Abstract
Content
- Introduction
- 1. Timeliness of the topic
- 2. The purpose and objectives of the research, expected results
- 3. Development of the stand
- 3.1 Choosing a the motor
- 3.2 Choosing a microcontroller
- 3.3 Choosing a driver
- References
Introduction
In the modern world the state of electrification of industry and the development of complex automation systems shows that their basis is regulated electric drive, which is becoming more widely used in all spheres of life and activity from manufacturing to the sphere of everyday life.
This trend can be seen in the rapid development of 3D printing technology. With each passing day technology is taking root on CNC milling faster improved and become more accessible. Today, the 3D-printer print almost anything you can print: layout of the building itself, or even the construction, food, metal, bioprosthesis [1]. There is also a technology capable of creating living human tissues to replace vital organs and quickly heal open wounds [2].
1. Timeliness of the topic
In this master's work to develop a governance model will be used by the software Matlab is already a long time is used to model a variety of industrial process automation up to robotics. The physical model includes stepper motors, servo which is relatively cheaper, but in the worst degree controlled. It follows the importance of improving the stepper motor control accuracy and efficiency of the electric drive as a whole, with the help of available software in Matlab Simulink environment.
2. The purpose and objectives of the research, expected results
Objective: development of electric control system mechanism with two degrees of freedom.
The main objectives of the study:
- Selection of the motor.
- Selection of the controller and the actuator driver.
- The implementation of the physical model.
- Design of a mathematical model in MATLAB
- Analysis of the data obtained.
For experimental evaluation of the theoretical results and the formation of the foundation of further research, as the practical results it is planned to develop Simulink-model system in Matlab program.
3. Development of the stand
3.1 Choosing a the motor.
A stepper motor is an electromechanical device that converts electrical control signals into pulses the angular displacement of the rotor (binary mechanical displacement) in its latched position. The stepper motor can perform precise positioning and speed control without encoder feedback. It is more suitable for systems that operate at low acceleration and constant load. If the stepper motor to exceed its load time, information on the rotor position is lost and the system requires the deployment by, for example, limit switch or other sensor [3].
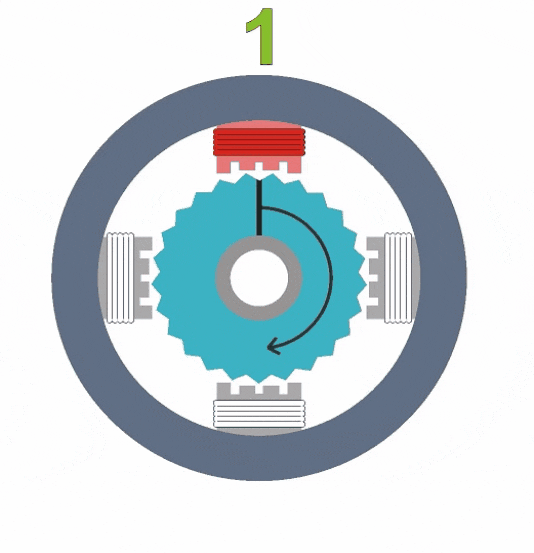
Picture 1 - The principle of operation of the stepper motor
Advantages of a stepper motor:
- Stability. It can handle a wide range of loads.
- It does not require feedback. The rotation angle laid in engine design.
- Relatively inexpensive relative to other traffic control systems.
- Standardized frame size and performance.
- Automatic connection technology. Easy to install and use.
- Safe. In the event of any failure is automatically stopping the engine.
- Long service life.
- High torque at low speeds.
- Repeatability. Returning to precisely the same position.
- Overload protection. The engine can be damaged due to mechanical overload.
Disadvantages of a stepper motor:
- Low efficiency. The engine uses a considerable amount of energy in spite of the load.
- The torque decreases as the rotation speed increases
- Low accuracy.
- Inclined to resonance. It requires micro-steps to smooth motion.
- Missing steps are not displayed.
- Low torque in relation to inertia. Not able to increase the load quickly.
- The engine will not pick up speed after instantaneous restart.
- Noisy at medium and high speeds.
- Useful low power in relation to size and weight.
Servo - type of electromechanical actuators that are not continuously rotate as stepper motors, and the signal transferred to a particular position and maintain it, and move to a different position for the next signal. The servo is also used feedback mechanism, so it can handle errors in positioning and correct them. Thus, if some force puts pressure drive and will change its position, the actuator will apply the force in the opposite direction, and try to fix the error. This leads to a high positioning accuracy [4].
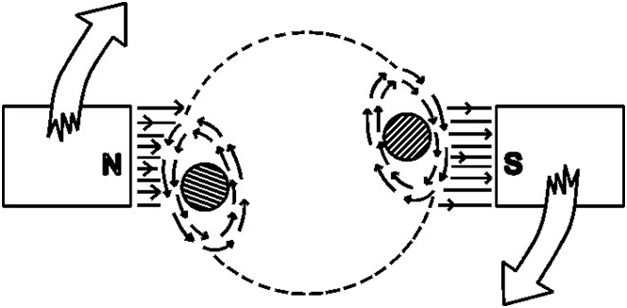
Picture 2 - The principle of operation of the servo motor
The advantages of servo motors:
- For small size engine you can get high power
- Large capacity range
- It tracks the position, through the use of feedback
- High torque in relation to the inertia
- The possibility of rapid acceleration and deceleration
- At high speed, high torque
- The permissible noise limits at high speeds
- Complete lack of resonance and vibration
- positioning accuracy
- A wide range of speed control.
- Accuracy of speed and torque stability.
- High static torque at zero speed.
- High overload capacity
- Small acceleration time
- Small moment of inertia of the motor, low weight, compact size.
Based on the above comparison, the stepping motor has been chosen to implement the working stand.
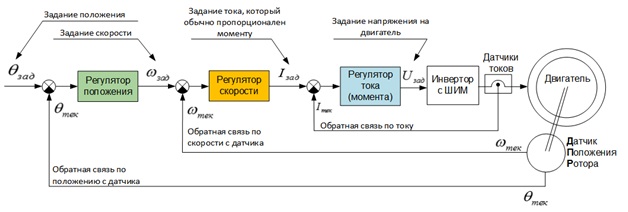
Picture 3 - Three-loop control system of the slave [5]
Feedback provides a great opportunity for the motor control, so the maximum compensation of the lack of planned use of the positioning mode. This allows you to limit the stepper motor speed, acceleration and current.
3.2 Choosing a microcontroller.
3.2 Choosing a microcontroller.
For realization of tasks require considerable microcontroller performance and compatibility with MATLAB. On the basis of these criteria was selected STM32F4Discovery.
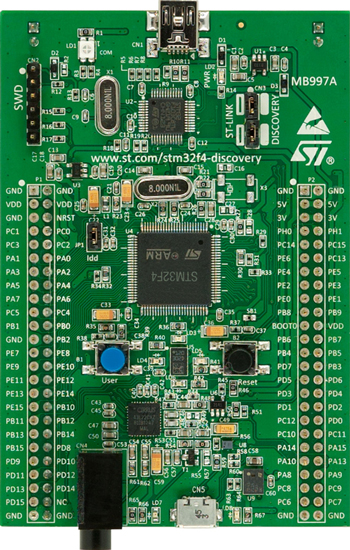
Picture 4 - STM32F4Discovery
At the heart of the board is STM32F407VGT6 microcontroller with a core ARM Cortex-M4 and the maximum clock frequency of 168 MHz, it can be used in digital signal processing and other applications, where you need maximum performance. The presence of 1 megabyte of flash memory and 192 Kbytes of RAM simply impressive. It presents all standard peripherals, such as the DAC, ADC, SPI, I2C, PWM, RTC. There is also support USB host and the Ethernet, there DCMI interface to connect the camera to connect the SDIO and SD cards, as well as hardware random number generator. Microcontrollers STM32f4 characterized by the presence of pre-needled them loader. With this bootloader user downloads a program to the microcontroller without the use of traditional individual programmers and hardware connected to the computer via USB-interface [6].
3.3 Choosing a microcontroller.
3.3 Choosing driver.
Typically, logic signals to control the stepper motor generates the microcontroller. Resources modern microcontroller is enough for this, even in the "heavy" mode - microstepping.
To connect stepper motors through the low-voltage logic signal microcontrollers required signal amplifiers - drivers.
The driver features include:
- providing the necessary voltage and current to the phase windings of the motor;
- Switching windings;
- inclusion;
- Off;
- a change of polarity;
- Protection of the switching elements of the voltage of self-induction coils [7].
Stepper motor driver L298n was chosen to provide the aforementioned functionality.
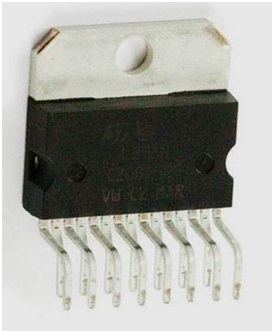
Pic. 5 - Stepper Motor Driver L298N
L298N is full bridge driver to control the bi-directional loads with currents up to 2 A and voltages up to 46 V.
- The driver is designed to control components with inductive loads such as solenoids, relays, stepper motors.
- The control signals are TTL compatible levels.
- Two inputs enable permission to disconnect the load from the input signals irrespective of the chip.
- It is possible to connect external current sensors for the protection and control of the current of each bridge.
- The device is protected against overheating at + 70 ° C
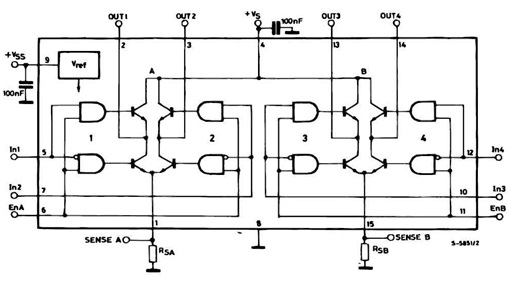
Picture 6 - Block diagram L298N [8]
Remarks
At the time of writing this essay master's work is not yet complete. Estimated completion date: May 2017 The full text of work and materials on the topic can be obtained from the author or his manager after that date.
References
1. Аддитивные технологии в машиностроении / Зленко М.А., Попович А.А., Мутылина И.Н. Учебное пособие. – Санкт-Петербург, СПбГУ, 2013 - 6с.
2. 3Д печать органов [электронный ресурс] – Режим доступа: 3d-expo.ru
3. Кенио Т. – Шаговые двигатели и их микропроцессорные системы управления / Перевод с англ. М.: Энергоатомиздат, 1987. — 200 с.
4. Сервопривод [электронный ресурс] – Режим доступа: Википедия
5. Поддержание положения в сервоприводе: подчинённое регулирование vs шаговый режим [электронный ресурс], – Режим доступа geektimes.ru
6. STM32F4DISCOVERY [электронный ресурс] – Режим доступа: www.st.com
7. Драйверы шагового двигателя: униполярный, биполярный, L298N. [электронный ресурс] – Режим доступа: mypractic.ru
8. Программируемые роботы. Создаем робота для своей домашней мастерской / Вильямс Дж. Пер. с анг. А. Ю. Карцева – М.: НТ Пресс, 2006. – 240с.