Abstract
Ñîäåðæàíèå
- Introduction
- 1. Relevance of the topic
- 2. Purposes and tasks
- 3. Review of researches and development
- Conclusion
- References
Introduction
Quality of continuous preparation and stability of pouring – the interconnected process parameters. Deposits of nonmetallic inclusions on walls of the channel of a steelpouring path (a glass batcher and the immersed glass, including steelpouring openings) compel to reduce the speed of continuous pouring up to its complete cessation. Nonmetallic inclusions can lead to major defects of metal. The deposits which are formed in the channel worsen pouring conditions, having indirect impact and on quantity captivity: reduction of the section through passage of a metalwire results in unevenness of a stream and fluctuations of level of metal in a crystallizer that promotes hit of integumentary slag from a crystallizer in metal and, as a result, to violation of uniformity of process of formation of structure of an ingot.
1. Relevance of the topic
The solution of tasks on this subject can be entered in the list priority as it mentions two such important factors of production, namely - decline in production and qualities of metal, because of a tightening of a submersible glass.
2. Purposes and tasks
The purpose of work is consideration of overgrowing of submersible glasses, tightening speed, structure of the formed nonmetallic inclusions on glass walls, and also research of the minimum decrease in temperature became, suppression of secondary oxidation and reduction of a specific surface of contact of metal with a glass for reduction of speed of overgrowing.
3. Review of researches and development
Are necessary for delay of process of a tightening: protection of a stream of metal against secondary oxidation throughout a metallurgical path, including production of metal from a steelpouring ladle; decrease of the activity of oxygen and the content of nonmetallic oxidic inclusions in steel before pouring due to pumping out of metal and processing by its recovery slags; modifying of nonmetallic inclusions of alumina input in calcium metal; creation of conditions for removal of inclusions in an intermediate ladle as a result of application of turbostop, partitions, thresholds, inflation of argon in metal in an intermediate ladle; these measures are effective in combination with use of slag-forming mixes; use in a design of metal wires of the refractory materials interacting with aluminous nonmetallic inclusions, for example containing calcium zirconate, with formation of allegedly fusible connections which are washed away then a metal stream, or use of the not moistened materials forming a gas layer on contact a refractory materials – nonmetallic inclusions.
These are, of course, not all known measures; for example, the questions of hydrodynamics of the expiration of metal, geometry the steel-tapping hole of channels aren't raised that in some cases can play an essential role.
The typical picture of deposits which is usually fixed on internal surfaces of the immersed glasses, is presented in fig. 1. It is visible that deposits on walls of the immersed glasses have zone structure. The phase structure of deposits on walls of the glasses immersed the corundum- graphite (according to the petrographic and X-ray phase analysis) when pouring staly St3 and 17GS is given below. In the dynamo steel containing 0,45% [Al] the main phase of deposits it is presented by alumina, including in a friable zone. Presence at steel 10G2BT of the titan at quantity to 0,08% was shown available calcium geksaalyuminat (Ñàη6Al2O3), the containing Ti2O3.
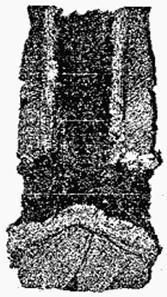
Figure 1. Nature of deposits on an internal surface of the SEN
Phase structure of deposits on walls of the glasses immersed the corundum-graphite:
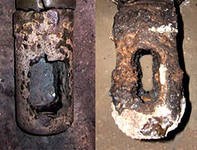
Figure 2. Overgrowing of a steelporing SEN.
It is also necessary to note that in deposits a significant amount of reguluses of metal by the sizes 0,001 – 4 mm as which matrix the oxidic component serves is observed.
In some cases metal represents a matrix in which nonmetallic inclusions in a look the contain alumina compound difficult structure are placed. Thus metal occupies 30 – 95% of volume of a layer. This option is typical for conditions of pouring of steel with a temperature in an intermediate ladle at the level of the lower limit of a pouring. Macro - and the microstructure of deposits on walls of channels of the immersed glasses is presented respectively in fig. 1 and 2 during the pouring of steel of the following structure, %: 0,13 – 0,14 C; 0,63 – 0,64 Mn; 0,21 – 0,25 Si; 0,018 – 0,025 S; 0,014 – 0,018 P; 0,03 – 0,04 Cr; 0,03 – 0,06 Ni; 0,03 Cu; 0,02 – 0,04 A1; 0,002 Ti. Temperature began also the end of pouring 1555 – 1570 and 1540 – 1555 °C respectively. Chemical and phase composition of the deposits given on fig. 2, following %: 1 – iron metal (98,66 Fe; 0,88 Mn; 0,46 O); 2 – partially oxidized iron (90,6 Fe; 1,46 Mn; 7,97 O); 3 – corundum (70,7 Al; 29,30 O); 4 – difficult manganic spinel (72,84 Al2O3; 16,82 MNO; 7,21 MgO; 2,45 FeO; 0,68 TiO2); 5 – difficult manganese aluminosilicate (27,95 Al2O3; 27,61 SiO2; 27,70 MNO; 4,12 Na2O; 3,77 TiO2; 3,0 ÑàO; 2,29 K2O; 2,69 ZrO2; 1,0 MgO). Thus iron and corundum prevail, and difficult manganese aluminosilicate and partially oxidized iron are present at a small amount.
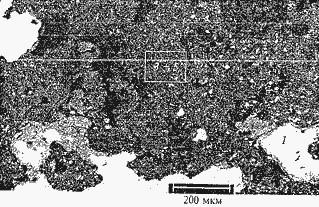
Figure 3. A microstructure of deposits on a wall of the channel of the immersed glass after service, 1 – iron metal; 2 – the iron which is partially oxidized; 3 – corundum; 4 – spinel manganic; 5 – difficult manganese aluminosilicate
More typical deposits on walls of the immersed glasses include a congestion of lamellar corundum, geksa-and dialyuminat of calcium and spinel of difficult structure with impregnations of reguluses of iron.
The nature of nonmetallic inclusions in deposits at the contents [A1]×0,03% in combination with processing by the high-limy deoxidated slag or TShS (CaO + CaF2) corresponds to composition of aluminates of calcium and magnesium with presence of particles of alumina. Research of structure of nonmetallic inclusions in Electrostal deoxidated by aluminum after processing by "white" slag shows that inclusions consist mainly of aluminates of calcium and magnesian spinel. Thus the greatest number of aluminates of calcium is presented by ÑàO particles · to 6Al2O3 and ÑàO·2Al2O3. The inclusions corresponding to a phase 12CaO·7Al2O3, meets extremely seldom and in small quantity. Big aluminates of calcium contains, as a rule, crystals of the emitted magnesian spinel.
We will consider conditions of formation of nonmetallic inclusions of the second and third sort in deoxidated by aluminum became also the mechanism of their adjournment on walls of submersible channels.
In the conditions of pouring of metal on an entrance to a glass batcher of an intermediate ladle temperature of metal is equal to t = to tL + (35 – 40) °C. Steel comes to a crystallizer at a temperature close to temperature of a likvidus (1475 – 1545 °C). It is possible to assume that on a fire-resistant cold wall of a glass there is a reduction of temperature to two-phase area below up to solidus temperature.
At the movement of liquid metal on a metalwire the stream of metal deviates a vertical and starts concerning a wall of the immersed glass, for example because of not coaxiality of an arrangement of a stopper monoblock of rather razlivochny opening of a glass and vertical movements at regulation of level of metal in a crystallizer. Corundum-graphite glasses (25 – 30% C), especially cold, have the increased heat conductivity. We will note that heat conductivity of graphite at the room temperature is three times higher, than at 1000 °C, and four times, than at 1500 °C.
As a result of heat exchange of a cold wall of an refractory materials and steel on a surface of a glass sow is formed. Thus, the heat conductivity of a wall is higher, the formation of metal sow is more probable.
In the spilled steel in the dissolved look there are an oxygen and strong elements deoxidants, such as A1, Sa, Mg. Thus, in steel difficult products of a deoxidation have to be formed. For the analysis and a solution of the problem of nonmetallic inclusions it is useful to use, in our opinion, the surfaces of solubility of components calculated by G.G. Mikhaylov in liquid metal (PRKM) which allow to establish a complex of the oxidic phases which are formed at interaction of metal fusion of Fe system: Få – Ñ – Î – À1 – Ñà – Mg with the dissolved oxygen.
In figures 3 and 4 PRKM in Fe systems: Få – Ñ – Î – À1 – Ñà and Få – Ñ – Î – À1 – Ñà – Mg are presented at 1500 and 1550 °C and 101 kPas. Fat lines set concentration areas of liquid metal here, equilibrium from one of oxidic phases – products of a deoxidation became which nature is specified in parentheses. Thin lines put oxygen sections submersible channels.
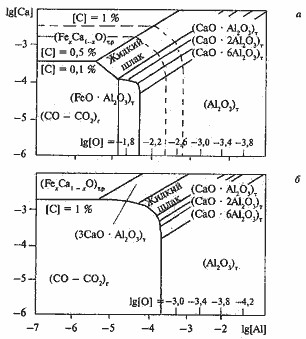
Figure 4. Fe system PRKM: Få – Ñ – Î – À1 – Ñà at 1550 (a) and 1500 °C, p = 101 kPas
![Fe system PRKM: Få – Ñ – Î – À1 – Ñà – Mg at °C, ð = 101 kPas, 5·10-3% [Ca] (a) and 5·10-4% [Ca]](images/ris5.jpg)
Figure 5. Fe system PRKM: Få – Ñ – Î – À1 – Ñà – Mg at °C, ð = 101 kPas, 5·10-3% [Ca] (a) and 5·10-4% [Ca]
According to contents [A1], [Ñà], [Mg] and PRKM for the systems given on fig. 4 and 5, equilibrium nonmetallic inclusions have to contain aluminates of calcium of structure of Ñàη6Al2O3; Ñàη2Al2O3; ÑàηAl2O3; system spinels FåηAl2O3 – MgηAl2O3 (gertsinit-alyumomagniyevy spinel).
At the high content of aluminum in steel corundum (Al2O3) will be an equilibrium phase in inclusions of oxides. At small contents of aluminum (≤0,01%), to Ñà and Ìg (< 10-6 – 10-7%) the equilibrium structure of nonmetallic inclusions is presented by the oxides of difficult structure which are in addition containing SiO2, ÌnÎ, FåÎ. At the contents [A1]≥0,03% and rather low concentration [Mg] and [Ñà], according to Fe system PRKM – With – About – A1 – Sa – Mg which are allocated inclusions will correspond to corundum. At a pouring temperature the structure of deposits depends on the maintenance of Sa, Mg, A1 which are in fusion.
One of ways of prevention of overgrowing of an intermediate glass at continuous pouring of steel, is refinement of steel from the nonmetallic inclusions which are formed at a metal deoxidants.
Now many ways of a deoxidants of steel are known, the basic from them which is widely put into practice is the besieging deoxidants. The essence of this method consists that the deoxidants entered into liquid metal interact with the oxygen dissolved in it, forming the oxides which are allocated from metal fusion in the form of a firm or liquid phase. Especially the importance thus is attached to questions of removal from liquid metal of nonmetallic inclusions products of a deoxidants.
On kinetics of removal of nonmetallic inclusions their such properties as melting temperature, density, specific interphase energy have a great influence on surfaces metal - inclusion.
Actually deoxidants steel carry out to furnaces and a ladle or only in a ladle. This process is carried out in some stages, the deoxidants regulating an order of introduction and their quantity.
Because of secondary oxidation there is a waste of aluminum and calcium that affects on purity of metal.
During pouring metal contacts to oxygen of the surrounding atmosphere that can lead to increase in the content of oxygen and nonmetallic inclusions in steel and reduce efficiency of extra oven refinement of metal.
At a solution of the problem of a tightening of a glass of an intermediate ladle the attention of protection against oxidation is paid on a site steel-bucket intermediate-bucket, and also conditions of metal in an intermediate ladle.
Ðouring | Quantity of swimming trunks | Content of oxygen, mass fraction, % | Content of nonmetallic inclusions, mass fraction, % | ||
in steel–bucket | in cast metal | in steel–bucket | in cast metal | ||
With protection of a stream of metal from steel–bucket | 7 | 0,0066 | 0,0098 | 0,0068 | 0,043 |
With protection of a stream of metal from steel–bucket and metal mirrors in intermediate–bucket | 5 | 0,0067 | 0,0089 | 0,0069 | 0,040 |
Without slag aiming in in termediate–bucket | 5 | 0,0066 | 0,009 | 0,0069 | 0,047 |
With aiming of slag in termediate–bucket | 5 | 0,0064 | 0,0085 | 0,0066 | 0,037 |
From table 2 it is visible that giving propane - butane mix under a cover of a intermediate-bucket promotes decrease in the content in cast metal of oxygen and nonmetallic inclusions. For protection of a mirror of metal used various mixes for targeting of slag in an intermediate ladle. When pouring 10 skilled swimming trunks the following materials are tested: mix silikokaltion, fluorspar and grog powder (1:1,5:2,5); mix of fluorspar, recovery electrooven slag and grog powder (5:2:1); the calcinated soda, cryolitas.
All used materials quickly melted, forming zhidkopodvizhny slag. The slag which is formed at mix fusion a silikokaltion, fluorspar and grog powder was more acceptable and it used for further tests. With such slag five skilled swimming trunks were poured, giving it at the beginning of pouring. The data provided in table 2 show that use of slag-forming mix promotes decrease in the content in cast metal of oxygen and nonmetallic inclusions. The composition of the slag which is selected from a intermediate-bucket at the beginning the middle and the end of pouring is given in table 2.
Sampling in process | Chemical composition of slag, mass fraction,% | ||||||
Ðouring | CaO | MgO | Al2O3 | SiO2 | Cr2O3 | MnO | FeO |
At the beginning | 30.30 | 0.04 | 12.0 | 34.80 | 0.83 | 3.24 | 2.68 |
In the middle | 23.30 | 0.03 | 12.5 | 38.40 | 10.10 | 6.53 | 2.76 |
At the end | 20.30 | 0.03 | 12.1 | 40.60 | 14.24 | 9.12 | 2.63 |
Nature of change of the content of oxides of silicon, manganese and chrome in slag testifies to considerable removal from liquid steel of nonmetallic inclusions in the course of pouring.
Due to noted features it is necessary to weaken secondary oxidation of metal on a site an intermediate ladle crystallizer. However these at best can reduce the content of oxygen in metal at the level of its concentration in an intermediate ladle. For receiving bigger effect it is necessary to protect metal on a site a steelpouring ladle - an intermediate ladle.
Follows from the told that for increase of purity of metal it is necessary to seek to deoxidate more deeply it, to spill with the greatest possible speed and to protect a stream from contact with air. For protection against secondary oxidation use a number of ways, for example such as pouring in the atmosphere of argon, pouring under level now, etc.
Conclusion
For prevention of overgrowing of an intermediate ladle at continuous pouring of steel it is necessary to refine steel from the nonmetallic inclusions which are formed at a metal deoxidate.
For this purpose it is necessary to know structure and the nature of the nonmetallic inclusions which are in liquid metal.
"Overgrowing" of a glass happens, probably, inclusions of the alumina which is formed at a deoxidate became aluminum. The metal purge by argon is applied to removal of refractory inclusions of alumina by emerging in a slag phase. The purge argon after a deoxidate of steel is a necessary measure for steel refinement.
At an additive in calcium metal nonmetallic inclusions of alumina are transformed to calcium aluminates. Aluminates of calcium have lower temperature of melting and their hardening happens in MNLZ crystallizer. The most optimum structure of inclusions from the point of view of temperature of melting of the formed inclusions is recommended at the maintenance of 50 - 52% of oxide of calcium. When pouring of the modified metal the number of overgrowth of a glass of an intermediate ladle significantly is reduced.
Necessary condition of modifying is the optimum ratio of the entered aluminum and calcium providing inclusions with a low temperature of melting.
Existence of secondary oxidation of metal at extra oven processing and pouring has an adverse effect on purity of metal. At secondary oxidation there is a waste of aluminum and especially calcium in steel. For protection against secondary oxidation it is necessary to protect a metal mirror slag-forming mixes, to apply pouring under level and in the atmosphere of neutral gas (argon).
References
- Smirnov A.N. Modern ogneupor and technologies in production became / À.N. Smirnov – Donetsk: Noulidzh, 2013. – 179ñ.
- Zborshchik A.M. Abstract of lectures on discipline "Steel metallurgy" / À.Ì. Zborshchik – Donetsk: SHEI «DonNÒU», 2008. – 238 ñ.
- Zborshchik A.M. Abstract of lectures on discipline "Special methods of molding" / À.Ì. Zborshchik – Donetsk: SHEI «DonNÒU», 2007. – 158 ñ.
- Dyudkin D.A., Ukhin V.E. Ogneupora and their operation / D.A. Dyudkin , V.E. Ukhin - Donetsk: SHEI «DonNÒU»
- Smirnov À.Í., Safonov V.M., Dorokhova L.V., Tsuprun A.Yu. Metallurgical mini-plants / À.N. Smirnov, V.M. Safonov ,L.V. Dorokhova ,A.Yu. Tsuprun – Donetsk: Nord-Pres, 2005. - 469 ñ.