Abstract
Contents
- Introduction
- Relevance of the Topic
- Goals and Objectives, Expected Results
- Overview of Research and Development
- References
Introduction
Present theoretical analysis of the metal treatment under pressure received new opportunities related to a rapid development of numerous methods of problem solving in continuum mechanics. Since the late twentieth century, the finite element technique has been used more widely in solving problems of formation due to the emergence of technical capacities of computer engineering.
Mathematical modeling of processes of material treatment under pressure is of great importance for the development of theory and practice since it is implemented for analysis and optimization of the process in exploration, such as rolling, pressing, drawing, forging, volumetric and sheet metal stamping.
Relevance of the Topic
At the moment, modern metallurgy for production of the billets applies the continuous casting method in CCM in most cases (more than 60%). In spite of the rapid development of this technology and continuous advancement of the equipment, it is comparatively new, which raises a number of unresolved or partially resolved questions in its context. For instance, such problems concern the quality of billets. There are several types of defects: External (surface cracks), internal (liquation, porosity), and geometrical (rhombic shape).
Today a method of “soft” crimping is used for solving a number of problems related to defects of continuous cast steel billet. The method includes crimping of the continuous cast steel billet in the stream by changing it insignificantly (level of deformation is less than 1%) on the sites in the two-phase state (with core uncrystallized). Implementation of this method can require withdrawal and straightening unit or a specialized unit that completes the process of “soft” mechanic crimping.
The leaders in production of continuous casting machines (CCM) and related equipment are the following states: Germany («SIMENS-VAI», «SMS-DEMAG»); Italy («DANIELI»); Japan («SUMITOMO»); CIS (JSC "Engineering Corporation" Uralmash "", JSC "NKMZ"). These producers are trendsetters that define direction in development of equipment and technology related to continuous casting of billets[1, 2, 3].
Goals and Objectives, Expected Results
The goal of the present study is modeling of several widely spread schemes of arranging equipment during the process of “soft” mechanic crimping and identifying deformation characteristics in different straightening sites in different compression modes. Defining appropriateness of implementing the method of “soft” mechanic crimping exclusively on withdrawal and straightening unit. Deformation characteristics of units of “soft” crimping in different deformation modes (smooth, stepwise, and others).
Due to the current tendency in the field of design and simulation of metallurgical processes, computer simulation is actively involved to make the process more cost- and time-efficient. There is a range of computer applications for such simulations that apply a finite element technique. Such programs include the following: Universal - ANSYS, ABAQUS; specialized for metal treatment under pressure - DEFORM 3D, Q-FORM. The present study utilized the DEFORM 3D software package.
One of the schemes of arranging the straightening and bending equipment by “SMS Siemag AG” was used in the context of the present study with no crimping in the withdrawal and straightening unit and with smooth (equal in each pair of rollers compression ratio) in the site of “soft” crimping.
Geometry of the model was built with the ADS (Automatic Design System) Compass-3D (Компас-3D). This model contains 6 (six) rollers (with the diameter of 320 mm each) of the withdrawal and straightening unit and 4 sections with 8 rollers per section (with the diameter of 160 mm each) of the machine that realizes “soft” crimping. The geometry was selected in accordance to the scheme of “SMS Siemag AG” units.
A billet chosen for this simulation has the following geometric settings: length needed for objective calculations – 6000 mm; bending radius of the billet with CCM before it passes the withdrawal and straightening unit – 6000 mm; a square cross-section with dimensions 150x150 mm. According to the State Standard for this cross-section, deviation of the size should not exceed 2.5 mm. Simulation takes place with the temperature on the surface of 1150°С and in the core of 1450°С.
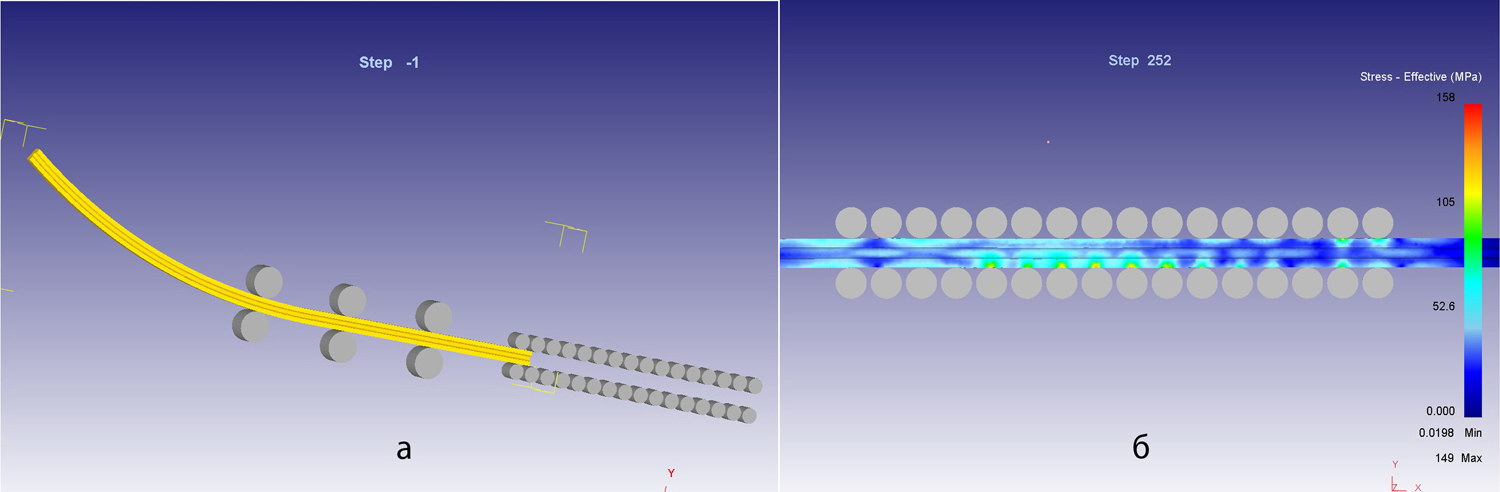
Further measures in the context of the research will include improved detailing of this model intended to receive more accurate results. In addition, a range of calculations will be completed for this unit with different crimping modes and methods (stepwise, singular) and analytical comparison of these options will be done to identify the most appropriate one for implementation and utilization. Afterwards, a similar simulation, calculation, and analysis will be completed with some portion of the most widely spread unit arrangement modes on the bending and straightening site. Cases of crimping of billets of other cross-sections will be simulated for every unit. Eventually, a comparative analysis of all units will demonstrate appropriate modes of crimping and all cross-sections to identify statistical correlations of the bending process, straightening, and “soft” crimping for further technological modification[1, 2, 3].
Overview of Research and Development
Experimental studies of the “soft” crimping of continuous cast steel billets in industrial environment were conducted using the withdrawal and straightening device of the continuous casting machine of Yenakiyevo Metallurgical Plant.
Lately JSC “Yenakiyevo Metallurgical Plant” implements a program aimed at efficiency increase with continuous casting machines. Experts of the manufacturing company of the existing continuous casting machine, JSC “NKMZ” were involved for monitoring of the presently existing steel casting technology in continuous casting machines, and recommendations on implementation of diverse technical and technological decisions aimed at elimination of flaws and increase of the continuous casting machine efficiency. The basic conclusions on the offered modernization program for continuous casting machine were the following: Increase of the continuous casting machine efficiency may be achieved partially through speed increase. After completing a range of changes, the speed of casting of continuous cast steel billet increased by 15-20%; in particular, average speed of the casting of the area with dimensions of 150x150 mm, production of which takes approximately 60% of the overall work of continuous casting machine, increased from 2.65 meters per minute to 3.2 meters per minute. Formation of the shrinkage defects was noticed in the axial portion of the billet due to comments on the temperature mode of casting, cooling uniformity and efficiency of the continuous cast steel billet in the secondary cooling zone when casting every separate batch. On average, the defect score of axial porosity increased from 0.5 to 1.0-1.5 points after shifting to high-speed casting. Besides, formation of contraction cavities was identified in some batches; sizes of cavities were 1.0-2.0 mm.
To reduce shrinkage defects in axial zone of continuous cast steel billet, it was suggested to consider the option of crimping the billet in rolls of the withdrawal and straightening unit by increasing the pressure for drawing rolls of the withdrawal and straightening unit. The first stage of implementation included a theoretical calculation of the required effort to eliminate shrinkage in axial zone, but also to keep geometrical settings of the square billet within its valid values after crimping.
Theoretical calculation and further practical experiment was completed while casting of the continuous cast steel billet with the cross-section of 150x150 mm. The experiment enabled to identify that continuous cast steel billet with the cross-section of 150x150 mm and the size of its absolute crimping of 1.5 mm requires pressure of hydraulic fluid supplied to the piston cavity to be increased by 0.9 MPa. In other words, it should be increased from 1.6 MPa to 2.5 MPa, which should facilitate the increase of the pressing force of the working rollers from 36.2 kN to 56.6 kN.
The second stage of implementation includes evaluation of the continuous cast steel billet crimping efficiency by the rollers of the withdrawal and straightening unit after preparation, coordination and approval of the technological task in a systematic way through adding 0.2 MPa to reach the initial value of the working fluid pressure of the cylinder of 1.6 MPa by implementing increased pressure on the rollers of the withdrawal and straightening unit when casting experimental batches. The experiment of using increased pressure of crimping on the rollers of the withdrawal and straightening unit was conducted on the stream #6 of the continuous casting machine #2. Casting of the experimental batches started on February 7, 2011 when casting the S235 steel grade. Every stage included adding of 0.2-0.3 MPa to the existing pressing of rollers of the withdrawal and straightening unit; 10 castings were completed in every stage with measurement of the geometrical sizes of the continuous cast steel billet in the hot stream, visual quality assurance of the billet surface for defects, selection of templates for macrostructure control, control of the casting speed and temperature of the billet surface before withdrawal and straightening unit. During the experiment on the stream #6, systematic increase of the pressure of hydraulic fluid of the cylinders of pressing the pinch rolls, measurement of the sides of the continuous cast billet in the hot stream on the unloading rack was done before the billet was submitted to the kant refregirator. With the pressure set at 2.3 MPa, the height of the billet was 147.5 mm (with the value of crimping 2.5 mm), width of the billet 152.0 mm (expansion of the billet 2.5 mm), according to the technical conditions TU U-27.1-00191193-023-2001 “continuous cast steel billet of square section,” permissible variation on the side of the square is ±3.5 mm. Shrinkage was completely eliminated after setting the value of the pressure on pinch rolls of the withdrawal and straightening unit at 2.3 MPa due to crimping of the hardened surface layers in a vertical dimension with an axial extrusion zone of the molten metal in a direction opposite to the casting. Overview of the selected templates (Fig. 4.2) supports the idea of the absence of the shrinkage defects and absence of strain cracks.
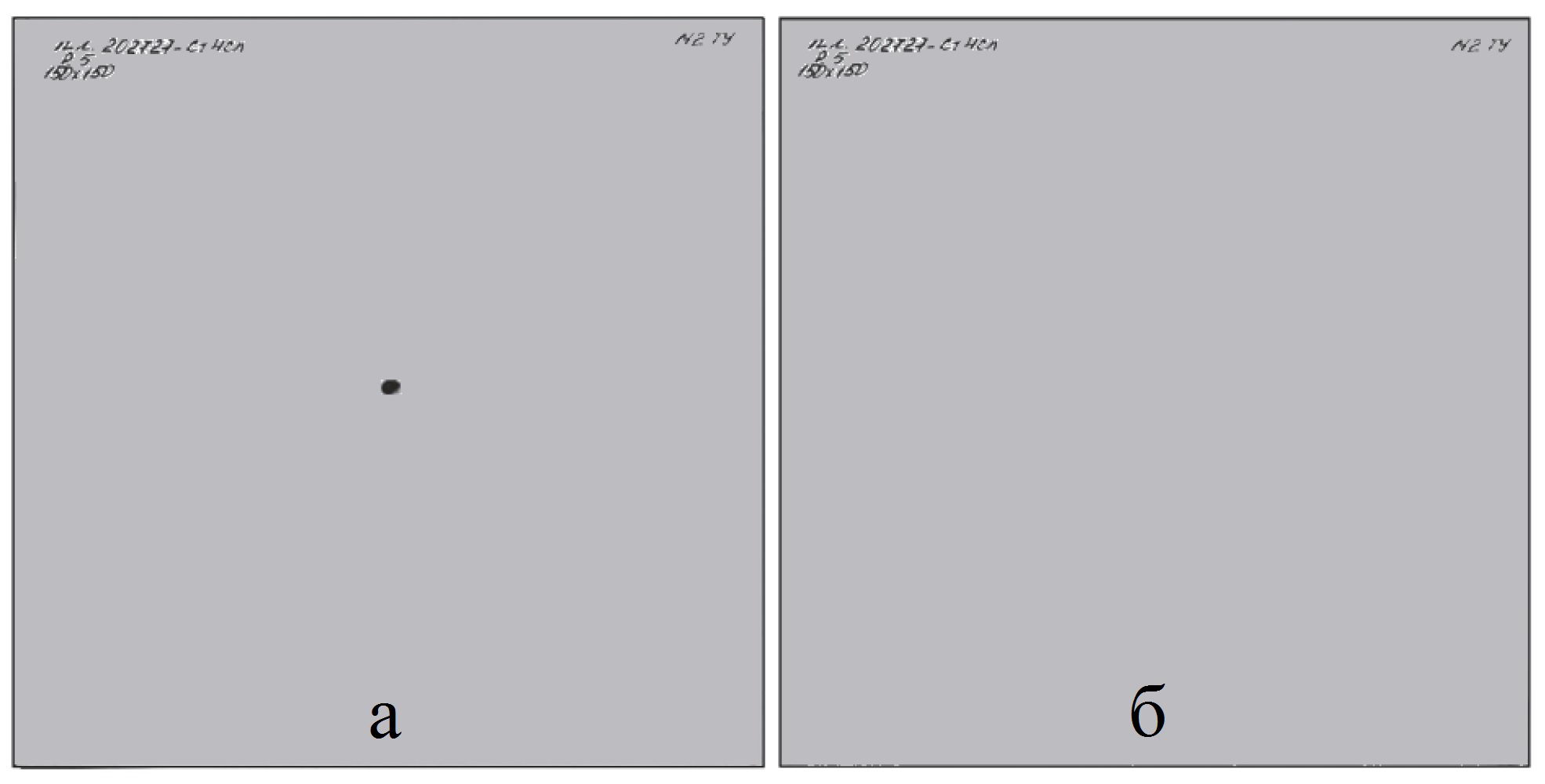
Results of the experiments conducted in industrial environment to explore “soft” crimping processes can be seen in Fig. 2 and in the Tables 1 and 2
Number of the Stream | The working fluid pressure supplied to the cylinder of the rolls pinching device of the withdrawal and straightening unit, MPa | Number of castings | Average speed of casting, meters per minute | Average temperature of the billet before withdrawal and straightening unit, 0С |
6 | 2,5 | 1128 | 2,98 | 1104 |
5 | 1,6 | 1115 | 2,93 | 1096 |
Number of the Stream | Average sizes of the sides of the square of CCB, mm/td> | Average score of axial porosity | Average size of the contraction cavity, mm | Average score of axial cracks |
6 | 148,5 x 151 | 0 | 0,5 | 0,5 |
5 | 150 x 150 | 2 | 2,5 | 0,5 |
After completing the report on the experiment, starting with March 30, 2011, for the continuous casting machine #2, the roll pressure was increased in the withdrawal and straightening unit to crimp the continuous cast steel billet and eliminate shrinkage defects in the axial zone of the billet.
Overall, the results of the completed experiments prove that implementation of the “soft” crimping with continuous cast steel billets is of sufficient effectiveness, which should be considered when creating new and improving the existing equipment of continuous casting machine[4].
References
- Смирнов А.Н. и др. Непрерывная разливка сортовой заготовки: Монография. / А.Н. Смирнов, С.В. Куберский, А.Л. Подкорытов, В.Е. Ухин, А.В. Кравченко, А.Ю. Оробцев – Донецк: Цифровая типография, 2012. – 417 с.
- Смирнов А.Н и др. Непрерывная розливка стали: Монография /Смирнов А.Н., Куберский С.В., Штепан Е.В Донецк: Донецкий Националый Технический Университет, 2012. – 417 с.
- Ручко, В. Н. Анализ особенностей и пути совершенствования конструкций тянуще-правильных машин сортовых МНЛЗ / В.Н. Ручко, Е.Н. Смирнов // Металлургические процессы и оборудование. - 2011. - №2. - С. 32-39.
- Куберский С. В. и др. Эксперементальное исследование процессов мягкого обжатия непрерывнолитой сортовой заготовки в промышленных условиях / Восточно-Европейский журнал передовых технологий. – 2011. – 4/7(52). – С. 41-43.