Реферат за темою випускної роботи
Зміст
- Вступ
- 1. Джерела утворення і ресурси вторинних кольорових металів
- 1.1 Отримання кольорових металів
- 1.2 Класифікація відходів
- 2. Обслуговування шахтних печей
- 3. Плавка мідевмісних відходів у відбивних печах
- 4. Плавка мідевмисних відходів у електричних печах
- 4.1 Індукційні канальні печі
- 4.2 Конвертація чорної міді
- 4.3 Вогняне рафінування конвертерної міді
- 4.4 Плавка свинцевовмисних відходів в котлах
- 4.5 Пічні агрегати для плавки лому й відходів алюмінію
- 4.6 Вогняні відбивні печі
- 4.7 Барабанні печі, що обертаються
- 5. Канальна індукційна піч
- 5.1 Індукційні тигельні печі
- 5.2 Дугові електричні печі
- 5.3 Розвиток дугових печей постійного струму
- 5.4 Індукційні печі середньої частоти
- Висновки
- Перелік посилань
Вступ
Основне призначення вторинної кольорової металургії полягає в забезпеченні збору, заготівлі, первинної обробки, виробництва сплавів і напівфабрикатів з використанням лому та відходів кольорових металів. В наш час заготовлюються лом і відходи практично всіх кольорових металів. Враховуючи обмеженість запасів рудної сировини й багатих родовищ, лом і відходи кольорових металів набувають все більшого значення в задоволенні потреби народного господарства в алюмінії, міді, свинцю, цинку та дорогоцінних металів. До найбільш важливих видів, що мають народногосподарське значення, належить металева та металовмісна вторинна сировина, що включає всі відходи при виробництві й обробці металу, а також різні металовироби,що вибувають з сфери виробничого та побутового споживання. Відходи, що утворюються на першому та другому металургійних переділах, у ливарному виробництві й використовувані безпосередньо, належать до оборотних відходів. Металургія вторинних кольорових металів - виключно складна в організаційному відношенні галузь промислового виробництва. Це зумовлено насамперед тим, що брухт і відходи кольорових металів і сплавів утворюються в усіх без винятку областях їх споживання. Виходячи з цього всі підприємства та організації тим або іншим способом беруть участь у виробництві вторинних металів за виробничою структурою можна розділити на чотири основні групи: 1) підприємства та організації - ломосдатчики; 2) виробничо-заготівельні управління без металургійного виробництва; 3) виробничі об'єднання та виробничо-заготівельні управління з металургійним виробництвом; 4) металургійні заводи, що переробляють вторинну сировину.
Групи і марки визначають хімічний склад сировини. Для кожного класу встановлено до 10 і більше груп. До першої групи відносять чисті метали, до другої і наступним - їх сплави, до останньої - несортовані (змішані) брухт і відходи. Сортність вторинної сировини в першу чергу визначається ступенем його засміченості. При цьому враховуються також розміри окремих компонентів брухту і відходів. До першого сорту відносять вторинну сировину (крім класу М), якість якого може бути охарактеризоване супровідним паспортом, де вказується найменування сировини, клас і група (марка) партії. Другий сорт - брухт і відходи, що складаються із сплавів однієї марки або групи, але з більшою засміченістю, ніж в 1-му сорті. Третій сорт - брухт і відходи, що поставляються за групами сплавів, мають приделки з чорних металлови характеризуються більшою засміченістю, ніж сировина 2-го сорту. До нивкосортным відносять брухт і відходи, що не відповідають вимогам, що пред'являються до сортів основних груп. Змішаний (несортоване) брухт і відходи переробні підприємства приймають тільки за попереднім погодженням з ними постачальників вторинної сировини. Специфіка вторинної сировини, його різноманіття, комплексність завдань, що стоять при його переработкеуво багатьох випадках зумовлює застосування складних багатостадійних технологічних схем. Особливе місце в таких схемах займають збір і первинна підготовка вторинної сировини до металургійної переробки.
1. Джерела утворення і ресурси вторинних кольорових металів
1.1 Отримання кольорових металів
Метал з руди та метал з відходів не має хімічних і фізичних відмінностей. Проте енергетичні витрати для отримання металу з руди значно більші (іноді на порядок), ніж при отримання металу з відходів. Для України спосіб отримання кольорових металів з лому та відходів їх виробництва став після 1991 р. надзвичайно актуальним. Це пояснюється тим, що в Україні відсутня промислова здобич руд алюмінію, міді, цинку, свинцю й низки інших кольорових металів. На сучасному етапі з кольорових металів з власної рудної бази в Україні виробляються тільки титан, ртуть, цирконій, кремній, гафній і уран.
З урахуванням приведених даних можна зробити певні висновки: • одним з основних джерел алюмінієвої, свинцевої, цинкової та мідної сировини на ринку. України будуть лом і відходи кольорових металів; • лом і відходи кольорових металів економічно доцільно переробляти на крупних спеціалізованих підприємствах, що мають у своєму розпорядженні сучасні технології та устаткування для обробки, сортування, підготовки й переробки вторинної сировини.
1.2 Класифікація відходів
Значна кількість видів відходів і різноманітність технологій їх переробки, як вторинної сировини, диктують необхідність чіткої їх класифікації, ДСТУ 3211-95 (ГОСТ 1639-93). Класифікація лому й відходів кольорових металів – поділ лому й відходів за видами, фізичними ознаками,хімічним складом і засміченістю. Відходи кольорових металів і сплавів ділять на класи, групи і сорти. Клас – одиниця класифікаційного поділу, що визначає лом і відходи кольорових металів і сплавів за фізичними ознаках (лом,ошурки, шлак і т.п.). Група – одиниця класифікаційного поділу, що визначає сукупність марок кольорових металів і сплавів, об’єднаних за механічними та (або) по технологічними властивостями й близькими за хімічним складом (чистий алюміній, алюмінієві ливарні сплави, алюмінієві сплави, що деформуються, і т.п.). Сорт – одиниця класифікаційного поділу, що характеризує лом і відходи кольорових металів і сплавів за видами, засміченістю і розмірами.
Лом і відходи кольорових металів підрозділяються за видами металів: • мідь і мідні сплави; • алюміній і алюмінієві сплави; • вольфрам, вольфрамовмісні хімічні сполуки, сплави вольфраму; • кадмій; кобальт, його сполуки та сплави; • магній і магнієві сплави; • молібден, молібденовмісні хімічні сполуки й сплави; • нікель і нікелеві сплави; • олово та олово-свинцеві сплави; • ртуть та її з’єднання; • свинець і свинцеві сплави; • титан і титанові сплави; • цинк і цинкові сплави; • лом складний; • лом побутовий.
2. Обслуговування шахтних печей
Шихту для шахтної печі готують на шихтовому дворі й доставляють на колошниковий майданчик у вагонетках з кузовом, що перекидається. У кожній вагонетці, як правило, поміщається один якийсь компонент шихти. У разі скіпового завантаження вагонетки вивантажуються безпосередньо у ківш скіпа.
Крім правильного підбору шихти та її завантаження, палива для нормальні роботи печі необхідно також забезпечити рівномірну й достатню подачу в піч повітря. Зазвичай повітря подається під тиском від 0,04 до 0,10 кг/см2 (400...1000 мм вод. ст.) Повітря вдувається в піч через фурми, які встановлюються у фурмених отворах охолоджуваних водою кесонів. Діаметр фурм залежить від їх числа, необхідного для шахтної печі кількості повітря, тиск дуття та опору проходженню повітря через стовп шахти в шахтній печі.
Після того, як метал піднімається до рівня шлакової льотки, починається випуск металу з печі в ківш. Ковші виготовляють литими із сталі. Усередині ковші футерують шамотною або динасовою цеглиною. Перед випуском металлу футерований ківш розігрівають. Ємність ковша повинна забезпечити випуск у нього всього металу, що утворився від плавління однієї колоші (зазвичай 8...10 т). Після випуску металу йому дають небагато відстоятися й потім за допомогою мостового крана обережно зливають шлак, що потрапив у ківш, у виливниці, встановлені на шлакорозливній машині або на «шлакове поле». Тільки після цього розплавлений метал заливають у конвертер для подальшої переробки. Тривалість випуску металу складає декілька хвилин. Метал випускається при вимкненому дутті.
Шлакову льотку затикають ломиком і закладають глиною. Робітники обслуговують печі, повинні:
- забезпечувати своєчасне та правильне завантаження шихти й палива;
- стежити за станом фурм і характеристикою дуття (тиск і кількість подаваного повітря), за температурою води, виникаючої з кесонів, яка не повинна бути вище 70...80 °С;
- своєчасно забезпечувати випуск металу та шлаку, підтримувати в порядку льотки та стежити за збереження об’єму горну, за температурою, кількістю та якістю (складом) продуктів плавління,висотою висипу, станом колошника, добиватися скорочення підсосів повітря через завантажувальні вікна – своєчасно їх закривати,швидко завантажувати, одночасно відкривати тільки одне вікно й тому подібне.
Шахтне плавління мідевмісного лому та відходів при вдаваній, є насправді процессом складним, таким, що вимагає великого досвіду й уваги при його проведення. Невеликі відхилення від режиму викликають ускладнення та неполадки в роботі печі й нерідко виводять її з ладу. Основні неполадки в шахтній печі відбуваються перш за все через наявності великої кількості цинку в шихті, причому чим вищии його вміст, тим більша вірогідність прояву ускладнень.
3. Плавка мідевмісних відходів у відбивних печах
Відбивне плавка у вторинній кольоровій металургії служить для отримання у відбивних печах з лому й відходів підготовчих і марочних сплавів. У цих печах виплавляють більше половини вторинних кольорових металів. Місткість відбивних печей, що діють, залежить від однорідності шихти, яка за хімічним складом постачається і складає від 5 до 100 т. Разом з міддю у відбивних печах плавлять бронзу. У вітчизняній вторинній кольоровій металургії олов’яні й безолов’яні бронзи плавлять переважно в однокамерних відбивних печах місткістю 15...45 т. За конструкцією відбивні печі розділяють на однокамерні й двокамерні.
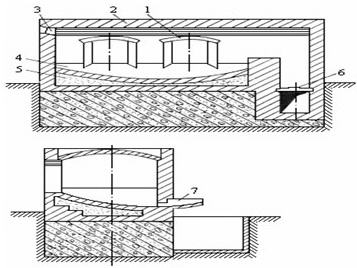
1 –завантажувальне вікно; 2 – звід печі; 3 – гнізда для пальника; 4 –плавильна камера; 5 – подіна; 6 – боров; 7 – льотки
Рисунок 1 – Схема однокамерної відбивної печі
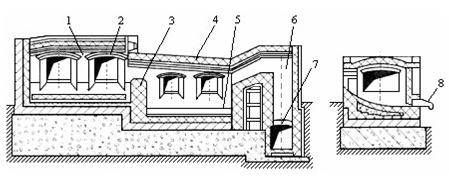
1 – плавильна камера; 2 – завантажувальне вікно; 3 – поріг; 4 – звід; 5- копильник; 6 – аптейк; 7 – боров; 8 – льотки
Рисунок 2 – Двокамерна відбивна піч
4. Плавка мідевмисних відходів у електричних печах
Для приготування сплавів у вторинній кольоровій металургові разом з паливними застосовуються й електричні печі, індукційні канальні та тигельні, а також печі опору. Плавлення металу в електричних печах порівняно з отриманням сплавів у відбивних печах має деякі особливості. Завдяки активному електродинамічному перемішуванню в індукційних печах шихта плавиться під шаром розплаву, що забезпечує мінімальне окислення металу при порівняно невеликій поверхні ванни, захищеною оксидною плівкою. Індукційна плавка забезпечує велику продуктивність і високу якість металу, а також рівномірний хімічний склад і температуру по всій ванні, різке скорочення об’єму та концентрації шкідливих речовин у газах, що виділяються, малі безповоротні втрати металу. Окрім цього, простота обслуговування, можливість комплексної автоматизації технологічного процесу при експлуатації електричних печей поєднуються з хорошими санітарно-гігієнічними умовами праці.
4.1 Індукційні канальні печі
Основним конструктивним елементом канальної печі є індукційна одиниця, що є закритим каналом, утвореним футерівкою. У вітчизняній вторинній кольоровій металургії знайшли застосування індукційні канальні печі (ІКП) з вертикальними каналами одно-, двох- і трифазного виконання, що забезпечують однонаправлений рух металу (ОРМ)
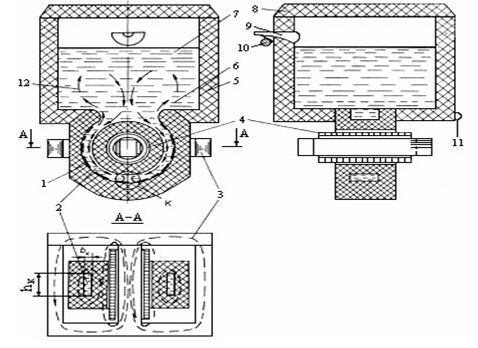
1 – подовий камінь; 2 – плавильний канал; 3 – магнітодроти; 4 – індуктор; 5 – ванна печі; 6, 7 – рівні металу до та після зливу; 8 – кришка; 9 – зливна шкарпетка; 10 – осі нахилу печі; 11 – вузли кріплення тросу для нахилу печі; 12 – напрями руху рідкого металу; К – зона максимальної температури металу
Рисунок 3 – Індукційна канальна електропіч
4.2 Конвертація чорної міді
Чорною міддю називають мідь, виплавлену у відбивних або шахтних печах. Чорновою міддю називається продукт, отриманий в результаті продування чорної міді в конвертері.
Операція ця здійснюється в апараті, що має назву конвертер, звідки й сам процес отримав назву конвертація. Метою конвертації є максимальне видалення цинку, олова, свинцю та частково сурми в газову фазу й переклад ведення нікелю, заліза та частини сурми в шлак з тим, щоб у міді, що залишається в конвертері після продування, містилося цих домішок якомога менше. Проте практично відокремити мідь від домішок у конвертері вдається лише частково, оскільки:
Шахтне плавління мідевмісного лому та відходів при вдаваній, є насправді процессом складним, таким, що вимагає великого досвіду й уваги при його проведення. Невеликі відхилення від режиму викликають ускладнення та неполадки в роботі печі й нерідко виводять її з ладу. Основні неполадки в шахтній печі відбуваються перш за все через наявності великої кількості цинку в шихті, причому чим вищии його вміст, тим більша вірогідність прояву ускладнень.
• по-перше, цинк, свинець, олово, сурма та нікель неминуче залишаються в невеликих кількостях у конвертерній міді;
• по-друге, частина міді переходить у шлак разом з частиною нікелю, сурми, цинку, свинцю та олова, з якого доводиться ці метали витягувати знов.
Горизонтальним конвертером - є сталевий зварний циліндр з торцевими стінками, футерований хромомагнезитовою цеглою (товщина футерівки 380...460 мм, в області фурменого поясу 460...540 мм). На кінцях укріплено два сталеві литі ободи, якими конвертер спирається на сталеві ролики. Один з ободів гладкий, а інший з вінцевою шестернею. За допомогою вінцевої шестерні та зубчатої передачі конвертер через редуктор може повертатися навколо горизонтальної осі. Ролики (бігуни) вільно обертаються навколо осей, що спираються на підшипники, які укріплені на рамі, встановленій на масивному фундаменті. Цеглину бажано класти на шар листового азбесту й обов’язково мати між кожухом і кладкою шар засипки з азбесту. З торців кожух закритий листовою сталлю завтовшки. 15...20 мм.
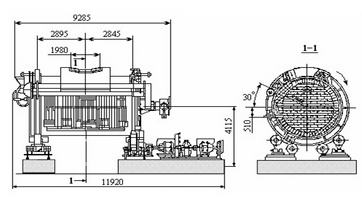
Рисунок 4 – Горизонтальний конвертер місткістю 40 т
4.3 Вогняне рафінування конвертерної міді
Процеси, що протікають при вогняному рафінуванні міді. Окислювальне (вогняне) рафінування міді засноване на тому, що більшість домішок, що містяться в ній, маєють більшу спорідненість до кисню, ніж сама мідь, і більшість оксидів, що утворюються при окисленні домішок, у міді нерозчинні, внаслідок цього виділяються з міді з видаленням у вигляді шлаку. Проте вогняним рафінуванням не можна видалити такі домішки, як благородні метали та вісмут, оскільки вони мають з киснем меншу спорідненість,ніж мідь, і тому не окислюватимуться, знаходячись у розплаві міді.
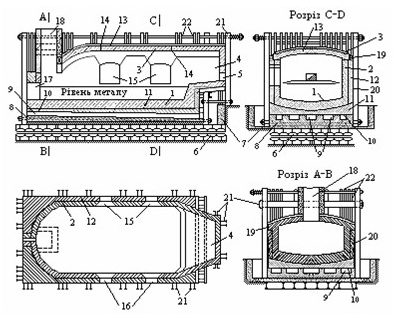
Рисунок 5 – Стаціонарна піч для вогняного рафінування міді
4.4 Плавка свинцевовмисних відходів в котлах
Плавка металевого свинцю в котлах економічна унаслідок низької температури плавлення та низької теплоємності свинцю. Для розплавлення й перегріву 1 т свинцю до 400 °С потрібно за розрахунком лише 18 тис. ккал, що відповідає теплу 2,6 кг умовного палива, що спалюється повністю до СO2, що виділяється. Сталеві котли, які використовуються для виплавки свинцю,допускають короткочасний перегрів до 700...800 °С, але тривало служать лише при нагріві до температури, що не перевищує 600 °С. Тому для переробки у котлах придатний тільки такий лом, який розплавляється при температурі нижче 600 °С.
4.5 Пічні агрегати для плавки лому й відходів алюмінію
Для плавки алюмінієвмісного лому і відходів застосовують печі різноманітних конструкцій: полум’яні відбивні, шахтні – що обертаються, поворотні - що обертаються, електричні індукційні, а також комбінації перерахованих типів. Вибір печі обумовлений технічною та економічною доцільністю для плавки певного виду сировини. Наприклад, для плавки чистих відходів (висікання,стружки) й лому без залізних припрацювань підходять індукційні або такі, що обертаються печі тиглів. Вогняні відбивні печі пристосовані для плавки великогабаритного лому із залізними приробленнями. При виборі печей велике значення має місткість печі, яка повинна відповідати об’ємам виробництва, що гарантує безперебійну роботу агрегату, а також способи нагріву.
4.6 Вогняні відбивні печі
Найбільшого поширення набули універсальні вогняні відбивні печі, у яких плавлять будь-яку сировину:стружку, обріз, літаковий і кусковий лом із залізними припрацюваннями тощо. Вони мають високу продуктивність і прості в обслуговуванні. Металева шихта відбивних печей для плавки вторинної алюмінієвої сировини різноманітна й складається з обрізів, лому й відходів ливарних і деформованих сплавів, брикетів, стружки, шлаків і відходів власного виробництва, сухої роздробленої стружки,підготовчих сплавів і ін. Використання того або іншого виду металевої шихти в плавці залежить від пічного агрегату, заданої марки сплаву.
4.7 Барабанні печі, що обертаються
Для плавки дрібної шихти, головним чином стружки, висікання, мілкошматкових знімань тощо, які не містить залізних припрацювань застосовують короткобарабанні печі, що обертаються. Піч складається із сталевого футерованого барабана, встановленого на опорних роликах, швидкість обертання якого регулюється в діапазоні 1...8 хв. Для посилення перемішуючого ефекту при обертанні печі поперечний перетин футерівки виконують у вигляді багатокутника. Піч опалюють газом або мазутом. Шихту завантажують через отвір у одному з торців печі. Льотка розташовується на бічній стороні барабану.
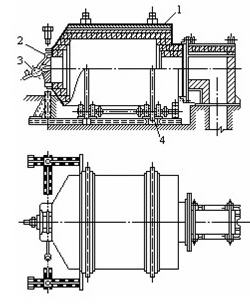
Рисунок 6 – Короткобарабанна роторна піч
5. Канальна індукційна піч
За принципом дії представляє своєрідний трансформатор, вторинною обмоткою якого служить U-подібний канал у футерівці череневого каменя, заповнений металом. Первинна обмотка - мідна трубка у вигляді спіралі, що охолоджується проточною водою. U-подібний канал охоплює спіраль первинної обмотки, усередині спіралі різміщується магніто-провід. Змінний струм, проходячи первинною обмоткою, утворює навколо себе та вторинної обмотки змінне магнітне поле, що створює в каналі ЕРС індукції. Струм, що виник в каналі, нагріває метал,який перебуває в ньому, і внаслідок його циркуляції нагріває весь метал у в печі.
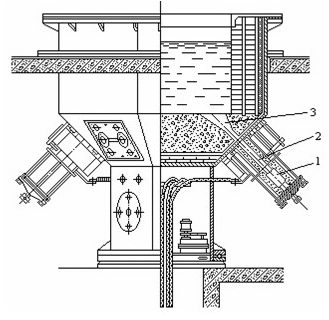
1, 2 – горизонтальний і вертикальний канал, відповідно; 3 – ванни
Рисунок 7 – Пристрій алюмінієвої канальної печі ІАК-25К
5.1 Індукційні тигельні печі
Промислової частоти також працюють за принципом трансформатора. Первинною обмоткою є трубчастий охолоджуваний проточною водою індуктор, навколишній тигель печі. Вторинна обмотка - метал у тиглі.
Індукційні печі тиглів промислової частоти мають такі переваги:
- низькі втрати металу на чад;
- високий тепловий ККД;
- проведення плавки без флюсу або з мінімальною його кількістю.
До недоліків можна віднести:
- заборона на плавку сировини із залізними припрацюваннями;
- необхідність наявності в тиглі залишку (болото) металу від попередньої плавки.
5.2 Дугові електричні печі
Широке застосування знайшли в ливарних цехах машіностроітельних заводів дугові електропечі (трифазні) змінного струму для плавки чавуну і сталі, а також в якості печей очікування (міксери). Електроплавка має ряд переваг: низький угар елементів, можливість отримання більш точного складу чавуну з меншим ко-лічеством шкідливих домішок, високий перегрів, кращі санітарно-гігієнічні умови плавки, можливість механізації і автома-тизації, а також регулювання процесу плавки. Плавку можна весті на твердій і рідкій завалке.Електродуговие печі працюють з основною і кислою футеровкою. Найбільш часто застосовують електродуговие печі з кислою футеровкою. У цих печах велика стойкость футерування, нижче її вартість, менше питома витрата електроенергіі, електродів і тривалість плавки. Печі з основ¬ной футеровкою застосовують для плавки легованих чавунів з високім вмістом алюмінію (так як алюміній енергійно восстанавлівает кремній з двоокису кремнію і руйнує кислу футеровку печі), марганцю та хрому, а також з незначним содержаніем сірки (до 0,04%). У дугових печах електрична дуга виникає безпосередньо між електродом і розплавляється металевої шихтою. Електріческій режим печі регулюють, змінюючи напругу на електродах або довжину дуги. Зміна напруги на електродах здійснюють шляхом перемикання ступенів трансформатора. Піч харчується від трифазної мережі промислової частоти напругою 6 ? 35 кВ. Для зменшення втрат електроенергії пічні трансформатори устанавлівают максимально ближче до печі. Основними вузлами дугового трифазної печі змінного струму є: металевий каркас, механізм нахилу, футеровка, звід, механізм переміщення зводу, електродів і електродотримачів, електрообладнання, система водяного охолодження і гідравлічної системи приводу механізмів.
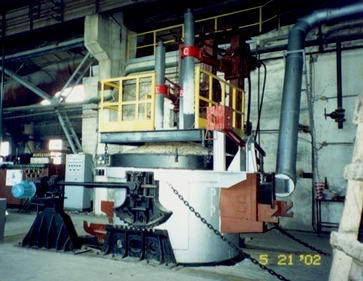
Рисунок 8 – Дугова печ перемiнного струму модель ДСП-1,5
5.3 Розвиток дугових печей постійного струму
Відмінною особливістю дугових печей постійного струму (ДППТ) є наявність тільки одного верхнього графітового електрода (катода), розташованого вздовж вертикальної осі печі, і подових електродів (анодів) в подині печі .
Світове лідерство у застосуванні ДППТ належить Японії, де за останні вісім років впроваджено понад 13 печей, включаючи сверх¬мощние. Активно розвивають їх застосування США, Південна Корея, Індія та інші країни.
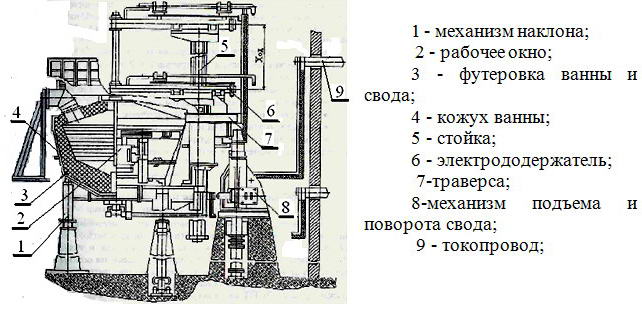
Рисунок 9– Дугова піч постійного струму для плавки чавуну і сталі
Основні передумови впровадження цих печей:
• більш низька витрата електродів 1,5...2,0 кг / т;
• економія електроенергії 3...5%;
• ефективне, більш рівномірний розподіл теплоти;
• зниження витрати вогнетривких матеріалів;
• природне перемішування розплаву;
• більш простий догляд за піччю;
• зменшення негативного впливу на живильнумережу,можливість підключення в мережі з меншою потужністю короткого замикання.
5.4 Індукційні печі середньої частоти
Технічні та економічні переваги індукційних печей середньої частоти (ИПСЧ) обумовлені ефектом внутрішнього нагріву шихти вихровими струмами. Індукційний метод забезпечує виділення теплоти безпосередньо в металі без теплопередачі випромінюванням або конвекцією, що зазвичай супроводжується значними втратами. Індукційні печі мають значно більший технологічний ККД, ніж агрегати, що працюють на паливі. У порівнянні з індукційними печами промислової частоти (ІППП) плавка чавуну на середній частоті має деякі переваги:
• садочный режим плавки (без використання «болота») дозволяє виключити попередню сушіння шихти та пов'язані з нею витрати, а також скоротити витрати на футеровку, так як її довговічність при садочном режимі плавки зростає і, нарешті, виключити непродуктивні витрати праці, електроенергії та матеріалів, пов'язані з неможливістю відключення ІППП на час перерв у роботі;
• допустима питома потужність, що підводиться до металу, в 3 рази вище, ніж у ІППП (в ИПСЧ - 1000 і ІППП - 300 кВт-год/т), що забезпечує короткі цикли плавки (40...45 хв), підвищує теплотехнічний ККД;
• витрата електроенергії вдвічі менше, ніж у ІППП, що працюють у безперервному циклі плавки з частковим зливом металу і періодичної дозагрузкой шихти;
• можливість роботи в режимі стабілізації активної потужності на всьому циклі плавки, починаючи з «холодного» стану шихти (активна потужність на середніх частотах передається за рахунок феромагнітних властивостей шихти) і закінчуючи розплавом металу (активна потужність підводиться за рахунок вихрових струмів у вузькому шарі ванни розплаву, що дозволяє підвищити ефективність використання встановленої потужності електрообладнання при високій якості споживаної електроенергії).
Питома витрата електроенергії на тонну чавуну наближений до кращих показників дугових печей змінного і постійного струму. Однак процес плавки в ИПСЧ позбавлений недоліків, властивих ДСП:• інтенсивні пило - і газовыброси, що вимагають додаткових витрат на газоочистку;
• значний витрата графітових електродів;
•інтенсивний вплив на живлення енергосистеми, пов'язане з нерівномірним характером навантаження в циклі плавки, виникненням експлуатаційних коротких замикань, низькою якістю споживання електроенергії, що вимагає значних витрат на компенсуючі пристрої зовнішньої електромережі.
Життєвий цикл будь-якого виробу, машини, апарату закінчується внаслідок морального або фізичного їх зносу. Брухт (відходи споживання), в більшості випадків, це складне, багатокомпонентну сировину, при переробці якого потрібні спеціальні технологічні схеми і відповідне апаратурне оформлення.
В даний час основними агрегатами для плавки алюмінієвих відходів є полум'яні відбивні печі. Однак прагнення скоротити втрати металу при переплаву шихти з розвиненою, забрудненою поверхнею (брухт, стружка, шлак тощо) послужило основною причиною для розробки роторних печей з горизонтальною віссю обертання, а в подальшому і розробки роторних печей з похилою віссю обертання, різною місткістю в діапазоні 5…20т по алюмінію.
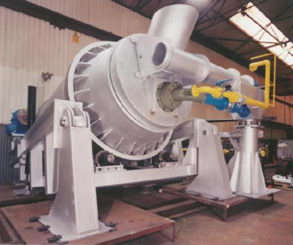
Рисунок 10 - Індукційні печі середньої частоти
Цей тип печей має значні переваги перед усіма типами печей експлуатованими в даний час для плавлення брухту кольорових металів і в першу чергу для плавки шлаків і забруднених відходів. Переваги роторних печей з похилою віссю обертання полягають у наступному:
1. Скорочення витрати флюсу(солі)на50%;
2. Збільшення продуктивності печі на70%;
3. Збільшення завантажувального вікна;
4. Відсутність додаткових випускних вікон для зливу шлаку.
Для прискорення процесу плавки та підвищення теплотехнічного ККД пічні агрегати оснащені пристроями виброционных живильників для подачі брухту дробленого в піч, а також пристосуваннями для фільтрації розплаву і безокислительной розливання металу на полегшених конвеєрах в злитки масою 4...6 кг.
Полум'яні стаціонарні одне або двокамерні відбивні печі з завантаженням сировини через бічні завантажувальні вікна. У таких печах можна переробляти різноманітну сировину, однак при плавленні шихти з розвиненою забрудненою поверхнею (шлак, стружка, дрібна обрізь тощо) спостерігається значний вигар металу. При завантаженні сировини з великим вмістом заліза відомі випадки підвищення вмісту останнього в розплаві, збільшується тривалість чищення плавильної камери, зростають втрати металлузішлаками.
В торцевій частині корпусу печі з боку виходу димових газів (продуктів згоряння) встановлений газохід з мембраною для забезпечення вибухобезпечною експлуатації печі. Для випуску з печі рідкого металу і шлаку в циліндричної частини барабана робляться два діаметральних протилежно розташованих вікна для установки льоток, які в процесі плавки (обертання барабана) закриті спеціальним пристроєм.
Висновки
У всіх технологічних процесах, пов'язаних з отриманням і обробкою металів, широко застосовують теплотехнічні агрегати - печі різного типу і призначення. Використовуваня:
- За технологічним призначенням (виробництво того чи іншого матеріалу або сплаву);
- По виду теплового процесу (плавильні, нагрівальні, сушильні, ...);
- По режиму роботи (безперервно працюють і періодичної дії);
- За температурою в робочому просторі (низькотемпературні, до 400...500°C, середньотемпературні, до 800...900 °С і високотемпературні, понад 1000 °С);
- По джерелу енергії (паливні, електричні, автогенні з генерацією за рахунок хімічної енергії сировинних матеріалів);
- За способом транспортування, завантаження і розвантаження матеріалу (штовхальні, роликові, протяжні, печі з крокуючим подом, з бічної видачею металу тощо);
Технологія приготування сплавів і застосовуються плавильні агрегати для кожного з цих видів виробництва має специфічні особливості. Найбільший вплив на вибір плавильних агрегатів для окремих підприємств надають наступні чинники: склад шихтових матеріалів, обсяги виробництва і номенклатура сплавів, технологічні обмеження по використанню відходів власного виробництва, а також необхідність забезпечення технологічних вимог щодо якості випущених напівфабрикатів і рентабельності їхвиробництва, наявність енергетичних джерел.
Проаналізовано пічні агрегати, що використовуються в даний час і перспективні види обладнання, показано їх переваги та недоліки при виробництві: Шахтне плавління мідевмісного лому та відходів при вдаваній, є насправді процессом складним, таким, що вимагає великого досвіду й уваги при його проведення. Невеликі відхилення від режиму викликають ускладнення та неполадки в роботі печі й нерідко виводять її з ладу.При цьому економічна ефективність мінімальна або взагалі відсутня, оскільки витрати на виробництво кисню не компенсуються зниженням витрат на кокс, а втрати міді і олова збільшуються.
Індукційна плавка забезпечує велику продуктивність і високу якість металу, а також рівномірний хімічний склад і температуру по всій ванні, різке скорочення об’єму та концентрації шкідливих речовин у газах, що виділяються, малі безповоротні втрати металу. Проте вогняним рафінуванням не можна видалити такі домішки, як благородні метали та вісмут, оскільки вони мають з киснем меншу спорідненість,ніж мідь, і тому не окислюватимуться, знаходячись у розплаві міді.
Сталеві котли, які використовуються для виплавки свинцю,допускають короткочасний перегрів до 700...800 °С, але тривало служать лише при нагріві до температури, що не перевищує 600 °С.Тому для переробки у котлах придатний тільки такий лом, який розплавляється при температурі нижче 600 °С.
Для плавки алюмінієвмісного лому і відходів застосовують печі різноманітних конструкцій: полум’яні відбивні, шахтні – що обертаються, поворотні - що обертаються, електричні індукційні, а також комбінації перерахованих типів.
Індукційна тигельна печ маэ заборону на плавку сировини із залізними припрацюваннями та необхідність наявності в тиглі залишку (болото) металу від попередньої плавки.
В даний час основними агрегатами для плавки алюмінієвих відходів є полум'яні відбивні печі. Однак прагнення скоротити втрати металу при переплаву шихти з розвиненою, забрудненою поверхнею (брухт, стружка, шлак тощо) послужило основною причиною для розробки роторних печей з горизонтальною віссю обертання, а в подальшому і розробки роторних печей з похилою віссю обертання.
Слід зазначити, що роторні печі типу ПРНА активно використовуються також в якості агрегатів при вхідному контролі постачання брухту і відходів, т.я. велика швидкість плавки, механізація процесу найбільш повно відповідають якісної та кількісної оцінки сировини.
Перелік посилань
- Бредихин, В. Н., статья : Экологические и технологические проблемы переработки алюминиевых отходов.
- М .С.Шкляр Печи вторичной цветной металлургии: М.Метал,1987,216с.
- Бредихин В. Н. ,Маняк М. О. ,Смирнов В. О. Металлургия кольорових металлив (частина 7).Вторинна металлургия кольорових металлiв.
- http://ukrbascompany.at.ua/index/organizacionnye_i_tekhnologicheskie_osobennosti_proizvodstva_aljuminievykh_splavov/0-182.
- http://media.ls.urfu.ru/497/1284/2791/.