Реферат по теме выпускной работы
Содержание
- Введение
- 1. Актуальность темы
- 2. Цель и задачи работы, планируемые результаты
- 3. Методология модернизации и технического перевооружения ректификационных комплексов химических предприятий
- 4. Оптимизация одноколонных ректификационных аппаратов для химических технологий и процессов нефтепереработки
- 5. Переработка химических продуктов коксования как способ минимизации негативного воздействия на окружающую среду
- Выводы
- Список источников
Введение
Природные энергоносители, такие как нефть, природный газ, газовый конденсат, уголь имеют важнейшее значение в развитии всех отраслей народного хозяйства. Широкая потребность в продуктах нефтепереработки в последнее десятилетие привела к интенсивному росту нефтехимической промышленности. В настоящее время остро встает вопрос о расширении ассортимента товарной продукции, улучшения ее качества и снижении энергозатрат.
Для решения этих вопросов необходимо усовершенствование существующих и разработка более эффективных схем разделения и утилизации углеводородного сырья, действующего технологического оборудования и промышленных технологий.
Кроме этого, на предприятиях, имеющих технологическую потребность в тепловой энергии круглый год важным и актуальным является организация оптимальной схемы энерго- и ресурсосбережения. В настоящее время для решения этих задач широко используются мини-ТЭЦ, где наряду с электроэнергией потребитель использует, т. е. утилизирует и тепловую энергию, повышая тем самым общий КПД установок. Мини-ТЭЦ представляют собой современное высокотехнологичное и энергосберегающее оборудование, наиболее приемлемое, с позиций «эффективность–стоимость».
1. Актуальность темы
При анализе и оптимизации сложных технических комплексов, таких как объекты нефтеперерабатывающей промышленности, основополагающим методологическим приемом является системный подход, который позволяет оценивать влияние различных факторов на эффективность функционирования химико-технологической системы (ХТС). Задача оптимизации может решаться как для системы в целом, так и для ее отдельных элементов с учетом внутренних связей между отдельными составляющими ХТС.
Одной из важнейших составляющих технологического цикла современных химических и нефтехимических производств являются процессы разделения. Примером может служить комплекс выделения бензола на установке каталитического риформинга, включающий блоки стабилизации катализата, экстракции ароматических углеводородов и вторичной ректификации индивидуальных компонентов. Оптимизации отдельных процессов разделения в промышленности, в том числе при выделении бензола, посвящено большое количество работ таких авторов, как В. В. Кафаров, С. С. Хачатрян, А. А. Гайле. Однако комплексного анализа взаимосвязанных технологических блоков промышленной установки не производилось.
Ввиду постоянно растущего спроса на бензол на мировом рынке углеводородов (200–300 тыс. т/год), одной из важных задач, которая может быть решена методами системного анализа при исследовании ХТС производства бензола, является повышение производительности действующих установок.
2. Цель и задачи работы, планируемые результаты
Цель работы заключается в анализе существующих и новейших методов оптимизации режимов работы ректификационного оборудования, используемых в различных процессах химической технологии, а также в составлении собственных алгоритмов.
Задачи, решаемые для достижения указанной цели:
- Анализ технологических систем по выделению различных химических продуктов.
- Обоснование конструктивных характеристик оборудования, используемых в технологических схемах.
- Разработка математической модели режимов работы ректификационных колонн.
- Составление алгоритмов оптимизации ректификационных аппаратов.
- Технико-экономическое обоснование технических решений.
Объект исследования: процессы разделения веществ в ректификационных установках.
Предмет исследования: аппаратурное оформление процессов разделения веществ.
Научная новизна работы ззаключается в разработке алгоритма оптимизации аппаратурного оформления процессов разделения веществ на основе анализа различных методов модернизации существующих ректификационных комплексов и анализа влияния различных факторов на эффективность процессов.
Практическое значение работы заключается в использовании результатов работы для снижения энерго-, и материалопотребления при принятии проектных решений и промышленном внедрении модернизированных установок.
3. Методология модернизации и технического перевооружения ректификационных комплексов химических предприятий
Основная доля в потреблении энергии в химических и нефтехимических технологиях (до 80%) приходится на систему выделения продуктов из реакционной массы и их очистки методами ректификации. Эти комплексы во многом определяют выход и качество товарных продуктов. Как правило, все входящие в ректификационные комплексы аппараты связаны между собой материальными и энергетическими потоками, образующими нередко технологические рециклы. Структурная вариантность технологий выделения химических продуктов (ТВХП) из одной и той же реакционной смеси, влияющая как на энергетику, так и на аппаратурное оформление, как правило, велика [1].
Снижение энергоемкости, увеличение выхода и повышение качества товарных продуктов, обеспечение технологической стабильности и безопасности существующих и вновь создаваемых производств может существенно повысить их конкурентную способность и экспортный потенциал химических и нефтехимических производств.
Вместе с тем на нефтеперерабатывающих заводах часто возникает необходимость повышения мощности установок и их эффективности при сохранении существующих корпусов колонн и технологической обвязки. Данные задачи можно решить за счет модернизации существующих ректификационных комплексов.
При обследовании действующих производств проводится анализ структуры технологической схемы, покомпонентного материального баланса, режимов работы каждой технологической стадии, конструктивных характеристик существующего оборудования и систем управления. Формулируются (совместно с предприятиями) требования к оптимизации производств: повышение выхода и качества продуктов, снижение энергоемкости, удаление лимитирующих примесей и т. д. Полученная в результате обследования информация по структуре технологической схемы, параметрам процесса, конструктивным характеристикам оборудования и системе управления является основой для разработки оптимальной технологии [2].
Следующим и основополагающим этапом при разработке новых современных технологий и модернизации существующих является аппаратурно-технологическая оптимизация отдельных стадий и технологии в целом при стационарных условиях работы. Причем предварительный синтез ТВХП или результаты комплексного обследования действующей технологии являются в данном случае первым приближением для оптимизации. Последовательность работ данного этапа укрупненно представлена на рис. 3.1 [3].
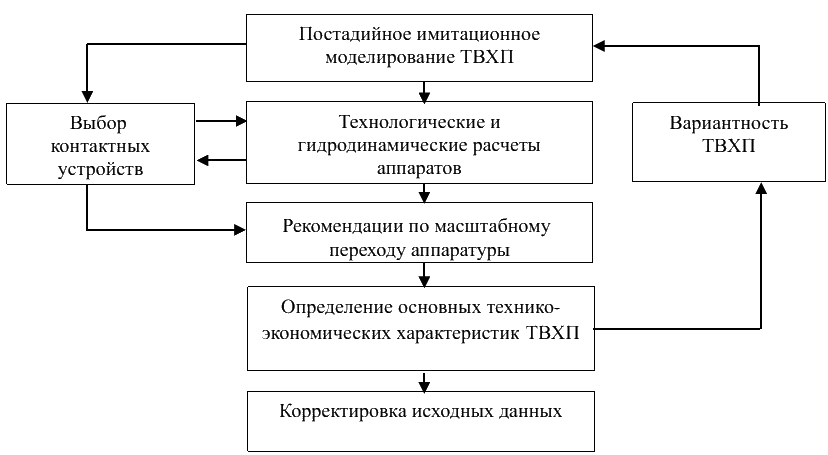
Рисунок 3.1 — Последовательность аппаратурно-технической оптимизации при стационарных условиях работы
4. Оптимизация одноколонных ректификационных аппаратов для химических технологий и процессов нефтепереработки
Оптимизация работы одноколонных ректификационных аппаратов непрерывного действия — составная часть задачи повышения ресурсо- и энергосбережения химических и нефтехимических производств. В литературе подробно описаны методы расчета оптимального флегмового числа при заданной степени разделения [4–8]. Методом сканирования при использовании мощной вычислительной техники и известных программных комплексов (CHEMCAD, ASPEN+ и др.) можно, перебрав множество вариантов, выбрать приемлемые для практической реализации технологические режимы и эффективность колонны.
Использование алгоритмов поиска оптимума, с анализом и экспертной оценкой получаемых результатов на определенных шагах, резко сокращает количество вычислительных работ.
Учет эффектов повышения выхода и чистоты продуктов:
- при их отборе из ректификационных колонн в виде боковых погонов с формированием буферной зоны определенной эффективности между точкой отбора целевого продукта и верхом колонны;
- при удалении промежуточных примесей из зон их концентрационных экстремумов, максимизированных за счет оптимизации технологических режимов и эффективности колонны;
- при циклических отборах примесей при малых величинах отборов (1 ... 5 % от подачи питания), — часто приводит при оптимизации к качественно новым техническим решениям.
На примерах разделения метиламинов, ряда фторорганических продуктов, очистки фурфурола, получения метилового, этилового, пропиловых спиртов, разделения продуктов нефтехимии расчетными методами установлено и экспериментально подтверждено, что при наличии экстремумов концентраций примесей по высоте колонны их величина и положение зависят от эффективности колонны и технологических режимов. Повышение эффективности колонны и флегмовых чисел приводит к росту экстремумов концентраций. Удаление примесей из зоны экстремумов в виде боковых отборов повышает чистоту как кубовых продуктов, так и дистиллятов.
При выделении химических продуктов из реакционных смесей и их очистке, когда доля отбора мала (для легколетучих и промежуточных примесей менее 1 %, для высококипящих примесей, отбираемых в виде кубовой жидкости — менее 5 %), использование циклических отборов при равных энергозатратах приводит к более высокой степени разделения, обеспечивает запас технологической устойчивости и более высокое качество продуктов, чем при постоянном отборе [5–7]. Частота и скважность отборов определяются на основе алгоритмов расчета переходных процессов в ректификационных колоннах. Типичными примерами эффективности циклических отборов являются колонны выделения легколетучих примесей (фурана и др.) и 1-бутанола в производстве ТГФ из фурфурола, колонна отделения легколетучих примесей при очистке ацетона в производстве ПВ, товарная колонна и колонна концентрирования метанола в производстве этилового спирта.
Алгоритм оптимизации одноколонных аппаратов, основанный на интегральном использовании установленных эффектов, приведен на рис. 4. 1, где R — флегмовое число; е — доля отбора дистиллята, кмоль/кмоль; Е — энергия, затрачиваемая на проведение процесса, кДж; Р — давление в колонне, МПа; N — эффективность ректификационной колонны (число теоретических тарелок); Nf — номер теоретической тарелки колонны (считая снизу), на которую подается питание.
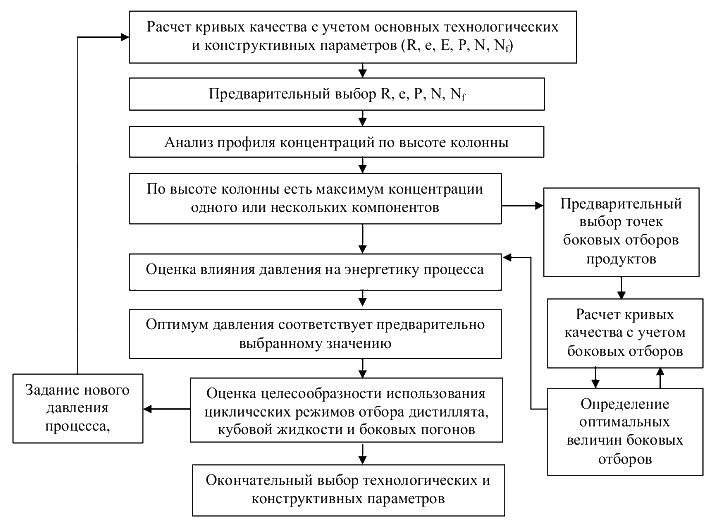
Рисунок 4.1 — Алгоритм оптимизации одноколонных аппаратов непрерывного действия
Оптимальные характеристики (эффективность колонны (Nопт), точки ввода питания (Nfопт), точки и величины боковых отборов продуктов (Nfбо, ебо), флегмовое число (Rопт), доля отбора дистиллята (еопт), давление процесса (Ропт) определяются с помощью построения и анализа семейства «кривых качества». Под «кривыми качества» понимаются зависимости Еотн = f (N, N/Nf) или N = f (Еотн, N/Nf), Еотн = f (Nf), Еотн = f (P), каждая точка которых характеризует совокупность конструктивных и технологических параметров, обеспечивающих требуемые показатели качества товарного продукта, являющиеся постоянной величиной для всего множества точек. Параметр Еотн = (R+1)·e косвенно характеризует величину энергозатрат (Е) на ректификацию [6].
5. Переработка химических продуктов коксования как способ минимизации негативного воздействия на окружающую среду
Коксохимическая промышленность обеспечивает ресурсами черную, цветную металлургию и ряд других производств, где необходимы топливо и восстановитель, а также является источником разнообразного химического сырья. Кроме кокса, продуктами коксохимии являются фракции каменноугольной смолы, сырой бензол и др.
Технологии улавливания химических продуктов коксования, их очистки и переработки требуют постоянного совершенствования, поскольку далеко не всегда соответствуют современным требованиям экологии и ресурсосбережения.
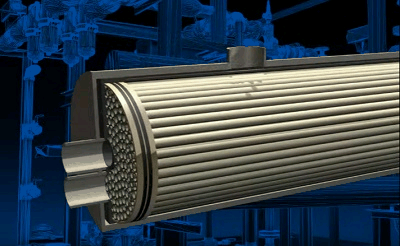
Рисунок 5.1 — Процесс разделения коксового газа в ректификационной колонне
анимация: 4 кадра, 6 циклов повторения, 143 килобайт
Для улавливания сырого бензола используется поглотительная фракция каменноугольной смолы. Она содержит множество компонентов, основными из которых являются, нафталин, метилнафталины, аценафтен. Сорбцию бензола обеспечивает присутствие в поглотительном масле метилнафталинов, а нафталин обладает незначительными сорбционными способностями. Кроме того, при адсорбции бензола происходят значительные выбросы нафталина в атмосферу. Таким образом, поглотительное масло, получаемое при фракционировании смолы, низкого качества из-за высокого содержания (до 60% масс.) в нем нафталина.
Получение улучшенного поглотительного масла на основе поглотительной фракции каменноугольной смолы будет способствовать снижению выбросов нафталина в атмосферу и получению его в качестве товарного продукта, увеличению абсорбционной способности поглотительного масла. Таким образом, процесс «улучшения» масла предполагает удаление из него нафталина.
Нафталин и метилнафталины обладают относительно близкими температурами кипения (218 °С, 241 °С, 245 °С), поэтому для выделения нафталина из поглотительной фракции каменноугольной смолы мы предлагаем азеотропную ректификацию. Согласно литературным данным [9], азеотропным агентом может служить капроновая кислота, которая образует азеотропную смесь с нафталином, а с метилнафталинами смеси зеотропны.
Для создания ректификационной схемы производства улучшенного поглотительного масла, прежде всего, необходимо было изучить парожидкостное равновесие в бинарных системах, образованных компонентами изучаемой смеси. Это позволяет изучить закономерности ректификационного разделения в вычислительном эксперименте.
Прогнозирование парожидкостного равновесия производилось с помощью групповой модели UNIFAC, а описание полученных псевдоэкспериментальных данных осуществлялось с использованием уравнения вильсона, в результате чего были определены параметры бинарного взаимодействия веществ в исследуемой смеси. Pависимость упругости пара индивидуальных веществ от их температур кипения моделировалась уравнением Антуана.
Результаты математической обработки — параметры уравнения Вильсона для всех двухкомпонентных систем исследуемой смеси были положены в основу расчета процесса ректификации.
Ректификационное разделение в вычислительном эксперименте принято было проводить на колонне периодического действия диаметром 1 м. Критерием параметрической оптимизации режима работы колонны служил минимум энергозатрат при заданном качестве продуктов разделения. Оптимизируемыми параметрами являлись: общая эффективность колонны (число теоретических тарелок) — Nт.т, флегмовое число — R, продолжительность ректификационного разделения — т.
Перед нами были поставлены две задачи:
- удалить нафталин из поглотительной фракции с помощью азеотропной ректификации;
- провести регенерацию разделяющего агента;
Регенерация разделяющего агента будет проводиться также путем ректификации при изменении давления с 760 мм рт. ст. до 20 мм рт. ст.
В ходе моделирования нами было выявлено, что азеотропная смесь капроновая кислота - нафталин при понижении давления обогащается капроновой кислотой (рис. 5. 2). При давлении 10 мм рт. ст. происходит инверсия, смесь становится зеотропной, и нафталин является низкокипящим компонентом. Исходя из этого, с целью минимизации расхода разделительного агента, было принято проводить разделение поглотительной фракции при давлении 20 мм рт. ст., т. е. смесь еще азеотропная и она максимально обогащена нафталином [10].
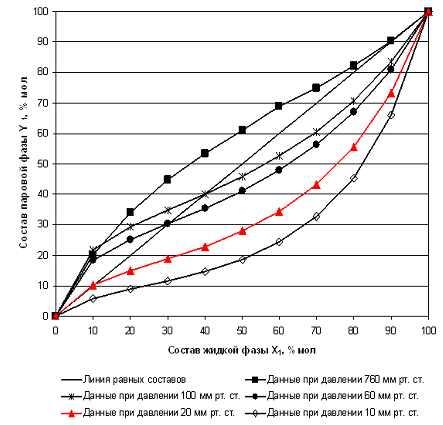
Рисунок 5.2 — Равновесие жидкость–пар в системе капроновая кислота (1) – нафталин (2)
Предлагается технологическая схема получения улучшенного поглотительного масла. Основной разделительный элемент — ректификационная колонна периодического действия, на которой попеременно реализуются процессы отделения нафталина и регенерации азеотропного агента.
На первой стадии нафталин выделяется в виде азеотропной смеси с капроновой кислотой в дистиллят.
Выводы
При модернизации ректификационных комплексов последние необходимо рассматривать в неразрывной связи: технология + аппаратура + система автоматического управления.
Разработка технических решений по модернизации ректификационных комплексов должна включать ряд взаимосвязанных этапов: а) системный анализ существующего производства; б) аппаратурно-технологическую оптимизацию в условиях стационарной работы с использованием имитационного моделирования, включающего минимальный эксперимент и оптимизацию численными методами; в) обеспечение технологической устойчивости; г) моделирование ситуаций пускового периода.
Разработанная методология создания новых и модернизации существующих ректификационных комплексов позволяет при минимальных затратах временных и материальных ресурсов решать задачи по техническому перевооружению химических и нефтехимических производств с выбором экономически оптимальных вариантов.
При написании данного реферата магистерская работа еще не завершена. Окончательное завершение: июнь 2017 года. Полный текст работы и материалы по теме могут быть получены у автора или его руководителя после указанной даты.
Список источников
- Леонтьев В. С., Смыкалов П. Ю. Физико-химические и математические основы интенсификации и модернизации технологических процессов и оборудования для технологического перевооружения предприятий химической индустрии // Тезисы докладов V научно-технической конференции «Технохимия — 2003». СПб., 2003. C. 97 – 98.
- Леонтьев В. С., Смыкалов П. Ю. Создание современных экономически оптимальных технологий в химической промышленности и модернизация существующих производств с целью энерго- и ресурсосбережения // Тезисы докладов IV Международной научно-техническая конференции «Технохимия — 2002». СПб., 2002. С. 3 – 4.
- Леонтьев В. С., Шариков Ю. В., Седов В. М. Подход к модернизации и техническому перевооружению ректификационных комплексов в нефтехимической промышленности // Материалы отраслевого совещания главных механиков нефтеперерабатывающих и нефтехимических предприятий России и СНГ. М.: Компрессорная и химическая техника, 2003. С. 110 – 117.
- Анисимов И. В., Бодров В. И., Покровский В. Б. Математическое моделирование и оптимизация ректификационных установок. М.: Химия, 1975, 216 с.
- Бояринов А. И., Кафаров В. В. Методы оптимизации в химической технологии. М.: Химия, 1975. — 575 с.
- Петлюк Ф. Б., Серафимов Л. А. Многокомпонентная ректификация. Теория и расчет. М.: Химия, 1983, 304 с.
- Кафаров В. В. Методы кибернетики в химии и химической технологии. М.: Химия 1985. — 468 с.
- Леонтьев В. С. Разработка оптимальных систем разделения химических продуктов // Тезисы докладов Международной научно-практической конференции «Химия для топливно-энергетического комплекса России». С.-Пб., 2000. С. 92 – 93.
- Огородников С. К., Лестева Т. М., Коган В. Б. Азеотропные смеси. — С-Пб.: Химия, 1971. — 848 с.
- Гарбер Ю. Н., Караваев Н. М., Зыков Д. Д. // Украинский химический журнал, Т. 21, вып. 2, 1955. - С. 177 – 179.