Реферат на тему: Оптимизация параметров исполнительного органа проходческого комбайна по критерию износа резцов
Содержание
- Введение
- 1. Актуальность темы
- 2. Цель и задачи исследования, планируемые результаты
- 3. Оценка расчетных характеристик нагружения
- 4. Установление влияния износа резцов на машину
- 4.1 Установление влияния износа резцов на производительность проходческого комбайна
- 4.2 Установление влияния износа резцов на ресурс элементов трансмисии
- 5. Разработка модели оптимизации схемы набора резцов по критерию их износа
- Выводы
- Список источников
Введение
Проходческие комбайны (ПК) предназначены для проведения подготовительных горных выработок [7]. Их применение позволяет механизировать основные процессы проходческого цикла – разрушение горной породы, ее удаление из забоя выработки и погрузку на транспортные средства.
К ПК предъявляется ряд общих требований, основными из которых являются:
- Высокие значения основных макроуровневых параметров, интегрально характеризующих их уровень качества и степень конкурентоспособности при представительных горнотехнических условиях эксплуатации: максимально возможных теоретической и технической производительностей; 80%-го ресурса до капитального ремонта.
- Достаточно полный охват вероятных областей использования: по размерам и формам выработок разного назначения (штреки, ходки и т. д.) при минимальном переборе породы; по крепости и абразивности разрушаемых горных пород.
- Достаточно низкие удельные энергозатраты при выполнении рабочих операций.
- Эргономическое удобство управления, высокая безопасность и требуемые санитарно-гигиенические условия при работе обслуживающего персонала.
1. Актуальность темы
Эффективность угольных шахт, напрямую зависит от уровня механизации и автоматизации ведения горных работ. Одно из направлений для снижения себестоимости полезного ископаемого, является концентрация горных работ. Достижение данного требования, возможно лишь при использовании современных технологий, при условии того, что они используют максимально возможный потенциал техники за счет адаптации ее под горно-технико-геологическим условиям шахты.
Комбайновый метод проведения горных выработок, является наиболее эффективным, и по сравнению с другими имеет свои преимущества. Например, сравнивая с буровзрывным способом ведения горных выработок, комбайновый обеспечивает требуемый контур выработки без дополнительных операций, также целостность пород кровли, следовательно, обеспечивает их устойчивость.
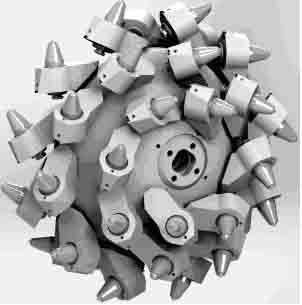
Рисунок 1 – Структурная модель аксиальной коронки
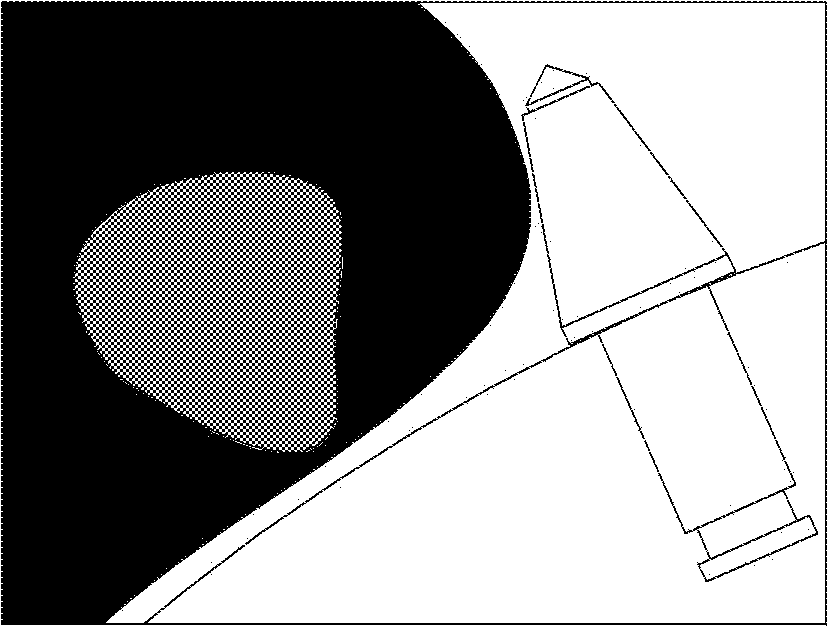
Рисунок 2 – Разрушение резцом горной массы
(анимация: 10 кадров, 10 циклов повторения, 144 килобайт)
Проходческие комбайны оснащаются продольно или (рис. 1) поперечно-осевыми коронками, куда, в резцедержатели устанавливают режущий инструмент (резцы). Учитывая то, что новые, мехатронные механизированные комплексы способны [5] обеспечить добычу угля до 6 тыс. т. в сутки, следовательно, темпы проходки вспомогательных выработок должен быть существенно выше – этого можно достигнуть, путем полного, эффективного использования потенциала проходческой техники.
Во время работы проходческого комбайна в забое, а именно, разрушение горного массива (рис. 2) – весь процесс непрерывно сопровождается износом, за счет истирания резца об породу, а в некоторых случае и полном, мгновенном выходе резца из строя, что характерно при попадании в зону резания твердых включений. Все перечисленное ведет к повышению удельных энергозатрат, большим динамическим нагрузкам (ударам), что ведет к снижению теоретической производительности машины, следовательно, повышается длительность разрушения объема горной массы, что ведет к повышению циклов нагружения – это все ведет к снижению ресурса всей машины в целом и отклонению показателей технического уровня от нормативных показателей.
2. Цель и задачи исследования, планируемые результаты
Целью исследования является оптимизация параметров исполнительного органа проходческого комбайна, для уменьшения износа режущего инструмента.
Основные задачи исследования:
- Разработать программу для оценки ресурса элементов проходческого комбайна методом
дождя
. Экспериментальные данные были получены с использованием математической модели разработанной на кафедре горные машины; - Установить влияние износа резцов на производительность проходческого комбайна;
- Установить влияние износа резцов на ресурс элементов трансмиссии;
- Разработать модель оптимизации схемы набора резцов по критерию их износа.
Объект исследования: рабочие процессы исполнительного органа проходческого комбайна.
Предмет исследования: параметры исполнительного органа, обеспечивающие уменьшение удельных энергозатрат и повышение ресурса режущего инструмента.
В рамках магистерской работы планируется получения параметров для конструирования исполнительного органа, который будет обеспечивать уменьшенный износ режущего инструмента на основе оптимального многокритериального проектирования.
3. Оценка расчетных характеристик нагружения
Характер изменения нагрузок во времени можно [1] разделить на регулярные и нерегулярные.
Регулярные нагружения по ГОСТ 23207–78 называют нагружение, характеризующееся периодическим законом изменения нагрузок с одним максимумом в течении одного периода при постоянстве параметров цикла напряжений в [6] течении всего времени испытаний или эксплуатации. Все виды нагружений, которые не удовлетворяют это определение, называют нерегулярными. К ним относят бигармоническое, полигармоническое, блочное и случайное нагружения.
В большинстве случаев на практике имеет место случайный характер изменения напряжений во времени. В нашем случае, мы имеем широкопрофильные процессы нагружений во времени (рис. 3).
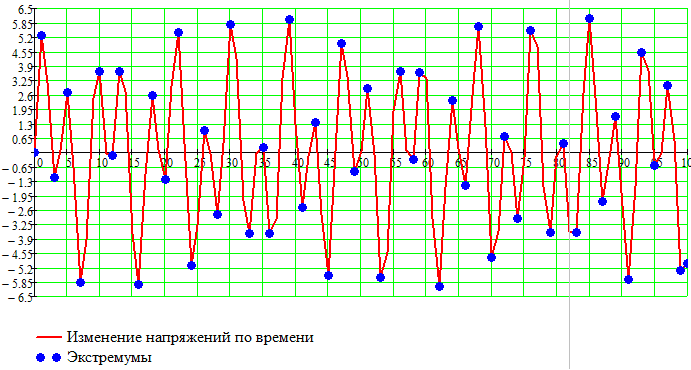
Рисунок 3 – Диаграмма широкополосного процесса напряжения
В случае широкополосного процесса (рис. 3) к выделению амплитуд напряжений, оказывающих основное влияние на накопление усталостных повреждений, можно подходить по разному. Схематизация случайных процессов, целью которых является получение функции распределения амплитуд напряжений, эквивалентной данному случайному процессу по степени вносимого усталостного повреждения. Для широкополосных процессов результаты могут не совпадать, иногда эти различия очень существенны. Принято считать, что наиболее приемлемые результаты для оценки долговечности дает метод полных циклов.
Широкое распространение получил метод, именуемый метод дождя
ГОСТ 25.101–83 [2]. Данный метод приводит к практически таким же результатам что и метод полных циклов, но он более удобен для программирования его на ЭВМ. Смысл цикла таков, [2] что ось времени направлена вертикально вниз. Пусть линии, соединяющие соседние экстремумы это последовательность крыш, по которым стекают потоки дождя. Номерам максимумов соответствуют нечетные числа, номера минимумов четные. Траектории потоков определяют в соответствии со следующими правилами:
- Потоки начинаются с внутренней стороны экстремумов последовательно. Каждый поток определяет полуцикл нагружения. Величину размах определяют проекцией траектории потока на ось нагрузки.
- Поток, начавшийся в точке максимума, прерывается в тот момент, когда встретится больший максимум, больший, чем исходный.
- Поток начавшийся в точке минимума, прерывается, когда встретится минимум меньший, чем исходный.
- При встрече на одной из крыш нескольких потоков движение продолжает тот, который берет начало в экстремуме с меньшим номером, а остальные прерываются.
- Поток, не встретивший препятствий, падает на землю.
Метод «дождя» позволяет ввести схематизацию в режиме реального времени. При этом запоминают лишь траектории потоков дождя и обработку производят по мере ввода экстремумов.
На основе вышеизложенного была [3] составлена блок-схема метода (рис. 4)
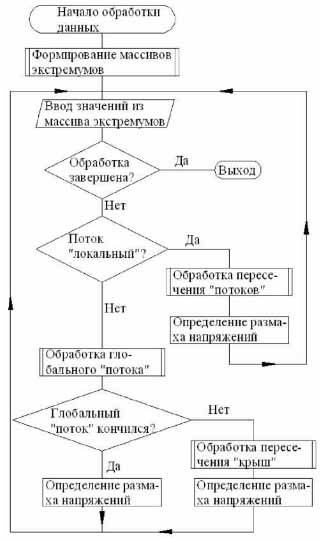
Рисунок 3 – Общий алгоритм метода дождя
С использованием алгоритма и составленной блок-схемы, а также используем разработанную кафедре горные машины математическую модель для определения циклограммы нагружения зададим цикл (рис. 4) для определения потоков сбегающих каплей из крыш
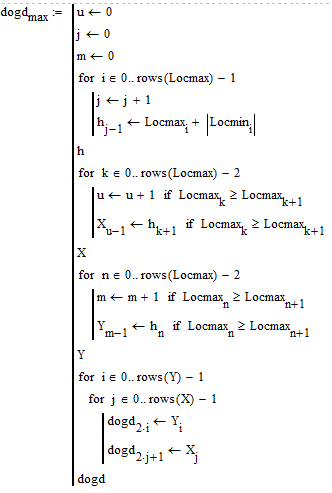
Рисунок 4 – Цикл метода дождя
4. Влияния износа резцов на процесс фрезерования
4.1 Установление влияния износа резцов на производительность проходческого комбайна
В соответствии с поставленной целью техническое состояние комбайна определялось степенями затупления резцов исполнительного органа. Известно, что в различных режимах разрушения забоя на резцах поперечно-осевой коронки формируется существенно различное параметры среза. В результате объемы породы, разрушаемые отдельными резцами, могут существенно отличатся.
Цикл обработки забоя включает различные режимы, что необходимо учитывать при анализе износа резцов на показатели рабочего процесса комбайна. Средневзвешенная доля отделяемой от массива породы, приходящаяся на i-тую линию резания, с учетом удельного веса режимов бкового и вертикального резов в цикле обработки забоя определяется по формуле:
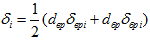
где: dвр dбр – удельный вес соответственно режимов бокового и вертикального резов в цикле обработки забоя;
δврi δбрi – доли отделяемой от массива породы, приходящиеся на i-тую линию резания соответственно в режимах бокового и вертикального резов. Здесь:
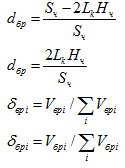
где: Hч – высота выработки в проходке;
Lk – длина коронки;
Vбрi Vврi – объем отделяемой от массы породы соответственно в режимах бокового и вертикального резов, приходящиеся на на i-тую линию резания.
На основании вычисленного эксперимента, следует рассмотреть следующие состояния резцов коронки:
- Все резцы острые, что соответствуют началу работы комбайн после замены всех резцов. Это состояние следует принять как базовое для сравнительной оценки;
- Резцы затуплены пропорционально средневзвешенными долями отделяемой от массива породы за цикл обработки забоя (
пропорциональный износ
); - Резцы затуплены одинаково (
равномерный износ
). При этом также принимаются различные суммарные объемы породы, разрушенной исполнительным органом, однако считается, что они делятся между контактирующими резцами в равных долях; - Все резцы на коронках острые, кроме установленных в одной из линий резаний. При этом затупление этих резцов соответствует случаю равномерного износа всех резцов коронки при достижении заданной величины объема разрушенной породы.
Таким образом, план вычислительного эксперимента можно представить в виде таблицы 1.
Таблица 1 – План вычислительного эксперимента
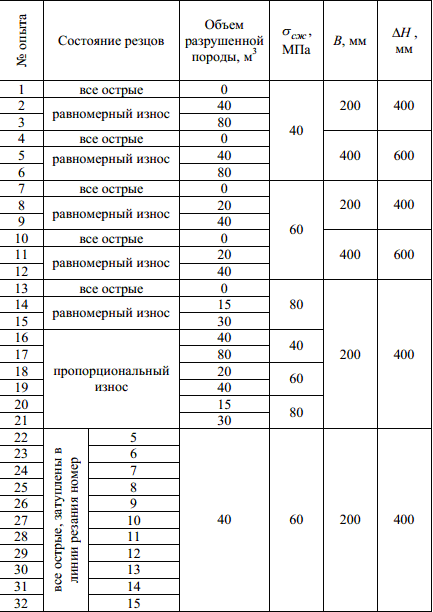
Эксперимент реализовывался как полнофакторный с перебором всех сочетаний факторов. Регистрируемыми параметрами являлись момент в трансмиссии и мощность приводного двигателя.
Анализ таблицы 1 показал, что практически во всех опытах вычислительного эксперимента удалось обеспечить режимы работы привода резания с полным использованием установленной мощности. С ростом объема разрушенной породы, удельные энергозатраты существенно возрастают&ndashдля рассмотренных диапазонов значение разрушенного объема примерно в 2 раза.
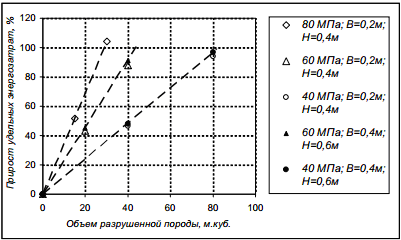
Рисунок 5 – Прирост средних за цикл обработки забоя удельных энергозатрат при равномерном износе резцов
На рисунке приведены графики изменения относительного прироста средних за цикл обработки забоя удельных энергозатрат при равномерном износе резцов от объема разрушенной породы при различных временных сопротивлениях одноосному сжатию и режимных параметрах. Анализ графиков позволил установить:
- Зависимость прироста удельных энергозатрат от объема разрушенной породы за средний цикл обработки забоя, имеет линейный вид;
- Абсолютное значение удельных энергозатрат зависит от глубины зарубки и шага фрезерования коронки, в то время как прирост удельных энергозатрат не зависит от указанных режимных параметров.
Влияние износа отдельных резцов на общие удельные энергозатраты неодинаково. На рисунке 6 приведена диаграмма относительного изменения средних за цикл разрушения забоя удельных энергозатрат при работе с одним затуплены резцом.
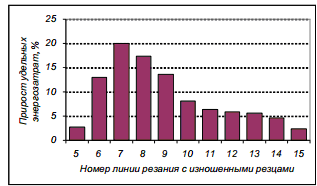
Рисунок 6 – Диаграмма относительного изменения средних за цикл разрушения забоя удельных энергозатрат при работе с одним затуплены резцом
Для оценки влияния различных видов состояния коронки по износу резцов – с равномерным или пропорциональным износом – на энергоемкость разрушения забоя на рисунке 7 построены графики относительного прироста средних за цикл удельных энергозатрат от объема разрушенной породы при различных ее крепостях.
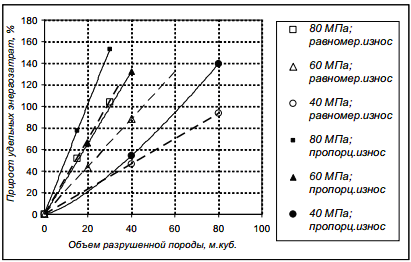
Рисунок 7 – Прирост средних за цикл обработки забоя удельных энергозатрат при равномерном и пропорциональном износе резцов
Анализ приведенных графиков позволяет сделать вывод, что по мере разрушения забоя из-за затупления резцов теоретическая производительность падает по гиперболическому закону. Для обеспечения производительности комбайна на высоком уровне необходима достаточно частая замена режущего инструмента.
4.2 Установление влияния износа резцов на ресурс элементов трансмисии
На рисунке 8 построены графики [4] прироста накопленной за цикл обработки забоя повреждаемости в элементах трансмиссии исполнительного органа от объема разрушенной породы при различных прочностях породы и режимных параметрах. Графики построены для показателя степени кривой усталости 3 (рис. 8, а) и 6 (рис. 8, б) при условии равномерного износа резцов. В качестве базового значения накопленной повреждаемости принимались соответствующие значения при работе с острыми резцами. Анализ полученых зависимостей показал, что при равномерном износе резцов:
- Накопленная повреждаемость за цикл обработки забоя линейно возрастает с увеличением объема разрушенной породы. Эта закономерность имеет место при работе с полным использованием усталостной мощности приводного двигателя;
- Глубина зарубки коронок в массив и шаг фрезерования влияют на прирост накопленной за цикл обработки забоя повреждаемости в элементах трансмиссии.
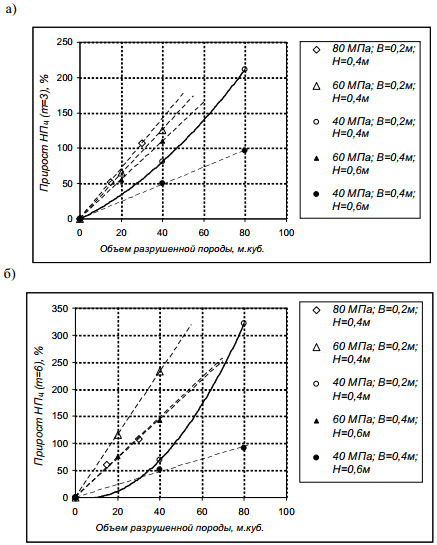
Рисунок 8 – Прирост средних за цикл обработки забоя удельных энергозатрат при равномерном (a) и пропорциональном (б) износе резцов
Для оценки принимаем относительный ресурс, который считаем по формуле:
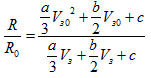
где: R0 – ресурс элемента трансмиссии, соответствующий базовой периодичности замены;
Vз – периодичность замены режущего инструмента.
С использованием выше приведенной зависимости были построены графики относительного ресурса от периодичности замены режущего инструмента для случая равномерного износа резцов.
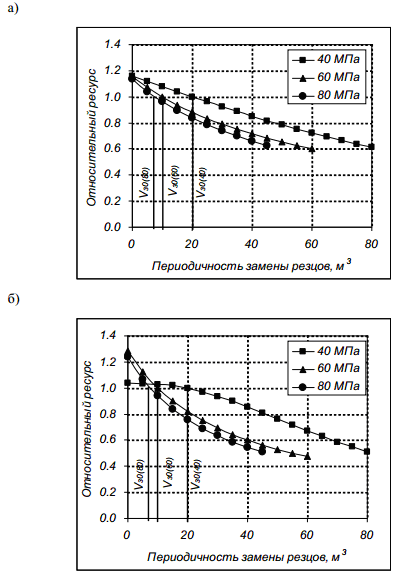
Рисунок 9 – Зависимость относительного ресурса от периодичности замены режущего инструмента для элементов трансмиссии
Графики построены для различных временных сопротивлений одноостному сжатию пород.
Таким образом, износ режущего инструмента существенно влияет на ресурс элементов трансмиссии привода резания, что требует учета при обосновании стратегии замены изношенных резцов ввиду возможности более частных ремонтных работ, что обусловит снижение темпов проведения выработок.
5. Разработка модели оптимизации схемы набора резцов по критерию их износа
Задача оптимизации в [4] общем виде может быть сформулирована следующем образом: найти оптимальное значение переменных проектирования, при которых целевая функция качества достигает наилучшего показателя при использовании проходческого комбайна в заданной области горно-геологических условий эксплуатации с учетом ограничивающих факторов на возможные значения переменных проектирования.
Основной задачей при разработке математической модели оптимизации является корректное задание целевой функции, которая должна достаточно точно отражать связь переменных проектирования с критериями качества машины. Эти критерии являются противоречивыми, могут быть приведены к единому показателю – месячный темп проходки выработки. Этот показатель учитывает как положительных эффект от роста теоретической производителности машины, так и отрицательное влияние простоем, связанных с текущими и капитальными ремонтами комбайна.
Таким образом, решая задачу оптимизации, выраженную математической моделью, можно получить рациональное значения периодичности замены, предельных удельных энергозатрат за цикл разрушения забоя, при достижении которых необходима замена резцов и количества заменяемых резцов.
Выводы
В магистерской работе представленно решение научно – технического вопроса, имеющего важное народнохозяйстенное значение, заключающийся в оптимизации параметров исполнительного органа проходческого комбайна по критерию износа резца, позволяющее повысить темпы проведения горных выработок и продления ресурса элементов конструкции машины.
Список источников
- Когаев В.П., Махутов Н.А., Гусенков А.П. Расчеты деталей машин и конструкций на прочность и долговечность: Справочник. – М.: «Машиностроение», 1985. – 224 c.
- Межгосударственный стандарт. Расчет и испытание на прочность. Методы схематизации случайных процессов нагружения элементов мшины и конструкций и статического представления результатов. ГОСТ 25.101–83.
- Григорьева Ольга Александровна. Инженерные методы оценки прочности и долговечности якорных связей и райзеров шельфовых сооружений. Диссертация на соискание научной степени кандидата технических наук. Специальность 05. 23. 17 Строительная механика. Санкт-Петербург, 2009.
- Бридун Игорь Игоревич. Обоснование критериев и структуры средств технической диагностики исполнительного органа проходческого комбайна. Диссертация на соискание ученой степени кандидата технических наук. Специальность 05. 05. 06 Горные машины. УКД 622.232.7. Донецк, 2014.
- ДСТУ 3625–97 Комбайны проходческие. Термины и определения.
- Сопротивление усталости. Основные термины, определения и обозначения. ГОСТ 23207–78.
- Горные машины для подземной добычи угля: Учебное пособие для ВУЗов / Горбатов П. А. и др.