Abstract
- Introduction
- 1. Power generation and secondary resources nonferrous metals
- 1.1 Otrymannya ferrous metals
- 1.2 Klasyfikatsiya waste
- 2. Services shaft furnace
- 3. Melting midevmisnyh waste in reflective furnace
- 4. Melting midevmysnyh waste in electric furnaces
- 4.1 Induktsiyni channel furnace
- 4.2 Conversion of black copper
- 4.3 Fire refining of converter coppe
- 4.4 Melting svyntsevovmysnyh waste in boilers
- 4.5 Units furnace for melting aluminum scrap and waste
- 4.6 Fire oven chops
- 4.7 Drum oven, rotating
- 5. Kanalna induction furnace
- 5.1 Induction Melting furnace
- 5.2 Arc electric furnace
- 5.3 Arc electric furnace
- 5.4 Medium frequency induction furnace
- Conclusions
- References
Introduction
The main purpose of secondary nonferrous metallurgy is to provide gathering, harvesting, primary processing, production of alloys and semi-finished products using scrap and waste ferrous metals. Nowadays harvested scrap and waste of almost all ferrous metals. Given the limited reserves of ore deposits and rich, scrap and wastes are becoming increasingly important in meeting the needs of the economy in aluminum, copper, lead, zinc and precious metals. The most important species with economic importance, belongs to metal and metal-recycled waste includes all the production and processing of metals and various hardware retiring from the field of industrial and household consumption. Waste generated in the first and second metallurgical, in foundries and used directly relate to working waste. Metallurgy Nonferrous secondary metal - extremely difficult in the organizational sense of industrial production. This is due primarily to the fact that scrap and waste ferrous metals and alloys produced in any and all areas of consumption. Based on this, all businesses and organizations in some way involved in the production of secondary metals production structure can be divided into four main groups: 1) enterprises and organizations - lomosdatchyky; 2) production and procurement management without metal production; 3) production associations and industrial and procurement management of metallurgical production; 4) smelters that process recycled materials.
Groups and brands determine the chemical composition of materials. For each class is set to 10 or more groups. The first group includes pure metals, the second and subsequent - alloys to the last - unsorted (mixed) waste and scrap. Grade secondary raw material is primarily determined by the degree of pollution. It also takes into account the size of the individual components of scrap and waste. By first grade include recycled materials (other than Class M), the quality of which can be characterized accompanying passport, stating the name of raw materials, class and group (brand) Party. Class II - scrap and waste consisting of alloys of one brand or group, but with more debris than the 1st grade. Third grade - scrap and waste supplied by groups of alloys with prydelky ferrous metals are more littered than raw 2nd grade. By include scrap and waste that do not meet the requirements for varieties of major groups. Mixed (unsorted) waste and scrap processors accept only by prior arrangement with their suppliers of raw materials. Specificity of secondary raw materials, its diversity, complexity challenges when it many cases leads to complex multi-application technology schemes. A special place in such schemes take fee and initial training of secondary raw materials for steel processing.
1. Power generation and secondary nonferrous metals resources
1.1 Receiving ferrous metals
The metal ore and metal waste has chemical and physical differences. However, energy costs for metal from ore much larger (sometimes an order of magnitude) than the receipt of the waste metal. For Ukraine method for non-ferrous metals from scrap and waste their production began after 1991 is extremely important. This is due to the fact that Ukraine has no prey industrial ores aluminum, copper, zinc, lead and a number of other non-ferrous metals. At present, non-ferrous metals from ore own base in Ukraine produced just titanium, mercury, zirconium, silicon, hafnium and uranium.
In view of the data can draw some conclusions: • a major source of aluminum, lead, zinc and copper raw materials to rynku.Ukrayiny will scrape and wastes; • Scrap and wastes economically feasible to recycle large specialized companies that possess advanced technology and equipment for processing, sorting, treatment and recycling.
1.2 Classification of waste
A large number and variety of waste recycling technologies as secondary raw materials dictate the need for a clear classification, GOST 3211-95 (GOST 1639-93). Classification of scrap and waste ferrous metals - the division of scrap and waste by type, physical characteristics, chemical composition and debris. Waste nonferrous metals and alloys are divided into classes, groups and varieties. Class - classification division unit that determines scrap and waste products of nonferrous metals and alloys on the physical characteristics (scrap, sawdust, slag, etc.). Group - a unit classification division that defines a set of brands nonferrous metals and alloys, combined with the mechanical and (or) to close the technological properties and chemical composition (pure aluminum, aluminum casting alloys, aluminum alloys deformed, etc .). Quality - a unit classification division that characterizes scrap and waste ferrous metals and alloys by type, grade and size.
Scrap metal, wastes are classified by type of metal: • Copper and copper alloys; • aluminum and aluminum alloys; • tungsten, volframovmisni chemical compounds, alloys of tungsten; • cadmium; cobalt and its compounds and alloys; • Magnesium and magnesium alloys; • molybdenum, molibdenovmisni chemical compounds and alloys; • nickel and nickel alloys; • tin and tin-lead alloys; • mercury and its compounds; • Lead and lead alloys; • titanium and titanium alloys; • zinc and zinc alloys; • Scrap complex; • Domestic scrap.
2. Services shaft furnace
Charge for the shaft furnace is prepared to charge the yard and delivered to the flue area in trolleys with a body that is upset. Each vahonettsi usually placed one component of a mixture. If the skip loading the truck unloaded directly into the bucket Luchina.
In addition to proper selection of the charge and its load, fuel for normal operation of the furnace necessary to ensure uniform and sufficient flow of air to the furnace. Typically, air is supplied under pressure from 0.04 to 0.10 kg / cm2 (400 ... 1000 mm of water. In.) Air is blown into the furnace through the lance fitted to furmenyh openings cooled water caissons. The diameter of the lances depends on their number required for the shaft furnace of air pressure and blast resistance to the passage of air through the pillar mine shaft furnace.
After the metal rises to the level of the slag notch, begins production of the metal in the ladle furnace. Buckets made of cast steel. Inside buckets lined with fireclay brick or silica. Before the release of heated metal lined bucket. The capacity of the bucket should ensure release it just metal formed by melting of a trouser-leg (usually 8 ... 10 tons). After the release of metal give it a little stand, and then use the bridge crane carefully poured into slag, which hit the bucket, the mold set in shlakorozlyvniy car or "slag field." Only then molten metal is poured into the converter for further processing. The duration of release of the metal is several minutes. The metal is produced at blast off..
slag notch caulk and crowbar lay clay. Workers serving the furnace should:
- provide timely and correct batch loading and fuel;
- watch as lance and blowing characteristics (pressure and quantity of supplied air), the temperature of the water emerging from the caissons, which should not be above 70...80 °C;
- provide timely release of metal and slag notch in order to maintain and monitor the storage space of the furnace, the temperature, the quantity and quality (composition) product melting height of rash as top of the furnace, to achieve reduction in air leak through the windows boot - on time close them quickly upload simultaneously open only one window and the like.
Mining midevmisnoho melting scrap and waste in the imaginary, is actually a complex process, one that requires a lot of experience and attention in its implementation. Small deviations from the regime cause complications and problems in the furnace and often displays her down. The main problem in the shaft furnace occur primarily because of the large number of zinc in the charge, and the higher the content, the more likely manifestations of complications.
3. Melting copper-bearing waste in reflective furnaces
Reflecting smelting of secondary nonferrous metallurgy used to get in reflective furnaces from scrap and waste preparatory and vintage alloys. These furnaces smelted more than half of secondary nonferrous metals. Capacity reflective furnaces that are dependent on the homogeneity of the mixture, which supplied chemical composition and from 5 to 100 t. Copper in reverberatory furnaces melted bronze. In the domestic secondary non-ferrous metals and tin bronze melted bezolov'yani mainly reflecting a single-chamber furnaces with a capacity of 15 ... 45 tons. By design chops oven divided into two-chamber and single chamber..
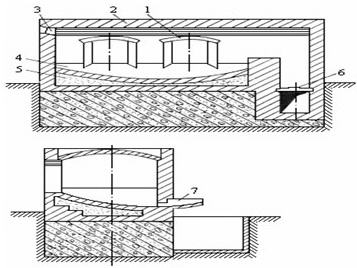
1 - window; 2 - arch furnace; 3 - slot burner; 4 - camera; 5 - denis; 6 - fought; 7 - notch
Figure 1 – Scheme reflectivity single-furnace
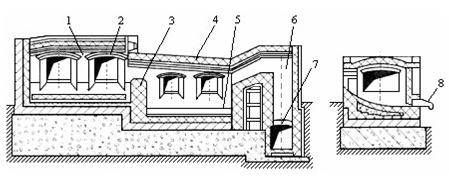
1 - melting chamber; 2 - Load window; 3 - the threshold; 4 - set; 5- kopylnyk; 6 - apteyk; 7 - fought; 8 - notch
Figure 2 – Two-chamber furnace chop
4. Melting copper-bearing waste in electric furnaces
To prepare the alloys in the secondary color metallurgist with used fuel and electric furnaces, induction channel and crucible and furnace resistance. Melting metal in electric furnaces compared with obtaining alloys in reverberatory furnaces has some peculiarities. Due to the active mixing in electrodynamic induction furnace charge is melted under a layer of melt, which ensures minimal oxidation of the metal at a relatively small pool surface, protected oxide film. Induction melting provides great performance and high quality metal and uniform chemical composition and temperature throughout the bath, a sharp reduction in the volume and concentration of pollutants in the gases released, small metal discard. In addition, ease of maintenance, the possibility of complex automation of the process in the operation of electric furnaces combined with good hygienic conditions
4.1 Induktsiyni channel furnace
The basic building block is the induction channel furnace unit that is a closed channel formed lining. In the domestic secondary non-ferrous metals have been used induction channel furnace (ICP) with vertical channels one-, two- and three-phase performance, providing one-way movement of metal (OPM)p>
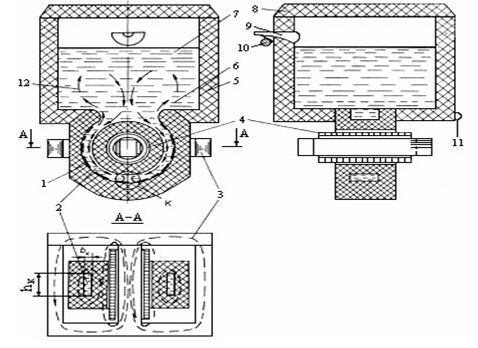
1 - stone troughs; 2 - melting channel; 3 - mahnitodroty; 4 - inductor; 5 - bath furnace; 6, 7 - metal levels before and after discharge; 8 - a cover; 9 - drain sock; 10 - axis tilt furnace; 11 - mounts rope tilting furnace; 12 - the direction of motion of liquid metal; K - the zone of maximum temperature metal
Figure 3 - channel induction electric furnace
Conversion of black copper
Black copper is called copper smelted in reverberatory or shaft furnaces. Called blister copper product obtained by blowing black copper converter
This Operation is carried out in the unit entitled converter, hence the process called conversion. The aim is to maximize the conversion of removing zinc, tin, lead and antimony part in the gas phase and driving translation nickel, iron and antimony of the slag so that the copper that remains in the converter after blowing, contain these impurities as possible. However, almost separate from impurities in the copper converter can only partially because:
Mining copper-bearing melting scrap and waste in the imaginary, is actually a complex process, one that requires a lot of experience and attention in its implementation. Small deviations from the regime cause complications and problems in the furnace and often displays her down. The main problem in the shaft furnace occur primarily because of the large number of zinc in the charge, and the higher the content, the more likely manifestations of complications.
• Firstly, zinc, lead, tin, antimony and nickel inevitably remain small amounts of copper in converter;
• Secondly, of copper slag goes into the part with nickel, antimony, zinc, lead and tin, which has to extract these metals again.
Horizontal converter - is a welded steel cylinder with end walls lined bricks (lining thickness of 380...460 mm in furmenoho zone 460...540 mm). At the ends of two steel reinforced cast rims which currency is based on steel rollers. One smooth rims and another with coronary gear. With the crown gears and toothed gear transmission through converter can be rotated around a horizontal axis. Rollers (runners) freely rotate around axes, based on the bearings, which are fastened to the frame, installed on a massive foundation. Brick advisable to put a layer of sheet asbestos and must be between the casing and masonry backfill layer of asbestos. On the ends closed sheet steel casing thickness 15...20 mm.
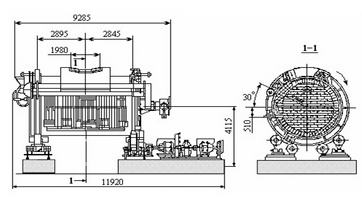
Figure 4 - Horizontal converter capacity of 40 tons
4.3 Fire refining of converter copper
The processes occurring during fire refining copper. Oxidative (fire) copper refining based on the fact that most of the impurities contained in it, mayeyut greater affinity for oxygen than the copper and most oxides formed by oxidation of contaminants insoluble in copper, therefore out of copper with removal in the form of slag. However, the refining of fire can not remove impurities such as noble metals and bismuth, as they have a lower affinity for oxygen than copper, and therefore not okyslyuvatymutsya while in the molten copper.
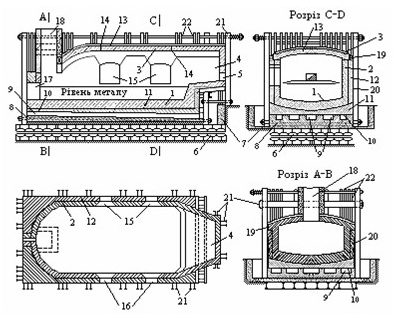
Figure 5 - Inpatient fiery furnace for refining copper
4.4 Melting waste in boilers
Melting metal oxides in boilers due to the economic low melting point and low specific heat of lead. To melting and overheating 1 ton of lead to 400 °C required for the calculation of only 18 thousand. Kcal corresponding to warm 2.6 kg of fuel burned completely to CO2 released. Steel boilers are used for the smelting of lead, allowing short-term overheating to 700...800 °C, but lasted only serve upon heating to a temperature not exceeding 600 °C. Therefore processing in boilers suitable only such scrap, which is melted at a temperature below 600 °C.
4.5 Units furnace for melting scrap and waste aluminum
For the melting of scrap and waste alyuminiyevmisnoho furnace used different designs: fiery chops, mine - Rotating swivel - Rotating electrical induction, as well as combinations of these types. Choosing the furnace due to technical and economic feasibility for melting certain type of raw material. For example, for melting pure waste (cutting, shaving) and scrap iron prypratsyuvan without suitable induction or that rotating furnace crucible. Fire chops melting furnace adapted for bulky scrap with iron pryroblennyamy. When selecting ovens of great importance to capacity oven that must meet production volume, which ensures uninterrupted operation of the unit, as well as ways of heating.
4.6 Fire oven chops
The most widely used universal chops fiery furnace in which melted any raw shavings, trim, airplane and lump scrap of iron prypratsyuvannyamy more. They have high performance and easy to maintain. The metal reflective charge furnaces for smelting secondary aluminum materials diverse and consists of trim, scrap and waste casting and deformed alloys, pellets, chips, slag and wastes of own production of dry crushed chips, training and other alloys. The use of a type of metal smelting in the charge depends on the heating unit mark given alloy.
4.7 Drum oven, rotating
For melting small charge, mainly chips, cutting, etc. milkoshmatkovyh zniman that does not contain iron prypratsyuvan used korotkobarabanni oven, rotating .Pich is lined with steel drum mounted on the supporting rollers, the speed is regulated in the range of 1 ... 8 min-1. Lining stuffed or presented a special shaped bricks. To enhance the stirring effect by rotating furnace cross-section lining made as a polygon. Oven heats gas or fuel oil. Charge charged through the hole in one end of the furnace. Notch located on the side of the drum
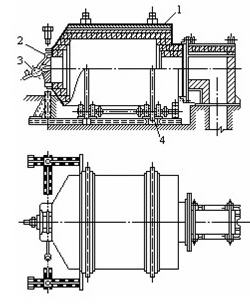
Figure 6-rotary furnace
5. Channel induction furnace
According to the principle of action represents a kind of transformer secondary winding which is U-shaped channel in futerivtsi stone hearth filled with metal. The primary winding - copper tube in a spiral that cools running water. U-shaped channel includes primary winding spiral, spiral inside rizmischuyetsya magnetic wire. AC passing primary winding forms around itself and the secondary winding alternating magnetic field, creating a channel EMF induction. The current that emerged in the channel, heats metal that is in it, and because of its circulation heats all the metal in a furnace.
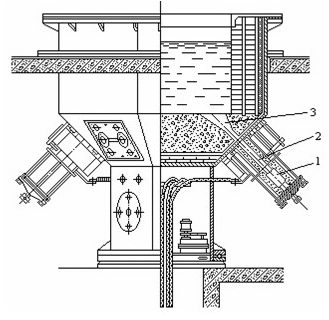
1, 2 - horizontal and vertical channel, respectively; 3 - tub bottom induction unit
Figure 7 - The unit of aluminum channel furnace Aviation Engineering-25K
5.1 Induction Melting furnace
Industrial frequency also work on a transformer. The primary winding is cooled tubular running water inductor surrounding the crucible furnace. Secondary winding - metal in the crucible.
Induction crucible furnace of industrial frequency with the following advantages:
- low loss of metal on fumes;
- high thermal efficiency;
- without melting of flux or its minimum quantity.
The disadvantages are:
- ban on raw materials from iron smelting;
- the need for balance in the crucible (swamp) from the previous metal melting.
5.2 Electric arc furnace
widely adopted in foundries factories mashinostroitelnyh electric arc (three-phase) alternating current for melting iron and steel, as well as stoves mode (mixers). Electro has several advantages: low fumes elements, the possibility of more accurate iron with less co-lichestvom contaminants, high overheat, better sanitary conditions of melting, the possibility of mechanization and Automatics-ization and regulation of the smelting process. Melting could lead to solid and liquid zavalke. Elektroduhovye furnace working with basic and acidic lining. The most frequently used elektroduhovye furnace with acid lining. In these large furnaces stoykost lining, lower costs, lower specific consumption of electricity, electrodes and duration of melting. Furnaces with lining osnov¬noy used for smelting iron alloy with a high content of aluminum (as aluminum vigorously vosstanavlivaet silicon from silicon dioxide and acid destroys the lining of the furnace), manganese and chromium, as well as soderzhaniem low sulfur (to 0.04%). In electric arc furnaces electric arc occurs directly between the electrode and the metal melted charge. Elektricheskiy regime governing the furnace by changing the voltage on the electrode or arc length. Changing the voltage on the electrodes carried by switching transformer degrees. Oven is powered by three-phase network power frequency voltage 6...35 kV. To reduce power losses furnace transformer ustanavlivayut most close to the furnace. The main units of three-phase arc furnace AC are: metal frame, tilt mechanism, lining, arch, arch mechanism for moving the electrodes and electrode, electrical, water cooling system and hydraulic system drive mechanism
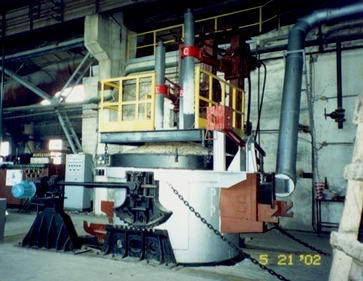
Figure 8 - Arc bake variable conductors model DSP-1,5
5.3 Development of DC arc furnaces
A distinctive feature of DC arc furnaces (DPPT) is the presence of only one of the upper graphite electrode (cathode) located along the vertical axis of the furnace and hearth electrodes (anodes) in the hearth of the furnace.
The global leader in application DPPT belongs to Japan, where for the past eight years, introduced more than 13 kilns, including sverh¬moschnye. Actively developing their application US, South Korea, India and other countries.
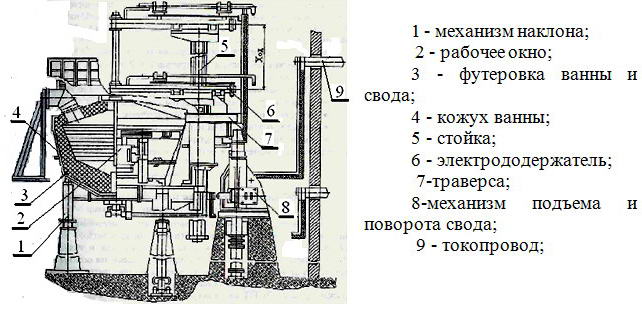
Figure 9- DC arc furnace for melting iron and steel
The basic premise implementation of these furnaces:
• lower consumption of electrodes 1,5 - 2,0 kg / t;
• energy saving 3 - 5%;
• efficient, more even distribution of heat
• reduce the consumption of refractory materials;
• natural mixing of the melt;
• easier care stove;
• reduce the negative impact, to connect the network with less power short circuit.
5.4 Medium frequency induction furnace
The technical and economic advantages of medium frequency induction furnaces (YPSCH) due to the effect of internal heating charge eddy currents. Induction method provides a selection of heat directly to the metal without heat radiation or convection, which is usually accompanied by significant losses. Induction stoves have much greater technological efficiency than devices that operate on fuel. Compared with the induction furnaces of industrial frequency (IPPP) smelting iron at medium frequency has some advantages:
• melting mode (when the "swamp") eliminates a previous drying of the charge and related costs as well as reduce the cost of lining, because its durability in sedimentary regime of melting increases and finally eliminate unproductive spending labor, energy and materials associated with the inability to disable IPPP at the time of interruption
• allowable specific power supplied to the metal, 3 times higher than in the IPPP (in YPSCH - 1000 and IPPP - 300 kWh / t), which provides short cycles of melting (40...45 min), increases Thermotechnical efficiency;
• power consumption less than half of IPPP operating in a continuous loop with partial melting metal drain and periodic dozahruzkoy charge;
• ability to work in active power mode stabilization throughout the cycle of melting, since the "cold" state of charge (active power at medium frequencies transmitted through the ferromagnetic properties of charge) to the molten metal (active power supplied by eddy currents in the narrow layer molten pool, thus enhancing the efficiency of the installed capacity of electric with high quality electricity consumed). Specific energy consumption per ton of iron close to the best performance arc furnaces AC and DC. However, the melting YPSCH without drawbacks inherent in DSP:
• intense dust - and requiring additional costs for purification;
• significant costs graphite electrodes;
• intense impact on the power grid, due to uneven loading in a cycle of melting, the emergence of operational short circuits, low quality electricity consumption, requiring significant expenditure on compensating devices external grid.
The life cycle of any product, machinery, apparatus ends because of their moral or physical deterioration. Scrap (waste consumption), in most cases, is a complex, multi-commodity, the processing of which requires special technological schemes and the appropriate hardware design.
Currently, the main units for smelting aluminum waste is reflective fiery furnace. However, the desire to reduce the loss of metal during melting of the charge developed, contaminated surface (scrap, shavings, slag, etc.) was the main reason for the development of rotary furnaces with horizontal axis of rotation, and subsequently developing rotary kilns with oblique rotation axis, varying capacity in the range of 5...20t. by aluminum.
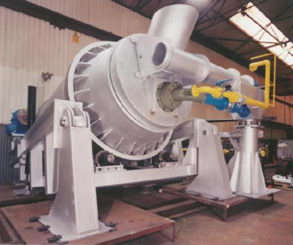
Figure 10 - medium frequency induction furnace
This type of furnace has significant advantages over all types of furnaces is being exploited for melting of non-ferrous metals and especially the melting slag and contaminated waste. Benefits rotary kilns with oblique axis of rotation are as follows:
1. Reducing costs flux (salt) na50%;
2. Increased productivity oven na70%;
3. Increased boot windows;
4. No additional exhaust windows to drain slag.
To accelerate the process of melting and increasing the efficiency of heating furnace units are equipped with devices feeders for feeding crushed scrap into the furnace and devices for filtering molten metal pouring bezokyslytelnoy and lightweight conveyor bars masoyu 4...6kg.
Ardently fixed one or two-chamber furnace with reflective material loading through the side windows boot. In these furnaces can recycle a variety of raw materials, but the melting of the charge developed contaminated surface (slag, chips, small bleeds, etc.) there is a significant vyhar metal. When loading material with a high iron content are cases increase to the latter melt, increasing the duration of the cleaning melting chamber, increasing loss metal from slag.
At the front of the chassis of the furnace exit flue gases (combustion products) hazohid membrane installed for explosion-proof operation of the furnace. For the release of the furnace of molten metal and slag in a cylindrical drum made of two diametrically opposite spaced windows for installation letok that in the process of smelting (drum) closed with a special device.
Conclusions
In all technological processes related to receipt and processing of metals, widely used thermal units - ovens of various type and purpose. USED:
- For technological purpose (production of a material or alloy);
- By type of heat process (melting, heating, drying, ...);
- For mode (continuous running and batch);
- Over temperature in the working space (low to 400...500 °C, for medium to 800...900 °C and high-temperature, over 1000 °C);
- For a source of energy (fuel, electrical, autogenous generation of energy through chemical raw materials) ;
- By way of transportation, loading and unloading material (pushing, roller, broaching, furnace with walking hearth, side-delivery metal, etc.);
The technology used cooking alloys and melting units for each of these production has specific characteristics. The biggest influence on the choice of melting units for individual enterprises provide the following factors: the composition of charge materials, production volume and nomenclature alloys technological limits to waste their own production, as well as the need to ensure technological requirements for quality and profitability semi issued theirproduction, availability of energy sources.
stove analysis units used in present and future equipment shown their advantages and disadvantages in the production: Mine containing copper melting scrap and waste in the imaginary, is actually a complex process, one that requires a lot of experience and attention in its implementation. Small deviations from the regime cause complications and problems in the furnace and often deduce it from ladu.Pry that economic efficiency is minimal or non-existent, as production costs are not offset by a decrease in oxygen costs for coke, and the loss of copper and tin increased.
Induction melting provides great performance and high quality metal and uniform chemical composition and temperature throughout the bath, a sharp reduction in the volume and concentration of pollutants in the gases released, small metal discard. However, the refining of fire can not remove impurities such as noble metals and bismuth, as they have a lower affinity for oxygen than copper, and therefore not okyslyuvatymutsya while in the molten copper.
Steel boilers are used for the smelting of lead, allowing short-term overheating to 700...800 °C, but lasted only serve upon heating to a temperature not exceeding 600 °C.Tomu processing in boilers suitable only such scrap, which is melted at temperatures below 600 °C.
For the melting of scrap and waste aluminum containing furnace used different designs: fiery chops, mine - Rotating swivel - Rotating electrical induction, as well as combinations of these types.
Duction crucible Pec Mahe ban on raw materials from iron smelting and the need for balance in the crucible (swamp) from the previous metal smelting.
Currently, the main units for smelting aluminum wastewis reflective fiery furnace. However, the desire to reduce the loss of metal during melting of the charge developed, contaminated surface (scrap, shavings, slag, etc.) was the main reason for the development of rotary furnaces with horizontal axis of rotation, and subsequently developing rotary furnaces with an inclined axis of rotation.
It should be noted that the rotary kiln type PRNA also widely used as control units for incoming supply of scrap and waste, v. To. High speed melting, mechanization process more fully meet the qualitative and quantitative evaluation of raw materials
References
- Bredikhin, VN, Article: Environmental and Technological Problems Converting aluminum containing waste.
- M.S.Shklyar STOVES vtorychnoy tsvetnoy Metallurgy: M.Metal, 1987, -216s.
- .Bredyhyn VN Maniak MA, Smirnov VA ferrous Metallurgy metallyv (part 7) .Vtorynna Metallurgy kolorovûh metallyyv.
- http://ukrbascompany.at.ua/index/organizacionnye_i_tekhnologicheskie_osobennosti_proizvodstva_aljuminievykh_splavov/0-182.
- http://media.ls.urfu.ru/497/1284/2791/.