Abstract for Improving the efficiency of hydro cleaning underground tanks coal mines
Content
Introduction
Efficient operation of the mine drainage installation depends on the pollution (siltation) underground containers (the headers, suction wells, sumps, etc.). Consequently, it affects the financial well-being of the enterprise and, t. To. Dewatering installations are powerful power consumers in the enterprise (25%). As practice shows operating drainage installations, uptime is only 1400...2000 hours, and the efficiency of the drainage installation is equal to the 0,42...0,46. As a result of reduced performance, even a properly designed drainage installation in a few months changes its characteristics by 10–15%.
Purification of the headers from the slurry will increase resource efficiency drainage installation as a whole, by increasing the resource wearing parts, to which the work on the clean water is a primary necessity. On the removal of the sludge from the water tanks annually spent 440 thousand. man-shifts and more than 2,8 mln UAH. This often traditional methods are very time-consuming and ineffective and are reduced to hand-cleaning water tanks [2].
One of the technologies replacing manual labor is the use of hydraulic elevator.
1. Theme urgency
Hydrodynamic cleaning underground tanks differs significantly from the mechanical, so that the increased safety, reduced number of staff, there is a substantial savings, continuity.
2. Goal and tasks of the research
The study aims to improve the efficiency hydromechanical cleaning underground tanks using hydroelevators advanced design solutions.
The main objectives of the study:
- An analysis of the literature on existing methods of cleaning silo tanks.
- Justification of energy efficiency hydroelevators ways of working.
- Numerical modeling workflow hydraulic elevator.
- Development of recommendations to improve the energy efficiency of hydraulic elevator and the cleaning efficiency of underground tanks.
3. Overview
When hydroelevating technology combined into one process cleaning and pumping water. Basic equipment – hydraulic elevator.
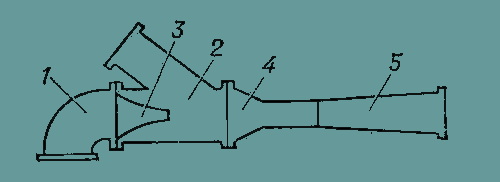
Figure 1 – hydroelevators:
1 – penstock, 2 – suction pipe, 3 – nozzles, 4 – confuser and mixing chamber, 5 – diffuser
The principle of operation is based on a hydraulic elevator the law of conservation of energy of the liquid, the Bernoulli equation:
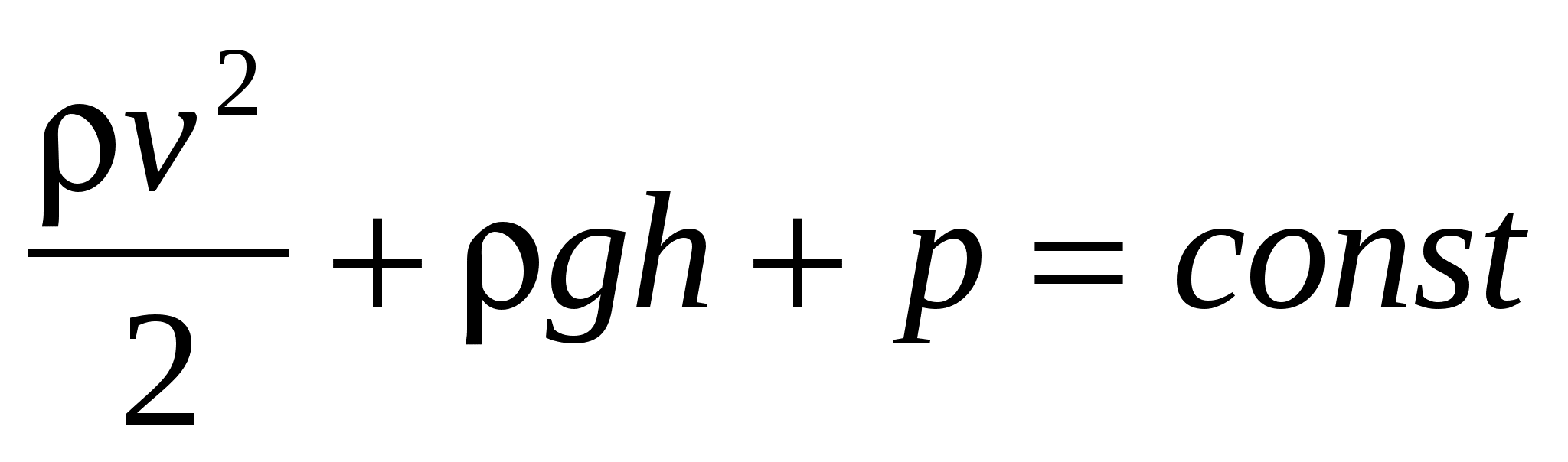
The working fluid (pellet), doing the calculated pressure in the nozzle (nozzle) increases the speed (velocity pressure), ie. E. Creates the first term of the Bernoulli equation; thereby correspondingly reduced the second term (the pressure energy), as the third term (energy of position) and the amount of power – constant.
The sudden reduction in pressure receiving chamber a vacuum is created, whereby the pulp (water) in the suction tube sucked. Here, a mixture of the working fluid and suction, having a high speed mixing chamber (neck) hydraulic elevator, enters the diffuser, which gradually takes the fast expanding energy partially back into pressure energy; this energy It is used in an injection pipe for lifting or transfer the entire mass of water or sediment.
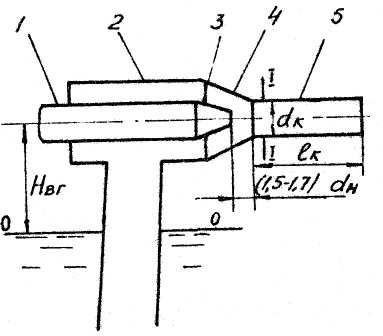
Figure 2 – Working hydraulic elevator:
1 – penstock,
2 – suction pipe, 3 – nozzles 4 – confuser, 5 – the mixing chamber
(animation: 5 frames, 6 cycles of repetition, 21.6 KB)
This apparatus has no moving or rotating parts, easy to manufacture, has small dimensions and weight. These qualities are at low capital and operating costs and high feeding provide reliable and durable operation in harsh and cramped underground conditions: under the rubble, in the flooded area or gassy. When the process of cleaning is eliminated hydroelevating fill water systems during repeated its launch. Experience has shown that the hydroelevating cleaning is performed with a minimal number staff. Comparative analysis of the mechanical and hydroelevating cleaning methods showed that the increase hydroelevating labor productivity in the 15–20 times; improve reliability (availability factor is increased from 0,8 to 0,99), the durability of the pumps the main drainage 5–8 times; reduce the cost of cleaning equipment 4–6 times, the power consumption in the 1,5–2 times; improve conditions operation and increased safety. In addition, the development and production of hydroelevators any power companies operate, operating such installations, the use of hydraulic elevator only for pumping water from sumps skip shaft instead of centrifugal pumps while maintaining the mechanical method of cleaning it is technically and economically feasible [5].
The main drawback hydroelevators – low efficiency, which is the best modern structures, working in optimal conditions, without greater than 30% and usually much lower, only 10–15%. With increasing efficiency slurry lift hydraulic elevator sharply It reduced, which makes it virtually unusable at considerable height and distance of transportation of the pumped liquid. None hydroelevators least have a fairly broad and successful application.
References
- Kamenev P. N. hydroelevators other inkjet devices / P. N. Kamenev. – M .: Mashstroyizdat, 1950. – 346 p.
- Maleev V. B. Special means of drainage and purification of mine drainage hydromechanized containers / V. B. Maleev, E. I. Daniov, V. Yakovlev. – Donetsk, Donetsk National Technical University, 1986.
- Bolotskih N. S. Research waterjet pumps. Hydraulic machines. / N. S. Bolotskih. – Rep. Mezhv. Coll., Kharkov, 1973, vol. 7. – P.93-99.
- Geyer V. G. Airlift installation / V. G. Geyer, V. S. Pashchenko, L. N. Kozyryatsky, J. Antonov. – Donetsk, Donetsk National Technical University, 1982.
- Bezuglov N. N. Hydroelevators in coal mines / N. N. Bezuglov, L. N. Bezuglova, A. J. Goncharov. – Moscow, Nedra, 1987.
- Bezuglova LN Hydroelevating method of treatment of mine water tanks / L. N. Bezuglova. – Coal, 1983 – №4. P. 25-26.
- Special means of drainage and purification of mine drainage hydromechanized containers: Textbook. – Donetsk: PDI, 1986. – 36 p.
- Geyer V. G. Hydraulics and hydraulic / Geyer V., V. S. Dulin, A. G. Borumensky, A. N. Zarya – M .: Nedra, 1981. – 295 p.
- Krnvchenko G. I. Hydro transients in hydropower plants / G. I. Krnvchenko, N. N. Arshenevskny, E. V. Kvyatkovskaya, V. M. Klabukov . – M., "Energy", 1975. – 367 p.
- Abkhazia V. I. dredging, mining sand and gravel / V. I. Abhazin. – M., "Energy", 1972. – 139 p.