Abstract
Content
- Introduction
- 1. Theme urgency
- 2. Goal and tasks of the research
- 3. Modernization methodology and technical re-equipment of rectification complexes in the chemical industry
- 4. Optimization one-column distillation apparatus for chemical technology and refining processes
- 5. Processing of chemical coke products as a way to minimize negative impacts on the environment
- Conclusion
- References
Introduction
Natural energy sources such as oil, natural gas, gas condensate and coal are essential in the development of all sectors of the economy. The wide demand for refined petroleum products in the past decade has led to an intensive growth of the petrochemical industry. Currently sharply raises the question of expanding the range of marketable products, improve its quality and reduce energy consumption.
To address these issues by the current technological equipment and industrial technology, it is necessary improvement of existing and the development of more effective separation schemes and recovery of hydrocarbons.
1. Theme urgency
The analysis and optimization of complex technical systems, such as the refining industry facilities, basic methodological technique is a systematic approach that allows you to assess the impact of various factors on the efficiency of the chemical-technological system (CTS). The optimization problem can be solved both for the system as a whole and for its individual elements, taking into account the internal connections between the individual components of the CTS.
One of the most important components in the technological cycle of modern chemical and petrochemical industries are separation processes. An example is the isolation of benzene complex to the catalytic reforming units comprising stabilizing catalysate, aromatics extraction, and the individual components of the secondary rectification. Optimization of individual separation processes in the industry, including the allocation of benzene in a large number of works by authors such as V. V. Kafarov, S. S. Khachatryan, A. A. Gayle. However, a comprehensive analysis of interrelated technological blocks production plant was carried out.
2. Goal and tasks of the research
The goal of the work is to analyze existing and new methods of rectification equipment regimes optimization are used in various chemical engineering processes, as well as in drawing up their own algorithms.
Main tasks of the research:
- Analysis of technological systems for chemical separation products.
- Substantiation of design equipment characteristics, which used in the technological schemes.
- Development of a mathematical model modes fractionators.
- Drawing optimization algorithms distillation apparatus.
- The feasibility study of technical solutions.
Research object: the separation processes of substances in distillation plants.
Research subject: hardware design separation processes substances.
The scientific novelty of the work is to develop an algorithm to optimize hardware design separation processes of substances on the basis of the analysis of different methods for upgrading existing complexes distillation and analysis of the impact of various factors on the process efficiency.
The practical significance of the work is to use the results of the work for reduce the energy and materials when making design decisions and commercialization of modernized installations.
3. Modernization methodology and technical re-equipment of rectification complexes in the chemical industry
The major share of energy consumption in the chemical and petrochemical technologies (80%) are in the product recovery system from the reaction mixture and purification methods of distillation. These complexes are largely determine the yield and quality of end products. As a rule, all members of the distillation apparatus complexes are linked material and energy flows, often forming process recycles. Structural variation technology selection of chemical products (TSCP) of the same reaction mixture usually high, which affects both the energy sector and in the hardware design [1].
Reduced energy consumption, increase the yield and improve the quality of end products, which ensuring process stability and security of existing and new industries can significantly improved their competitiveness and export potential of the chemical and petrochemical industries.
However, in refineries often necessary to increase plant capacity and efficiency while maintaining the existing columns and towers process piping. These problems can be solved by upgrading the existing distillation systems.
An examination of existing production conducted flowsheet structure analysis, exploded material balance, modes of operation of each process step, the structural characteristics of the existing equipment and control systems. Requirements for the optimization of production are formulated (together with enterprises) increase in the yield and product quality, reducing energy consumption, limiting the removal of impurities, etc. The resulting survey information on the technological scheme of the structure, process parameters, design characteristics of the equipment and the control system is the based for the development of optimal technology [2].
The next and fundamental step in the development of new technologies and modernization of existing technology is a hardware-optimization of the individual steps and the technology in general under stationary conditions. Moreover, the preliminary synthesis TSCP or the results of a comprehensive survey of the current technology in this case are a first approximation for optimization [3].
4. Optimization one-column distillation apparatus for chemical technology and refining processes
Optimizing one-column distillation continuous machines is the problem part of the increasing resource and energy conservation in chemical and petrochemical industries. The literature describes in detail the methods of calculating the optimum reflux ratio at a given degree of separation [4–8]. If we use the method of scanning using a powerful computer technology and well-known software packages (CHEMCAD, ASPEN+, etc.), we can touch a variety of options to choose acceptable for the practical implementation of the process conditions and the effectiveness of the column.
Using the optimum search algorithms, analysis and expert evaluation of the results in certain steps, dramatically reducing the amount of computing work.
Accounting effects of yield increasing and products purity:
- in the selection of the distillation columns in the form of side straps to form a buffer zone between a certain point the efficiency of the expected product and the top of the column selection;
- the removal of impurities from the intermediate zones of concentration extremes are maximized by optimization of technological regimes and the column effectiveness;
- under cyclic impurities selections at small values of selections (1 ... 5% of the power supply), by optimization often leads to qualitatively new technical solutions.
In the examples, the methylamines separation, a number organofluorine product, purification of furfural obtain methyl, ethyl, propyl spirits, separating petrochemicals calculation methods is established and experimentally verified that the presence of extrema impurity concentrations along the column height of their size and position depend on the efficiency of the column and technological regimes. Improving the efficiency of the column and a reflux ratio it leads to an increase number of extremal concentrations. Removing impurities from the extrema of the lateral zones in the form of selections it leads to an increases as the purity of the bottoms and distillates.
5. Processing of chemical coke products as a way to minimize negative impacts on the environment
Coke industry provides resources black, non-ferrous metals and a number of other industries that require the fuel and a reducing agent, and is also a source of various chemical raw materials. Besides coke, coke products are fractions of coal tar, crude benzene, and others.
Technology capture chemical coke products, cleaning and processing require continuous improvement, because not always correspond to the modern requirements of ecology and energy saving.
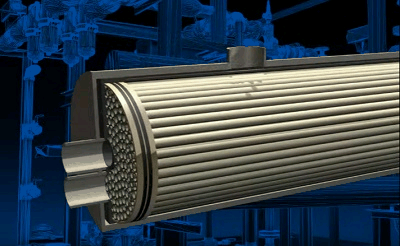
Figure 5.1 — Separations processes of coke oven gas in rectification column
animation: 4 frames, 6 cycles of repeating, 143 kilobytes
To capture the crude benzene is used absorption fraction of coal tar. It contains a number of components, the main ones are, naphthalene, methylnaphthalene, acenaphthene. Sorption of benzene provides a presence in the absorption methylnaphthalenes oil and naphthalene has negligible sorption capacity. Moreover, when adsorption occurs benzene naphthalene significant emissions into the atmosphere. Thus, absorption oil, which resin obtained by fractionation of low quality because the high content (do 60 wt.%) naphthalene therein.
Preparation based on an improved oil absorbency absorption fraction of coal tar naphthalene will reduce emissions and obtain it as a commodity product, an increase in the absorption of oil absorption capacity. Thus, the process of "improving" oil involves the removal of naphthalene from it.
Rectifying circuit for creating improved wash oil production is primarily needed to examine vapor-liquid equilibrium in binary systems, a mixture formed by the components studied. This makes it possible to study patterns of rectification separation in the computing experiment.
Conclusion
If you are upgrading distillation complexes last to be seen in close connection: technology + equipment + automatic control system.
Development of technical decisions on distillation systems modernization should included a number of interrelated steps: a) a systematic analysis of existing production; b) hardware and technology optimization in the conditions of stationary operation using simulation, which including the minimum experiment and optimization of numerical methods; c) to ensure the stability of the process; g) simulations start-up period.
Develop a methodology for the creation new distillations and modernization of existing distillation systems allows for minimal time and material resources to solve the problems on modernization of chemical and petrochemical plants with a choice of cost-optimal choices.
This master's work is not completed yet. Final completion: June 2017. The full text of the work and materials on the topic can be obtained from the author or his head after this date.
References
- Леонтьев В. С., Смыкалов П. Ю. Физико-химические и математические основы интенсификации и модернизации технологических процессов и оборудования для технологического перевооружения предприятий химической индустрии // Тезисы докладов V научно-технической конференции «Технохимия — 2003». СПб., 2003. C. 97 – 98.
- Леонтьев В. С., Смыкалов П. Ю. Создание современных экономически оптимальных технологий в химической промышленности и модернизация существующих производств с целью энерго- и ресурсосбережения // Тезисы докладов IV Международной научно-техническая конференции «Технохимия — 2002». СПб., 2002. С. 3 – 4.
- Леонтьев В. С., Шариков Ю. В., Седов В. М. Подход к модернизации и техническому перевооружению ректификационных комплексов в нефтехимической промышленности // Материалы отраслевого совещания главных механиков нефтеперерабатывающих и нефтехимических предприятий России и СНГ. М.: Компрессорная и химическая техника, 2003. С. 110 – 117.
- Анисимов И. В., Бодров В. И., Покровский В. Б. Математическое моделирование и оптимизация ректификационных установок. М.: Химия, 1975, 216 с.
- Бояринов А. И., Кафаров В. В. Методы оптимизации в химической технологии. М.: Химия, 1975. — 575 с.
- Петлюк Ф. Б., Серафимов Л. А. Многокомпонентная ректификация. Теория и расчет. М.: Химия, 1983, 304 с.
- Кафаров В. В. Методы кибернетики в химии и химической технологии. М.: Химия 1985. — 468 с.
- Леонтьев В. С. Разработка оптимальных систем разделения химических продуктов // Тезисы докладов Международной научно-практической конференции «Химия для топливно-энергетического комплекса России». С.-Пб., 2000. С. 92 – 93.
- Огородников С. К., Лестева Т. М., Коган В. Б. Азеотропные смеси. — С-Пб.: Химия, 1971. — 848 с.
- Гарбер Ю. Н., Караваев Н. М., Зыков Д. Д. // Украинский химический журнал, Т. 21, вып. 2, 1955. - С. 177 – 179.