Abstract
Maintenance
- Introduction
- 1. The relevance and novelty of the topic
- 2. The purpose and objectives of the study
- 3. Research results
- 3.1. Characteristics of the main conveyor line as the automation object
- 3.2. Review of existing technical solutions in the field of automation of the main conveyor linet
- 3.3. Justification and development of the automated control of main conveyor line
- Findings
- References
Introduction
Mining is one of the most important sectors of our region. Efficiency of coal is largely dependent on the clarity and reliability of the transport silo. In the coal mines for the delivery of minerals from the bottom, as well as its transport conveyors are widely used.
Modern coal mines are characterized by a high concentration of production, using a high-performance, coal technology and sophisticated energy-electromechanical systems. Efficiency of coal is largely dependent on the clarity and reliability of the mine vehicle, so the process requires a large coal transport reliability, efficiency, high efficiency.
1. The relevance and novelty of the topic
Conveyors and conveyor lines – a sophisticated automation objects both from the perspective of management and in terms of operational safety.
The main task of automating conveyor lines is a centralized management process to start and stop, providing automatic protection in order to reduce energy consumption, material consumption and elimination of emergency modes. In addition, the current task becomes automatic temperature control operation of the belt conveyor.
For alert thermal regime of the belt include heating drums, belt and carrying rollers, as well as overheating of the engine conveyors.
The main reasons for the emergence of places of local overheating of the belt conveyor are jamming roller breakage due to roller bearings, excessive friction tape. Therefore, to ensure safe operation of the belt conveyor is necessary to constantly monitor the temperature of the roller, belt fabrics, other mechanisms of the conveyor and the temperature of the surrounding air.
2. The purpose and objectives of the study
As a result of fire belts going up to 30% of fires in mines. Fires due to fire belts, lead to loss of life, extended downtime and material costs.
The study aims to increase the level of safety of operation of coal mine conveyor belt through a system of automated control of heating modes, allowing to minimize the risk of fire elements of the conveyor.
Prevent overheating and consequently fire the tape will reduce the material costs of recovery of the conveyor belt because it is the most expensive element of the conveyor.
3. Research results
3.1. Characteristics of the main conveyor line as the automation object
Automation of conveyor transport equipment provides the means of automatic control and protection of each conveyor and management as separate conveyors, and the entire line.
Under the automated conveyor line refers to this line, which is united by a common conveyor control system that ensures compliance with the required interlocks and protections, as well as the automatic implementation of laws start, stop conveyor line.
The aim is to increase the automation of conveyors of their performance, reliability, security, performance and reducing injuries. The latter is achieved by the introduction of various locks, protection and expansion of information opportunities of automation equipment.
3.2. Review of existing technical solutions in the field of automation of the main conveyor line
For automatic protection against overheating bearings electromechanical equipment and automatic control and regulation of various thermal processes was widespread sensors TDL-2, in which the sensing element is a fusible alloy of Wood [1].
Temperature sensor TDL-2 has a brass tip, Wood's alloy which is soldered pin connected through a spring to the roller. In preparation for the sensor to protect by turning 90° clockwise, roller winding up the spring, and make contacts. When heated to the softening temperature of the tip of the alloy (65–75 °C), the rod is released and the movable portion, turning, opens (or closes) contacts. When the cause of overheating and the cooling of the alloy by turning the sensor is in working condition.
Consider the complex control of conveyors and conveyor lines AUCK-1M (hereinafter machinery AUK-1M) [1–2].
Equipment AUК-1M is designed to monitor and control the operation of fixed line (up to three branches) and half-unbranched lines consisting of tape and scraper conveyors. The number of conveyors in line 10.
AUК-1M equipment performs the following functions:
1) The automatic start sequence conveyors included in a line in the reverse direction of movement of traffic, with the necessary time delay between starts of individual Drive;
2) Start from the control panel or remote push-button station as a whole assembly line and parts thereof;
3) run from the control panel or remote push-button station of the assembly line without shutting down the operating pipelines and supply warning;
4) Local start-up of any drives in the pipeline inspection, repair and testing;
5) control of the set maximum time for each run of the conveyor;
6) automatic shutdown of the conveyor drive in emergency mode and turn off the following pipelines feeding the load on the conveyor surface;
7) the ability to run with the termination of an emergency anywhere in the conveyor line;
8) the ability to work on equipment branched conveyor line.
The whole complex performs 53 functions.
Consider equipment AUK.3.
AUK.3 complex – a new generation of equipment based on microprocessors and provides the following controls:
1) local automated control of conveyor;
2) automated management of the conveyor line;
3) automatic control of the conveyor line, carried out by teams of technology sensors with the necessary protective shutdowns and lockouts;
4) the automatic start sequence conveyors included in a line in a row in the reverse direction of movement of traffic;
5) run part of the conveyor line;
6) Start conveyor assembly line without stopping the conveyor is already working;
7) off of the assembly line;
8) control a single conveyor without control panel.
Functionality of the complex increased by 28 new features compared to the complex AUK.1M.
Automated control system of conveyor lines (SAUKL) is designed to:
– Automated management and control of branched and unbranched conveyor lines consisting of belt conveyors for transporting cargo and transportation of people, with the number of pipelines managed by one set of APU and ALS to 60 units and an unlimited number of routes;
– Local or centralized automated management and control of individual pipelines belonging or not belonging to the conveyor line;
– Remote control and status monitoring accompanying accessories;
– Automatic recording and storage of information on the work of the conveyors and related equipment, controls and settings, the protective shutdown and lockout.
SAUKL equipment designed for use in underground mines, hazardous gas and dust.
To date, the only instrument designed temperature control drive drums AKTL-1 [3].
The equipment is designed to monitor shells nefuterovanogo drive pulley and belt conveyor to protect the tape from a fire in the slips. Monitoring is carried out both during rotation and during standstill of the drum.
In the case of slip conveyor drive drum shell and heat sensor. Upon heating mantle to a temperature of 700 °С conveyor disabled. Re-conveyor can be started only after the temperature of the drum shell for 5–7 °С below the permissible.
This equipment automation and protection of pipelines has several drawbacks:
– The complexity of the design and operation;
– The inability to transfer operational control to another object;
– The inability to harmonize with the equipment assembly lines of automation;
– The inability to control Tension conveyor belt;
– The inability to collect information on the thermal regime of a few lines of conveyors.
Thus, all the above systems and automation means operates the required control and diagnostic functions of temperature rise during operation of the belt conveyor. Most of them are made on the basis of outdated components, which greatly reduces the functionality of the equipment.
For the most complete control you need to use modern means of screening, diagnosis and monitoring of the drive motor, drive pulley, carrying rollers and the conveyor belt.
3.3. Justification and development of the automated control of main conveyor line
By the thermal regime of the conveyor belt are heated drums, ribbons and carrying rollers, and motor heating to a temperature at which it is possible ignition of coal dust or other combustible substances and materials due to the lack of protection on or off, preventing the emergency mode of operation of the conveyor.
The fire can become overheated motor bearings due to lack of lubrication, misalignment of shaft, etc.
Work is always accompanied by his blood pressure by heating, which is caused by processes occurring in it, and energy loss. Standard service life of the motor is determined, ultimately, the permissible temperature of its isolation. In modern engines using multiple classes insulation permissible temperature which is a class A – 105 °C, E – 120 °C, B – 130 °C, F – 155 °C, H – 180 °C, C – over 180 °C. Excessive temperatures lead to premature failure of isolation and significantly shorten its life.
The process of heating the drive drum, tape and distributed physical elements of the belt conveyor (carrying rollers) its mode, and the tension of the incoming branches trailing ribbons, specific load on the tape, the technical condition of carrying rollers and technological parameters of the belt conveyor, such as width tape drive drum diameter and the length of the belt conveyor.
The main influencing parameters – it is mass per unit length of the transported material. Increased loading conveyor belt tension and weakening leads to an increase of the working arc slip, which improves the abrasion tape and can cause slip hazard. This slip increases the temperature in the zone of coupling tape and reel, which reaches 300–350 °C for 15 minutes operation. In the case of operating losses occur slippage energy expended on overcoming the forces of friction, which causes a change of the temperature in the contact zone of the drum – tape.
Consider the process of heating for the friction pair drive pulley – belt
(Figure 1).
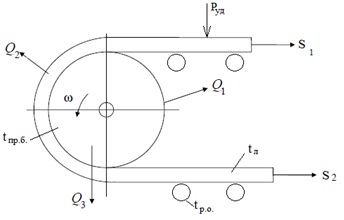
Figure 1 – Block diagram of a pair of drive pulley - belt
Fig. 1 shows: S1 and S2 – tension of the incoming branches and trailing ribbons; Q1 – amount of heat removed by radiation; Q2 – the amount of heat removed by natural convection; Q3 – the amount of heat removed by forced convection, tpr.b – the temperature of the drive drum; tr.o – temperature roller carriages; tl – temperature tape; Pyd – specific load on the tape.
Efficient temperature control modes belt conveyor can be provided with a system of automated control of technical means of selection of information, the following basic functions:
– Monitoring the actual temperature of the environment at the site of installation of the conveyor along its length with the possibility of collecting, processing and storing the received information;
– Control of temperature rise at its points of possible upgrade, for example, conveyor rollers, the motor of the drum, with the feeding of the local light signal of an excess temperature signal link;
– Control of average temperature and rate of change along the conveyor sections with signal transmission via the communication of the place of a possible accident;
– Control of belt tension force and the specific load on it.
For the most complete thermal model works conveyor belt must be direct or indirect method to control all influencing parameters. The direct (contact) control methods include measuring tape tension branches, the specific load on the tape, measure the temperature of the bearing units of the motor stator, the temperature of the drive drum. Indirect (contactless) methods include measuring the temperature of heating tape and carrying rollers.
To control the heating belt and roller carriages along the entire length of the conveyor, as well as fire prevention tape applied linear temperature detectors (heat cable) PHSC, manufactured by Protectowire (USA) [8].
Linear Heat Detector PHSC is a unique heat detector in the form of a cable, which allows you to identify the source of heat anywhere along its length.
The temperature of the drive drum of the conveyor belt is measured thermal resistance included in the bridge circuit.
Specific load on the tape is determined by weighing conveyor company SBS, allows you to automatically calibrate tape monitor deviations and weighing no load on the tape to detect the material remaining on the tape to record the passage of time, the percentage of blank tape for the selected period of time. Intelligent digital sensor unit load SFT in protection IP 65 does not require calibration and provides very high resolution (1:1,000,000).
The tension laden branches tape measure piezoresistive transducer mounted on the tensioning station.
Temperature monitoring of the motor bearing units is carried out by means of temperature controller.
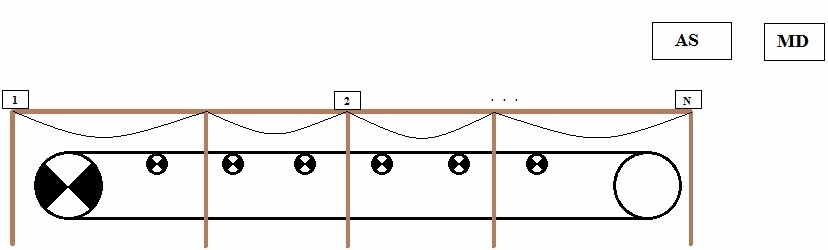
Figure 2 – Diagnostics heating roller carriages (animation: 11 frames, 5 cycles, the interval of 700 ms, 129 kb)
Figure 4 are listed: 1, 2 ... N – Interfaces heat cable, AS – Automation System, MD – manager of the mine.
Findings
The problem of excess temperature control heating elements mine belt along its length is rather complicated, it is associated with a significant length of the line of control, which can exceed 2 km. In addition, affected by heavy duty mine equipment: vibration, coal dust, the possibility of a sharp rise in temperature, and others.
The application of the system enables effective and timely monitoring of thermal modes of mine conveyor belt, prevents the development of emergency situations to minimize the cost of repair and restoration of the tape and, therefore, impermissible reduces downtime and increases its longevity.
In writing this essay master's qualification work is not completed. Date of final completion – January 2016. Full text of work and materials on a work theme can be received from the author or his supervisor after that date.
References
- Груба В. И., Никулин Э. К., Оголобченко А. С. Технические средства автоматизации в горной промышленности. – К.: ИСМО, 1998. – 373 с.
- Справочник по автоматизации шахтного конвейерного транспорта / Н. И. Стадник, В. Г. Ильюшенко, С. И. Егоров и др. – К.: Техника, 1992. – 438с.
- Автоматизация подземных горных работ/ Под ред. проф. А. А. Иванова. – К.: Вища школа, 1987. – 328с.
- Требования к автоматизации шахтных конвейеров и конвейерных линий. – М.: Недра, 1981. – 25 с.
- Автоматизация производства на угольных шахтах / Г. И. Бедняк, В. А. Ульшин, В. П. Довженко и др. – К.: Техника, 1989. – 272с.
- Гаврилов П. Д., Гимельштейн Л. Я., Медведев А. Е. Автоматизация производственных процессов. Учебник для вузов. М.: Недра, 1985, 215 с.
- Д. В. Хананов, А. Я. Грудачев. Аналіз процесів нагріву конвеєрної стрічки при повній пробуксовці приводного барабана шахтного конвеєра в аварійному режимі роботи. Наукові праці Донецького національного технічного університету. Донецьк: ДВНЗ „ДонНТУ“, 2009. – С. 256–265. – (Сер.Гірничо-електромеханічна; Вип.17(157)
- Линейный тепловой извещатель PHSC (термокабель). Режим доступа: http://www.phsc.ru/
- Венгеров И. Р. Теплофизика шахт и рудников. Математические модели. – Монография в 2-х том. том 1 – Донецк: Норд-Пресс, 2008. – 632с.
- Правила безопасности в угольных и сланцевых шахтах. Г.: «Недра», 1986. – 432с.
- Шахмейстер Л. Г., Дмитриев В. Г. Теория и расчет ленточных конвейеров – 2-е изд., перераб. и доп. – М.: Машиностроение, 1987. – 336 с.