этом количество выделяющейся пыли резко увеличивается с уменьшением влажности шихты < 7%.
Серьезные трудности возникают при загрузке термоподготовленной шихты. Для загрузки шихты, прошедшей термоподготовку, применение традиционных способов бездымной загрузки с отсосом газов загрузки в газосборники совершенно невозможно из-за увеличения уноса пыли в газосборники и связанного с этим ухудшения качества каменноугольной смолы и пека.Термическая подготовка шихты к коксованию заключается в нагреве ее до температуры 150-200 °С с целью снижения влажности и повышения насыпной плотности. В настоящее время используют в основном два метода нагрева шихты: газовым теплоносителем (в сушилках кипящего слоя и в трубах-сушилках) и нагрев шихты горячим кусковым коксом (совмещенный процесс термоподготовки шихты и сухого тушения кокса).
Например, в установке термической обработки шихты на коксовой батарее №7 АО «ЗСМК» в качестве первой ступени очистки теплоносителя после трубы-сушилки установлен батарейный циклон со 100 элементами диаметром 229 мм. На второй сту пени использован мокрый пылеуловитель. Громоздкость, ненадежность и недостаточная эффективность мультициклона (степень очистки 88%) требуют на следующих этапах испытания дополнить схему коническим циклоном. Расчетная степень очистки дополнительного циклона 76,5%, концентрация пыли уменьшается с 26-47 до 5,1 г/м3, что позволяет снизить остаточное содержание пыли на выбросе в атмосферу до 0,15 г/м3.
Совмещенный процесс термической подготовки шихты и сухого тушения кокса, разработанный ВУХИНом, имеет существенные преимущества как с точки зрения технологии и утилизации тепла, так и по своим экологическим показателям. Суть этой технологии (рисунок 1) заключается в смешивании измельченной влажной шихты с раскаленным кусковым коксом с последующим отделением нагретой шихты от потушенного кокса.
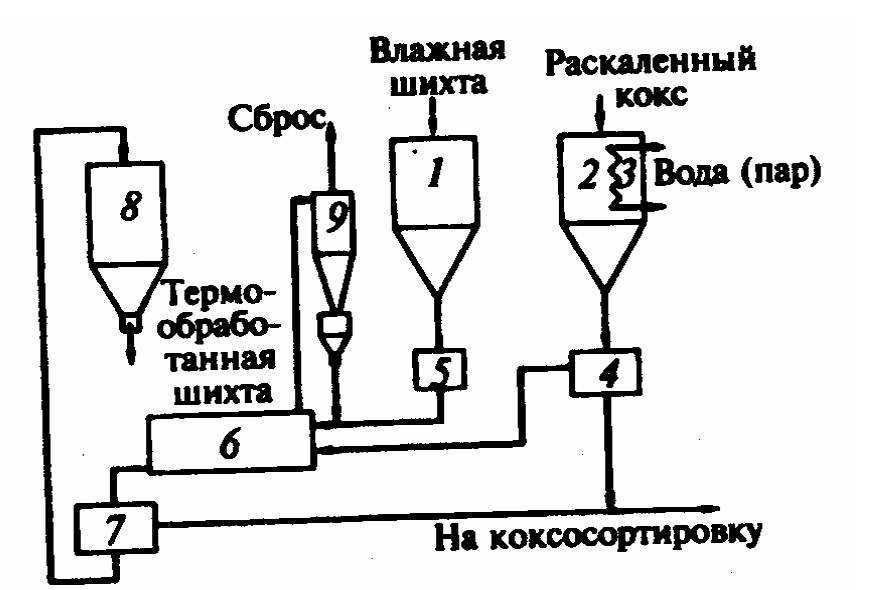
1-бункер исходной шихты; 2-бункер раскаленного кокса; 3-рекуператор избыточного тепла кокса; 4-рассев раскаленного кокса; 5-загрузчик исходной шихты; 6-теплообменный аппарат; 7-рассев углекоксовой смеси; 8-бункер термически подготовленной шихты; 9-циклон-отделитель угольной пыли
Рисунок 1 – Схема совмещенного процесса термоподготовки шихты и тушения кокса
Опытно-промышленные исследования этого процесса на установке производитель-ностью 10-12 т/ч проведены на Криворожском КХЗ. Процесс происходит в закрытом теплообменном аппарате, откуда водяные пары за счет естественной тяги поступают на очистку в циклон типа ЦН-15 и выбрасываются в атмосферу. К водяным парам, объем которых определяется влажностью шихты, вследствие неплотностей в аппаратах подсасывается воздух в количестве 25% от объема паров. Суммарный удельный объем выделяющихся газов при исходной влажности шихты 8,9-9,1% составляет 120-140 м3/т шихты, содержание пыли в этих газах в среднем -14 г/м3. Сбрасываемая пылегазовая смесь имеет температуру - 100 °С; находящиеся в ней частицы угольной пыли, являясь центрами конденсации, покрываются водяной пленкой, благодаря чему они коагулируют и легко улавливаются в циклоне. Степень очистки в циклоне достигает 99,2%, а остаточная концентрация пыли 110 мг/м3.
Применяемые за рубежом способы уменьшения пылегазовых выбросов, образующихся при загрузке печей, основаны на отводе в газосборник путем инжекции пара или надсмольной воды под высоким давлением в стояк, а также отсосе газов из печи и очистке перед выбросом в атмосферу. Отсасывающее и газоочистное оборудование размещено на углезагрузочном вагоне или стационарно установлено на земле.
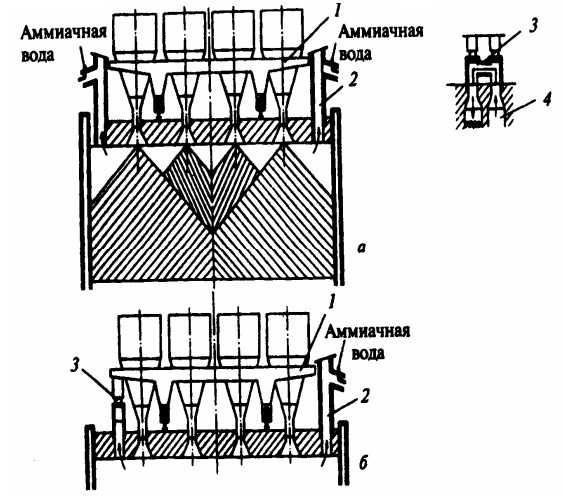
1-углезагрузочный вагон; 2-стояк; 3-перепускной трубопровод, соединяющий загружаемую коксовую печь 4 с соседней; а - с отводом газов через стояки загружаемой печи; б - дополнительным отводом через смежную камеру
Рисунок 2 - Система бездымной загрузки шихты путем гидроинжекции
На новых батареях в Германии и других странах бездымная загрузка шихты обеспечивается отсосом газов в газосборник путем гидроинжекции.Для печей с широкими камерами коксования (масса загружаемой шихты 50 т) при оптимальном расположении загрузочных стояков и соответствующей конструкции углезагрузочного вагона требуемая эффективность достигается при отводе газов через стояк загружаемой печи (рис. 2, а). Для большей гарантии бездымности на коксовой стороне батареи предусматривают иногда мини-стояки, через которые загружаемая печь во время загрузки шихты соединяется со смежной печью с помощью U-образного перепускного патрубка (рис. 2, б) для отвода части газов в газосборник через соседнюю камеру.
Широко применяются за рубежом и комбинированные системы отсоса образующихся при загрузке газов: в газосборник печи и стационарный вытяжной газопровод на верху батареи. Для этого используются модифицированные углезагрузочные вагоны, оборудованные системами сбора, сжигания и передачи газа, которые не могут быть направлены в газосборник, в стационарный газопровод. В процессе загрузки шихты углезагрузочный вагон с помощью специальных устройств подсоединяется к вытяжному газопроводу
Такие системы предпочитают также внедрять при модернизации коксовых батарей, поскольку оборудование их мини-стояками на коксовой стороне сопряжено с большим объемом работ на перекрытии батарей, а применение гидроинженкции с отсосом газов, образующихся при загрузке, только через стояк загружаемой печи не обеспечивает требуемой бездымности.Системы бездымной загрузки шихты, внедренные в последние годы на некоторых вновь построенных и реконструированных коксовых батареях, рассмотрены ниже.
В Германии на заводе в Дуйсбург-Хукингене фирмы «Майнесманнререн-верке» на коксовой батарее с печами объемом 70 м3 (разовая загрузка 60 т шихты 10%-ной влажности) бездымность загрузки шихты обеспечивается применением гидроинжекции. Загрузка угольной шихты в печь осуществляется через четыре люка за 90 с. Коксовая батарея оборудована газосборником диаметром 1400 мм на машинной стороне, который разделен по длине на три участка с индивидуальным отводом от каждого, и стояками увеличенной высоты с встроенными клапанными коробками и гидравлическим уплотнением крышек.
На заводе «Проспер»фирмы «Рурколе»(Германия) на двух новых коксовых батареях с печами объемом 62м3 для загрузки шихты применяется четырех-бункерная углезагрузочная машина (масса с шихтой около 290 т), бункера которой оснащены горизонтальными шнековыми питателями для принудительной выгрузки шихты.
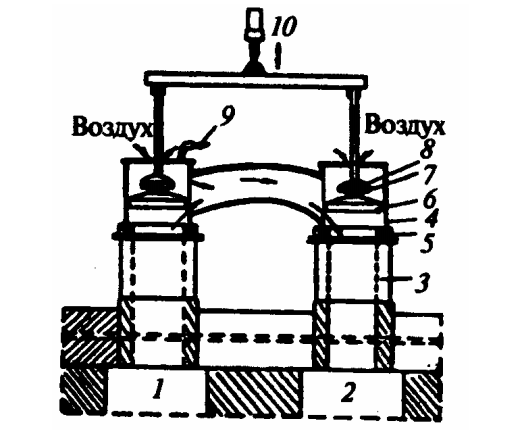
1-загружаемая камера; 2-смежная камера; 3-газоотводящий патрубок; 4-перепускная труба; 5-водяной затвор; 6-крышка; 7-магнит; 8-уплотнительный конус; 9-клапан сброса; 10-гидроцилиндр
Рисунок 3 - Схема соединения смежных камер коксования при загрузке шихты
Для обеспечения бездымной загрузки шихты также применяется система гидроинжекции (давление надсмольной воды 3,5 МПа); отсос газов осуществляется через загружаемую и соседнюю камеры коксования. С этой целью на коксовой стороне батареи установлены мини-стояки, соединяемые попарно перепускной трубой (рисунок 3). К концу процесса загрузки приводится в действие клапан, через который поступает воздух для вытеснения остаточных газов из перепускной трубы.
Применение систем комбинированного отсоса образующихся при загрузке шихты газов в газосборник коксовой печи и стационарный вытяжной газопровод широко практикуется в Японии. Системами бездымной загрузки такого типа оснащены практически все батареи. Бездымная загрузка осуществляется путем отсоса части запыленных газов в газосборник печи за счет инжекции аммиачной воды в стояк, а остального количества газов после сжигания - в вытяжной стационарный газопровод, проходящий вдоль коксовой батареи (рисунок 4). Мощность инжекционной форсунки обычно выбирают так, чтобы обеспечить отсос в газосборник почти половины образующихся при загрузке газов.
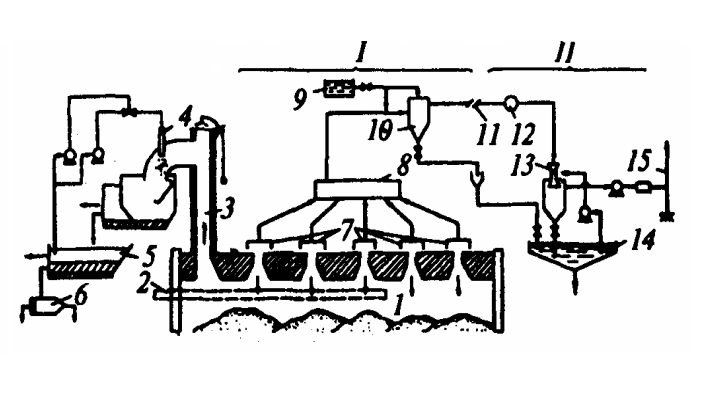
1-камера коксования; 2-планирная штанга; 3-стояк; 4-форсунка для инжекции аммиачной воды; 5-смолоотстойник; 6-центробежный отделитель; 7-вытяжные колпаки; 8-камера сжигания запыленных газов; 9-емкость с водой; 10-пылеосадитель; 11-соединительный клапан; 12-стационарный вытяжной газопровод; 13-скруббер Вентури; 14-сгуститель; 15-дымовая труба;
I–оборудование, монтируемое на углезагрузочном вагоне; II–оборудование, монтируемое на земле
Рисунок 4 - Система бездымной загрузки шихты в коксовые печи
Японской системой бездымной загрузки оснащена коксовая батарея № 1 (60 печей высотой 6,1 м) на металлургическом заводе фирмы «ЛТВ Стил» в Чикаго (США), расположенном в промышленном районе с высоким уровнем загрязнения атмосферы, и на коксовой батарее металлургического завода фирмы «Соллак» в Сереманже (Франция). Для загрузки шихты применяется углезагрузочная машина сварной портальной конструкции, которая монтируется на четырех приводных тележках. Четыре бункера машины выполнены из коррозионностойкой стали, оборудованы песковыми питателями и механически регулируемыми измерительными устройствами для контроля уровня заполнения. Газы отсасываются в газосборник батареи путем инжекции в стояки аммиачной воды под давлением 4,2 МПа, частично сжигаются и через кольцевое пространство телескопов и сборный коллектор на углезагрузочной машине поступают в стационарный вытяжной газопровод, соединенный с системой газоочистки. Эта система расположена в конце коксовой батареи и включает сатуратор, промывочный скруббер Вентури, сепаратор и вытяжной вентилятор. Система работает по циклическому графику, общая продолжительность рабочего цикла 7 мин 25 с.
В последние годы для очистки газов, образующихся при загрузке наряду с мокрыми методами очистки, получают применение тканевые фильтры. Способ сухой очистки таких газов впервые применен в Нидерландах при модернизации коксового цеха №1 на заводе фирмы «Хооговенс»в Эймейдене. Для обеспечения бездымности загрузки шихты четырех-бункерная углезагрузочная машина с тарельчатыми питателями оборудована системой газо-проводов и устройств, обеспечивающих отвод газов в стационарный вытяжной газопровод.
Загрузка печи осуществляется автоматически, выпуск шихты из бункеров машины регулируется так, чтобы скорость разгрузки каждого бункера соответствовала заданной. Газы очищают в тканевых фильтрах «Микропул», работающих под давлением в автоматическом режиме. В качестве сорбента и вспомогательного фильтрующего материала используют известняк или доломит тонкого помола. Свежий сорбент периодически подается в трубопровод загрязненного газа за несколько метров до фильтра, оседает на рукавах фильтраиобразуетлобовой слой. Остаточнаяконцентрация пыли в газах составляет 1 мг/м3.
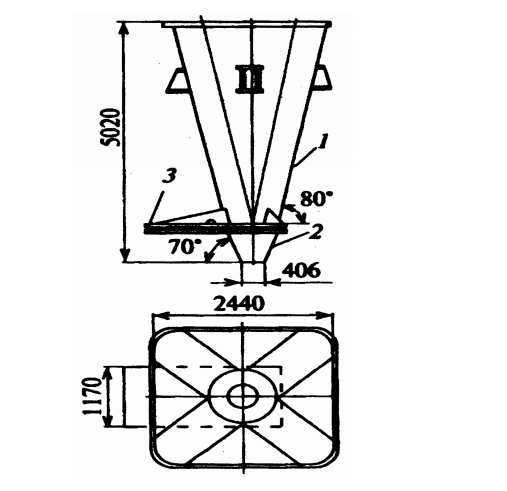
1-бункер; 2-переходной конус; 3-отсекающая заслонка
Рисунок 5 - Конструкция бункера с массовым потоком шихты
В Великобритании в качестве эффективного решения, обеспечивающего бездымность загрузки шихты в коксовые печи, все большее распространение получает способ последовательной загрузки шихты с использованием углезагрузочных вагонов (УЗВ), работающих по принципу создания массового потока выгружаемой шихты. Сущность принципа истечения шихты по модели массового потока состоит в том, что частицы шихты при ее выгрузке из бункера находятся в движении в любой точке объема бункера (как в осевой зоне, так и на периферии). Это предотвращает зависание шихты в бункере, сводообразование и неоднородность потока шихты во времени.
Первый бункер новой конструкции (рисунок 5) емкостью 8,5 т,в форме перевернутой пирамиды с углом наклона стенок 80° и выпускным отверстием диаметром 914 мм , был изготовлен из малоуглеродистой стали толщиной 8 мм и оснащен комплектом переходных конусов из нержавеющей стали с выпускными отверстиями разных. Испытания бункера подтвердили, что разработанная конструкция обеспечивает условия для массового потока шихты и требуемую скорость загрузки даже при использовании трудно текущей шихты высокой влажности (до 14%) при диаметре разгрузочного отверстия не менее 356 мм. Более того, нормальное истечение шихты из бункера обеспечивалось даже после хранения ее в бункере в течение 6 сут., а также легко возобновлялось в случае прерывания потока.
На коксохимических предприятиях нашей страны шихту загружают также углезагрузочными вагонами. Углезагрузочный вагон с 3 или 4 бункерами устанавливается над люками подлежащей загрузке камеры, выпускные патрубки бункеров с помощью теле-скопических устройств присоединяются к загрузочным люкам, после чего производится выпуск шихты. Бездымность загрузки, как правило, обеспечивают путем отcoca всех газов загрузки в газосборники. Наиболее распространен метод эвакуации газов загрузки через стояки с помощью паровых инжекторов. При этом эффективность отсоса зависит от давления пара на форсунках (0,7-0,9 МПа).
Основным недостатком метода пароинжекции с точки зрения зашиты окружающей среды является увеличение количества аммиачной воды в результате конденсации пара, израсходованного для отсоса газов загрузки. В связи с этим в последнее время преимущественное распространение получает гидроинжекция с использованием аммиачной воды цикла газосборников. Для реализации этого метода необходим насос давлением до 2-3 МПа (рисунок 6) и трубопроводы высокого давления для подачи воды к форсункам.
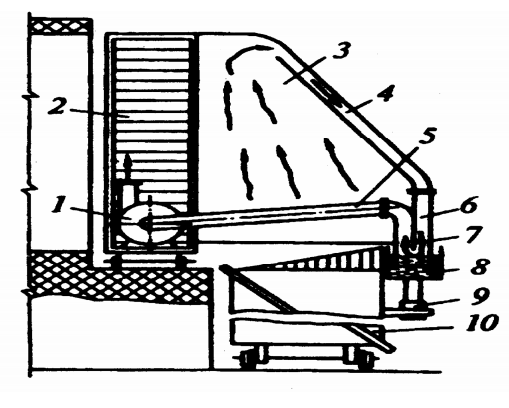
1-вентилятор; 2-коксонаправляющая; 3-зонт; 4-горячий газоход; 5-холодный газоход; 6-тройник; 7-перегородка; 8-емкость с водой; 9-пневмоцилиндр; 10-тушильный вагон.
Рисунок 6 - Схема передвижной установки беспылевой выдачи кокса
Опыт применения гидроинжекции показал, что системы работают устойчиво и при давлении воды >2 МПа, практически полностью обеспечивая отсос газов. Недостатком этого метода является необходимость регулярной чистки стояков, колена которых зарастают отложениями в течение 7-10 сут.; при несоблюдении графика чистки изменяется форма струй, вследствие чего резко снижается эффективность инжекции.
3.3 Снижение выбросов при выдаче кокса
Борьба с выбросами при выталкивании кокса из печных камер - одна из наиболее сложных задач. Над раскаленным коксом, попадающим в тушительный или коксовозный вагоны, возникает интенсивное восходящее течение нагретого воздуха, которое вовлекает в движение значительные массы окружающего атмосферного воздуха. Этот подсасываемый (эжектируемый) из атмосферы поток подхватывает образующиеся при разрушении коксового пирога частицы пыли и увлекает их вверх. В результате возникает окрашенное пылевое облако значительных размеров, в котором кроме пыли могут содержаться и газообразные вредные вещества, выделяющиеся из кокса; объем этих газов сравнительно невелик и обычно не превышает нескольких десятков кубометров.
Образование пылевого облака при выдаче происходит весьма быстро, и этот неорганизованный выброс принято относить к залповым. При выдаче кокса недостаточной готовности наблюдается образование густых облаков плотного черного или черно-зеленого дума. Такие явления наблюдаются при незавершенности процесса коксования в центре угольной загрузки или неравномерном обогреве печей, приводящем к образованию в загрузке холодных зон.
Существует несколько вариантов систем беспылевой выдачи кокса: пылеотсасывающие зонты над коксонаправляющей и тушильными вагонами; перекрытия над рельсовым путем тушильного вагона; комбинированные системы беспылевой выдачи и тушения кокса.
Наибольшее признание получили системы с устройством зонтов, отсосом и очисткой газов выдачи. При этом отсасывающее и пылеулавливающее оборудование проектируют как в передвижном, так и в стационарном исполнении. На практике чаще всего используются системы с передвижным зонтом и стационарной системой пылеулавливания. В качестве пылеуловителей применяют скрубберы Вентури, мокрые электрофильтры, тканевые фильтры. В последнее время за рубежом наблюдается тенденция перехода только на сухие пылеуловители, как правило, рукавные фильтры.
В СНГ первоначально применялась передвижная система обеспыливания газов выдачи, смонтированная на двересъемной машине. Легкий зонт соединялся с группой из двух циклонов и дымососом. Такие системы на батарее с объемом камер 41,6 м3 улавливали примерно 750 кг пыли в сутки. Однако предусмотренное проектом удаление пыли из бункеров циклонов шнековыми транспортерами оказалось неработоспособным, циклоны быстро забивались пылью, что приводит к интенсивному износу дымососов и выходу их из строя.
В 1983г. на Коммунарском коксохимическом заводе была пущена первая установка беспылевой выдачи кокса (УБВК) со стационарной системой отсоса и очистки газов (рисунок 7). В последующие годы подобные установки были смонтированы ещё на ряде заводов.
Существующие тенденции все еще базируются на увеличении объема отсасываемых газов до 150-180 тыс. м3/ч с соответствующим увеличением размеров и констру кции зонта. Концентрация пыли в отсасываемом из-под зонта газе достигает 18-22 г/м3. Устанавливая на первой ступени очистки группы циклонов, достигают суммарной степени очистки 99,1-99,2% при остаточной концентрации пыли в газах выдачи 0,11-0,22 г/м3. Нетрудно видеть, что увеличив объем отсасываемых газов, получаем повышенную запыленность, уменьшение которой до требуемых норм требует повышения степени очистки.
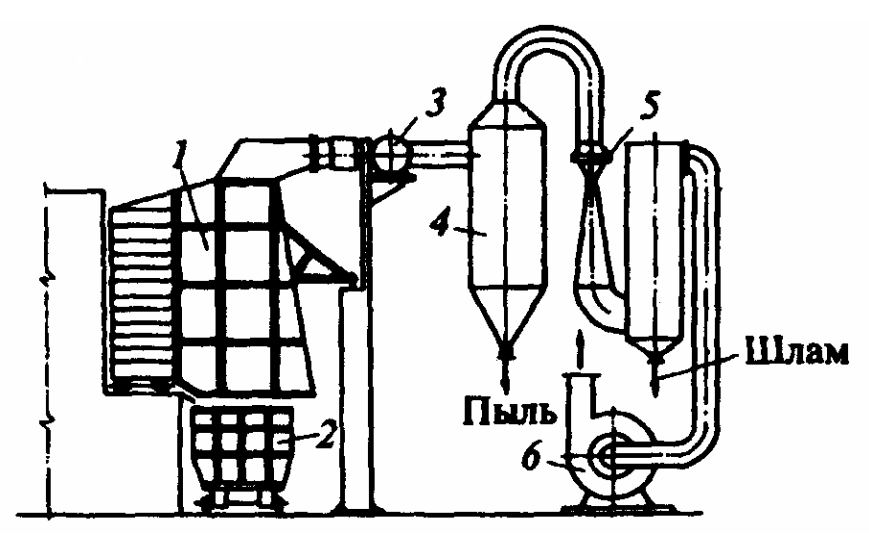
Рисунок 7 - Схема установки беспылевой выдачи кокса со стационарной системой очистки
Для сокращения неорганизованных выбросов, образующихся при выдаче кокса из камер коксования в тушильный вагон, на коксовых батареях № 5 и 6КХП АО «Северсталь»в 1997г. построена установка беспылевой выдачи кокса. На двересъемной машине установлен зонт, который закрывает «корзину» коксонаправляющей и тушильный вагон. С помощью телескопических патрубков, установленных на зонте, происходит стыковка зонта и газового коллектора, предназначенного для транспортировки газо-воздушной смеси на очистку в двух электрофильтрах типа ЭГА. Затем воздух, очищенный от мелкодисперсной пыли до концентрации 50-80 мг/м3, выбрасывается в атмосферу, а уловленная электрофиль -трами пыль используется как добавка в шихту для коксования. Сокращение выбросов пыли в атмосферу при выдаче кокса составляет 200 т/год.
Из всех применяемых в настоящее время за рубежом систем беспылевой выдачи кокса (перекрытие над всей коксовой стороной батареи; отсос и очистка выделяющихся газов в стационарной системе скрубберов; пылеулавливающие зонты над коксонаправляющей и тушильным вагоном с газоочистным оборудованием на тушильном вагоне или соединенной с ним платформе; пылеулавливающие зонты над коксонаправляющей и тушильным вагоном со стационарными вытяжным газопроводом и системой газоочистки) наиболее эффективными признаны системы последнего типа. В Японии такими системами оснащены практически все коксовые батареи.
Схема одной из таких систем показана на рисунке 8. Ширина пылеулавливающего зонта равна ширине коксоприемного вагона, длина колеблется от 6до 10 м в зависимости от объема камеры коксования. Мощность дымососа в системе беспылевой выдачи при 40 °С составляет 2500-4500 м3/мин в зависимости от объема камеры коксования. Для очистки газов применяются как мокрые, так и сухие методы очистки.
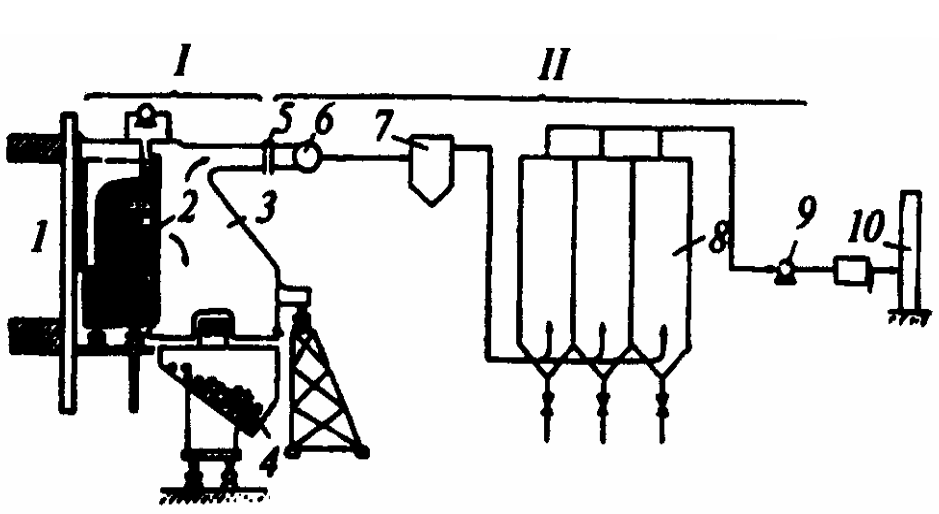
1-камера коксования; 2-коксонаправляющая; 3-пылеулавливающий зонт; 4-коксоприемный вагон; 5-соединительный клапан; 6-стационарный вытяжной газопровод; 7-пылеосадитель; 8-тканевый фильтр; 9-дымосос; 10-дымовая труба;
I–оборудование, монтируемое на коксонаправляющей; II–оборудование, монтируемое на земле
Рисунок 8 - Система беспылевой выдачи кокса из печей
Широкое признание в мире получила система беспылевой выдачи типа «Министер Штайн», разработанная фирмой «Хартунг, Кун унд Ко» (Германия). Эта система обеспечивает практически 100%-ное пылеулавливание (остаточное содержание пыли в газах после тканевых фильтров составляет < 20 мг/м3). Выбросы пыли при выдаче кокса снижаются до 5 г/т кокса. Пропускная способность газоочистки с тканевыми фильтрами, используемой в этой системе беспылевой выдачи, составляет > 200 тыс. м3/ч. Система отличается oт других систем такого типа способом стыковки газопровода с пылеулавливающим зонтом. Передвижной зонт закрывает полностью коксоприемный вагон и коксонаправляющую во время выдачи кокса. Зонт опирается на площадку коксовой стороны батареи и дополнительный рельс. Его подключают к стационарному газопроводу перед выдачей кокса с помощью соединительного патрубка, движущегося на тележке над верхней частью газопровода, имеющей расщелину, закрытую решеткой, которая служит опорой для ленты из высокотемпературного эластомера, закрывающей расщелину. Такая конструкция устраняет необходимость в оборудовании стационарного газопровода множеством заслонок напротив каждой печи. Для предохраненияот перегрева отсасываемые при выдаче кокса газы охлаждают в рекуператоре.
Система беспылевой выдачи кокса типа «Министер Штайн»в последние годы внедрена на новых коксовых батареях в Германии, Великобритании, Нидерландах, США. В ходе совершенствования указанной системы фирмой «Хартунг, Кун унд Ко»разрабо-тана конструкция новой коксонаправляющей машины, выполненной как единое целое с пылеулавливающим зонтом. Такими системами беспылевой выдачи кокса в Германии оснащены все новые коксовые батареи на ряде заводов.
3.4 Пылеподавление при тушении кокса
Процесс мокрого тушения кокса в его обычном аппаратурном оформлении чрезвычайно сложен с точки зрения очистки выбрасываемой парогазовой смеси. В течение 1 -2 мин из тушильной башни современного коксохимического завода выбрасывается в атмосферу около 20 тыс. м3 водяного пара, объем которого увеличивается из-за подсоса окружающего воздуха. Использование загрязненной воды для тушения кокса приводит к увеличению выбросов вредных веществ. Так, при использовании чистой воды количество выбрасываемых в атмосферу твердых частиц составляет 0,23-1,13 кг/т кокса, а при применении сточных вод 0,68- 2,26 кг/т кокса. Удельный вынос пыли на 1 т кокса увеличивается на 0,4 г при увеличении сухого остатка в циркулирующей воде на 0,1 г/ч. Сокращение выбросов твердых частиц в процессе мокрого тушения при обычном аппаратурном оформлении достигается устройством специальных каплеотбойников либо дополнительных ярусов распыления воды через форсунки.
На металлургическом заводе фирмы «Бритиш стил»в Порт-Толботе тушильная башня, выполненная из армированного бетона и футерованная плотным кислотоупорным кирпичом, заканчивается деревянной трубой с устройством для задержания твердых частиц.
На металлургическомзаводе в Дуйсбург-Хукингене фирмы «Маннесманнререн-верке» коксовая батарея с печами объемом 70 м3 оборудована тушильной башней, представляющей собой боковую вытяжную деревянную трубу со стальной обшивкой высотой 40 м. Площадь поперечного сечения башни в четыре раза больше площади тушения, что обеспечивает снижение скорости паров на выходе и количества выбрасываемой пыли.
Для экологической защиты за рубежом разрабатываются и внедряются принципиально новые способы мокрого тушения. В ФРГ фирмой «Эшвейлер Бергверксферайн» разработан способ тушения кокса под давлением. Система состоит из тушильного вагона, узкого зонта, соединенного с коксонаправляющей и подключенного к системе обеспыливания, и станции тушения. Когда тушильный вагон установлен для выдачи, контейнер вагона поднимается вплотную к зонту. В то же время телескопический газоход, идущий от верхней части зонта, присоединяют к двум обычным скрубберам, расположенным на шасси тушильного вагона (рисунок 9). В качестве альтернативного варианта зонт может быть подсоединен к вытяжному газопроводу со стационарной обеспыливающей установкой.
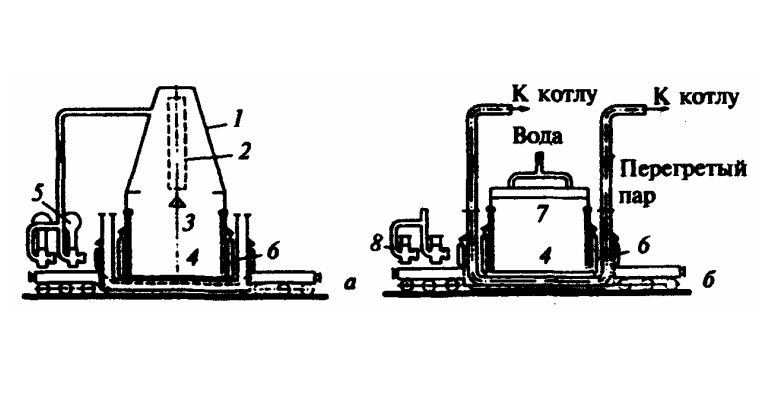
1-пылеулавливающий зонт; 2-кокс из коксонаправляющей; 3-распределитель; 4-кокс; 5-чистый газ; 6-гидроцилиндры; 7-крышка с соплами; 8-скрубберы
Рисунок 9 - Схема процесса тушения кокса под давленим
Подсосы воздуха минимальны, поэтому объем отсасываемых газов может быть уменьшен на 20% от обычно отводимого в системе беспылевой выдачи типа «Министер Штайн». Расход воды на тушение составляет 0,6-0,7 м3/т кокса.
В США фирмой «Кресс» разработаны способ косвенного охлаждения кокса водой и оборудование для беспылевой выдачи. Выдача кокса из печи производится в стальной контейнер, идентичный по форме и размерам камере коксования и установленный на автомобильной платформе. По мере продвижения горячего коксового пирога из камеры коксования в контейнер производится орошение контейнера водой. По окончании выдачи и удалении выталкивающей штанги из печи скользящая дверь контейнера закрывается и производится автоматическое уплотнение его с помощью водоохлаждаемого и водозаполненного уплотнения из эластомера.
Заполненный коксом контейнер транспортируется затем от печи к тушильной станции,где он по роликам перекатывается с автомобильной платформы на специальный стеллаж, вмещающий несколько контейнеров. Процесс охлаждения кокса водой, стекающей по герметичным стенкам контейнера, продолжается здесь до тех пор, пока температура кокса не снизится ниже точки повторного воспламенения его (~ 2,5 ч). Затем контейнер с охлаж-денным коксом вновь перегружается на автомобильную платформу и транспортируется к модифицированной коксовой рампе, оборудованной дверью гильотинного типа с уплотнением, что предотвращает выбросы пыли в атмосферу при разгрузке кокса. Плат-форма наклоняет контейнер к рампе для облегчения схода кокса из него. С рампы кокс самотеком поступает на коксосортировку, а пустой контейнер транспортируется для приема кокса из очередной разгружаемой печи.
Основным преимуществом этого способа является возможность получения абсолютно сухого кокса, поскольку при охлаждении он не контактирует с водой. Физическое тепло кокса передается путем конвекции водоохлаждаемым стенкам контейнера и может быть легко утилизировано для различных производственных целей. Благодаря мягкому режиму охлаждения и отсутствию промежуточных перегрузок улучшаются структурные и прочностные свойства кокса, сокращаются потери от измельчения. Полностью устраняются выбросы в атмосферу от выдачи до сортировки кокса.
Капитальные затраты на такую систему снижаются на 80%, поскольку не требуется коксонаправляющей, тушильного вагона, тушильной башни и другого оборудования, а выход кокса повышается на 12-15%. Для обслуживания каждых шести печей батареи требуется один контейнер; длительность цикла пробега несущей автоплатформы для каждой выдачи кокса составила 7,5 мин. В промышленном масштабе эта технология внедрена на металлургическом заводе в Спарроус-Пойнте фирмы «Бетлихем Стил»(США), на двух коксовых батареях. Технология обеспечивает снижение на 90%выбросов при выдаче и тушении кокса.
При сухом тушении кокса экологические проблемы связаны с необходимостью сброса в атмосферу избыточной части циркулирующего охлаждающего газа, содержащего 8-14% СО и загрязненного коксовой пылью. Кроме того, повышается концентрация пыли на трактах коксоподачи и в отделении коксосортировки, в связи с чем, возникает необходимость в усиленной аспирации этих помещений и очистке большого объема вентиляционных выбросов.
Для снижения пылевыделения на коксосортировке, конвейерах кокса, загрузочных устройствах доменной печи при использовании кокса сухого тушения в Японии, например, применяют орошение кокса в процессе передачи на конвейер, ведущий к доменной печи, водой в количестве 0,5% без добавления смачивателей.В составе УСТК имеются два источника организованных выбросов в атмосферу: свеча избыточного инертного газа после дымососа и свеча, через которую выбрасываются газы, выделяющиеся из кокса в форкамере. Значительное загрязнение атмосферы этими выбросами (удельные выбросы пыли составляют соответственно 5,7-11,5 и 17,6-28,8 г/м3 потушенного кокса) требует разработки мероприятий по их сокращению. Кроме пыли, выбросы свечей УСТК содержат значительное количество СО (до 5 и 18% (объемн.) соответственно из свечи дымососа и форкамеры).
Внедрение сухого тушения кокса на отечественных коксохимических заводах необходимо, прежде всего потому, что оно позволяет улучшить качество кокса в условиях непрерывно ухудшающейся сырьевой базы коксования. Однако в современном исполнении установки сухого тушения кокса выбрасывают в атмосферу большее количество вредных веществ, чем тушильные башни при мокром тушении кокса биохимически очищенной сточной водой. Однако, одним из достоинств способа сухого тушения кокса в экологическом отношении является то, что выбросы на этих установках носят организованныйхарактер и могут быть подвергнуты очистке, благодаря чему достигается общее сокращение удельных выбросов в атмосферу при производстве кокса. Температура кокса после УСТК достигает 150-200 °С. При транспортировании, перегрузках, грохочении такого кокса происходит интенсивное пылевыделение, поэтому технологическое оборудование снабжают аспирационными установками. Назначение аспирационных систем - создание благоприятных условий труда по содержанию вредных веществ в воздухе производственных помещений путем предотвращения выделений из неплотностей технологического оборудования. Аспирационные системы располагают в соответствии с технологической схемой УСТК и сортировки кокса сухого тушения (рисунок 10).
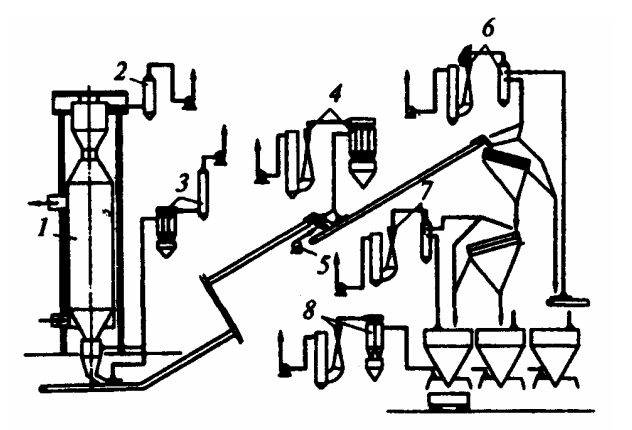
1-камера УСТК; 2-а.с. узла загрузки УСТК (скруббер ЦС); 3-а.с. узла выгрузки УСТК (группа циклонов ЦН, скруббер ЦС); 4-а.с. перегрузочного узла (группа циклонов, скрубер КМП); 5-дутьевой вентилятор станции обеспыливания кокса; 6-а.с. валкового грохота (коллектор ВК, скруббер КМП); 7-а.с. инерционного грохота (коллектор ВК, скрубер КМП); 8-а.с. узла погрузки кокса в вагоны (группа циклонов ЦН, скруббер КМП)
Рисунок 10 - Схема аспирационных систем (а.с.) УСТК и коксосортировки (ОАО «НТМК»)
В состав аспирационных систем включают сухие и мокрые пылеуловители. При выгрузке горячего кокса из камер УСТК выделяется много пыли, поэтому обычно применяют двухступенчатую схему очистки. В качестве первой степени используют группы циклонов типа ЦН-15, имеющие достаточно высокую эффективность пылеулавливания (87-97%) при умеренном гидравличес ком сопротивлении (0,35-1,15 кПа). На второй ступени пылеулавливания устанавливают скрубберы ЦС-ВТИ. Фактическая степень улавливания пыли в них - от 60 до 90% и определяется в основ ном расходом орошающей жидкости и качеством еераспыления. Коксовая пыль по существующей классификации может быть, как правило, отнесена к классу крупнодисперсных. Это упрощает задачу обеспыливания аспирационного воздуха сухими методами.
4. Расчет эколого – экономической эффективности применения установки сухого тушения кокса на примере Макеевского коксохимического завода чао «МАКЕЕВКОКС»
Расчет эколого – экономической эффективности применения установки сухого тушения кокса на примере макеевского коксохимического завода ЧАО «МАКЕЕВКОКС» выполнен для годового объёма производства кокса 860 тыс. т. Ставка экологического налога, грн/т выбросов: аммиак – 269,08; сероводород – 4 610,83; диоксид серы – 1 434,71; монооксид углерода – 54,05; оксиды азота – 1434,71; фенол – 6 512,02, бенз(а)пирен – 1 977 992. Инвестируемые средства на реализацию проекта по внедрению УСТК составляют 200 млн. грн. Ставка кредита 25 %. Были расчитаны затраты на производство кокса, а также затраты, связанные с экологическими платежами до и после внедрения УСТК. Также были произведены расчеты эффективности от производства пара и электроэнергии. Расчет калькуляции себестоимости продукции показан в табл.1.
Таблица 1 – Расчет калькуляции себестоимости кокса
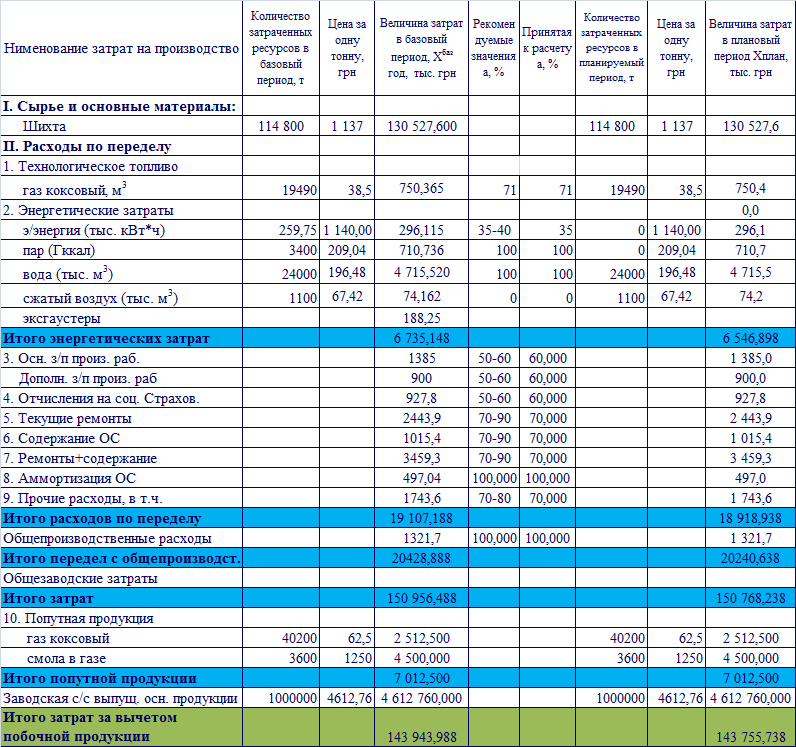
Результаты расчетов от внедрения УСТК приведены в таблице 2.
Таблица 2 – Результаты расчета эффективности внедрения УСТК
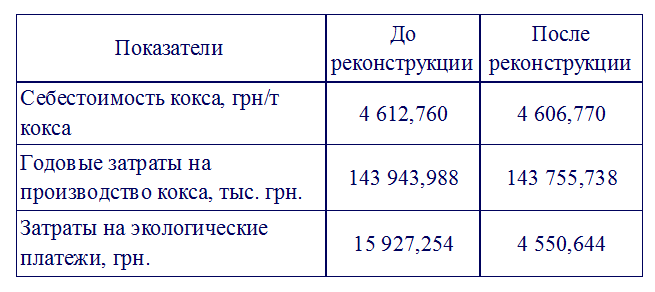
Из табл. 1 видно что затраты на производство кокса до и после внедрения УСТК состовляют соответственно 143 927 тыс. грн/год и 143 755 тыс. грн/год. Изменения затрат на производство кокса после реконструкции составляют 188,25 тыс. грн. Экологические платежи сокращаются в 3,5 раза. При этом срок окупаемости проекта (учитывая выплаты по кредиту со ставкой в 25%) составляет 2,3 года (смотри табл. 3).
Таблица 3 – Расчет срока аккупаемости УСТК
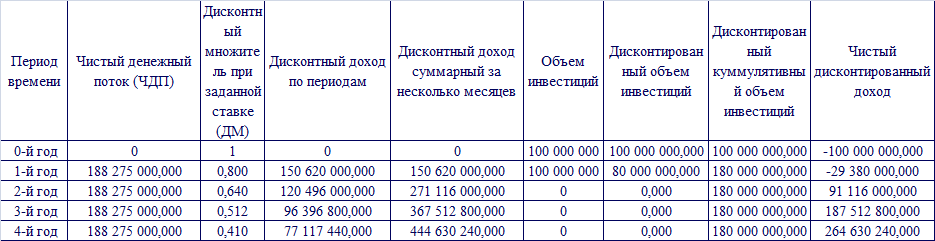
Расчет по определению эффективности от производства пара на УСТК показывает, что при себестоимости 1 Гкал пара в 50 грн (цена пара, производимого с использованием топлива, при этом равна 100 грн./Гкал. При тушении 1.0 млн. т/год кокса будет произведено пара 350 тыс. Гкал. Эффект использования пара УСТК составляет 26 млн. грн. в год.
Расчет по определению эффективности производства электроэнергии из пара показывает, что на паре УСТК энергетических параметров ~4 МПа и 44°С можно производить до 100 кВт*ч электроэнергии на 1 т потушенного кокса при работе турбогенератора в конденсационном режиме и 55 кВт*ч при работе в режиме с отборами пара 0.16 Гкал/т потушенного кокса. Эффект производства электроэнергии составляет 11,4 млн. грн/год.
Выводы
Преминение системы бездымной загрузки угольной шихты в камеру коксования и установки беспылевой выдачи кокса позволяет снизить выбросы в атмосферу на 90%.
Приминение установки сухого тушения кокса обесречивает:
- Снизить затраты на производство кокса с 143 927 тыс. грн/год до 143 755 тыс. грн/год;
- В следствии снижении выбросов в атмосферу экологические отчисления сократятся в 3,5 раза;
- Эффект от использования пара УСТК составляет 26 млн. грн. в год;
- Эффект производства электроэнергии составляет 11,4 млн. грн/год;
- Срок окупаемости проекта (учитывая выплаты по кредиту со ставкой в 25%) составляет 2,3 года.
При написании данного реферата магистерская работа еще не завершена. Окончательное завершение: декабрь 2015 года. Полный текст работы и материалы по теме могут быть получены у автора или его руководителя после указанной даты.
Список источников
- БольшинаЕ.П. Экология металлургического производства: Курс лекций. – Новотроицк: НФ НИТУ «МИСиС», 2012. – 155 с.
- Кауфман А.А., Харлампович Г.Д. Технология коксохимического производства: Учебное пособие. – Екатерингбург: ВУХИН-НКА, 2005. – 288 с.
- Кауфман А.А. Мастер коксового производства. – Екатеринбург: ВУХИН, 2002. – 228 с.
- Иванов Е.Б. Технология производства кокса / Е.Б. Иванов, Д.А. Мучник. – Издательское объединение «Вища школа», 1976. – 232 с.
- Мищенко И.М. Черная металургия и охрана окружающей среды: учебное пособие. – Донецк: ГВУЗ «ДонНТУ», 2013. – 452 с.
- Успенский С. К. и др. Совершенствование технического уровня и повышение эффективности установок сухого тушения кокса // Кокс и химия. 1988, с. 38 – 41.
- Родькин С. П. и др. Комплексная оценка эффективности сухого тушения кокса // Кокс и химия. 1988. № 4, с. 48 – 51.
- Кокс. Коксохимическое производство [Электронный ресурс]. – Режим доступа: http://www.metaljournal.com.ua/coke.
- Сухоруков В.И. Научные основы совершенствования техники и технологи производства кокса. – Екатеринбург: ВУХИН-НКА, 1999. – 393 с.
- Пыриков А.Н. Защита окружающей среды на коксохимических предприятиях / А.Н. Пыриков, С.К. Васнин, Б.Н. Баранбаев. – М.: Интермет – инжиниринг, 2000. – 176 с.
- Родионов А.И. Техника защиты окружающей среды / А.И. Родионов, Н.С. Торочешников. – М.: Химия, 1989. – 325 с.
- Лейбович Р.Е. Технология коксохимических производств / Р.Е. Лейбович, Я.М.Обуховский, С.Я. Сатановский, П.М. Кутовой. – М.: Металлургия, 1974. – 420 с.
- Браун Н.В., Глущенко И.М. Перспективные направления развития коксохимического производства. – М.: Металлургия, 1989 г. – 272 с.
- Рудыка В.И. Коксовая батарея с печными камерами объемом 51 м3 и боковым подводом смешанного газа / В.И. Рудыка, Н.Ю. Чеботарев, О.Н. Суренский, В.В. Деревич // Кокс и химия, - 2009. - № 7. – С. 25-27.
- Власов Г.О. Системный анализ коксохимического производства / Г.О. Власов, В.И. Саранчук, В.М. Чуищєв, В.В. Ошовський. – Д.: ДонГТУ «Східний видавничий дім», 2002. – 296 с.
- Ярошенко Ю.Г. Энергоэффективные и ресурсосберегающие технологи черной металлургии: учебное пособие / Ю.Г. Ярошенко, Я.М. Гордон, И.Ю. Ходоровская. Под ред. Ю.Г. Ярошенко. – Екатеринбург: ООО «УИПЦ», 2012. – 670 с.
- Зингерман Ю.Е. Внедрение установки беспылевой выдачи кокса / Ю.Е. Зингерман, В.Б. Каменюка, Т.Ф. Трембач // Кокс и химия, – 2004. – № 7. – С. 34
- Лейбович Р.Е. Технология коксохимического производства: Учебник для техникумов, изд. 3-е, доп. и перераб / Р.Е. Лейбович, Е.И. Яковлева. – М.: Металлургия, 1982. – 360 с.
- Зингерман Ю.Е. Внедрение новых технологий и разработок / Ю.Е. Зингерман, В.И. Рудыка, В.В. Кривонос, В.В. Гураль // Кокс и химия. - 2009. – № 9. – С. 51
- Общая схема коксохимического производства [Электронный ресурс]. – Режим доступа: http://opeaulay.ucoz.ru/news/obshhaja....
- Углеподготовительный цех коксохимического производства [Электронный ресурс]. – Режим доступа: http://www.borpak.ru/ugolnaya....
- Зашквара В.Т. Подготовка углей к коксованию / В.Т. Зашквара, А.Г. Дюканов. – М.: Металлургия, 1981. – 260 с.
- Жидко А.С. Совершенствование и оптимизация технологи подготовки углей для коксавания. – Челябинск: Металлургия, 1989. – 189 с.
- Посохов М.Ю. Первая установка избирательного измельчения углей с пневмосепарацией в Китае/ М.Ю. Посохов, В.И. Сухоруков, Чэнь Кай // Кокс и химия, - 2006. - № 7. – С. 5-9.
- Иванов Е.Б. Технология производства кокса / Е.Б. Иванов, Д.А. Мучник. – Издательское объединение «Вища школа», 1976. – 232 с.
- Пыриков А.Н. Защита окружающей среды на коксохимических предприятиях / А.Н. Пыриков, С.К. Васнин, Б.Н. Баранбаев. – М.: Интермет – инжиниринг, 2000. – 176 с.
- Родионов А.И. Техника защиты окружающей среды / А.И. Родионов, Н.С. Торочешников. – М.: Химия, 1989. – 325 с.
- Браун Н.В., Глущенко И.М. Перспективные направления развития коксохимического производства. – М.: Металлургия, 1989 г. – 272 с.
- Рудыка В.И. Коксовая батарея с печными камерами объемом 51 м3 и боковым подводом смешанного газа / В.И. Рудыка, Н.Ю. Чеботарев, О.Н. Суренский, В.В. Деревич // Кокс и химия, - 2009. - № 7. – С. 25-27.
- Власов Г.О. Системный анализ коксохимического производства / Г.О. Власов, В.И. Саранчук, В.М. Чуищєв, В.В. Ошовський. – Д.: ДонГТУ «Східний видавничий дім», 2002. – 296 с.
- Зингерман Ю.Е. Внедрение установки беспылевой выдачи кокса / Ю.Е. Зингерман, В.Б. Каменюка, Т.Ф. Трембач // Кокс и химия, – 2004. – № 7. – С. 34
- Бородин М.В. Энергоресурсы коксохимической промышленности Украины. Направления их использования / М. В. Бородин, В. Ю. Попов, Э. В. Старченко // Кокс и химия – 2000. - № 7 – С. 45 – 47.
- Зингерман Ю.Е. Внедрение новых технологий и разработок / Ю.Е. Зингерман, В.И. Рудыка, В.В. Кривонос, В.В. Гураль // Кокс и химия. - 2009. – № 9. – С. 51
- Газоочистные аппараты и установки в металлургическом производстве. Учебник для вузов/ С.Б. Старк. Изд. 2-е, перераб. и доп. – М.: Металлургия, 1990. –400 с.
- Инженерная защита окружающей среды. Учебное пособие / под ред. Воробьева О.Г. –СПб.: изд. Лань, 2002. –288 с.
- Курс инженерной экологии. Учебник для вузов/ Под ред. Мазура И.И. – М., Высшая школа, 1999. – 447 с.
- Мазур, И.И. Курс инженерной экологии. Учебник для вузов /И.И. Мазур, О.И. Молдаванов / под ред. И.И. Мазура –М.: Высшая школа, 1999. –447 с.
- Воскобойников В.Г. Общая металлургия. Учебник для вузов/В.Г. Воскобойников, В.А. Кудрин, А.М. Якушев. 6-изд., перераб. и доп. – М.: ИКЦ «Академкнига», 2002. –768 с.
- Цветков, Ю.В. О создании экологически чистого энергометаллургического комплекса /Ю.В. Цветков//Экология и промышленность России, № 5, 1999, с.11-15.
- Денисенко, Г.Ф. Охрана окружающей среды в черной металлургии. Учебное пособие / Г.Ф. Денисенко, З.И. Губонина. –М.: Металлургия, 1989. –120 с.