Зміст
- Вступ
- 1. Актуальність теми
- 2. Мета і завдання дослідження
- 3. Огляд досліджень і розробок
- 3.1 Зниження викидів в углеподготовительном цеху
- 3.2 Зниження викидів при завантаженні коксових печей
- 3.3 Зниження викидів при видачі коксу
- 3.4 Знепилювання при гасінні коксу
- 4. Дослідження екологічних проблем і розробка заходів по підвищенню екологічної безпеки при виробництві коксу в умовах Макіївського коксохімічного заводу ЧАО "Макіївкокс"
- Висновки
- Список джерел
Вступ
Сьогодні на сучасних коксохімічних заводах впроваджуються нові передові маловідходні ресурсозберігаючі технології, що дозволяють не лише підвищити якість вироблюваного коксу, але і понизити споживання непоновлюваних природних ресурсів (вугілля, природний газ), понизити утворення викидів, скидань і відходів на виході.
Проте в Україні майже усе устаткування підприємств коксохімічної промисловості марально та фізично застаріло, це пов'язано в першу чергу з тим, що в Україну не йде великих фінансових інвестицій на реконструкцію заводів. І як наслідок підприємства не можуть дозволити собі встановлювати сучасніше устаткування для підготовки вугільної шихти, виробництва коксу вищої якості, його охолодження, а також високоефективних очисних споруд для очищення забруднених газів, що відходять, і знешкодження відходів.
Посилення екологічних вимог до коксохімічних підприємств, основних агрегатів і устаткування, стало вимагати від коксохіміків зусиль для реконструкції і технічного переоснащення підприємств за рішенням питань охорони повітряного і водного середовища.
1. Актуальность темы
Підприємства коксохімічної промисловості є одними з основних джерел потрапляння забруднюючих речовин у довкілля (ОС). Нині в Україні функціонує 13 великих коксохімічних підприємства, 7 з яких зосереджені в Донецькій області. Екологічні проблеми посилюються ще і тим, що ці підприємства розташовані в регіонах зі значною концентрацією промислового виробництва і високою щільністю населення.
Украй несприятлива екологічна обстановка, що склалася останніми роками у великих металургійних центрах, певною мірою обумовлена низькими темпами технічного переозброєння коксохімічної підгалузі, повільним впровадженням в практику нових технологічних процесів,сучасних агрегатів і устаткування.
Коксохімічні заводи займають провідне місце по викидах шкідливих речовин серед підприємств чорної металургії. До них відносять пил, оксиди азоту, діоксид сірки, оксид вуглецю, аміак, фенол, бензол, нафталін, сірководень, ціаністий водень і графіт.
Тому найважливішим соціальним завданням, що стоїть перед коксохімічними підприємствами, є підвищення екологічної безпеки виробництва, технічне переоснащення коксохімічних підприємств, здійснення великомасштабної програми будівництва природоохоронних об'єктів, впровадження сучасних екологічно безпечних технологічних процесів.
На сучасних заводах впроваджують передові технології, що дозволяють понизити викиди забруднюючих речовин в атмосферу. До основних з них відносять установки бездимного завантаження вугільної шихти до камери коксування, установки бездимної видачі і сухого гасіння коксу. Проте, останнім часом все більшу актуальність придбаває вдосконалення технологічних процесів на всіх стадіях виробництва коксу (підготовка, завантаження, коксування вугілля, видача, охолодження і сортування коксу). Цим стадіям виробництва коксу належить зараз більше 70% залпових викидів.
2. Мета та завдання дослідження
Метою є розробка і впровадження раціональних технологій виробництва коксу, що дозволяють підвищити якість коксу і одночасно скоротити шкідливі викиди.
Основні завдання дослідження:
- Вивчити основне джерела забруднення довкілля на усіх етапах виробництва коксу;
- Вивчити сучасні вітчизняні і зарубіжні технології виробництва коксу : підготовки вугільної шихти,завантаження її в коксову піч, процес коксування, вивантаження коксу з коксової печі і його охолодження;
- Розглянути можливі способи зниження викидів забруднюючих речовин на усіх етапах виробництва коксу;
- Дати характеристику чинникам, що впливають на основні характеристики металургійного коксу, і розробити пропозиції по поліпшенню якості коксу;
- Пошук оптимальних шляхів вдосконалення технологічних процесів виробництва коксу;
- Розрахувати економічний і екологічний ефект від впровадження технології, що знижують шкідливі викиди і підвищують якість коксу.
Об'єкт дослідження: Макіївський коксохімічний завод ПАТ "Макїївкокс".
Предмет дослідження: Технологічні процеси підготовки вугільної шихти, завантаження її в коксову піч, процес коксування, вивантаження коксу з коксової печі і його охолодження.
3. Огляд досліджень і розробок
Нині на коксохімічних заводах застосовується наступна класифікація коксових цехів в екологічному відношенні:
- цехи, де немає ніяких заходів по захисту атмосферного воздуxa.
- цехи, де є бездимне завантаження вугільної шихти, очищення опалювального газу від сірководня до залишкового змісту 3,0 г/м3 і біохімічне очищення стічних вод перед їх використанням на гасіння коксу;
- цехи, де окрім вказаних в п. 2 заходів є установка для беспылевой видачі коксу.
3.1 Зниження викидів у вуглепідготовчому цеху
У вуглепідготовчих цехах з вугілля, призначеного для коксування, готується вугільна шихта заданої якості. При цьому відповідно до технологічної схеми виконуються наступні операції: прийом, розвантаження і складування вугілля, дозування, дроблення, сепарація і змішення компонентою шихти. Усі ці операції, а також транспортування вугілля і шихти супроводжуються виділенням в навколишнє повітря вугільного пилу, кількість якого залежить від вологості вугілля.
При коливаннях вологості вугілля в межах 7,0-8,5% кількості пилу, що відноситься, практично постійно і складає при відкритому складі вугілля без обробки штабелів зв'язуючими речовинами 350 г/т, при обробці штабелів розчином винилацетата абостиролбутадиеновой смолою 140 г/т, за наявності закритого складу вугілля 60 г/т коксу.
Одним з чинників, що впливають на запилену повітря виробничих приміщень, є прибирання пилу, що осів, з поверхонь підлог, стін і устаткування. На коксохімічних підприємствах найбільше поширення отримало мокре прибирання, що обумовлено вибухонебезпечними властивостями вугільного пилу. Проте досвід сухого пиловловлювання на ряду підприємств показує, що в принципі можна робити і сухе прибирання. В цьому випадку доцільно використати централізовані установки пилососів з водо-кільцевими вакуум-насосами.
Це дозволить позбавитися від водно-шламового господарства, спростити експлуатацію системи, але зажадає облаштування розгалуженої мережі комунікацій,очищення повітря перед викидом в атмосферу і вирішення питань утилізації уловленого сухого пилу.
До теперішнього часу основним способом уловлювання вугільного пилу залишається мокрий. У зв'язку з цим на підприємствах найбільш поширені відцентрові скрубери, швидкісні промивачі, циклони з водяною плівкою; у ряді випадків застосовуються оригінальні конструкції, розроблені підприємствами. Останнім часом з'явилися ротоклони. Сухі колектори, що використовуються як перший ступінь очищення, у більшості випадків обладнали пристроями для подання і розпиляло води.
Ефективність уловлювання вугільного пилу в мокрих апаратах дуже різна, що пов'язано, мабуть, як з щільністю зрошування і якістю того, що розпиляло рідини, так і з дисперсністю уловлюваних часток. Необхідність комплексного рішення природоохоронних проблем обумовлює перспективність сухих методів при знепилюванні газів і повітря. Це підтверджує багаторічний досвід експлуатації сухих пиловловлювачів на ряду підприємств (ВАТ "Северсталь", АТ "Испат-Кармет", ВАТ"Магнітогорський металургійний комбінат").
Зокрема, циклони СИОТ успішно експлуатуються на Губахинском заводі більше 25 років для знепилювання аспіраційного повітря при підготовці і збагаченні вугілля. Міра очищення складає 70-84что при фактичній початковій запиленій < 200 мг/м3 цілком достатньо длядосягнення санітарних норм на викиді в атмосферу.
У циклонах діаметром 4000 мм після сушилок флотоконцентрату в АТ "Западно-сибирский металургійний комбінат" міра очищення досягає в середньому 88,5% при коливаннях початкової запиленісті від 10 до 130 г/м3 і витраті газів, що очищаються, від 43,2 до61,3 тис. м3/ч.
До перспективних методів слід віднести застосування електрофільтрів. Як відомо, у вугільній промисловості і на теплових електростанціях широко застосовуються електрофільтри УВП (вугільний, вертикальний,пластинчатий). Останнім часом замість цих електрофільтрів випускаються апарати УВВ (уніфікований, вертикальний, вибухобезпечний). Електрофільтри УВВ призначені для уловлювання вугільному пилу з концентрацією до 60 г/м3 при температурі газу до 130 °С
Застосування таких порівняно дорогих апаратів, як електрофільтри, економічно виправдане при великих масштабах очищення. Загальна продуктивність досить громіздкої установки ~ 1500 тис. м3/ч. При початковій концентрації коксівного і агломераційного пилу близько1,42 г/м3 залишкова запилена складає 40-60 мг/м3 (тобто середня міра очищення ~ 96,5%)
Прийнятні результати отримані ВУХИНом при випробуваннях конічних циклонів. Надмірний газ-теплоносій розбавляли повітрям до вмісту кисню 3-7% (об’емн.), підігрівали до 450-550 °С, піддавали каталітичному очищенню від органічних сполук в реакторі киплячого шару, а потім направляли в циклон на очищення від пилу. Міра уловлювання тонкодисперсногопилу з концентрацією 4,8-6,9 г/м3составила ок.90%.
У АТ "НЛМК" також є досвід застосування циклонів для знепилювання аспіраційного повітря на закритому складів вугілля. Міра уловлювання вугільного пилу в групах з трьох циклонів діаметром 1,2 м складає 96,8-97,0.
Таким чином, найбільш ефективні технічні рішення проблеми уловлювання вугільного пилу – застосування високоефективних сухих циклонів, а при проектуванні нових підприємств децентралізованних систем з використанням електрофільтрів.
3.2 Зниження викидів при завантаженні коксових печей
При завантаженні вологої вугільної шихти в розжарену пічну камеру утворюється ~5 м3 газів на кожну тонну завантаженої шихти. Ці гази містять 10-60 г/м3 зважених часток вугільного і напівкоксового пилу. У перерахунку на 1 т вироблюваного коксу виділення пилу при завантаженні печей досягає 150-400 г/т, при цьому кількість пилу, що виділяється, різко збільшується зі зменшенням вологості шихти < 7%.
Серйозні труднощі виникають при завантаженні термопідготовленної шихти. Для завантаження шихти, що пройшла термопідготовку, застосування традиційних способів бездимного завантаження з відсмоктуванням газів завантаження в газозбірники абсолютно неможливе із-за збільшення віднесення пилу в газозбірники і пов'язаного з цим погіршення якості кам'яно-вугільної смоли та пеку. Термічна підготовка шихти до коксування полягає в нагріві її до температури 150-200 °С з метою зниження вологості і підвищення насипної щільності.
Нині використовують в основному два методи нагріву шихти: газовим теплоносієм (у сушарках киплячого шару у трубах-сушарках) і нагрів шихти гарячим кусковим коксом (поєднаний процес термопідготовки шихти і сухого гасіння коксу).
Наприклад, в установці термічної обробки шихти на коксовій батареї №7 АТ "ЗСМК" в якості першого ступеня очищення теплоносія після труби-сушарки встановлений батарейний циклон з 100 елементами діаметром 229 мм. На другої ступені використаний мокрий пиловловлювач. Громіздкість, ненадійність і недостатня ефективність мультициклону (міра очищення 88%)%) вимагають на наступних етапах випробування доповнити схему конічним циклоном.
Розрахункова міра очищення додаткового циклону 76,5% концентрація пилу зменшується з 26-47 до 5,1 г/м3, що дозволяє понизити залишкове утримування пилу навикиді в атмосферу до 0,15 г/м3.
Поєднаний процес термічної підготовки шихти і сухого гасіння коксу, розроблений ВУХИНом, має істотні переваги як з точки зору технології та утилізації тепла, так і по своїм екологічним показникам. Суть цієї технології (малюнок 1) полягає в змішуванні подрібненої вологої шихти з розжареним кусковим коксом з подальшим відділенням нагрітої шихти від загашеного коксу.
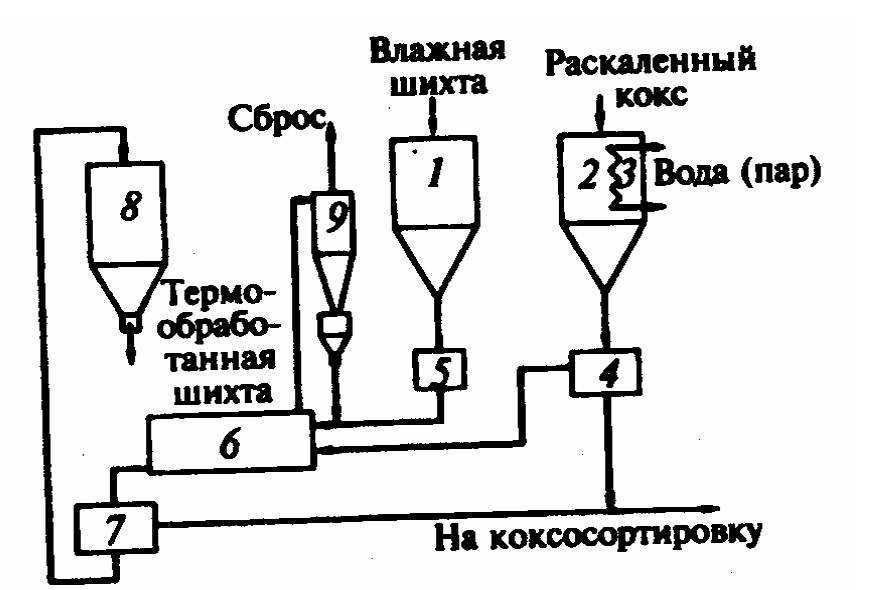
1-бункер початкової шихти; 2-бункер розжареного коксу; 3-рекуператор надмірного тепла коксу; 4-рассів розплавленного коксу; 5-загрузчик початкової шихти; 6-теплообмінний апарат; 7-рассів вуглекоксовой суміші; 8-бункер термічно підготовленої шихти; 9-циклон-відділювач вугільного пилу.
Малюнок 1 - Схема поєднаного процесу термоподготовки шихти і гасіння коксу
Дослідно-промислові дослідження цього процесу на установці продуктивністю 10-12 т/ч проведені на Криворізькому КХЗ. Процес відбувається у закритому теплообмінному апараті, звідки водяні пари за рахунок природної тяги поступають на очищення в циклон типу ЦН-15 і викидаються в атмосферу. До водяних пар, об'єм яких визначається вологістю шихти, внаслідок нещільності в апаратах підсмоктується повітря у кількості 25% від об'єму пари.
Сумарний питомий об'єм газів, що виділяються, при початковій вологості шихти 8,9-9,16% складає 120-140м3/т шихти, зміст пилу в цих газах в середньому - 14 г/м3. Пилегазова суміш, що скидається, має температуру - 100 °С; частки вугільного пилу, що знаходяться в ній,будучи центрами конденсації, покриваються водяною плівкою, завдяки чому вони коагулюють і легко уловлюються в циклоні. Міра очищення в циклоні досягає 99,2%, а залишкова концентрація пилу 110 мг/м3.
Вживані за кордоном способи зменшення пилегазових викидів, що утворюються при завантаженні печей, грунтовані на відведенні в газозбірник шляхом інжекції пари або надсмольной води під високим тиском в стояк, а також відсмоктуванні газів з печі і очищенні перед викидом в атмосферу. Відсисаюче і газоочисне устаткування розміщене на вуглезавантажувальному вагоні або стаціонарно встановлене на землі.
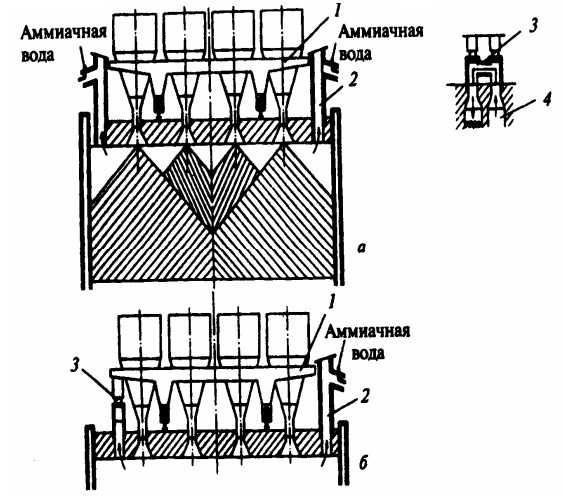
1-вуглезавантажувальний вагон; 2-стояк; 3-перепускний трубопровід, що сполучає завантажувану коксову піч 4 з сусідньою; а - з відведенням газів через стояки завантажуваної печі; б – додатковим відведенням через суміжну камеру
Малюнок 2 - Система бездимного завантаження шихти шляхом гідроінжекції
На нових батареях в Німеччині і інших країнах бездимне завантаження шихти забезпечується відсмоктуванням газів в газозбірник шляхом гідроінжекції. Для печей з широкими камерами коксування (маса завантажуваної шихти 50 т) при оптимальному розташуванні завантажувальних стояків і відповідної конструкції вуглезавантажувального вагону необхідна ефективність досягається при відведенні газів через стояк завантажуваної печі (мал. 2, а).
Для більшої гарантії бездимності на коксовій стороні батареї передбачають іноді міні-стояки, через які завантажувана піч під час завантаження шихти з'єднується з суміжною піччю за допомогою U-образного перепускного патрубка (мал. 2, б) для відведення частини газів в газозбірник через сусідню камеру.
Широко застосовуються за кордоном і комбіновані системи відсмоктування газів, що утворюються при завантаженні : в газозбірник печі і стаціонарний витяжний газопровід на верху батареї.
Для цього використовуються модифіковані вуглезавантажувальні вагони, обладнані системами збору,спалювання і передачі газу, які не можуть бути спрямовані в газозбірник, в стаціонарний газопровід. В процесі завантаження шихти вуглезавантажувальний вагон за допомогою спеціальних пристроїв під'єднується до витяжного газопроводу.
Такі системи вважають за краще також впроваджувати при модернізації коксових батарей, оскільки устаткування їх міні-стояками на коксовій стороні зв'язане з великим об'ємом робіт на перекритті батарей, а застосування гідроінженкції з відсмоктуванням газів, що утворюються при завантаженні, тільки через стояк завантажуваної печі не забезпечує необхідної бездимності. Системибездимного завантаження шихти, впроваджені останніми роками на деяких знову побудованих і реконструйованих коксових батареях, розглянуті нижче.
У Німеччині на заводі в Дуйсбург-Хукингене фірми "Майнесманнререн-верке" на коксовій батареї з печами об'ємом 70 м3 (разове завантаження 60 т шихти 10 % вологості) бездимність завантаження шихти забезпечується застосуванням гідроінжекції. Завантаження вугільної шихти в піч здійснюється через чотири люки за 90 с.
Коксова батарея обладнана газозбірником діаметром 1400 мм на машинній стороні, який розділений по довжині на три ділянки з індивідуальним відведенням від кожного, і стояками збільшеної висоти зі в будованими клапанними коробками і гідравлічним ущільненням кришок.
На заводі "Проспер" фірми "Рурколе" (Німеччина) на двох нових коксових батареях з печами об'ємом 62 м3 для завантаження шихти застосовується чотирьох-бункерна вугленавантажувальна машина (маса з шихтою близько 290 т),бункери якої оснащені горизонтальними шнековими живильниками для примусового вивантаження шихти.
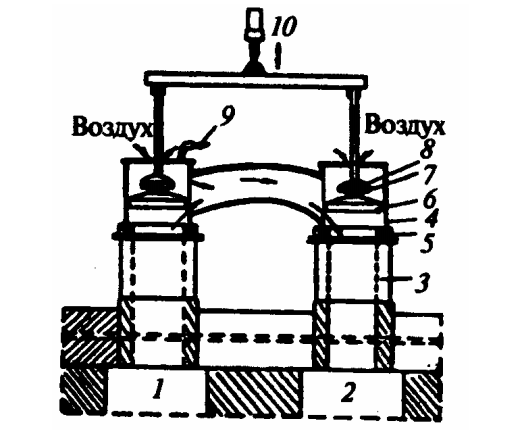
1-завантажувана камера; 2-суміжна камера; 3-газоотводящий патрубок; 4-перепускна труба; 5-водяний затвор; 6-крышка; 7-магнит; конус 8-ущільнювача; 9-клапан скидання; 10-гидроцилиндр
Малюнок 3 - Схема з'єднання суміжних камер коксування при завантаженні шихти
Для забезпечення бездимного завантаження шихти також застосовується система гідроінжекції (тиск над смольної води 3,5 МПа); відсмоктування газів здійснюється через завантажувану і сусідню камери коксування. З цією метою на коксовій стороні батареї встановлені міні-стояки, що сполучаються попарно перепускною трубою (малюнок 3). До кінця процесу завантаження наводиться в дію клапан,через який поступає повітря для витіснення залишкових газів з перепускної труби.
Застосування систем комбінованого відсмоктування газів,що утворюються при завантаженні шихти, в газозбірник коксової печі і стаціонарний витяжний газопровід широко практикується в Японії. Системами бездимного завантаження такого типу оснащені практично усі батареї. Бездимне завантаження здійснюється шляхом відсмоктування частини запилених газів в газозбірник печі за рахунок інжекції аміачної води в стояк, а іншої кількості газів після спалювання - у витяжний стаціонарний газопровід, що проходить уздовж коксової батареї (малюнок 4).
Потужність інжекційної форсунки зазвичай вибирають так,щоб забезпечити відсмоктування в газозбірник майже половини газів, що утворюються при завантаженні.
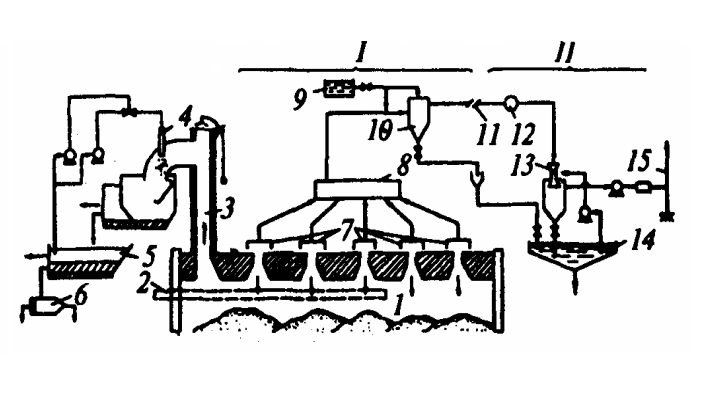
1-камера коксування; 2-планирная штанга; 3-стояк; 4-форсунка для інжекції аміачної води; 5-смолоотстойник; 6-відцентровийвіддільник; 7-витяжні ковпаки; 8-камера спалювання запилених газів; 9-емкость з водою; 10- пилоосаджувач; 11-сполучний клапан; 12-стаціонарний витяжний газопровід; 13-скруббер Вентури; 14-згущувач; 15-димова труба;
I- устаткування, що монтується на вуглезавантажувальному вагоні; II- устаткування монтоване на землі
Малюнок 4 - Система бездимного завантаження шихти в коксові печі
Японською системою бездимного завантаження оснащена коксова батарея № 1 (60 печей заввишки 6,1 м) на металургійному заводі фірми "ЛТВ Стил" в Чикаго(США), розташованому в промисловому районі з високим рівнем забруднення атмосфери, і на коксовій батареї металургійного заводу фірми "Соллак" в Сереманже (Франція). Для завантаження шихти застосовується вуглезавантажувальна машина зварної портальної конструкції,яка монтується на чотирьох приводних візках. Чотири бункери машини виконані з корозійностійкої сталі,обладнані писковими живильниками і механічно-регульованими вимірювальними пристроями для контролю рівня заповнення. Гази відсисаються в газозбірник батареї шляхом інжекції в стояки аміачної води під тиском 4,2 МПа, частково спалюються і через кільцевий простір телескопів і збірний колектор на вуглезавантажувальній машині поступають в стаціонарний витяжний газопровід, сполучений з системою газоочищення.
Ця система розташована у кінці коксової батареї і включає сатуратор, промивальний скрубер Вентури, сепаратор і витяжний вентилятор. Система працює по циклічному графіку, загальна тривалість робочого циклу 7 мін 25 с.
Останніми роками для очищення газів, що утворюються при завантаженні разом з мокрими методами очищення,отримують застосування тканинні фільтри. Спосіб сухого очищення таких газів уперше застосований в Нідерландах при модернізації коксового цеху №1 на заводі фірми "Хооговенс" в Эймейдене. Для забезпечення бездимності завантаження шихти чотирьох-бункерна вуглезавантажувальна машина з тарілчастими живильниками обладнана системою газо-проводов і пристроїв, що забезпечують відведення газів в стаціонарний витяжний газопровід.
Завантаження печі здійснюється автоматично, випуск шихти з бункерів машини регулюється так, щоб швидкість розвантаження кожного бункера відповідала заданою. Гази очищають в тканинних фільтрах "Мікропул", працюючих під тиском в автоматичному режимі. В якості сорбенту і допоміжного матеріалу, що фільтрує,використовують вапняк або доломіт тонкого помелу. Свіжий сорбент періодично подається в трубопровід забрудненого газу за декілька метрів до фільтру, осідає на рукавах фільтра та образуэ лобовий шар. Остатня концентрація пилу в газах складає 1 мг/м3.
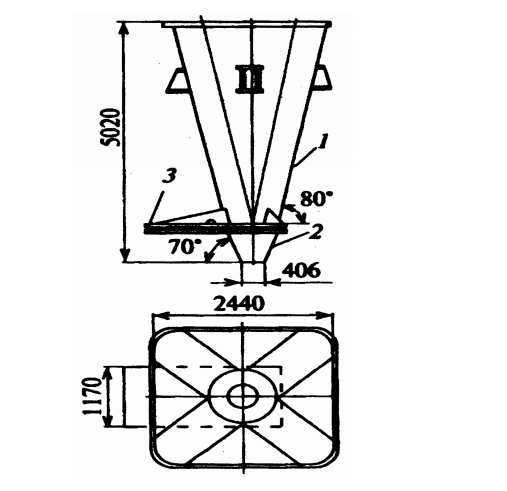
1-бункер; 2-перехідною конус; 3-відсікаюча заслінка
Малюнок 5 - Конструкція бункера з масовим потоком шихти
У Великобританії в якості ефективного рішення, що забезпечує бездимність завантаження шихти в коксові печі, все більше поширення отримує спосіб послідовного завантаження шихти з використанням вугленавантажувальних вагонів (ВЗВ), працюючих за принципом створення масового потоку вивантажуваної шихти. Суть принципу витікання шихти по моделі масового потоку полягає в тому,що частки шихти при її вивантаженні з бункера знаходяться в русі у будь-якій точці об'єму бункера (як у осьовій зоні, так і на периферії). Це запобігає зависанню шихти у бункері, утворенню склепіння і неоднорідності потоку шихти в часі.
Перший бункер нової конструкції (малюнок 5) місткістю 8,5 т, у формі перевернутої піраміди з кутом нахилу стінок 80° випускним отвором діаметром 914 мм, був виготовлений з маловуглецевої сталі завтовшки 8 мм і оснащений комплектом перехідних конусів з нержавіючої сталі з випускними отворами різних.
Випробування бункера підтвердили, що розроблена конструкція забезпечує умови для масового потоку шихти і необхідну швидкість завантаження навіть при використанні важко поточної шихти високої вологості (до 14%) при діаметрі розвантажувального отвору не менше 356мм. Більше того, нормальне витікання шихти з бункера забезпечувалося навіть після зберігання її у бункерів продовж 6 доб., а також легко поновлювалося у разі переривання потоку.
На коксохімічних підприємствах нашої країни шихту завантажують також вуглезавантажувальними вагонами. Вуглезавантажувальний вагон з 3 або 4 бункерами встановлюється над люками належному завантаженню камери, випускні патрубки бункерів за допомогою теле-скопических пристроїв приєднуються до завантажувальних люків, після чого робиться випуск шихти. Бездимність завантаження, як правило,забезпечують шляхом отcoca усіх газів завантаження в газозбірники.
Найбільш поширений метод евакуації газів завантаження через стояки за допомогою парових інжекторів. При цьому ефективність відсмоктування залежить від тиску пари на форсунках (0,7-0,9 МПа).
Основним недоліком методу пароінжекції з точки зору захисту довкілля являється збільшення кількості аміачної води в результаті конденсації пари, витраченої для відсмоктування газів завантаження. У зв'язку з цим останнім часом переважного поширення набуває гідроінжекція з використанням аміачної води циклу газозбірників.
Для реалізації цього методу потрібний насос тиском до 2-3 МПа (малюнок 6) і трубопроводи високого тиску для подання води до форсунок.
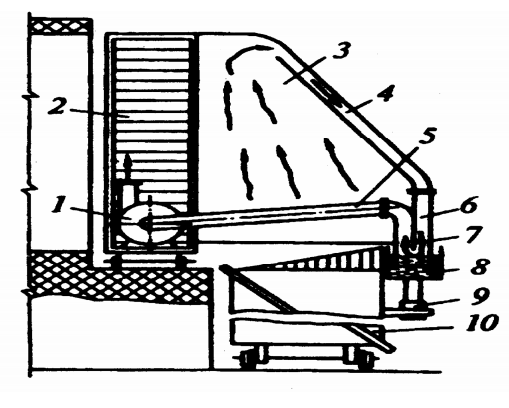
1-вентилятор; 2-коксонаправляюча; 3-зонт; 4-гарячий газохід; 5-холодний газохід; 6-тройник; 7-перегородка; 8- місткість з водою; 9-пневмоцилиндр; 10-гасильний вагон.
Малюнок 6 - Схема пересувної установки бездимної вигрузки коксу
Досвід застосування гідроінжекції показав, що системи працюють стійко і при тиску води >2 МПа, практично повністю забезпечуючи відсмоктування газів. Недоліком цього методу є необхідність регулярного чищення стояків,коліна яких заростають відкладеннями впродовж 7-10 доб.; при недотриманні графіку чищення змінюється форма струменів, внаслідок чого різко знижується ефективні гідроінжекції.
3.3 Зниження викидів при видачі коксу
Боротьба з викидами при виштовхуванні коксу з пічних камер - одне з найбільш складних завдань. Над розжареним коксом, що потрапляє в тушительний або коксо-перисувні вагони, виникає інтенсивна висхідна течія нагрітого повітря, яка залучає до руху значні маси навколишнього атмосферного повітря. Цей підсмоктуваний (що ежектується) з атмосфери потік підхоплює ті, що утворюються при руйнуванні коксового пирога частки пилу і захоплює їх вгору.
В результаті виникає забарвлена пилова хмара значних розмірів, в якій окрім пилу можуть міститися і газоподібні шкідливі речовини, що виділяються з коксу; об'єм цих газів порівняно невеликий і зазвичай не перевищує декількох десятків кубометрів.
Утворення пилової хмари при видачі відбувається дуже швидко, і цей неорганізований викид прийнято відносити до залпових. При видачі коксу недостатній готовності спостерігається утворення густих хмар щільного чорного або чорно-зеленого диму. Такі явища спостерігаються при незавершеності процесу коксування в центрі вугільногозавантаження або нерівномірному обігріві печей, що призводить до появи в завантаженні холодних зон.
Існує декілька варіантів систем бездимної видачі коксу : пилевідсасуючі парасольки над коксонаправляючою гасильних вагонів; перекриття над рейковим шляхом гасильного вагону; комбіновані системи бездимної видачі і гасіння коксу.
Найбільше визнання отримали системи з облаштуванням парасольок, відсмоктуванням і очищенням газів видачі. При цьому відсисаюче і пиловловлююче устаткування проектують як в пересувному, так і в стаціонарному виконанні. На практиці найчастіше використовуються системи з пересувною парасолькою і стаціонарною системою пиловловлювання. В якості пиловловлювачів застосовують скрубери Вентури, мокрі електрофільтри,тканинні фільтри.
Останнім часом за кордоном спостерігається тенденція переходу тільки на сухі пиловловлювачі, як правило, рукавні фільтри. У СНД спочатку застосовувалася пересувна система знепилювання газів видачі, змонтована на дверес’емної машині. Легка парасолька з'єднувалася з групою з двох циклонів і димотягочем. Такі системи на батареї з об'ємом камер 41,6 м3 уловлювали приблизно 750 кг пилу в добу. Проте передбачене проектом видалення пилу з бункерів циклонів шнековими транспортерами виявилося непрацездатним, циклони швидко забивалися пилом, що призводить до інтенсивного зносу димотягочів і виходу їх з ладу.
У 1983г. на Коммунарском коксохімічному заводі була пущена перша установка бездимної видачі коксу (УБВК) із стаціонарною системою відсмоктування і очищення газів (малюнок 7). У подальші роки подібні установки були змонтовані ще на ряду заводів. Існуючі тенденції все ще базуються на збільшенні об'єму газів, що відсисаються, до 150-180 тис. м3/ч з відповідним збільшенням розмірів і конструкції парасольки.
Концентрація пилу в газі, що відсисається з підпарасольки, досягає 18-22 г/ м3. Встановлюючи на-першому ступені очищення групи циклонів, досягають сумарної міри очищення 99,1-99,2% при залишкової концентрації пилу в газах видачі 0,11-0,22 г/м3. Неважко бачити, що збільшивши об'єм газів, що відсисаються, отримуємо підвищену запилену, зменшення якої до необхідних норм вимагає підвищення міри очищення.
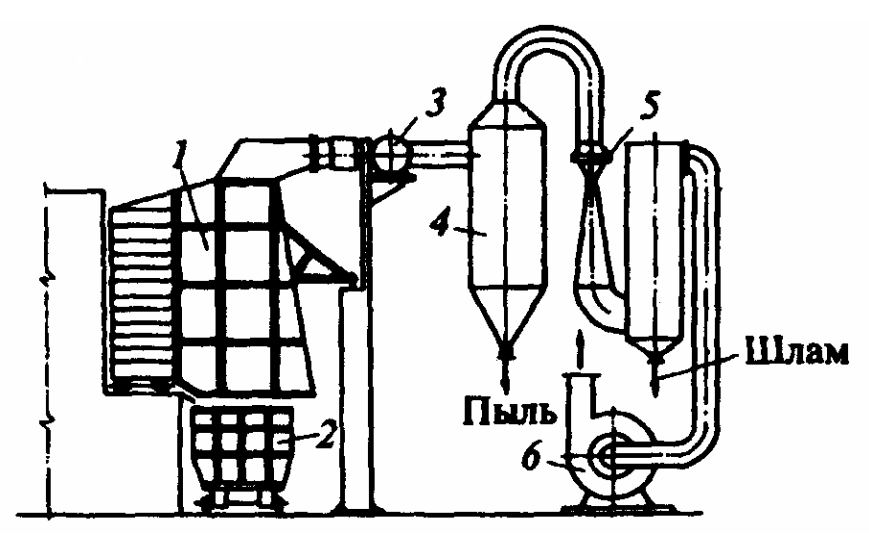
Малюнок 7 - Схема установки бездимної видачі коксу із стаціонарною системою очищення
Для скорочення неорганізованих викидів, що утворюються при видачі коксу з камер коксування в гасильний вагон, на коксових батареях № 5 і 6КХП АТ "Северсталь" в 1997г. побудована установка бездимної видачі коксу. На дверез’ємної машині встановлена парасолька, яка закриває "кошик" коксонаправляючої і гасильний вагон.
За допомогою телескопічних патрубків, встановлених на парасольці, відбувається стикування парасольки і газового колектора, призначеного для транспортування газоповітрянної суміші на очищення в двох електрофільтрахтипу ЭГА. Потім повітря, очищене від мелкодисперснойпилу до концентрації 50-80 мг/ м3, викидається в атмосферу, а уловлена электрофільтрами пил використовується як добавка в шихту для коксування. Скорочення викидів пилу в атмосферу при видачі коксу складає 200 т/рік.
Вживаних нині за кордоном систем бездимної видачі коксу (перекриття над усією коксовою стороною батареї; відсмоктування і очищення газів, що виділяються, в стаціонарній системі скруберів; пиловловлюючі парасольки над коксонаправляючою і гасильним вагоном з газоочисним устаткуванням на гасильному вагоні або сполученій з ним платформі; пиловловлюючі парасольки над коксонаправляючою і гасильним вагоном із стаціонарними витяжним газопроводом і системою газоочищення) найбільш ефективними визнані системи останнього типу.
У Японії такими системами оснащені практично усі коксові батареї. Схема однієї з таких систем показана на малюнку 8. Ширина пиловловлюючої парасольки дорівнює ширині коксоприемного вагону, довжина коливається від 6 до 10 м залежно від об'єму камери коксування. Потужність димотягача в системі бездимної видачі при 40 °С складає 2500-4500 м3/мін залежно від об'єму камери коксування. Для очищення газів застосовуються як мокрі,так і сухі методи очищення.
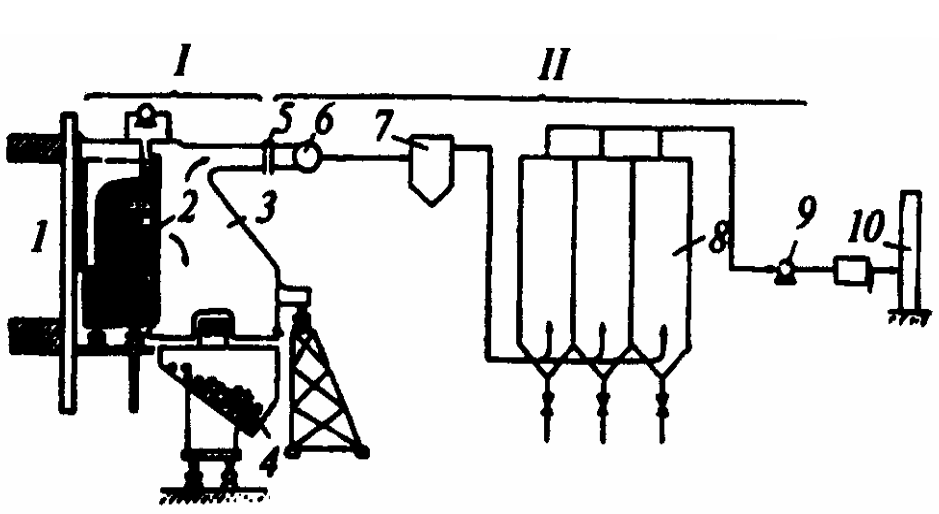
1-камера коксування; 2-коксонаправляющая; 3-пиловловлююча парасолька; 4-коксоприемный вагон; 5-сполучний клапан; 6-стаціонарний витяжний газопровід; 7-пылеосадитель; 8-тканинний фільтр; 9-дымосос; 10-димова труба;
I- устаткування, що монтується на коксонаправляючій; II-устаткування, що монтується на землі
Малюнок 8 - Система бездимної видачі коксу з печей
Широке визнання у світі отримала система бездимної видачі типу "Министер Штайн", розроблена фірмою"Хартунг, Кун унд Ко" (Німеччина). Ця система забезпечує практично 100 % пиловловлювання (залишковий зміст пилу в газах після тканинних фільтрів складає < 20 мг/м3). Викиди пилу при видачі коксу знижуються до 5 г/т коксу. Пропускна спроможність газоочищення з тканинними фільтрами, використовуваної в цій системі бездимної видачі, складає > 200 тис. м3/ч.
Система відрізняється oт інших систем такого типу способом стикування газопроводу з пиловловлюючою парасолькою. Пересувна парасолька закриває повністю коксоприємний вагон і коксонаправляючою під час видачі коксу. Парасолька спирається на майданчик коксової сторони батареї і додаткову рейку.
Його підключають до стаціонарного газопроводу перед видачею коксу за допомогою сполучного патрубка, що рухається на візку над верхньою частиною газопроводу, що має тріщину, закриту гратами, які служать опорою для стрічки з високотемпературного єластомера, що закриває тріщину. Така конструкція усуває необхідність в устаткуванні стаціонарного газопроводу безліччю заслінок навпроти кожної печі.
Система бездимної видачі коксу типу "Министер Штайн" останніми роками впроваджена на нових коксових батареях в Німеччині, Великобританії, Нідерландах, США. В ході вдосконалення вказаної системи фірмою "Хартунг,Кун унд Ко" разробленна конструкція нової коксонаправляючої машини, виконаної як єдине ціле з пиловловлюючою парасолькою. Такими системами бездимної видачі коксу в Німеччині оснащені усі нові коксові батареї на ряду заводів.
3.4 Знепилювання при гасінні коксу
Процес мокрого гасіння коксу в його звичайному апаратурному оформленні надзвичайно складений з точки зору очищення парогазової суміші, що викидається. Впродовж 1 -2 мін з гасильної вежі сучасного коксохімічного заводу викидається в атмосферу близько 20 тис. м3 водяна пара, об'єм якої збільшується із-за підсосу навколишнього повітря. Використання забрудненої води для гасіння коксу призводить до збільшення викидів шкідливих речовин.
Так, при використанні чистої води кількість твердих часток, що викидаються в атмосферу, складає 0,23-1,13 кг/т коксу,а при застосуванні стічних вод 0,68- 2,26 кг/т коксу. Питоме винесення пилу на 1 т коксу збільшується на 0,4 г при збільшенні сухого залишку в циркулюючій воді на 0,1г/ч. Скорочення викидів твердих часток в процесі мокрого гасіння при звичайному апаратурному оформленні досягається облаштуванням спеціальних краплевідбійників або додаткових ярусів того, що розпиляло води через форсунки.
На металургійному заводі фірми "Бритиш стил" в Порт-Толботе гасильна вежа, виконана з армованого бетону і футерована щільною кислототривкою цеглиною,закінчується дерев'яною трубою з пристроєм для затримання твердих часток. На металургійному заводі в Дуйсбург-Хукингене фірми "Маннесманнререн-верке" коксова батарея з печами об'ємом 70 м3 обладнана гасильною вежею, що є бічною витяжною дерев'яною трубою із сталевою обшивкою заввишки 40 м. Площа поперечного перерізувежі в чотири рази більше площі гасіння, що забезпечує зниження швидкості пари на виході і кількості пилу, що викидається.
Для екологічного захисту за кордоном розробляються і впроваджуються принципово нові способи мокрого гасіння. У ФРН фірмою "Эшвейлер Бергверксферайн" розроблений спосіб гасіння коксу під тиском. Система складається з гасильного вагону, вузької парасольки, сполученої з коксонаправляючеї і підключеного до системи знепилювання, і станції гасіння. Коли гасильний вагон встановлений для видачі, контейнер вагону піднімається впритул до парасольки.
В той же час телескопічний газохід, що йде від верхньої частини парасольки, приєднують до двох звичайних скруберів, розташованих на шасі гасильного вагону (малюнок 9). В якості альтернативного варіанту парасолька може бути приєднана до витяжного газопроводу із стаціонарною знепилюючою установкою.
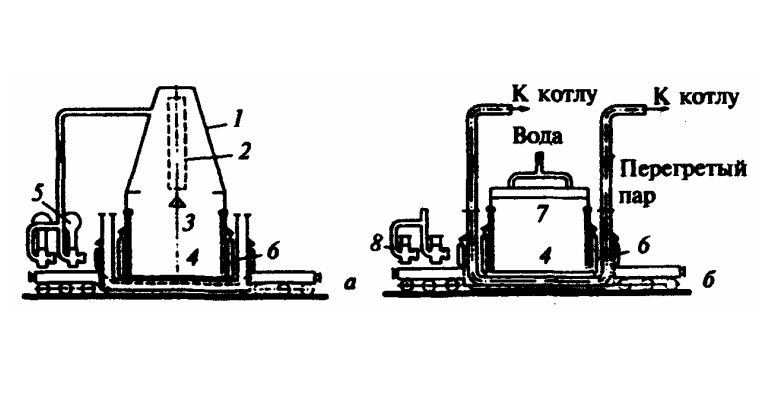
1-пиловловлююча парасолька; 2-кокс зкоксонаправляющей; 3-распределитель; 4-кокс; 5-чистий газ; 6-гидроцилиндры; 7-крышка з соплами; 8-скрубберы
Малюнок 9 - Схема процесу гасіння коксу під давленим
Підсоси повітря мінімальні, тому об'єм газів, що відсисаються, може бути зменшений на 20от що зазвичай відводиться в системі бездимної видачі типу "МинистерШтайн". Витрата води на гасіння складає 0,6-0,7 м3/т коксу. У США фірмою "Хрінниця" розроблені спосіб непрямого охолодження коксу водою і устаткування для бездимної видачі. Видача коксу з печі робиться в сталевий контейнер, ідентичний за формою і розмірам камері коксування і встановлений на автомобільній платформі. У міру просування гарячого коксового пирога з камери коксування в контейнер робиться зрошування контейнера водою.
Після закінчення видачі і видаленні виштовхуючої штанги з печі ковзаючі двері контейнера закриваються і робляться автоматичне ущільнення його за допомогою водоохолоджуваного і водозаповненого ущільнення зеластомера. Заповнений коксом контейнер транспортується потім відпечі до гасильної станції, де він по роликах перекочується з автомобільної платформи на спеціальний стелаж, що вміщує декілька контейнерів. Процес охолодження коксу водою, що стікає по герметичних стінках контейнера, триває тут до тих пір, поки температура коксу не знизиться нижче точки повторного займання його (~ 2,5 г.).
Потім контейнер з охолодженим коксом знову перевантажується на автомобільну платформу і транспортується до модифікованої коксової рампи, обладнаної дверима типу гільйотини з ущільненням, що запобігає викидам пилу в атмосферу при розвантаженні коксу. Платформа нахиляє контейнер до рампи для полегшення сходу коксу з нього. З рампи кокс самопливно поступає на коксосортіровку, а порожній контейнер транспортується для прийому коксу з чергової розвантажуваної печі.
Основною перевагою цього способу є можливість отримання абсолютно сухого коксу, оскільки при охолодженні він не контактує з водою. Фізичне тепло коксу передається шляхом конвекції водо охолоджуваним стінкам контейнера і може легко утилізувати для різних виробничих цілей. Завдяки м'якому режиму охолодження і відсутності проміжних перевантажень покращуються структурні і прочностні властивості коксу, скорочуються втрати від подрібнення.
Повністю усуваються викиди в атмосферу від видачі досортування коксу. Капітальні витрати на таку систему знижуються на 80% оскільки не потрібно коксонаправляючої, гасильноговагону, гасильної вежі і іншого устаткування, а вихід коксу підвищується на 12-15%. Для обслуговування кожних шести печей батареї потрібно один контейнер; тривалість циклу пробігу автоплатформи, що несе, для кожної видачі коксу склала 7,5 хв.
У промисловому масштабі ця технологія впроваджена на металургійному заводі в Спарроус-Пойнте фірми "Бетлихем Стил" (США), на двох коксових батареях. Технологія забезпечує зниження на 90% викидів при видачі і гасінні коксу. При сухому гасінні коксу екологічні проблеми пов'язані з необхідністю скидання в атмосферу надмірної частини циркулюючого охолоджувального газу, 8-14% СО, що містить, і забрудненого коксовим пилом. Крім того, підвищується концентрація пилу на трактах коксоподачі і у відділенні коксосортировки, у зв'язку з чим, виникає необхідність в посиленій аспірації цих приміщень і очищенні великого об'єму вентиляційних викидів.
Для зниження пиле виделення на коксосортировке, конвеєрах коксу, завантажувальних облаштуваннях доменної печі при використанні коксу сухого гасіння в Японії, наприклад, застосовують зрошування коксу в процесі передачі на конвеєр, що веде до доменної печі,водою у кількості 0,5% без додавання змочувачів.
У складі УСТК є два джерела організованих викидів в атмосферу: свічка надмірного інертного газу після димососу і свічка, через яку викидаються гази, що виділяються з коксу у форкамері. Значне забруднення атмосфери цими викидами (питомі викиди пилу складають відповідно до 5,7-11,5 і 17,6-28,8 г/м3 згашений кокс) вимагає розробки заходів по їх скороченню. Окрім пилу, викиди свічок УСТК містять значну кількість СО (до 5 і 18% (объемн.) відповідно зі свічки димососу і форкамери).
Впровадження сухого гасіння коксу на вітчизняних коксохімічних заводах потрібне, передусім тому, що воно дозволяє поліпшити якість коксу в умовах сировинної бази коксування, що безперервно погіршується. Проте в сучасному виконанні установки сухого гасіння коксу викидають в атмосферу більшу кількість шкідливих речовин, чим гасильні вежі при мокрому гасінні коксу біохімічно очищеною стічною водою.
Проте, одним з достоїнств способу сухого гасіння коксу в екологічному відношенні є те, що викиди на цих установках носять організований характер і можуть бути піддані очищенню, завдяки чому досягається загальне скорочення питомих викидів в атмосферу при виробництві коксу.
Температура коксу після УСТК досягає 150-200 °С. При транспортуванні, перевантаженнях, грохоченні такого коксу відбувається інтенсивне пилевиділення, тому технологічне устаткування забезпечують аспірацій ними установками. Призначення аспіраційних систем - створення сприятливих умов праці за змістом шкідливих речовин в повітрі виробничих приміщень шляхом відвертання виділень з нещільності технологічного устаткування.
Аспіраційні системи розташовують відповідно до технологічної схеми УСТК і сортування коксу сухого гасіння (малюнок 10).
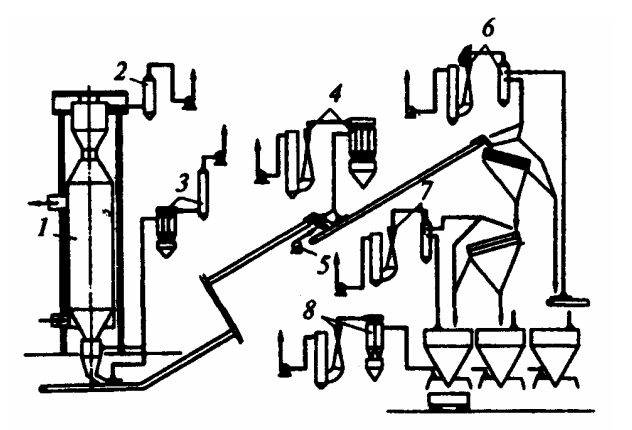
-камера УСТК; 2-а.с. вузла завантаження УСТК (скруберЦС); 3-а.с. вузла вивантаження УСТК (група циклонів ЦН,скрубер ЦС); 4-а.с. перевантажувального вузла (групациклонів, скрубер КМП); 5-дутьевой вентилятор станціїзнепилювання коксу; 6-а.с. валкового гуркоту (колектор ВК,скрубер КМП); 7-а.с. інерційного гуркоту (колектор ВК,скрубер КМП); 8-а.с. вузла вантаження коксу у вагони(група циклонів ЦН, скрубер КМП)
Малюнок 10 - Схема аспіраційних систем (а.с.) УСТК і коксосортировки (ВАТ "НТМК")
До складу аспіраційних систем включають сухі і мокрі пиловловлювачі. При вивантаженні гарячого коксу з камер УСТК виділяється багато пилу, тому зазвичай застосовують двоступінчату схему очищення. В якості першого ступеня використовують групи циклонів типу ЦН-15, що мають досить високу ефективність пиловловлювання (87-97%) при помірному гідравлічному опорі (0,35-1,15 кПа). На другому ступені пиловловлювання встановлюють скрубери ЦС-ВТИ. Фактична міра уловлювання пилу в них - від 60 до 90% і визначається в основному витратою зрошуючої рідини і якістю її распилення. Коксовий пил по існуючій класифікації може бути, як правило, віднесена до класу крупно дисперсних. Це спрощує завдання знепилювання аспіраційного повітря сухими методами.
4. Розрахунок еколого – економічній ефективності застосування установки сухого гасіння коксу на прикладі Макіївського коксохімічного заводу ЧАО"МАКІЇВКОКС"
Розрахунок еколого - економічній ефективності застосування установки сухого гасіння коксу на прикладі Макіївського коксохімічного заводу ЧАО "МАІЇВКОКС" виконаний для річного обсягу виробництва коксу 860 тис.т. Ставу екологічного податку, грн/т викидів : аміак - 269,08; сірководень - 4 610,83; діоксид сірки - 1 434,71; монооксидвуглецю - 54,05; оксиди азоту - 1434,7; фенол - 6 512,02,бенз(а)пирен - 1 977 992. Кошти, що інвестуються, на реалізацію проекту по впровадженню УСТК складають 200 млн. грн. Ставка кредиту 25% .
Були розрахованні витрати на виробництво коксу, а також витрати, пов'язані з екологічними платежами до і після впровадження УСТК. Також були зроблені розрахунки ефективності від виробництва пари і електроенергії. Розрахунок калькуляції собівартості продукції показаний в таблиці.1.
Таблиця 1 - Розрахунок калькуляції собівартості коксу
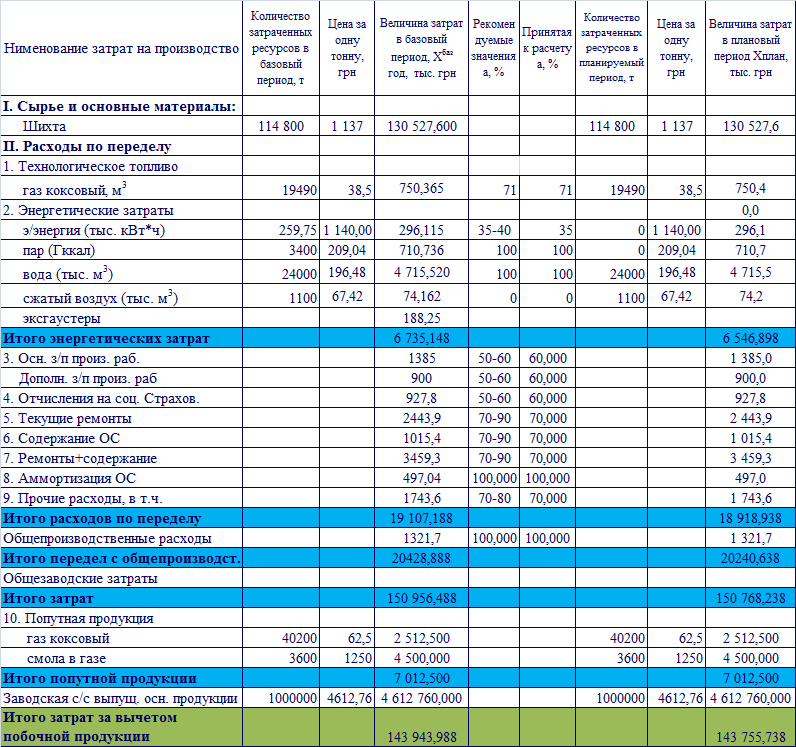
Результати розрахунків від впровадження УСТК приведені в таблиці 2.
Таблиця 2 - Результати розрахунку ефективності впровадження УСТК
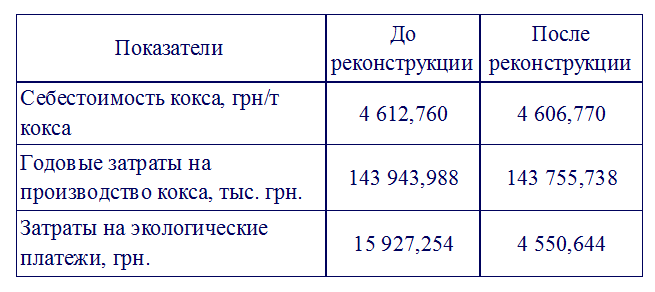
З таблиці. 1 видно що витрати на виробництво коксу до і після впровадження УСТК складають відповідно до 143 927 тис. грн/рік і 143 755 тис. грн/рік. Зміни витрат на виробництво коксу після реконструкції складають 188,25 тис. грн Екологічні платежі скорочуються в 3,5 рази. При цьому термін окупності проекту (враховуючи виплати по кредиту із ставкою в 25составляет 2,3 року (дивися таблицю. 3).
Таблиця 3 - Розрахунок терміну окупаемості УСТК
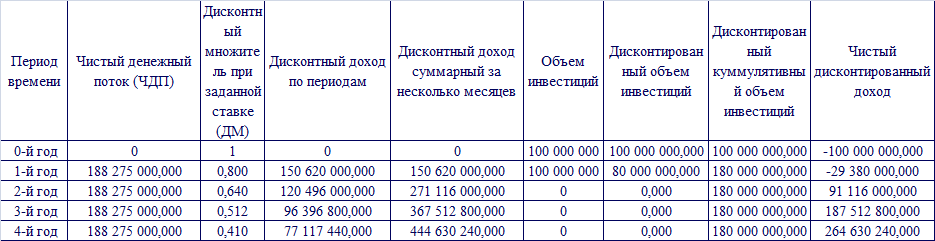
Розрахунок за визначенням ефективності від виробництва пари на УСТК показує, що при собівартості 1Гкал пари в 50 грн (ціна пари, вироблюваної з використанням палива, при цьому дорівнює 100 грн/Гкал.При гасінні 1.0 млн. т/рік коксу буде зроблений пара 350тис. Гкал. Ефект використання пари УСТК складає 26 млн.грн в рік.
Розрахунок за визначенням ефективності виробництва електроенергії з пари показує, що на парі УСТК енергетичних параметрів ~4 МПа і 44°З можна робити до100 кВт*ч електроенергії на 1 т загашеного коксу при роботі турбогенератора в конденсаційному режимі і 55кВт*ч при роботі в режимі з відборами пари 0.16 Гкал/т загашеного коксу. Ефект виробництва електроенергії складає 11,4 млн. грн/рік.
Висновки:
Впровадження системи бездимного завантаження вугільної шихти в камеру коксування і установки бездимної видачі коксу дозволяє понизити викиди в атмосферу на 90%.
Впровадження установки сухого гасіння коксу забезпечує:
- зниження витрат на виробництво коксу з 143 927 тис. грн/рік до 143 755 тис.грн/рік;;
- зниження екологічних відрахувань в 3,5 разу;
- Ефект від використання пари УСТК складає 26 млн. грн врік;
- Ефект виробництва електроенергії складає 11,4 млн. грн/рік;
- Термін окупності проекту (враховуючи виплати по кредиту із ставкою в 25составляет 2,3 року.
При написанні даного реферату магістерська робота ще не завершена. Остаточне завершення: грудень 2011 року. Повний текст роботи та матеріали по темі можуть бути отримані у автора або його керівника після вказаної дати.
Перелік посилань
- БольшинаЕ.П. Экология металлургического производства: Курс лекций. – Новотроицк: НФ НИТУ «МИСиС», 2012. – 155 с.
- Кауфман А.А., Харлампович Г.Д. Технология коксохимического производства: Учебное пособие. – Екатерингбург: ВУХИН-НКА, 2005. – 288 с.
- Кауфман А.А. Мастер коксового производства. – Екатеринбург: ВУХИН, 2002. – 228 с.
- Иванов Е.Б. Технология производства кокса / Е.Б. Иванов, Д.А. Мучник. – Издательское объединение «Вища школа», 1976. – 232 с.
- Мищенко И.М. Черная металургия и охрана окружающей среды: учебное пособие. – Донецк: ГВУЗ «ДонНТУ», 2013. – 452 с.
- Успенский С. К. и др. Совершенствование технического уровня и повышение эффективности установок сухого тушения кокса // Кокс и химия. 1988, с. 38 – 41.
- Родькин С. П. и др. Комплексная оценка эффективности сухого тушения кокса // Кокс и химия. 1988. № 4, с. 48 – 51.
- Кокс. Коксохимическое производство [Электронный ресурс]. – Режим доступа: http://www.metaljournal.com.ua/coke.
- Сухоруков В.И. Научные основы совершенствования техники и технологи производства кокса. – Екатеринбург: ВУХИН-НКА, 1999. – 393 с.
- Пыриков А.Н. Защита окружающей среды на коксохимических предприятиях / А.Н. Пыриков, С.К. Васнин, Б.Н. Баранбаев. – М.: Интермет – инжиниринг, 2000. – 176 с.
- Родионов А.И. Техника защиты окружающей среды / А.И. Родионов, Н.С. Торочешников. – М.: Химия, 1989. – 325 с.
- Лейбович Р.Е. Технология коксохимических производств / Р.Е. Лейбович, Я.М.Обуховский, С.Я. Сатановский, П.М. Кутовой. – М.: Металлургия, 1974. – 420 с.
- Браун Н.В., Глущенко И.М. Перспективные направления развития коксохимического производства. – М.: Металлургия, 1989 г. – 272 с.
- Рудыка В.И. Коксовая батарея с печными камерами объемом и боковым подводом смешанного газа / В.И. Рудыка, Н.Ю. Чеботарев, О.Н. Суренский, В.В. Деревич // Кокс и химия, - 2009. - № 7. – С. 25-27.
- Власов Г.О. Системный анализ коксохимического производства / Г.О. Власов, В.И. Саранчук, В.М. Чуищєв, В.В. Ошовський. – Д.: ДонГТУ «Східний видавничий дім», 2002. – 296 с.
- Ярошенко Ю.Г. Энергоэффективные и ресурсосберегающие технологи черной металлургии: учебное пособие / Ю.Г. Ярошенко, Я.М. Гордон, И.Ю. Ходоровская. Под ред. Ю.Г. Ярошенко. – Екатеринбург: ООО «УИПЦ», 2012. – 670 с.
- Зингерман Ю.Е. Внедрение установки беспылевой выдачи кокса / Ю.Е. Зингерман, В.Б. Каменюка, Т.Ф. Трембач // Кокс и химия, – 2004. – № 7. – С. 34
- Лейбович Р.Е. Технология коксохимического производства: Учебник для техникумов, изд. 3-е, доп. и перераб / Р.Е. Лейбович, Е.И. Яковлева. – М.: Металлургия, 1982. – 360 с.
- Зингерман Ю.Е. Внедрение новых технологий и разработок / Ю.Е. Зингерман, В.И. Рудыка, В.В. Кривонос, В.В. Гураль // Кокс и химия. - 2009. – № 9. – С. 51
- Общая схема коксохимического производства [Электронный ресурс]. – Режим доступа: http://opeaulay.ucoz.ru/news/obshhaja....
- Углеподготовительный цех коксохимического производства [Электронный ресурс]. – Режим доступа: http://www.borpak.ru/ugolnaya....
- Зашквара В.Т. Подготовка углей к коксованию / В.Т. Зашквара, А.Г. Дюканов. – М.: Металлургия, 1981. – 260 с.
- Жидко А.С. Совершенствование и оптимизация технологи подготовки углей для коксавания. – Челябинск: Металлургия, 1989. – 189 с.
- Посохов М.Ю. Первая установка избирательного измельчения углей с пневмосепарацией в Китае/ М.Ю. Посохов, В.И. Сухоруков, Чэнь Кай // Кокс и химия, - 2006. - № 7. – С. 5-9.
- Иванов Е.Б. Технология производства кокса / Е.Б. Иванов, Д.А. Мучник. – Издательское объединение «Вища школа», 1976. – 232 с.
- Пыриков А.Н. Защита окружающей среды на коксохимических предприятиях / А.Н. Пыриков, С.К. Васнин, Б.Н. Баранбаев. – М.: Интермет – инжиниринг, 2000. – 176 с.
- Родионов А.И. Техника защиты окружающей среды / А.И. Родионов, Н.С. Торочешников. – М.: Химия, 1989. – 325 с.
- Браун Н.В., Глущенко И.М. Перспективные направления развития коксохимического производства. – М.: Металлургия, 1989 г. – 272 с.
- Рудыка В.И. Коксовая батарея с печными камерами объемом 51 м3 и боковым подводом смешанного газа / В.И. Рудыка, Н.Ю. Чеботарев, О.Н. Суренский, В.В. Деревич // Кокс и химия, - 2009. - № 7. – С. 25-27.
- Власов Г.О. Системный анализ коксохимического производства / Г.О. Власов, В.И. Саранчук, В.М. Чуищєв, В.В. Ошовський. – Д.: ДонГТУ «Східний видавничий дім», 2002. – 296 с.
- Зингерман Ю.Е. Внедрение установки беспылевой выдачи кокса / Ю.Е. Зингерман, В.Б. Каменюка, Т.Ф. Трембач // Кокс и химия, – 2004. – № 7. – С. 34
- Бородин М.В. Энергоресурсы коксохимической промышленности Украины. Направления их использования / М. В. Бородин, В. Ю. Попов, Э. В. Старченко // Кокс и химия – 2000. - № 7 – С. 45 – 47.
- Зингерман Ю.Е. Внедрение новых технологий и разработок / Ю.Е. Зингерман, В.И. Рудыка, В.В. Кривонос, В.В. Гураль // Кокс и химия. - 2009. – № 9. – С. 51
- Газоочистные аппараты и установки в металлургическом производстве. Учебник для вузов/ С.Б. Старк. Изд. 2-е, перераб. и доп. – М.: Металлургия, 1990. –400 с.
- Инженерная защита окружающей среды. Учебное пособие / под ред. Воробьева О.Г. –СПб.: изд. Лань, 2002. –288 с.
- Курс инженерной экологии. Учебник для вузов/ Под ред. Мазура И.И. – М., Высшая школа, 1999. – 447 с.
- Мазур, И.И. Курс инженерной экологии. Учебник для вузов /И.И. Мазур, О.И. Молдаванов / под ред. И.И. Мазура –М.: Высшая школа, 1999. –447 с.
- Воскобойников В.Г. Общая металлургия. Учебник для вузов/В.Г. Воскобойников, В.А. Кудрин, А.М. Якушев. 6-изд., перераб. и доп. – М.: ИКЦ «Академкнига», 2002. –768 с.
- Цветков, Ю.В. О создании экологически чистого энергометаллургического комплекса /Ю.В. Цветков//Экология и промышленность России, № 5, 1999, с.11-15.
- Денисенко, Г.Ф. Охрана окружающей среды в черной металлургии. Учебное пособие / Г.Ф. Денисенко, З.И. Губонина. –М.: Металлургия, 1989. –120 с.