Реферат за темою випускної роботи
Зміст
- Вступ
- 1. Актуальність і новизна теми
- 2. Мета і задачі дослідження
- 3. Результати досліджень
- 3.1 Характеристика магістральної конвеєрної лінії як об’єкта автоматизації
- 3.2 Огляд існуючих технічних рішень в області автоматизації магістральної конвеєрної лінії
- 3.3 Обгрунтування та розробка системи автоматизованого контролю магістральної конвеєрної лінії
- Висновки
- Перелік посилань
Вступ
Гірнича промисловість є однією з найважливіших галузей нашого регіону. Ефективність вуглевидобутку в значній мірі залежить від чіткості і надійності роботи шахтного транспорту. У вугільних шахтах і рудниках для доставки корисної копалини із забою, а також її транспортування широко застосовуються стрічкові конвеєри.
Технологічний процес транспортування вантажів і матеріалів є одним з найважливіших у функціонуванні вугільної шахти.
Сучасні вугільні шахти характеризуються високою концентрацією виробництва, використанням високопродуктивної вугільної техніки і складних енергоємних електромеханічних систем. Ефективність вуглевидобутку в значній мірі залежить від чіткості і надійності роботи шахтного транспорту, тому процес транспортування вугілля вимагає великої надійності, ефективності, високого ККД.
1. Актуальність і новизна теми
Стрічкові конвеєри і конвеєрні лінії – це складні об’єкти автоматизації як з позиції управління ними, так і з точки зору забезпечення безпеки експлуатації.
Основною метою автоматизації конвеєрних ліній є централізоване управління процесом пуску і зупинки, забезпечення автоматичних захистів з метою зменшення енерговитрат, витрати матеріалів і виключення аварійних режимів роботи. Крім того, актуальним стає використання автоматичного контролю температурних режимів роботи стрічкового конвеєра.
До аварійних теплових режимів роботи стрічкового конвеєра відноситься нагрів барабанів, стрічки та роликоопор, а також перегрів двигуна конвеєра.
Основними причинами появи місць локального перегріву стрічкового конвеєра є заклинювання ролика внаслідок поломки підшипників ролика, надмірне тертя стрічки. Тому для забезпечення безпечної роботи стрічкового конвеєра необхідно постійно контролювати температуру роликів, стрічкового полотна, інших механізмів конвеєра і температуру навколишнього повітря.
2. Мета і задачі дослідження
Внаслідок загоряння стрічок відбувається до 30% пожеж на шахтах. Пожежі, пов’язані із загорянням стрічок, призводять до загибелі людей, тривалих простоїв і матеріальних витрат.
Метою дослідження є підвищення рівня безпеки експлуатації шахтного стрічкового конвеєра шляхом створення системи автоматизованого контролю теплових режимів роботи, що дозволяє мінімізувати ризик загоряння елементів конвеєра.
Запобігання перегріву, і, як наслідок, загоряння стрічки допоможе зменшити матеріальні витрати на відновлення конвеєрної стрічки, оскільки вона є найдорожчим елементом конвеєра.
3. Результати досліджень
3.1 Характеристика магістральної конвеєрної лінії як об’єкта автоматизації
Підземний транспорт – найбільш складна складова частина транспорту підприємства. Він містить три основних транспортних комплексу: дільничний, магістральний і комплекс околоствольного двору. Дільничний транспорт об’єднує засоби та спеціальне обладнання, призначене для переміщення вантажів від очисних і підготовчих забоїв до основних магістральних виробок (основного горизонту), а також у зворотному напрямку – різних допоміжних матеріалів, обладнання і в обох напрямках – людей. Магістральний транспорт обслуговує всі вантажопотоки по магістральних виробках і пов’язує дільничний комплекс з комплексом околоствольного двору. Транспортний комплекс околоствольного двору призначений для прийому і відправлення всіх вантажів, що надходять в шахту і з неї.
Поширеність стрічкових конвеєрів на виробництві обумовлена їх перевагами: високою продуктивністю, простотою конструкції, невеликою витратою енергії, надійністю, можливістю транспортування вантажу на великі відстані з великою швидкістю і т.п.
Автоматизація конвеєрного транспорту передбачає оснащення засобами автоматичного контролю та захисту кожного конвеєра і управління як окремими конвеєрами, так і всією лінією.
Під автоматизованою конвеєрною лінією розуміється така лінія, конвеєри якої об’єднані загальною системою управління, що забезпечує дотримання необхідних блокувань і захистів, а також автоматичну реалізацію законів пуску, зупинки і дозапуска конвеєрної лінії.
Основними факторами, що впливають на процес автоматизації конвеєрних ліній є: різноманітність технологічних схем конвеєрних ліній по конфігурації, довжині, числу конвеєрів і відгалужень; різнотипність конвеєрів за їх технологічним призначенням, продуктивності, конструктивним виконанням, довжині і динамічним характеристикам; різнотипність приводів конвеєрів по числу і типу двигунів і т.д.
Системи автоматизації конвеєрних ліній з урахуванням сучасного рівня вдосконалення конвеєрів повинні володіти функціональними можливостями, що забезпечують:
– управління конвеєрною лінією з пульта управління;
– автоматичний пуск конвеєрів в лінії в напрямку проти вантажопотоку за допомогою пускового пристрою;
– автоматичну подачу звукового попереджувального сигналу перед пуском конвеєрної лінії;
– можливість дозапуска частини конвеєрної лінії при інших працюючих конвеєрах;
– автоматичний контроль швидкості руху стрічки конвеєра;
– включення на пуск кожного наступного конвеєра тільки після досягнення попереднім конвеєром заданої швидкості;
– оперативне відключення всієї конвеєрної лінії з пункту управління;
– екстрене припинення пуску і екстрену зупинку будь-якого конвеєра з будь-якої точки по його довжині;
– автоматичне аварійне відключення конвеєра при наступних порушеннях: відсутності сигналу про досягнення заданої швидкості при пуску, зниженні швидкості під час роботи несучого полотна або тягового ланцюга до 75% номінальної при несправності приводу конвеєра, неприпустимому перегріві приводних барабанів, масла в турбомуфті; сходу стрічки в сторону; завалі місць перевантаження і несправності ланцюгів управління і контролю:
– можливість накладення гальм при оперативному та аварійному відключенні стрічкових конвеєрів тільки при швидкості стрічки менше 0,5 м/с;
– для конвеєрів з автоматичною натяжною станцією при зниженні швидкості стрічки до 75% номінальної включення натяжної станції на збільшення натягу стрічки;
– сигналізацію на пульті управління про число конвеєрів, що працюють в лінії, маршруті;
– сигналізацію на блоках управління про несправний стан і причини несправності конвеєра;
– інформацію про стан конвеєрної лінії в систему оперативного диспетчерського контролю та управління шахти.
Метою автоматизації конвеєрів є підвищення їх продуктивності, надійності, безпеки праці та зниження травматизму. Останнє досягається за рахунок введення різних блокувань, захистів і розширення інформаційних можливостей апаратури автоматизації.
3.2 Огляд існуючих технічних рішень в області автоматизації магістральної конвеєрної лінії
Наразі майже всі конвеєрні лінії на шахтах автоматизовані. Розвиток автоматизації шахтних конвеєрних ліній протягом тривалого періоду визначався необхідністю зниження трудомісткості управління та підвищення безпеки експлуатації конвеєрного транспорту. У зв’язку з цим широке поширення набуло автоматизоване управління конвеєрною лінією, технічна сутність якого полягає в централізації управління процесами пуску-зупинки конвеєрів, а також у забезпеченні автоматичного захисту при виникненні аварійних ситуацій.
Для автоматичного захисту від перегріву підшипників електромеханічного обладнання, а також автоматичного контролю та регулювання різних теплових процесів великого поширення набули датчики ТДЛ-2, в яких чутливим елементом є легкоплавкий сплав Вуда [1].
Термодатчик ТДЛ-2 має латунний наконечник, в який сплавом Вуда упаяний стрижень, з’єднаний через пружину з валиком. Таке з’єднання, що заміняє храповий механізм, забезпечує відносний поворот стержня і валика тільки в напрямку розвороту витків пружини, нижній кінець якої через втулку сполучений з валиком, а верхній – закріплений в корпусі датчика.
При підготовці датчика до захисту поворотом ручки на 90° за годинниковою стрілкою, валиком заводиться пружина і замикаються контакти. При нагріванні наконечника до температури розм’якшення сплаву (65–75 °С) стрижень звільняється, і рухома частина, розвертаючись, розмикає (або замикає) контакти. Після усунення причини перегріву і охолодження сплаву поворотом ручки датчик приводиться в робочий стан.
У гірській промисловості існує досить велика кількість способів автоматизації конвеєрів і конвеєрних ліній. Основними системами автоматизації стрічкових конвеєрів і конвеєрних ліній являються АУК-1М, АУК.3 САУКЛ, УКІ та інші.
Розглянемо комплекс управління конвеєрами і конвеєрними лініями АУК-1М (далі апаратура АУК-1М [1–2].
Апаратура АУК-1М призначена для контролю та управління роботою стаціонарних ліній (до трьох відгалужень) і напівстаціонарних нерозгалужених ліній з стрічкових і скребкових конвеєрів. Число конвеєрів в лінії до 10.
Апаратура АУК-1М виконує такі основні функції:
1) послідовний автоматичний пуск конвеєрів, включених в лінію в порядку, зворотному напрямку руху вантажопотоку, з необхідною витримкою часу між пусками окремих приводів;
2) пуск з пульта управління або з виносного кнопкового поста як всієї конвеєрної лінії так і його частини;
3) запуск з пульта управління або з виносного кнопкового поста частини конвеєрної лінії без відключення працюючих конвеєрів і з подачею попереджувальної сигналізації;
4) місцевий пуск будь-якого приводу конвеєра при оглядах, ремонтах та випробуванні;
5) контроль заданого максимального часу запуску кожного конвеєра;
6) автоматичне відключення приводу конвеєра при аварійних режимах і відключення наступних конвеєрів, що подають вантаж на поверхневий конвеєр;
7) можливість екстреного припинення запуску з будь-якої точки конвеєрної лінії;
8) можливість роботи апаратури на розгалуженій конвеєрної лінії.
У цілому комплекс виконує 53 функції, а також забезпечує виконання наступних блокувань:
1) виключає пуск конвеєра при несправності ланцюгів управління звукової сигналізації;
2) забезпечує пуск наступного конвеєра лінії тільки після встановлення робочої швидкості руху несучого органу попереднього конвеєра;
3) забезпечує відключення всіх конвеєрів, що транспортують вантаж на зупинений конвеєр;
4) унеможливлює автоматизований запуск конвеєра, переведеного на ремонтно-оцінний режим;
5) унеможливлює включення конвеєра в ремонтно-налагоджувальних режимі при фіксації елементів пуску;
6) унеможливлює повторний запуск конвеєра при аварійному відключенні засобами контролю руху його несучого органу, а також пуск конвеєра в разі його заштибовки.
Поряд із зазначеними функціями апаратура АУК-1М має цілий ряд різних захистів, сигналізацію та телефонний зв’язок.
Структурна схема апаратури АУК-1М приведено рисунку 1.
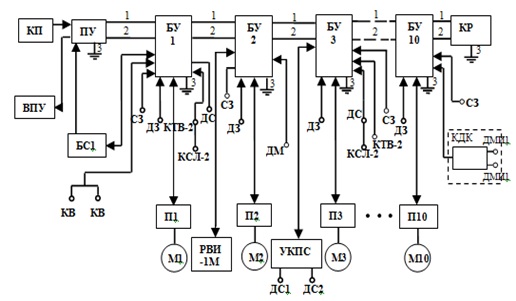
Рисунок 1 – Структурна схема апаратури АУК-1М
До складу апаратури АУК-1М входять:
– Пульт управління ПУ;
– Виносний прилад-покажчик ВПУ;
– Блоки управління БУ (за кількістю конвеєрів в лінії);
– Блок кінцевого реле БКР;
– Датчики швидкості ДС типу УПДС або ДКС, ДМ-2 або ДМ-2М;
– Датчики контролю сходу стрічки типу КСЛ-2;
– Кабель-тросові вимикачі типу КТВ-2;
– Датчики заштибовки ДЗ;
– Телефонні трубки;
– Сирени типу ВСС-3М або гудки типу ГПРВ-2М.
Дана апаратура широко використовується на шахтах, задовольняє всім вимогам, що пред'являються до локальних засобів автоматизації конвеєрних ліній, але не контролює температурні режими роботи конвеєрних ліній.
Розглянемо апаратуру АУК.3.
Комплекс АУК.3 – апаратура нового покоління на базі мікропроцесорів і забезпечує наступні види управління:
1) місцеве автоматизоване управління конвеєром;
2) централізоване автоматизоване управління конвеєрною лінією;
3) автоматичне керування конвеєрною лінією, здійснюване за командами технологічних датчиків з дотриманням необхідних захисних відключень і блокувань;
4) автоматичний послідовний запуск конвеєрів, включених в лінію в порядку, зворотному напрямку руху вантажопотоку;
5) запуск частині конвеєрної лінії;
6) пуск конвеєрів конвеєрної лінії без зупинки вже працюючих конвеєрів;
7) відключення частини конвеєрної лінії;
8) управління одиночним конвеєром без застосування пульта керування.
Комплекс АУК-3 забезпечує наступні захисту та блокування:
1) контроль запуску конвеєра за часом;
2) контроль цілісності лінії попереджувальної сигналізації;
3) контроль зниження швидкості руху стрічки конвеєра нижче допустимої величини;
4) контроль перевищення швидкості руху стрічки конвеєра вище допустимої величини;
5) контроль пробуксовки стрічки по приводного барабана;
6) контроль зниження швидкості приводного барабана нижче допустимої величини;
7) контроль зниження швидкості стрічки для накладання гальм;
8) відключення конвеєра з будь-якої точки по його довжині;
9) контроль сходу стрічки конвеєра в сторону.
Комплекс АУК-3 забезпечує наступну інформацію та зв’язок:
1) номер відключеного (аварійного) конвеєра;
2) кількість працюючих конвеєрів у лінії;
3) причина аварійного відключення конвеєра (диференційована);
4) зупинка конвеєрної лінії у зв’язку з відключенням технологічного ланцюга, що знаходиться попереду.
Функціональні можливості комплексу збільшено на 28 нових функцій у порівнянні з комплексом АУК.1М.
Наступна апаратура – САУКЛ [1–3].
Система автоматизованого управління конвеєрними лініями (САУКЛ) призначена для:
– централізованого автоматизованого управління і контролю роботи розгалуженими і нерозгалужених конвеєрними лініями, що складаються з стрічкових конвеєрів, призначених для транспортування вантажу і перевезення людей, з числом конвеєрів керованих через один комплект АПУ і АЛС до 60 одиниць і необмеженим числом маршрутів;
– централізованого або місцевого автоматизованого управління і контролю роботи окремими конвеєрами, що входять або не входять до складу конвеєрної лінії;
– телеуправління і контролю стану супутнім допоміжним обладнанням;
– автоматичної реєстрації і зберігання інформації про роботу конвеєрів і супутнього устаткування, командах управління та настройках, захисних відключеннях і блокуваннях.
Апаратура САУКЛ розрахована на застосування в підземних виробках шахт, небезпечних по газу і пилу.
Структурно система САУКЛ складається з комплекту пульта управління, який розташовується в диспетчерській шахти і комплектів апаратних засобів, що встановлюються на конвеєрах.
Іскробезпека в САУКЛ забезпечується гальванічною розв'язкою електричних ланцюгів пульта управління, лінії зв’язку, лінії телефону, лінії модулів лінійних, лінії взаємоблокування, ланцюга живлення датчика електродного і ланцюгів живлення електронних схем, а також застосуванням схем, що забезпечують обмеження потужності можливої іскри за рахунок обмеження струму короткого замикання.
Телефонний зв’язок здійснюється по двухпроводной лінії і забезпечує телефонний симплексний канал між пультом управління і блоками управління конвеєрами.
Реалізація функцій САУКЛ здійснюється за допомогою програм, які знаходяться в ПУ і в кожному БУК.
Структурна схема апаратури САУКЛ приведена на рисунку 2.
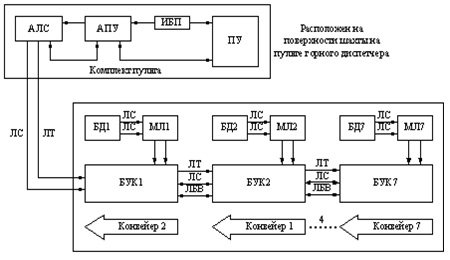
Рисунок 2 – Структурна схема апаратури САУКЛ
На сьогоднішній день розроблена єдина апаратура контролю температури приводних барабанів АКТЛ-1 [3]. Апаратура призначена для контролю обечайки нефутерованого приводного барабана стрічкового конвеєра і для захисту стрічки від загоряння при пробуксовці. Контроль здійснюється як в процесі обертання так і при нерухомому стані барабана.
До складу апаратури АКТЛ-1 входять стабілізоване джерело живлення, високочастотний генератор сигналів, термодатчик, вузол прийому–передачі сигналів і блок сигналізації. Термодатчик ТД-1 являє собою порожню сталеву шпильку, всередині якої розташований термочутливий елемент, виконаний у вигляді котушки індуктивності з феритовим сердечником. Термодатчик герметизується епоксидним компаундом і вбудовується в обечайку барабана. Принцип датчика заснований на використанні ефекту різкого зменшення магнітної проникності при нагріванні його до певної температури.
У разі пробуксовки конвеєра обечайка приводного барабана і термодатчик нагріваються. При нагріванні обечайки до температури 700 °С конвеєр відключається. Повторно конвеєр можна запустити тільки після зниження температури обечайки барабана на 5–7 °С нижче допустимої.
Дана апаратура автоматизації та захисту конвеєрів має низку недоліків:
– складність конструкції і принципу дії;
– неможливість оперативного перенесення на інший об’єкт контролю;
– неможливість узгодження з апаратурою автоматизації конвеєрних ліній;
– неможливість управління натяжна станцією стрічкового конвеєра;
– неможливість збору інформації про тепловий режим від декількох конвеєрів лінії.
Таким чином, всі перераховані вище системи та засоби автоматизації не виконують необхідних функцій контролю та діагностики наростання температури при роботі стрічкового конвеєра. Більшість з них виконана на застарілій елементній базі, що значно скорочує функціональні можливості апаратури.
Для найбільш повного контролю необхідно використовувати сучасні засоби відбору, діагностики та моніторингу стану приводного двигуна, приводного барабана, роликоопор і стрічки конвеєра.
3.3 Обгрунтування та розробка системи автоматизованого контролю магістральної конвеєрної лінії
До теплових режимам роботи стрічкового конвеєра відносяться нагрів барабанів, стрічки та роликоопор, а також нагрів двигуна до температури, при якій можливе займання вугільного пилу або інших горючих речовин і матеріалів через відсутність або відключення захистів, що запобігають аварійний режим роботи конвеєра.
Причиною пожежі може стати перегрів підшипників двигуна через недостатньої смазки, перекосів валу і т.д.
Основною характеристикою навантажувальних режимів є теплова характеристика електродвигуна. Робота АД завжди супроводжується його нагріванням, що обумовлено відбуваються у ньому процесами і втратами енергії. Нормативний термін служби електродвигуна визначається, в кінцевому рахунку, допустимою температурою нагріву його ізоляції. У сучасних двигунах застосовується кілька класів ізоляції, допустима температура нагріву яких становить для класу А – 105 °С, Е – 120 °С, В – 130 °С, F – 155 °C, H – 180 °C, С понад 180 °С. Перевищення допустимої температури веде до передчасного руйнування ізоляції і істотного скорочення терміну його служби.
Процес нагріву приводного барабана, стрічки і розподілених фізичних елементів стрічкового конвеєра (роликоопор) визначається режимом його роботи, натягом набігаючої і збігаючої гілок стрічки, питомим навантаженням на стрічку, технічним станом роликоопор (заштибовка), а також технологічними параметрами стрічкового конвеєра, такими як: ширина стрічки, діаметр приводного барабана і довжина стрічкового конвеєра.
Основний впливаючий параметр – це погонна маса матеріалу, що транспортується. Підвищення завантаження конвеєра і ослаблений натяг стрічки призводять до збільшення дуги робочого проковзування, що підвищує стирання стрічки і може викликати аварійну пробуксовку. У разі пробуксовки зростає температура в зоні зчеплення стрічки і барабана, яка досягає 300–350 °С за 15 хв його роботи. У разі робочого проковзування відбуваються втрати енергії, що витрачаються на подолання сил тертя, частина яких викликає зміну температури в зоні контакту барабан – стрічка.
Розглянемо процес нагріву для фрикційної пари приводний барабан – стрічка
(рис.3).
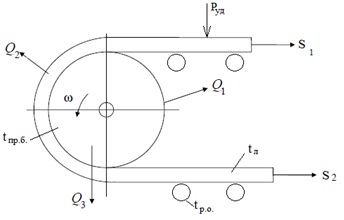
Рисунок 3 – Структурна схема пари приводний барабан – стрічка
На рис. 3 приведено: S1 і S2 – натяг набігаючої і збігаючої гілок стрічки; Q1 – кількість тепла, відведена випромінюванням; Q2 – кількість тепла, відведена природною конвекцією; Q3 – кількість тепла, відведена вимушеною конвекцією, tпр.б – температура приводного барабана; tр.о – температура роликоопор; Tл – температура стрічки; Руд – питоме навантаження на стрічку.
Рівняння теплового балансу процесу нагрівання приводного барабана і стрічки має вигляд [7]:

де Qутв – кількість тепла, утворена під час роботи конвеєра, ккал/год;
Qнб – кількість тепла, що витрачається на нагрів барабана і стрічки, ккал;
Q1 – кількість тепла, відведена випромінюванням, ккал/год;
Q2 – кількість тепла, відведена природною конвекцією, ккал/год;
Q3 – кількість тепла, відведена вимушеної конвекцією, ккал/год;
T – час роботи конвеєра.
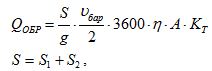
де S – сумарне натягнення гілок стрічки;
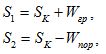
де Wгр и Wпор – опори руху стрічки відповідно на навантаженій і порожній гілках.
Аналіз рівняння теплового балансу і діаграми натягу показує, що тепловий режим роботи стрічкового конвеєра визначається питомим навантаженням на стрічку, а також зусиллями натягу завантаженої і порожньої гілок.
Ефективний температурний контроль режимів роботи стрічкового конвеєра може бути забезпечений системою автоматизованого контролю з технічними засобами відбору інформації, які виконують такі основні функції:
– забезпечення контролю фактичної температури навколишнього середовища в місці установки конвеєра по всій його довжині з можливістю збору, обробки та зберігання отриманої інформації;
– контроль перевищення температури в точках її можливого підвищення, наприклад, у роликів конвеєра, електродвигуна, барабана, з подачею місцевого світлового сигналу про місце перевищення температури, сигналу по лінії зв’язку;
– контроль середньої температури і швидкості її зміни уздовж ділянок конвеєра з передачею сигналу по лінії зв’язку про місце можливої аварії;
– забезпечення контролю зусилля натягу стрічки і питомого навантаження на ній.
Для отримання найбільш повної теплової моделі роботи стрічкового конвеєра необхідно прямим або непрямим методом контролювати всі впливаючі параметри. До прямих (контактних) методів контролю відноситься вимір натягу гілок стрічки, питомого навантаження на стрічку, вимірювання температури підшипникових вузлів статора двигуна, температури приводного барабана. До непрямих (безконтактних) методів належать вимір температури нагріву стрічки і роликоопор.
Для контролю нагрівання стрічки і роликоопор по всій довжині конвеєра, а також попередження спалаху стрічки застосовується лінійний температурний сповіщувач (термокабель) PHSC, виробництва компанії Protectowire (США) [8].
Лінійний тепловий сповіщувач PHSC являє собою унікальний тепловий детектор у вигляді кабелю, який дозволяє виявити джерело перегріву в будь-якому місці по всій його довжині.
Термокабель PHSC TRI-Wire генерує окремі сигнали спрацьовування («Предтревога») і пожежної тривоги в залежності від встановлених температурних порогів захисту.
Температура приводного барабана стрічкового конвеєра вимірюється термоопором, включеним в мостову схему.
Питоме навантаження на стрічку визначається конвеєрними вагами фірми SBS, що дозволяють автоматично тарувати стрічку, здійснювати моніторинг відхилень зважування та відсутність вантажу на стрічці, виявляти матеріал, що залишається на стрічці, фіксувати відсоток часу проходження порожньої стрічки за вибраний період часу. Інтелектуальний цифровий датчик питомого навантаження SFT в конструктивному виконанні IP 65 не вимагає тарировки і забезпечує дуже високий дозвіл (1:1'000'000).
Натяг навантаженої гілки стрічки вимірюється тензорезистивним перетворювачем, встановленим на натяжній станції.
Контроль температури підшипникових вузлів двигуна здійснюється за допомогою термоконтроллера.
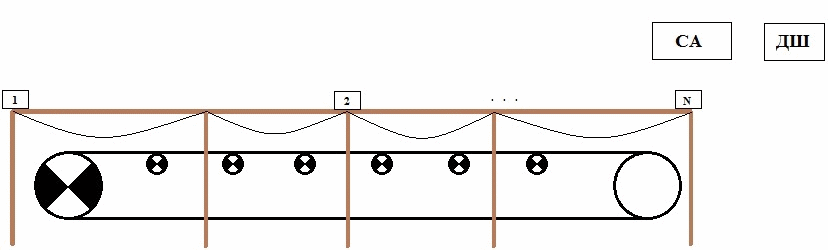
Рисунок 4 – Діагностика нагріву роликоопор (анімація: 11 кадрів, 5 циклів, інтервал 700 мс, 129 кб)
На рис. 4 зазначені: 1, 2 ... N – інтерфейсні модулі термокабеля, СА – система автоматизації, ДШ – диспетчер шахти.
Висновки
Проблема контролю над перевищенням температури нагрівання елементів шахтного стрічкового конвеєра по його довжині є досить складною, вона пов’язана зі значною протяжністю лінії контролю, яка може перевищувати 2 кілометри. Крім того, позначаються важкі умови експлуатації шахтного устаткування: вібрація, вугільний пил, можливість різкого підвищення температури тощо.
Застосування розробленої системи дозволяє здійснювати ефективний і своєчасний контроль теплових режимів роботи шахтного стрічкового конвеєра, попереджає розвиток аварійних ситуацій, мінімізує витрати на ремонт і відновлення стрічки і, як наслідок, скорочує неприпустимі простої обладнання, а також підвищує його довговічність.
При написанні даного реферату кваліфікаційна робота магістра не завершена. Дата остаточного завершення роботи – січень 2016 року. Повний текст роботи та матеріали по темі роботи можуть бути отримані у автора або його наукового керівника після зазначеної дати.
Перелік посилань
- Груба В. И., Никулин Э. К., Оголобченко А. С. Технические средства автоматизации в горной промышленности. – К.: ИСМО, 1998. – 373 с.
- Справочник по автоматизации шахтного конвейерного транспорта / Н. И. Стадник, В. Г. Ильюшенко, С. И. Егоров и др. – К.: Техника, 1992. – 438с.
- Автоматизация подземных горных работ/ Под ред. проф. А. А. Иванова. – К.: Вища школа, 1987. – 328с.
- Требования к автоматизации шахтных конвейеров и конвейерных линий. – М.: Недра, 1981. – 25 с.
- Автоматизация производства на угольных шахтах / Г. И. Бедняк, В. А. Ульшин, В. П. Довженко и др. – К.: Техника, 1989. – 272с.
- Гаврилов П. Д., Гимельштейн Л. Я., Медведев А. Е. Автоматизация производственных процессов. Учебник для вузов. М.: Недра, 1985, 215 с.
- Д. В. Хананов, А. Я. Грудачев. Аналіз процесів нагріву конвеєрної стрічки при повній пробуксовці приводного барабана шахтного конвеєра в аварійному режимі роботи. Наукові праці Донецького національного технічного університету. Донецьк: ДВНЗ „ДонНТУ“, 2009. – С. 256–265. – (Сер.Гірничо-електромеханічна; Вип.17(157)
- Линейный тепловой извещатель PHSC (термокабель). Режим доступа: http://www.phsc.ru/
- Венгеров И. Р. Теплофизика шахт и рудников. Математические модели. – Монография в 2-х том. том 1 – Донецк: Норд-Пресс, 2008. – 632с.
- Правила безопасности в угольных и сланцевых шахтах. Г.: «Недра», 1986. – 432с.
- Шахмейстер Л. Г., Дмитриев В. Г. Теория и расчет ленточных конвейеров – 2-е изд., перераб. и доп. – М.: Машиностроение, 1987. – 336 с.